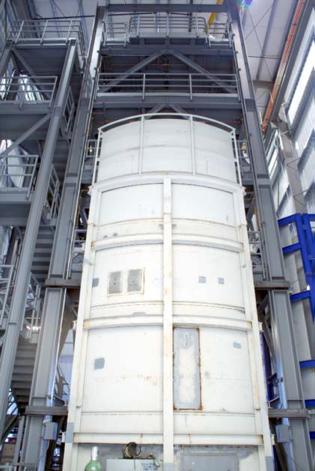
8 minute read
Technology Development Process
Electrical Discharge Machining (EDM) Lab
The Technology Development Center (TDC) is the heart of our tooling and technology development process. It allows engineers and technicians to work side by side to quickly move from design to prototype to final fit up while maintaining proper documentation, integrating lessons learned, and minimizing rework. The TDC is equipped with all tooling and equipment needed to perform large scale metal fabrication and assembly. We have industrial grade milling machines, laser engravers, hydraulic presses, welding operations and a wide variety of calibrated tooling to ensure the final product is built to specification. The EDM lab allows the engineering and tooling design team to quickly test and monitor the tooling prototypes that are intended to be used to perform EDM operations underwater in the reactor. By providing three different test tanks of increasing capacity, the tool testing process remains both effective and efficient.
Advertisement
Reactor Services Test Tower
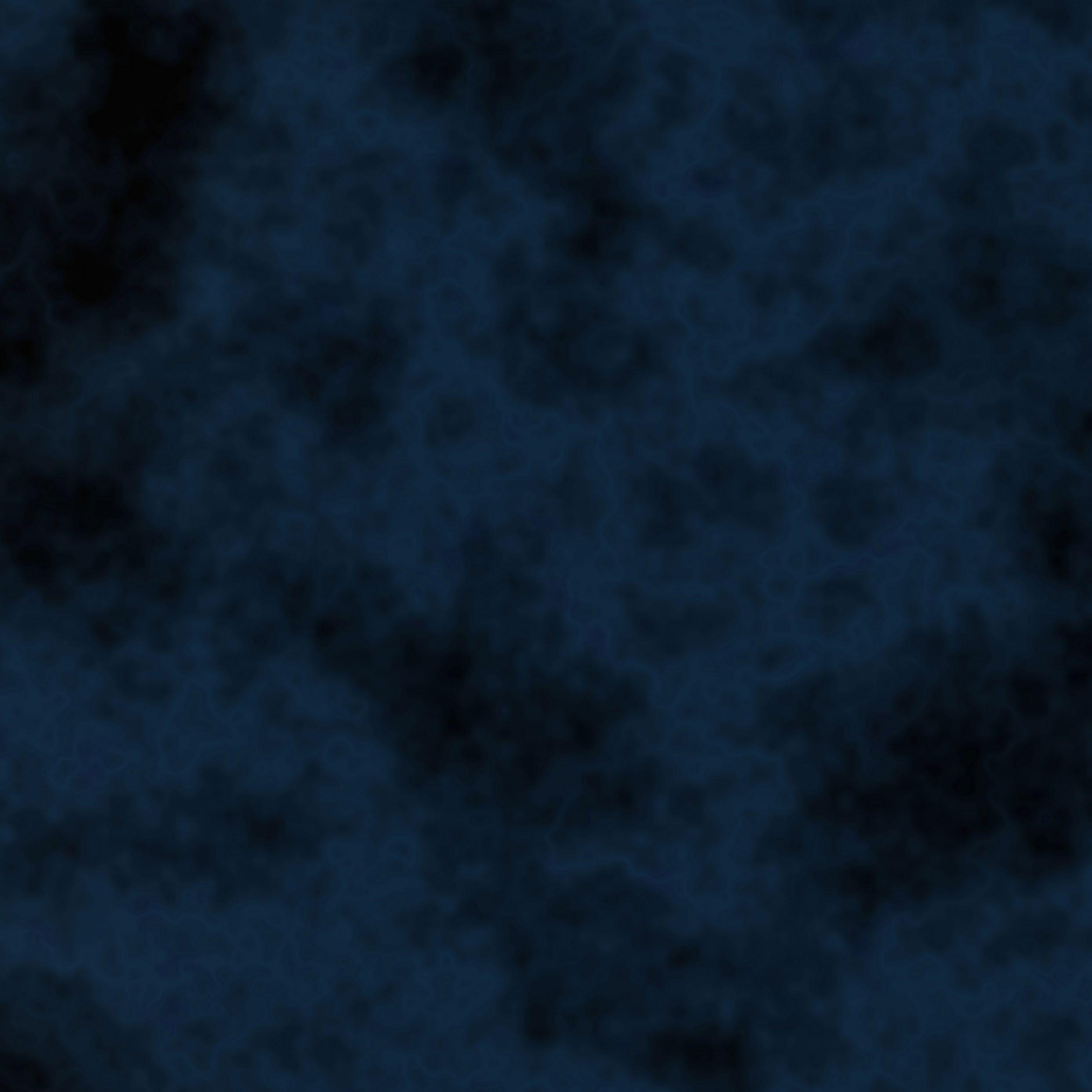
The Reactor Services Test Tower (RSTT) is an 80 ft tall building with a centralized work platform. This allows multiple projects to work simultaneously on full scale reactor mockups with true-to-site dimensions. Technicians work from the platform above while engineers verify tooling and hardware fit/ function at ground level. The RSTT is also home to a tooling test fixture that can simulate operating reactor pressures and
Technology Development Center
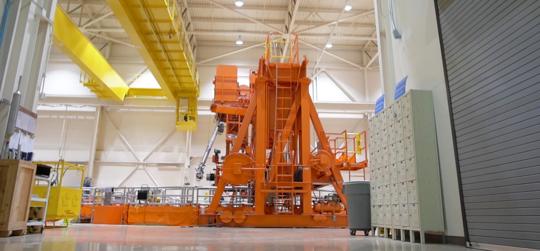
temperatures up to 575 oF and 1350 psig.
