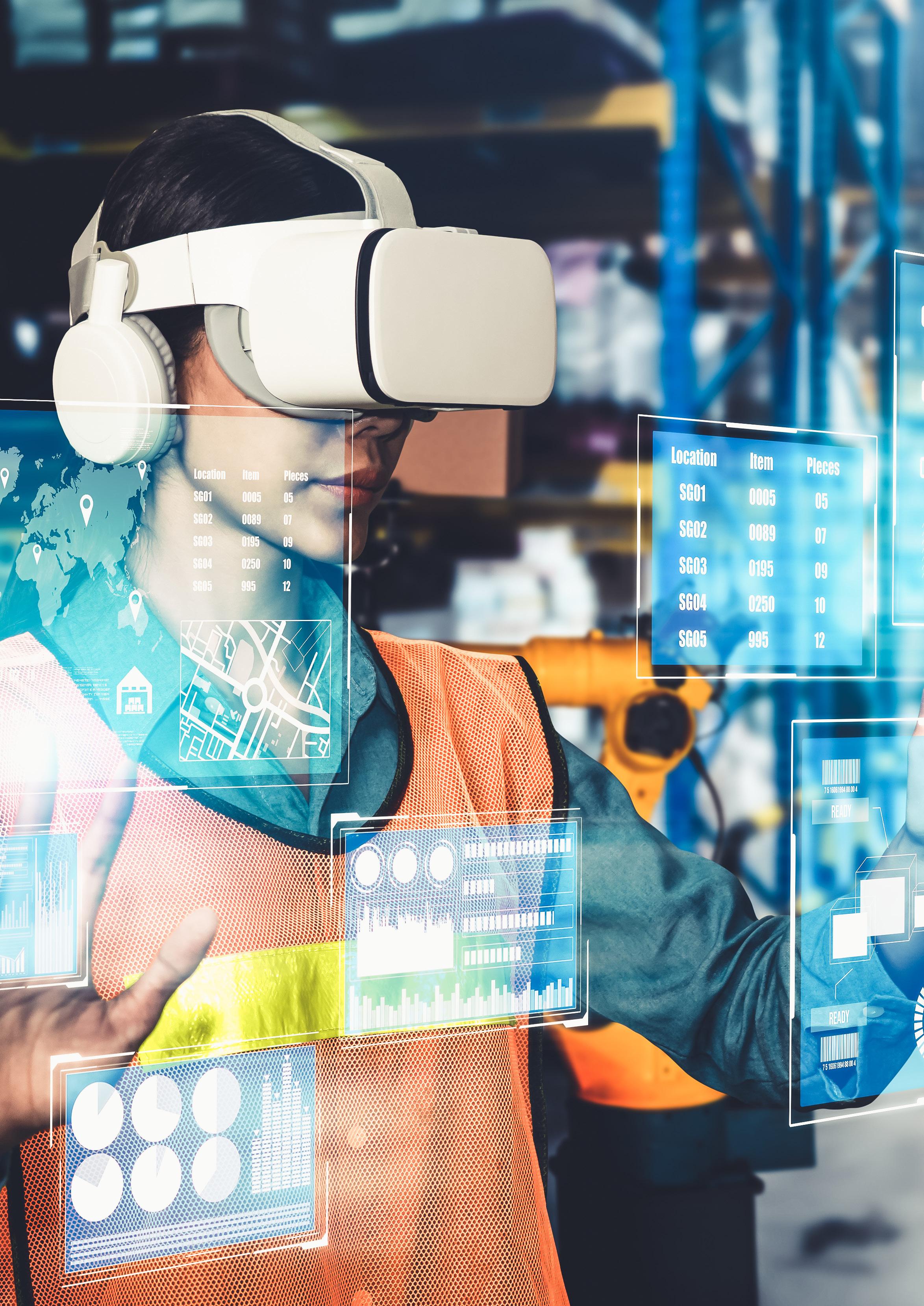
4 minute read
The role of AI and AR in transforming logistics
What role can AI and AR play in the future?
