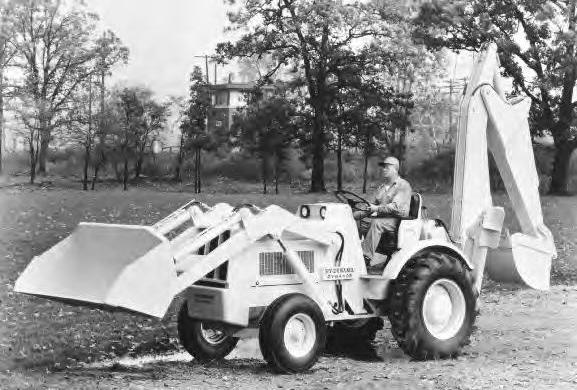
22 minute read
THE DYNAMIC DYNAHOE! TRACING THE HISTORY OF THE DYNAHOE
Keith Haddock Traces the History of the Dynahoe, One of the Largest Loader-Backhoes Ever Built.
The loader-backhoe is still one of the most popular and visible of all types of construction machines. It reigned as the mainstay of mechanized utility work over some twoand-a-half decades after first finding popularity in the 1950s. With the advent of miniexcavators, increased popularity of skid steer loaders, and an abundance of companies making compact-sized machines, the loaderbackhoe still survives. It possesses multitask capabilities not found in the competition, and often able to complete all tasks on small jobs with just the one machine. It’s able to do the excavating, loading, lifting, backfilling and cleanup, and when finished can take off by road to a nearby job without waiting for lowboy or trailer.
The Hy-Dynamic Company of Lake Bluff, Ill., was one of many companies entering the loader-backhoe market in the 1950s. In 1959 it introduced its first machine, the famous Dynahoe loader-backhoe, a machine quite different from anything else on the market. Competitive loaderbackhoes had originated as agricultural wheel tractors and were generally much smaller in capacity and lightly built. But the unique Dynahoe was heavily built from the ground up as an excavating machine, and the largest of its type on the market. The average loader-backhoe in the early 1970s had a digging depth from 14 to 17 ft., an 80-hp engine, and weighed 10 tons. In contrast, the largest Dynahoe boasted a digging depth of 20 ft., carried a 155-hp engine, and weighed 16 tons.
One of the first Dynahoe models was the Model A, which came equipped with a Continental F-244 gasoline engine developing 65 hp. The Model AD was also offered with 65-hp Continental HD-277 diesel engine. Maximum digging depth was 13 ft. and backhoe loading height 12 ft. Operating weight was just over 6 tons.
Hy-Dynamic certainly set out to produce something superior to anything else available. Even this early design from 1959 sported a neat efficient backhoe linkage, integrated design and massive frame. Of course this concept and philosophy resulted in a relatively high purchase price, and consequently the Dynahoe never sold in huge quantities throughout its production life. But it served a niche market for the contractor who wanted extra capacity, production and mobility.
In 1966 Hy-Dynamic upgraded its Dynahoe models and launched a new range of machines with a 3-digit nomenclature, the first two digits indicating digging depth in feet. Models A and AD were replaced by the model 140, and other models in the new lineup included the short-lived 120 and 130 (discontinued by 1968), and the larger 160. In 1968 the 190 and 200-4 models were added, the latter being a heavy 4-wheel drive model with four large equal-sized wheels, and a 20-ft. digging depth.
In 1971 Bucyrus-Erie Company acquired the Hy-Dynamic Corporation. The loader backhoes were continued as Bucyrus-Erie products and the well-respected Dynahoe name was retained. This acquisition came at a time when Bucyrus-Erie’s Construction Equipment Division was at the height of its activity, and demonstrated the company’s desire to capture all segments of that market. The acquisition provided BucyrusErie with a solid line of loaderbackhoe models 140, 160, 190 and 200-4. It also provided a line of rough-terrain, wheelmounted hydraulic cranes up to 18 tons capacity, introduced by Hy-Dynamic in 1966.
Soon after Bucyrus-Erie acquired the Dynahoe machines it upgraded the range to the B-series. Now all machines were equipped with GM Detroit diesel engines and featured advanced hydraulics and increased operating weights. The 140B was powered by a 90-hp, 3-cylinder Detroit 3-53 diesel engine with torque converter. The backhoe reached to 22 ft. at ground level and the loader bucket held 1 ¼ cu. yds. Machine weight was 14,800 lbs. This intermediatesized 160B carried the same 90-hp GM engine as the 140B but with digging depth increased to 16 ft. by interchanging the boom foot pivot and boom hoist cylinder pivot positions. The lower boom position achieved greater digging depth but reduced loading height by some 3 ft. Machine weight increased to 15,800 lbs. The larger 190B came with the same Detroit 3-53 diesel as in the 160-B, but rated higher at 95 hp. It was basically the same machine as the 160B but with deeper backhoe digging depth to 19 ft. and increased loading height to 12 ft. 9 in. Front loader capacity for both machines was 1 ½ cu. yds.
About the same time as the Bucyrus-Erie acquisition, the model 190-4, a 4-wheeldrive version of the 190, was introduced. Boasting four equal-sized wheels, it was powered by a 4-cylinder Detroit 4-53 diesel of 126 hp. As with the larger 4-wheel drive 200-4, steering on the 190-4 was provided to the rear wheels only and the front axle was free to oscillate. In operation the 190-4 weighed 22,750 lbs. including ROPS cab and supported a standard loader bucket of 1 ¾ cu.yds.
The Dynahoe 200-4 became the 200-4B under the Bucyrus-Erie banner. With an operating weight of 32,300 lbs. including ROPS cab it was the largest Dynahoe model. It carried a GM Detroit 4-71 diesel engine of 162-hp and could achieve a top road speed of 18 mph. The standard loader bucket carried 2 ¼ cu. yds. and the backhoe could pick
up a load of 11,600 lbs.
