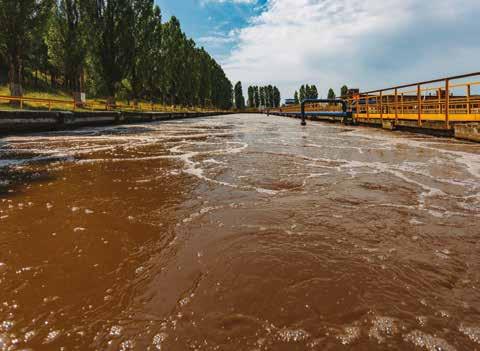
17 minute read
Phosphorus Removal
A natural step towards chemical-free phosphorus removal
Ben Hazard of Te-Tech Process Solutions discusses how primary sludge fermentation can improve biological P removal and reduce chemical usage, sludge production and operational costs.
Advertisement
With tightening phosphorus consents and population growth, AMP7 has seen an increase in phosphorus removal schemes across the industry and this number will grow even more in AMP8. The default solution for many smaller works is to install chemical dosing and tertiary treatment, as this appears superficially to be the simplest solution with the lowest capital cost. However, the main chemicals used for P precipitation (iron and aluminium salts) are not a sustainable resource and, with supply chain issues, demand is expected to exceed the supply in the not-too-distant future, affecting price, quality and reliability of supply. It’s time for another look at enhanced biological phosphorus removal technologies.
Primary sludge fermentation (PSF) has the potential to significantly enhance the phosphorus removal performance by enabling Enhanced Bio-P Removal (EBPR). By increasing the volume of volatile fatty acids (VFAs) available for phosphate accumulating organisms, biological phosphorus removal can occur where it was previously impossible due to insufficient VFA concentrations in the raw wastewater.
It’s Sustainable & Cost Effective
Alongside improved EBPR, PSF reduces the need for chemical precipitants and can potentially remove the need for chemical dosing altogether, bringing both cost savings and improving resilience and sustainability. Additionally, PSF reduces the volume of excess sludge produced, reducing sludge disposal and treatment costs.
All about VFAs
Whilst the biochemistry is complex, the principles are quite simple. In anaerobic conditions bacteria called “phosphate accumulating organisms” (PAOs) consume VFAs and release phosphorus as phosphate. Then in aerobic conditions they take up phosphate and convert into polyphosphate chains within their cellular structure. Given the right conditions and with sufficient VFAs available, the uptake of phosphorus in the aerobic stage is greater than the release of phosphorus in the anaerobic stage, so there is net reduction on phosphorus which is removed with the biological sludge in the final settling tank after the aerobic stage. Properly managed, this removal can exceed 80%. It’s mostly about getting the right amount of VFAs. PSF ensures that there is a sufficient quantity of VFAs, by fermenting some of the primary sludge anaerobically for several days, which increases the VFA concentration. After settlement, the VFA rich supernatant is returned to the anaerobic “selector tank”.
The Process of PSF
The process consists of three separate stages: 1. Primary sludge is directed to one of two alternating batch fermenters which operate out of phase with each other to give a pseudo-continuous flow through the system. 2. The fermented sludge is mixed with raw wastewater in an elutriation tank for enhanced washout of the VFAs and pH regulation. 3. Finally, the fermented primary sludge and wastewater mix is separated in a thickener with the VFA-rich supernatant being sent to the anaerobic tank of the biological treatment stage. To achieve optimal VFA production rates, the parameter that needs to be controlled is the sludge retention time in the PSF reactor tanks. This is quite an ambitious task as the VFA production rate depends on a number of different variables such as the reactor temperature, certain sludge specifics (e.g. origin of volatile suspended solids), and the presence of inhibitors. Online temperature, pH and ORP monitoring indicate where the process lies in terms of hydrolysis and subsequent fermentation. Based on this, the control system creates an optimal operational regime for sludge feeding and withdrawal, producing around 100 – 200 g VFA/kg COD. In conventional activated sludge plants, a significant portion of COD is removed from the main process line in the primary sludge. However, primary sludge fermentation returns about 30% of the COD removed to the main process line with the fermenter effluent, although it is typically readily degradable.
