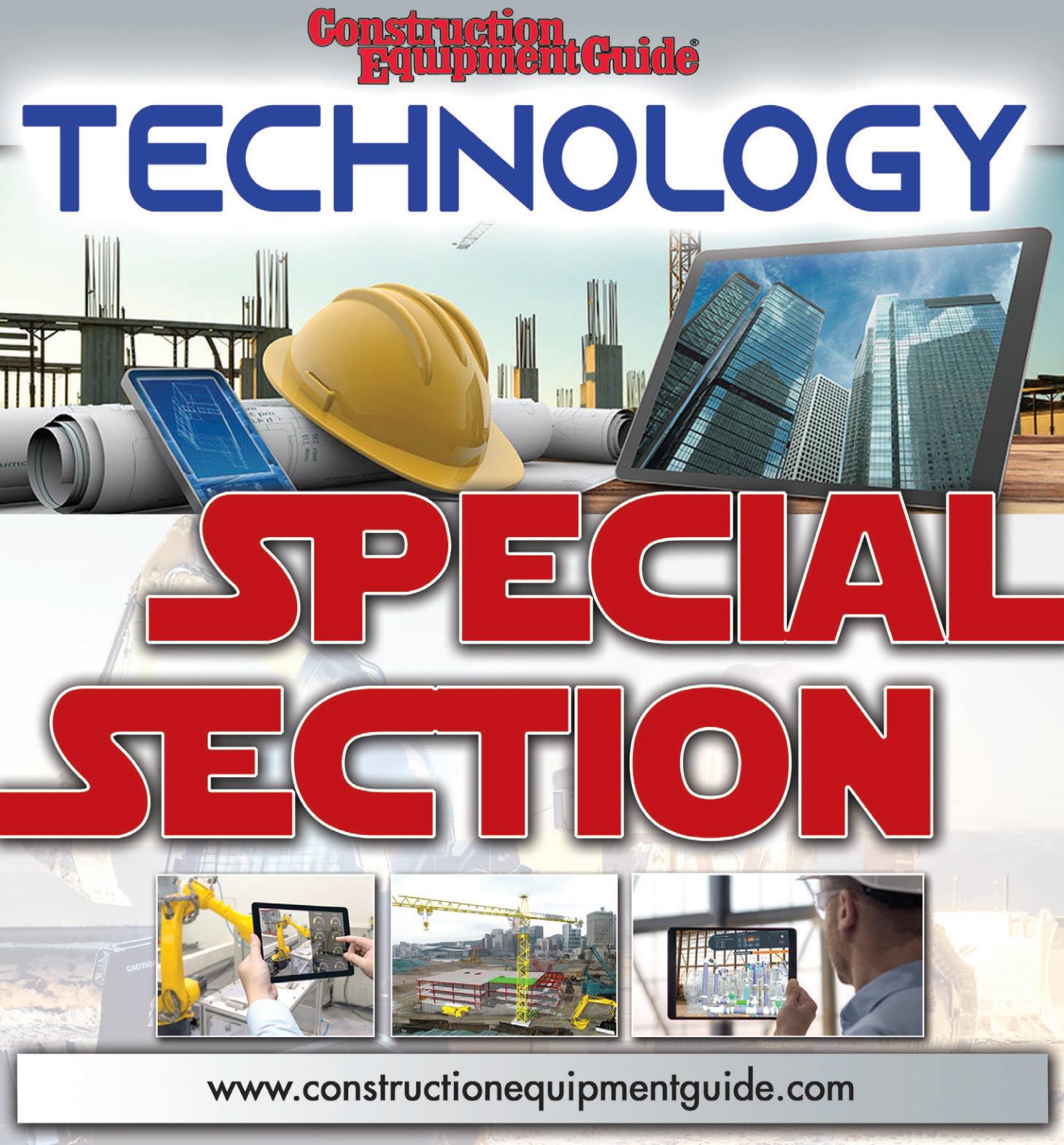
19 minute read
Technology Section
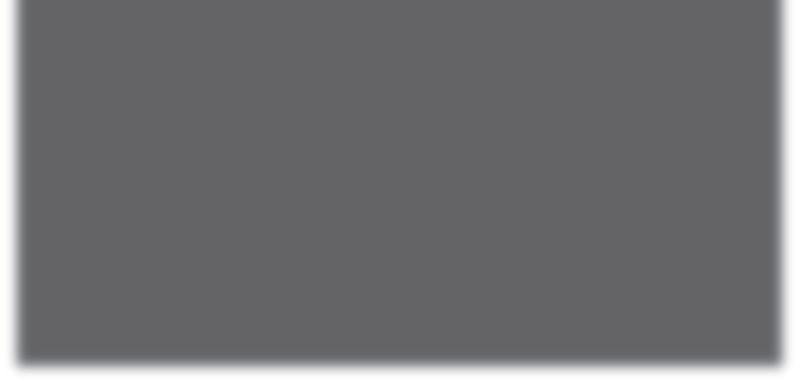
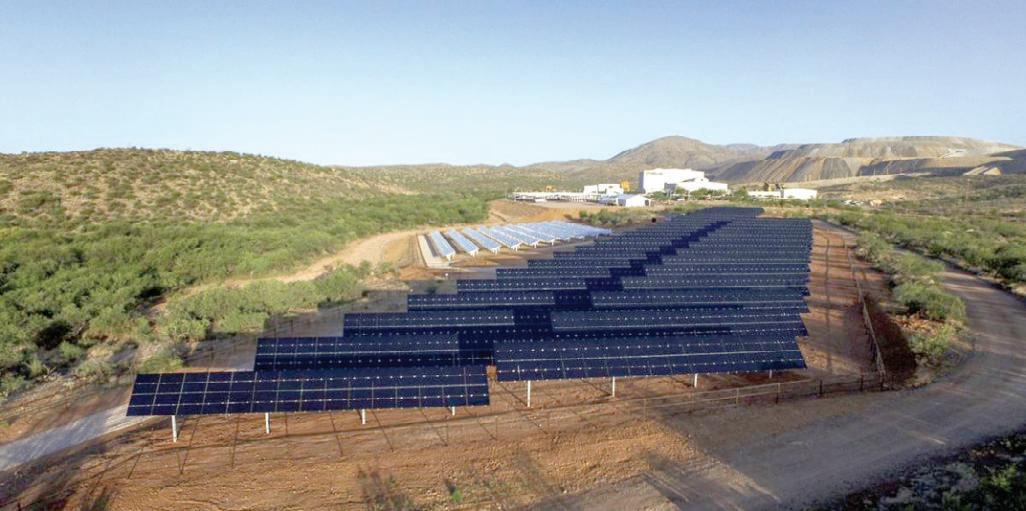
Caterpillar Inc. announced a successful demonstration of its first battery electric 793 large mining truck and a significant investment to transform its Arizona-based proving ground into a sustainable testing and validation hub of the future.
Caterpillar completed development of its first battery electric 793 prototype with support from key mining customers participating in Caterpillar’s Early Learner program. Participants of the program with definitive electrification agreements include BHP, Freeport-McMoRan, Newmont Corporation, Rio Tinto and Teck Resources Limited.
“Our global team came together to develop this battery truck at an accelerated pace to help our customers meet their sustainability commitments,” said Resource Industries Group President Denise Johnson. “This demonstration is a significant milestone, and we are excited for these trucks to get to work at customers’ sites around the world in the near future.”
The Early Learner program launched in 2021 and focuses on accelerating the development and validation of Caterpillar’s battery electric trucks at participating customers’ sites. This approach supports the individual commitments each Early Learner participant has made to reduce and eliminate greenhouse gas emissions from their operations. A primary objective of the program is for Caterpillar to collaborate more closely with its customers as the industry undergoes transformational change through the energy transition.
Early Learner customers came together to witness a live demonstration of Caterpillar’s prototype battery truck on a 4.3-mi. course. During the event, Caterpillar monitored over 1,100 data channels, gathering 110,000 data points per second, to validate simulation and engineering modeling capabilities.
Fully loaded to its rated capacity, the truck achieved a top speed of 37.3 mph. The loaded truck traveled 0.62 mi. up a 10 percent grade at 7.5 mph. The truck also performed a 0.62 mi. run on a 10 percent downhill grade, capturing the energy that would normally be lost to heat and regenerating that energy to the battery.
