
6 minute read
SAKAI AMERICA CELEBRATES 20 YEARS IN ADAIRSVILLE, GA.
866-430-7539
www.jfwequipment.com sales@jfwequipment.com
Serving the Asphalt Industry for 30 Years
2007 Etnyre Centennial II distributor, 2000 gallons, computerized w/1 ft cut-offs, propane heat, 16 ft spray bar, Ford F750 Super Duty, Cat C7 diesel engine, 6 spd trans, 2 spd axle $65,000
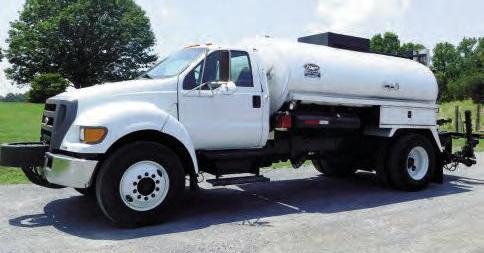
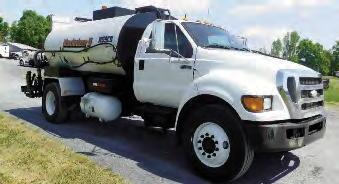
2015 Rosco Maximizer 2B distributor, 1900 gal, Max 2B computer w/1 ft cut-offs, propane heat, 12 ft spray bar, Ford F750XL, Cummins dsl eng, auto trans, 2 spd axle - $123,000
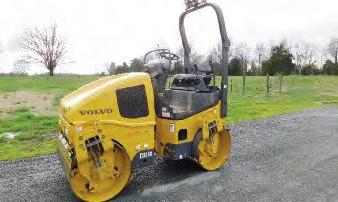
2017 Volvo DD25B double drum 47” vibratory roller, Volvo dsl eng, double drum drive, water system, 413 hrs, 3 tons - $34,000
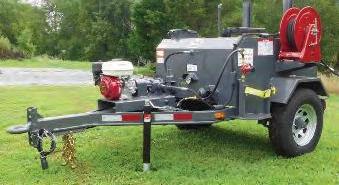
New Marathon TPS250T tack distributor, Honda gas eng, 10GPM pump, 250 gal, 5 ft spray wand w/50 ft hose, propane heat, flushing system, electric brakes $11,500 (also avail w/spray bar) 2010 Bomag BW11RH pneumatic roller, 9 wheels, Cummins B3.3 diesel engine, articulates, water system $35,000
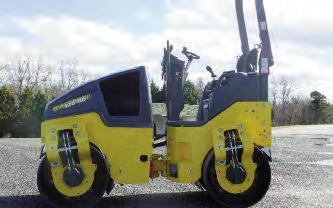
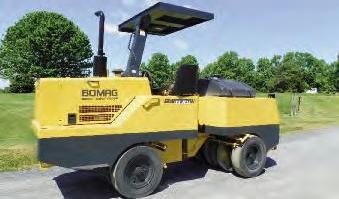
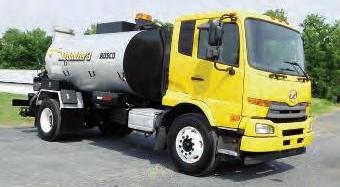
2013 Rosco Maximizer 3B distributor, 1550 gallons, Max3B computer, diesel heat, 16 ft extending spray bar, overnight heater, UD truck w/UD 6H7 diesel eng, auto trans, GVW 32,900, 10,563 miles - $110,000
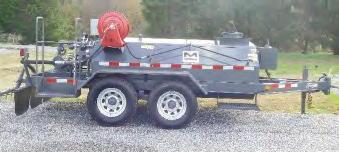
New Marathon LD600PT asphalt distributor, 585 gallons, Honda 11 hp electric start gas eng, 80 GPM hyd. pumping system, propane heat, auto temp control, fully insulated tank, 8 ft spray bar, operator’s platform, 5 ft spray wand & 50 ft hose, flushing system, recovery tank, electric brakes & electric breakaway - $37,200
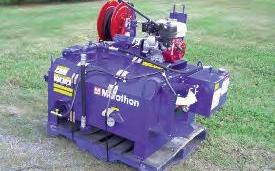
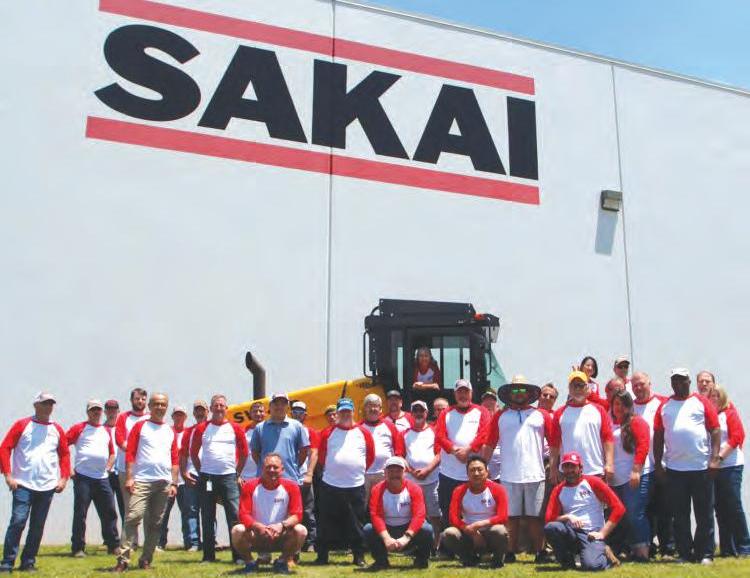
Fifty employees work at the Sakai America facility in Adairsville, Ga. The location serves as the North American headquarters, has a 175-ft. long assembly line, 97,000 sq. ft. of office and warehouse space within two buildings and more than 40 acres of land for testing and machine storage.
Sakai America Inc. is celebrating 20 years of assembling asphalt and soil rollers in Adairsville, Ga., in May.