Packaged PSF Systems
Te-Tech Process Solutions have developed the te-fermTM packaged primary sludge fermentation system that can be easily retrofitted even into small plants. It uses conventional technology together with realtime control based on online monitoring of temperature, pH and oxidation reduction potential (ORP) to maximise the rate of VFA production. A complete process evaluation service for companies considering te-fermTM including a full evaluation of cost benefits and sustainability is available from Te-Tech. Contact Te-Tech now: enquiries@te-tech.co.uk
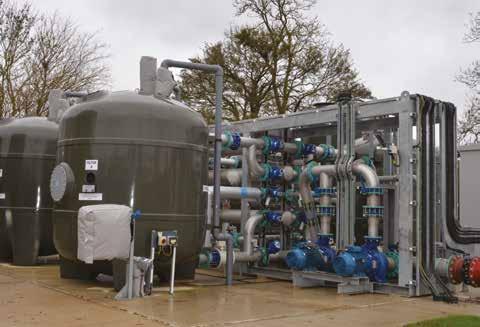

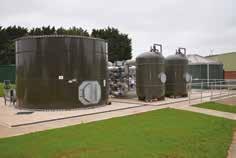
Proving your technology is only half the battle; how it stands up to long-term operational pressures is where you really stand out
During AMP6 and subsequent CIP2 P removal trials, the focus was on identifying those tertiary solids removal (TSR) technologies that could achieve the stringent Phosphorus consent requirements demanded in AMP 7 and beyond. FilterClear® was one such technology that proved capable of meeting even the most stringent consents across the UK.
But stopping there would be doing a disservice to our clients and the public who rely on the safe and reliable provision of water & treatment and discharge of wastewater. Both the trials and real-world experience has highlighted that the key to achieving consistently reliable results is upstream optimisation and TSR maintenance. The market now knows which technologies can meet the required consents; knowing those that not only satisfy them but continue to perform under challenging operating conditions and over a long period of time is critical. After all, a failure leading to a pollution incident is still a failure; past performance counts for nothing. A strong commitment to research & development has further enhanced the technology. Today, FilterClear provides the lowest whole life cost solution for the more challenging P removal applications across the UK. It’s now accepted industry wide that FilterClear can remove P to <0.1mg/l, but that’s only half the story. Being able to sustain long term performance with negligible operator input and maintenance is where the technology stands apart. One of the areas where FilterClear excels is the extremely efficient backwashing regime. This not only eliminates the need for routine out of service mechanical and chemical media cleans, but also provides the lowest daily consistent backwash volume generation versus other technologies. But even best laid plans can go awry. Sewage treatment works can have mechanical upsets, blanket spills and/or slime events which can cause some fouling and elevated backwash pressures within the system. In the rare event that remedial action is required to remove any unwanted biomass growth from the media, (3 cases in nearly five years operation of our plants), simply soaking the media with alkali quickly restores normal operation. Alkali pearls are added to the vessel via the top media inspection hatch and then agitated with the blower. After 1 – 2 hours, the alkali breakdown the biomass and restore the media to “as new” condition.
Taking this process a step further, an “alkali soak” function is incorporated into FilterClear’s PLC software. This procedure eliminates the need for labour intensive cleaning services – with associated H&S risks - with the operator simply activating the “alkali soak” function on the HMI and is prompted by the HMI through the various stages of the process. What could be simpler and safer. To learn more about FilterClear visit www.bluewaterbio.com/filterclear
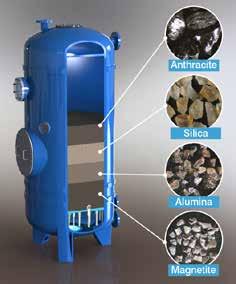
Balancing the risks of new and old Phosphorus removal technologies: is it really better the devil you know?
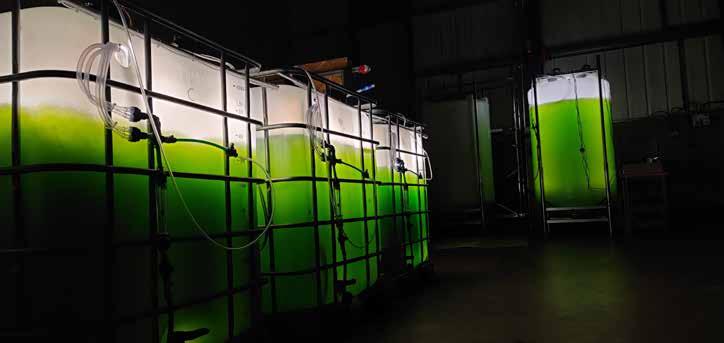
All sectors are working to become more sustainable and reduce the impact they have on the environment. For the water industry, though, all this change has to be undertaken while continuing to deliver proper operations, safe drinking water and controlled effluent discharge. It’s a delicate balance that would be an enormous challenge, if it weren’t for I-Phyc’s natural-based approach to removing P from wastewater. But there still may be some perceived risks to adopting this technology, Matt Baldry, Director at I-Phyc, explains…
If you were going out to buy a car today, you’d need a good excuse to tell your friends and family if you chose a diesel or petrol vehicle when clearly electric is the right choice for our planet and future generations. But, internally, your decision would no doubt be influenced by your fears and the risks, be they real or imagined. You might be asking yourself, will the range be adequate, what if I can’t find charging points, etc. It’s understandable and a natural part of the process in the widescale adoption of new technologies. To all but the early adopters, it’s a new technology, so the risks, nuances and considerations are unknown.