In 1973 Bucyrus-Erie closed the Lake Bluff, Ill., plant and transferred Dynahoe manufacture to existing B-E plants at Evansville, Erie and South Milwaukee. Although not selling in huge quantities like the smaller competitive machines, the Dynahoe continued to serve a niche market and garnered sufficient customers to keep the machines in Bucyrus-Erie’s product line until the company decided to dismantle and sell its entire Construction Equipment Division in 1985.
From 1974 the popular 4-wheel-drive Dynahoe 190-4 loader-backhoe was sold in the United Kingdom by Ruston-Bucyrus Ltd. of Lincoln. Sold as an R-B machine, its specification was identical to the American model except for a Ford 2715E diesel engine developing 108 hp replacing the Detroit engine. However, sales were discontinued in 1979, likely as a result of stiff competition from lower-priced, home-built machines and the onslaught of competition from smaller hydraulic excavators.
In 1985 manufacturing rights and designs of the Dynahoe were sold to Northwest Engineering Co. of Green Bay, Wis., and a group of former company employees established a new company, Bucyrus Construction Products (BCP) in Erie, Pa. The following year Northwest Engineering Co. became Terex Corporation.
After purchasing the Dynahoe line in 1985, Northwest Engineering/BCP continued to build the 190 and 190-4 until new models were introduced in 1987 under Terex. These were the 290 (109 hp and 20,700 lbs. weight) and the 490 (127 hp and 24,850 lbs weight). The new 290 and 490 were basically upgraded versions of the former 190 and 190-4 models, possessing similar specifications, Detroit engine, torque converter, and digging depth to 19 ft. In the late 1980s Terex Corporation shuffled its various divisions and BCP became an affiliate of Koehring Cranes & Excavators, another Terex division. In 1990, as a final grasp for market share, BCP upgraded its two Dynahoe models to the 290K and 490K. These were almost identical to the previous models except that John Deere engines of 110 and 121 hp provided power. Unfortunately sales continued to dwindle and the last Dynahoe was shipped from the factory in 1993.
Keith Haddock photo
The Dynahoe Model A was one of Hy-Dynamic Company’s first loader-backhoes. The Model AD was a similar machine, but powered by a diesel engine. About the HCEA
The Historical Construction Equipment Association (HCEA) is a 501(c)3 non-profit organization dedicated to preserving the history of the construction, dredging and surface mining equipment industries. With approximately 3,800 members in 25 countries, its activities include publication of a quarterly educational magazine, Equipment Echoes, from which this article is reprinted with permission; operation of National Construction Equipment Museum and archives in Bowling Green, Ohio; and hosting an annual working exhibition of restored construction equipment. Its 2018 show will be Aug. 24 to 26 at the Le Sueur Pioneer Power Show, Le Sueur, Minnesota. Individual memberships within the USA and Canada are $35 for one year, $65.95 for two years and $99.95 for three years, and $45.00 U.S. elsewhere. HCEA seeks to develop relationships in the equipment manufacturing industry, and offers a college scholarship for engineering and construction management students. Information is available at www.hcea.net, or by calling 419-352-5616 or e-mailing info@hcea.net.
(This story also can be found on Construction Equipment Guide’s website at www.constructionequipmentguide.com.)
Construction Equipment Guide• Backhoes & Attachments Section• www.constructionequipmentguide.com • August 4, 2021 • Page 73 Deere Improves Performance With L-Series Upgrades
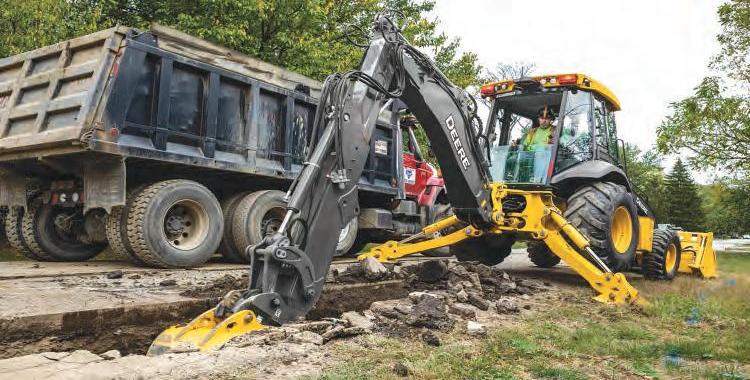
One of the most notable updates, the 310L, 310SL, 315SL, 310SL HL and 410L models are now equipped with a 4.5L John Deere PowerTech EWL engine, increasing power, improving torque and providing greater reliability.
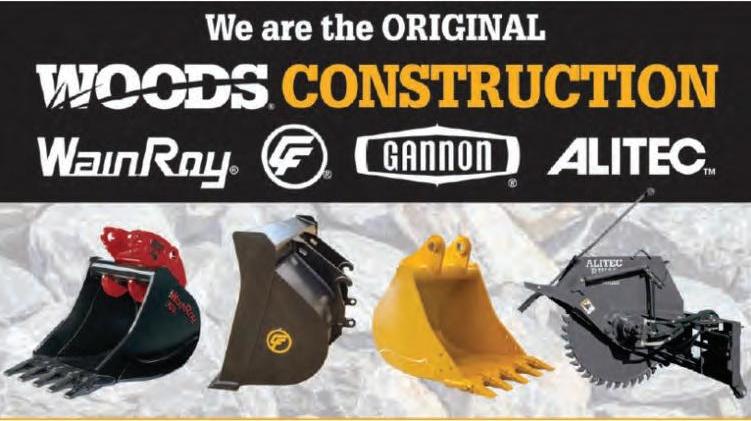
Get what you ask for!
