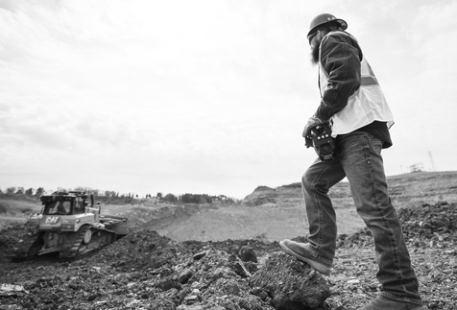
19 minute read
CAT OFFERS COMMAND REMOTE OPERATION FOR MEDIUM DOZERS
To boost jobsite safety in hazardous dozing conditions, Caterpillar announced the expansion of Command remote machine operation to Cat D5, D6, and D7 Dozers.
Command for Dozing removes operators from the cab and offers remote operating from a safe distance in applications such as overburden/reclamation work, ripping overburden or leach pads, slurry pond dozing, and operation around hazardous materials or unstable surfaces.
Next generation dozers are shipped from the factory remote ready, making field installation fast with only a few additional parts required. With Command fully integrated with the machine’s electronic and hydraulic systems, remote operation delivers quick response, smooth control and virtually no latency.
Companies have the option of equipping dozers with line-of-sight (LOS) or non-lineof-sight (NLOS) operation, and a groundlevel switch quickly toggles between manual and remote dozer operation. To help improve jobsite productivity, Command allows production to restart immediately following disruptive processes, such as blasting in quarry applications.
Beyond improving safe operation and increasing productivity, Command for Dozing offers a potential solution to worker shortages and added training opportunities for newer operators. By allowing the operator to work outside the machine, Command opens opportunities to those with physical limitations which prevent them from climbing into the equipment. It can attract a new generation of worker while increasing the longevity of experienced operators.
Two Options, Precise Control
Portable and lightweight, the command console (LOS) allows workers to work outside of the cab while remaining on site and in direct visual contact with the dozer. With its range reaching 437 yds., the console positions the user for optimum visibility.
Requiring no on-site communications infrastructure, it is ideal for short-term and emergency remote operation. An ergonomic console layout features intuitive controls with ISO symbols that provides access to all dozer functions, while an LED display offers clear readout of machine status.
Furthering operation simplicity, the console (LOS) system supports multiple assist technologies the operator would have from inside the cab, including traction control, AutoCarry and stable blade. Unlocking with an electronic access card, the console can be configured to control another machine equipped with Command by simply changing out an RFID chip. Its lithium-ion battery provides a quick charge and long run times in varying ambient temperatures.
Built-in safety features stop all dozer movements if the remote shutdown switch is pressed, wireless communication is lost, or the console is tilted more than 45 degrees.
The command station provides non-lineof-site operation from the comfort of an airconditioned office on-site or many miles away, as distance is limited only by the capabilities of the wireless network. By eliminating the fatigue-inducing vibration of machine movements in the cab, operators can work with less fatigue.
The configurable station features a similar feel to the cab with familiar controls, complete with pedals, joysticks, adjustable seat, switches and storage. Multiple screen displays offer visuals from the left and right cutting edges, blade top-center and rearview that includes the ripper.
Beyond supporting assist technologies offered by the console (LOS), the command station (NLOS) offers compatibility with blade load monitor, slope assist and Grade with 3D with the same response time as in the cab. Users can easily switch to operating a different command-equipped machine — dozer, wheel loader or excavator — from the same or different sites with virtually no downtime for shift changes or for travel to the job site.
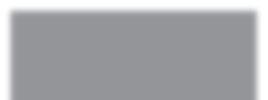
With its range reaching 437 yds., the console positions the user for optimum visibility.
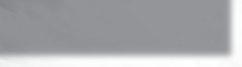
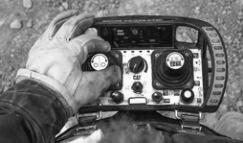
Doosan Plans to Produce Larger Model DD130 in 2023
DOOSAN from page 54 machine functions are not used for a predetermined period, the auto idle feature idles the dozer engine to reduce fuel consumption. When the operator moves the controls, the dozer automatically returns to the previous throttle setting.
The auto shutdown feature saves fuel and helps lower warranty hours. When the feature is enabled, the engine shuts down after it has been idling for a specified period. Default shutdown occurs after five minutes of idling but can be set for longer periods by the operator using the Smart Touch display. Versatility
Doosan dozers come standard with piping for an optional ripper attachment. The ripper attachment features parallel linkage that helps maintain a constant angle to the ground regardless of the height. The attachment can quickly break up hard, rugged materials prior to grading, and it can be used to install erosion control. Also available as an attachment is a towing draw bar, allowing operators to use the Doosan dozer to tow other equipment on a job site. Durability
One of the dozer’s key features is its undercarriage design. Doosan developed its dozer undercarriage system to help lower the total cost of operation. The design includes both single- and dual-flange rollers for improved durability and long life.
