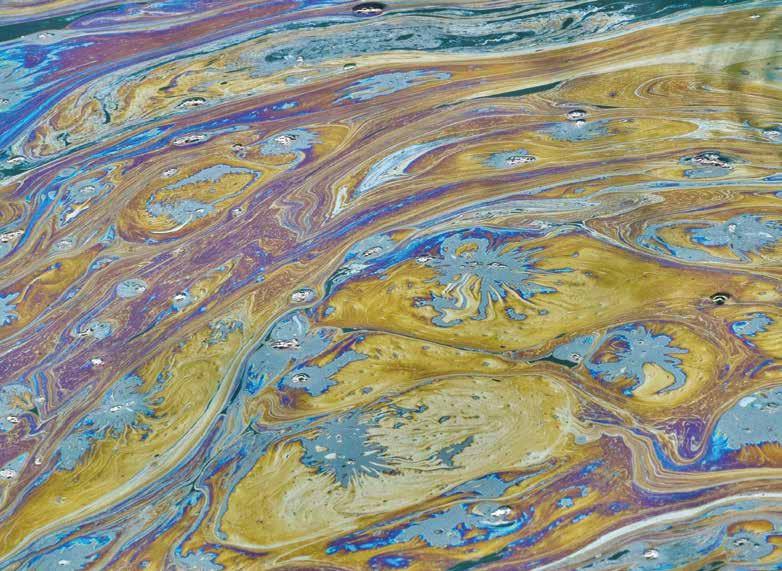
32 minute read
Wastewater Treatment & Technology
Industry and academia need to talk more to solve water challenges
Despite widespread interest in finding innovative ways to monitor and remove pollutants and pathogens from wastewater, a significant unmet challenge remains, as Dr Robin Knight, of IN-PART, discusses.
Advertisement
Water is key to a wide range of industrial processes, chemicals and materials production, and agriculture. There are few industrial sectors that do not rely on water in their value chain. Yet many of these processes create polluted wastewater which harms human health and the environment.
Water pollution is a challenge in need of a collaborative solution
IN-PART regularly surveys and consults our network of 6,000 science, engineering and technology companies to understand the unmet R&D needs they are seeking solutions to.
Recent conversations with our industry network – including with water technology companies like De Nora, Evoqua, Hach and Puraffinity, and companies involved in water R&D such as Suez, Veolia, Southern Water, Beko, and AkzoNobel – zeroed in on the fact that water monitoring and treatment was a major unsolved challenge across sectors. These conversations, which included a series of webinars, uncovered a range of priorities. The overarching message was a widespread need for new, more accurate, easy-to-use, rapid, continuous flow sensors, and new materials and techniques to remove a wide range of pollutants. Much talk was about more accurate detection and removal of existing pollutants including particulates, heavy metals, and bacteria. Microplastics, PFAS, and organic pesticides and their derivatives, were also flagged as having a serious unmet need for detection and removal. Concerns were raised about nanoparticles – used in products such as hard-wearing paints and coatings, sunscreens, and self-cleaning windows – where little is known about the health and environmental implications. What underpinned all of these commercial problems was that the solutions will require finely tuned devices developed by people with a deep understanding of the physical and chemical properties of these pollutants, and advanced analytical techniques. In other words, people in academia.
Uncovering solutions to water treatment from academia
Our Global Challenge campaign was a vindication of this. Having broadly defined the scope of the challenge by surveying the research from academia already uploaded on our matchmaking platform, Connect, we invited the global research community to submit water monitoring and treatment solutions.
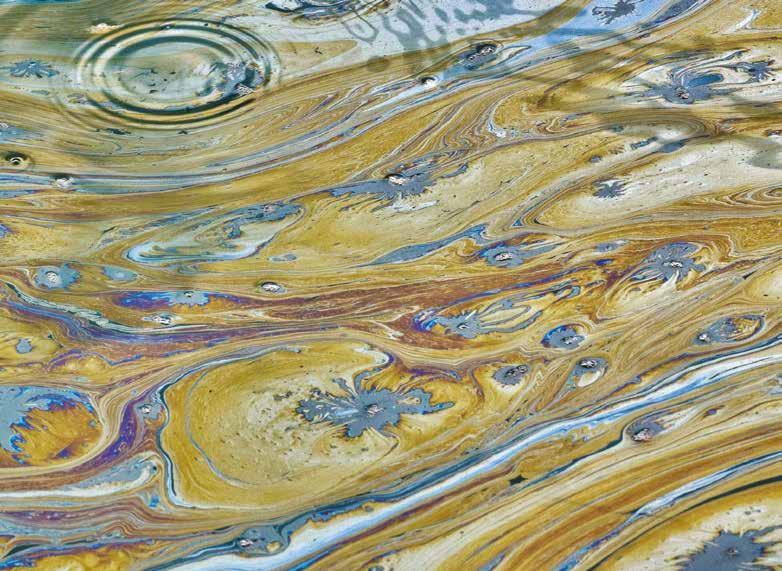
In just six weeks we surfaced over 100 innovations from around the world previously unknown to our water industry network. Half (43%) related to the treatment of water for pollutants, 20% to the treatment of water for natural particulates and pathogens (20%) and 17% to the detection of pollutants in water. Solutions we surfaced included a portable, low-cost, reusable sensor to detect and quantify up to 10 different PFAS molecules (New Jersey Institute of Technology); and robust, inexpensive sorbents to remove PFAS contaminants from water (Suny Research Foundation, NY). Others included reusable smart filters based on polymeric compounds capable of trapping five of the UK’s most common pesticides, and a plant growth regulator (University of Lincoln). And a technique to capture silver nanoparticles – found in a variety of modern technology, from nanomedical imaging to toothpaste – in replaceable, easy-to-use capsules using a novel ion-exchange method (University of Massachusetts Dartmouth). These and others have attracted considerable interest from companies looking for water treatment and monitoring solutions (here is a summary of the top 20 water innovations by industry engagement).
