
7 minute read
CATERPILLAR GC Series Vibratory Soil Compactor
Page 52 • May 19, 2021 • www.constructionequipmentguide.com •Paving Section • Construction Equipment Guide Cat GC Series Single Drum Vibratory Soil Compactors Deliver Simple Ops
Caterpillar expands its single drum vibratory soil compactor line with the introduction of the new 84-in. Cat GC Series, built for simple operation, high reliability and low cost-per-hour performance.
Offering high static linear load and more weight at the drum for enhanced compaction, the new series consists of the 10-tonne-class CS10 GC, 11-tonne CS11 GC and CP11 GC, and 12-tonne CS12 GC and CP12 GC. With both smooth (CS) and padfoot (CP) drum models available for compaction of granular and cohesive soils, the new models deliver reliable performance for road building, site preparation, large residential construction, large earth fill and agriculture applications.
The new GC Series is powered by the 120.7 hp (90.0 kW) Cat C3.6 diesel engine that meets stringent U.S. EPA Tier IV
Final / EU Stage V emission standards. Standard Eco-Mode operation reduces engine speed to 2,000 rpm to deliver up to 10 percent fuel savings over operation at high idle. The engine’s long oil and filter change interval helps to lower service time and costs.
Easy-to-select speed control offers one-button switching from working to travel speed. The compactors’ single propel pump with limited slip differential rear axle deliver expectation-exceeding gradeability up to 55 percent for the 10- and 11-tonne models and up to 50 percent for 12-tonne models.
All compactors feature a low overall 9.8 ft. (3 m) height plus improved tie-down locations for fast, low-cost transport that meets market regulations.
Simple, Comfortable Operation
quickly change from high to low amplitude. Additional XT weight kits and padfoot shell kits for CS smooth drum models increase machine flexibility. Weight kits for the CS10 GC and CS11 GC replace the front bumper and add weights under the yoke tube of the CS 11 GC to bump each model up to the next weight class, expanding application capabilities. The same B Series shell kit design converts GC Series smooth drum compactors into a padfoot drum roller, allowing these machines to efficiently compact cohesive soils as well as granular. Simplified controls and operation allow even the most inexperienced operator to quickly learn GC compactor operation. Digital readouts offer a quick glance of critical operating data and are customizable for operator preference. All main controls are located on the right-side console for easy access and include propel lever with vibration control, engine throttle and Eco-Mode selection, and emergency stop and parking brake. Standard auto-vibe automatically starts/stops machine vibration based on propel lever position to prevent compaction while not moving. The new GC Series offers improved operator platform ingress/egress with angled steps, anti-skid entrance and conveniently located handrails. Ergonomically grouped controls deliver efficient operation, while an iso-mounted operator station with rubber floor mat minimizes vibration feedback to reduce fatigue. Machine design delivers increased visibility around the The new GC Series is powered by the 120.7 hp (90.0 kW) Cat C3.6 compactor, allowing the operator to quickly diesel engine that meets stringent U.S. EPA Tier IV Final/EU Stage V see work area obstructions without strainemission standards. ing. Internal and external mirrors provide added visibility and the optional rear vision camera further expands the operator’s view toward the rear of the machine, allowing the operator to quickly see the work area without obstructions or straining.
Convenient Service, Technology
The reliable new Cat GC Series of soil compactors feature industry-leading service intervals to lower maintenance costs and keep the machines on the job. Both hydraulic oil and eccentric housing oil boast a 3,000-hour/3-year change interval, and the engine oil and filter are changed at 500 hours. The articulation joint and battery are both maintenance-free. Compactor design offers convenient access to the hydraulic oil tank, filter and S·O·SSM oil sampling ports without lifting the hood.
Proven Cat Performance, Flexibility All rollers come standard with Product Link Elite that cap-
The new GC vibratory soil compactors feature the Cat tures critical operating data, monitors machine health, and exclusive pod-style vibration system, providing a long 3- provides service reminders and fault code alerts to improve year/3,000-hour service interval for reliable operation. fleet management. A host of optional scalable technologies Providing more weight at the drum than the B Series, these are available for the new GC Series, including Machine new models offer high compaction performance. Dual Drive Power, Compaction Meter Value, mapping and amplitude and frequency increase compaction versatility of machine-to-machine communication. the new line, and a single button allows the operator to For more information, visit www.cat.com. DOBBS EQUIPMENT
(844) 4 MY DOBBS www.dobbsequipment.com Riverview, FL (Main Office) (813) 620-1000
Fort Myers, FL (239) 334-3627
Lutz, FL (813) 995-0841
Miami, FL (305) 592-5740
Orlando, FL (407) 299-1212
Pompano Beach Parts, FL (954) 977-9541
Riverview Parts, FL (813) 621-4902
Sarasota Parts, FL (941) 960-2004
West Palm Beach, FL (561) 848-6618
REYNOLDS-WARREN EQUIPMENT CO.