Customers can choose from several track guards to enhance uptime protection. They include general-purpose and full guard options to fit the jobsite conditions. In addition, track shoe options are available to help distribute the load to the ground. Thinner tracks are used for rugged, rocky environments. A low-ground pressure option is available for sandy soil conditions. Serviceability
An in-line precleaner helps improve filter life and is integrated with the air cleaner. It’s also more compact to fit in the smaller engine compartment. Self-cleaning and maintenance-free, the intake system can expel a variety of debris, including mud, snow, rain, leaves, sawdust and chaff.
Doosan designed its dozer undercarriage for convenience and cost-effective maintenance. Areas of the undercarriage that naturally experience greater wear and tear are easy to access. For example, a removable side panel provides access to an area to add grease to the undercarriage’s tension system. Customers can order replacement parts through their local Doosan dealer.
To help minimize fuel-related issues, Doosan offers a filter-type high-performance water separator, which captures moisture in the fuel and reduces impurities. Standard pre-filters and dual main filters achieve a high degree of purity that minimize fuel system failures. The fuel filter water separator and the main fuel filter can easily be reached by lifting a panel on the front of the dozer.
Common, everyday maintenance items can be accessed from ground level, including the following components: • Electronic main control valve • Diesel fill • Diesel exhaust fluid fill • Hydraulic oil fill • Fuel filter • Engine oil filter • Air cleaner • Battery • Windshield wash tank
When necessary, owners can tilt the dozer cabin to reach critical components. Even with the cab tilted, the dozer can be started while the machine is being diagnosed or repaired.
Doosan DD100 dozers are designed with a unique hydraulically controlled cooling system and come standard with a reversible fan. Operators can set the fan to automatically reverse at a predetermined time interval. The cooling system is in the rear of the machine instead of the front. This contributes to better visibility to the blade from the operator’s point of view.
Doosan DD100
Dozer Specifications* • Horsepower (gross): 122 hp (91 kW) • Horsepower (gross): 122 hp (91 kW) • Operating weight: 22,300 – 24,900 lb. (10.1 – 11.3 t) • Blade capacity: 2.9 – 3.4 cu. yd. (2.2 – 2.6 cu m) • Blade height: 3 ft. 7 in. (1.1 m) • Blade width: 8 ft. 11 in. – 10 ft. 6 in. (2.7 – 3.2 m) • Blade angle: 23 degrees • Drawbar pull: 35,300 lbf. (16 ton-force) • Tumbler distance**: 7 ft. 7 in. (2.3 m) • Travel speed, max: 5.6 mph (9 kmh) • Dozer cabin is ROPS/FOPS certified *Specifications represent the DD100 US10 and US20 configurations **Tumbler distance is from idler center to motor center
For more information, visit na.DoosanEquipment.com.
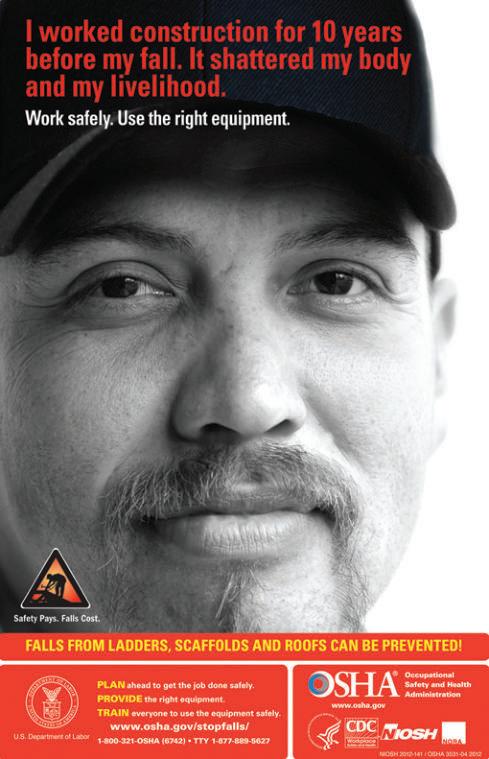
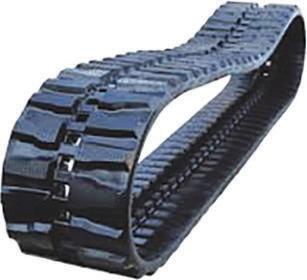
Also Carr y Bucket Teeth and Cutting Edges
Caterpillar® John Deere® Komatsu® Case® Hitachi® Liebherr® Volvo® Kobelco® Kubota® Bobcat® Takeuchi®
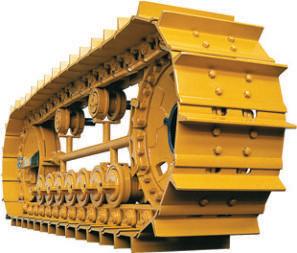
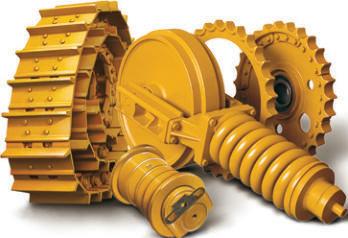
Call For a FREE ESTIMATE!