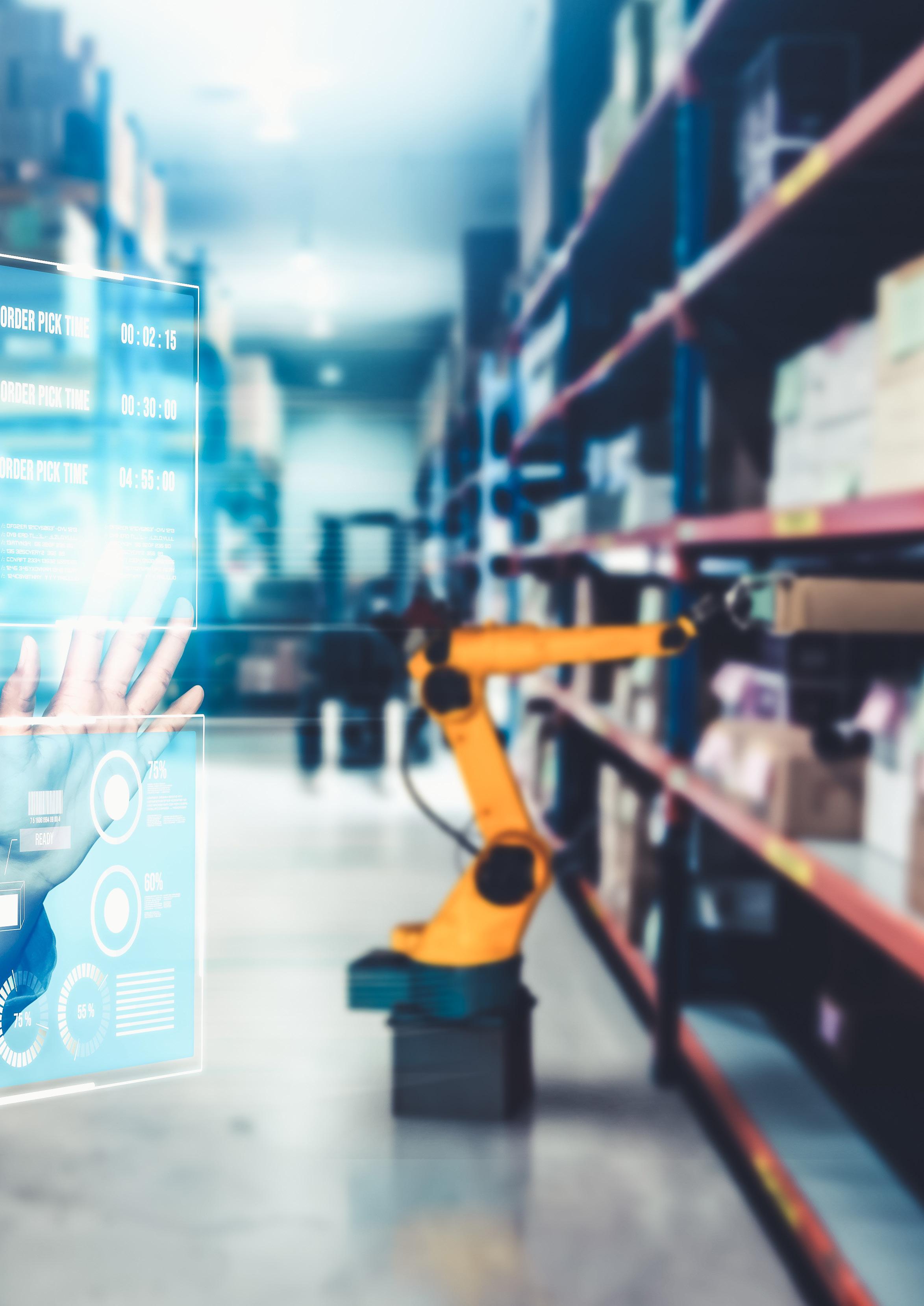
Industry 4.0 technology and its rapid adoption during the pandemic has assisted many businesses in navigating labour and productivity challenges by streamlining factory and process workflows.
ugmented reality (AR), artificial intelligence (AI), robotics and IoT continue to make their way into supply chain operations and logistics, driving new levels of efficiencies with increased cost avoidance.
Warehouse workflow optimisation is a critical component to the success of any logistics-related business. Businesses save millions of dollars by organising their business processes and workflows effectively. Typically, logistical issues arise because of the human tendency to make mistakes. In this case, technology and its integration with existing systems comes first in problem-solving. Many businesses are exploring or have opted for augmented reality warehouse handling software to improve a variety of business processes. Using AR for warehouse management activities such as warehouse planning, inventory control management, order picking and material handling can simplify and improve complex warehouse operations, thereby strengthening supply chain processes.

