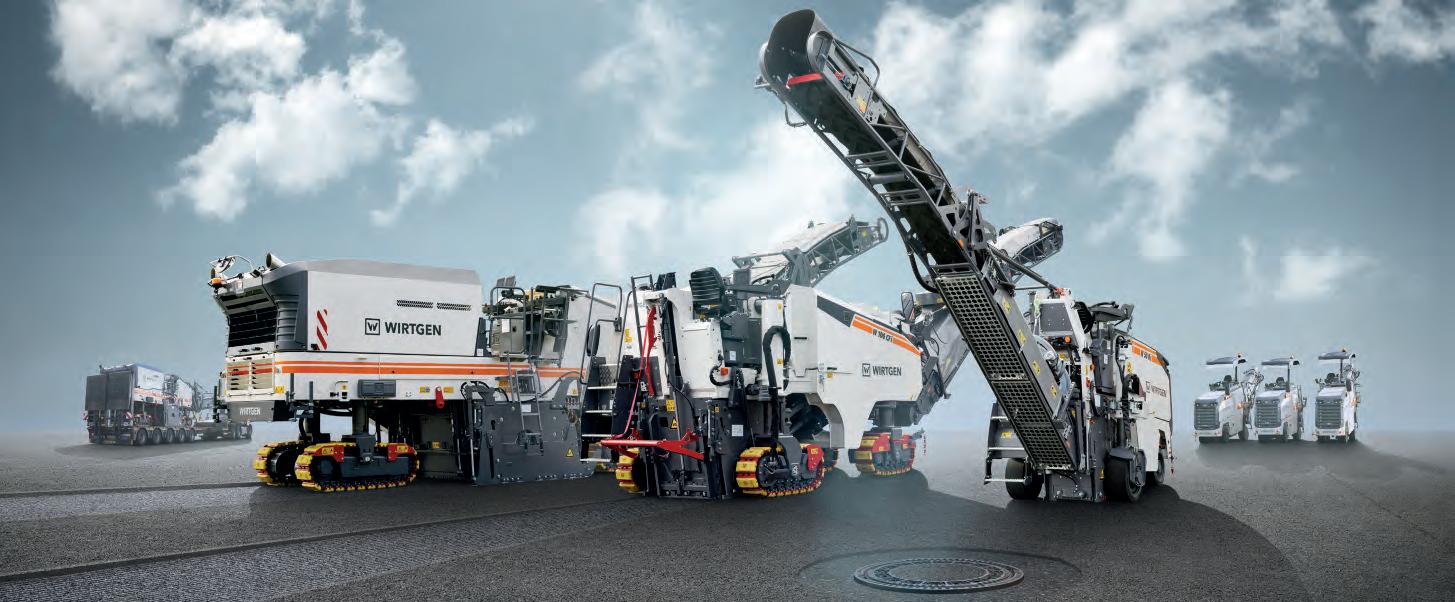
15 minute read
BOMAG BM 500/15-2, BM 600/15-2 Compact Cold Planers
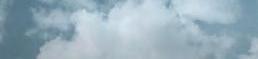
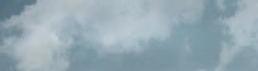

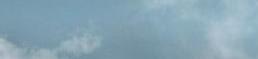

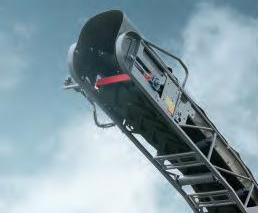
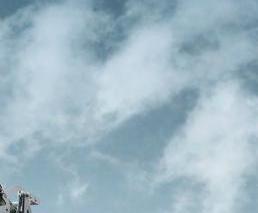
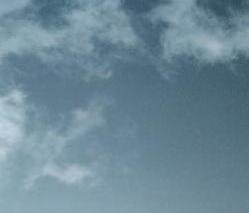





10421 Guilford Road Jessup, MD 20794 301/725-7394 Fax: 301/725-7361 38420 Sussex Highway Delmar, DE 19940 302/846-3033 Fax: 302/846-0763