Upon completing the entire run, the truck maintained enough battery energy to perform additional complete cycles. Mine Site of Future
The prototype truck was built at Caterpillar’s Tucson Proving Ground, located in Green Valley, Ariz.
In support of the energy transition, Caterpillar is investing to transform the proving ground into a working, sustainable “mine site of the future” by installing and utilizing a variety of renewable energy sources. The objective is to implement the same sustainable solutions mining companies will use at their own operations to learn firsthand what it takes to run an electrified mine site and effectively support customers through the changes.
“The transformation of the Tucson Proving Ground allows Caterpillar to demonstrate our energy transition commitments and serve as a stronger advisor to customers as we navigate the changes together. We know it will take an integrated, site-level solution for miners to achieve their carbonreduction goals, and we’re here to help as they redefine the way they mine for generations to come,” said Johnson.
As part of the site transformation, the company will install the latest advancements in sustainability technology, including green hydrogen production, natural gas and 100
SuccessfulCaterpillar Demonstrates First Battery Electric Large Mining Truck A view of Caterpillar’s Tucson Proving Ground’s solar field. percent hydrogen reciprocating engine power generation, fuel cell power generation and expanded energy storage systems. The site also will leverage a variety of renewable power sources, including wind, solar and hydrogen, capable of powering the facility and its products as they become electrified. The transformation of the facility also will serve as a learning platform for optimizing charging and energy management integration. For more information, visit www.caterpillar.com. Caterpillar early learner customers attended the demonstration of the company’s first battery electric 793 mining truck.