The importance of industryacademic partnerships in solving global challenges
We did not create any of these innovations – they have been developed by leading academic researchers in universities across the world. But thanks to the Challenge, we were able to connect those developing the solutions to those who need them. This matchmaking is important if we are to make progress towards solving global problems like water pollution. Academic researchers all over the world are creating solutions to combat the greatest challenges we face today. But their work sometimes stays locked up in labs or on small local trials, and does not always make it into the hands of the right people working in industry who need the solutions. Similarly, people with the expertise and the research often do not appreciate its full range of potential applications around the world. Partnerships between academia and industry are not a new thing, but their profile has grown in recent years, and the pandemic in particular showed just how powerful academia-industry collaboration is, through the rapid development of life-saving vaccines. A partnership between academia and industry is particularly advantageous when there is a problem in need of a complex scientific solution – especially one that involves advanced physical, chemical or biological analyses and an understanding of materials. Researchers bring specialist scientific expertise, industry brings an understanding of real-world need.
This Global Challenge campaign is a testament to this. Through this challenge, we’ve initiated 100 new conversations between industry and academia that otherwise would not have happened. Soon, some of these will turn into collaborations that make a real impact on reducing water pollution and improving water quality worldwide. Dr Robin Knight is a co-founder of IN-PART, a service that matches research pioneers from academia with decision-makers in industry. The full results of the Challenge are detailed in a white paper published on the campaign alongside a full list of water treatment innovations.
Maximise Thermal Hydrolysis production with correct pump
According to government sources, there are 7,078 sewage treatment works (STW) in England and Wales, and 10,814 STW in Scotland and Northern Ireland. Pumping and storing sludge cake during the wastewater treatment process can be costly, driving water companies to technologies that reduce their volume to minimise such costs.
This can be achieved through conventional Anaerobic Digestion (AD) or through Advanced Anaerobic Digestion (ADD) processes, such as Thermal Hydrolysis Process (THP). ADD can reduce the volume of solids and increase the yield of biogas used to power engines. This can make plants energy self-sufficient or generate income by exporting power to the National Grid.
Anglian Water’s Cotton Valley
At Cotton Valley Sludge Treatment Centre (STC), one of Anglian Water’s ten main STCs, competitor’s progressive cavity pumps were installed to back mix the dewatered sludge and pump it into the THP. The two pumps were costing overall circa £100K per annum due to rotor and stator changes every 3-6 months. Their inability to transfer no more than 3.5m3/h (bottleneck and limiting biogas production) meant the site was not able to meet the design criteria limiting the amount of imported raw cake being handled to only 120 tonnes per day. Additionally, before pump maintenance could be carried out, the silo had to be emptied. This also meant cake imports from satellite sites had to be diverted, which resulted in substantial logistical costs. SEEPEX supplied and installed two custom-made open hopper pumps with a dimensionally identical hopper to fit within the same footprint of the original pumps whilst delivering over 55% increased throughput capacity from 3.5m3/hr to 5.5m3/ hr.
Prior to the installation of the new pumps, Anglian Water was processing approx. 120 tonnes per day of imported sludge cake with both pumps running. With the new pumps installed, the customer is now able to exceed this by 50% (from 120 tonnes up to 180 tonnes) whilst maintaining the same footprint and motor size.
“Due to the reliability and performance of the new SEEPEX pumps there is an increase in uptime of the cake import facility at Cotton Valley,” explains Luke Fish, Production Manager at Anglian Water. “This has not only allowed us to increase the sludge throughput on site and therefore generate more biogas but has also given us significant savings in logistics and raw cake storage costs.”