Automation is critical for companies seeking to
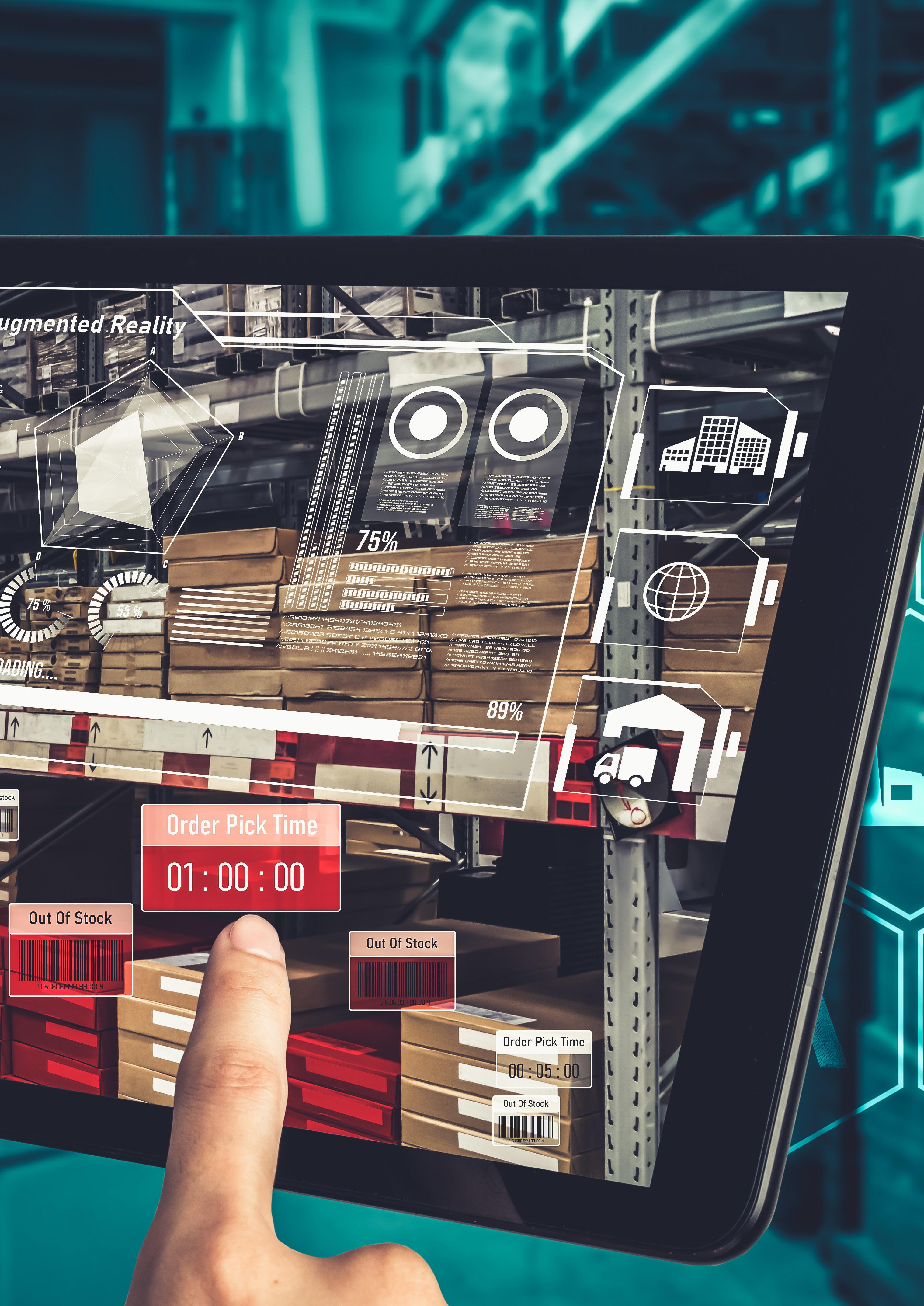
improve warehouse operations. The use of AR in a warehouse is a great way to improve agility, incentivize employees and save money.
Let’s take the example of one of the most cost intensive tasks in warehousing – order picking. This process focuses on getting the right product as requested by customers at the right time and in the right quantities with no damage to the product. Customers expect all products and services to be delivered quickly in today’s technologically advanced world.