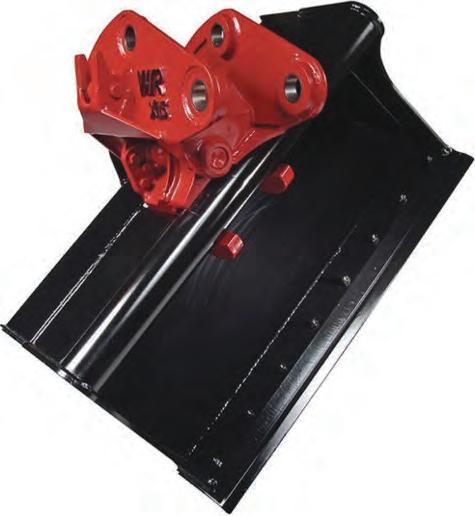
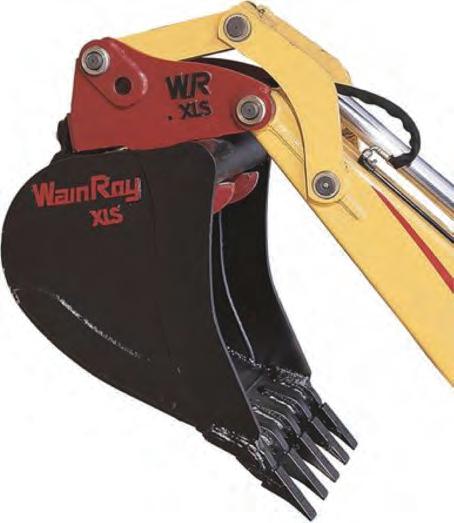
John Deere upgraded its L-Series backhoe loaders, unveiling significant machine improvements designed to boost productivity, maximize uptime and reduce operating costs.
Ranging across the L-Series Backhoe lineup, the updates, which include engine upgrades, new pressure-compensated loadsensing (PCLS) hydraulics on the 310SL model and machine control improvements, enhance operation and machine performance.
One of the most notable updates, the 310L, 310SL, 315SL, 310SL HL and 410L models are now equipped with a 4.5L John Deere PowerTech EWL engine, increasing power, improving torque and providing greater reliability. This Final Tier IV engine results in a boost in horsepower across the models, while the removal of the exhaust gas recirculation system and components improves reliability, according to the manufacturer.
The redesign also includes improved filter locations for easier access when changing or servicing fuel and diesel exhaust fluid filters. Additionally, the 310SL is now available with PCLS hydraulics.
Already offered on the 310SL HL, 410L and 710L, the PCLS system results in increased productivity and improved backhoe controllability at any engine speed. In addition, trenching operation can be conducted at lower engine rpm, reducing fuel consumption and lowering job site noise.
“We are committed to continuously improving our equipment to offer our customers more value out of their machines,” said Brian Hennings, product manager, John Deere Construction & Forestry. “With these upgrades, we are directly addressing our customers’ needs. These upgrades build upon the best features found on the L-Series machines, resulting in a lineup designed to power through the toughest jobs.”
The 310SL is now equipped with Lift Mode. When enabled, it automatically sets the engine speed to 1,400 rpm and increases max hydraulic pressure to 4,000 psi, for up to a 10 to 15 percent increase in backhoe lift capacity. Additionally, buttons for the horn, selective flow, auxiliary proportional roller and extendable dipper stick have been integrated into the backhoe pilot controls, improving ease of use.
Now available as a base offering on the 310SL, 315SL, 310SL HL, 410L and 710L models, AutoShift technology automatically adjusts the transmission to the most appropriate gear for an enhanced operator experience. Additionally, the five models now feature Auto Ride Control as the only ride control option, eliminating the need to manually turn on and off during load and carry applications. Auto Ride Control enhances ease of use, improves ride quality and reduces front bucket material spillage.
Other key features include an LED boom light kit for increased visibility to the bottom of the trench and a redesigned loader lever linkage that reduces resistance and improves its throw and feel.
The 310L EP model includes updates designed to deliver more value at an economical price. Key changes to the 310L EP include a simpler front-axle design and a four-speed manual synchromesh transmission. Directional changes remain controlled with a steering column mounted lever for forward, neutral and reverse.
For more information, visit www.deere.com/.

AVAILABLE FOR ALL MAJOR OEM MACHINES
Buckets
Digging, Ditching, V-Rock, Skeleton, Slab Thumbs
Rigid, Hydraulic, Main Pin, Progressive Link Couplers
Rigid, Manual, Swinger, Hydraulic, Jump Latch Grapples
From 1.5MT to 560MT Class Machines
Get what you pay for!
