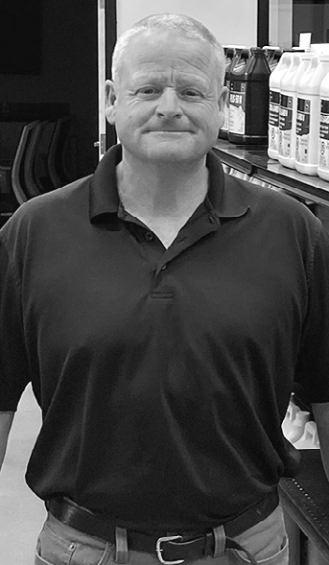
42 minute read
substantial completion should occur by Nov 2022. Sealand was awarded the contract on May 3, 2021. According to NYSDOT, the work being done is to overlay the existing deteriorated concrete
Page 30 ï June 22, 2022 ï www.constructionequipmentguide.com ï CONSTRUCTION EQUIPMENT GUIDE Five Star Equipment Names Territory Sales Mgr., Central N.Y.
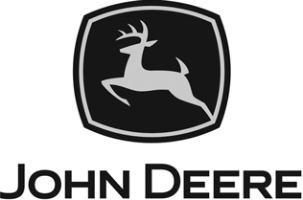
Jay Durand Five Star Equipment photo
Five Star Equipment, the John Deere distributor of central and western New York and central Pennsylvania, announced that Jay Durand has joined the company in the role of territory sales manager of central New York.
Durand is a seasoned professional with 30 years of experience working with contractors in matching up their needs with the proper equipment.
Durand prides himself on his ability to work closely with his customers and determine what options best fit their needs, whether it be rental, lease or purchase, and his ability to match the right sized machine to his customers’ project needs. He is fully versed in all the available mechanical and hydraulic attachments that dramatically increase the efficiency of carriers in many applications. Durand also is fully trained in all the latest automation and GPS technology.
“I’m really excited about representing the John Deere brand, a made in America product that is extremely well accepted in the marketplace and is a leader in the industry,” Durand said. “Five Star Equipment has come a long way in showing their commitment to central New York with their brand-new state-of-the-art facility in Syracuse.”
John Deere announced an expanded relationship with Wacker Neuson, a manufacturer of compact and construction machines, for 0 to 9-metric-ton excavators, to include North America.
John Deere and Wacker Neuson will collaborate on the development of excavators less than 5-metric-tons, including battery electric excavators, that will be manufactured by Wacker Neuson. Additionally, John Deere will have control of the design, manufacturing and technology innovation, for the 5-9-metric-ton models, leveraging a solid foundation from Wacker Neuson.
“Excavators are an integral part of our customers’ job sites, and we anticipate growing demand to continue,” said Domenic Ruccolo, senior vice president, sales, marketing and product support, global construction equipment, John Deere.
“As we look to the future of our excavator line-up, this agreement will allow us greater flexibility as we continue to deliver a robust product portfolio that prioritizes the operator
experience.” Distribution, parts, service and support will continue through the John Deere dealer network. “We’re excited about the expanded agreement as it supports our goal of bringing productivitydriven features and industry leading technology to customers with greater agility,” said Jerred Pauwels, vice president, excavators, strategy and business development, John Deere. “Through this relationship, we’ll innovate faster, and offer additional features and performance differentiation for our customers.” The Wacker Neuson Group is an international group of companies headquartered in Munich, Germany, employing approximately 6,000 people worldwide. As a leading manufacturer of light and compact equipment, the Group offers its customers a broad portfolio of products and a wide range of services. For more information, visit www.johndeere.com/. Understanding OSHA’s New Compliance Directive
The Occupational Safety and Health Administration (OSHA) has released a new compliance directive, CPL 02-01-063 for cranes and derricks. This directive replaces the 2014 compliance directive CPL 02-01057 and addresses the changes in the crane rule that OSHA made in 2018.
The new compliance directive only revises the existing section on operator training, certification and evaluation and leaves the other sections of the 2014 directive unchanged.
The focus areas of the compliance directive are: • When to initiate an inspection into an operator’s training, certification and evaluation • How to approach an inspection involving multi-purpose equipment and multiemployer work sites • How to determine whether the operator has received training that meets the requirements of the standard • What steps to take when inspecting the certification/license of an operator • How to address certification concerns such as fraudulent certifications or testing organizations not meeting requirements • When an employer would need to conduct additional evaluations for an operator
While compliance directives provide OSHA enforcement personnel with guidance on conducting inspections and policy on citing violations of the standard, the guidance and explanation can be helpful for employers.
At the NCCCO Foundation Industry Forum held in November 2021, OSHA provided the top 10 citations for cranes in construction for 2020-2021. Of these, three are related to the certification/qualification process for personnel: standard 1926.1427(a) — certification of operators; standard 1926.1425(c)(3) — Materials rigged by a qualified rigger; standard 1926.1428(a) — Signal person qualifications
The 2018 crane rule from OSHA provided a framework for establishing operator competency for the construction industry. The operator must be: Trained + Certified/Licensed + Evaluated = Qualified.
In the compliance directive OSHA states that there is no particular order in which an employer must comply with the training, certification and evaluation elements and further reiterates that should an operator not meet all three criteria, they are considered to be an “operator-in-training.” Operator-In-Training
Operator-in-training allows the operator to continue operating cranes when they are not yet certified/licensed or evaluated as required, but in such cases the operation must be under supervision of a trainer.
OSHA expects there to be a continuous cycle of training, certification and evaluation. As operators switch types of cranes, they may assume an operating-in-training status pending the applicable new certification. As changes in equipment and operating activities require different or higher levels of crane operating knowledge, skills and abilities, employers will need to ensure that the operator has been trained and evaluated in these areas.
While the standard does not require employers to create and maintain training records, compliance officers are directed to ask for training records, program materials and interview the employer and employees to determine what training was provided.
Employers should determine if the operator has been sufficiently trained by a prior employer or other means, such as a labor union, and is familiar with the crane(s) and its operations. OSHA recognizes that not all operators-in-training will be inexperienced operators or unfamiliar with the crane(s) and doesn’t require additional training by each employer if the requirement has already been met.
Lastly, OSHA points out that employers have a continuing duty to monitor the performance of their operators to determine whether retraining is necessary. Compliance officers are encouraged to conduct interviews to determine what steps the employer has taken to identify concerns about the operator’s ability to safely operate the crane and perform assigned tasks and what steps the employer has taken when such concerns have been identified.
Operator Certification/License
Once a determination is made that the equipment operated is within the scope of the rule (see 1926.1400) and that none of the exceptions of 1926.1427(a) apply, there are essentially four key questions on the flowchart provided by OSHA in the directive: • Is the operator certified/licensed? • Was the certification/license issued by an accredited testing organization, an audited employer program or compliant state or local government licensing program?
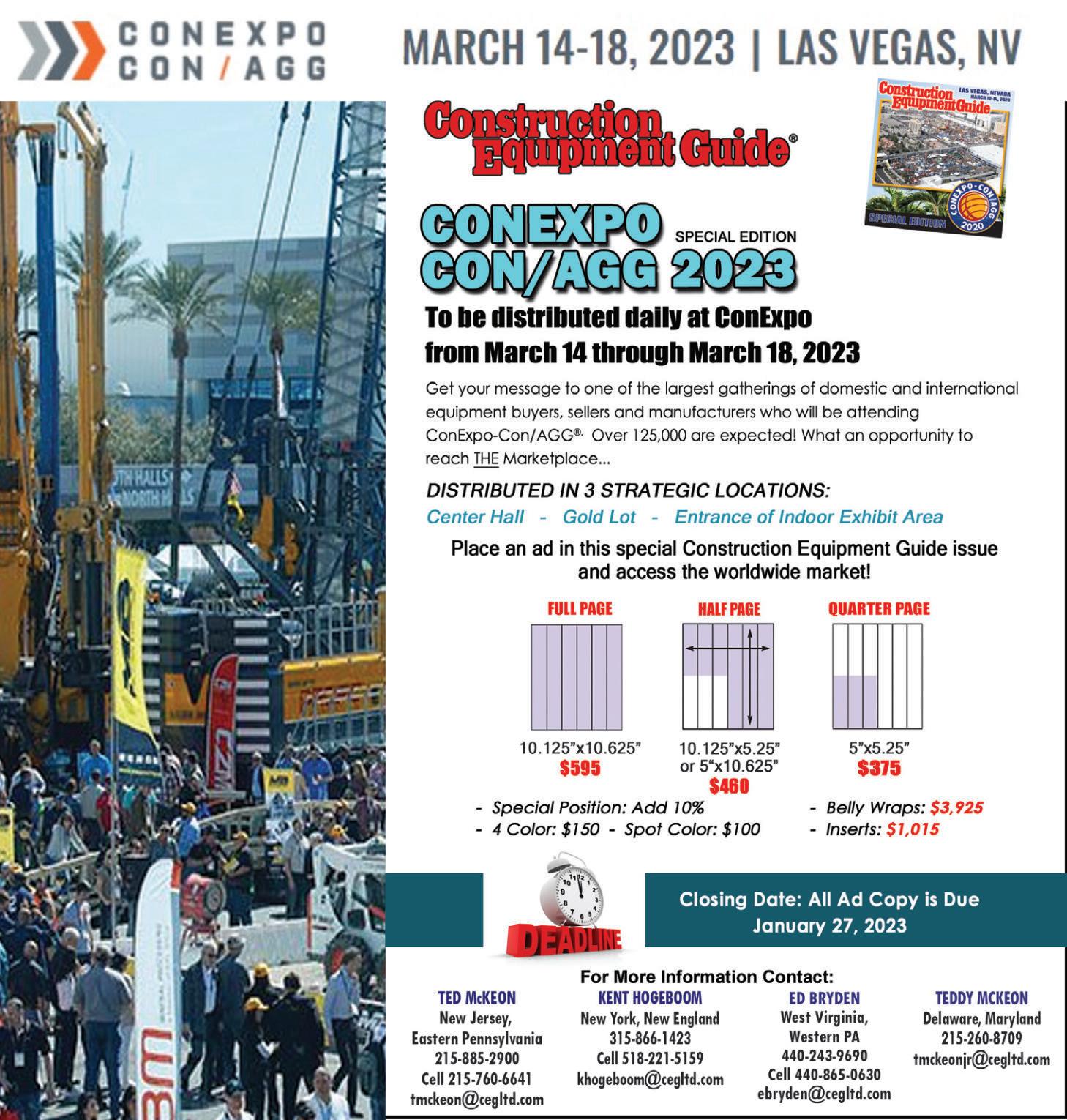
CHARGING from page 1
That would mean charging stations with a mile of major highways, easily located online or through an app.