At a Major Advanced Digestion plant in the UK
Existing competitor’s progressive cavity (PC) pumps at a large AD plant were unreliable, causing downtime to the thermal hydrolysis streams. When the THP feed pumps were offline, this affected production and biogas generation. To address this, SEEPEX delivered a custom-made open hopper PC pump fitted with Maintain-In-Place technology to replace the original pump, incorporating condition monitoring and digital solutions. SEEPEX Maintain-In-Place technology includes Rotor Joint Access (RJA) and Drive Joint Access (DJA) which simplifies maintenance and improves availability of equipment. To complement these features, the pump’s baseplate is manufactured in three pieces (on wheels) which enables individual sections of the pump to be removed for maintenance or major overhaul. SEEPEX Digital Solutions facilitate preventative maintenance, equipment availability and process optimisation, which has a direct impact on reactive costs and biogas production – contributing to net zero objectives and increased sustainability. Since installation, there has been zero downtime and no drop off in performance, and the sludge handling process has gained resilience.
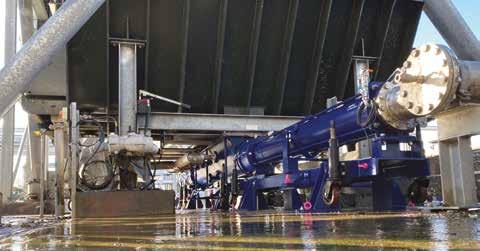
Zero downtime and no drop off in performance with SEEPEX PC Pumps and Digital Solutions
At another Major UK Thermal Hydrolysis Plant
SEEPEX open hopper pumps were used to replace unreliable chain conveyor systems. These pumps are used in two applications. Firstly, to transport the imported dewatered sludge from the imported belt facilities at a capacity of up to 75 m3/h with dry solids up to 32% to either of the two pre-THP silos, enabling a 20-minute turnaround time for the trucks to unload and prevent backlog of vehicles. Secondly, to transport the indigenous dewatered sludge from the four decanting centrifuges to a third pre-THP silo. Pump maintenance is carried out at ground level, improving health and safety issues associated with working at height with the previous conveyor installation. In addition, with the new SEEPEX pumps, the site now benefits from increased availability of their THP streams with subsequent improvements in gas yield.
The Key: Reliability and Right Feedstock
To achieve the full benefits of advanced digestion by thermal hydrolysis requires reliable and efficient delivery of feedstock to the process. SEEPEX solutions combine back mixing expertise with open hopper PC pump technology to both transfer and blend imported and indigenous dewatered sludges to the precise DS % content. This ensures optimum digestion and maximises biogas production, reducing carbon footprint.
seepex.com
The perfect pumps: Verder provides pumps for every stage of the wastewater treatment process
Wastewater treatment is 24-hour a day process, with domestic and industrial waste produced at all times of the day. Wastewater treatment is complex multi-stage process, but to meet these requirements many additional processes are needed to treat inflows, dose process chemicals, force particle sedimentation and remove contaminants to make water potable and waste safe for storage.
Pumping problems:
After waste has been screened for large objects such as wood, metal and plastics, flocculants are added so the solids precipitate in the bottom of the tank as sludge. Depending on the incoming liquid stream, additional chemicals may be added to neutralise contaminants or optimise pH levels. Lime, or milk of lime is one of the most widely used chemicals with excellent pH adjustment properties. Unfortunately, it is not an easy product to pump. It requires high line velocities and is highly abrasive, resulting in high rotor and stator wear rates on conventional pumps e.g., progressive cavity pumps. Traditional methods of lime dosing may prove tricky with frequent downtime. Once the liquid has been through primary treatment, the treated sludge is transported to farms for use as fertiliser, or anaerobically digested to produce biogas which can be sold into national grid networks. A proportion of the sludge is filter pressed and shipped to landfill. Ferric sludge is produced after flocculation and is deposited at the bottom of settling tanks forming a sludge blanket. This sludge can be extremely abrasive, causing stator wear on a traditional progressive cavity pump. This results in needing to increase the pump speed to maintain the flow rate. This increased speed increases suction pressure and reduces the amount of settled sludge content as more water is pulled into the lines, ultimately contaminating the already treated liquid. Waste water processes also need to verify the quality of the incoming waste stream and use analysers to detect the presence of contaminants or monitor key parameters that impact on downstream operations. Analysers need to be fed with consistent liquid volumes for optimum reporting and subsequent process control. Some pumps used in this application are not able to provide this reliability, so process control is less precise.
The solution - Verder pumps:
The Verderflex range of Dura peristaltic pumps are easy to install and maintain, significantly reducing downtime and minimising disruption. The pumps are extremely accurate and reliable, giving complete control over the treatment process. In the Dura pumps, the product is totally contained within the hose, eliminating the possibility that any moving parts can clog or corrode. This makes a peristaltic pump the perfect choice for pumping high solid content slurries such as lime. In filter press applications, consistent suction reduces water content for drier sludge and lower waste disposal costs. Verder pumps are ideal for this type of application. In testing scenarios, there are several pumps which could be used to improve the process. The new Verderflex Ds500 is ideal for metering and dosing and can give accurate quantities of liquid time and time again. As standard, the Ds500 is IoT enabled and can be monitored via the Remote Assistant app to provide process reports and updates for auditing purposes. The easy-to-change click and go cartridge can be swapped in a matter of seconds, meaning nasty chemicals are contained. Pumping wastewater sounds very easy, but often fluid contains long fibres and other abrasive solids. For water treatment a lot of different aggressive or abrasive chemicals are necessary. As a specialist for the water and wastewater industry, we can offer you a lot of different pumps which are designed with treatment works in mind and can handle most of the difficult fluids.
