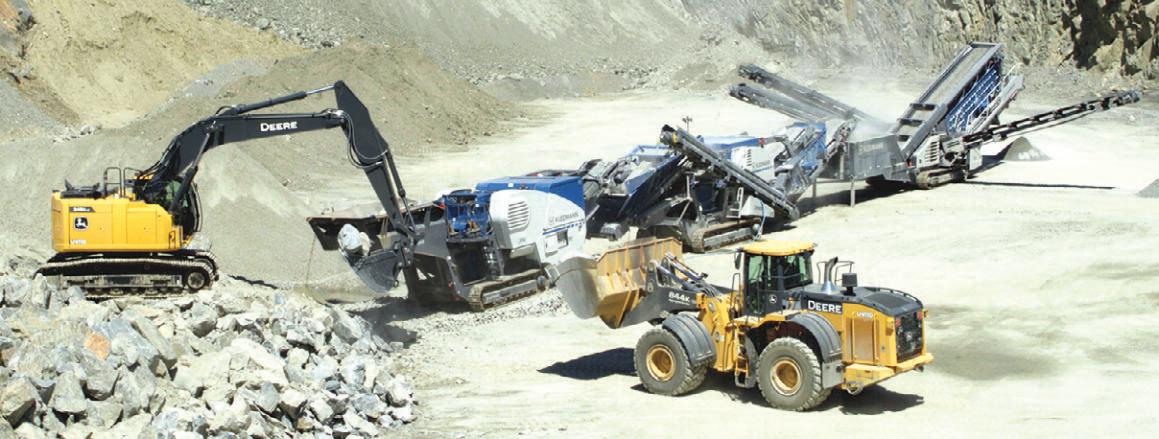
18 minute read
Aggregate & Recycling Section
Pages 57-75 Aggregate Production and Recycling Section
For more information on crushing, screening and recycling equipment, visit CEG's Web site at www.constructionequipmentguide.com. ‘Manosh By Gosh’ … Biz Offers Extensive Array of Services
N.A. Manosh Corp. of Vermont’s website boasts “When it comes to water, well and construction drilling, wastewater and septic services, geothermal heating and cooling, aggregate materials and related excavation…it’s ‘Manosh by Gosh.’”
As Nick Manosh, son of the company’s founder, tells the story, “In 1958, my dad [Howard Manosh], who had been an equipment operator, sold his 55 Chevy for $1500 for a down payment to buy a John Deere tractor with a Pippin backhoe and started working nights and weekends doing whatever work he could find.”
In 1965, Howard Manosh identified a growing need for clean accessible water; he purchased the company’s first drilling rig and the catch phrase, “Manosh by Gosh” took root. In the 1970s, as Vermont became a vacation destination and the ski slopes took hold, the economy grew in the area and Howard further diversified the company, known at that time as H.A. Manosh Corp. At one point he diversified the company into operating an asbestos mine, which was quite successful until the government banned asbestos in the late 1970s.
Nick Manosh joined his father’s growing company right out of high school. He eventually purchased the assets of H.A. Manosh from his father and two brothers. Today Nick’s son, Connor, represents the third generation of the Manosh family and Connor focuses his attention primarily on the water drilling and pumping aspect of the company’s business.
Today, the company is a major force in the construction industry, offering a wide variety of highly diversified services, including septic pumping and sewer inspection services, along with storm water and catch basin cleaning and pump/lift station maintenance.
The company has six drilling rigs and, not only does it do residential well drilling, but it also does municipal and commercial, construction drilling within about a 250-mi. radius of central Vermont. The company also offers water treatment services to properly treat the water that is generated from its drilling services to produce ideal drinking water.
N.A. Manosh also has expanded into geothermal heating and cooling for both commercial and residential.
As it has expanded into the geothermal work, it covers a significantly larger area with projects as far away as Portland, Maine, and Cambridge, Mass. With fuel prices increasing the market for that kind of work, the geothermal side of the business could
N.A. Manosh transports its complete Kleemann portable crushing spread among its various quarries. expand considerably. One of the centerpieces of the N.A. Manosh operation is its four aggregate production facilities that were purchased to support the company’s growing construction division. The facilities produce: • washed manufactured sand; • road sand/screened sand; • mound sand; • stone (round and ledge) — 1-1/4-in., 3/4-in., 3/8-in., 2-5-in.; • quarry rip-rap; • 1-1/2-in. plant mix; • 1-in. minus Staymat; • 1-1/2-in. crushed gravel; ¾-in. crusher run gravel • bank run gravel; • bank run sand/fill; • topsoil (regular and screened); • granular backfill; • over run stone; • dense graded; • 1-in. minus ditch stone; and • State Spec materials Approximately a year ago, Nick saw a significant opportunity to grow the aggregate side of the business. A major road project, reclaiming and repaving of Route 15 in
C2C Visuals photo CEG photo (L-R): With the Kleemann MOBICAT EVO are Jason Vandeweert, branch manager of United Construction & Forestry in Williston, Vt.; Justin Jennett, general manager of United Ag & Turf; and Nick Manosh, president of N.A. Manosh.