Training Classes and Evolutions
The full-scale reactor, internal vessel components, and refuel floor in the STTC provide an ideal training ground for nuclear workers without the concerns of dose and contaminations associated with performing on-the-job training at site.
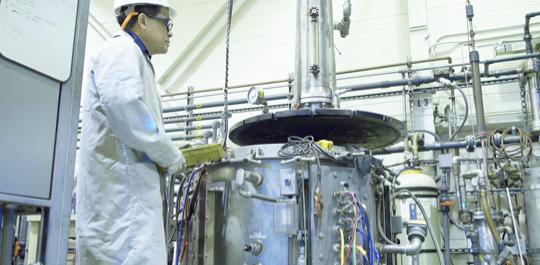
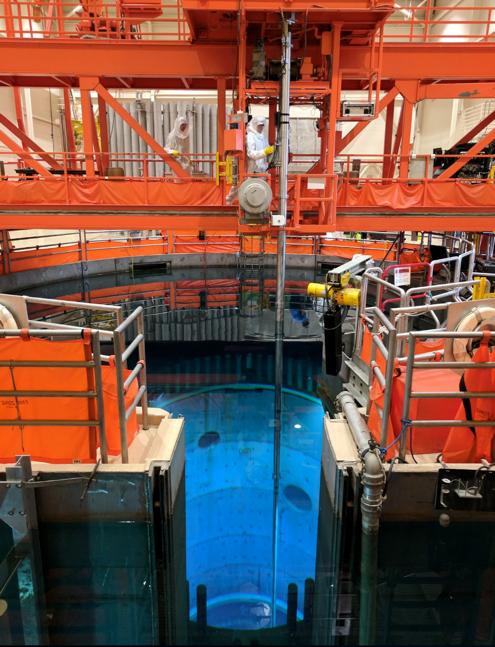
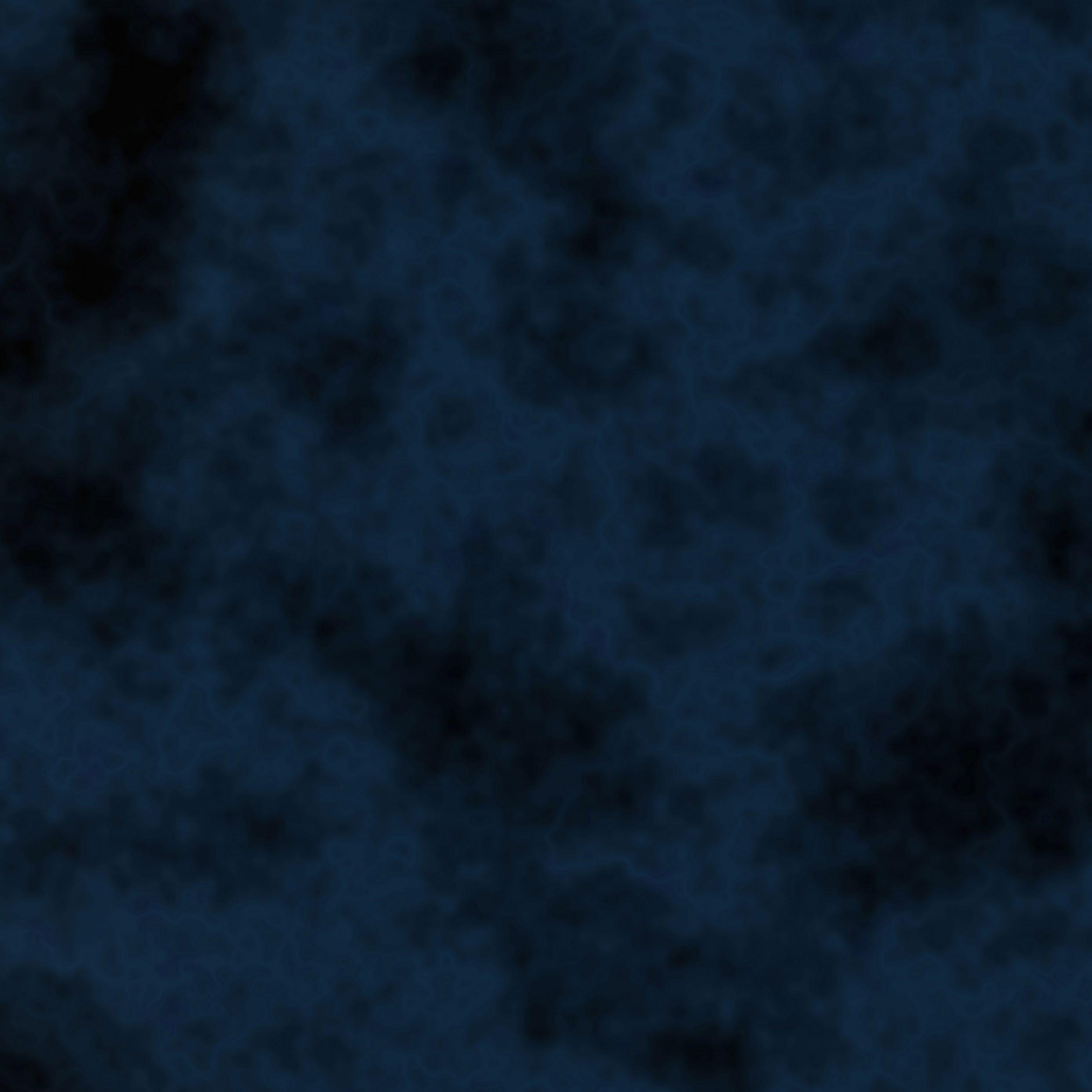
Technicians can move seamlessly from a classroom presentation to a small benchtop mockup demonstration and finish by executing the evolution as they would at site.