12051 Tac Court Manassas, VA 20109 703/257-2381 Fax: 703/257-2383
450 E. Church Road King of Prussia, PA 19406 610/279-5200 Fax: 610/279-6366 ELLIOTT & FRANTZ, INC.
WWW.ELLIOTTFRANTZ.COM
Bomag’s Compact Cold Planers Feature Multiple Upgrades
Available in 3- and 4-wheel designs, the Bomag BM 500/15-2 and BM 600/15-2 compact mills feature a reengineered vibration-isolated operator’s station that improves operator efficiency and productivity. A new suspension seat with optional heating boasts a 45-degree slewing angle for increased visibility to the left cutting edge and front/rear of the machine. The main control console is fully adjustable to fit individual operator preferences and simplified control grouping improves machine operating efficiency.
Machine leveling sensors are now integrated into the side plate cylinders of the new mills. A new 7-in. (17.8-cm) full graphic color display offers intuitive operation and leveling control for efficient mill set-up. The conveyor joystick control has been repositioned for easier access, and it integrates both lifting and lowering functions for faster operation.
Advancements to hydraulic system efficiency boost transport speed to 3.7 mph (6 kmh) for 3-wheel and 6.2 mph (10 kmh) for 4-wheel configurations. Maximum milling speed for 4-wheel configurations is increased by more than 25 percent for both models to significantly improve machine productivity.
The Bomag BM 500/15-2 offers a maximum milling width of 19.7 in. (50 cm) and the BM 600/15-2 a maximum width of 23.6 in. (60 cm). Four extra cutting tools positioned at the left- and right-edge rings plus optimal arrangement of the tools across the
drum delivers uniform, low vibration milling and smooth milled edges. A range of standard, fine, power and trenching drum designs are available in widths from 3.15 to 23.6 in. (8 to 60 cm) with all featuring standard quick-exchange designs.
The machines’ new super-light conveyor design features an increased, 30-degree swiveling angle in both directions for more rates time-saving support brackets and multi-coupling for fast removal in minutes. All conveyor hoses and wiring are now positioned within the frame, reducing the chance of damage and improving machine uptime. A 140.8-hp (105-kW) diesel engine meeting stringent Tier IV Final (Stage V) emissions standards powers the new Bomag BM 500/15-2 and BM 600/15-2 cold planers. Each model features improved front-to-rear weight balance, enhancing traction. Both machines offer a minimum milling radius of just 9.6 in. (24.4 cm) for efficient milling around obstructions like manhole covers.
The machines’ new triple-setting water pump system — sprinkling, high-flow and refill/suction — allows the operator to adjust waterflow as needed to extend intervals between refills. A large plate positioned at the front of the machine delivers enhanced protection to prevent damage to the water tank and hood.
For more information, visit www.bomag.com.
The Bomag BM 500/15-2 offers a maximum milling width of 19.7 in. (50 cm) and the BM 600/15-2 a maximum width of 23.6 in. (60 cm).