see MANOSH page 66
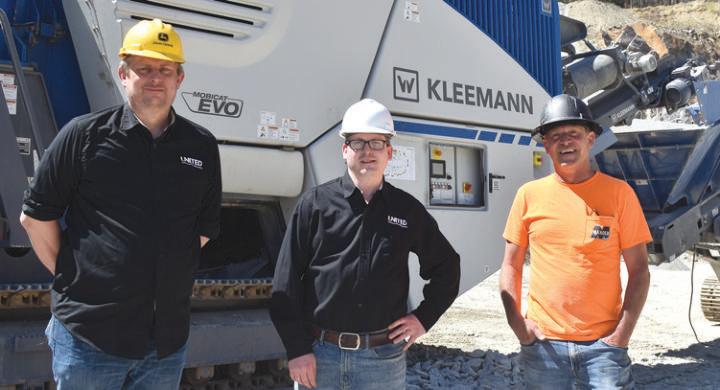
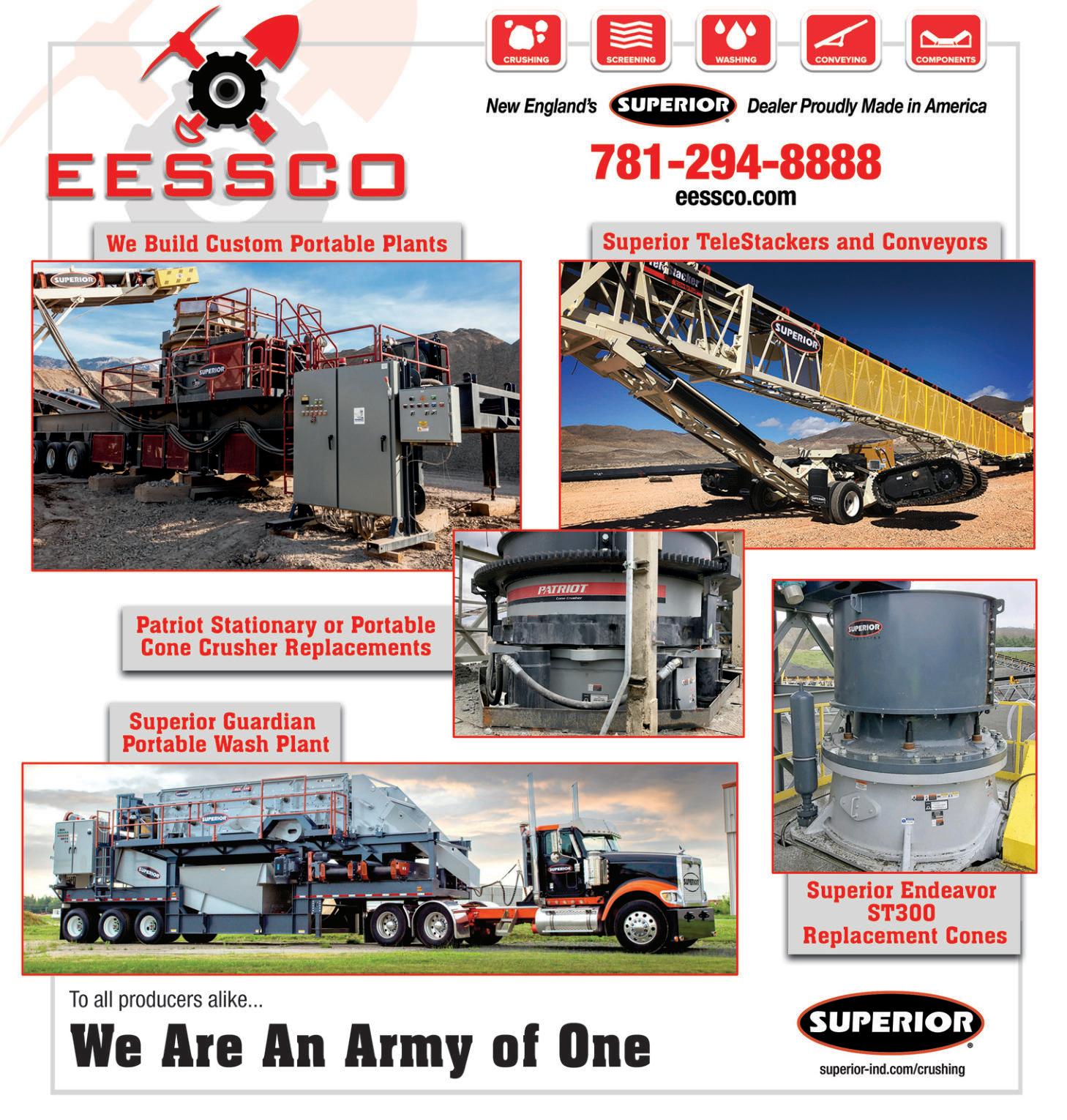
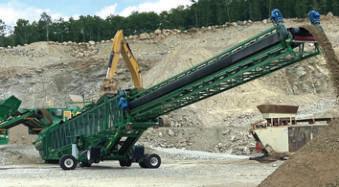
2021 MCCLOSKEY SDX130: Serial Number: 90666, New Telescoping Stacker 36"x130' Electric Hydraulic Power WEG 20HP. Standard Hopper, Pivot Point, Hydraulic Landing Gear, Hydraulic Wheel Drive, Remote Greaselines, Walking Beam w/Lift Axle >>>Call
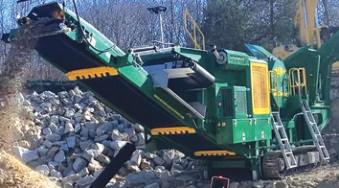
2021 MCCLOSKEY J40: Hours: 389, Serial Number: 90232, Belt Protection Deflector Plate, Overband Magnet on Main, Working lights, Safety Beacon Lights, Telematics, Volvo D8 T4F 252HP Engine >>>>Call 2022 MCCLOSKEY ST100T: Hours: 53, Serial Number: 92129, Stacker with Impact Idlers Under Hopper, Upgraded Belt Cleaner/Scraper, Telematics, Upgraded Hydraulics, CAT C2.8 Tier 4F/ Stage V 74HP Engine >>>>>>>>>>>>>>>>>>>>>>>>>>>>>>>>>>>>>>>>>>>Call
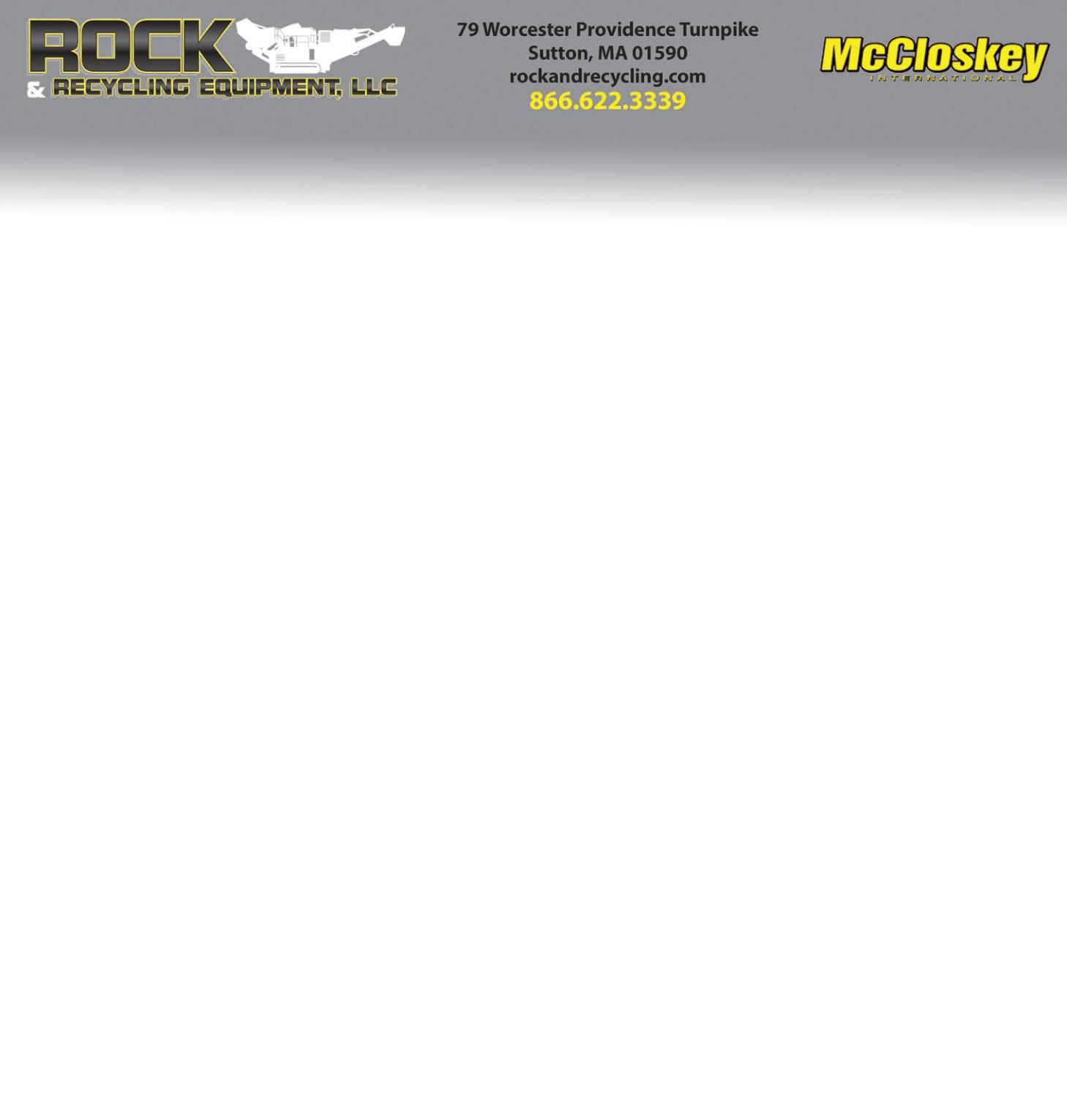
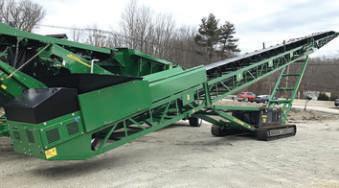
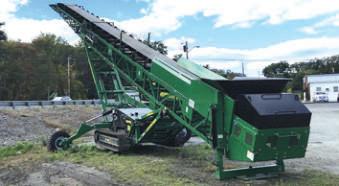
2022 MCCLOSKEY ST80TLA: Hours: 10, Serial Number: 92289, Lift Axle, Hopper Wear Plates, Impact Idlers, Belt Cleaner/Scraper, CAT 2.2 Tier 4F 49HP Engine >> >>>>>>>>>>>>>>>>>>>>>>>>>>>>>>>>>>>>>>>>>>>>>>>>>>>>>>>>>Call
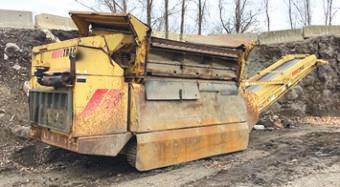
2006 EXTEC ROBOTRAC: Hours: 5,008, Serial Number: 9872, Well maintained. Deutz Engine. 