Fuel Moving
The fuel moving course allows technicians to become proficient and qualified in the process of fuel movement. Supervisors training is available to enhance fuel movement observations and efficiencies. Many sites leverage this training by holding a SRO teambuilding session just prior to their outage. This enables the SRO to pair up with their assigned fuel movers and practice as a team which greatly improves the accuracy and efficiency of the team.
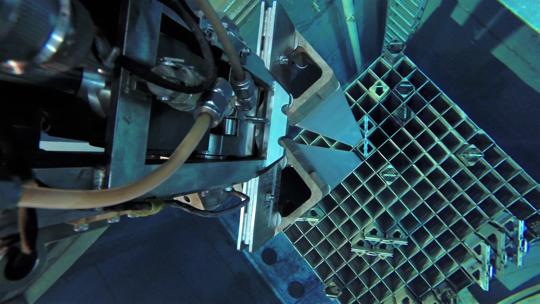
As previously mentioned, the facility is equipped with a fully manual PAR Refueling Platform and a NF500 cylindrical mast. The bridge is equipped with digital load cells, XYZ readouts. It has the same console indications and interlock displays that the operators will see at site. The typical training includes spent fuel pool to spent fuel pool moves, core to core moves, core to pool moves, and pool to core moves. There are also double blade guides available for the same sequence of moves. There is the ability to adjust the formatting of the STTC’s fuel move sheets to match a site-specific format or requirement. This greatly reduces the risk of error when transitioning from training to site execution while improving the efficiency of the spotters who are assigned to placekeep the move sheets.
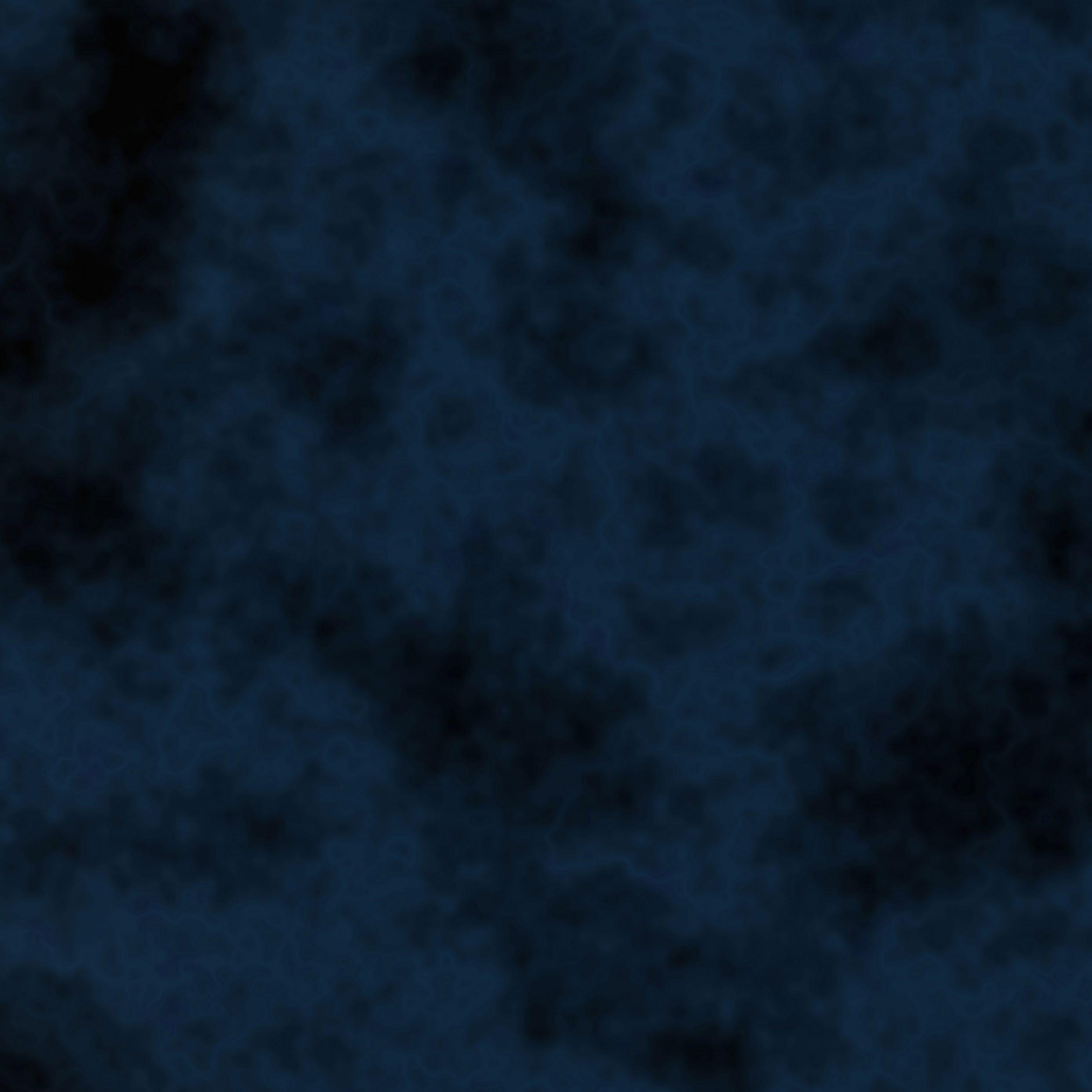
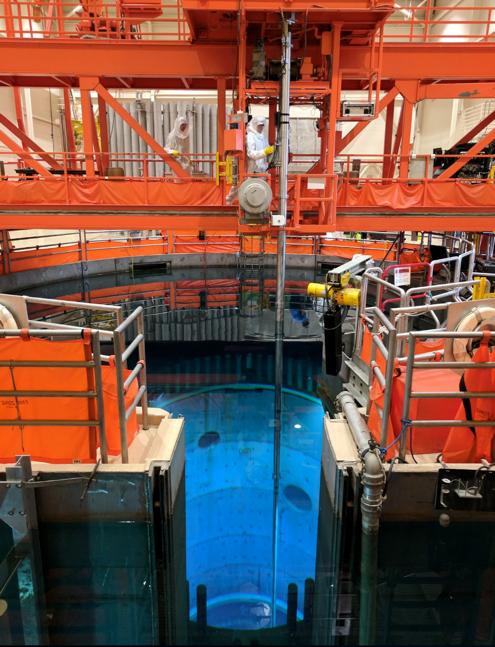
There is also a Reactor Cavity Work Platform (RCWP) installed in the vessel for camera handlers to practice inspections while fuel is being moved. This mirrors the conditions at site to best prepare the fuel movers for parallel path work.