As they say, it’s better the devil you know. But, to that point, there are dangers and risks around petrol and diesel engines. We tend to discount the myriad problems relating to breakdowns, maintenance expenses, air quality, GHG emissions, and so on, when we consider petrol and diesel engines because they are expected, and we’ve learned to live with them.
Compare that to the water industry, which is under growing public and political pressure regarding sewage and CSO discharges and the general state of rivers in the UK. People from all walks of life are demanding change; School strikes, Clean Rivers Campaign, Surfers Against Sewage are all gaining media attention. CSOs are a contributing factor of this negative press, even if the logic is flawed, and chemical dosing isn’t helping. The process has never been risk or consequence free but, in the past, chemical dosing was the answer to the question. Even though chemical dosing still pollutes the effluent with iron, there were no other options. It is also a carbon emitter; Net Zero cannot be achieved with chemical dosing. There’s also the cost and supply of the chemicals themselves, which are increasingly unstable. There’s the cost of maintaining the infrastructure, of employing and training skilled staff, health and safety, and sludge removal.
However, now things are different. The replacement technology, is Bio-P removal – harnessing the natural power of microalgae to remove P from wastewater as well as ammonia and other contaminants all in a single process. The by-product of this process is not sludge, but excess algae, which can be reused. The contaminants it removes from wastewater can be harvested and sold on. The technology is modular and does not rely on flow rates, so is suitable for even the smallest plants in the country. The investment case, however, is complicated. The two systems are not at all like-for-like. Ferric dosing costs include the chemicals themselves, the process including sludge removal and disposal, training, maintenance and cautionary infrastructure like showers in case of a spill. But on top of this is the environmental cost, the carbon cost and the risk of keeping chemicals so near water courses.
With Bio-P removal, the main cost is upfront - the tank and flow system. There are also soft costs like the space they take up, and they do need to be on hard ground so that might be an investment if a particular plant doesn’t have such a space. The microalgae are self-sustaining, so the only ongoing costs are the modest energy expenditure on the LED lights used to help the microalgae grow, and another energy cost for separating the microalgae from the effluent.
All of these costs are offset by the environmental benefits. There is no iron discharge, it’s a completely chemical and sludge-free process meaning less processing and lorries on the road. All the P it removes and biomass it generates can be sold on. Microalgae also photosynthesises, so it removes carbon dioxide from the atmosphere. I-Phyc’s Bio-P removal system can lock away 17 tonnes of CO2 per year at 1,000 population equivalent works. Like electric vehicles, in the long-term, it’s a no-brainer.
To find out more about I-Phyc’s Bio-P removal system, visit, www.i-phyc.com.
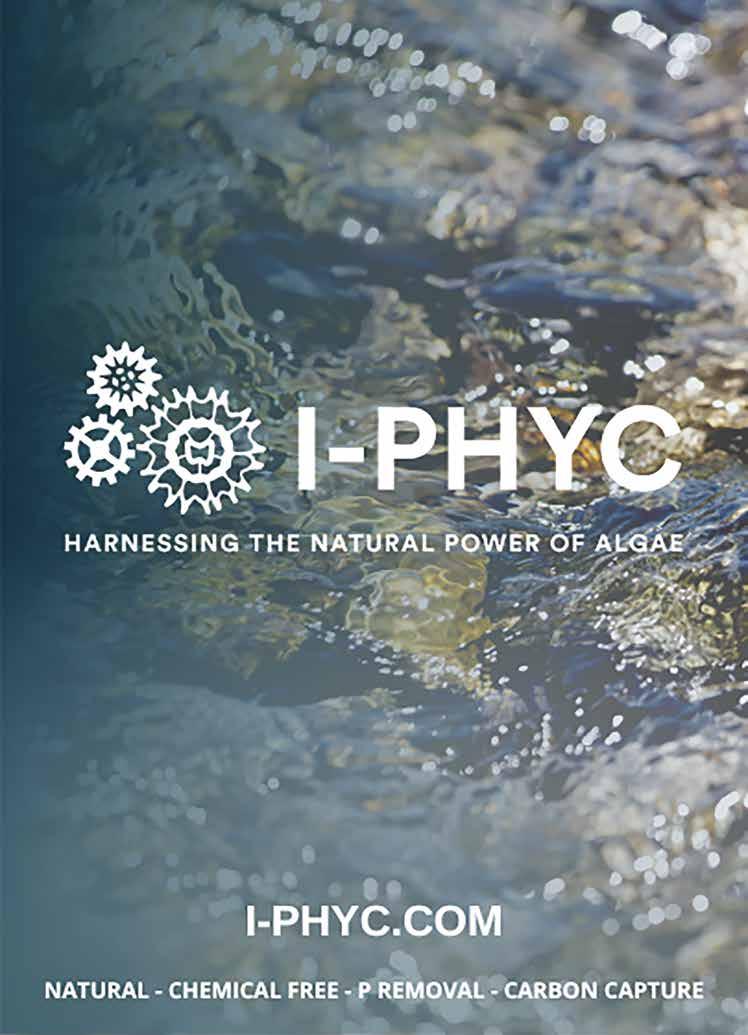
Wastewater treatment is not just a piece of cake
Remo Schulz, CEO of Saxlund Group, discusses German-led changes in European legislation for phosphorous recovery, and how innovation is supporting sustainability goals in wastewater recovery.