“Sakai America has experienced exceptional growth over the past 20 years in the United States. We have proudly assembled over 3,500 machines here in our Adairsville, Ga., facility, and look forward to being part of this community for many years to come,” said Yasunori Azumi, president Sakai America.
Sakai America offers a wide range of high-force vibratory compactors designed for compacting asphalt pavement and for road and building site ground preparation. The machine portfolio includes industryleading oscillatory asphalt rollers in several size classes and an exclusive vibratory pneumatic tire roller, according to the manufacturer.
The company utilizes a strong nationwide dealer network for the sale and support of its products.
Kevin McClain, VP Sakai America, helped build the Sakai America Adairsville facility 20 years ago.
“I started with Sakai America in 2000, and was part of the team that selected this site to build our first U.S. assembly facility. When the building was finished in 2001, we started our current 20-year run of assembling heavy equipment here in Georgia. We currently assemble four of our best-selling machines here in Adairsville, and this summer, we will be bringing our SW774 series in-house as well. That machine is currently made in Japan by our parent company, but we’re excited to have another model to assemble here in the U.S.”
Sakai was founded in Japan in 1918 for the manufacture and repair of diesel locomotives and engines. Since that time, the company has evolved and now boasts a wide range of vibratory compactors and road-building heavy machinery. To strengthen its global footprint, Sakai vibratory compactors were introduced to North America in 1976. Then in 2001, it began U.S. manufacturing operations in its current location of Adairsville, Ga.
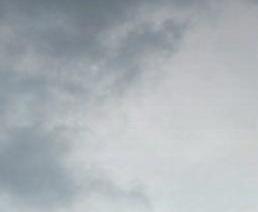
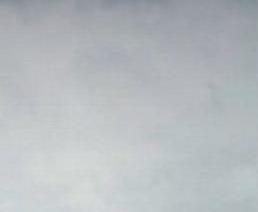
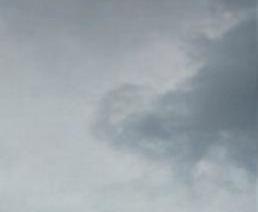
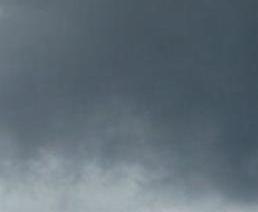
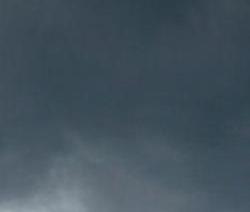





OEV

10421 Guilford Road Jessup, MD 20794 301/725-7394 Fax: 301/725-7361 38420 Sussex Highway Delmar, DE 19940 302/846-3033 Fax: 302/846-0763
12051 Tac Court Manassas, VA 20109 703/257-2381 Fax: 703/257-2383
450 E. Church Road King of Prussia, PA 19406 610/279-5200 Fax: 610/279-6366
ELLIOTT & FRANTZ, INC.