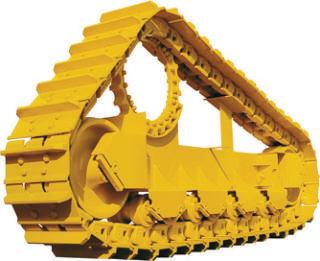
Tractor Tracs Inc.
Undercarriage Specialists
5505 Caterpillar Drive, Apex, NC 27539 919-387-1050 ï 888-526-9740 ï www.tractortracs.com
CHART from page 52
MODEL ENGINE POWER WEIGHT ENGINE TYPE HP (KW) LBS. (KG)
DOOSAN INFRACORE
Specs shown are for the XL Blade configuration.
DD100 122 (91) 22,046 (10,000) Doosan D34 JOHN DEERE
Loaders 655K 155 (116) 40,614 (18,422) John Deere PowerTech PVS 6068 655K Waste Handler 155 (116) 42,120 (19,104) John Deere PowerTech PVS 6068 755K 194 (145) 45,178 (20,492) John Deere PowerTech PVS 6068 755K Waste Handler 194 (145) 50,675 (22,985) John Deere PowerTech PVS 6068 Dozers 450K 80 (60) 17,510-18,752 (7,959-8,522) John Deere PowerTech PWS 4045 550K 92 (69) 19,758-21,000 (8,981-9,544) John Deere PowerTech PWS 4045 650K 104 (78) 21,320-22,343 (9,691-10,156) John Deere PowerTech PWS 4045 650K SmartGrade 104 (78) 21,320–22,343 (9,691–10,156) John Deere PowerTech PWS 4045 700L 135 (101) 30,900–32,088 (14,016–14,555) John Deere PowerTech PVS 6068 700L SmartGrade 135 (101) 30,900–32,088 (14,016–14,555) John Deere PowerTech PVS 6068 750L 175 (131) 37,569–40,040 (17,041–18,162) John Deere PowerTech PVS 6068 750L SmartGrade 175 (131) 37,569–40,040 (17,041–18,162) John Deere PowerTech PVS 6068 850L 225 (168) 47,578–51,356 (21,581–23,295) John Deere PowerTech PSS 6090 850L SmartGrade 225 (168) 47,578–51,356 (21,581–23,295) John Deere PowerTech PSS 6090 850L Waste Handler 225 (168) 54,086–54,353 (24,533–24,654) John Deere PowerTech PSS 6090 950K 265 (198) w/ OSD blade / 280 (209) w/ PAT blade 65,300–73,700 (29,606–33,431) John Deere PowerTech PSS 6090 950K SmartGrade 265 (198) w/ OSD blade / 280 (209) w/ PAT blade 65,300–73,700 (29,606–33,431) John Deere PowerTech PSS 6090 950K Waste Handler 265 (198) w/ OSD blade / 280 (209) w/ PAT blade 71,250–75,150 (32,325–34,100) John Deere PowerTech PSS 6090 1050K 350 (261) 95,400–96,100 (43,270–43,590) John Deere PowerTech PSS 6135 1050K Waste Handler 350 (261) 102,700–103,300 (46,600–46,850) John Deere PowerTech PSS 6135
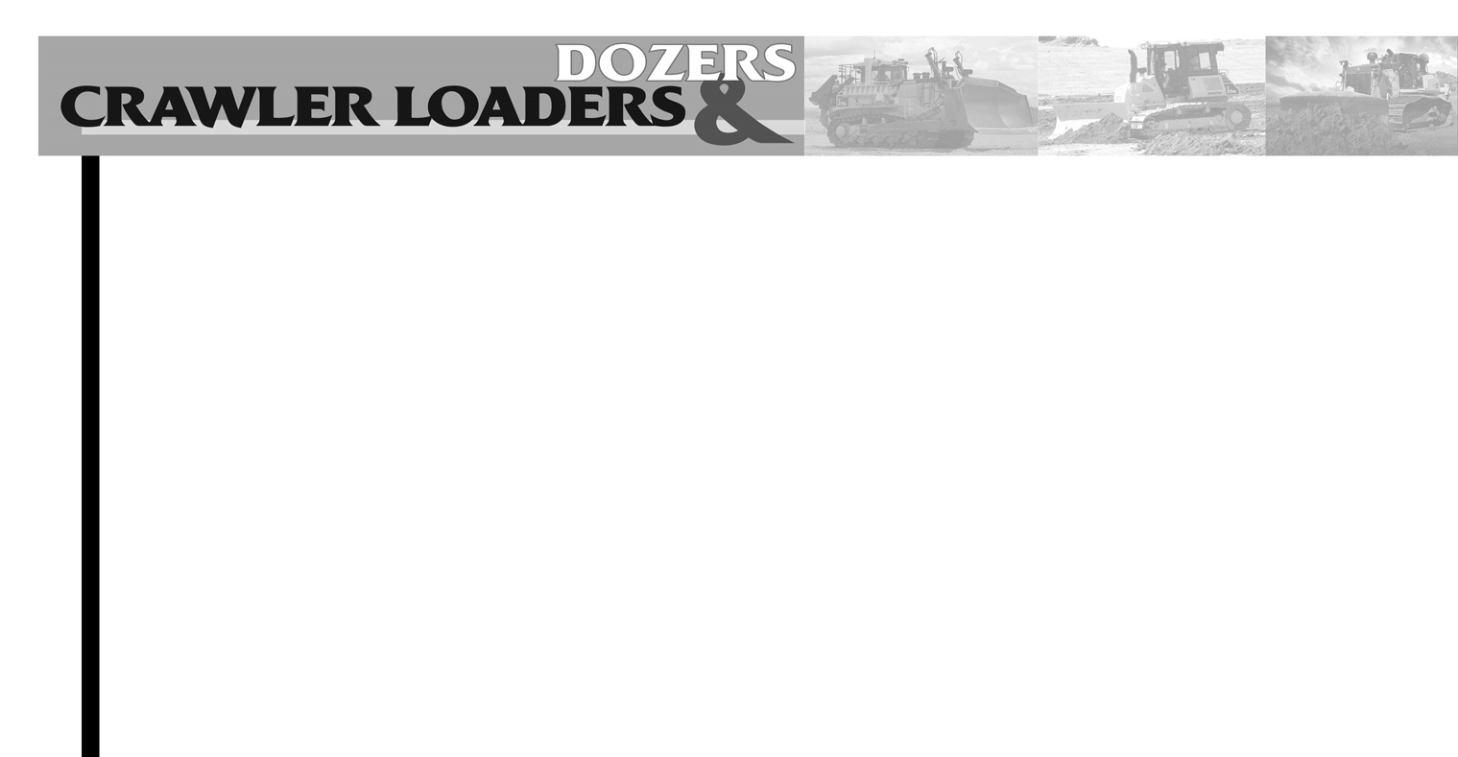
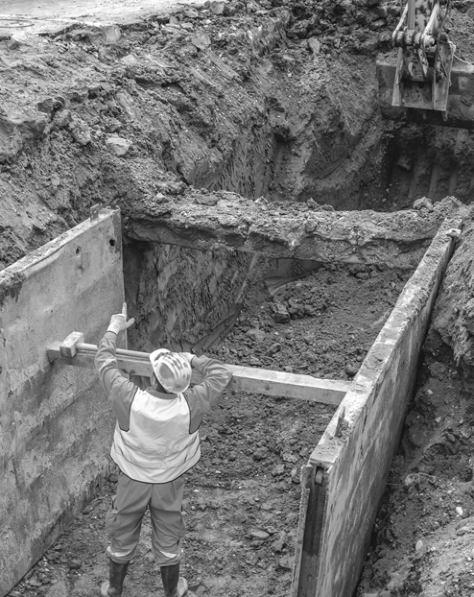
This year, the updated A10.12 excavation safety standard, Safety Requirements for Excavation, was approved. It details the design of an excavation plan and applies to all open excavations, including trenches. After 22 fatalities related to trenching were recorded, OSHA stepped up its excavation site inspection program.