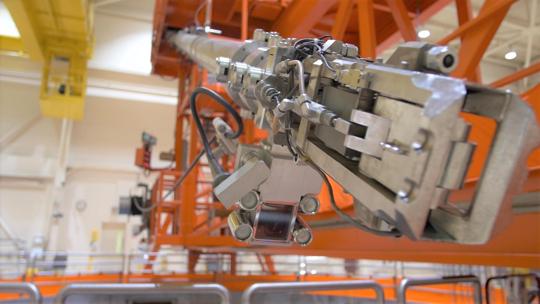
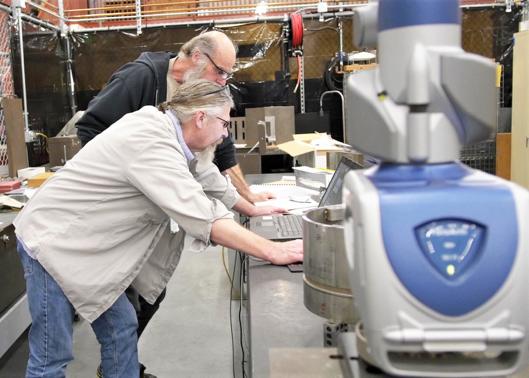
Technical Director Training
The technical director (TD) course is designed to enhance the individual’s understanding of refuel operations and outage execution while obtaining the skills needed to be a qualified supervisor at site. The class has a wide range of topics and draws from very in-depth source material which allows the instructor to tailor the agenda and content to the skill and knowledge level of the students.
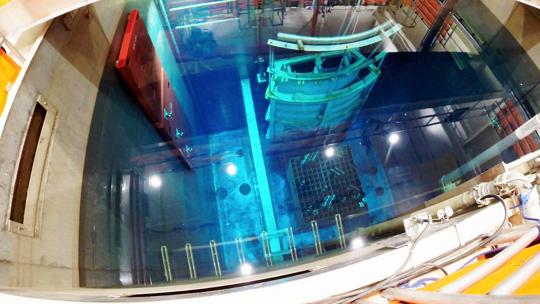
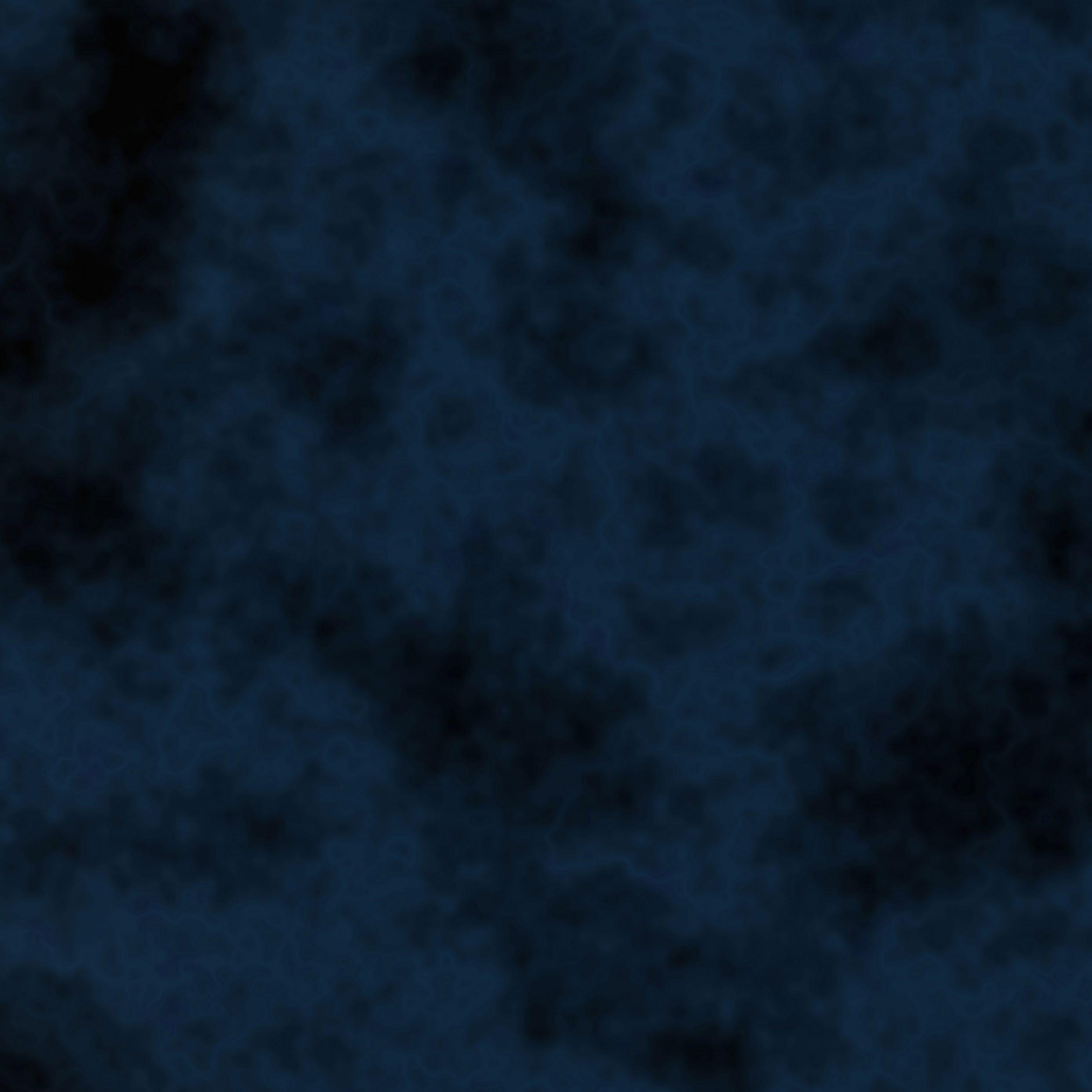
TD training is both classroom and lab based, taking advantage of the facilities to maximize the students’ understanding. Specifically, the course covers reactor disassembly/ reassembly, control rod blade exchange, nuclear instrumentation exchange, fuel moving, new fuel receipt, and outage scheduling optimization.
Other Course Offerings