It makes sense to put the status of the industry in context. Specifically in Europe there is continuing debate on the appropriate handling of sludge as the defined solid waste produce from wastewater and sewage treatment.
Safer methods
The late 20th-century drive to clean final effluent discharge into rivers and seas means that sludge cake must now be safely utilised and disposed of. Putting raw or lime treated sludge cake directly onto agricultural land does not have a long-term future, while land filling is costly and a lost opportunity. Methods to safely utilise sludge cake are major drivers for wastewater companies. Dewatered sludge cake is generally 18 – 35% dry solids, and a nonfree flowing material that can be variable in its mechanical handling properties due to process, location and / or season.
Pollution control at source is crucial
The wastewater sector is under pressure due to the presence of degradable and nondegradable pollutants entering our sewers and from the increased flow to sewers caused by climate change and urban development. The sector is being asked to deliver clean water by removing these pollutants from wastewater; however, this process generates an increasing amount of urban wastewater treatment sludge (UWWTS) and treatment efforts, as well as carbon emissions and higher costs to customers. Improved control of pollution at source is urgently needed for all non-biodegradable pollutants if we are to truly embrace the circular economy. The new EU Zero Pollution Action Plan is based on a ‘zero pollution hierarchy’. This is outlined by research from organisations such as EurEau (the European Federation of National Associations of Water Services), representing national drinking and wastewater service providers from 29 countries. The Position Papers are of particular note: ‘Enabling the circular potential of sewage sludge within the EU legislative framework’ and further analysis in ‘Waste water treatment – sludge management’. Innovative business models such as asset management and sludge retail followed by disruptive applications like hydrogen fuel from sludge will drive the circular economy of the European sludge treatment systems market. It may be an established market in this respect, but many of its utilities suffer from ageing infrastructure where retrofits and rehabilitation will be key, along with technologies addressing micropollutants in sludge. The European Commission has approved fertiliser generated sludge, a key driver to minimise waste, lower energy consumption and reduce the risk of phosphorus shortage. The market is broadly classified into two systems: sludge treatment and sludge recovery. The former include sludge thickening & dewatering, sludge digestion and sludge drying. The latter consist of nutrient recovery and alternate materials. The sludge treatment systems and recovery market are expected to expand at a CAGR of 6.51% from 2019 to 2025.

Processing methods
There are currently three main methods of utilisation / disposal: ADD sludge Widely seen in the UK and across Europe, this method generates additional anaerobic activity, boosting energy recovery in Anaerobic Digestion AD plants. There are currently two main technologies:
Thermal hydrolysis, where sludge is heated to a high temperature under pressure, and subjected to rapid decompression causing the solids fraction of the sludge to disintegrate.
Enzymic hydrolysis, where the sludge is broken down into small components which are acidified, before the material is transferred into the anaerobic digestion plant. EfW sludge Sludge cake is used widely in EfW plants and cement plants to dispose of material, and when having a high dry solids content, gain beneficial energy. It can be combusted when mixed with other waste fuels or monocombusted on its own. Drying sludge cake using waste heat turns it into a valuable fuel. Sludge for Phosphate Recovery Recent European legislation, most notably in Germany, means that Phosphate recovery is
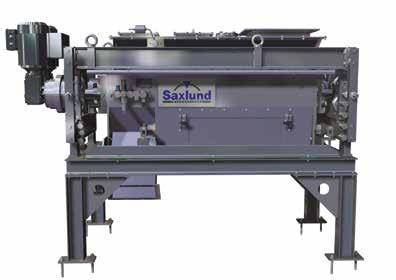

a driver for change, with a move away from co-combustion to the building of new monocombustion plants.