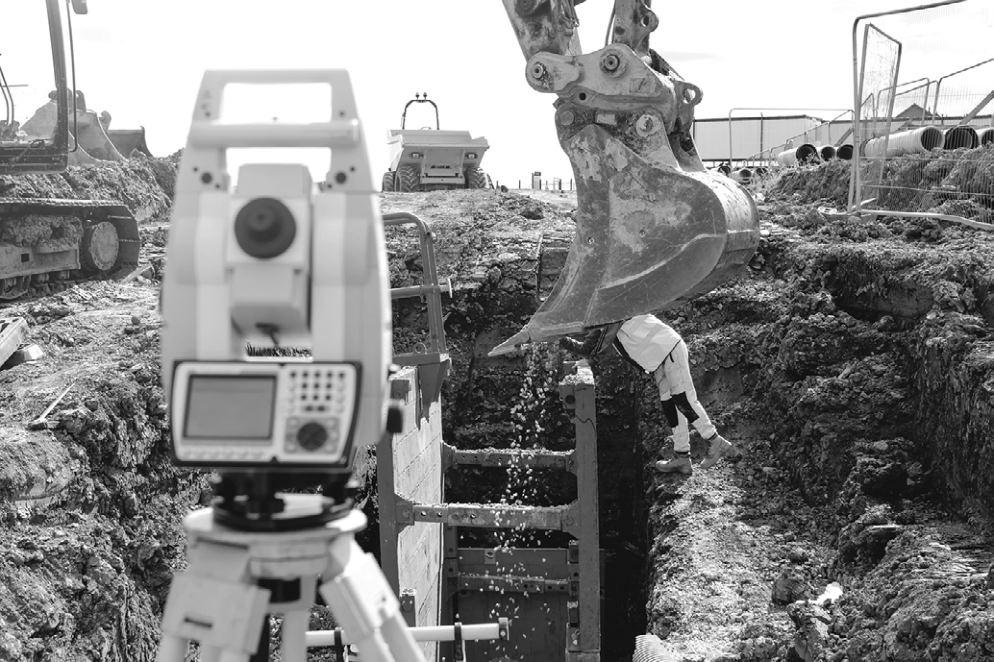
TRENCHING from page 1
OSHA called on all employers engaged in trenching and excavation activities to act immediately “to ensure that required protections are fully in place every single time their employees step down into or work near a trench.”
Doug Parker, assistant secretary for occupational safety and health, said in a matter of seconds workers can be buried under thousands of pounds of soil and rocks in an unsafe trench.
He wants to see the increase in the number of workers needlessly dying and suffering serious injuries in trenching incidents stopped.
“Every one of these tragedies could have been prevented had employers complied with OSHA standards,” said Parker. “There simply is no excuse for ignoring safety requirements to prevent trench collapses and cave-ins.”
The agency reported that 22 deaths in the first half of 2022 surpasses the total of 15 in 2021.
In June, two workers aged 20 and 39 died in Jarrell, Texas, when the unprotected trench more than 20 ft. deep collapsed upon them as they worked.
OSHA noted that trench shields sat unused beside the excavation. This incident prompted the agency to announce the enhancements.
To stress the dangers of disregarding federal workplace safety requirements, OSHA enforcement staff will consider every available tool at the agency’s disposal, said the agency.
“These actions will place additional emphasis on how agency officials evaluate penalties, including criminal referrals for federal or state prosecution to hold employers and others accountable.”
OSHA compliance officers will perform trench inspections nationwide and may stop by and inspect any excavation site during their daily duties.
Industry Gives Its Blessing
The National Utility Contractors Association (NUCA) marked this year’s Trench Safety Stand Down by reinforcing the idea that safety training is key to an employee’s daily activity.
The association believes safety training also is critical to a well-functioning utility construction job site.
“Time and time again, evidence shows that the key to significantly reducing the risks associated with our industry is employee training and reinforcement,” said Mike Flowers, NUCA’s director for safety, training and education.
This year, according to the association, 23,000 workers employed by 345 companies on 1,978 job sites participated in a stand down training event the week of June 20 to 24.
The goal of the event is to provide those who work in and around trenches and excavations with information about current excavation requirements and safety procedures.
OSHA and the North American Excavation Shoring Association (NAXSA) joined forces to host the Colorado Trench Safety Summit in early October.
The free event included classroom training, roundtable discussions and live demonstrations.
A similar event took place in Southlake, Texas, with the North Texas NUCA chapter in September.
Early this year, ANSI announced approval of the updated A10.12 excavation safety standard, Safety Requirements for Excavation.
The standard details how to design an excavation plan, including responsibilities, training and duties, assessing underground utilities, water accumulation and stability of adjacent structures and protecting workers from falls, cave-ins and confined spaces.
