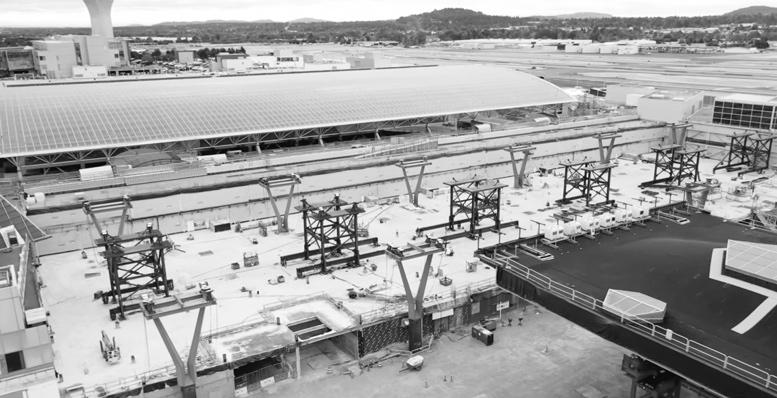
1 minute read
Crews Construct, Transport Wood Roof Pieces One By One
ROOF from page 1 pedestrians, the installation of the roof panels could begin. Each panel, referred to as a super cassette, was installed using stationary skidding propelled by strand jacks and lowered with the skidding jacks onto column isolators.
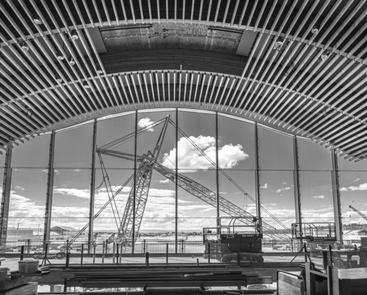
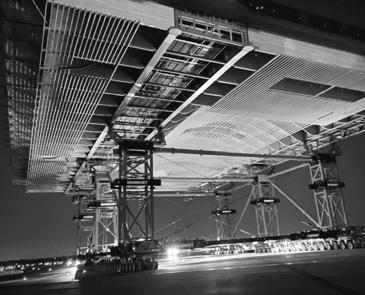
The next set of panels were then rolled into position down the bottom flanges of the previously set panels. The panels were safely secured with consideration for potential elevated wind and project specific seismic requirements before the public were allowed to reoccupy the area below.
A major complexity of the project was the wood material used in the roof panels’ construction. Deflection of the roof panels was a major concern of the client and the roof designers, so at each point in the jacking, transport and installation process, deflection of the roof was monitored and kept within stringent criteria.
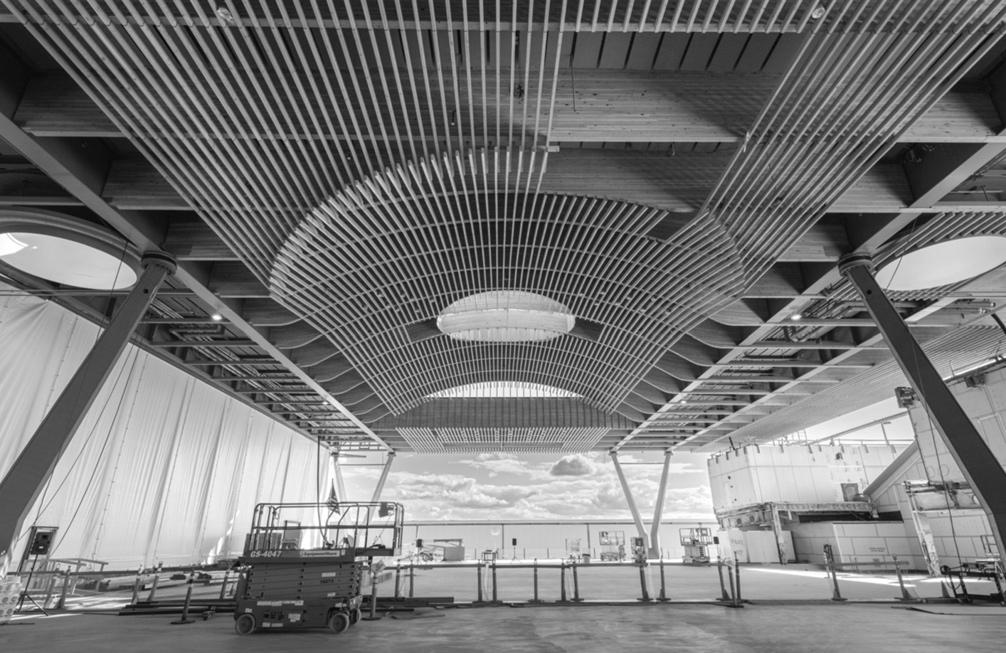
Only the super cassette pieces had steel girders in the longitudinal direction to support the 82-ft. wooden arches and to allow the panels to be “launched” using stationary skidding equipment. Also, the supports for the launching jacks were temporary towers supported by wooden piles, which were installed in the 1950s.