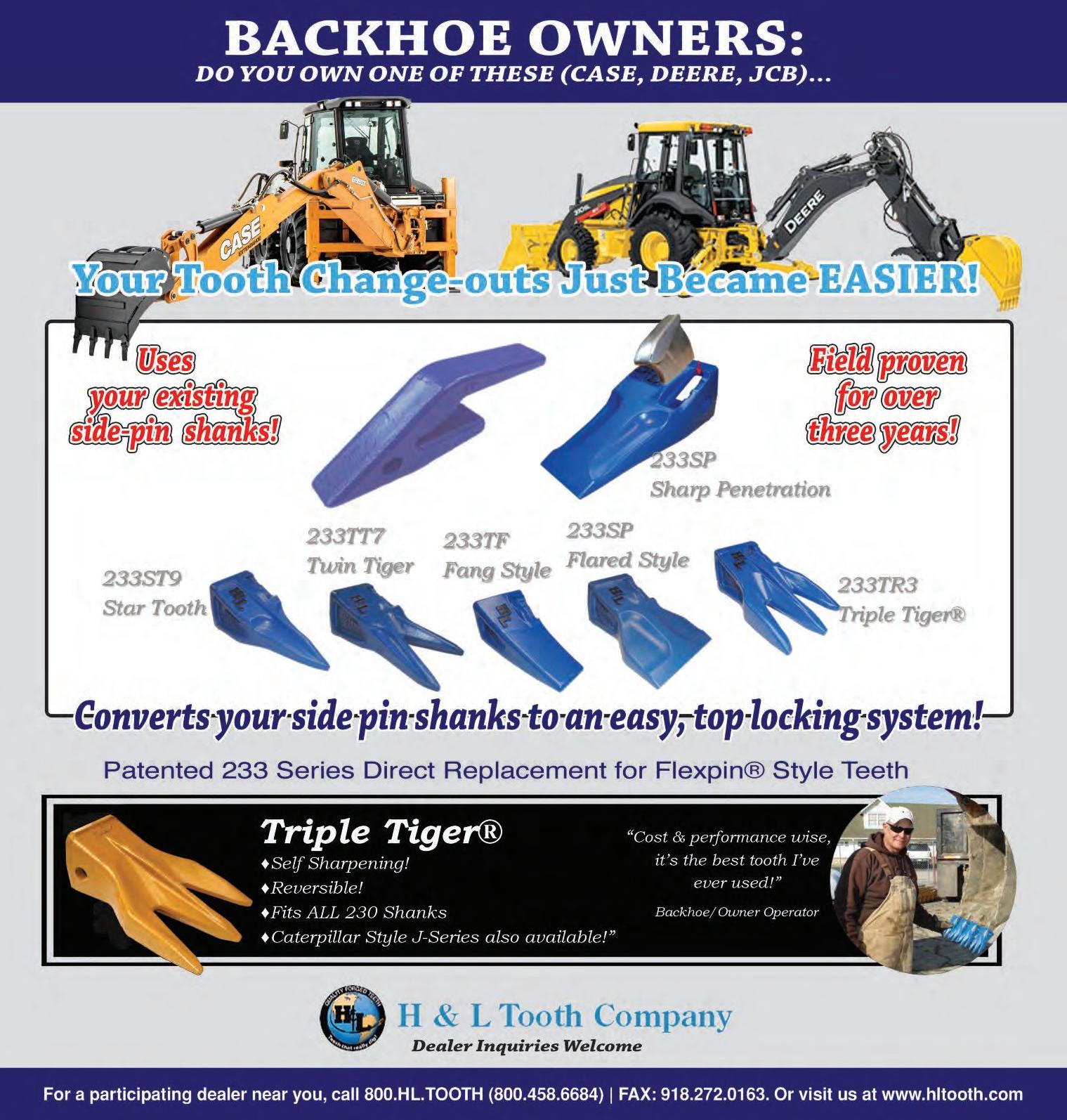
OSHA from page 1
ship, store or handle hazardous materials, but construction employers may face new burdens, cautioned Sparkman.
Contractors “may have new compliance obligations from some materials now being classified as ‘hazardous’ or managed in a different hazard class, resulting in new program, training and communication obligations.”
The amendments seek to modify certain hazard classes, conditions for labeling and language used on safety data sheets (SDS). Updates to the HCS classification and labeling framework, for consistency with more recent versions of GHS, are also proposed.
“OSHA’s proposed HCS amendments have the potential to affect many products used on construction sites, including aerosolized products and products in small containers, as well as alter some chemical product labels and SDSs,” said Sparkman in an article in EHS Today.
One major amendment proposes to revise criteria for the classification of certain health and physical hazards, including unstable gases, non-flammable aerosols, skin corrosion, or irritation, eye irritation and aerosols, generally.
Sparkman pointed out that the proposed amendments also would create a new hazard class for desensitized explosives.
If this happens, contractors will need to ensure proper product classification, and update their written programs, SDS and training materials to comply.
Attorneys Cressinda Schlag and Kelli Morgan Dreger of the Jackson Lewis law firm also pointed out that “employers may need to modify their labeling procedures and methods of communicating chemical hazards to workers and other employers on site.”
Opposing the proposed amendments, Cal/OSHA contends they will, in effect, reduce the amount and quality of chemical hazard information available to workers.
The state agency believes the rules discount chemical evaluations from the regulatory agencies including the EPA.
Tackling Heat
Attorney Courtney Malveaux of Jackson Lewis believes OSHA’s standard for heat illness prevention may be the most consequential for the construction industry.
The number one weather-related killer, heat has become more dangerous in recent years as global temperatures have continued to rise, said Malveaux.
OSHA’s General Duty Clause has served as a catch-all for hazards not addressed by a specific standard. But that will change, said Malveaux, if OSHA follows state standards already in place.
The agency could mandate break times and require employers to monitor employee acclimatization, as well as outdoor temperatures and humidity levels.
Bloomberg Law reports that the OSHA heat rule proposal isn’t all that hot, though. In just the pre-rule stage, the federal agency’s proposed measure may not make any progress toward becoming reality until October.
That’s when the agency will issue a request for information seeking public input on a possible rulemaking on heat illness prevention in indoor and outdoor settings.
A request for information “would allow the agency to begin a dialogue and engage with stakeholders to explore the potential for rulemaking on this topic,” according to the Association of Builders and Contractors (ABC).
OSHA spokeswoman Denisha Braxton said “OSHA continues strong enforcement related to heat illness using the General Duty Clause.”
Daniel Kaplan, a partner of Foley & Lardner LLP in Madison, Wis., believes a federal OSHA heat stress rule could be useful if it’s clear about how employers should comply.
He suggests employer should check their precautions against OSHA’s guidance in the heat stress section of its technical manual.