www.reynoldswarren.com 1945 Forest Parkway Lake City, GA 30260 (800) 875-5659 (404) 361-1593
180 Thunderbird Drive Richmond Hill, GA 30324 (912) 445-2880
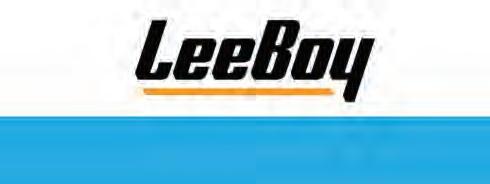
TUNNEL from page 41
Branscome immediately rerouted its empty dump trucks onto the opposite lane of the tunnel, exiting the lane on a ramp before the barrier closing the road to the public. This contingency plan enabled the paving operation to continue, although at a reduced rate, until the accidents in the other tunnel were cleared.
The completed project, approximately 1 mi. in each direction, required milling the top 2 in. of deteriorated asphalt and replacing it with fresh asphalt produced at Branscome’s asphalt plant located just over one mile from the project. VDOT paid Branscome $1.5 million for the completed job.
The mix design allowed 15 percent of the
road to be recycled materials. Workers used approximately 4,000 tons of asphalt for the project.
The job required workers to contend with numerous obstacles. In addition to working in the tight confines of a tunnel, which restricted the flow of the construction, Branscome workers had to work around manholes, curbs and iron stormwater drains without causing damage.
“Another consideration was the physical layout,” said Jacobs. “The contractor had to store the equipment at either end of the tunnel and had just two lanes to move equipment and bring trucks to deliver asphalt.”
The tunnel’s road surface was 100 ft. below the water at its deepest point, allowing massive ships to pass overhead. Being that far underwater meant that stormwater drains were critical and could not be damaged.
These challenges were different from a typical interstate paving project.
“The contractor covered the stormwater drains with steel plates during asphalt milling removal and asphalt placement operations,” said Lance Eller, VDOT’s construction manager of Hampton Roads District. “A vacuum truck was available to clean all storm drains after asphalt placement and to ensure debris removal. During removal operations, the contractor utilized jackhammers, skid steers with milling head attachments and pickaxes to ensure the asphalt was removed as needed. During placement operations, asphalt was feathered down with shovels and rakes to ensure proper drainage in all areas.”
Despite the painstaking manual labor, Branscome workers completed paving on the first weekend seven hours early and the second weekend 18 hours early. This enabled VDOT to shut down early the extensive detour some drivers had to take over the James River Bridge or through the Hampton Bridge-Tunnel.
The Branscome team also balanced their work amid COVID restrictions. Workers had little problem maintaining social distancing for much of the work. But crucial meetings usually held onsite transferred to virtual meetings to minimize exposure. This was especially important since an outbreak could have imperiled the team’s tight deadlines to finish paving and return the tunnel to normal traffic. Masks, sanitizing stations and wipes were used as needed during the project operations.
Naturally, projects of this complexity require cooperation between trucking, asphalt plant operations and subcontractors, which included Richmond Traffic Control, McGowan Group and Commercial Power Sweeping.
“I believe the planning process and teamwork were key reasons the project was so successful,” said Sidney Hazelwood, project manager of Branscome. “We had buy-in from all team members and subcontractors. We had a solid plan that everyone understood, and we were able to execute that plan flawlessly both weekends.”
With traffic now back to normal in the tunnel, the VDOT and Branscome team saw the teamwork pay off.
“Frankly, I was surprised that the project could be completed in only two weekends,” said Eller. “I was also impressed by the quality of the work achieved by Branscome and the great communication between the two teams. It was a once in a career project.” CEG
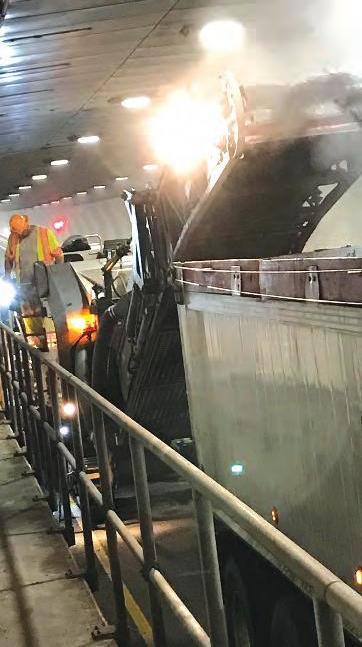
The milling in the tunnel was performed in tight quarters. The milling and paving were restricted by the confines of the tunnel.