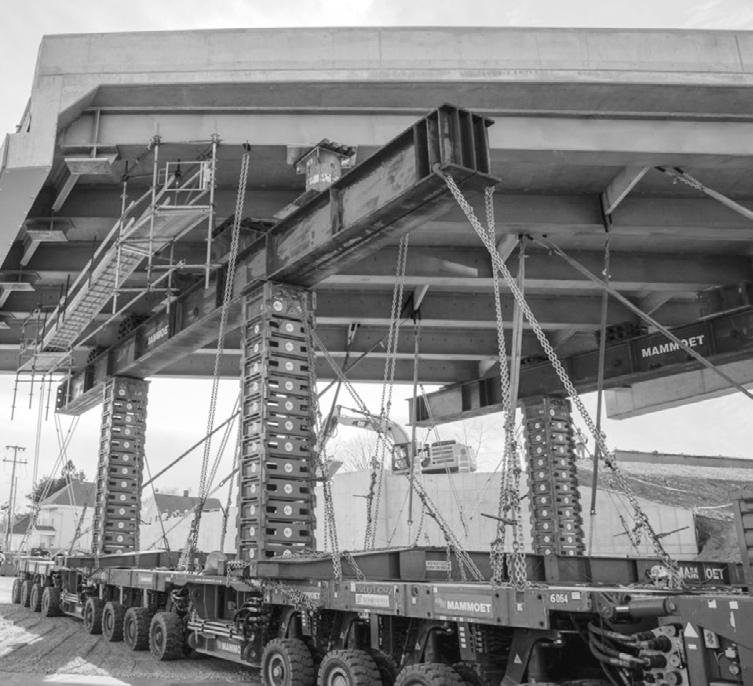
To mitigate any issues, Mammoet performed extensive friction testing in its Rosharon, Texas, yard prior to execution to ensure no structural damage occurred to a mockup roof panel and that the design values presented to the client for strand jack anchoring were realistic. When executing the job on site, Mammoet closely monitored the loads and deflections to ensure that they were in line with the tested values.
(All photos courtesy of Mammoet.)
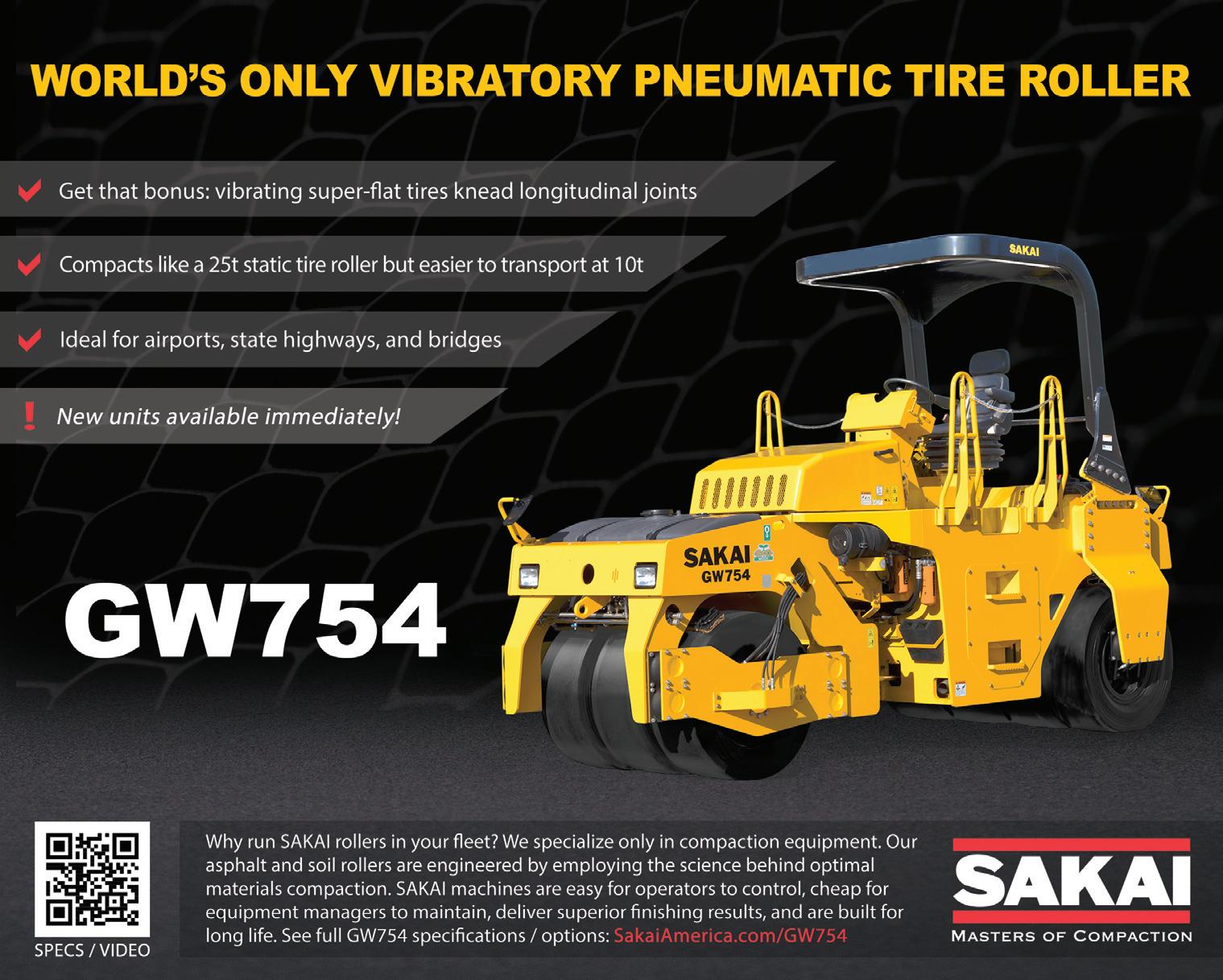