The stations would be configured with enough outlets to avoid long waits to charge. User fees would be similar across the system.
Setting the Stage
According to the department of transportation, the proposed rule would establish the groundwork for states to build federally-funded charging station projects across a national EV charging network.
The standards also establish workforce requirements for installation, maintenance and operations to increase the safety and reliability of charging station function and use and create and support good-paying, highly-skilled jobs across the country.
Earlier this year, the Biden administration earmarked approximately $5 billion for states over the next five years to build out a national EV charging network.
“To support the transition to electric vehicles, we must build a national charging network that makes finding a charge as easy as filling up at a gas station,” said Buttigieg. “These new ground rules will help create a network of EV chargers across the country that are convenient, affordable, reliable and accessible for all Americans.”
The IIJA provides states with the funding and framework to build out a reliable charging network, said Stephanie Pollack, deputy federal highway administrator.
“This is a foundational step that will provide EV drivers with predictable access to reliable electric vehicle charging access across the United States.”
States will develop their EV deployment plans in concert with the Joint Office of Energy and Transportation, established by the infrastructure act.
The agency is providing direct technical assistance and support to states with the National Electric Vehicle Infrastructure program.
“We’re making sure that charging stations are easily and equally accessible, allowing every American to get coast to coast in an electric vehicle,” said Jennifer M. Granholm, secretary of energy. “The investments will not only build an interconnected national charging network, but also boost local economies and strengthen our independence from fossil fuels.” Big Picture
FHWA released other resources to help states complete deployment plans and access funding to build out the charging network.
These include new program questions and answers and a new tool to help evaluate the best locations for charging stations when it may not be possible to install at the required 50-mile intervals.
Charging stations would contain a minimum number and type of chargers capable of supporting drivers’ fast charging needs.
Additionally, rules would require consistency regarding the installation, operation and maintenance of projects to provide the traveling public with reliable charging expectations.
The proposed rule would further specify the required minimum density of provided chargers, payment methods and requirements for customer support services.
Proposed rules also will set strong certification standards for the workers installing, operating and maintaining electric vehicle chargers, said DOT, ensuring funds support good-paying, high-quality jobs and chargers are installed by a highly-skilled, professional workforce.
The proposed rule also will support workforce development and onthe-job training, “building the cleanenergy workforce of the future.” Other proposed requirements would help create a seamless national network of EV charging infrastructure that could communicate and operate on the same software platforms from one state to another. They would address traffic control devices and on-premise signage; data submittal requirements to help create a public EV charging database; and network connectivity requirements to allow for secure remote monitoring, diagnostics, control. Additionally, the FHWA proposes standardized communication of charging price and availability to help consumers make informed decisions about trip planning and when and where to charge their EVs. Building the Grid Ken Thomson of Facility Builders believes building EV charging stations enables the contractor to facilitate a host of people transferring their vehicular power away from fossil The proposed rule would establish guidelines for states to begin building EV charging stations. fuels and toward electricity. “As accessibility to recharging stations continues to grow, the momentum is apt to snowball.” The construction is relatively straightfor-
“We’re making sure that charging stations ward, he said. Most of the interfaces are prepackaged units available from several are easily and equally accessible, allowing suppliers. The contractor’s job is to set up the interevery American to get coast to coast in an face, ensure that all standards and safety regulations are met and work out parking and electric vehicle.” accessibility options with the station owner. “Comparatively, natural gas filling staJennifer M. Granholm tions are more complicated to construct, primarily due to accommodating the tank, con-Secretary of Energy trolling moisture content and the greater number of interfacing options to choose among.” Of course, details have to be worked out and choices made in the process of building. Whether the installation is public or private, residential or commercial, the number of parking spaces with access to charging interfaces must all be determined. One also has to calculate charging capacity, determine means of access and set the charging standard, he said. A private station is appropriate for commercial vehicle fleets and also for individually assigned use at residences or places of employment. Public accessibility implies the need for see CHARGING page 52
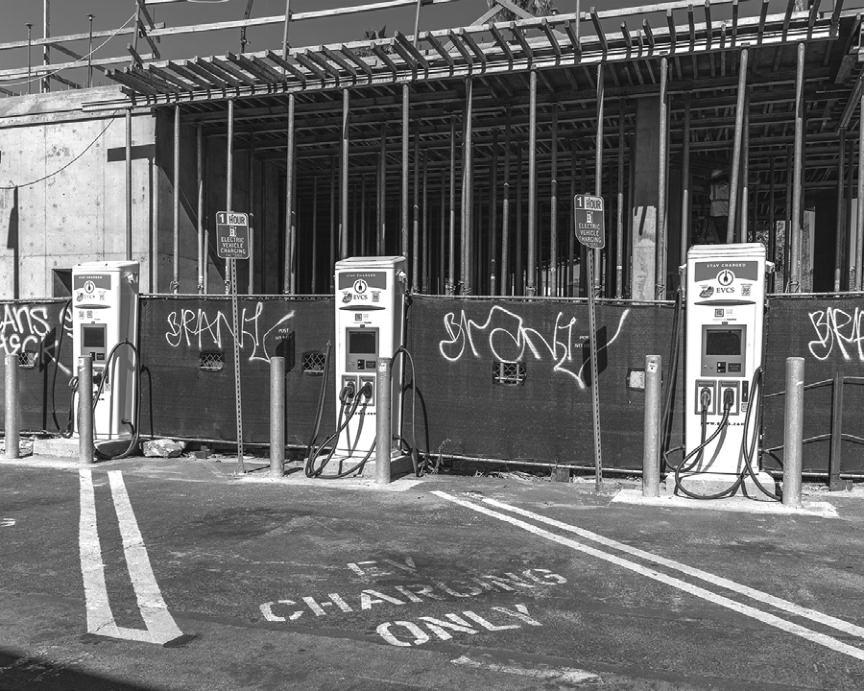
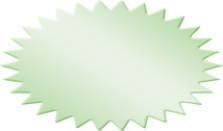
60 International Blvd • Brewster, NY 10509 845/278-7766 Fax: 845/278-4431 E-mail: dan@wtractor.com
Now Serving All of Connecticut
LATE MODEL EQUIPMENT
EXCAVATORS:
2013 BOBCAT E45, 2351 HOURS, CAB HVAC, MANUAL COUPLER, PLUMBED, RUBBER TRACKS .... ..................................................................................................................................................$49,995 1978 JOHN DEERE 690B, 7840 HOURS, CAT CONTROLS ..........................................................SOLD 2012 KOBELCO SK170-9, 3690 HOURS, CAB HVAC, COUPLER & THUMB, REAR CAMERA, 36” BKT ..................................................................................................................................................$98,995 2016 KOBELCO SK85, 1235 HOURS, CAB HVAC, PLUMBED, MANUAL COUPLER ................$79,995 1995 SAMSUNG SE280LC2, 9723 HOURS, 2 BUCKETS, NEWER BOTTOM, CUMMINGS ENGINE .......... ........................................................................................................................................................$30,000 BACKHOES:
2009 NEW HOLLAND B90B, 2650 HOURS, EXTENDAHOE, CAB W/HEAT....................................SOLD 2000 NEW HOLLAND LB75, CAB W/HEAT, 7700 HOURS, 4WD, FLIPOVER FORKS, UB 1000 LB HAMMER ....................................................................................................................................$29,995 TRACTORS:
2015 KUBOTA MX5200, TRACTOR W/LOADER & BHOE, 100 HOURS, LIKE NEW ..................$49,995 CHIPPERS:
2020 MORBARK 1215, GAS GM, PSI ENGINE, 89 HP, 12” DRUM, AUTO FEED, 94 HOURS ......SOLD WHEEL LOADERS:
2007 KAWASAKI 70TMV, CAB, HVAC, 2208 HOURS, 3.25 YD BKT, COUPLER, FORKS, TOOL CARRIER MACHINE ................................................................................................................................SOLD NEW HOLLAND LW170B, 3YD BKT, JRB COUPLER, CAB HVAC, CAB HAS RUST/ROT. MAKE AN OFFER ......................................................................................................................................$40,000 SCREENERS:
2018 VIBROSCREEN SCM40C BOX SCREENER W/CONVEYOR ............................................$129,000 2021 VIBROSCREEN SCM40, NEW ..........................................................................................$79,995 2021 VIBROSCREEN SCM27, NEW ..........................................................................................$45,000 NEW VIBROSCREEN SCM75C BOX SCREEN W/CONVEYOR, TIER 3 ENGINE ......................$165,000 NEW VIBROSCREEN SCM115T TROMMEL, NO DPF, NO DEF ..............................................$150,000 2018 VIBROSCREEN SCM115T TROMMEL, 400 HOURS, NO DPF, NO DEF..........................$123,500 SKID STEER LOADERS:
2012 NEW HOLLAND L223, 2549 HOURS, CAB HVAC, PILOT CONTROLS, 2 SPEED ............$37,995 2017 NEW HOLLAND L220, 217 HOURS, CAB HVAC, PILOT CONTROLS, 2 SPEED, JUST SERVICED ......................................................................................................................................................SOLD 2018 KUBOTA SSV75, 184 HOURS, CAB HVAC, PILOT CONTROLS, 2 SPEED, 1 YEAR WARRANTY LEFT ..............................................................................................................................................SOLD
MISCELLANEOUS:
2001 BOMAG 156-3 VIBRATORY ROLLER, OPEN CAB, SINGLE 57” DRUM, 1704 HOURS, 6.5 TON VIBRATORY ....................................................................................................................................$34,995 2014 DOOSAN DXB260 BREAKER, 8500 LBS, FOR DX350, HAMMER TOP FOR PIN GRABBER $35,000 GROUSER TRACKS FOR SKID STEER, MODEL 14740F-9, FITS TIRE SIZE 12X16.5 ....................$2,500 2014 JCB 510 TELEHANDLER, 3200 HOURS, OPEN CAB, 55.9’ REACH, 10,000 LB LIFT, SOLID TIRES ........................................................................................................................................$57,995 2021 LANDPRIDE 50” REVERSE TILLER, 3 PT MOUNT ............................................................$2,880 KOBELCO SK170
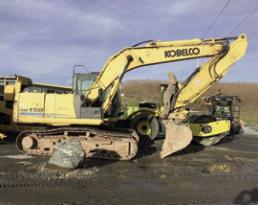

VIBROSCREEN SCM75C
See dealer for financing details. CNH Capital America LLC standard terms and conditions apply. Subject to customer credit qualifications. CNH Capital America LLC reserves the right to cancel any program without notice.