10’x8’10” screen deck with side discharge conveyor >>>>>>>>>>>>$59,500 2022 MCCLOSKEY 516R-T: Hours: 68, Serial Number: 92344, Hydraulic Tipping Grid over Hopper, Remote Start/Stop Feeder, Fitted Safety Beacons, Telematics, CAT C3.4 Tier 4F 74HP Engine >>>>>>>>>>>>>>>>>>>>>>>Call 2022 MCCLOSKEY TS4065: Hours: 11, Serial Number: 78684, Standard Hopper, Wear Plate Lining in Hopper, Impact Bed in Hopper, Hydraulic Top Fold, Remote Greaselines, CAT C2.2 Tier 4/Stage V 67HP Engine >>>>>>>>>>>>>>>>>>>>>>>>>>>>>>>>>>>>>>>>>>>>>>>>>Call
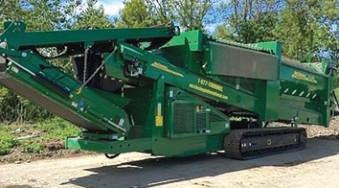
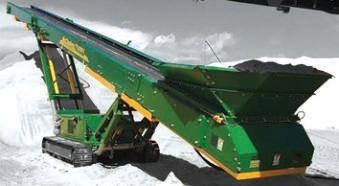
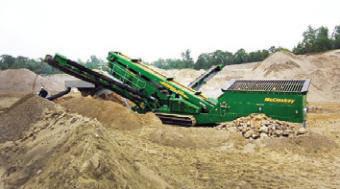
2020 MCCLOSKEY S190 3D: Hours: 543, Horsepower: 130 hp, Serial Number: 91405, Tracked Triple Deck Heavy Duty Screener. CAT Tier 4F Engine. 15ft Feeding Hopper. Chevron Belt on Main Conveyor. Remote Machine Shut Off >>>>>>>>>>>>>>>>>>>>>>>>>>>>>>>>>>>>>Call
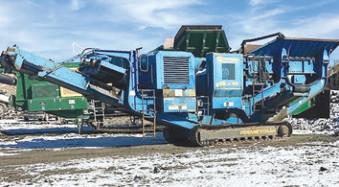
2003 TEREX PEGSON 2644 PREMIERTRAK: Hours: 11,448, Engine: Cat C9, 1 Owner Machine, New Jaw Dies, New Cheek Plates, Jaw Box has been recently rebuilt, New Bearings in Pittman, New Toggle >>>>>>>>>>>>>$225,000 2020 MCCLOSKEY C3: Hours: 1614, Horsepower: 510 hp, Serial Number: 91189, METSO designed cone, 300 HP Class. Volvo D13 Medium Cone Liner currently installed. >>>>>>>>>>>>>>>>>>>>>>>>>>>>>>>>>>>>>>>>>>>>Call
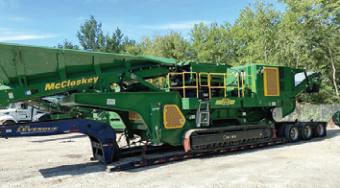
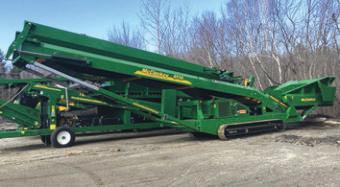
2021 MCCLOSKEY RF80: Hours: 124, Serial Number: 77883, Hopper Wear Plates, Extended Hopper Wing Plates, Upgraded Belt/Cleaner Scraper, Variable Speed and Start Stop Feeder Kit, CAT C3.6 Tier 4/Stage V 134HP Engine >>>>>>>>>>>>>>>>>>>>>>>>>>>>>Call
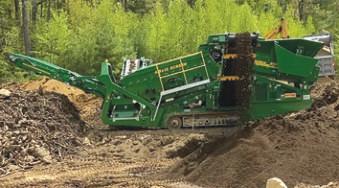