IIn addition to the courses already described, below is a list of the course titles with brief descriptions along with an abbreviated list of training capabilities. These can be mixed and matched to create a custom training program that focuses on specific areas of interest.
Reactor Maintenance Level 1 – Vessel technician qualification for disassembly and reassembly. Activities include RPV Head removal/install, dryer removal/install, separator removal/install, RPV stud tension/detension, RPV nut and stud removal/install, and drywell head bolt removal/install.
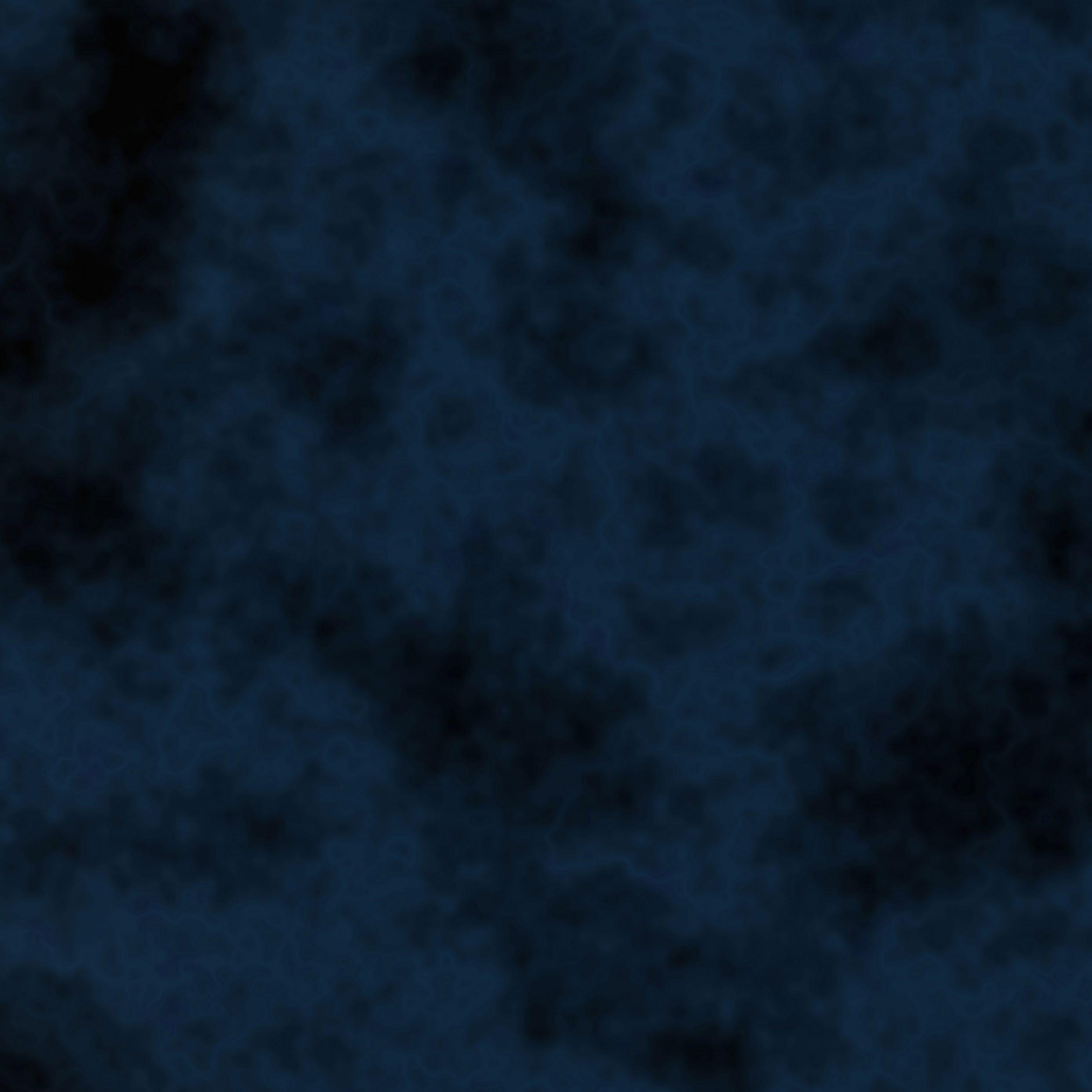
Refuel Floor Activities & Operations – Reactor service technicians develop camera handling skills and receive inspections qualification. Activities include B&W D-40 operation, RJ 2110 Color operation on a rope or pole, jet pump inspections, sparger/piping inspections, and resolution demonstration checks.