WWW.ELLIOTTFRANTZ.COM
The Worldwide Leader in Concrete Paving Technology
info@gomaco.com ❘ www.gomaco.com
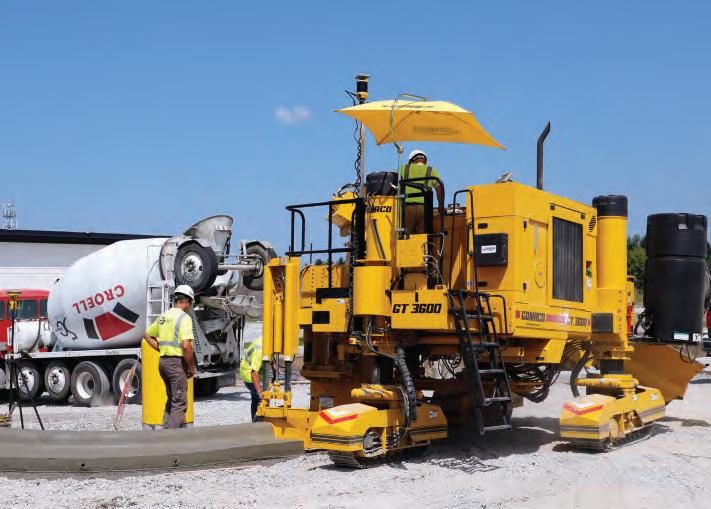
CONCRETE STREETS AND HIGHWAYS ❘ AIRPORT RUNWAYS ❘ CURB AND GUTTER ❘ SIDEWALKS RECREATIONAL TRAILS ❘ SAFETY BARRIER ❘ BRIDGE PARAPET ❘ BRIDGE DECKS ❘ IRRIGATION CANALS GOMACO CORPORATION IN IDA GROVE, IOWA, USA ❘ 712-364-3347
Murrysville, PA 724/327-1300
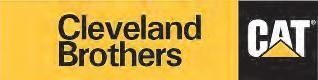
Somerset, PA 814/445-7915
Cat 815 Built for High-Speed, High-Quality Soil Compaction
COMPACTOR from page 61
Lower Maintenance Costs Up to 9 Percent
The new 815 soil compactor features improved airflow technology to reduce cleaning and maintenance. A new radial air filter delivers three times the life of the previous design, and operators are alerted to airflow blockages by an electronic air inlet restriction indicator.
The compactor’s electronics bay is located inside the updated cab to improve servicing ease in a climate-controlled environment. Sight gauges for the coolant, transmission oil and hydraulic system provide quick inspection with reduced contamination risk. Grouped hydraulic oil, fuel cooler and condenser service points, along with centralized grease points, help to further minimize maintenance time. Access to the emergency shutdown, battery disconnect and jump start are quickly and conveniently accessed from ground level.
Heavy-duty main structures are built to be rebuilt, offering multiple life cycles to lower total cost of ownership for the new 815. Heat-treated and direct-hardened, the adjustable cleaner bar tips deliver increased wear life with lower operating costs. The durable tamping tips deliver a long life and are replaceable.
Proven, Smooth Power
The Cat 815 soil compactor is powered by the field-proven Cat C7.1 engine designed for maximum fuel economy, reliable performance and increased power density. Two engine package options are available — U.S. EPA Tier IV Final/EU Stage V and Tier III/Stage IIIA equivalent — for meeting local market emission standard requirements. Automatic engine and electric system shutdown controls reduce unnecessary idling to lower fuel consumption.
Its Advanced Productivity Electronic Control System (APECS) transmission control delivers improved shifting performance, achieves greater momentum on grades and saves on fuel by carrying that momentum through shift points.
For more information, visit www.cat.com.