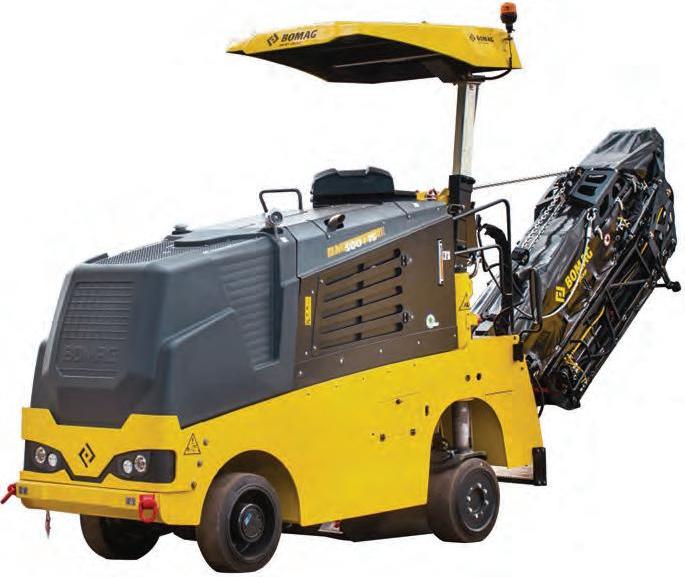
Page 54 • May 12, 2021 • www.constructionequipmentguide.com •Paving Section • Construction Equipment Guide Blue Smoke Control Nixes Hot-Mix Asphalt’s Odor-Causing Emissions
Blue Smoke Control, a division of Anaheim, Calif.-based ogy of X-VOCS can stand on its own, but it also combines Butler-Justice Inc., introduced X-VOCS, the company’s well with our industry-standard Blue Smoke Control system newest system for eradicating odor-causing emissions pro- to reduce both odor and blue smoke, which are some of the duced as a byproduct during hot-mix asphalt production. most common causes of neighborhood and Air Quality
Invisible emissions from plants — specifically, the odor- Board issues.” causing volatile organic compounds (VOCs) that reside in Blue Smoke Control division of Butler-Justice Inc. is a hot asphalt storage tanks — can create a number of chal- leading supplier of complete blue smoke control and odor lenges for producers, ranging from regulatory requirements control systems that eliminate both the blue haze typically to overt opposition from neighbors. found during the production of hot mix asphalt, as well as
The X-VOCS System features proprietary carbon absorp- odor-causing VOCs. With hundreds of successful installation technology designed to filter and remove up to 99 per- tions in the continental United States and Hawaii, as well as cent of odors and VOCs, such as Hydrogen Sulfide (H2S), Canada, Mexico, Australia and Europe, Blue Smoke Control from tanks. achieves the highest standards of emissions control, with rea-
X-VOCS incorporates a five-stage filtration system. In the sonable initial investment costs and economical ongoing first three stages, a series of filters remove more than 95 per- expenses, according to the manufacturer. cent of targeted particulates down to 0.3 microns. In the final For more information, call 714/696-7599 or visit two stages, carbon filtration beds remove remaining odors www.bluesmokecontrol.com. and volatiles. The X-VOCS system is ideal for new plants, and also is easily retrofittable into existing operations, with minimal modifications to the plant, according to the company.
Further, when the X-VOCS technology is coupled with the company’s Blue Smoke Control system, emissions from hot-mix plants can be reduced to nearly zero, providing owners with the means to achieve the highest level of environmental stewardship. Implementation of this technology has been proven to virtually end calls from nearby neighbors regarding odor and visual emissions. Similar to X-VOCS, the Blue Smoke Control system is retrofittable with few plant modifications.
