
10 minute read
White reflective roof coatings: Improving the sustainability of existing roofs
sized on/off boiler will short cycle for over 90 per cent of the heating season. If we are over sizing above the maximum input needed, we are making the problem even worse.
Number two: match the heat output to the actual load by staging or modulating the input to the boiler plant. A 5:1 turn-down ratio will reduce short cycling to only 14 per cent of the heating season. There are more and more boilers on the market today that can reach down to a 20 per cent (5:1) firing rate, and even lower, and in larger schools, the staging of multiple boilers has the same effect as modulating a single boiler. See how powerful the P.10 chart is in illustrating some of these principles. The variation illustrated below is a perfect example of how we can utilize this tool.
Number three – Use outdoor reset to lower water temperatures as low as possible, whenever possible. This is a “nobrainer” and should be required of any boiler. Some movement in this country is afoot to legislate mandatory outdoor reset control for all boilers; however, there is significant push-back from some stakeholders who have yet to embrace the concept of low temperature hydronic boilers, and therefore who do not have products that can easily comply. Reducing water temperature based on warmer outdoor temperatures works for just about any heating application you can imagine. Many doubters deny this strategy can work with baseboard radiators or fan coils, but they are just plain wrong. The chart below is from one of the biggest baseboard manufacturers in North America, and every manufacturer has similar specifications.
Based on these types of charts, a general rule for estimating is that a 10 degree Fahrenheit reduction in water temperature reduces heat output by 11 per cent, which just about perfectly tracks the reduction in heat loss from a space as the outdoor temperature warms up from design conditions. So you doubters out there have a hard look at the information presented here – this is not blue sky and wishful thinking, it is based on science and sound engineering principles, as well as many years of experience.
Outdoor reset is a proven strategy that saves energy big time for a very minor outlay – many boilers today, especially low temperature and condensing boilers, simply throw it in to their onboard control for free.
And lastly, number four: use condensing boilers to maximize the benefit from outdoor reset and to squeeze the last bit of energy from the flue gasses. We used to throw hot flue gasses up the chimney (500°F at the flue collar of an atmospheric boiler is not uncommon), along with a whole bunch of dilution air and water vapour. Now we can cool flue gasses down to as low as the boiler’s return water temperature and condense the water vapour right in the boiler, recovering the latent heat from the condensate – there’s nothing left to recover – we can get it all.

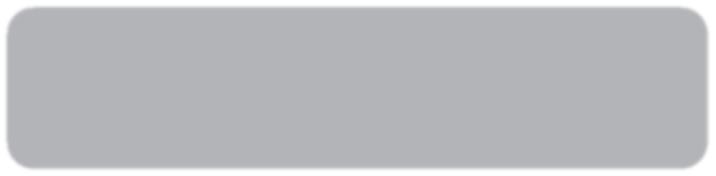
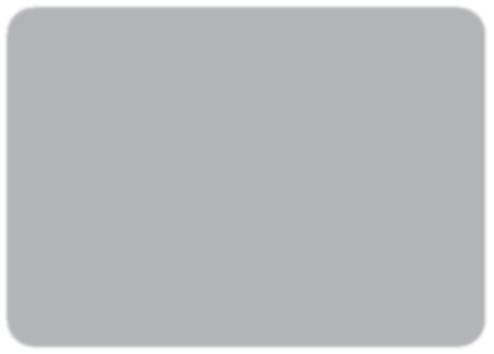
For further information, please visit the IBC Technologies website at http://www.ibcboiler.com/ or call (604) 877-0277.
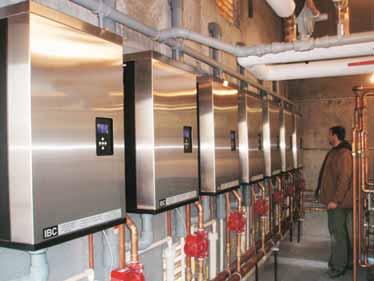
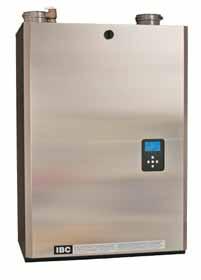
BY JASON SMITH

For more than a decade, buzzwords such as “cool roof” and “sustainable roofing” have dominated nearly every publication dealing with industrial roofing. However, it is sometimes mistakenly assumed that cool or sustainable roofing applies exclusively to new construction. What does it mean to have a sustainable roof? A sustainable roof is one that is “designed, constructed, maintained, and rehabilitated with an emphasis throughout its life cycle on using natural resources efficiently and preserving the global environment.”1
There are several ways to convert an existing commercial roof into a sustainable one. They include: the application of a reflective white (cool roof) coating; the addition of photovoltaic panels; and the application of metal or vegetative roofs. This article will focus on the rehabilitation aspect of sustainability; specifically, on the effects and benefits of the applying reflective coatings on the performance and life-cycle costing of the roof.