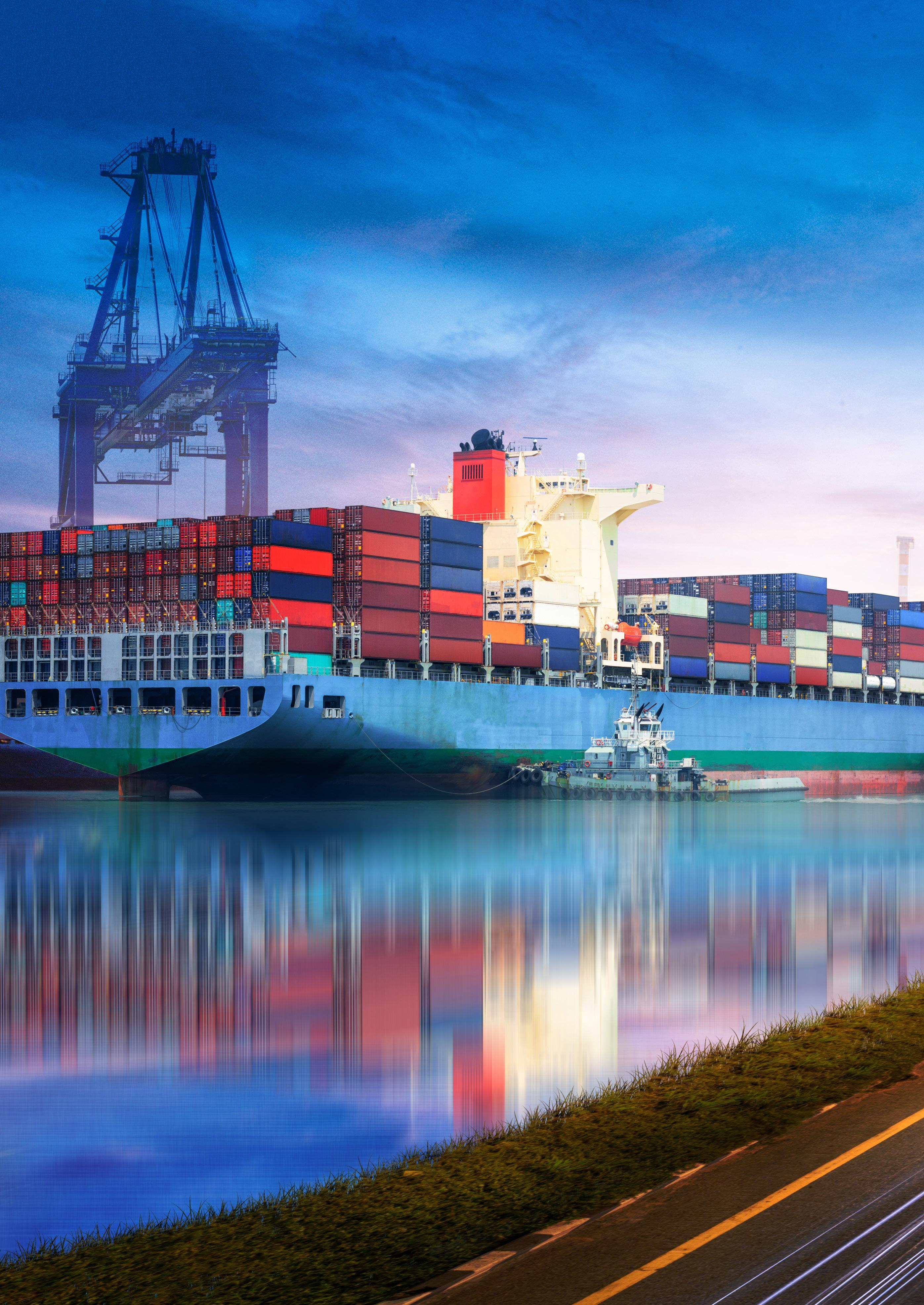
As a result, logistics companies are under constant pressure to streamline the order-picking process at the lowest possible cost to protect their revenue generation. The traditional approach to order picking is a time-consuming and painful process where associates navigate around the warehouse to
locate items that meet the needs of the customer. This manual method is extremely error-prone and very cumbersome.