According to Mike Butler, president of X-VOCS incorporates a five-stage filtration system. In the firstButler-Justice, “We worked for many years to three stages, a series of filters remove more than 95 percent of solve the odor and VOC issues associated with targeted particulates down to 0.3 microns. In the final two stages, asphalt production. The patent-pending technol- carbon filtration beds remove remaining odors and volatiles. LESLIE EQUIPMENT COMPANY
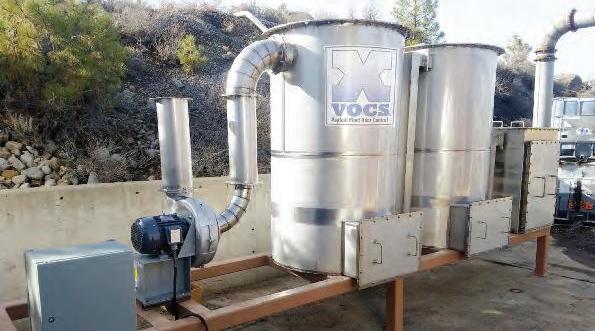
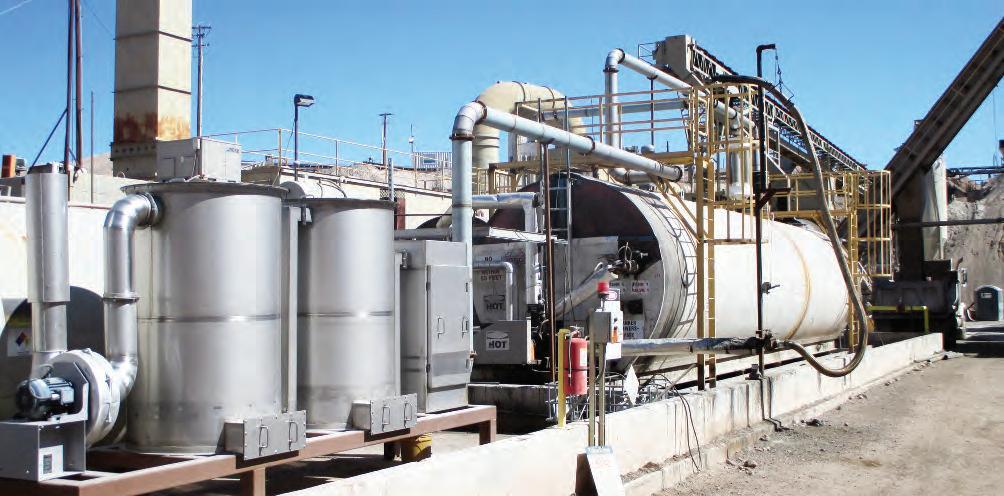
www.lec1.com
6248 Webster Road Cowen, WV 26206 304/226-3299 80 John Deere Lane Norton, WV 26285 304/636-6421
2098 Lillian Lane Pleasant Valley, WV 26554 304/534-5454
136 Clifftop Drive Beaver, WV 25813-1525 304/255-1525
19 Goff Crossing Drive Cross Lanes, WV 25313 304/204-1818
MONROE TRACTOR
www.monroetractor.com 1001 Lehigh Station Road 8194 State Route 415
Henrietta, NY 14467 Campbell, NY 14821 585/334-3867 607/739-8741 5035 Genesee Street 800/866-8912
Buffalo, NY 14225 6 Equipment Drive 716/681-7100 Binghamton, NY 13904 Toll Free: 800/834-9606 607/754-6570 7300 Eastman Road 866/321-4277
N. Syracuse, NY 13212 315/452-0000 Toll Free: 800/287-5286
SCHMIDT EQUIPMENT INC.
Serving MA and RI since 1956
www.schmidtequipment.com 80 Southbridge Rd. • Route 20 1620 Page Blvd
North Oxford, MA 01537 Springfield, MA 01104 508/987-8786 • 800/922-8295 413/543-5595 • 800/734-5594 2397 GAR Highway • Rte 6 & 136 4 Sterling Road
North Swansea, MA 02777 North Billerica, MA 01862 508/379-9810 • 800/456-6885 978/667-4345 • 800/531-2266 88 Camelot Drive • Unit 42 Plymouth, MA 02360 508/830-9997 • 800/916-0997
ROBERT H. FINKE & SONS INC.
www.finkeequipment.com 1569 US Route 9W Selkirk, NY 12158 888/266-9821 518/767-9331
NORTRAX
www.nortrax.com 98 Sheep Davis Road 300 Clinton Street Pembroke, NH 03275 Springfield, VT 05156 603/225-2769 802/885-6840