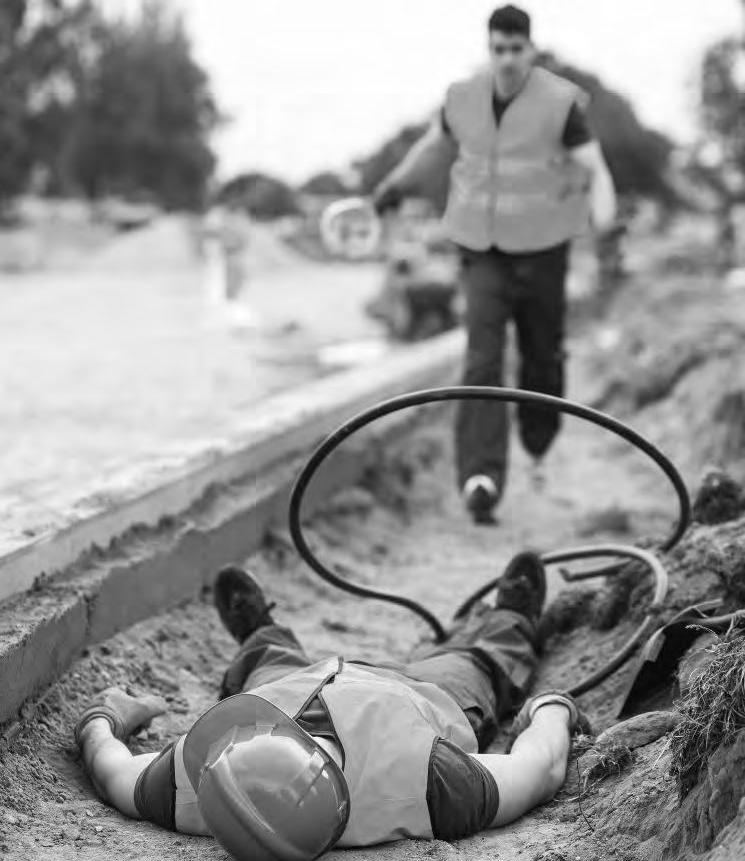
OSHA may beef up workplace injury and illness tracking under the Biden Administration. The agency wants to revert to the 2016 version of the rule.
see OSHA page 96
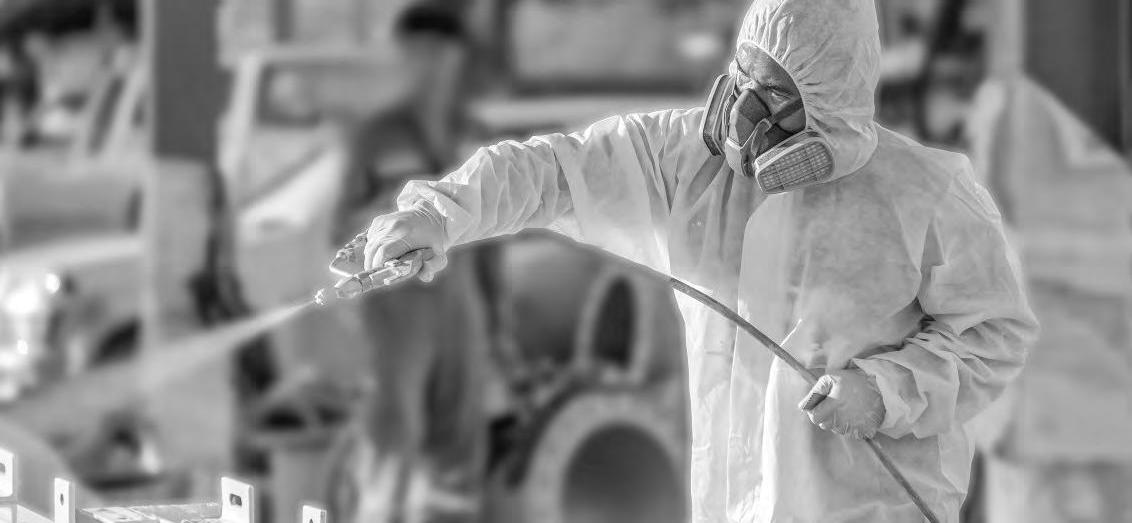
Mecalac Brings Its New Fleet Management System to N.A.