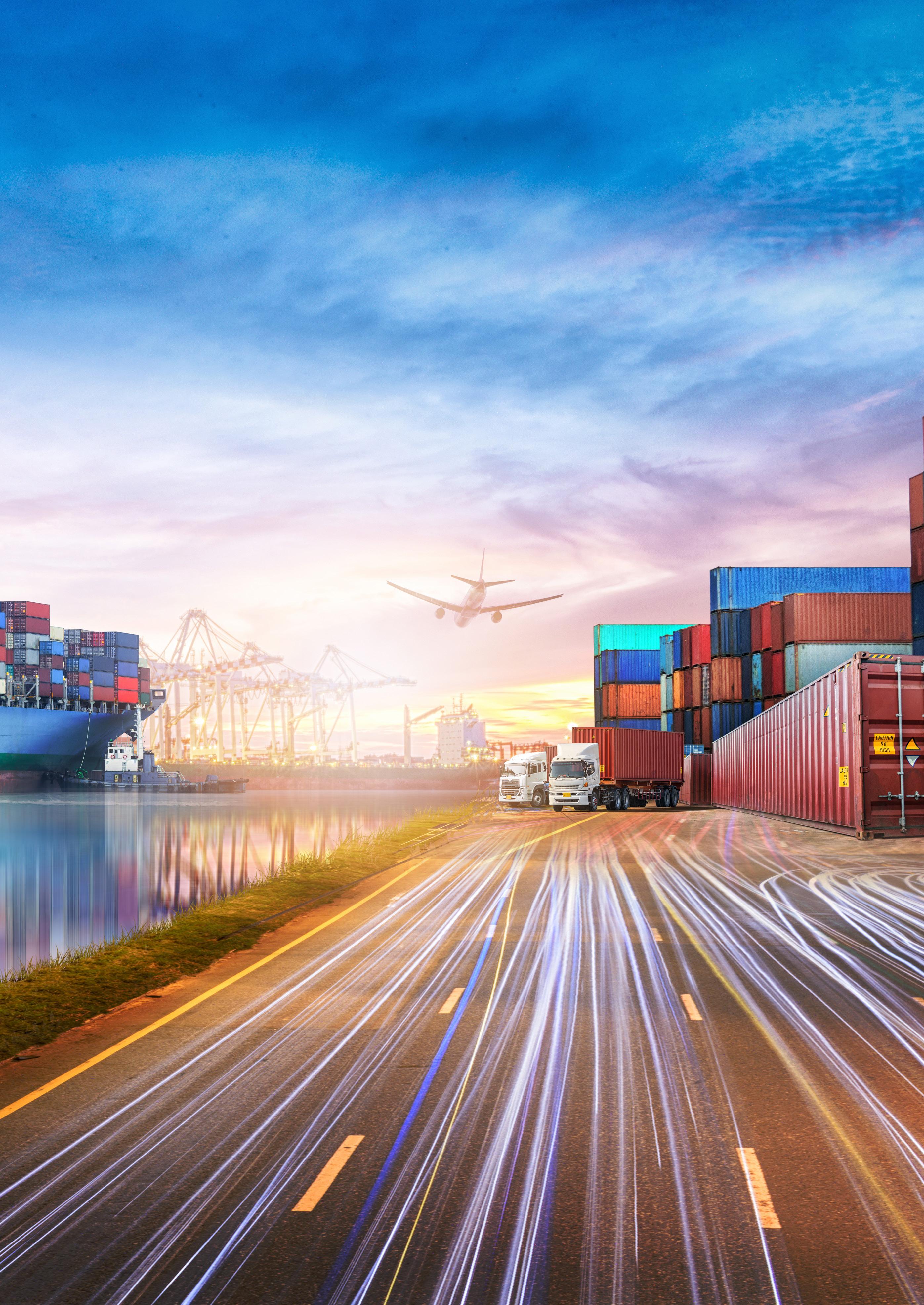
AR can help to streamline the overall order-picking process. When an operator is notified of a scheduled pick-up, an associate will enter a facility wearing an AR-based smart glass. The smart glass detects the barcodes of objects in the cart as the associate moves their head.