Advanced Refuel Floor Activities & Operations – Build on RFAO skills and train with advanced tooling. Activities include main steam line plug install/removal, jet pump maintenance, LPRM exchange & bending, CRB exchange, and reactor modifications.
In-Vessel Visual Inspection Level 2 - Reactor service technicians further improve camera handling skills and build their inspections knowledge to receive an IVVI Level 2 certification.
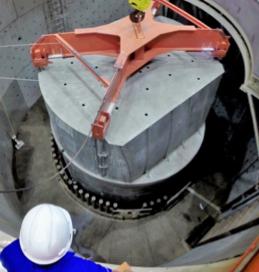
Training Capabilities
a. Fuel Moving b. Control Rod Blade Exchange c. Nuclear instrument Exchange d. Drytube Bending e. In-Vessel Visual Inspection f. New Fuel Receipt & Inspection g. Fuel Disassembly & Reconstitution h. Reactor Disassembly & Reassembly i. Main Steam Line Plug Install & Removal j. Fuel Pool Gate Removal & Install k. RPV Stud Detensioning & Tensioning l. RPV Stud/Nut Removal & Install
m. Jet Pump Maintenance
Technology Development Process
The process of designing, creating, and testing services tooling and technology in San Jose has been refined over the years to leverage the unique opportunities that the STTC facilities present. The ability to design and test in a true refuel floor environment allows the engineers to maintain a mindset that focuses on the end user and customer while still driving speed, experimentation, and continuous improvement.

After a tool is designed and then fabricated in the Technology Development Center, the engineers and technicians will conduct a dry fit test in the Reactor Services Test Tower. Typically, this is performed in a custom-made mockup with the true dimensions of all relevant vessel internal components (shroud/vessel radius, jet pump spacing, annulus width, feedwater spargers, etc.). This dry fit test is beneficial because engineers can see exactly how the tools or hardware interact with their surroundings during operation. They can quickly make modifications or improvements based on their observations and feedback from the technicians that are working with the tools.