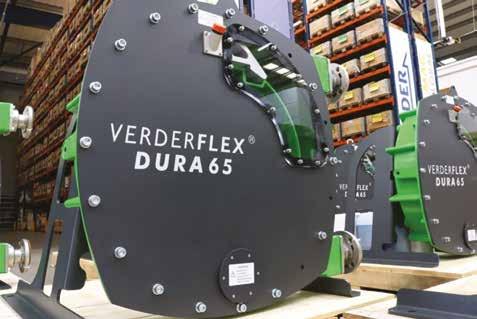

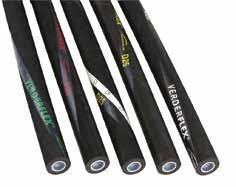
www.verder.co.uk
New biogas production landmark for Scottish Water’s acclaimed sludge facility at Nigg
If we took a short trip forward in time to 2040, and then looked back at how some organisations in the water industry successfully achieved Carbon Net Zero, it’s likely you’ll see a large four-letter word: NIGG.
This Scottish Water treatment centre in Aberdeen is currently leading the way as a centre of excellence for biogas production (from sludge), with its dedicated team tirelessly focused on improving efficiencies. This is a place that believes in ‘better’. It is also the first wastewater treatment plant in the United Kingdom to successfully co-digest. The Nigg Wastewater Treatment Works, which was built in 2002, has made some significant steps forward since Scottish Water took over ownership and operation in December, 2018; working with Cambi to upgrade the existing THP (thermal hydrolysis process) and importantly, installing a new digester mixing system, from Landia. From initially producing 250 cubic metres of gas per tonne of dry solids, levels have increased; first to 350, and has now climbed to an impressive 400 – 420. The 400-plus figure is also being achieved without unlimited, costly power. Typically, if standard propellers were in use, around 17 watts per cubic metre would be required, but with the Landia system running at what amounts to less than 12 hours in a 24-hour period, only 7 watts per cubic metre are needed for the anaerobic digester mixing. These latest numbers (at a site that has a small footprint for its energy output), are very much the result of fine-tuning and regular dialogue, as Nigg’s Operation Team Lead, Ewan Dickie, explains: “It is imperative that we understand the equipment and processes in front of us,” he said. “And two years on since the latest improvements began at Nigg, Landia are always there to answer any questions we have about enhancing the mixing of our digesters.” Prior to the upgrade, the facility had switched off the old compressor mixing system that had all too regularly caused problematical pipe blockages. The clean-out of the digesters for the upgrade revealed that 45% of the volume had been lost to grit and heavily compacted sludge.
Extremely robust mixing system
“Now,” added Ewan, “we have an extremely robust mixing system that comprehensively mixes our two 4000m3 digesters. We don’t get any problems. The mixers just sit in the background, working away. The equipment is also so much easier to maintain, because it’s externally-mounted”. Further evidence of Nigg proving how much energy from sludge can be produced at a wastewater treatment facility is its use of the biogas and heat from the Combined Heat & Power units (CHPs) for the site’s new boiler. £0.5M pa is now being saved on fuel oil. Two years ago, the original target set for utilising the CHPs (supplied by Clarke Energy) was 56%. It now stands at 73%. The CHPs were producing around 80% of the power required to run the site at Nigg. That figure has improved to the point where most of the time, Nigg is now exporting surplus energy to the National Grid. In addition to the intake from a local population of around 300,000, Nigg imports sludge cake from a further six Scottish Water wastewater treatment centres, and has commercial waste delivered from approximately 30 tankers per day. Since the introduction of the Landia digester mixing system and the upgrade of the Cambi THP, CO2 emissions have more than halved. The amount of biogas being produced has risen by more than 30%. In the first stage of the digester mixing process, the liquid (or sludge) is injected into the upper half of the tank, whilst biogas is aspirated from the top of the tank and mixed into the liquid. This not only has the benefit of reducing buoyancy at the surface of the liquid, but also sees the rising gas bubbles continue to mix after the pumps are switched off. Cambi’s proven Thermal Hydrolysis Process (THP) exposes sewage sludge at Nigg to high temperatures (160oC to 180oC) and pressures (about 6 bar), typically for 20 to 30 minutes for each batch to ensure pathogen kill. Sterilised and hydrolysed sludge is passed to the flash tank, which operates at atmospheric pressure. The sudden pressure-drop leads to substantial cell destruction of the organic matter in the sewage sludge, which is then cooled to its optimum temperature before it is fed to the digesters. Based on the proven ongoing success of Nigg’s biogas production, Scottish Water is considering the development of a further six sludge-to-energy facilities, which would represent a giant leap towards achieving the net zero target by 2040; five years earlier than the goal set by the Scottish Government.