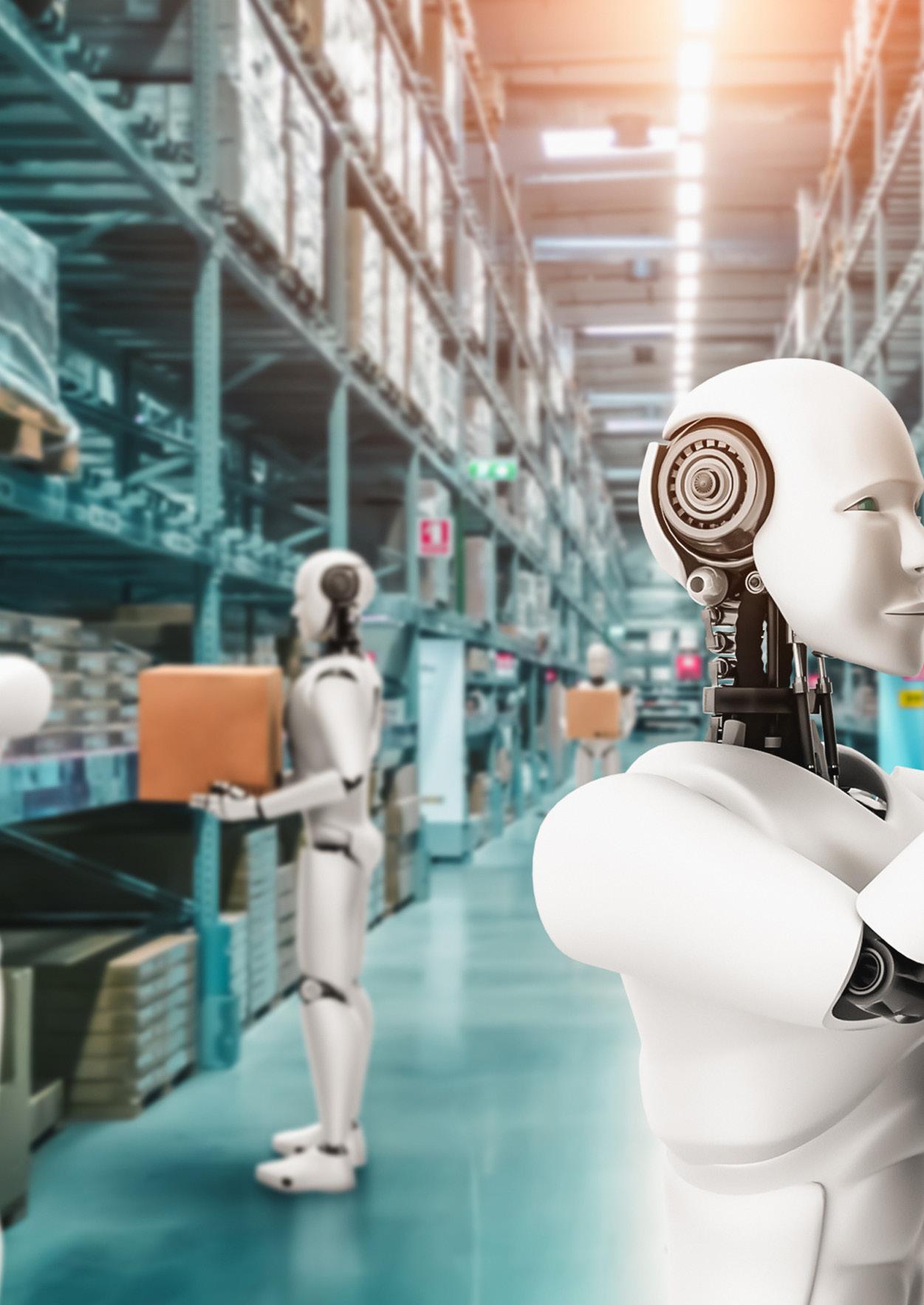
The operator is guided through machine learning-enabled algorithms aiding the operator visually and verbally. When the pick is finished, the information is saved in the system for future use.
This integration of business processes, workflows, warehouse management systems, AR equipment and AI optimises the user’s path through the warehouse. It replaces visual searching and manual text comparison with barcode scanning and automated visual cues. The form factor of AR hardware allows pickers to use both hands throughout the process. It also simplifies the information needed by the operator at each process step.

AR and robotics, when integrated well, solve ongoing critical challenges in logistics. In warehouse management, it is critical to consider items such as
efficient space usage, warehouse restructuring for unforeseen crises, and secure storage of high-selling or seasonal commodities in the plan. Bottom-up integration models requiring business processes and workflows to be standardised and streamlined enable system, equipment and AI to work in synch.