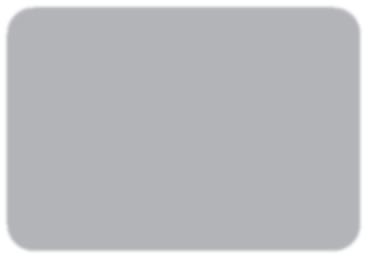
Extending the Expected Useful Life
The average expected useful life (EUL) of various roof systems is shown in the chart below.
As a roof comes to the end of its theoretical useful life, a roofing professional can determine if a roof is a candidate for en hanced sustainability through the use of a reflective coating. The typical approach for this determination would include an infrared scan to search for leaks or wet insulation. All identified wet areas must be cut out and replaced. In all cases, flashings surrounding scuppers, drains, penetrations and HVAC units need to be sealed, re-flashed, and replaced if damaged. All ridging, blisters, splits and fishmouths must be repaired. Any ponding areas must have either new drains or crickets installed (crickets are tapered triangles that help direct the flow of water to a drain). Once these issues are addressed, the roof can be coated.
The application of a reflective coating is one of the simplest ways a roof can become sustainable. Many of the roof coatings on the market can be applied with a regular paint roller. Multiple component reflective coatings (e.g., two-component polyurethanes and polyureas) require a metered dispenser system and a higher degree of operational sophistication. Reflec tive coatings come in a variety of chemistries, including acrylic, polyurethane, urea, silicone and polyurethane-urea hybrids. In addition, new advances in soy-based technology have allowed formulators to incorporate “greener” bio-based raw materials into their sustainable coatings.
Applying a reflective coating to a roof will add between five and ten years to the life of a properly designed roof. By implementing routine preventive maintenance (e.g., regular evaluations, cleaning drains, thermal scans to check for leaks, etc.), the working life of the roof can be extended even further. By extending the working life of the roof, the owner also realizes a significant cost saving. For example, a modified bitumen roof consisting of two-plies and a mineral cap sheet, with an esti-
ROOFING SYSTEM
Built Up (three- or four-ply) Modified Bitumen (two-ply)
Single Ply (TPO, Heat Weld PVC) Single Ply (EPDM, adhered) Metal (standing seam) SURFACE TYPE
Gravel
Granules
Unsurfaced/Eposed Membrane Unsurfaced/Eposed Membrane Fluoropolymer Paint
Source: “Roof Management Program for Multiple Roof Systems”, Interface, Nov. 2008. EUL (min. ¼ in/ft) 25-30 years 20-25 years 15-20 years 10-15 years 40 years
mated useful life of about 20 years, when painted with a reflective coating around year 20, can reduce the overall life-cycle cost of the roof by about 15 per cent.

Energy Savings
A good quality, reflective roof coating system will also save energy costs for the building owner. More than a third of the total energy in Canada is used to cool, heat and operate buildings. When compared to dark roofs, roofs with restorative white reflective coatings require up to 40 per cent less energy to cool the interior, reducing peak cooling demands by up to 15 per cent.
Online calculators, such as www.roofcalc.com, provide userfriendly calculating tools to determine approximate energy savings. The decrease in cost is directly related to the reflectivity and emissivity of the coating chosen, as shown in the chart below.
The temperature differential (the difference between the roof temperature and the air temperature) is indirectly proportional to the solar reflectance. Therefore, the more a coating reflects sunlight, the lower the temperature observed on the roof surface. The chart shows that coatings using titanium dioxide (white) come closest to optical whiteness (100 percent reflectance); titanium dioxide is therefore the best solar reflector available to formulators. Reflectivity is the primary criteria for obtaining roof coating Energy Star® qualification2, which uses the following reflectance guidelines: For roofs with slopes of 2:12 or less: For roofs with slopes greater than 2:12.
Coatings that continue to show high reflectance beyond the three-year mark translate to continued energy savings for the building owner. Emissivity, a measure of the ability of the coating to release absorbed heat, is not a requirement for Energy Star; however, emissivity values have been listed with re flec tance values of coatings since 2007.
Currently, 220 manufacturers have joined the Energy Star program.3 It should be noted that the simple addition of a reflective white coating can also add to the value of a roof by contributing valuable LEED® points4 .