VISIT OUR WEB SITE AT WWW.WTRACTOR.COM
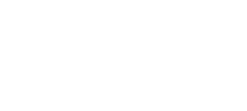


s ortuibrt
7021 Performance Drive N. Syracuse, NY 13212 800-342-7575
12 Mear Road Holbrook, MA 02343 508-868-7734 9 Finderne Avenue, Ste 7 Bridgewater, NJ 08807 908-203-0400
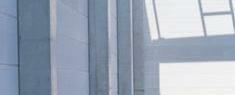
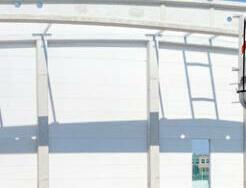

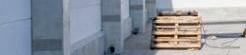
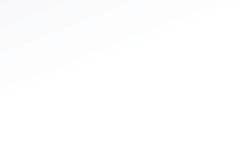
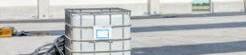
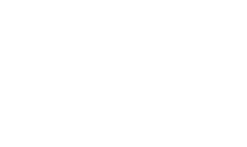
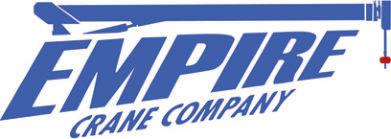
w w w .em pirecrane.com
SEALAND from page 1 pavement with asphalt to restore rideability and prevent deterioration of the entire pavement structure. The work currently going on is the second season of a two-season construction job. The project’s first season completed the same stretch of I-390 but in the northbound lanes.
Interstate 390 is a critical thoroughfare that connects the greater Rochester region and New York’s Southern Tier communities.
This section of I-390, constructed around 1976, has two lanes in each direction, with a shoulder on each side.
The funding for the project was provided by New York State and is part of the Statewide Transportation Improvement Program (STIP).
The road work is utilizing a method called “cracking and seating,” an innovative engineering technique that reuses the existing subbase for paving. It is projected to be 15 years before this stretch of road will need its next surface treatment.
“Safety is always the top priority at NYSDOT,” said NYSDOT Public Information Officer Joe Leathersich. “With this work zone, as with any work zone, it’s imperative that motorists slow down and pay attention to keep our crews and themselves safe.”
So far, Sealand has completed the northbound side of the project.
“The job is broken down into phases,” said Steve Howe, Sealand’s project manager. “We’re in the second year. The northbound side is pretty much complete, except for a little bit of guiderail work and signs and miscellaneous work.”
Crews are working on the southbound lanes.
‘The brunt of this job deals with heavy materials — most of the money is going into paving,” said Howe. “You also have fulldepth boxed out areas. We’re putting in underdrain in limited areas to help with drainage. There is also new guiderail going in some areas, and we’re doing a crack and set operation for the concrete highway. You just crack it about every two feet, clean it up and pave over it with three lifts of asphalt — six inches in total.
“The biggest challenge on this job is just coordination, trying to keep activities moving from one end to the other,” he added. “When you’re working on an expressway like this, you always have a crash truck with your crew. If I have a survey taking place, with people walking down the road and laying out spacing, you have to protect them. We’ll have 10 to 12 crash trucks out there when we’re busy, just staying behind everybody”
Crews have plenty of workspace in some areas.
‘It’s a long job we’re doing here,” said Howe. “It’s 10 miles on the southbound side this year. You can stretch this out, but you are limited on your closures and the state doesn’t want you to close a mile stretch of road and then open it up for 0.5 a mile, and then close it for another mile. There is room for equipment and materials. It has 12-foot lanes and 12 and 10-foot shoulders. We do have cars and trucks running next to us, so we have to be careful at all times.
“Our crews are doing a good job,” he added. “This year is going much better than last year. The project was awarded a little bit late, so we didn’t get started first thing last spring and we were working right into December. We can’t do this for this season. We have to place the top down and the road has to be striped before it gets cold. We had a much better start this year.”
There are no serious utility issues and there is no deep excavation. The underdrain installation has crews digging down 3 ft. and the full-depth boxed out areas are only digging a few feet. Nearly 95 percent of the work is being done via day shifts, with night work focusing on a couple of ramps that have to be milled and paved.
Howe is working with NYSDOT’s engineer-in-charge for the state.
‘We get along fine,” he said.
The work plan is based on closing one lane and working on it.
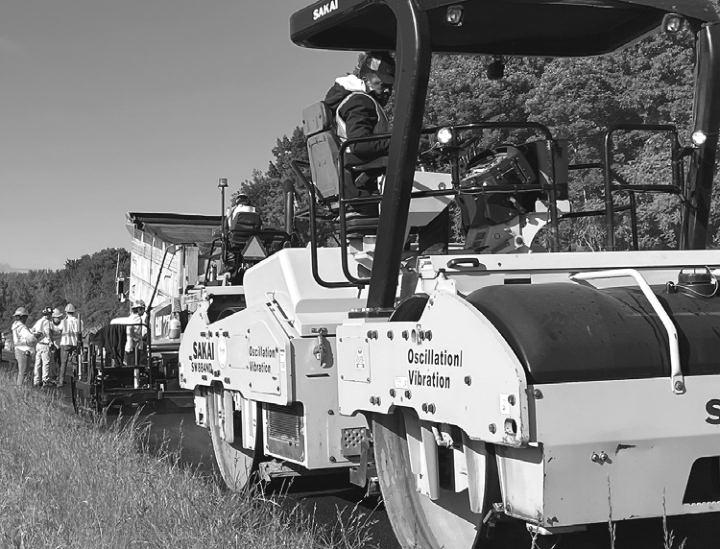
Peak days have approximately 100 Sealand and subcontractor personnel on site.