AR may be a huge benefit to warehouse managers and employees when it comes to overall warehouse layout design. It gives the option to experiment with modifications to the existing warehouse design due to its ability to generate digital, interactive 3D warehouse layouts. Warehouse managers and employees can determine if the plan properly matches the warehouse layout by conducting multiple trials and experiments with various work models.
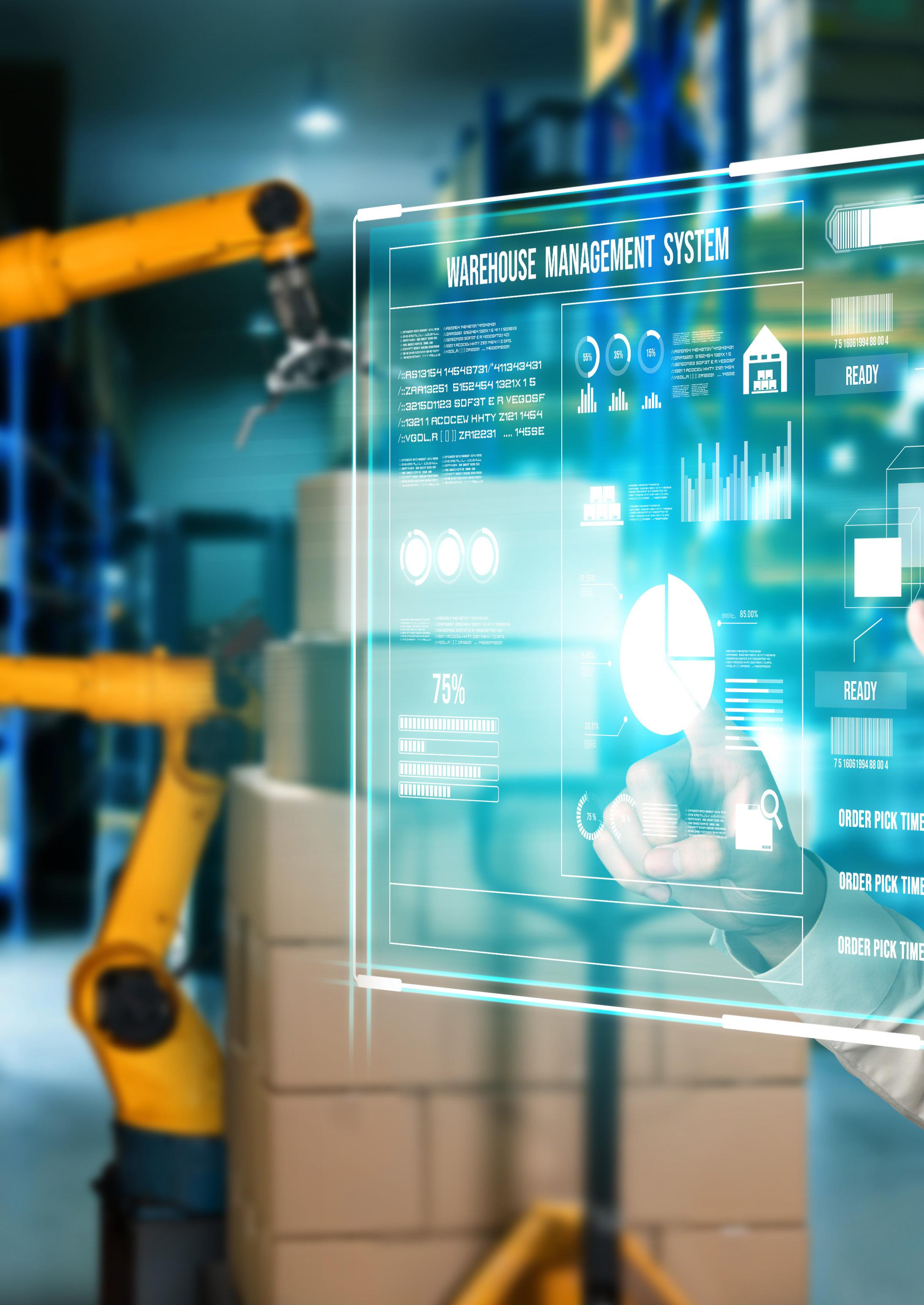
Inventory management is one of the most important and difficult
components of warehouse operations. Human involvement increases the likelihood of mistakes and erroneous put away/picks. As a result, we cannot assume that the task is always repeatable without fail. Some significant logistics organisations have used barcode scanning systems for inventory monitoring and management after realising the necessity to expedite this process. The process of inventory inspection and control has undergone a fresh wave of innovation with the introduction of barcode scanners.