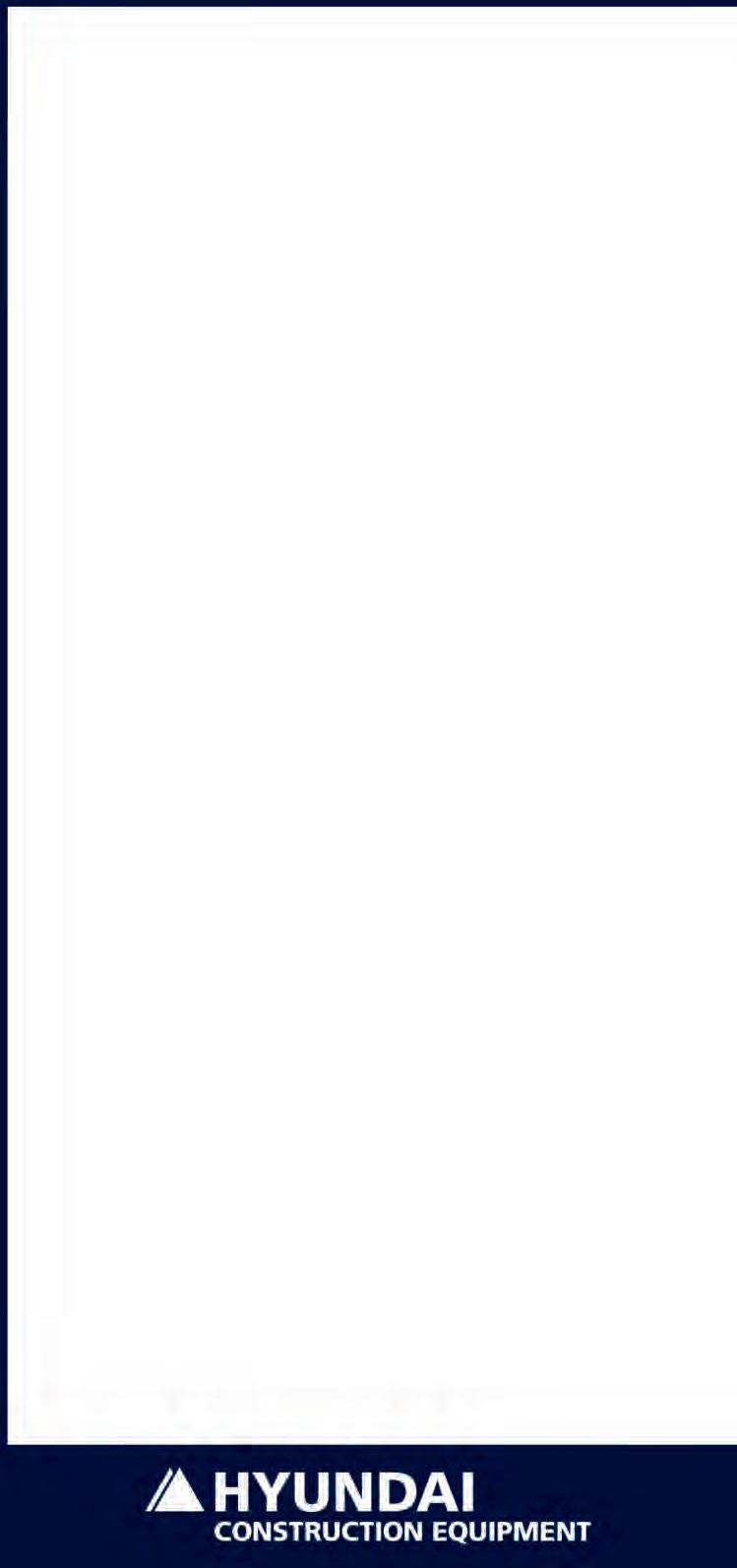
Mecalac, a global designer, manufacturer and distributor of compact construction equipment for urban environments, announced its fleet management system, MyMecalac, is now available in North America.
This telematics solution delivers everything from highlevel summaries to specific machine details, including maintenance, inspection and damage notifications, to empower fleet managers to boost efficiency and machine uptime.
“Telematics enabled machines increase productivity while maintaining high efficiency and safety,” said Peter Bigwood, general manager of Mecalac North America.
Mecalac’s telematics system, developed in partnership with Trackunit, a worldwide leader in telematics solutions, is accessible through a web portal, mymecalac.com, and a mobile app, MyMecalac. The system comes standard on all excavators and loaders in North America. The onboard telematics box continuously communicates information to the web portal. Users simply login to the web portal or app to access all machine data in real-time.
MyMecalac provides a complete fleet overview that shows users which machines are in top shape, and which need immediate attention or will require service soon. From there, those using the service can zoom into a specific machine to see everything from fuel consumption and oil pressure to the current engine load percentage and machine hours. This data allows fleet managers to schedule downtime for refueling, maintenance and repairs rather than having these tasks interrupt project timelines and profitability.
MyMecalac provides a complete fleet overview that shows users which machines are in top shape and which need immediate attention or will need service soon. From there, those using the service can zoom into a specific machine to see everything from fuel consumption and oil pressure to the current engine load percentage and machine hours.
Additionally, after registering in the web portal, alerts can be set up to notify the user when maintenance is required or when a fault code appears. This technology enables dealer technicians to remotely diagnose machine issues. The alert feature also acts as a theft prevention tool by notifying the owner if the machine moves from a designated zone or operates outside of designated hours. “This technology has proven itself as a real game changer for anyone managing a fleet,” Bigwood said. “Whether it’s scheduling fueling more efficiently or coordinating service intervals to maintain production levels, having access to this data remotely provides endless opportunities to improve dayto-day operations.” For more information, visit www.mecalac.com.
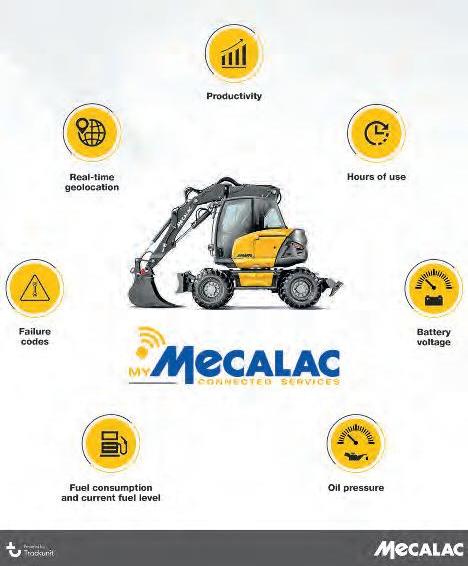
Would you like your company featured in Construction Equipment Guide?