1
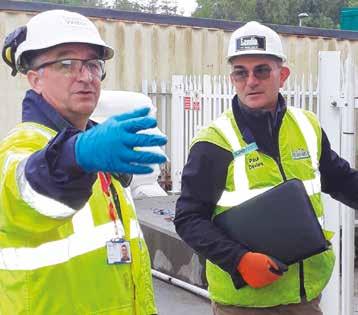
2
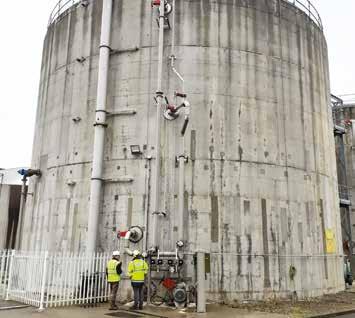
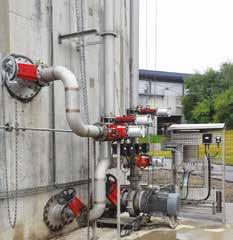
3 4
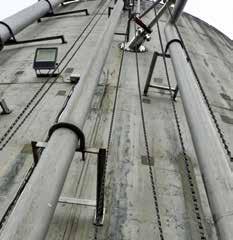
1
2
3
4
Since introducing Landia’s digester mixing system and upgrading Cambi’s THP, CO2 emissions at Nigg have more than halved
Nigg’s Operation Team Lead, Ewan Dickie (left) with Paul Davies from Landia
Easy to service outside the digester, the Landia Chopper Pump that forms part of the mixing system at Nigg
Landia’s digester mixing system at Nigg now produces a consistent 400 - 420 cubic metres of gas per tonne of dry solids
One shouldn’t be blasé about hearing the word ‘innovation’ in the water industry, but some would argue that it has become so overused that it has begun to lose its real meaning due to static purchasing habits. Nigg though is full of innovation, with constant, gradual progress, according to Simon Wrigglesworth, Operations Director for Scottish Water Grampian. “We’re all for genuine innovation”, he said, “but sometimes it’s not just about new technology; it can be about doing something differently. Cambi’s THP has been around for over 20 years, and the chopper pump, which is a key part of the digester mixing system, was invented by Landia back in 1950.”
He added: “It’s fair to say that at first, investing in the Landia mixing system seemed a bold move, because others were seen as a much ‘cheaper’ capital cost. But in an industry that promotes TOTEX, Landia were unmatched in providing meaningful numbers for the total cost of ownership, which showed that in the long term, they were in fact the least expensive option. We believe in what Henry Ford once said, that ‘If you do what you always do, you’ll always get what you’ve always had’. For us, ‘average’, and ‘same old, same old’, won’t do. We are adding resilience. The performance potential of the Landia digester mixing system is massive.”
Part of Nigg’s genuine innovation has also been its willingness to undertake a 3-month trial to co-digest residues from local distilleries and breweries with its domestic sewage. Not only were 58 tonnes of carbon saved, but the plant saw methane levels increased from 60% to 64%. This first for the industry in the UK, which was led by the publicly owned water company’s commercial subsidiary, Scottish Water Horizons, could be just the start of a move that could have a major positive impact to a more circular and sustainable economy. Keeping an ever-keen eye on all the production figures at Nigg is Process Engineer, Relina Dusa. During the past two years, she has worked on optimising the mixing with different run times, from 45 minutes per hour, down to 15. Operation now rests at 28 minutes per hour; not half an hour or thereabouts, but a very specific 28 minutes.
Need for proper mixing
have it”, said Relina. “It is important that we have experimented with different run times – and now I’m very happy with the gas yield of between 400 and 420 (cubes of gas per tonne of dry solids) that we’ve now reached. Over the past two years I have worked closely with Tony Challinor at Landia. We never have to wait for answers and feedback. There haven’t been any issues with the mixing system- and though it might sound like a small point, the Landia service engineers always clean up properly after themselves and leave everything tidy. We work well together.” From what has been learned and continues to be learned at Nigg, the prospect of Scottish Water developing six additional similar sites will be a landmark for the water industry in what can be achieved with sludge when optimising biogas production. Simon Wrigglesworth added: “We’ve come a long way with Nigg already. The water industry rightly has to focus on achieving regulatory compliance, but we’re always looking at how we can maximise the generation of green energy, in order to meet our commitment to reducing and ultimately eliminating carbon.” www.landiaworld.com
Achieve the best performance from your WWT plant
At OMEX we understand the importance of keeping the wastewater treatment facility at optimum performance. Below our operations manager, Dimitris Theodoridis, highlights the key points to achieve the best performance from your WWT plant:
Keep the biology strong and healthy
For the plant to function, the first area to look at is ensuring the biology is “happy”. Keeping the biology in working condition enables the plant to work, so this should usually be the first point to check on any site managers checklist. If the biology isn’t getting all the necessary elements it needs, such as adequate food, aeration and nutrition, the plant will subsequently fail and lose performance, this can in turn lead to wastewater being discharged with certain measured parameters being out of consent.