2021 MCCLOSKEY R105: Hours: 809, Serial Number: 77461, Screener with Remote Variable Speed Feeder, Remote Machine Shut off, Safety Beacon Lights, Telematics. CAT Tier 4F 130HP >>>>>>>>>>>>>>>>>>>>>>>Call
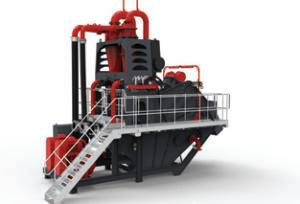
NEW MWS CSP200 COMPACT SAND PLANT, Serial Number: 20349, cost and energy efficient, exceptional performance, 14 x 6 dewatering screen, can produce 1 grade of sand, self regulating sump tank >>>>>>>Call 2021 MCCLOSKEY ST80: Hours: 6, Serial Number: 92183, CAT 2.2 Tier 4F 49 HP, Hydraulic Axle Jacks, Hydraulic Axle Extensions, Hydraulic Landing Gear, Hopper Wear Plates, Impact Idlers under Hopper Call 2021 MWS S190: Hours: 165, Serial Number: 91989, Screening Plant with Fitted Rinser Kit with Spray Bars on Screenbox, Aux Drive Circuit, Plain Belt on Main Conveyor >>>>>>>>>>>>>>>>>>>>>>>>>>>>>>>>>>>>>>>>Call 2021 MCCLOSKEY C2: Hours: 324, Serial Number: 92089, Metal Detector on Feeder, Discharge Chute on Main Conveyor, Upgraded Belt Cleaner/Scraper on Main, Telematics, CAT C9.3B Stage V/Tier 4F 375 HP Engine >>>>>>>>>>>>>>>>>>>>>>>>>>>>>>>>>>>>>>>>>>>>>Call
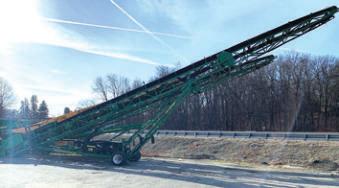

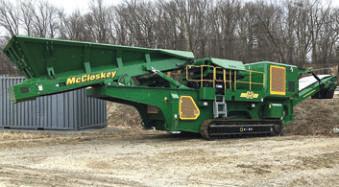
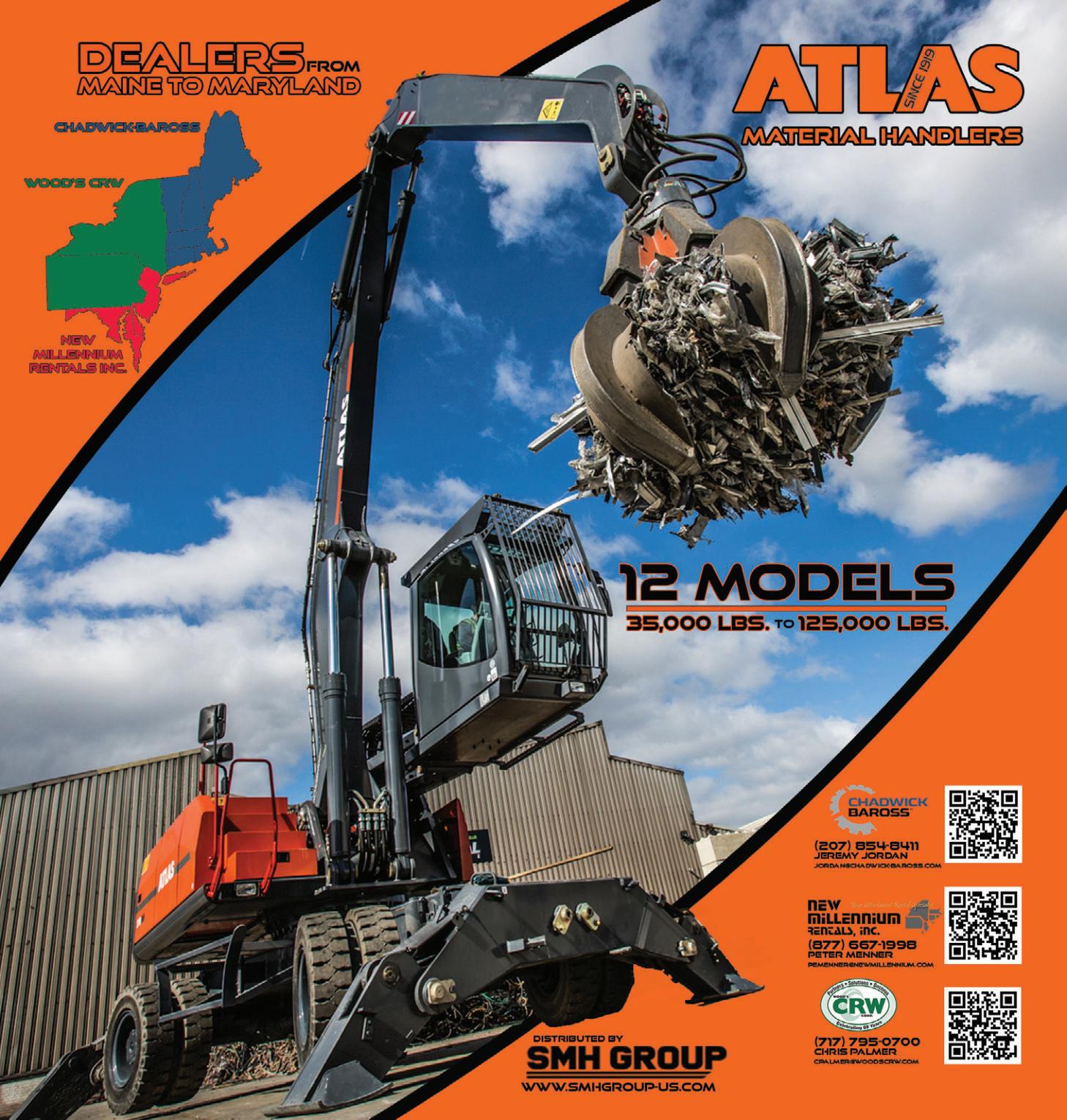
MANOSH from page 57 Vermont, was slated for the area that would consume a significant amount of aggregate product. It had been some time since the proper amount of investment had been made in the crushing and screening equipment as well as the earthmoving equipment in his quarries. The project would require tens of thousands of yards of specked material.