A Montano Co., Inc. www.amontanoco.com 571 Route 212 • Saugerties, NY 12477 845.247.0206
All Island Equipment www.allislandequipment.com 39 Jersey St. • West Babylon, NY 11704 631.643.2605
Butler Equipment www.butlerequip.com 631 New Park Avenue • West Hartford, CT 06110 860.233.5439
Chappell Tractor www.chappelltractor.com 454 Route 13 South • Milford, NH 03055 603.673.2640 251 Route 125 • Brentwood, NH 03833 800.616.5666 391 Loudon Road • Concord, NH 03301 800.358.6007
George & Swede Sales & Service www.georgeandswede.com 7155 Big Tree Rd. Pavilion (Buffalo/Rochester), NY 14525 585.584.3425
Highway Equipment Company www.highway-equipment.com 22035 Perry Highway • Zelienople (Pittsburgh), PA 724.452.7800 Dubois, PA 15801 814.371.3600 Millstone Township, NJ 08535 732.446.7600
Lorusso Heavy Equipment, LLC www.lhequip.com 160 Elm St. • Walpole, MA 02801 508.660.7600 Modern Group Ltd. www.moderngroup.com 2501 Durham Rd. • Bristol, PA 19007 800.866.3376 Allentown, PA 18106 610.398.1101 York, PA 17406 800.866.3376 Edison, NJ 08837 800.866.3376 Hasbrouck Heights, NJ 07604 201.288.1441
Quality Fleet Service, Inc. www.qualityfleetservice.com 548 New Ludlow Road • South Hadley, MA 01075 413.213.0632
Seaview Equipment LLC www.seaviewequipment.com 640 Crescent Ave. • Bridgeport, CT 06608 203.330.0130
TB Equipment & Rental www.tbequipment.net 892 Odlin Rd. • Bangor, ME 04401 207.262.0014
Tracey Road Equipment, Inc. www.traceyroad.com 6803 Manlius Center Rd. • East Syracuse, NY 13057 315.437.1471 • 800.872.2390 Adams Center, NY 315.788.0200 • 888.335.0200 Albany, NY 518.438.1100 • 866.740.8853 Kirkwood, NY 607.775.5010 • 800.370.9488 Queensbury, NY 518.793.9688 • 800.872.2390 Utica, NY 315.765.8746 • 800.872.2390
Whited Equipment Co. www.whitedtruck.com 2160 Hotel Road • Auburn, ME 04210 207.346.0279 873 Portland Road • Saco, ME 04072 844.430.6810
AEM Virtual Summit to Offer Solutions for Future Employee Development
As part of its ongoing efforts to inspire members and association partners in developing strategies to build a bigger, better workforce, AEM is offering its second-annual Workforce Solutions Summit.
This one-day virtual summit — scheduled for Aug. 19, 2021 — will offer valuable information and insights, as well as research-based solutions, to organizations looking to recruit, train and retain employees.
“It’s critically important for our industry to take a proactive and informed approach to workforce development activities, as well as developing the employees of tomorrow,” said AEM Senior Director of Workforce Solutions Julie Davis. “Manufacturing offers a wealth of incredible career opportunities, and this summit serves as a uniquely valuable forum for industry stakeholders to learn how to effectively recruit talent and promote the skilled trades.”
Feature speakers at this year’s Workforce Solutions Summit include: •YourExecutiveCoach.com’s Janyne Peek-Emsick, who will focus on the neuroscience of conflict • McKinsey & Company’s Bryan Hancock, who will discuss the future of work • Microsoft’s Lauren Gardner, who will cover diversity and inclusion • Workforce Alliance of South Central Kansas’s Keith Lawing, who will talk about connecting with local workforce development • Career Research Group’s Chris Czarnik, who will present on best practices related to employee retention and recruitment
In addition, several company representatives are scheduled to share strategies they are employing in order to influence workforce success in their organizations and communities. They include: • Linamar • UGDSB • GPS Education Partners • Komatsu Mining Corp.
AEM also will offer hands-on Workforce Pre-Summit Workshops on Aug. 17 and Aug. 18. Capacity is limited, so interested attendees should add the workshops to their order when registering for the Workforce Solutions Summit.
“Our Workforce Summit will cover topics to help our members and the industry develop a pipeline of talent to help them move their businesses forward, and many of the ideas presented can be easily implemented,” continued Davis.
“Ultimately, this summit is designed for all roles who have a stake in growing and developing a successful workforce — executives and company leaders, operation leads, training and hiring managers, and human resources and recruiting professionals,” she said. “Because finding talent is more than just a human resources issue, it’s a business issue.”
Sponsors for this year’s Workforce Solutions Summit are Apprenticeship Works!, GPS Education Partners, Green Mountain Lion Corporation and Ultra Consultants.
For additional information, download the summit agenda and the pre-summit workshop agenda, or contact AEM’s Julie Davis at jdavis@aem.org.
Deere Now Offers JDLink Connectivity Service Subscription at No Additional Charge
John Deere is improving the ability for customers to maximize machine performance and uptime through updates to the JDLink platform.
Starting July 14, 2021, customers will no longer need to renew their JDLink connectivity service subscription and can enable their JDLink service on any compatible machine in their organization at no additional charge. Additionally, once customers enable JDLink connectivity, they can select to automatically activate all future JDLink compatible models, further streamlining fleet management.
With this update to the JDLink service offering, it is easier than ever before for customers to maximize machine productivity and minimize downtime, the manufacturer said.
“John Deere has offered telematics for well over a decade and the boost in machine monitoring and machine uptime has been an overwhelming benefit to our customers,” said James Leibold, product marketing manager, connected solutions, John Deere. “With the next phase of our JDLink offering, we are making it easier for customers to manage their fleets. Instead of needing to keep track of renewal dates by each machine, owners and fleet managers can look at monitoring their equipment holistically and can focus on what’s important — keep their job sites running.”
Available on most new models, John Deere’s JDLink telematics solution delivers valuable fleet insights directly into the hands of the machine owner or fleet manager. The JDLink service enables customers access to vital data, such as machine location and utilization, time in idle, fuel level, upcoming maintenance, machine alerts, and more, all from a web or mobile platform.
Beyond machine monitoring, the JDLink solution also enables John Deere Connected Support, enabling the dealer to remotely identify critical issues and take action minimizing potential downtime or by remotely sending software payloads to ensure the machine is running efficiently.