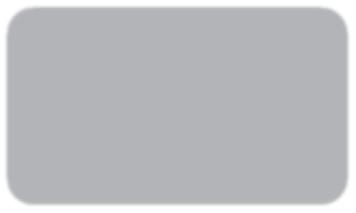
LEEDPoints
In 2003, building industry leaders formed the Canada Green Building Council (CaGBC). The council adopted LEED Canada, which is similar to the U.S. version of LEED, which was started in 1996. The mission of LEED is to reduce the heat island effect, the phenomena whereby heat is absorbed and reradiated by clusters of buildings in densely built areas. LEED provides a point rating system establishing maintenance standards not only for new construction, but also for building rehabilitation.
In roof rehabilitation, coatings that are used to improve reflectance and provide an additional water barrier can also help a facility earn valuable LEED points. Points (or credits) are earned based on a set of prerequisites in these six major
Initial Solar Reflectance Reflectance After Three Years ≥0.65 ≥0.50
Initial Solar Reflectance Reflectance After Three Years ≥0.25 ≥0.15
categories:
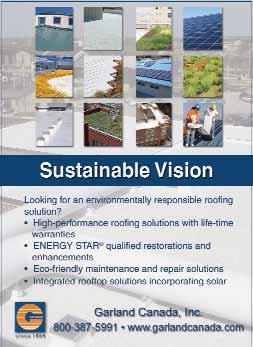
• Sustainable sites – 14 possible points • Energy and atmosphere – 5 possible points • Water efficiency – 17 possible points • Materials and resources – 13 possible points • Indoor environmental quality – 15 possible points • Innovation and design process – 5 possible points
The points required to obtain different LEED certifications range from 26 to 32 points (for the most basic certification) to 52 to 69 points (for the highest Platinum certification). Regardless of whether a roof coating is used as part of a restoration or new construction plan, LEED points are typically applied in the materials and resources category. Your local architect, roofing consultant, or manufacturer’s representative can typically help you analyze and compare the LEED contribution potential of various roofing solutions.
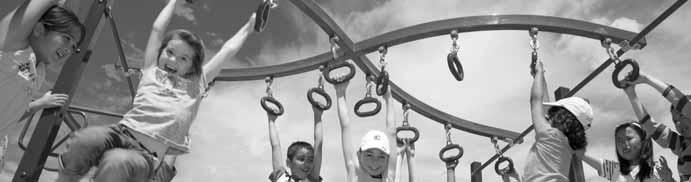
Time to stock up.
Get speedy delivery of all your playground parts from Blue Imp • heavy-duty, vandal-resistant parts & components • backed by the best warranty in the industry
Heavy-Duty Slash-Proof Swing Seat SP-526
Hammerlocks (Blue Imp’s standard) 89mm (3-1/2”) beam SP-14 60mm (2-3/8”) beam SP-15
Heavy-Duty Galvanized Steel Safety Chain SP-529
Wrap-Free Swing Bearing Hanger SP-16

To order parts, call us toll-free at 1-800-661-1462 Recreational Products of Canada Ltd.
Order today! 1-800-661-1462
Conclusion
With all of the buzz in the roofing in dustry regarding sustainability, using a reflective coating may be the simplest way for a building owner to reduce energy consumption while extending the working life of their roof. When used in conjunction with a responsible, ecofriendly restoration or rehabilitation plan, the use of a reflective coating can contribute to LEED certification, transforming an existing roof into a sustainable one.
About the Author: Jason Smith is a research and development chemist for The Garland Company, Inc., a manufacturer of high-performance solutions for the commercial building envelope . Prior to joining Garland, Smith was a senior development chemist for an international manufacturer and distributor specializing in adhesives for the industrial and consumer markets. He has an M.S. in polymer chemistry and coatings technology from DePaul University, Chicago.
Footnotes:
1 From Proceedings of the Sustainable
2 Low-Slope Roofing Workshop, Oak Ridge National Laboratory, October 1996. ENERGY STAR® is a registered trademark of the U.S. government. The ENERGY STAR Program represents a voluntary partnership between businesses and organizations and the federal government to promote energy efficien-
3
4 cy and environmental activities. From USGBC website: www.usgbc.org/leed/. LEED® Buildings performance refers to the Leadership in Energy and Environmental Design® (LEED) Green Building Rating System®, which is a voluntary, consensus-building national standard that was initiated by the U.S. Green Building Council (USGBC) for developing high-performance sustainable buildings. LEED®, Leadership in Energy and Environ mental Design®, and Green Building Rating System® are registered trademarks of The U.S. Green Building Council.