Once the tooling passes the dry fit tests and verifications, the mockup is moved into the reactor vessel where a wet test is performed in demineralized water at a depth of 80 feet. Here engineers and technicians perform the tool verification testing procedure (TVTP) to verify proper final fit and function. In parallel, the project implementation team practices with the tooling operation. They work with the engineers to develop the procedures and delivery methods to ensure the execution at site is safe, on schedule, and event free. After the TVTP is successfully passed, the tooling and hardware is inventoried, packed, inspected, and shipped off to support the project.
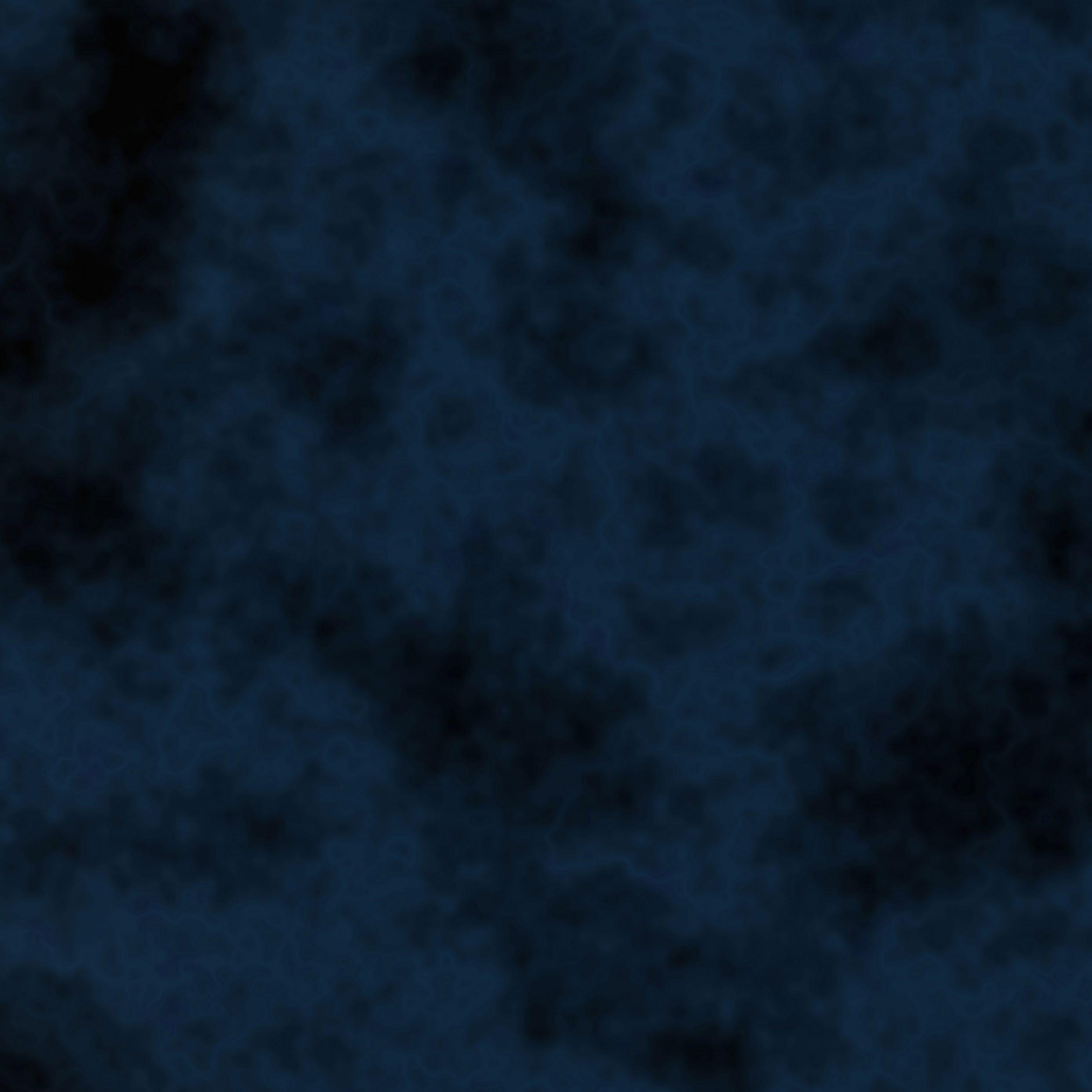
In addition to the formal design process detailed above, we frequently partner with customers to create and test next generation services technologies. One example is the Stealth Double Blade Guide. A customer approached us to help them with their fuel moving rates and identify potential critical path savings associated with DBG install/removal. A traditional DBG requires slower bridge speeds during install/removal and also has a ~10 minute visual inspection requirement per DBG after installing in an open cell to verify the legs did not cross and will not impact CRB insertion.

We were able to take these two areas of improvement and quickly prototype a solution that reduced the drag coefficient in water and also increased the torsional rigidity. This allows DBG movement at full bridge speed and eliminates the requirement of a visual inspection. The prototype was tested in the mockup and the customer verified that it met their needs. They ordered 19 as a trial run for an upcoming outage where they performed exactly as designed and are now working on a fleet-wide rollout.
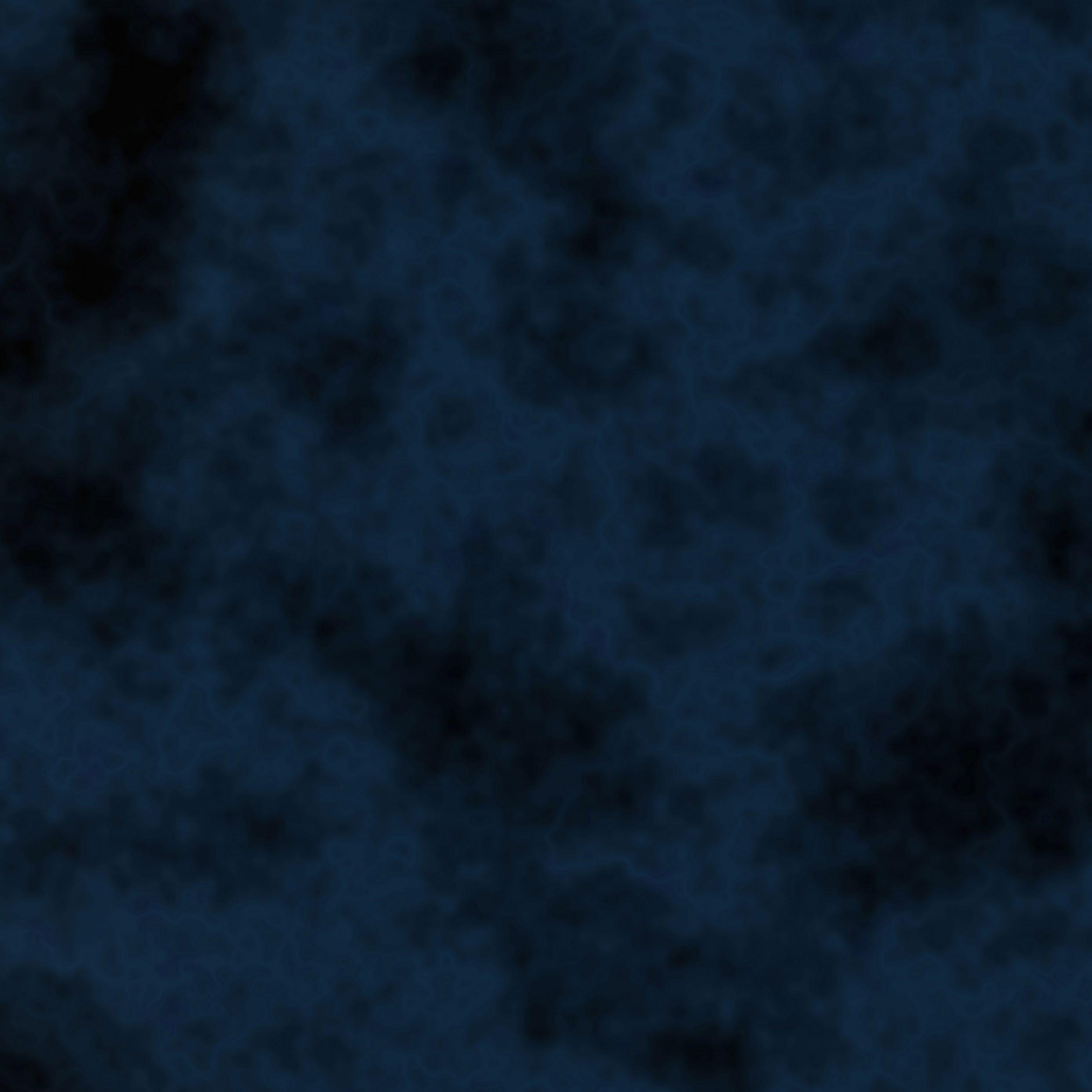
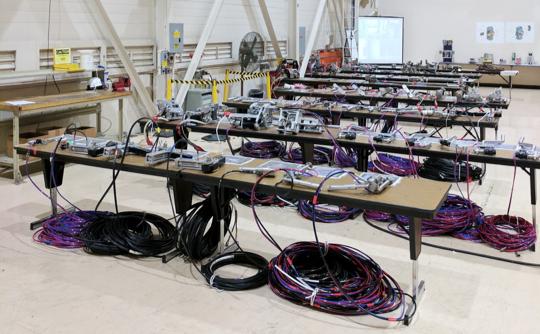
The STTC can also play a role in utility-led design and testing. A customer approached us with a tool used to scrub and vacuum the fuel pool walls and cavity floor.