Nutrient Profiling
The best way to assess the biology in the plant is to analyse it. OMEX offer full technical support and provide facilities to assess the performance of the bacteria in the plant. The fully accredited OMEX labs can offer an in-depth analysis and treatment of all the possible problems which can occur within the wastewater treatment industry. OMEX technical staff will collect a set of samples to establish the status of the biological process.
Technical Advice
Once a full nutritional analysis of the plant has been undertaken, results should be analysed and discussed with a technical expert, who is able to advise on the best course of action to improve and optimise the process. The OMEX technical sales team are able to assess the plant via lab analysis and in-depth discussion with the site operator/manager to gain a thorough understanding of any issues the plant is experiencing. Once this process is completed a tailored product programme is put together, along with recommendations and appropriate dosing rates to achieve the desired outcome.
Key OMEX products for WWT
OMEX offer a full range of products to help with the optimisation of the wastewater treatment process, including:
Magmex - an environmentally friendly pH neutraliser. In addition,
Magmex contains certain compounds that are beneficial nutrients needed by the biology within the plant
Nutromex N&P (Plus) - strengthens the biology, stabilises performance and enables a more effective breakdown of the organic content in the raw wastewater
Micromex - when the plant is lacking in the number of microorganisms needed to process, Micromex augments the biology cultures, effectively breaking down the unwanted organics Anomex - in activated sludge processes there is a risk of hydrogen sulphide in the sludge storage tank, Anomex is used to minimise the risk of sludge becoming septic.
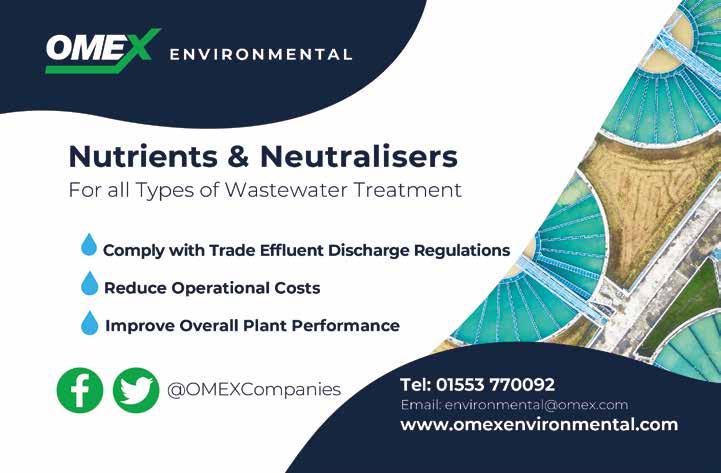
SEEPEX SAI optimises dewatering plant
Scottish Water’s Kinneil Kerse WwTW produces an estimated 4,701 tds of dewatered sludge which is conditioned with lime for use as fertiliser on land. The sludge operation at this site has been funded and is operated by Veolia who are contracted by Scottish Water. In 2021, as part of a modernisation project delivered by Veolia, two competitor’s progressive cavity (PC) pumps were installed to feed dewatered sludge into a SEEPEX lime mixing pump.
Blocked Pipework after Commissioning
After commissioning the new pumps, the site began to experience regular blockages in the discharge pipework which affected feeding the lime mixing process and sludge disposal. To clear the blockages the pipework had to be dismantled and the site incurred additional costs associated with the hire of a mobile lime dewatering unit. Veolia approached SEEPEX for a solution.
After assessing the installation, it was clear that the high friction losses generated when pumping 22-25 % DS sludge through 55m pipe length with a 3m. elevation including 3x 45° and 5x 90° bends were affecting the pumps’ performance. To address this, SEEPEX offered a trial for their Smart Air Injection (SAI). SAI is an energy efficient system that combines a SEEPEX open hopper progressive cavity pump with pneumatic dense phase conveying technology. The system is able to transport 16-40% DS dewatered sludge up to 1,000m. with a lower operating pressure requirement than conventional technology.