It applies to all open excavations, including trenches, made in the earth’s surface that require worker and/or property protection.
Defining Trench Safety
NUCA reported that OSHA’s standard 1926.650, Subpart P on trenching and excavation requires protective systems for trenches that are 5 ft. or deeper.
The federal agency warns that trench collapses are rarely survivable because a cubic yard of soil can weigh as much as 3,000 lbs.
“Trench hazards are well-known,” said OSHA, “yet far too many workers continue to be injured or killed during excavation work.”
The agency believes trench collapses, or cave-ins, are more likely than other excavation-related incidents to result in worker fatalities.
“It only takes seconds to become buried in thousands of pounds of soil.”
But trench hazards can be controlled when employers act responsibly, train employees and follow federal standards.
OSHA lists steps contractors can take to keep excavation work safe: • Ensure there is a safe way to enter and exit the trench; • Trenches must have cave-in protection — remember to Slope, Shore, Shield; • Keep materials away from the edge of the trench; • Look for standing water or other environmental hazards; and • Never enter a trench unless it is properly inspected
The National Institute of Occupational Safety and Health (NIOSH) warns that working in an unprotected trench is dangerous.
ARK ANSA S
A L M A T R A C T O R & E Q U I P M E N T 479-632-6300 doosandealers.com/Alma
L I F T T R U C K S E R V I C E S 501-568-3330 doosandealers.com/Little-Rock
FLO RIDA
B O B C A T O F J A C K S O N V I L L E 904-288-9181 doosandealers.com/Jacksonville
C O A S T A L M A C H I N E R Y 850-944-2002 doosandealers.com/Pensacola
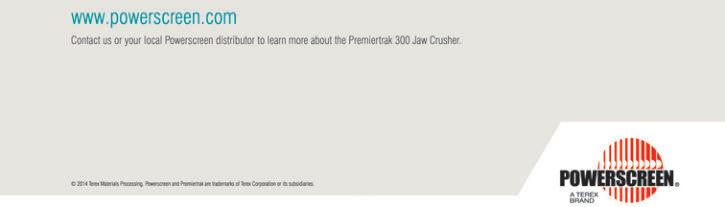
S Y N E R G Y E Q U I P M E N T 386-274-1002 doosandealers.com/Daytona-Beach
239-334-4987 doosandealers.com/Fort-Myers
305-362-6632 doosandealers.com/Miami
407-273-7383 doosandealers.com/Orlando
954-256-0583 doosandealers.com/Pompano-Beach
561-264-3287 doosandealers.com/Stuart
813-626-3470 doosandealers.com/ Tampa
TENNE SSEE
B O B C A T O F C L A R K S V I L L E 931-436-9555 doosandealers.com/Clarksville
B O B C A T O F N A S H V I L L E 615-941-4000 doosandealers.com/Nashville North Carolina, South Carolina, Virginia, West Virginia Powerscreen Mid-Atlantic, Inc.
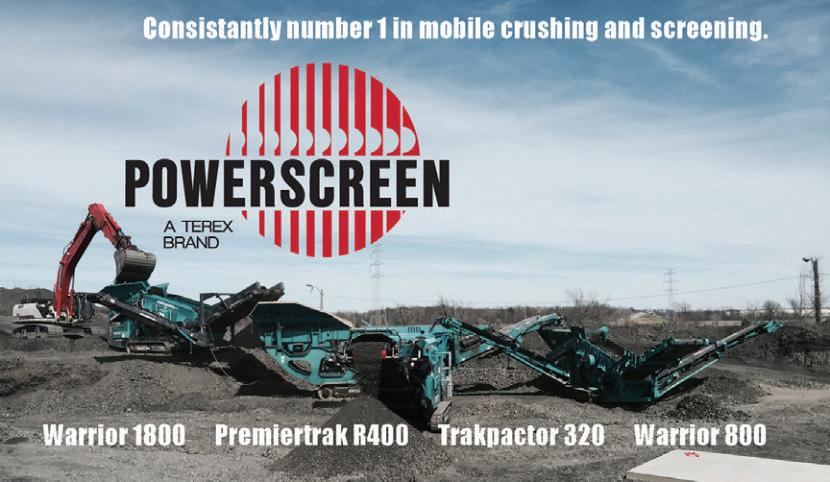
PO Box 2505 • Kernersville, NC 27285 Tel: 800-797-7276 Web: www.powerscreenmidatl.com
Most Material From Blasting, Drilling Operations Becomes Fill for Project
VDOT from page 32
Some 60 percent of the project contains solid rock, with the rest being a mix of clay and sandy soil. Blasting of the rock is going as expected. Humphreys noted, “Most of the material we remove will be used as fill for the new roadway.”
