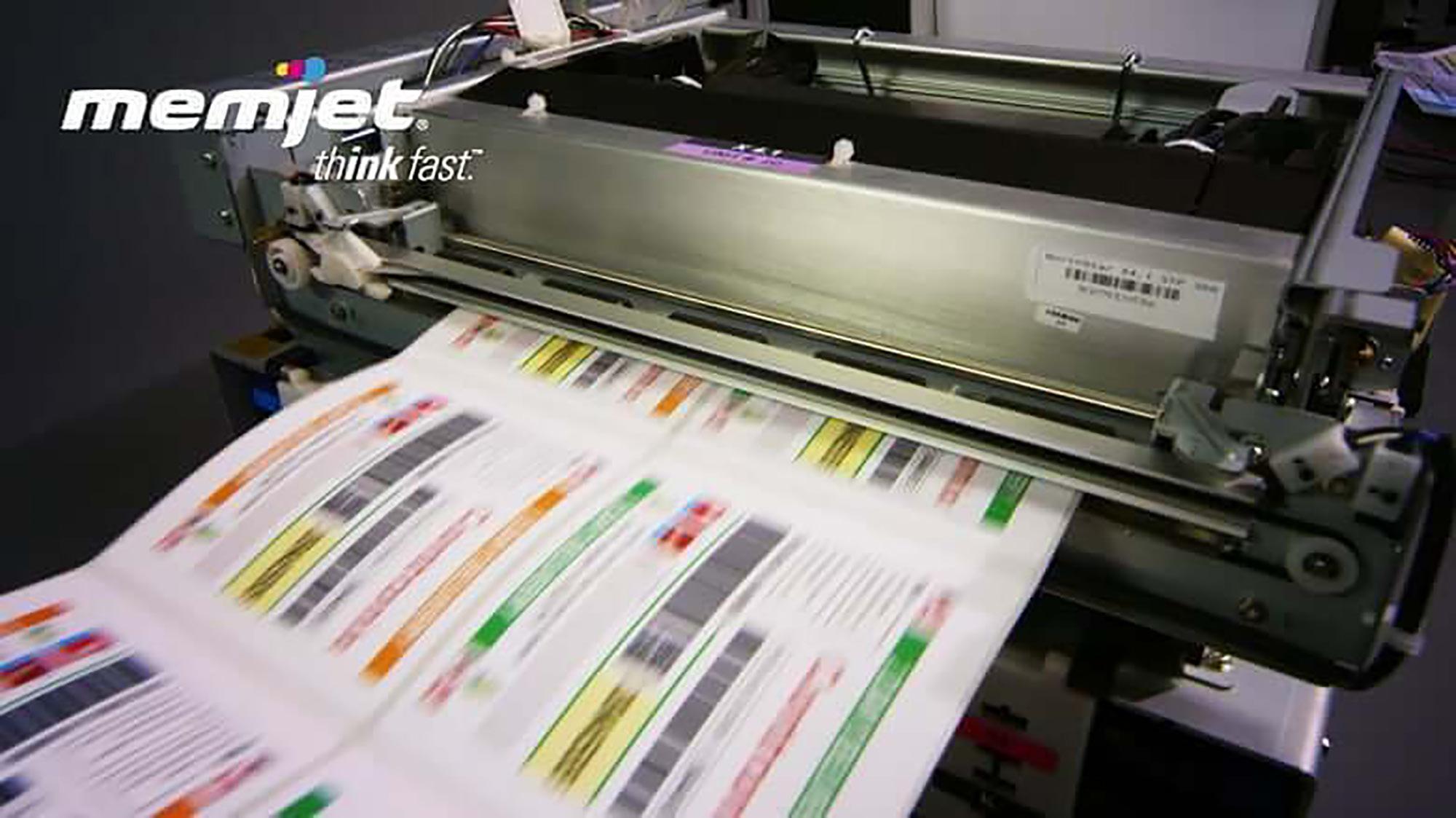
4 minute read
Paper, Primer, Performance. The Inkjet
Paper, Primer, Performance. The Inkjet Cost/Quality Trifecta
Let’s face it, no one wants to pay more than they need to for paper and everyone has a quality target that they need to hit. It seems like it would be pretty straightforward to test a bunch of papers for quality and choose the least expensive one. But with inkjet, no, not so easy.
Advertisement
From the quality perspective, aqueous inkjet will perform better on porous material if the surface has been prepared to prevent the ink from diving into the sheet – and taking the colorants along with it. The smoothness of the surface has an impact on keeping colorants on the surface, but the main factor is the chemistry of a treatment or coating added to the sheet. Aqueous inkjet has the opposite problem with non-porous surfaces; the ink can’t dive in at all and all the color runs off the page. Again, the typical solution is chemistry applied to the paper that allows the ink to stick and lets the water evaporate, supported by appropriate drying technology.