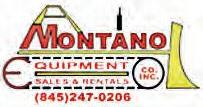
A. Montano Co, Inc.
571 Route 212 Saugerties, NY 12477 845-247-0206 www.amontanoco.com
Highway Equipment Company
22035 Perry Highway Zelienople, PA 16063 724-452-7800 5846 West Road McKean, PA 16426 814-476-7755 4690 Route 219 Dubois, PA 15801 814-371-3600 www.highway-equipment.com
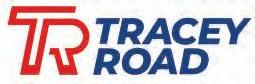
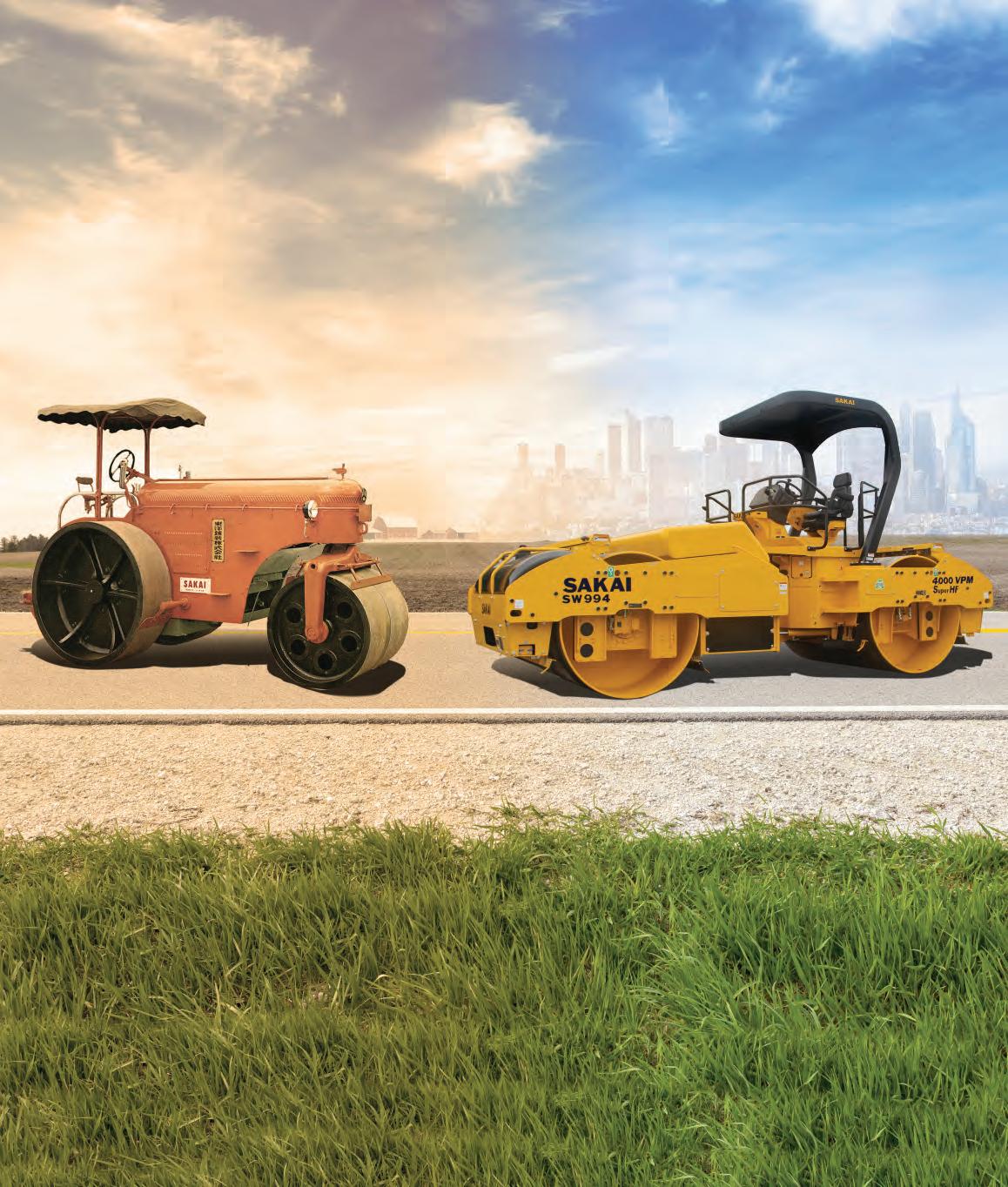
Tracey Road Equipment
Syracuse 6803 Manlius Center Rd East Syracuse, NY 13057 315-437-1471 Binghamton 1523 Route 11 North Kirkwood, NY 13795 607-775-5010 Rochester 300 Middle Rd Henrietta, NY 14467 585-334-5120 Watertown 19598 Cady Road Adams Center, NY 13606 315-788-0200 Albany 115 Railroad Ave. Albany, NY 12205 518-438-1100 www.traceyroad.com
Roads must be built. Worlds must be connected.