see SEALAND page 48
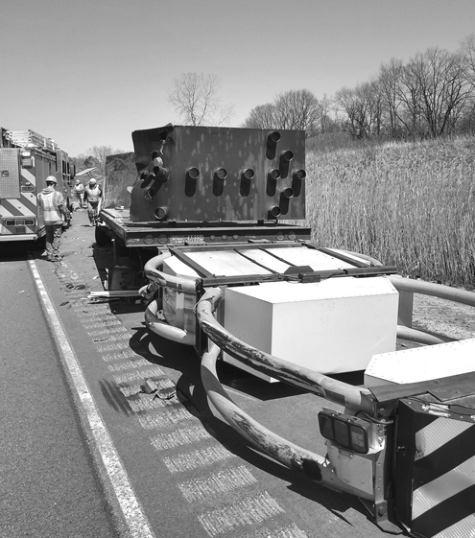
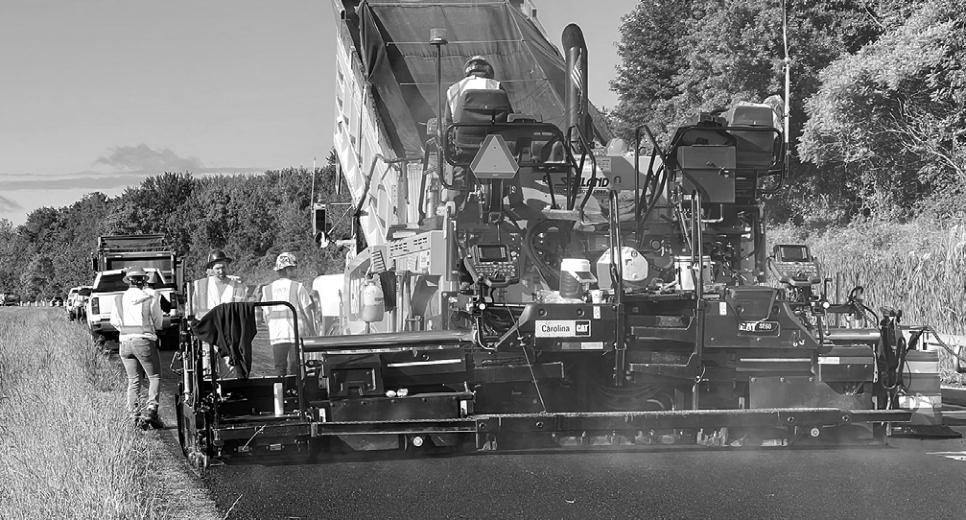
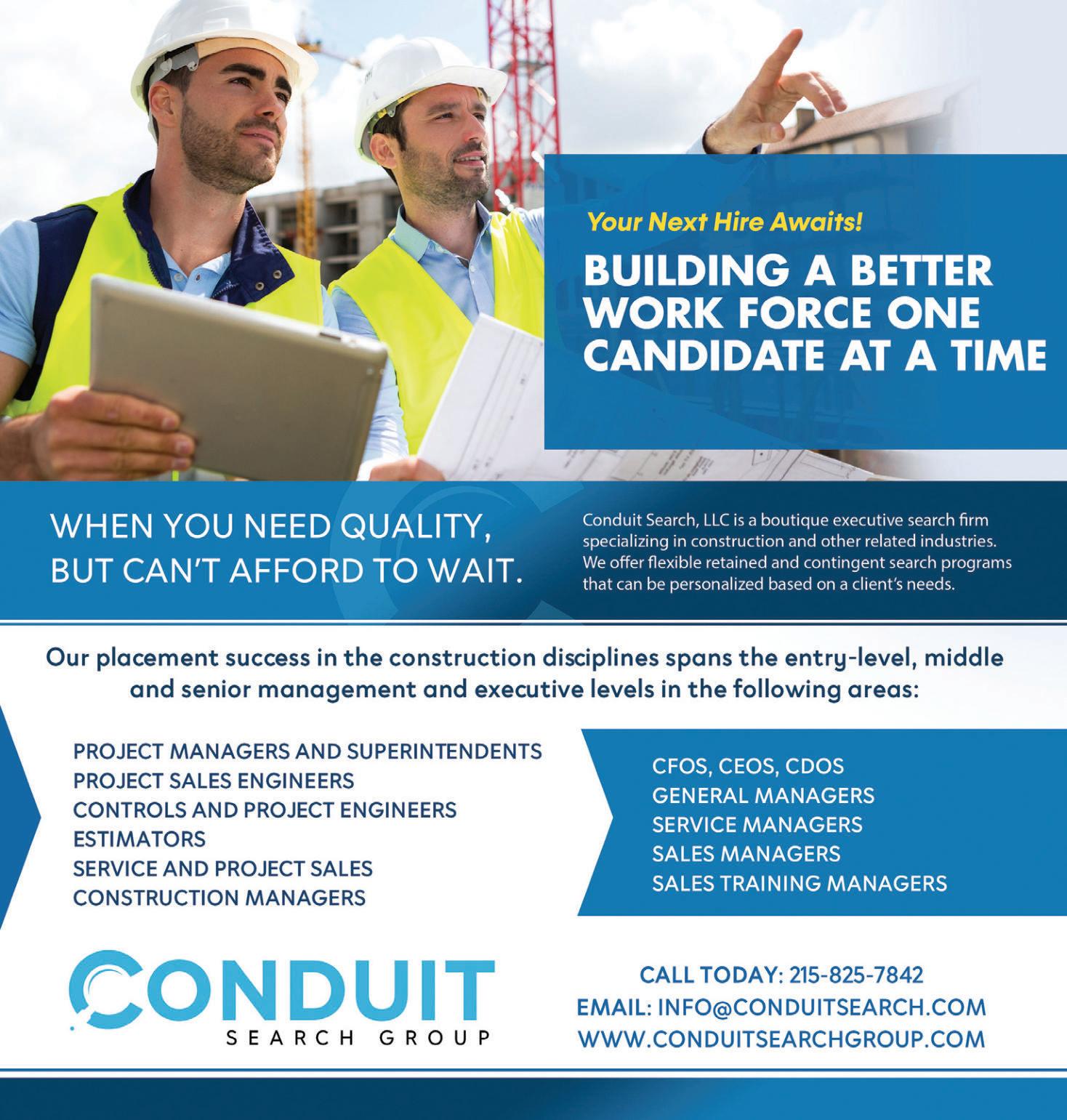
Page 44 ï June 22, 2022 ï www.constructionequipmentguide.com ï CONSTRUCTION EQUIPMENT GUIDE Caterpillar Announces Multi-Year Sponsorship of Major League Soccer
Caterpillar Inc. announced a multiyear sponsorship with Major League Soccer (MLS), the fastest growing sports League in North America.
With the highest percentage of millennial and multicultural fans of any U.S. sport, the sponsorship is designed to amplify the Caterpillar brand to a broader, more diverse audience in the United States and Canada and to engage with the League’s passionate fans more deeply.
“Caterpillar is eager to partner with Major League Soccer, as we share a joint commitment to being leaders in the communities where we live, work and play,” said Yvette Morrison, global director of marketing and brand of Caterpillar.
“We celebrate the people who do the work every day and are constantly looking for new ways to engage with our next generation of employees, customers and their families. This sponsorship provides a perfect opportunity for us to introduce Cat to a broader audience.”
“Caterpillar is a leading, global brand and Major League Soccer is honored to partner with a company whose values and dealer network are committed to building a better, more modern future for soccer communities across the world” said Carter Ladd, executive vice president of brand alliances and consumer products at MLS.
“Together, MLS and Caterpillar will engage long-standing customers and the most diverse fanbase in all of sports to positively impact the sport of soccer in the U.S. and Canada.”
MLS features the youngest and most diverse player pool of any of North American professional sports league with players from more than
82 countries. The sponsorship of MLS supports Caterpillar’s efforts to evolve the brand, and ensure the company is representative of the many employees and customers it serves. As a part of the sponsorship, MLS will collaborate with Caterpillar to integrate Cat products into the soccer ecosystem. Cat dealers also will have access to exclusive soccer experiences for their operators and customers as well as their families. Caterpillar recently collaborated with MLS in development of Cat Trials 12: No Hands, which features U.S. and International Federation of Association Football (FIFA) World Cup soccer legend, DaMarcus Beasley, teaming up with autonomous Cat equipment to make a trick shot. The Cat Trials 12 video can be viewed at http://www.cat.com/trial12. Doosan Names Top-Performing Dealers of 2021; Four Northeast Dealers Earn Kudos
Doosan Infracore North America announced its top-performing dealers of 2021. The top 10 dealers are among more than 170 Doosan construction equipment dealers in North America.
Doosan annually recognizes its heavy equipment dealers that have excelled in providing top-level performance in sales, parts and service to customers in their respective markets.
The following enterprises are the top 10 Doosan dealers of 2021 (headquarters in parentheses): • Barry Equipment Co. (Webster, Mass.) — fifth consecutive year • Best Line Leasing Inc. (State College, Pa.) • Bobcat of Mandan Inc. (Mandan, N.D.) — fourth consecutive year • Brown’s Industrial Sales (Lloydminster, Alberta, Canada) — second consecutive year • Capital Tractor Inc. (Greenwich, N.Y.) • CG Equipment (Guelph, Ontario, Canada) — third consecutive year • G. Stone Commercial Division (Middlebury, Vt.) — second consecutive year • Ironhide Equipment Inc. (Grand Forks, N.D.) • Paul Equipment and Sons (Balmoral, New Brunswick,
Canada) • Westerra Equipment (Abbotsford, British Columbia,
Canada) Top Doosan Dealer of 2021
Barry Equipment was the overall top-performing Doosan dealer in North America in 2021. The company was founded in 1985 by Tom Barry and has been a Doosan dealer since 2004. In early 2022, Barry Equipment announced a new location in South Windsor, Conn., complementing two locations in Webster, Mass. The company serves customers in Massachusetts, Connecticut and New York.
“We’re pleased to recognize our top-performing Doosan dealers of 2021,” said Todd Roecker, vice president of growth initiatives, Doosan Infracore North America.
“Our dealer network has made exceptional strides in growing the Doosan brand, as evidenced by the number of dealers being recognized for multiple years of excellence. We’re also pleased to see new dealers on this list who are helping us grow and expand in new territories.”
Top-performing Doosan dealers may choose from a selection of several incentives that will improve their profitability when selling and servicing Doosan equipment. In addition, Doosan North American leadership may look to these dealers for valuable input regarding Doosan initiatives and direction because they represent the dealer network well.
For more information, visit na.DoosanEquipment.com.
LiuGong Reveals Finance Program
LiuGong North America has announced a new private label program to become a one-stop shop for equipment and financing. The new LiuGong Finance program will serve customers and dealers with a multitude of benefits.
“As we continue to help support, grow and develop our customers and dealer network, we’re delighted to introduce LiuGong Finance,” said LiuGong North America President Andrew Ryan.
“We’ve built the LiuGong Finance program to include several components that will benefit our customer and dealer network and their businesses.”
LiuGong Finance will provide dealers with finance support for both LiuGong North America and non-competing products. Additionally, it will enable dealers to utilize competitive rates and flexible finance structures under a captive finance program. This helps to create a customer loyalty that can lead to future sales.