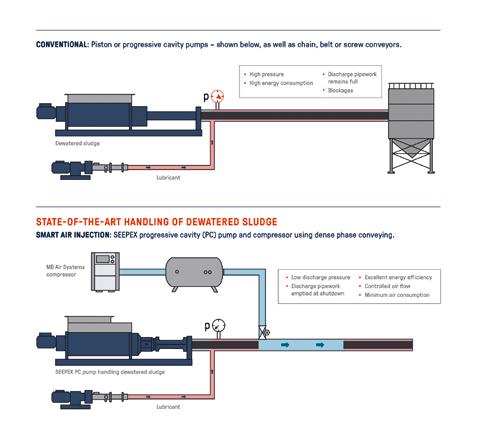
Veolia Blockage Free Solution for Sludge Cake Transfer
SEEPEX UK installed and commissioned the trial SAI system to demonstrate its effectiveness. Within the first 30 minutes of operation, SAI had cleared out all existing blockages and continued to perform. SEEPEX retrofitted the SAI system to the competitor’s equipment. This included: SEEPEX SAI controls and MB Air Systems’ compressor and air receiver, both companies being part of Ingersoll Rand. The SAI system has proven to be robust and reliable overcoming the existing pumps’ performance issues, enabling the sludge to be processed for land disposal. In addition, SAI enables the discharge pipework to be emptied when idle, removing the risk of blockages, thus reducing downtime and maintenance costs. Commenting on this project, Veolia said: “We were very happy to work with SEEPEX to get this SAI system installed. It has given our site a solution to a difficult issue and resolved it. We use this system daily and it is beneficial to our day to day working environment.”
Combined Service and Support
SEEPEX and MB Air Systems have joined forces to deliver mission-critical, energy-efficient and market-leading technology for conveying applications. Our conveying systems are fully supported by a trained team of Field Service Engineers for service, installation and aftermarket support. Together we offer our customers our combined experience and technical expertise, providing one interaction point and one contract – for a streamlined project.
seepex.com
Logan Energy works on Anglian Water carbon project
In what is thought to be an industry first, hydrogen experts Logan Energy have been chosen to play a key role in a ground-breaking project designed to cut the carbon emissions associated with wastewater treatment processes.
East Lothian-based Logan Energy are supplying and installing an electrolyser at a wastewater treatment plant in Cambridgeshire as part of an initiative led by Anglian Water, geographically the largest water company in England and Wales. The project is being watched closely by water companies across the UK as it has significant potential to be scaled up. Anglian Water says that Logan Energy were chosen to take part due to their ability to install as well as supply the type of electrolyser that meets the projects’ requirements, and because of Logan’s reputation for delivering support for innovative energy projects. As part of the Ofwat Water Breakthrough Challenge, the Triple Carbon Reduction project, led by Anglian Water, aims to develop, and demonstrate a novel integrated solution. The plan is to investigate using treated wastewater through an electrolyser to create hydrogen and oxygen. The oxygen will then be used within a novel wastewater treatment process (Membrane Aerated Biofilm Reactor/MABR), targeting the reduction of nitrous oxide which is a source of greenhouse gas emissions. The hydrogen could be used for different uses, in fuel cells, to displace diesel generators, or for local transport application. Also, by investigating using treated wastewater, the project aims to tackle resource recovery, without additional demand for drinking water resources and without compromising the water resilience needed to face climate change. The project will run for the until June 24. Process emissions are a key priority for the water sector, as they are among the most difficult to tackle. It is hoped that by using an electrolyser to generate oxygen, wastewater treatment processes will see a reduction in energy consumption of up to 85% and a reduction in nitrous oxide process emissions.
And by using renewable energy at the treatment works, the hydrogen created by the electrolyser will be classed as green hydrogen, indicating it has not been made using fossil fuels. If successful, there are industry-wide implications as the solution could be rolled out more widely and at a larger scale. Other utilities partnering in the project and expected to share the learnings include Northern Ireland Water, Severn Trent, Scottish Water and United Utilities.
Bill Ireland, Chief Executive of Logan Energy, said: “Logan Energy is driven by the desire to help other businesses meet their net zero ambitions and provide intelligent energy solutions. So many of today’s carbon challenges can be met with innovative ideas involving hydrogen. “Unusually for electrolysis projects, this project will use both the oxygen and hydrogen produced, further increasing the efficiency of the overall process. We’re excited to be chosen to take part in this important project with Anglian Water, which has huge scale-up potential, and look forward to seeing the results.” Giulia Pizzagalli, Innovation Projects Manager at Anglian Water, said: “We are excited about this innovative project, which will greatly support the delivery of the water sector’s drive to Net Zero by 2030, by aiming to reduce nitrous oxide emissions, increase the energy efficiency of wastewater treatment processes and generate a new renewable energy source via electrolysis. “This is a valuable opportunity to collaborate with Logan Energy. Their extensive expertise in the hydrogen sector will help our project advance the water sector’s position within the developing hydrogen landscape.”

We are excited about this innovative project, which will greatly support the delivery of the water sector’s drive to Net Zero by 2030, by aiming to reduce nitrous oxide emissions, increase the energy efficiency of wastewater treatment processes and generate a new renewable energy source via electrolysis.
Giulia Pizzagalli, Innovation Projects Manager at Anglian Water
United Utilities begins £50m investment to improve River Bollin through innovative wastewater treatment process
A £50 million investment at Macclesfield Wastewater Treatment Works (WwTW) will use innovative technology to help improve water quality in the River Bollin.