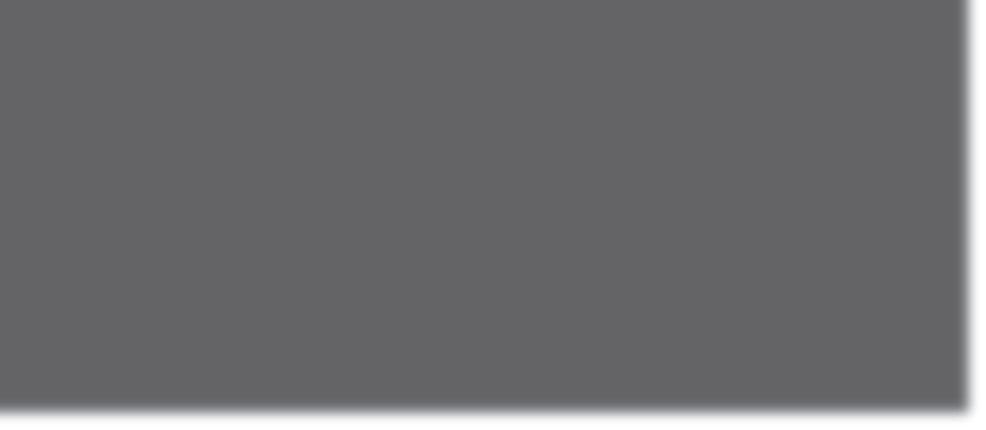

Construction Equipment Guide • Technology Section • www.constructionequipmentguide.com • January 15, 2023 • Page 51 Emission Compliance
Kubota Contributes to Carbon Neutral Lineup With D1105-K
Kubota has responded to the diverse needs of construction and industrial equipment manufacturers throughout the world, including compliance with the latest emission regulations in each country, with the development of the D1105-K.
Building off the D902-K, Kubota developed the D1105-K engine as a power source complying with the latest European, American and Chinese emission regulations.
“Stricter emission regulations not only in Europe but the rest of the world are currently driving decarbonization demand,” said Tomokazu Matsushita, president of Kubota Engine America.
“The electronic control of Kubota engines finely tune fuel injection to create better fuel efficiency than conventional mechanical engines, which reduces CO2 emissions and make exhaust gas cleaner. For these reasons, Kubota strives to broaden its electronically-controlled small engine lineup.”
The D1105-K engine consists of an 18.5kW (24.8HP) rated output, 3,000 rpm, 3 cylinders and a 1.123L displacement. Also equipped with the TVCR combustion system, the D1105-K engine combines Kubota’s original combustion system with a unique electronic control technology developed specifically for small engines. The engine adopts the unique Kubota TVCR combustion system to realize both greater fuel efficiency and a compact size that makes it easy to use as a replacement to conventional Kubota engines, according to the manufacturer. The D1105-K also utilizes a large oil pan, extending the period between essential regular oil changes up to 500 hours dependent on operating conditions. Overall, this provides better serviceability to reduce the time required for engine maintenance. In addition to complying with emission regulations worldwide, the D1105-K complies with China’s national smoke regulations, Category . The new TVCR combustion method reduces black smoke to an invisible level. Moreover, manufacturers can directly mount the ECU to the engine to reduce the burden on the machine design when swapping out the engine, which is expected to reduce the length of development.
Manufacturers can easily replace conventional mechanical engines with the D1105-K because specifications, such as the exterior dimensions as well as the position of the intake and exhaust and power take-off, stay the same. It also can reduce the extra labor placed on the design of the main machine generally necessary to install an engine with an electronic control unit, such as designing the installation position and harnesses, because the ECU is mounted directly to the engine.
Additionally, the Controller Area Network (CAN) allows microcontrollers and devices to communicate with one another without a host computer. The electronic control enables use of the CAN communication protocol, which can control engine rotation and torque through signals sent from the vehicles. The CAN also enables the collection of the engine drive data necessary for telematics technology. This data improves drivability and operational efficiency by aggregating the torque characteristics that mechanical control cannot realize to reduce rotation speed under sudden load.
Kubota will contribute to realizing a carbon-neutral society by bolstering its lineup of not only electronicallycontrolled large engines already under way but also electronically-controlled small diesel engines.
For more information, visit https://global.engine.kubota.co.jp/en/technology/tvcr/d1105k.html.

Industry Debut
JCB Unveils Hydrogen Refueller
JCB, developer of the world’s first working construction machines powered by hydrogen, unveiled another world first for the industry — a mobile hydrogen refueller.
JCB is investing in a project to produce super-efficient hydrogen engines and has already showcased working prototypes of a backhoe loader and Loadall telescopic handler powered by hydrogen.
On Oct. 21, the company announced another industry first — a mobile hydrogen refueller, providing a quickand-easy way for customers to refuel their machines on site. Approximately 97 percent of construction machines have fuel delivered to them while working on site. This means customers are already used to a transportable fuel, allowing refuelling to take place in a matter of minutes.
JCB Chairman Lord Bamford, who is leading JCB’s hydrogen project, said, “Since we became the first construction equipment company to unveil machines powered by hydrogen, many have asked how they can be refuelled.
“Well, today we have an answer with our new mobile hydrogen refuelling system, which allows hydrogen to be taken from on-site tube trailers and distributed to machines by our refueller as they work on the job site. This is no different to today when diesel is taken in bowsers to refuel machines.