For more information, visit www.johndeere.com. ASPHALT CARE EQUIPMENT INCORPORATED

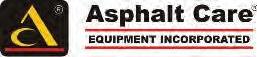
2765 Galloway Road Bensalem PA 19020 215/639-9800 1-800/223-1202 www.asphaltcare.com
BARRY EQUIPMENT COMPANY, INC.
30 Birch Island Road Webster, MA 01570 508/949-0005 www.barryequipment.com

CHAPPELL TRACTOR
454 Route 13 South Milford, NH 03055 800/698-2640 251 Route 125 Brentwood, NH 03833 800/616-5666 391 Loudon Rd. Concord, NH 03301 800/358-6007 www.chappelltractor.com
EQUIPMENT EAST
61 Silva Lane Dracut, MA 01826 978/454-3320 www.equipmenteast.com
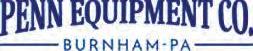
PENN EQUIPMENT CO.
100 Windmill Hill Burnham, PA 17009 717/248-8876 www.pennequip.biz
SCHLOUCH from page 16
Cumberland County
Penntex Construction Company Inc. selected Schlouch Inc. to prepare the 60.36-acre site for a 753,000 sq. ft. warehouse facility. The project is located off Centerville Road in Penn Township, Cumberland County, Pa. Work will be completed in fall 2022.
Lehigh County
Sunshine Two LTD named Schlouch to provide site preparation for Hidden Meadows Phase 2 featuring 90 townhouse units. Sal Lapio Homes is the developer of the residential project located off Rockrose Lane, Upper Macungie Township, Lehigh County, Pa. Work will be completed in summer 2021.
Luzerne County
Sand Springs Development Corporation chose Schlouch Incorporated to prepare self-storage units on the 5.5acre site for Sand Springs Phase 5B. Tuskes Homes is the developer of the project. The site is located in Butler Township, Luzerne County. Work will be completed in fall 2021.
Montgomery County
Pottsgrove Hunt Associates LLC named Schlouch Incorporated to provide site preparation for Pottsgrove Hunt: Phases 1A and 1B. The residential project will feature 143 single-family homes. The site is located off Kummerer Road in Upper Pottsgrove Township, Montgomery County. Catalyst Commercial Development is the construction manager for the project. Work will be completed in fall 2022.
Rouse Chamberlin Ltd. chose Schlouch Incorporated to prepare the 17.94-acre site for RC Weaver Property (Ashford). The development will consist of 15 single-family homes. The residential project is located on Linfield Trappe Road, Limerick Township, Montgomery County, Pa. Work will be completed in summer 2021.
Northampton County
CMC Development Corporation selected Schlouch Incorporated to prepare the 14.22-acre site for Northwood Farms Phase 4. Tuskes Homes is the developer of the project consisting of 29 single-family homes located at Highland Drive and Lisa Lane in Palmer Township, Northampton County. Work will be completed in fall 2021. (This story was reprinted with permission from OnSite With Schlouch Incorporated, Spring/Summer 2021 issue.)

Schlouch paving crew completes roadway for Hidden Meadows, Lehigh County, Pa.
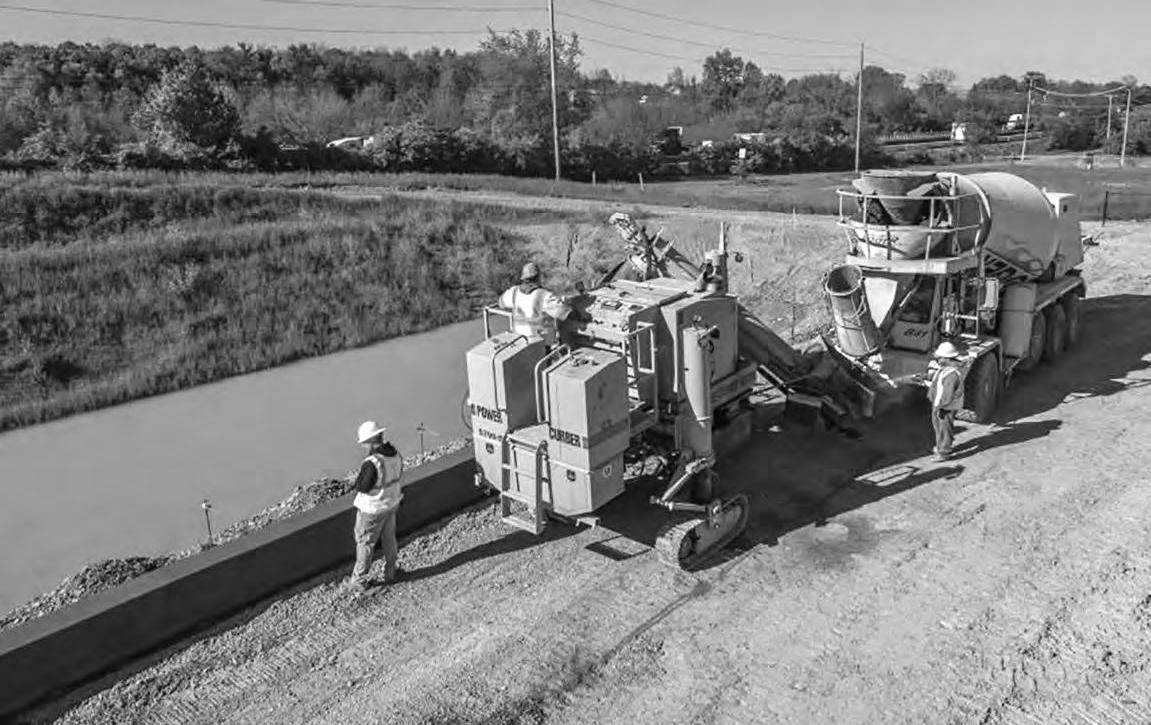