The project, being undertaken by United Utilities at its site in Prestbury, will mean lower phosphorous and ammonia levels in the treated water that is released from the works back into the environment. The stricter targets, being introduced from the end of 2024, are driven by the Water Framework Directive (WFD). To meet these lower nutrient limits, innovative Nuvoda Mobile Organic Biofilm (MOB) technology is being introduced for the first time at a United Utilities wastewater treatment works. This biological approach uses a highly renewable plant material to digest the sludge produced in the treatment process. It has a number of benefits, helping to optimise the wastewater treatment process, increase capacity, and improve nutrient removal, as well as being friendlier for the environment. The investment at Macclesfield WwTW will also provide additional treatment capacity to meet the needs of a growing population and ensure monitoring of flows and stormwater discharges continues. Alison Byrne, Project Manager at United Utilities, said: “At United Utilities we don’t just supply high quality water and treat wastewater – we also want to make our region greener, healthier, and stronger. “Investing in our wastewater treatment works is a vital part of that goal, and the project at Macclesfield will ensure we can continue to treat wastewater to the highest standards and help protect our local waterways. “It’s a challenging project as we have to ensure the new processes are installed offline while continuing to run the existing treatment works, but it’ll all be done within the current site footprint and with minimal impact to local residents.” The water company recently showed Macclesfield MP David Rutley and representatives from Mottram St Andrews Fly Fishing Club around the wastewater treatment works and highlighted how the site’s facilities are going to be upgraded. During the visit United Utilities also explained how a broad range of sectors with expertise and influence are working together to help continue to improve the health of the wider River Bollin catchment area.
Asked about what he thought of the investment work, David Rutley MP said: “It is positive to see United Utilities making a significant £50 million investment to upgrade Macclesfield’s Wastewater Treatment Works. Using innovative new technology the project will help ensure that the water is treated to high standards and improve the water quality in the River Bollin. I welcome this important investment and will continue to work with United Utilities on this and other initiatives to help improve the environment in our area and beyond.” Earlier this year United Utilities published its ‘Better Rivers, Better North West’ programme, outlining a £230 million investment plan to improve 184km of the region’s rivers..

From left, Chris Borradaile from United Utilities, David Rutley MP, David Martin, Mottram St Andrews Fly Fishing Club, Mark Sewell and Chris Lee, both United Utilities
Using innovative new technology the project will help ensure that the water is treated to high standards and improve the water quality in the River Bollin. I welcome this important investment and will continue to work with United Utilities on this and other initiatives to help improve the environment in our area and beyond.
‘The Beast’ is introduced to Woodhouse Mill treatment works
Yorkshire Water has partnered with Saveco to add a new sludge screen to its Woodhouse Mill wastewater treatment works – an industry first in the UK.
Known affectionately as ‘The Beast’, the new screen enables tankers to connect and pump sludge into it, rather than offloading sludge to a holding tank that is then fed into traditional screens by gravity. The technology has been used successfully in the US and will be introduced to treatment process at Woodhouse Mill. ‘The Beast’ is fully automated and can quickly remove debris, plastics and other solids from sludge. Ed Sutherland, project sponsor at Yorkshire Water, said: “We’re always looking at innovative ways to improve the operations of our wastewater treatment works. The Beast has been tried and tested in the US and will deliver significant benefits to the operation of Woodhouse Mill. “Ultimately, it enables sludge to be pumped directly into the screen, rather than the traditional method of using an upstream storage tank that feeds sludge through screens via gravity. Removing the need for an upstream feed tank will result in significant capital savings, which ultimately leads to a reduction in costs and benefits for our customers.”
‘The Beast’ is equipped with an integrated perforated plate VSA Drum Screen which washes, conveys, and dewaters wastewater screenings, as well as a self-cleaning screen basket and self-cleaning dewatering zone to deliver maximum efficiency. Comprising a dual motor drive powered by independent drum and auger speeds, max flow rates of up to 200 m3/h, a drum screen 5 to 6mm perforation and incline angle of 25 degrees designed to increase solids capacity, the “Beast” can also be connected through a Perrot joint to tankers or pipes. Designed without a lower drum support arm, the Beast can be used to eliminate rag accumulation.
Rotating around its axis, the cylindrical filter conveys the screenings into a loading hopper placed in the centre. A set of spray nozzles washes the filter during operation. A screw placed inside the conveying pipe (with its top inside the discharge hopper), conveys the screenings towards the next treatment stage where organic substances are washed out. Subsequently, solids are compacted and dewatered in the compacting and drainage area and finally, solids are discharged through a discharge chute. The Beast will be trialled at Woodhouse Mill and, if successful, will be installed at other treatment works around the region. Saveco’s municipal wastewater sector Manager Craig Webb said: “Achieving unprecedented success in the US market, the Beast is a game changer for how we will treat sludge going forward in the UK. “We are delighted to have earned Yorkshire Water’s trust and confidence to remedy the complex challenge of sludge treatment.”

Ed Sutherland, project sponsor at Yorkshire Water