Workers have been vigilant with the blasting and drilling so as not to disrupt normal traffic. They also have been careful with the 400 acres of land they impact.
“Our people are trying to disturb no more than what is needed,” said Humphreys. “Trees that are being removed are being salvaged as timber, turned into firewood or mulch. We have also modified the design of the project so that we dislodge less land than we had originally estimated.”
Reducing the impact on the land means less effect on streams as well. Still, the project has made careful plans for streams and stormwater.
“Before constructing the road, we will be placing large diameter culverts for handling the existing streams,” said Humphreys. “Twenty-nine new stormwater management basins will handle normal rains and runoff. They help remove silt and earth from storm waters so it can return to the groundwater cleaner than it might if unfiltered.”
Unlike paving, the excavation can be done nearly year around. But weather does present issues in this mountainous terrain.
“We try to work on top of the mountain and at times are shut out because it’s foggy and icy,” said Humphreys. “Then we move our team to the other end of the job and it’s clear and sunny.”
Safety is a priority for the team. Full-time safety personal and traffic maintenance people are assigned to the site and a project safety committee monitors the work regularly.
The attention to safety is essential with the prevalence of large pieces of equipment rumbling around the project and active blasting operations. The finished project is hard to envision as project completion is still a long way off. Humphreys is confident though that the finished product will be satisfying for motorists and truckers.
At present, Branch is using a Cat 385 excavator, two Cat 374 excavators, Cat D8 and D10 dozers and Cat 45-ton articulated dump trucks for the earthwork, supported by a fleet of smaller pieces. Efforts are also under way to mobilize 100ton rigid frame trucks and an appropriately sized excavator for upcoming earthwork.
Shannon Valentine of the VDOT at project inception, agreed about the significance of the project.
“Every year thousands of commuters, travelers and truckers take Route 58 as they travel along our Commonwealth’s southern border. The project represents a continuation of a multi-decade investment in the people and communities of rural and southwest Virginia.” CEG (All photos courtesy of Branch Civil.)
TRENCHING from page 58
The walls can collapse suddenly and without warning. When this happens, workers do not have time to move out of the way.
“A small amount of dirt may not seem dangerous, but can weigh more than 3,000 pounds — the weight of a compact car,” said the organization. “This small amount of dirt is enough to fatally crush and suffocate workers.”
Like OSHA, safety experts at NIOSH warn that “workers should never enter a trench that does not have a protective system in place.”
The protective system should be designed and installed by a competent person, someone who can identify hazards and is authorized to correct them.
Competent person training is available from many sources, noted NIOSH, including insurance companies, trade associations, labor unions and equipment manufacturers.
The best way to prevent trench collapse and trenching fatalities is to use other methods, when possible, said NIOSH.
Some options include directional boring, relining the pipe, pipe ramming and utility tunneling and pipe jacking.
Robots can be used on construction sites to transport, line and join large pipes to protect workers from serious injuries.
Robots may also reduce the need for pipe layers and other helpers to work at the bottom of the trench, according to the organization.
Trenches must be inspected by a knowledgeable person, be free of standing water and atmospheric hazards and have a safe means of entering and exiting prior to allowing a worker to enter.
“OSHA stands ready to assist any employer who needs help to comply with our trenching and excavation requirements,” Assistant Secretary Parker added. “We will conduct outreach programs in all of our 10 regions to help ensure any employer who wants assistance gets it. The stakes are too important.”
In fact, OSHA’s On-Site Consultation Program for small- and medium-sized businesses will help address trench-related illnesses and injuries in workplaces.
The agency also urges workers to contact their local OSHA or state plan office if their employer requires working in or beside trenches that are not sloped, shored or shielded, and are 5 or more feet deep.
Additional Advice
Caterpillar dealer Blanchard Machinery warns that the fatality rate for excavating is 112 percent higher than general construction.
“Trenching is a dangerous job,” said the West Columbia, S.C.-based, company. “But you can protect yourself and your team from injury with the right precautions. Anticipate the risks before they become hazards and be proactive with these trench safety tips.” • Understand proper trenching practices
Blanchard reiterates that the site manager should implement trenching techniques based on soil, trench dimensions and other site-specific factors.
“Never work in a trench without supporting the sides with a trench box, shoring, or combination of sloping and benching methods,” said Blanchard. • Follow site-specific trenching safety guidelines
Every work site is different, noted the company.
“Account for environmental and atmospheric conditions, soil type, trench dimensions and the work you’re doing in creating site-specific safety guidelines.”