Dealers and end users will have access to a dedicated finance team.
LiuGong Finance offers both retail financing and dealerowned rental fleet financing under the program. There are three types of retail financing included: FMV lease, equipment loan and custom structures. There are two types of dealer-owned rental fleet financing offered: rental equipment loan and custom structures.
For more information, visit www.liugongna.com. Award Worthy... ARTBA Hands High Honor to President Biden, Sen. Portman
President Joe Biden and U.S. Senator Rob Portman (ROhio) are the 2022 recipients of the American Road & Transportation Builders Association’s (ARTBA) highest honor — the “ARTBA Award.”
The award was given May 17 in Washington, D.C., during ARTBA’s 2022 Federal Issues Program and Transportation Construction Coalition’s (TCC) Fly-In.
Established in 1960, the ARTBA Award recognizes outstanding contributions that have advanced the broad goals of the association. Recipients have included governors, more than 25 U.S. senators or representatives, two U.S. secretaries of transportation, and dozens of top leaders and executives from government and the transportation construction industry private sector.
The president and senator are recognized for their leadership and willingness to work across the aisle to complete the landmark Infrastructure Investment and Jobs Act (IIJA). The November 2021 enacted law includes a five-year, $450 billion reauthorization of federal highway, public transit, and highway safety programs. It represents the largest increase in federal surface transportation investment in 65 years.
For more information, visit www.artba.org.
For a new apartment complex next to North Side Pittsburgh’s Garden Theater, Bill Gatti wanted to go with the latest state-of-the-art building material that is proving to be all the rage in the industry.
Wood.
Not two-by-fours, mind you, but cross-laminated timber, which Gatti and his firm, Trek Development Group, based in the Steel City, wants to help reduce carbon footprints in the area.
Cross-laminated timber panels look like giant sheets of plywood but offer much more — a green alternative to traditional building materials like steel and concrete.
That is what caught Gatti’s attention.
“It’s considered a very green solution,” he explained to the Pittsburgh Post-Gazette. “We’re always trying to push the envelope as much as we can with green technology.”
Gatti believes the 6 West North project may be the first, or at least one of the first, in the region to take advantage of the material.
Cross-laminated timber panels are made by gluing together pieces of wood cut from trees. The pieces are stacked in alternating directions and pressed together for strength. In fact, the finished product is strong enough to replace steel and concrete as building materials, even in taller buildings.
For the 6 West North project, Trek will be using a mix of steel, concrete and cross-laminated timber, with the timber component reserved for the building of ceiling and floors, according to the Post-Gazette.
In addition to the green benefits, the apartment complex will give renters of the planned 45 units an exposed wood ceiling in their bedrooms and living rooms. The floors, however, will be covered for acoustical reasons.
In all, about 20 percent of the five-story building will be made up of cross-laminated timber, said Kevin Wagstaff, a principal at the Perfido Weiskopf Wagstaff + Goettel architectural firm in Pittsburgh.
“We’re hoping that people will leave their blinds open, and will look up and see the wood ceilings,” he said.
Gatti said Trek and Q Development, another Pittsburgh company and Trek’s partner on the project, decided to do a “hybrid” form of construction in an effort “to balance practicality and innovation as best we can.”
He noted that using the cross-laminated timber will cost an additional $600,000.
But while the technology won’t save Trek and Q money, Gatti explained that “it’s a green technology and it’s aesthetically appealing. That was the driver for us.”
Trek is open to using it in future projects as well, he told the Post-Gazette.
“I think we’re going to see how it looks, how the market receives it, and how it performs, and consider using it more,” Gatti said.
Cross-laminated timber has been used on scores of other projects around the world.
They include an apartment building in Milwaukee, a recreation center at Clemson University in South Carolina, a 10-story residential building in London, an ecology education center in Maine and a five-story retail and office space in Denver.
Efforts Under Way to Rehab Garden Theater Area
Pittsburgh’s 6 West North complex, at the corner of Federal Street and West North Avenue, will feature a mix of one- and twobedroom units. The one-bedrooms will start at approximately $1,500 a month.
It is being built on vacant land that housed three Victorian-era structures that were demolished in 2019 by the Pittsburgh Urban Redevelopment Authority (URA) after being condemned by the city.
Construction on the new building is expected to be completed in February.
Trek and Q originally had planned to convert the 8,371-sq.-ft. Morton House next to the new apartment complex into six residential units.
But those plans changed when crews discovered structural flaws, including crumbling brick, that made the building unsafe to be occupied, Gatti said.
“It was like being held up by popsicle sticks,” he said. “There was just too much damage.”
After consultations with the URA and historic groups, Trek decided to demolish Morton House — which was made up of a pair of side-by-side structures — and build anew at the site.
Gatti described the situation as an “unexpected setback” in the development team’s plan for the block.
“Everyone wants to save historical buildings,” he noted. “But [there comes] a point that they’re not viable anymore.”
Michael Sriprasert, president of the Pittsburgh History and Landmarks Foundation (PHLF) and a consultant on the Garden Theater block development, said all the consulting parties agreed that the Morton House could be razed due to safety concerns.
At the same time, PHLF “strongly advocated for reuse of as much of the building materials as possible,” an idea that Gatti said the developers are hoping to carry out.
In place of the Morton House, Trek and Q will build a three-story structure with 10 apartments.
Combined, the two new buildings built on the adjacent sites will cost more than $20 million, Gatti told the Pittsburgh news source.
The Post-Gazette reported that at the Garden Theater, a former adults-only venue acquired by the URA in 2007 after a lengthy legal battle, Trek and Q are constructing three apartments on the mezzanine level.
They also are trying to lease 5,000 sq. ft. of retail space on the first level. The two development firms have been talking to restaurants and other vendors about moving into the space.
“We’re thinking it’s probably going to be a restaurant,” Gatti said.
As part of the Garden Theater project, Trek and Q refurbished and reinstalled the venue’s sign, which spells out “Garden” and has served as a neighborhood beacon for decades
Rendering Courtesy of Garden Theater Block website The new, mid-rise building will house 46 one, two and three bedroom living options. 6 W. North will be on the corner of W. North and Federal Street, connecting the Garden Theater and The Morton House.
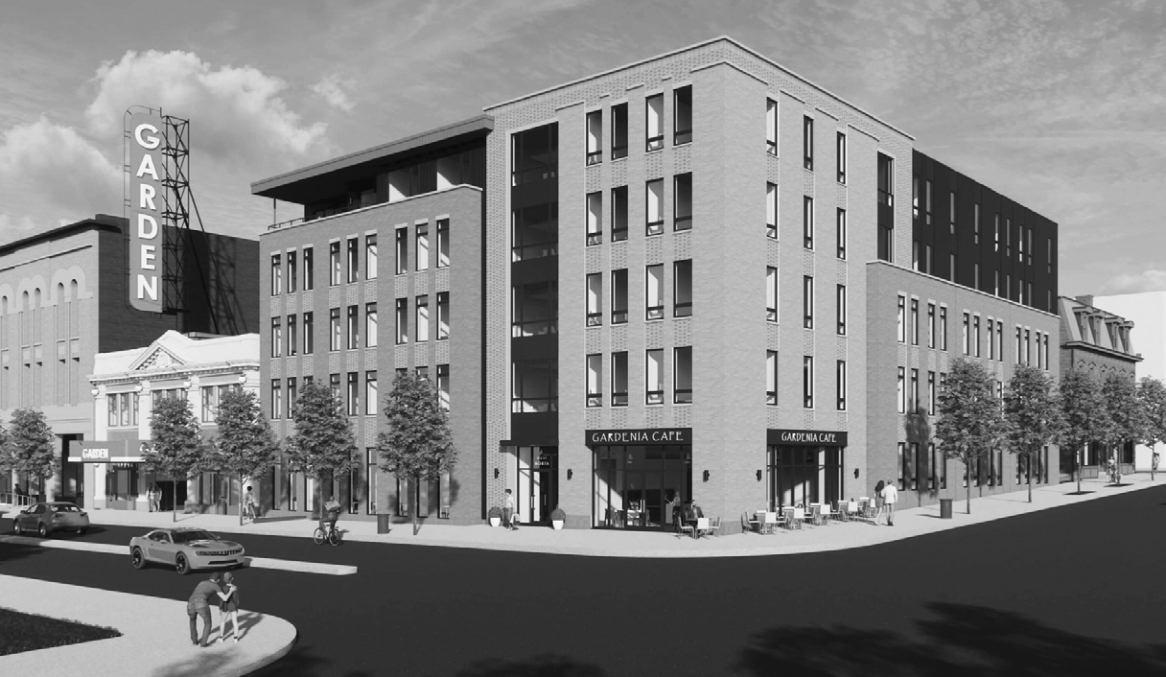
SEALAND from page 36
“I wish we they would put crossovers in and let us have a closed work area,” said Howe. “I’ve done that on previous jobs and it was safer and faster. I’ve broken the job into three areas of three-plus miles in each phase. We’re working on the first phase right now and we have three boxed out areas. We boxed out one side, did the paving and then moved the barrier and do the same thing on the other side. These are all your full-depth repair areas.”
The crews are honing their work via the repetitive nature of the project.
The concrete highway is in fairly good shape.
“I’ve driven down I-390 for quite a long time — they’ve done tons and tons of repairs before we even started this project where contractors would excavate small areas and do repairs,” said Howe. “We’re doing a few repairs, but not many. We just crack the concrete, do a couple of minor repairs and pave over it. We’re doing the underdrains at the same time as the boxed-out areas. They want the underdrains in 14 days before you do any cracking to help get rid of the water that been pooling around the concrete.”
