
2 minute read
Is there a move to factory processes? A new approach to procurement Manufacturer agnostic design
How the use of exoskeletons will change construction, p42
HOW TO BREAK DOWN OFFSITE’S PROCUREMENT BARRIER
Advertisement
UPTAKE COULD BE ACCELERATED WITH MANUFACTURER AGNOSTIC DESIGNS, ARGUE GIORGIO BIANCHI AND MARK BOYLE
Offsite manufacturing has recently been enjoying a renewed surge in popularity, helped by government support, innovative clients, environmental drivers, a dearth of skilled labour and the ongoing housing shortage. But there are still many barriers to wider uptake.
One barrier clients face is the conflict between achieving project security by engaging offsite suppliers early in the design process and maintaining commercial competitiveness in the procurement process. On the other side of the fence, offsite suppliers want to invest in production improvements but struggle without an advance order book or high-volume market demand.
Early engagement is important with offsite, allowing the design to capitalise on the supplier’s system, including
dimensional arrangements of walls and floors, materials and finishes. However, it locks the project into a single supplier and means the final cost is often negotiated rather than tendered.
Also, as the offsite industry comprises many independent manufacturers, each relying on its own specific method of construction and assembly – usually protected by intellectual property rights, which do not allow interchangeability of products, this increases the risk for clients and investors.
So how should clients decide when to select an offsite supplier, and be confident that it has the know-how and capacity to deliver, while still being commercially competitive?
In traditional build projects, progress and quality can be monitored directly
Each independent manufacturer has its own method of construction and assembly
as the works progress on site. This is different for offsite projects as a significant amount of investment in time and cost is needed before anything turns up on the site. This can mean significant financial and time risk, where clients have a building pre-sold or pre-let only weeks before commissioning and handover – yet the majority of the building is not on site nor tested for fit-up accuracy.
Designers can play a major role in resolving these challenges. The choice of the right offsite technology for a specific project is key. Designers should take full responsibility for this choice and the design associated with it up to tender stage, identifying opportunities for collaboration with multiple offsite manufacturers, thereby reducing reliance on a single supplier. This does require designers to develop advanced offsite capabilities and an in-depth knowledge of the manufacturing processes available.
This can be called ‘manufacturer agnostic design’ (MAD). MAD combines detailed design with knowledge of offsite systems, BIM, advanced visualisation techniques, manufacturing and site logistics. For designers to be successful in offering this service, engagement from the supply chain and know-how sharing are essential.
MAD allows a project to be designed to suit multiple offsite systems, and competitively tendered from a range of suppliers. This gives the client the advantages of an offsite approach on the project while still allowing open tender procurement.
Potentially this would not only drive the offsite industry towards more uniformity and standardisation, but also shift attitudes among developers and contractors, helping move construction towards more innovative and industrialised working methods. ●
Giorgio Bianchi is a director and Mark Boyle is director of engineering and technology at Robert Bird Group.
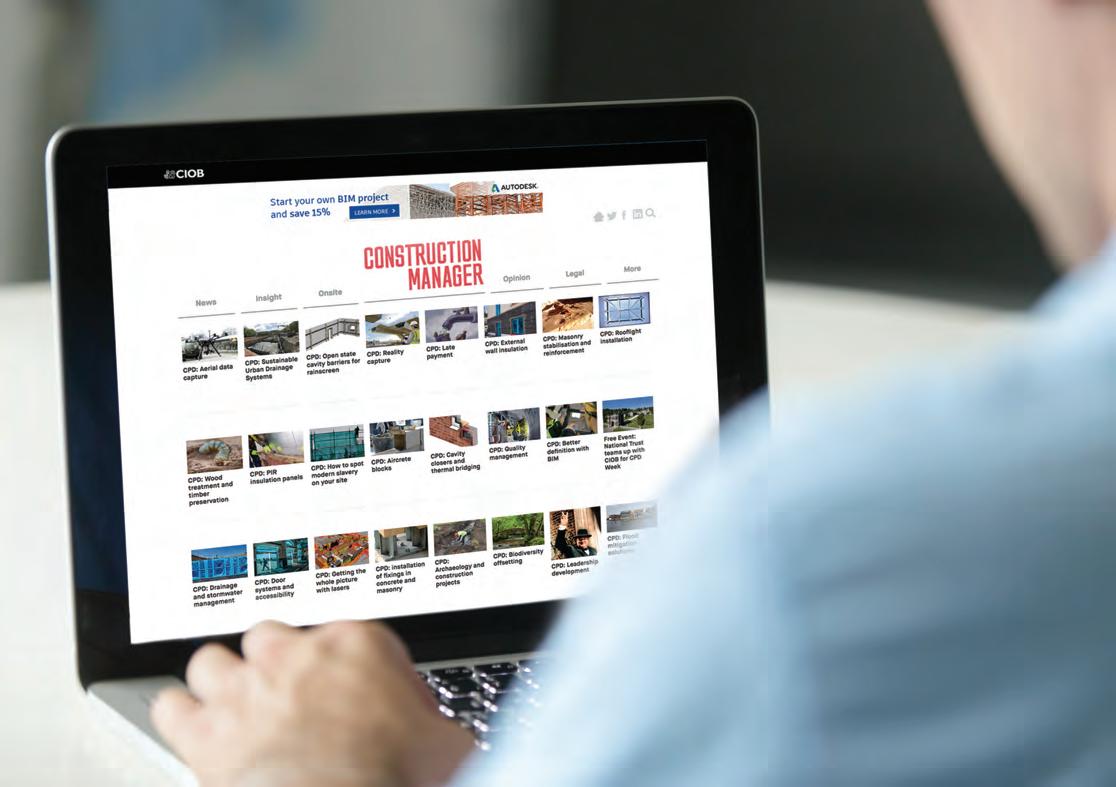