To bid competitively and make product quotas to go after the work that was coming to the area, Nick knew it was time to reinvest in his company.
After extensive research and looking at several different combinations of aggregate-producing and earthmoving equipment, Nick pulled the trigger on a major investment of John Deere and Kleemann equipment from United Construction & Forestry (formerly known as Nortrax) in Williston, Vt.
The package, which would be transported between the four aggregate pits, included a massive John Deere 844K 10-yd. loader; a John Deere 345G LC 80,000-lb. excavator; a Wirtgen WR250i asphalt recycler; a Kleemann MS15Z double-deck screening plant ideal for processing natural stone and recycled material; a Kleemann MS953 EVO portable tracked classifier screen; a Kleemann Mobicat MC110 Zi 44-in. x 28-in. portable tracked jaw crusher; and a Kleemann MOBICONE MC90Si EVO trackmounted cone crusher.
To put this package together, Nick worked closely with Justin Jennett of United Construction & Forestry. The closest heavy equipment dealer to N.A. Manosh, United Construction & Forestry was still a good 50 mi. away.
According to Nick, “We had a lot of objectives in making this purchase. We needed to make a better product. We needed to make a lot more product. We needed to lower our production costs. Ideally, we wanted to see our fuel consumption drop and we had to get great service from whomever we were going to make the purchase from.
“Justin Jennett with United Construction & Forestry was the right man for the job. We already knew John Deere equipment. My dad started the company with a John Deere tractor, and we had done some business with Justin in the past.
“But this was a big purchase, and it took a lot of hand holding on Justin’s part. The price had to be right, and he put together a great lease-purchase for us. It gave us an opportunity to use the equipment and know and have full confidence that it was going to meet all of our expectations before pulling the trigger on such a significant investment.
“The John Deere 844 loader was perfectly matched in size to meet the production capacities of our new Kleemann aggregate production line. We found out in a hurry that you needed a big loader to keep up with these Kleemann machines. With the crushers we were looking for a quality name that we could be as comfortable with as we are with John Deere.
“Kleemann is owned by John Deere; it has a reputation as being first in its class; and in our case, it’s serviced by the John Deere dealer who is located nearby, and it all came together in one nice package.
“The product we’ve been getting from the Kleemann spread has exceeded our expectations. Right away we were able to eliminate our wash plant. We process from the jaw to the scalper to the cone to the screening plant. Using that configuration, we were able to completely get away from washing. So, we don’t have to use any water and that makes our stone as clean as possible.
“The first year we did see a little bump upwards in our maintenance costs. We were all trying to get used to new equipment and that took a transition. This year our maintenance cost is down dramatically, and everything is running smoothly. Our operators needed to transition to a different type of operation as well.
“We did get a little nervous. There was a name change that happened during the process; Nortrax became United Construction & Forestry, which made us a little nervous. We were told nothing would change and we would continue to see the same level of service and so far, they have certainly held up their end of the bargain.”
For more information, visit http://www.UnitedCF.com and manosh.com. CEG
C2C Visuals photo A John Deere 345G LC excavator feeds a Kleemann MOBICAT MC110Zi 44 x 28 portable track crusher.