According to Blanchard, these rules should be safety standards across all trench settings. Never enter a trench with standing water or accumulating water without taking proper precautions to drain and prevent more flow. Workers should not work underneath suspended loads handled by heavy machinery. All trenches require safe and separate entry and exit points.
Minimize the chance of falling debris and struck-by injuries by keeping materials and equipment at least 2 ft. away from the trench edge and using retaining devices as needed.
Always stay aware of your surroundings and implement visual and audible warning systems like signs and alarms to know when equipment is in use or nearby. • Test and inspect trenches regularly
Trenches must be inspected before work begins each day to check for hazardous fumes, oxygen levels, water accumulation and environmental changes.
The inspector should reinspect trenches after environmental changes and natural events, like nearby blasting work or heavy rain. • Know the soil, environment
Soil type and quality are some of the most significant factors to consider when designing a trench.
Always conduct utility line tests before trenching. Mark gas, electrical, water and other lines with correct signage and barriers before operating any equipment.
“Failure to do so could result in injury and costly damage or fees,” warns Blanchard.
Plus, a competent person should conduct atmospheric testing in all trenches 4 ft. or deeper to ensure proper oxygen levels. Also, sites should have emergency rescue equipment available at all times, according to the Cat dealer. • Use a trench box — but don’t rely on
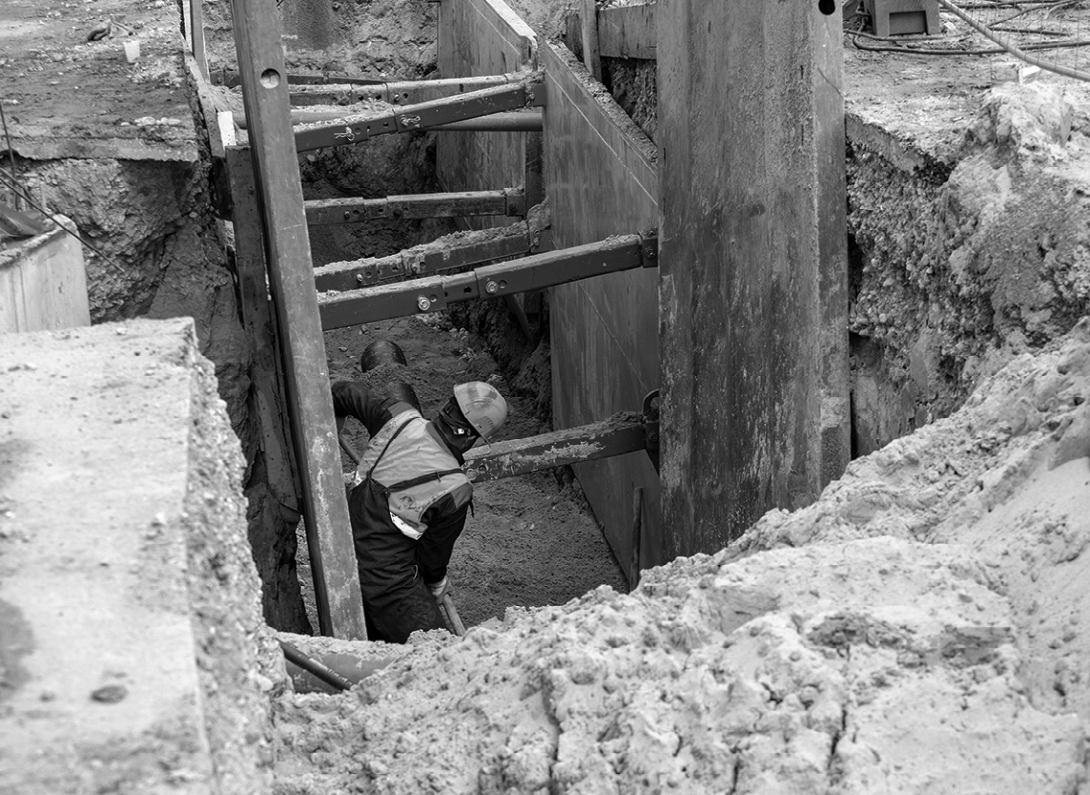
Prior to allowing a worker to enter, trenches must be inspected by a knowledgeable person, free of standing water and hazards and have a safe means of entering and exiting.
it
Trench boxes are in place to protect workers in the event of a cave-in and cannot always prevent the cave-in itself.
Proper barrier placement should include shoring and worker barriers with enough force to be greater than the force coming from the trench walls.
Avoid using trench boxes for greater depths than the manufacturer has rated them for and never work inside a damaged barrier.