“Fossil fuels are not the future and hydrogen is the practical solution to powering our machines in the decades to come. Our British engineers are doing a fantastic job in developing this technology, and there are many more exciting developments to come.”
A team of 100 engineers is working on the project. The first hydrogen-powered machine to be unveiled was a JCB backhoe loader, followed a year ago by a Loadall telescopic handler. The technology went on to be shown in the Green Zone at COP26 in Glasgow as world leaders debated measures to drastically reduce greenhouse emissions.
JCB has manufactured engines since 2004, producing them at plants in Derbyshire and in Delhi, India. Last year JCB celebrated a major milestone with the production of its 750,000th engine.
For more information, visit www.jcb.com.
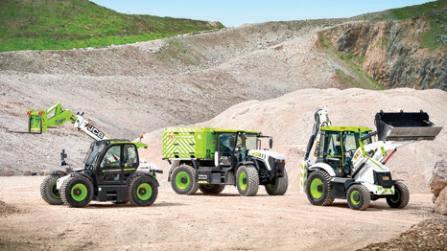
JCB’s mobile hydrogen refuelling system allows hydrogen to be taken from on-site tube trailers and distributed to machines by a refueller as they work on the job site.
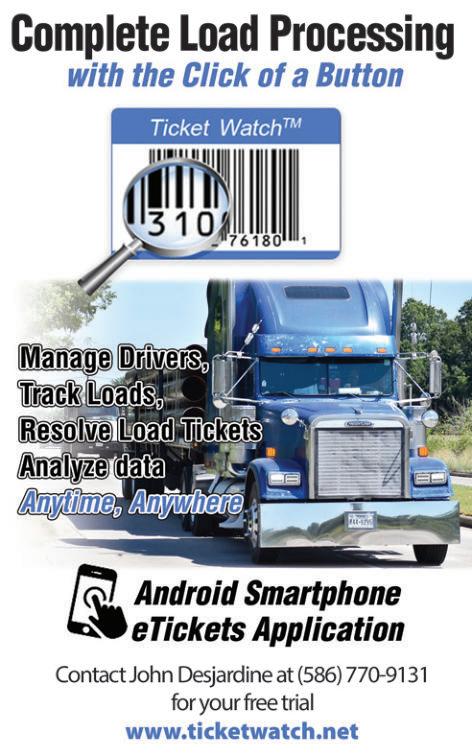
For construction companies of every size, the pandemic accelerated the shift toward hybrid information technology solutions that facilitate both remote and in-office communications between customers and employees.
In the marketplace today, this has increasingly involved mobile and office phones with integrated software that offer sophisticated voice, video, messaging and workforce management capabilities.
This has augmented the complexity of the phone system requirements and presented construction businesses with a plethora of options. Users usually operate from office phones and mobile devices and are working more in and out of the office, so there is a greater demand for forwarding messages to avoid missing calls.
Also, a host of new services beyond calling are often expected such as Short Message Service (SMS)/ Multimedia Messaging Service (MMS), video conferencing, visual voicemail and call recording. On top of all this, the phone system is increasingly connected through APIs to existing company systems such as contact centers, workforce management, and Customer Relationship Management systems (CRMs), so important data can be monitored and evaluated in various ways.
The challenge for construction companies, however, has been dealing with issues of quality and integration, along with constantly escalating provider prices and add-on fees that can end up costing over $70 per user each month. When managers need the services to stay operational but do not have the time or inclination to sort through complex billing, they can feel like a captive of their technology provider.
“Today, construction business owners feel besieged with all the software-as-a-service fees, which constantly creep upwards, never downwards in cost. They are enticed with low offers to start, and then the price doubles or triples on renewal or any changes,” said Eric Brackett, president of BTI Communications Group, a technology convergence provider serving the business and logistics sectors. The company acts as a single-source provider of complex phone (VoIP), network, and physical security systems, down to installation of wiring and conduit as well as cybersecurity monitoring and protection.
“Bait-and-switch phone system pricing is a huge burden on construction businesses when it becomes overhead and an operating expense,” he added. “Instead, managers want to capitalize the full cost over a few years or own the system with minimal operating expense.”
In addition, construction businesses prefer a phone system that includes access to every service option from the start, whether used or not, at a low fixed monthly rate, which eliminates extra fees and complexity.
“Business owners and managers appreciate having only one line item on the bill that covers everything. When the prices don’t change for a fixed period, this eliminates the issue of escalating expenses and surprise addon costs,” said Brackett.
He noted that such a system can improve both the customer and employee experience by integrating web services including voice, video, SMS/MMS, smartphone and PC, as well as contact center, CRM and workforce management.
“Today, a construction business phone system needs to enable working from anywhere, whether at the office, at home, or on the go, and offer the full breadth of communication technologies,” said Brackett.
He added that some of the more advanced marketplace options are now easier than ever to incorporate and use. These allow business employees to use their own smartphones without purchasing new equipment since the service functions with almost every cellular provider. To streamline use, a web portal can enable users to take control and easily manage the entire system through a simple interface.