Germany - leading the way?
Since the German Sewage Sludge Regulation was introduced in 2017, sewage sludge must be recycled to recover phosphorus. The aim is to gradually close the phosphorus cycle and reduce Germany’s dependence on phosphorus imports, saving resources and reducing soil contamination.
Phosphorus is primarily used as fertiliser. Germany - as with most other EU states – depends almost entirely on imports of mineral-based phosphorus fertilisers. If the new regulations are complied with, 50% to 60% of imports can be replaced by phosphorus recovered from sewage sludge. To achieve that aim, operators of larger sewage plants (population equivalent of > 50,000) are required to recover phosphorus from sewage sludge. Transition periods are allowed to help develop and optimise recovery processes. Large sewage plants (population equivalent of > 100,000) have 12 years to comply with the new regulation. Transition for smaller sewage plants (population equivalent of 50,000 to 100,000) is 15 years. However, sewage plant operators of the above sizes must submit their phosphate recycling concept to the regulatory authorities by the end of 2023. The war in Ukraine has left the world short of fertilisers, and prices are skyrocketing. Previously Russia and Belarus provided about 40% of the world’s exports of potash, according to Morgan Stanley, but sanctions have sent prices increasing at an exponential rate.
Rationale for German approach
Scientists from Cardiff University estimate that between 31,000 and 42,000 tonnes of microplastics (or 86 – 710 trillion microplastic particles) are applied to European soils annually, mirroring the concentration of microplastics found in ocean surface waters. Their study estimates that microplastics removed from raw sewage at wastewater treatment plants make up roughly 1% of the weight of sewage sludge, commonly used as farm fertiliser. The UK has potentially the highest amount of microplastic contamination in its soils, with 500 – 1000 microplastic particles per sq m of agricultural land applied per year, followed by Spain, Portugal and Germany. The study took samples from the Nash Wastewater Treatment Plant in Newport, which treats combined sewage from 300,000 people. Analysis revealed that the treatment plant was 100% effective in removing large microplastic particles, 1 – 5mm in size, from incoming sewage that would otherwise be released into the aquatic environment. Each gram of sewage sludge was shown to contain up to 24 microplastic particles, roughly 1% of its weight. This data was used to assess the impact of the use and application of sewage sludge as a fertiliser across Europe. Microplastics less than 1mm in size weren’t analysed, so the overall concentrations are likely to be a lot higher than their estimates. The German approach of incineration eradicates microplastics as they are combusted in the process, allowing the resulting ash to be used for phosphorous recovery.
Phosphorus Recovery from sewage sludge
Currently phosphorus recovery from sludge cake ash is only practical from monoincineration plants where just sludge cake is combusted. Sludge cake is used widely in a supplementary fuel in Energy from Waste plants but contamination from other materials in the ash means recovery is not possible. Existing capacity in mono-incineration plants is about 450,000 mg dry solids/a, equivalent to roughly 25% of the total dry sewage sludge mass produced, thus new plants are needed. An additional plant is required to extract phosphates from the ash. The new German Sewage Sludge Regulation requires a recovery rate of 80% in relation to input, so commercial plants are coming into operation (phos4green. glatt.com/projects/seraplant-haldensleben/)
Sludge satellites and processing hubs
The drive for innovation means projects are delivered as Satellite and Hubs. Smaller water treatment works will install sludge dewatering systems and Truck Loading storage silos, with 3 – 5 days of storage on each site. A larger water treatment works, with its own large indigenous sludge, will install a Sludge Cake Reception and Storage system that feeds the AAD or EfW process.
Future proofing
Germany has around 10,200 wastewater treatment plants which use approximately 4,400 gigawatt hours (GWh) of electricity per year (35 kWh/population equivalent per year), and account for around 0.7% of the power consumed in the country. aerzen.com/applications/water-and-wastewater-treatment/adviser/water-treatmentin-the-future.html. Aeration is by far the main consumer for almost all the wastewater treatment plants with sludge processes; while power consumed by plants with aerobic sludge stabilisation is between 60% and 80%, it is still around 50% for plants with sludge digestion. Renewable energy sources to power efficiency include hydroelectric power in the inlets and outlets, depending on available fall height. Particularly in the case of larger plants with sludge incineration, it is recommended to use bar screen debris as an additional fuel source. However, this technology is limited using bar screen debris washers, which reduce the accumulation of debris and also possible ash contamination.
Needless to say, a spectrum of new and emerging solutions is being tested, but they must be both safe to operate and offer a valuable return on investment.