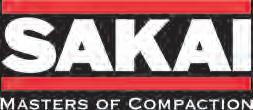
What began over a century ago...
Evolved into a combination of experience and innovation.

866-430-7539
www.jfwequipment.com sales@jfwequipment.com
Serving the Asphalt Industry for 30 Years
New Marathon LD600PT asphalt distributor, 585 gallons, Honda 11 hp electric start gas eng, 80 GPM hydraulic pumping system, propane heat, auto temp control, fully insulated tank, 8 ft spray bar, operator’s platform, 5 ft spray wand & 50 ft hose, flushing system, recovery tank, electric brakes & electric breakaway - $37,200
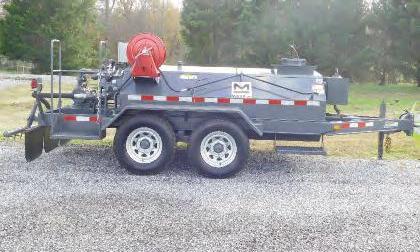
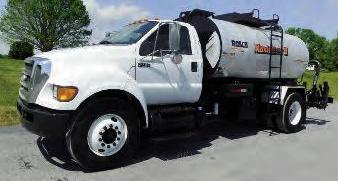
2015 Rosco Maximizer 2B distributor, 1900 gallons, Max 2B computer w/1 ft cut-offs, propane heat, 12 ft spray bar, Ford F750XL, Cummins dsl eng, Allison auto trans, 2 spd axle - $123,000
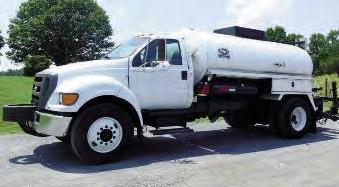
2007 Etnyre Centennial II distributor, 2000 gallons, computerized w/1 ft cut-offs, propane heat, 16 ft spray bar, Ford F750XL, Cat C7 diesel, 6 spd trans, 2 spd axle - $65,000
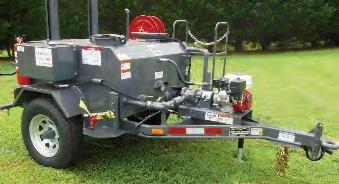
New Marathon TPS250T tack distributor, Honda gas eng, 18GPM pump, 250 gal, 5 ft spray wand w/50 ft hose, 6 ft spray bar, operator’s platform, propane burners, flushing system, electric brakes - $13,600 2020 Bomag BW120AD-5 double drum 47” vibratory roller, double drum drive, Kubota diesel engine, water system, 3 ton roller - $39,000
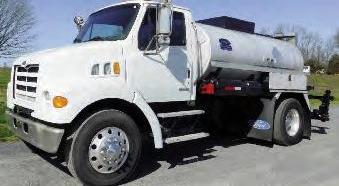
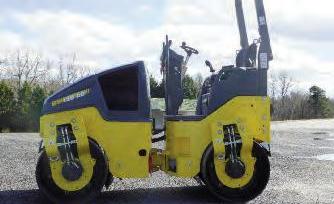

2011 Laymor 8HC broom, tow hitch, Kubota diesel engine, 8 ft broom, 414 hrs - $16,500

2003 Ingersoll Rand PT125R pneumatic roller, 9 wheels, Cummins 3.3L diesel engine, water system, 5 new tires - $28,000
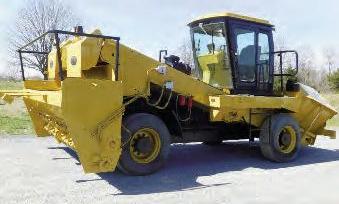
Grandmother, Granddaughter Utilize Dynapac Investment
FAMILY from page 49
tighter deadlines. This is why we have built a strong and long-term relationship with the Dynapac brand, working with both Anderson and the Dynapac team.