A serious amount of milling is taking place and equipment operators are using Wirtgen milling machines and Caterpillar 335 and 225 excavators with 48-in. buckets are helping to excavate the fill-up areas. There are many miniexcavators on site, such as Volvo 190s and Komatsu PC139s. Caterpillar 950 loaders are proving valuable.
‘We have an aggressive schedule this year and we got a lot of preliminary work done,” said Howe. “We have 120,000 tons of asphalt to do this year on the south side.”
Rochester Asphalt Materials is supplying the asphalt.
Assisting Howe are superintendents Sean Stewart and Norm Ahrens.
“We’re working well together,” said Howe. “Sean [Stewart] is a new guy with Sealand. He didn’t have a lot of experience doing roadwork. He used to build big concrete water tanks for cities. He has a lot of experience with personnel and safety. We have some very good foremen and the crews take pride in their work.”
Peak days have approximately 100 Sealand and subcontractor personnel on site. The main subcontractors are Pavilion for crack and seat concrete; Donnagle for milling; Phelps Guiderail for signs and guiderail; O.H. for striping; Natural Restorations for landscaping; and DiKat for electrical.
Excavated materials should yield 25,000 tons of concrete, and 15,000 tons of earth and rock. New materials include 80,000 tons of embankment and 240,000 tons of asphalt.
Additional equipment includes Broce brooms, Sakai rollers, a Barber Green paver, a Barber Green widener, Komatsu dozers and a Caterpillar 950 loader.
“On any construction job, maintenance is ongoing,” said Howe. “You never know what is going to break. The most common breakage is hydraulic lines and we’re rushing off to get new ones. We don’t have a mechanic that stays on site full-time. Sealand has three or four projects going on at any one time. When we do mainline paving, you can have 20 trucks running up asphalt. It’s a lot of wheels turning, so you need someone close if something breaks. There is no waiting. It has to be fixed immediately.”
Howe has been a project manager for 25 years and appreciates proper maintenance.
“You need really good mechanics,” he said. “We run this equipment hard all summer as construction in New York is pretty limited — you have a small window to get the work done. So, in the winter months, the equipment goes to the
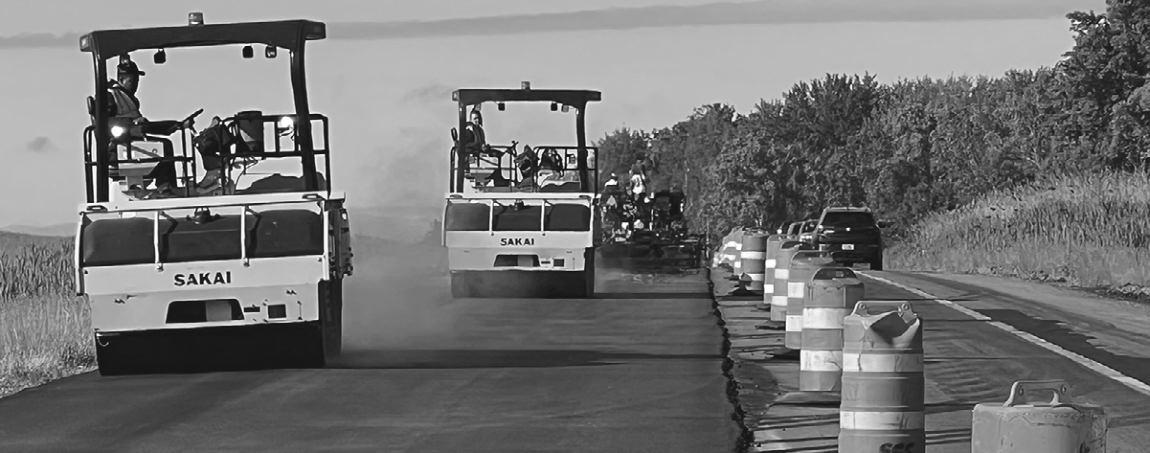
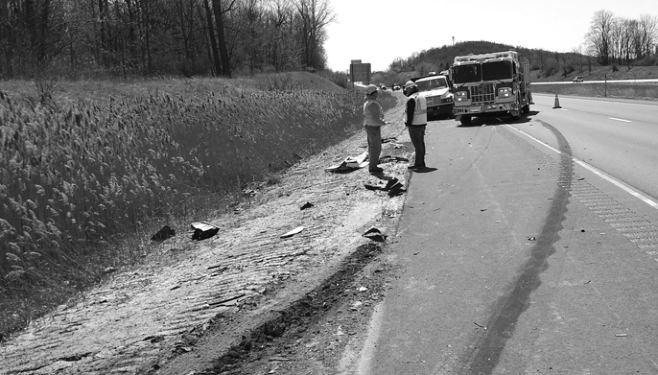
The New York State Department of Transportation (NYSDOT) is investing $32 million to resurface and improve 44 lane mi. of I-390. shop and that is where a lot of the key maintenance comes into play. They have to make sure everything is fine-tuned for the following season. ‘You also have to grease the equipment every day and check your fluid levels,” he added. “The operators let us know if they see something is wrong and we get a mechanic out there.” (All photos courtesy of Sealand Constructors Corp.) CEG “When you’re working on an expressway like this, you always have a crash truck with your crew,” said Steve Howe, Sealand’s project manager. “If I have a survey taking place, with people walking down the road and laying out spacing, you have to protect them.”
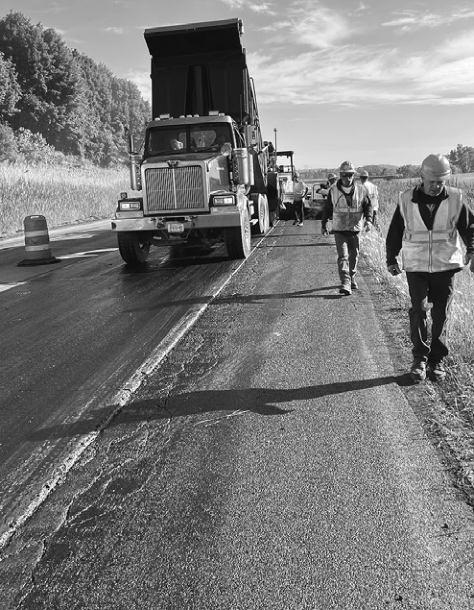
Page 50 ï June 22,2022 ï w w w .constructionequipm entguide.com ï C O N STR U C TIO N EQ U IPM EN T G U ID E Volvo CE Delivers Its First Fossil-Free Steel Articulated Hauler to Customer
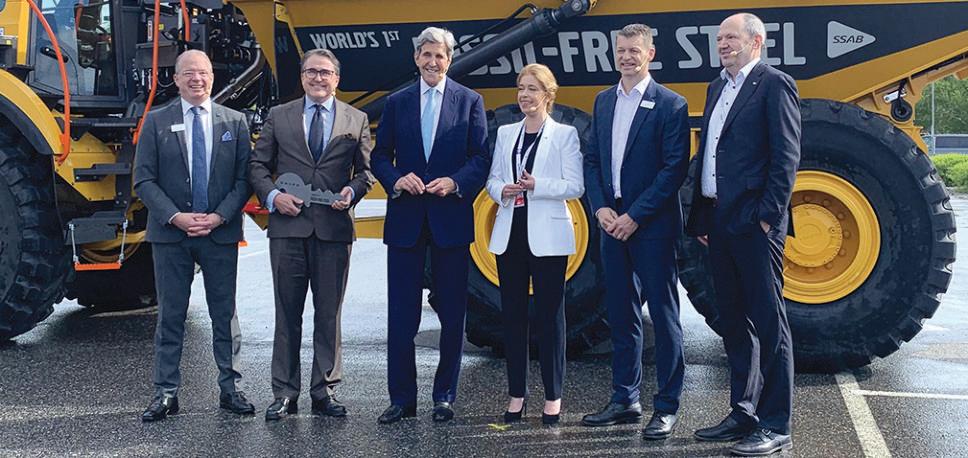
(L-R) are Martin Lundstedt, Tomas Carlsson, John Kerry, Annika Strandhäll, Melker Jernberg and Martin Lindqvist.
In the latest step on its path toward carbon neutrality, Volvo Construction Equipment (Volvo CE) became the first manufacturer to deliver a construction machine built using fossilfree steel to a customer.
This demonstrates the fast-tracking of innovation to real-world solutions as companies across the value chain come together to drive change, the company said.
The A30G articulated hauler built using fossil-free steel was handed over by Volvo CE President Melker Jernberg to long-standing customer NCC on June 1, 2022, at a ceremony hosted by LeadIt — the Leadership Group for Industry Transition — in conjunction with the United Nations environmental meeting Stockholm +50. It was attended by John Kerry, US Special Presidential Envoy to Climate and Annika Strandhäll, Swedish Minister for Climate.
The move comes just nine months after the company unveiled the world’s first vehicle concept using fossil-free steel, as part of the testing of the implementation in an ordinary production setup.
While commercial introduction is expected to be gradual with selected customers, this speedy first handover is an important milestone in the group’s ambition to drive industry transformation towards global climate goals.
The A30G is produced at Volvo CE’s Braås facility in Sweden, using the existing manufacturing process, with fossil-free steel from Swedish steel company SSAB.