Because this tool had never been used before, they wanted to test it in an environment similar to their reactor to see how it would function. They reserved the refuel floor for a week of testing and identified and corrected major FME and operability issues. They also recorded video of the tool in use which aided in operator training prior to the outage. This testing was critical to the success of the tool during the outage and resulted in no major delays or tooling failure during its initial deployment.
Whether it is through training technicians and supervisors with our multiple course offerings or developing advanced reactor tooling and technology, the GE Hitachi Services Technology Training Center is always ready to support and deliver for our customers.
visit us at: nuclear.gepower.com
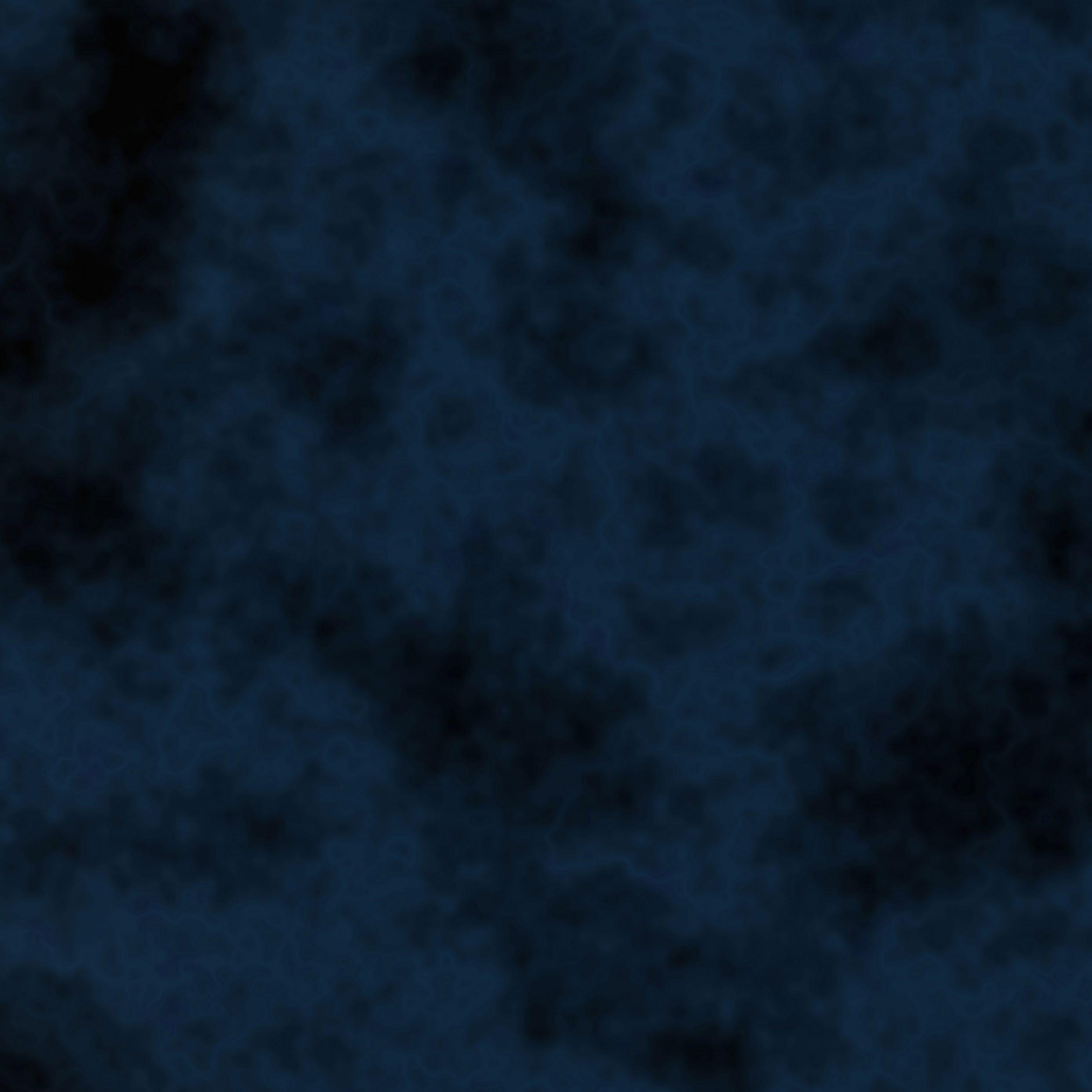
© 2018 GE Hitachi Nuclear Energy. All Rights Reserved.