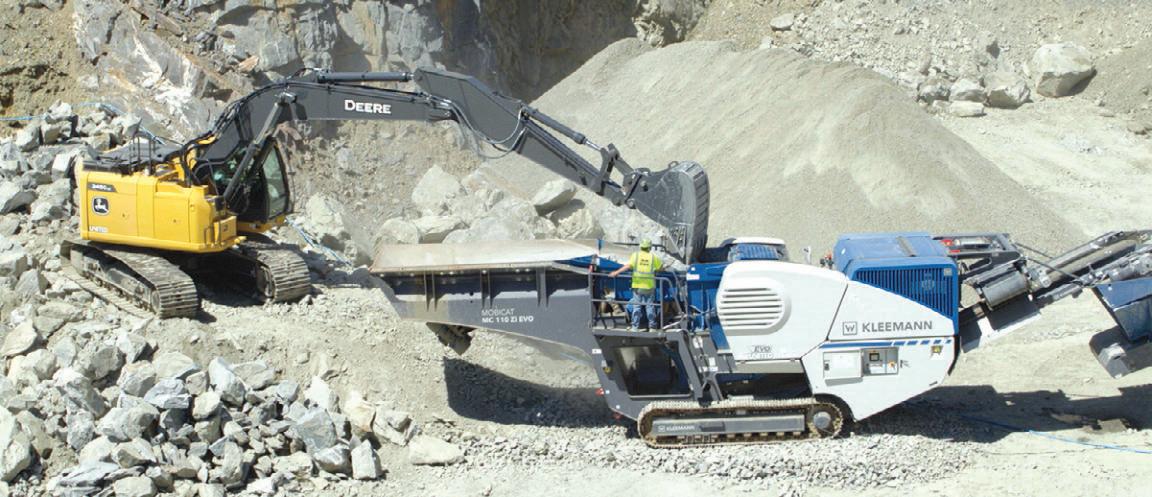
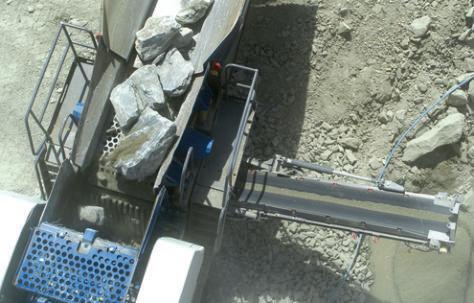
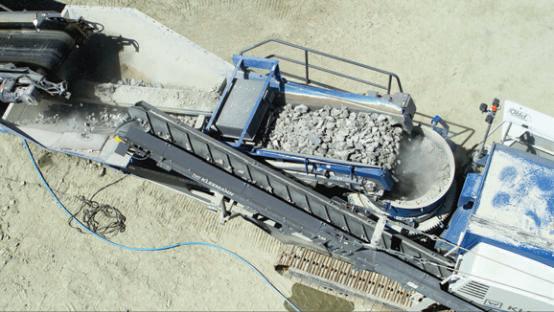
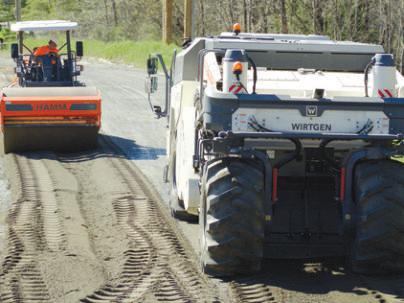
Page 70 • July 20, 2022 • www.constructionequipmentguide.com • Recycling Section • Construction Equipment Guide Rock & Recycling Equipment Expands Product Offering With Lippmann, MWS
Shane Fleming and Brendan Fox, owners of Rock & Recycling Equipment in Sutton, Mass., announced a significant expansion of the company’s product offerings.
Rock & Recycling Equipment has long been known as the exclusive supplier of McCloskey crushing and screening equipment for New England contractors and aggregate producers. Moving forward, Rock & Recycling Equipment also will be the distributor of Lippmann Milwaukee Inc. and MWS Equipment.
“Each of these companies’ product offerings will significantly enhance Rock & Recycling Equipment’s product offerings and ability to serve their customer base, in particular, the aggregate producer segment,” Fleming said.
Since 1923, Lippmann has continuously designed and manufactured quality aggregate processing equipment in Milwaukee, Wis. The company began as Lippmann Engineering Works, and the design of heavyduty primary jaw crushers became the cornerstone of its product line.
Today, Lippmann continues to maintain a reputation for building one of the heaviest and most reliable primary jaw crushers on the market, along with its expanded line of proven aggregate processing equipment designed to increase productivity and reduce cost, the company said.
“Lippmann is absolutely recognized as the leader in the stationary primary jaw crusher market,” Fleming said. “We are equally enthusiastic about introducing New England producers to other high quality Lippmann products, including their horizontal shaft impact crusher, vibrating grizzly feeders and other Lippmann ancillary products.” MWS Equipment (McCloskey Wash Systems) is a world leader in the engineering and manufacturing of highquality wet processing equipment or, in essence, equipment for manufacturing sand and washing stone. “In recent years there has been an increased demand for aggregate producers to have the ability to produce sand and washed stone,” Fleming said. “Our affiliation with
MWS will give us the ability to provide our customers with quality equipment that is backed with exceptional engineering and customer service. We are constantly looking for innovative products to assist our customers in enhancing their productivity and we are impressed with the offering MWS Equipment will add to our product portfolio.”
To support and develop its two new product offerings, Rock & Recycling is bringing Brian Lee on board as its division manager of Lippmann and MWS. Lee has spent nine years working for Lippmann serving in several positions, including service coordinator, inside sales representative, outside sales representative and as a territory manager working with dealers and end users supporting Lippmann products. He then spent two years with McCloskey working as a factory representative working with dealers and end users, where he developed a relationship with Rock & Recycling.
“I am optimistic about the opportunity of joining the Rock & Recycling team and helping them develop the Lippmann and MWS product offerings,” Lee said. “Having worked in the past with both Lippmann and Rock & Recycling, I am fully confident of both companies’ ability to identify the needs of their customers, help engineer and design the ideal products to satisfy those needs and support those products down the road.”
In his position at Rock & Recycling, Lee will be responsible for developing new sales for Lippmann as well as MWS, developing the proper inventory of stocked parts and training current sales and support staff.
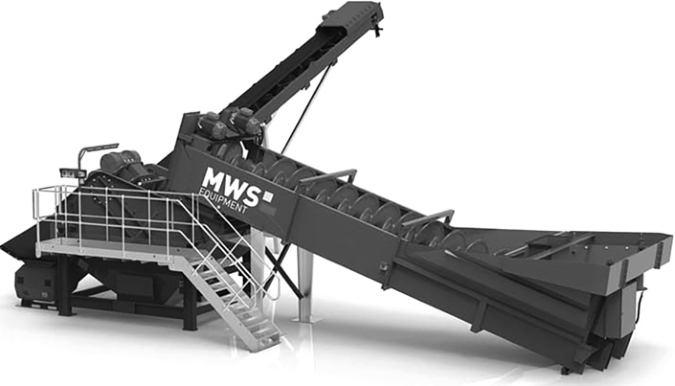
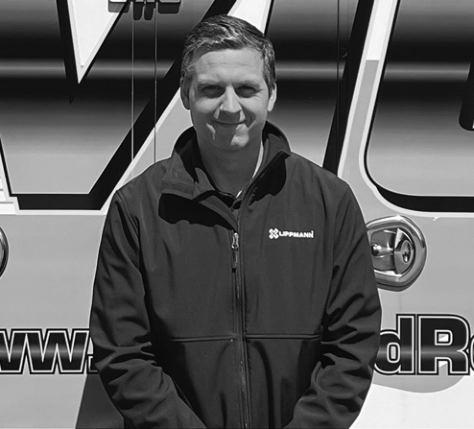
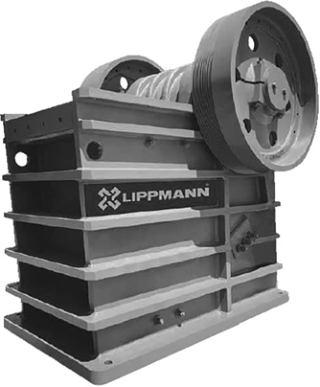
MSW photo MWS Equipment (McCloskey Wash Systems) is a world leader in the engineering and manufacturing of high-quality wet processing equipment.