Jernberg said, “We are sure that to succeed in decarbonizing the construction industry, actors in the value chain will need to collaborate and act. Thanks to our strong partner-
The A30G articulated hauler is made from fossil-free steel provided by partner SSAB. ships with other driven and forward-thinking companies, we are now able to lead the change towards fossil-free construction and be the first to deliver a machine built using fossilfree steel to a customer. Turning commitments into actions is key to building the world we want to live in.” Tomas Carlsson, CEO and president of NCC, said, “NCC has a firm commitment to contribute to sustainable development. We are working determinedly and systematically to reach that target, which includes selecting machines that live up to our high demands. As demonstrated in this great example, it takes strong and proactive partnerships between several players to make the sustainable shift possible.” As part of its Science-Based Targets commitment, Volvo CE is set to achieve net-zero greenhouse gas emissions by 2040. Alongside the electrification of its machines, the company recognizes the importance of reducing its carbon footprint across its entire value chain. This includes the raw materials used in its products, of which steel is a major component. The production using fossil-free steel in Volvo CE’s machines and components will be gradual and depend on aspects such as steel availability. For more information, visit www.volvogroup.com.
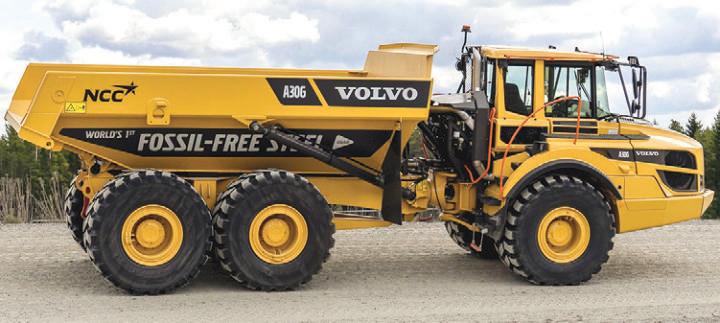
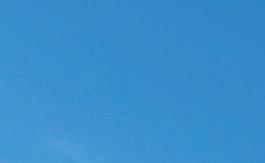
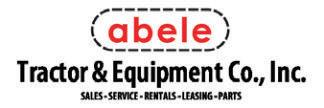
72 Everett Road Albany, NY 12205 518-438-4444 abeletractor.com
460 Main Street Spencer, MA 01562 508-885-7085 10 West Road Hudson, NH 03051 603-324-1164 ahearnequipment.com
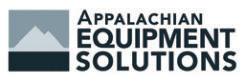
1750 Hackers Creek Road Jane Lew, WV 26378 304-786-9587 aesolutionswv.com
70 Upper Main Street Essex Junction, VT 05452 802-872-2666 ccrsalesvt.com
Ken Thomson Facility Builders
CHARGING from page 34 an interface equipped with a universal form of billing.
Public stations also need to provide more than one charging level option.
“Often when a new technology is introduced into an existing environment, some amount of alteration is necessary,” said Thomson.
In the case of bringing EV charge capability to a building, one may be laying extra conduit, adjusting electrical loads and changing parking assignments.
For multiple users, such as in a condominium or office building, additional measures might mean individualizing power usage records.
“Construction contracts in such cases need to spell out the terms of tenant improvements, especially if uninterrupted continual use of the space during construction is required.”
Other issues EV charging station owners should discuss with their general contractor include off-grid solutions, which can be installed under certain circumstances.
Examples are solar panels mounted on carports, rooftops or stand-alone structures.
“In some cases, unused power can be sold back to the utility,” said Thomson. “Another option is to connect to a special EV network grid, the power for which is 100 percent from renewable energy sources.”
For on-grid applications, it may be possible to implement a “smart grid” arrangement whereby charging is reduced at peak load hours or initiated at low-cost times.
It’s crucial for all types of businesses to think about how they can become part of the new fueling network, believes ChargePoint, an EV infrastructure company.
Rich Quattrini, vice president of customer solutions, said fuel retailers face a particularly urgent need to modernize operations to remain relevant and expand revenue generation opportunities.
“Organizations need to carefully choose and design their fuel retailing sites, especially when it comes to DC fast-charging,” said Quattrini.
Before even getting started with site design, though, a contractor will want to fully understand what to plan for. Here are Quattrini’s seven suggested considerations: 1. How much electrical supply will be needed?
Based on location and the volume of EV charging expected, the charging partner and utility can help estimate and request the type of electrical service and amount of power from the utility. 2. How much space is available for infrastructure?
Along with evaluating electrical needs, the amount of space available where that space is relative to other infrastructure, must be considered. Scaling to serve and provide fuel for a whole new set of drivers, think about where to put new electrical panels, remote power cabinets, conduit runs and the charging stations themselves. 3. What are the accessibility laws in the area? How will path of travel be accounted for?
Make sure to understand the accessibility requirements for the DC fast-charging installation jurisdiction. Where necessary, ensure appropriate access aisles as well as clear pathways into a convenience store from at least one charging stations. Think about wheelchair-accessible charging stations, curbs and tripping hazards to ensure convenient and safe customer flow. 4. How can finding and using chargers be simplified?
Lighting and signage are likely already in place on a gas fueling forecourt. Consider additional signage, online access and an app for wayfinding. 5. How will both commercial and passenger vehicles be served?
As larger EVs will visit a location, consider whether access by vehicles of all types will be allowed. How a site is configured will depend on what types of vehicles will be charging and where the charging ports are located. For most passenger vehicles, simply pulling or backing into a spot is the most desirable configuration. For larger vehicles, commercial vehicles or vehicles towing trailers, consider pull-through configurations for EV charging. Significant space is needed, so that can also factor into the layout. 6. What will be your next phase of fast charging site development?
While new technology will enable future EVs to charge at higher speeds, continued support of older EVs will also be critical. Avoid overbuilding, but put in a flexible solution that can expand over time when there are enough drivers to support payback on investment. 7. How will the project be funded and what can impact the return on investment?
EV charging is the future of fueling. Keep in mind funding regulations including locating charging sites in specific areas and offering a minimum charging speed. CEG
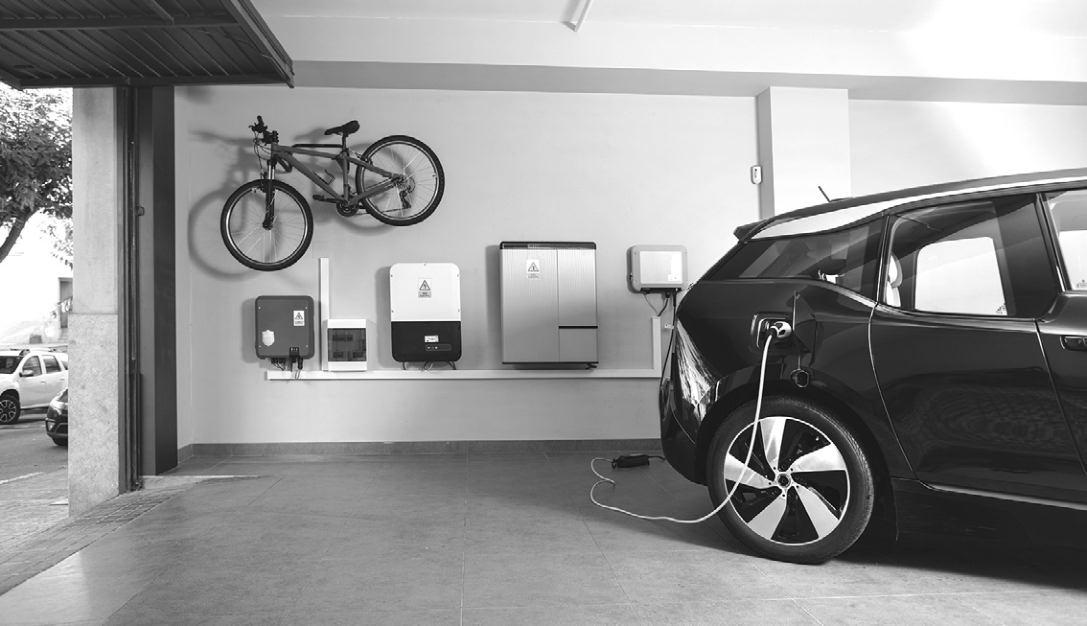
Rules would require consistency in installation, operation and maintenance of EV charging stations to provide the traveling public with system reliability.
Hyundai Doosan Infracore (HDI) successfully shipped the first Doosan dozer model DD100, a 9-metric-ton dozer targeted at the North American market.
HDI also produced two additional pilot machines and shipped them to North America for various performance tests, sales, marketing and service training.
The mass production of the Doosan DD100 will begin in June 2022 and will launch in North America in the third quarter. With the launch of the dozer, HDI hopes to create synergies with its existing excavator and wheel loader models.
“This is the next significant milestone in the development of the new Doosan dozers,” said Edward Song, CEO of Doosan Infracore North America. “Our North American dealers and their customers are eager for the arrival of the new Doosan dozers. We look forward to launching the new line of construction equipment later this year.”
This dozer model was the first to be produced through the collaboration of various departments at HDI, including development analysis, market research, competitive benchmarking, validation and pilot vehicle assembly. In addition, purchasing and quality teams investigated parts supply while production teams completed the first production dozer model.
HDI als¬o has set plans for its 13-metricton dozer — the Doosan DD130 — and will be shipping a pilot machine later this year. The company plans to start production, possibly as early as February 2023.
DD100 Dozer Features
The new 122-hp DD100 dozer expands the lineup of durable, rugged Doosan construction equipment. This new machine delivers powerful pushing performance, fuel efficiency and all-day operator comfort. It’s built for the most demanding conditions and features a dual/single flange-type roller with several track guard options, according to the manufacturer.