Video conferencing also facilitates collaboration anywhere on any device, and some or all calls can be recorded and retrieved as needed.
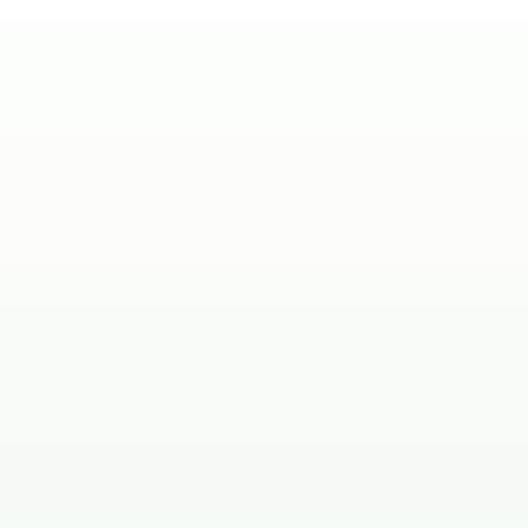
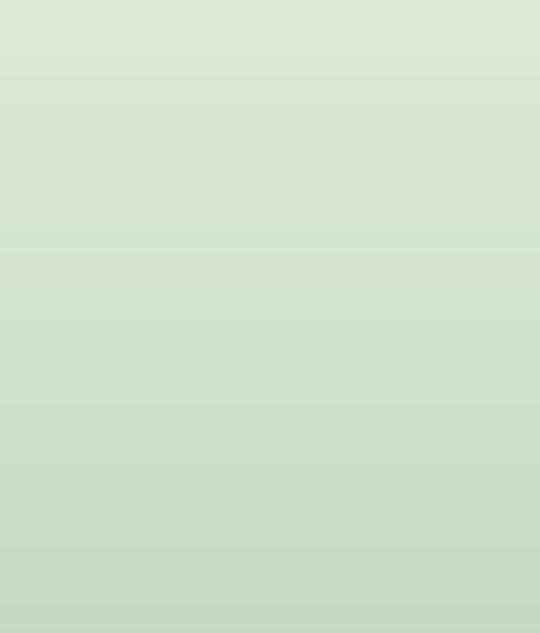
Optimizing Business Telecom
Astral Energy of Montvale, N.J., buys energy wholesale and sells it retail to more than 15,000 businesses in the B2B market. Ashton Fox, chief operating officer of Astral Energy, sought a more robust, stable solution than his existing telecom service provided.
“Many of our customers work off their smartphones on the road so texting and multimedia messaging is important to communicate with them. If our customers struggle to reach us or we are challenged to reach them because of our phone system, it doesn’t work,” said Fox.
“We were running into some issues with our provider’s call quality, SMS and MMS service, and technical support,” he added. “We also wanted better pricing transparency. We didn’t want to find out that we really needed a certain feature later and be asked to pay more for it every month, which would impact our budget.”
As a solution, Fox and Astral Energy turned to a new option in the business market called GoodPhone by BTI that provides complete web, voice, video, SMS, MMS, CRM, contact center, and workforce management service and integration for customers and employees.
The service functions on smartphones and office phones, as well as on PCs used as phones. Complete phone service with all the needed options costs a flat monthly rate of less than $25/user. For the contracted period, each user can utilize an unlimited number of phones as part of the same flat rate. Phones also can be rented or purchased from BTI, or existing VoIP devices used.
When employees use their personal smartphone by downloading the GoodPhone App, they no longer need to give out their personal cell information to handle business calls. Instead, they can provide clients with one office number to reach them, and make or take calls from their web phone, mobile app or desk phone while always displaying the office number.
“Employees only give out one business number and all calls and texts stay within the GoodPhone portal on their smartphone or PC app. If a customer calls their number and they don’t answer it on their smartphone, the call can be routed to the company voicemail, not their personal voicemail,” explained Brackett.
The service also allows businesses to text promotions and contact customers via SMS and MMS messages, as well as track the responses. Employees can monitor messages and set auto-responses with customized text from one account. The service facilitates resolving customer issues by enabling the search of text archives with a 360-degree view of customer interactions.
When video conferencing is required, the service currently allows up to 1,000 people to participate and up to 25 to share a screen.
Fox is very pleased not only with the ease of implementing the GoodPhone service but also its quality and reliability.
“The phones shipped to our office were already programmed, so I just had to plug them in. They essentially handed me a turnkey system,” said Fox.
Fox appreciates that the technology integrator is not just a phone company, which he believes has helped improve system dependability.
“The system is far more global and robust than what we had previously. It is very reliable, and we don’t have any issues. In a year we had less than 20 minutes of downtime, and they were very responsive in getting that resolved,” he said.
Fox credits the telecom service for easing his duties as a manager and COO. GoodPhone facilitates monitoring and managing the workforce from anywhere, and includes a web phone and smartphone app, a call statistics/call center dashboard, and realtime as well as historical reporting.