Lippmann photo Lippmann has a reputation for building one of the heaviest and most reliable primary jaw crushers on the market. JESCO Inc.
New Jersey & New York 118 St. Nicholas Ave. South Plainfield, NJ 08070 (908) 753-8080 1790 Route 38 Lumberton, NJ 08048 (609) 267-2020 1275 Bloomfield Ave. Fairfield, NJ 07004 (973) 227-2221 (800) 321-8080 497 Fishkill Ave. Beacon, NY 12508 (845) 831-1800 (800) 724-0725 110 East Jefryn Blvd. Deer Park, NY 11729 (844) 482-0910 www.jesco.us
MONROE TRACTOR
New York 1001 Lehigh Station Road Henrietta, NY 14467 (585) 334-3867 (866) 683-5338 5035 Genesee Street Buffalo, NY 14225 (716) 681-7100 (800) 834-9606 7300 Eastman Road N. Syracuse, NY 13212 (315) 452-0000 (800) 287-5286 8194 State Route 415 Campbell, NY 14821 (607) 739-8741 (800) 866-8912 6 Equipment Drive Bingamton, NY 13904 (607) 754-6570 (866) 321-4277 www.monroetractor.com GROFF TRACTOR & EQUIPMENT, LLC
Pennsylvania 6779 Carlisle Pike Mechanicsburg, PA 17050 (800) 33-GROFF (717) 766-7671 Ephrata, PA (717) 738-0220 State College, PA (814) 353-8400 Cranberry Twp., PA (724) 898-1535 New Stanton, PA (724) 755-0124 Ebensburg, PA (814) 472-7300 www.grofftractor.com
UNITED CONSTRUCTION & FORESTRY
New England 80 Southbridge Road Rt. 20 North Oxford, MA 01537 (508) 987-8786 (800) 922-8295 2397 GAR Hwy, Rt 6 & 136 North Swansea, MA (508) 379-9810 (800) 456-6885 88 Camelot Drive, Unit 42 Plymouth, MA (508) 830-9997 (800) 916-0997 1620 Page Blvd. Springfield, MA (413) 543-5595 (800) 734-5594 4 Sterling Road North Billerica, MA (978) 667-4345 (800) 531-2266 98 Sheep Davis Road Pembroke, NH 03275 (603) 225-2769 300 Clinton Street Springfield, VT 05156 (802) 885-6840 www.unitedcf.com
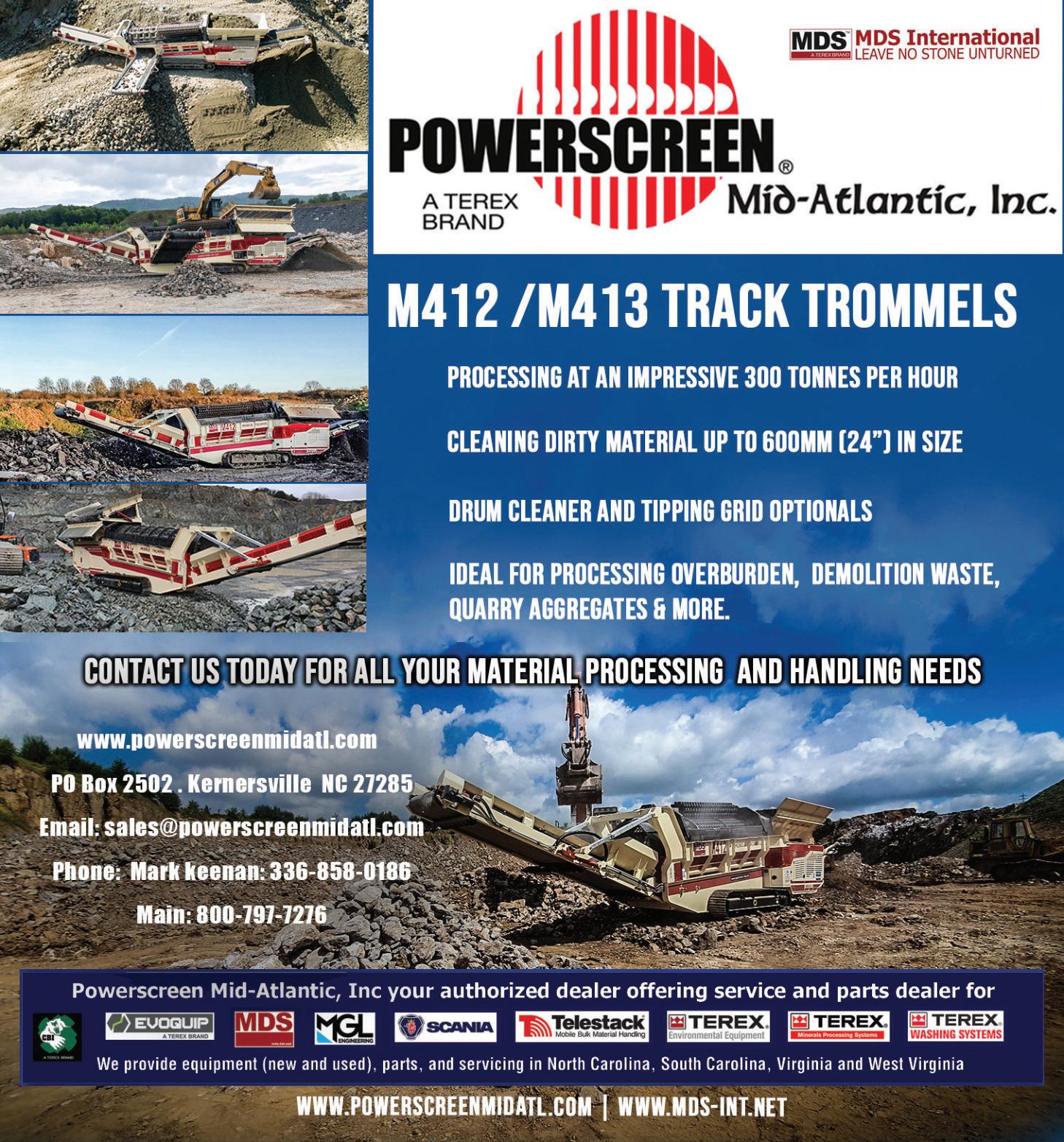
Page 74 • July 20, 2022 • www.constructionequipmentguide.com • Recycling Section • Construction Equipment Guide Komatsu, Codelco Agree to Conduct Trial of New Mining Tunnel Boring Machine
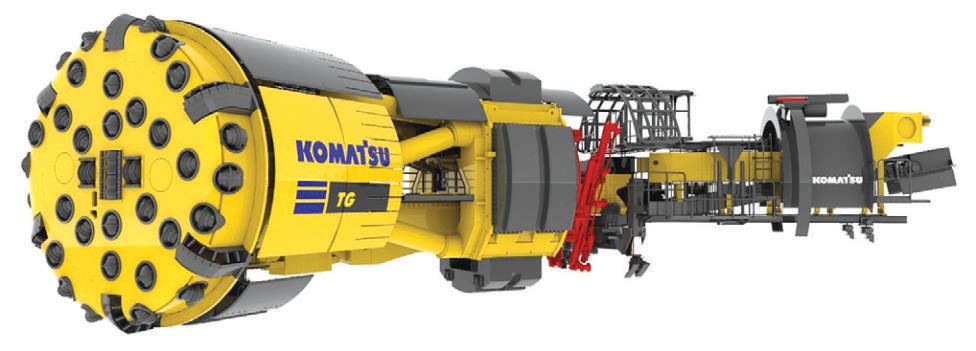
Komatsu’s tunnel boring machine (TBM) for underground hard rock mining.
Komatsu Ltd., through its subsidiary Komatsu Cummins Chile Ltda., has agreed with Codelco, a major state-owned mining company in Chile, to collaborate on trialing a new tunnel excavation method using Komatsu’s newly developed mining tunnel boring machine (TBM) starting in 2024 at Codelco’s Chuquicamata Mine in Chile.
Through trial use of the new machine, Komatsu and Codelco aim to speed up the potential introduction of this innovative technology.
Demand for underground mining equipment is expected to increase along with global demand for mineral resources that require increasingly deeper mining operations.
Komatsu developed the first TBM for rock excavation in 1963 for use in civil engineering in Japan. Since that time, the company has introduced a cumulative total of more than 2,300 TBM (including its micro tunneling machine) to the market.
Based on Komatsu’s experience in excavation, the mining TBM is equipped with new technologies that enable adaptability to small curves, reversing and passing intersections in hard rock tunnel excavation. Previously, use of TBM has generally been limited to excavating nearly straight tunnels.
This new technology improves the flexibility of the equipment and enables excavation of tunnels according to the more unique designs of each mine.