Designed with operators in mind, the DD100 features the 8-in. Smart Touch display, giving operators complete control from a convenient, easy-to-read touch screen. It also offers enhanced visibility with minimized front pillars, maximum glass area and a standard rearview camera — plus LED lights and front, rear and side wiper blades.
The DD100 features a Doosan engine with convenient maintenance access points and does not require the use of a diesel particulate filter to meet current emission standards. Doosan DD100 owners can add the 3D Machine Guidance and 3D Machine Control features as an option for greater accuracy and ease of operation.
Doosan DD100 Dozer Specs • Horsepower: 122 hp (91 kW) • Operating weight: 25,309 lb. (11,480 kg) • Blade capacity: 3 cu. yd. (2.3 cu m) • Blade height: 3 ft. 7 in. (1.1 m) • Blade width: 8 ft. 10 in. (2.7 m) • Blade angle: 22.5 degrees • Drawbar pull: 33,721 lbf. (15,296 kgf) • rack length: 7 ft. 7 in. (2.3 m) • Travel speed, max: 5.7 mph (9.2 kmh)
For more information, visit na.DoosanEquipment.com.
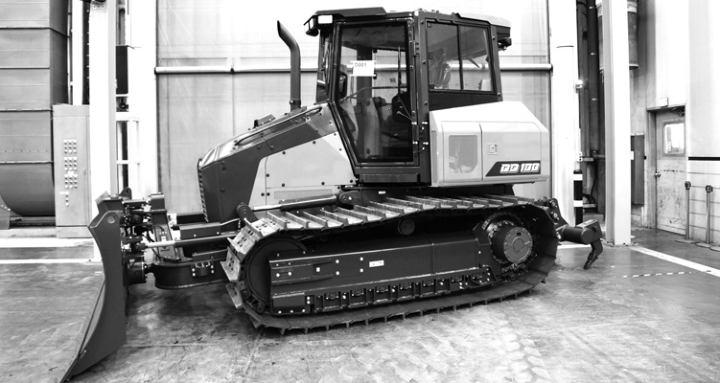
The mass production of the Doosan DD100 will begin in June 2022 and will launch in North America in the third quarter. With the launch of the dozer, HDI hopes to create synergies with its existing excavator and wheel loader models.
Chris Cornick to Lead Gilbane’s New Jersey Operations
Chris Cornick
Gilbane Building Company announced the promotion of Chris Cornick to vice president, business unit leader of New Jersey. In this role, he will oversee Gilbane’s operational, sales and administrative functions in New Jersey, based out of the firm’s downtown Newark office.
Cornick has worked for Gilbane for more than 15 years in field and operations roles, and most recently directed business development in New Jersey and served as principal in charge of strategic projects and accounts. He has extensive experience elevating Gilbane’s presence in New Jersey and working directly with clients across the company’s diverse market sectors and delivery methods.
Cornick takes the helm from Dan Shea, vice president, an accomplished construction executive who has played a senior leadership role in New Jersey for nine years. Shea will remain a strong part of the company’s operational team, focusing on project delivery excellence and strategic initiatives in advance of his planned retirement.
Cornick will assume his new leadership position on July 1, 2022.
“Chris has been such an integral part of our ongoing success in New Jersey,” said Shea. “I am confident that under Chris’ leadership Gilbane, our clients and the communities we build will experience even greater success.”
“Time and time again, we have seen Chris grow Gilbane’s business in New Jersey and cement our company as one of the most trusted and influential construction companies in the Garden State,” said Paul Choquette III, regional president, Gilbane Building Company.
“Chris is a true partner to our clients and committed to working with them to deliver the best outcomes, so he was a natural choice for this role. We thank Dan for his leadership in expanding our New Jersey operations, developing our deep team of construction experts, and instilling the principles and best practices that will ensure long-term success in the state.”
“It is an incredible honor to be tasked with building upon the foundation that we have established in New Jersey under Dan’s leadership,” said Cornick. “I am looking forward to leveraging our continuity, where the majority of the leadership team has been with us for the better portion of the past decade, to ensure that Gilbane is a great place to work and a company where the passion that our people have for building is evident.
“It is an exciting time to be in the construction industry in New Jersey, and I am eager to capitalize on the strengths, from a bestin-class preconstruction offering through superior construction execution, that we can offer clients here in the Garden State.”
For more information, visit www.gilbaneco.com.
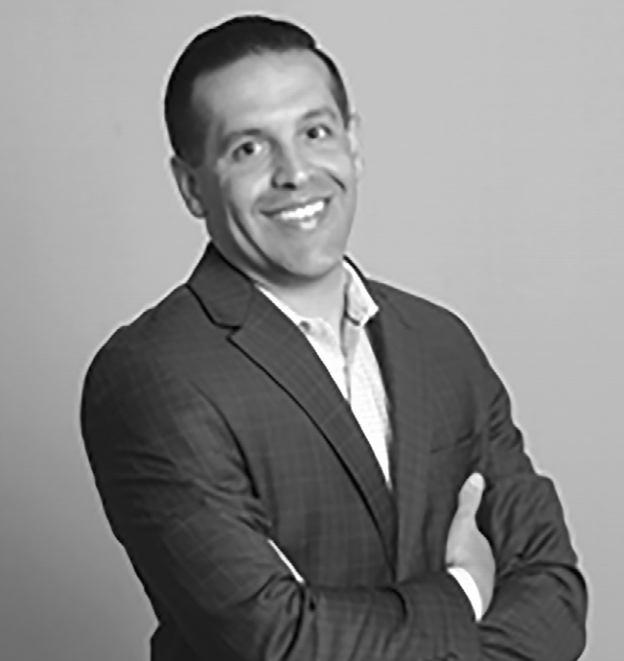
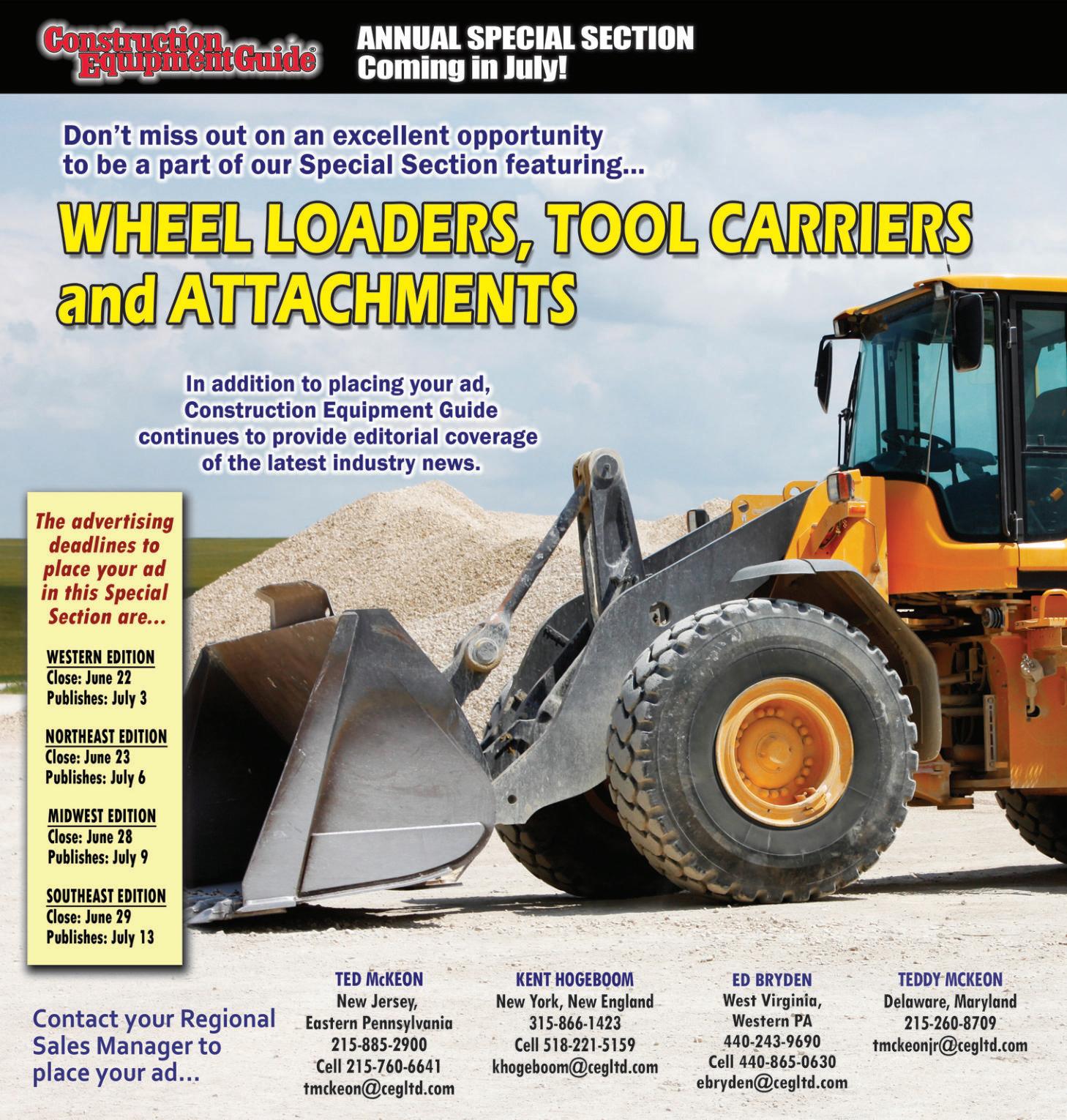