“As a manager, the way I can see and manage the whole backend is important. Unlike many apps, the mobile app actually works and does not just direct you to a website or browser. I’m able to do virtually everything I can do on a desktop inside the app,” said Fox.
“I’m able to manage my team more effectively with the service,” he added. “For instance, if there’s an issue with a customer on a phone call, I can quickly pull the recording on my phone to help resolve it.”
Other businesses also are finding value in simplifying the complexity of their phone systems at a low, flat monthly rate.
Market Contracting Services, a construction firm in Chicago, Ill., had remodeled its facility and planned to purchase costly landline phones for the office, but reconsidered when its technology integrator suggested a better option, according to Esmeralda Macias, the firm’s office manager.
“With the new VoIP smartphones BTI has available, we don’t have to pay for landlines. We can see everything online now through a portal, so can view all incoming and missed calls,” she said.
According to Macias, employees no longer have to sit at a desk to take calls since they can do so anywhere they have an internet connection.
“Even after hours, we can transfer calls to our smartphones. This has translated into better customer support and more sales,” she said.
From a budgetary perspective, the VoIP phone system also has a success. The system not only eliminates current carrier bills, but also includes unlimited local and domestic long distance.
“The landline phones and service were going to cost a lot more. By implementing GoodPhone, we are already way ahead financially — and we are just getting started with using the capabilities of the VoIP phones,” she said.