The mining TBM works by continuously performing a series of processes, such as excavating rock with disc cutters and discharging the chipped rock backwards with belt conveyors, while fortifying the excavated tunnel wall. Excavation with disc cutters improves tunnel strength and stability by creating a circular tunnel shape with smooth walls with less damage to the excavated tunnel (compared to drilling and blasting method). To support customers’ needs for increasingly sustainable ways of mining, the new machine runs off electricity, does not require the use of blasting and performs a series of tunnel excavation processes with a single machine, reducing the number of vehicles required overall. The result is a new excavation option that reduces the creation of greenhouse gases and particulate matter emissions for an improved underground environment that requires less ventilation than other methods. At the same time, it significantly increases the productivity of personnel associated with tunnel excavation work compared to conventional methods, according to the companies. In response to climate change and the need for solutions for environmental issues, Komatsu has been focusing on the development of equipment for the future of underground hard rock mining under the slogan of “No Blasting”, “No Batch”, “No Diesel.” The mining TBM and the new method embody this forward-looking approach and seek to help customers improve safety, environmental friendliness and productivity (shorter tunnel construction period and lower tunnel construction costs) at underground mines, and also will help them achieve a revolution in their mining operations. Per the company’s ongoing mid-term management plan “DANTOTSU Value — Together, to ‘The Next’ for sustainable growth”, Komatsu is working to expand offerings for underground hard rock mining, creating new value for customers with the development of new equipment, processes and technologies that will help operations step forward to the next stage for the workplace of the future and provide a more sustainable future for the next generation. For more information, visit www.komatsu.com.
(Brush Chippers, Stump Grinders)

Stephenson Equipment, Inc. www.stephensonequipment.com
Butler, PA 724-865-9221 Ebensburg, PA 814-886-5191 Harrisburg, PA (HQ) 800-325-6455 Wilkes-Barre, PA 866-667-6756
Robert H. Finke & Sons, Inc. www.finkeequipment.com 1569 US Route 9W ï Selkirk, NY 12158 518-767-9331
Bobcat of Saratoga www.bobcatofsaratoga.com 1279 Route 9 ï Gansevoort, NY 12831 518-798-9283
Westchester Tractor, Inc.
Westchester Tractor, Inc.
www.wtractor.com 60 International Blvd ï Brewster, NY 10509 845-278-7766
LARGE & SMALL EQUIPMENT DEALERS
(The Beast, Whole Tree Chippers, Sawmill / Chipmill Chippers, Track Carriers, Brush Chippers, Stump Grinders, Skid Steer Attachments)

Stephenson Equipment, Inc. www.stephensonequipment.com Butler, PA 724-865-9221
Ebensburg, PA 814-886-5191 Harrisburg, PA (HQ) 800-325-6455 Wilkes-Barre, PA 866-667-6756
Modern Group, Ltd www.moderngroup.com Headquarters: 2501 Durham Road ï Bristol, PA 19007 855-299-7698 75 New Street ï Edison, NJ 08837 800-846-5840 112-128 Route 17 North ï Hasbrouck Heights, NJ 07604 800-233-0197
K e e p U p W i t h A l l t h e I n d u s t r y N e w s S u b s c r i b e t o C o n s t r u c t i o n E q u i p m e n t G u i d e To d a y ! Toll Free 8 0 0 / 5 2 3 - 2 2 0 0