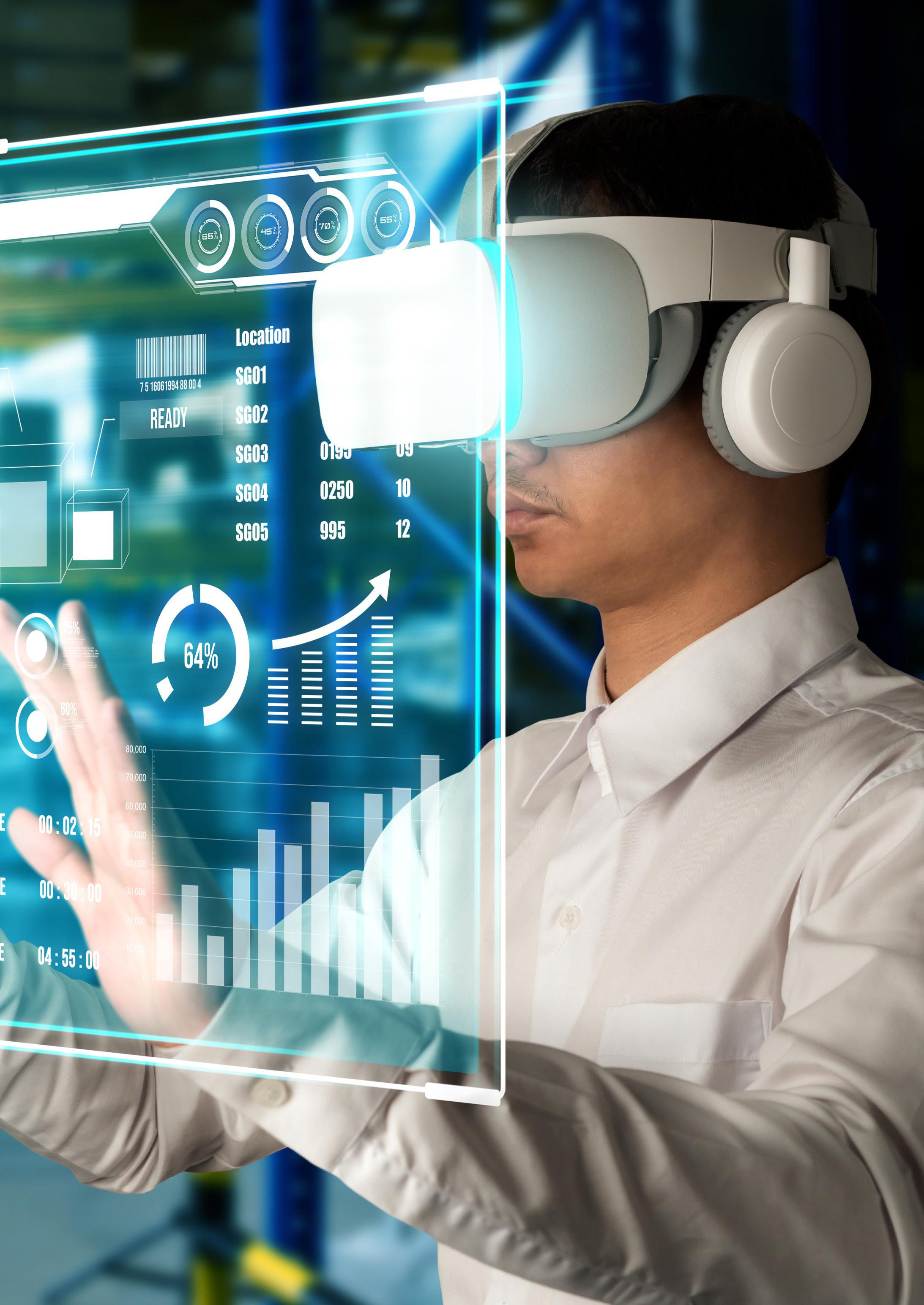
Furthermore, we can also use AR to provide virtual training to new staff, ensuring a stimulating environment for quick onboarding and effective collaboration with experienced personnel. This interactive style of education engages employees in their job and allows them to practise at their own leisure.