Business telecom systems have long been complex and costly, leading to user frustration. However, with greater choice in the marketplace today, construction businesses that integrate essentially all required telecom services through VoIP phones at a low, fixed cost can streamline their operations and gain a competitive advantage.
For more information, call 1-800HELPBTI (1-800-435-7284); email info@btigroup.com; or visit https://www.btigroup.com.

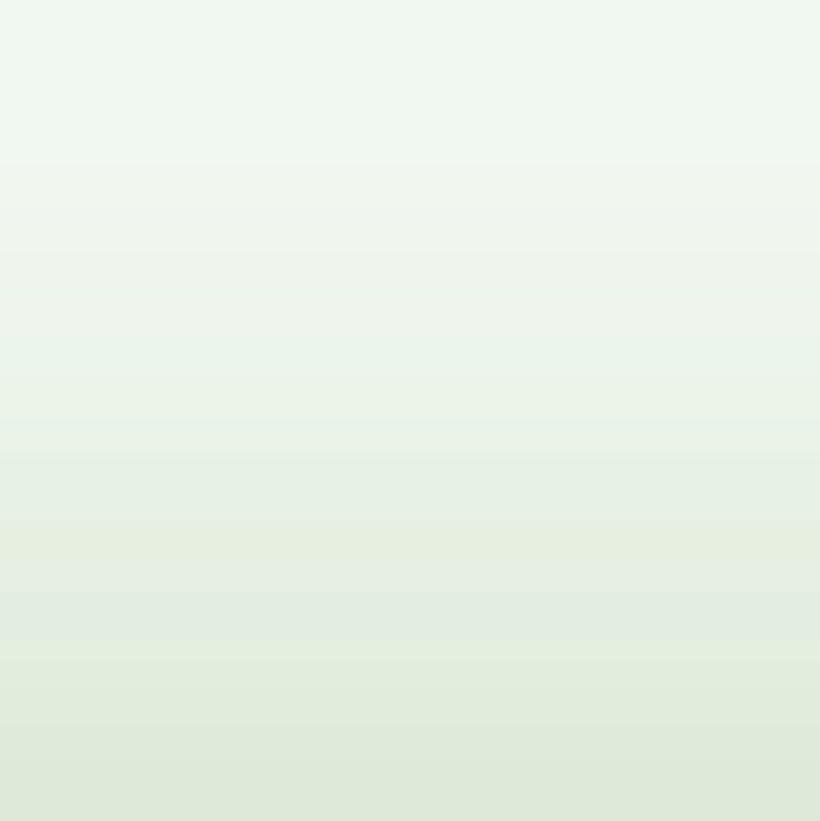
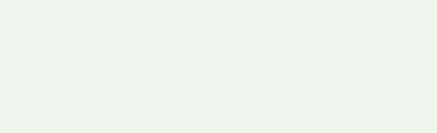
Calling N Construction Business VoI P Simplified
Innovation
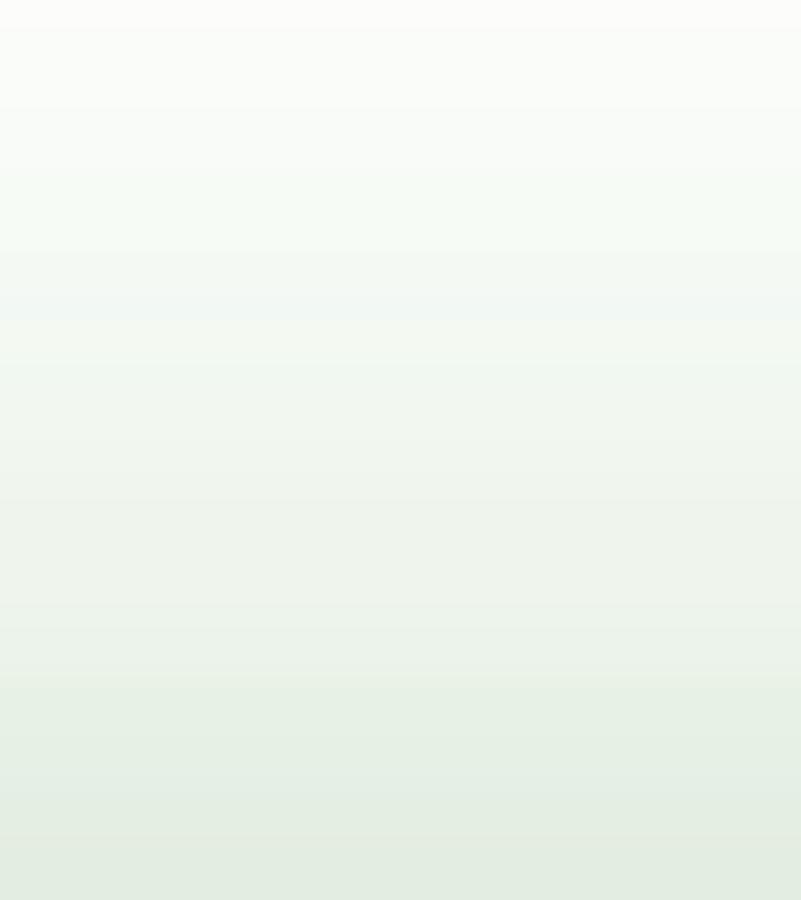

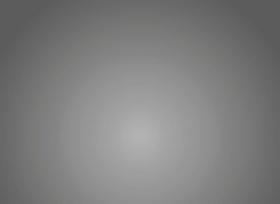
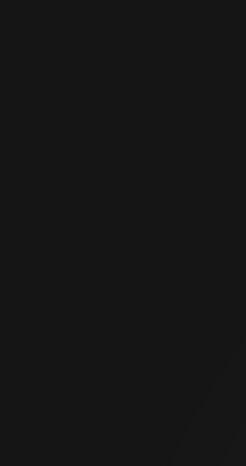
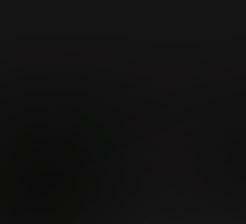
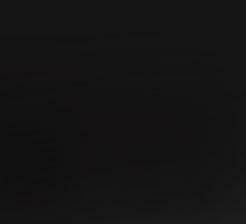
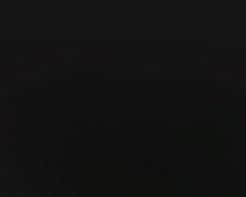
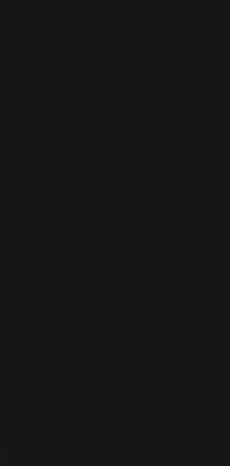
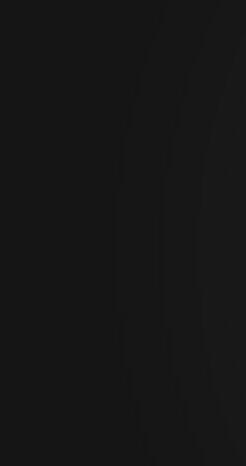
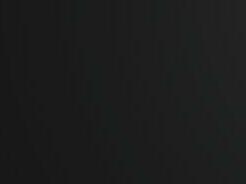
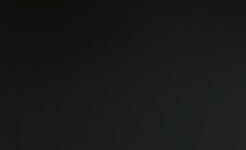
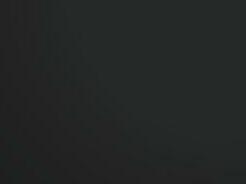
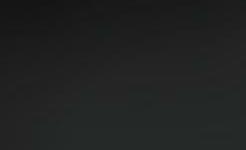
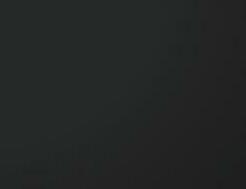
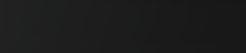
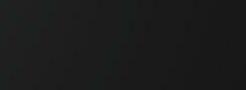
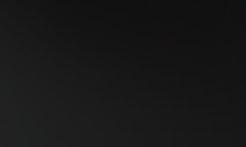


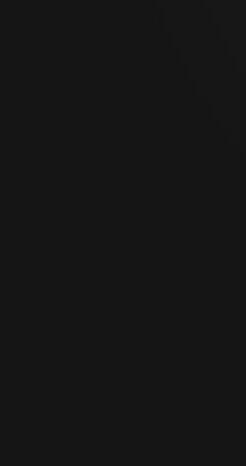
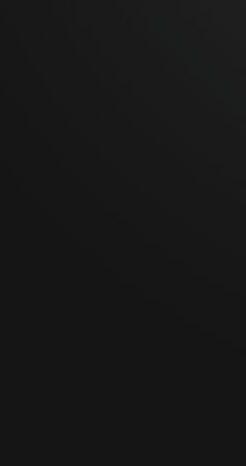
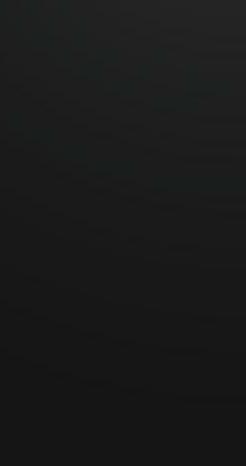
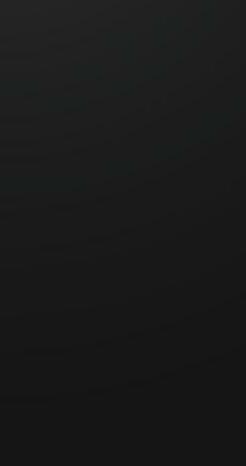
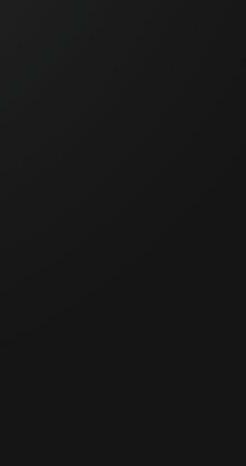
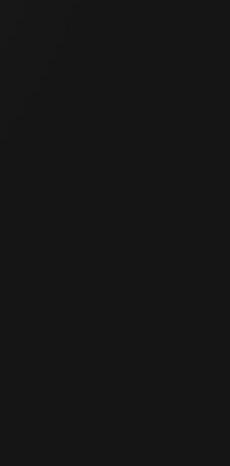
TicketWatch LLC announced an Android Smartphone eTickets application offering greater accessibility for its user friendly and cost-effective electronic ticket system. The system employs barcode scanning of material loads at pickup and drop off, with signatures and tickets generated instantly and synchronized for access from a desktop computer in real time. "We are excited to announce the release of our new Android smartphone app for TicketWatch. This app offers greater convenience, affordability and shorter startup time,” said John Desjardine, president and CEO of TicketWatch.