So now the cost factor. Where does this chemistry come from? You can buy inkjet treated or inkjet coated papers that are formulated with a precoating or primer baked in. These papers are designed to deliver top quality with compatible inkjet presses, but they come at a cost premium of 10 to 15 percent for inkjet treated and 30 to 50 percent or even more for inkjet coated grades.
There is also the option to apply precoatings or primers to offset grades before or during the printing process. Some inkjet presses have this option built in with primers that are either jetted through printheads or applied with an anilox. Jetting will apply the primer only where needed, where an anilox coating covers the whole sheet. Since the primer costs money, how it is applied makes a difference. Adding primer to an offset grade will cost less than buying a pre-treated paper, however, there is more to the cost discussion, particularly in mixed press environments.
Companies that are using both offset and inkjet typically buy high quantities of offset papers and it can be very cost effective to be able to use those same papers on inkjet too. Also note that there are far fewer inkjet formulated papers available than offset papers which can limit choice. Self-priming opens up more of the offset media library to the inkjet device. For some jobs, where color fidelity demands are not as high, priming may not be required so you can use it when you need it. However, this brings up another cost factor, ink consumption.
For applications like transaction printing and marketing letter mail, you may get the quality you need from some relatively smooth, uncoated, offset grades. However, you will very likely use more ink than you would with a treated sheet. Ink also costs money and relative ink consumption must be factored into the equation. Finally, consider that some presses are equipped with specially formulated aqueous inks that will print on offset
stocks, including gloss coated without the use of pre-coatings and primers. Again, there is a cost differential. These inks, as well as UV cured inks which also support a wide media range, cost significantly more than other aqueous inks.
To truly solve for the paper, primer performance puzzle you need to consider:
- How many papers do you need and in what quantity? - If you are an offset shop, how much “economy of scale” benefit do you get from the ability to leverage existing paper supply across all devices? - What color quality and clarity is needed and do you have multiple quality requirements on the same paper? - If self-priming, will you jet or anilox apply and what is the cost of the primer? - If self-priming, will you always apply primer, or only for certain types of jobs? - How much will priming or using pre-treated paper reduce ink consumption?
There are a lot of moving parts to consider, but the good news is you have more options than ever before to drive stunning inkjet quality on an everwidening range of media.
Printing Innovation Asia Issue 8 2020
23 DIGITAL PRINTING TECHNOLOGY THAT POWERS THE WAY WE PRINT TODAY.

VersaPass
Enter new markets and leverage new applications with this powerful customized solution that delivers affordable flexibility.
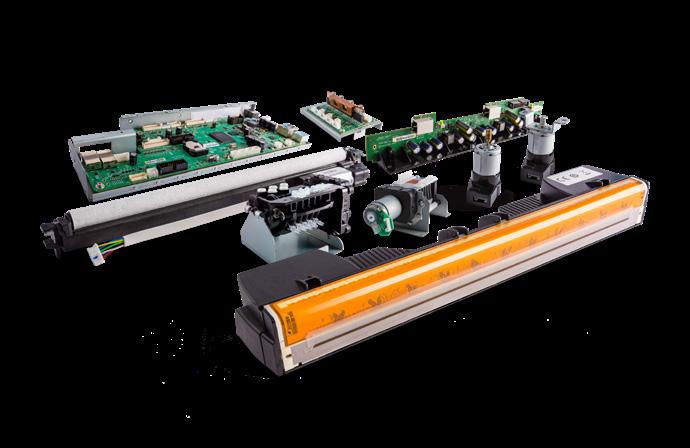
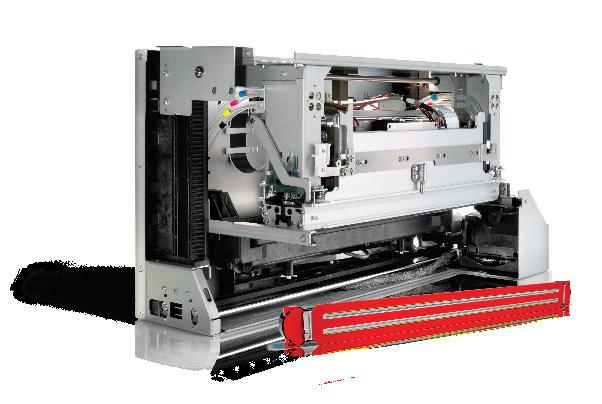
DuraFlex
Fast, affordable printing. Create a new breed of economical, high-performance solutions for a wide range of markets.

DuraLink
Delivering durability and versatility. Enabling the rapid, cost-effective development of next-generation solutions for high-volume print markets.