Every ticket is dated and time stamped, so there is no more waiting on drivers to turn in tickets, eliminating the need for paper tickets. It provides complete load processing with greatly increased record keeping speed, accuracy and documentation over typed or handwritten tickets.
The TicketWatch system offers improved load tracking and the ability to better manage drivers and analyze data anytime, anywhere. TicketWatch LLC offers system start up and customization with onsite training and technical support at no charge for as long as needed by the client.
“We have used TicketWatch on two successive excavation contracts requiring roughly 650,000 cubic yards of material to be hauled offsite,” said a representative from Earth Builders LP, a TicketWatch client. “In real time we were able to record and verify more than 50,000 loads ensuring that we were paid for every load and weren’t charged for loads that we didn’t haul. This was done using two cell phones syncing to the TicketWatch database in real time. Driver tickets were printed onsite with mobile printers, and we were able to check production in real time from the office.
“Using TicketWatch we were able to give the project owner confidence that they received the material they were paying for and gave us the ability to verify that we were not paying contract haulers for phantom loads. TicketWatch proved to be a simple and effective way to monitor over 500 loads per shift.”
For more information, visit www.ticketwatch.net. CEG
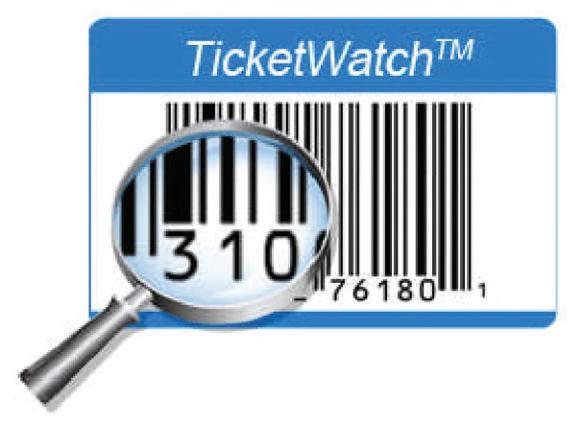
Electronic Access
TicketWatch Now Offers Android Smartphone App for eTicket System
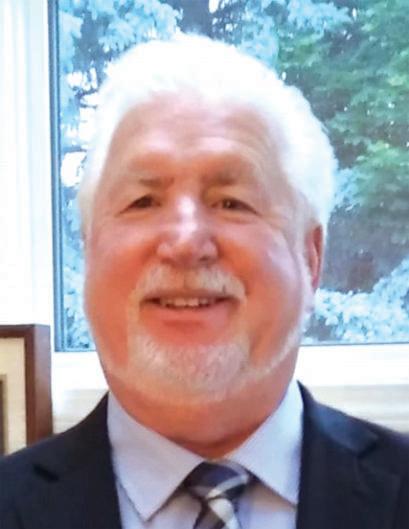