“A great example of how this helps our business is how Dynapac dealer sales manager Sean Engle has helped our team develop our proposition and skills throughout our journey. We have also had great support from the Dynapac and Anderson teams, as we move into using intelligent compaction control. This technology is now available on the Dynapac equipment and in our case training from Topcon Solutions for our operators, has help us quickly get to up to speed using the GPS enabled technology.
“We have also benefitted from great support from the Anderson Equipment Co. team, led by Steve Kenny. This has been a constant throughout all new equipment introductions, demos, walk-arounds and service support. This ongoing relationship helps us get the most out of our machines, using new technologies and equipment to optimise our performance on the job site.
“Equally by keeping our equipment in great condition, we can achieve industryleading uptime, helping us to maintain a competitive advantage.”
As part of the fleet investment, Cobleskill Stone also has opted for an extended warranty program on its new CC5200 VI rollers, working with Anderson to build this into the fleet finance package for the equipment.
“Ever since we started working with Cobleskill Stone over 30 years ago, they have been a real brand advocate,” said Steve Kenney of Anderson. “They love the build quality of the products and together we have developed a strong relationship with the team, who are very proactive in identifying any maintenance required. We also get to know the equipment very well, so we can recommend any preventative maintenance to maintain the high uptime levels they demand.”
Talking about operating the rollers with the latest technology, T’mara Deridder said: “I have been operating the equipment for some time now. What I like is how comfortable and simple it is to control. As I also work on quite busy sites, the visibility from the front and back of the roller is very good, which helps me feel like I can keep other people safe onsite.
“More recently it has been great to learn about the advanced capabilities of the Dynapac CC5200 VI rollers as they support intelligent compaction technology. This comes with a display in the cab that gives me all the information about the job and it is very easy to understand. Having had training on using this 3D technology I now know how to upload the models into the system and how to follow them on the display.
“I particularly like the fact that this technology also visualises the compaction levels reached. For example, I can now see my work in real-time with completed areas highlighted on my in-cab display. It’s certainly the way forward, especially for larger jobs.”
Adding his thoughts on the introduction of intelligent compaction, Moore said: “The move to intelligent compaction was very swift and smooth, as we had already been introduced to the possibility of integrating this technology on Dynapac rollers with Steve Kenny demonstrating the technology. This allowed us to confidently specify the technology within a bid for a key project, which we won.
“As soon as we were awarded the job, Steve and his team very quickly worked with us to coordinate the delivery of the machine, installation of the added sensors and display needed to use the intelligent compaction solution. Having trained our highly experienced operators, we are already delivering all the benefits of a 3D enabled Dynapac machine to our clients.”
Cobleskill Stone has already proven the benefits of the new rollers, and as more work is bid, the company is taking full advantage of the productivity and quality benefits associated with using its Dynapac roller fleet.
For more information on Dynapac products visit www.dynapac.us.
About Cobleskill Stone Products Inc.
Headquartered in Cobleskill, N.Y., Cobleskill Stone Products Inc produces limestone and high friction aggregate, sand and gravel products, asphalt (blacktop). It also provides construction services ranging from heavy highway construction to paving and site preparation work for industrial, commercial and residential sites.
About Anderson Equipment Company
Anderson Equipment Company is a distributor of earth moving and mobile equipment to the construction, mining, road building and specialty material handling industries.
JLG Industries Inc., an Oshkosh Corporation company and global manufacturer of mobile elevating work platforms (MEWPs) and telehandlers, announced that its manufacturing facility in Shippensburg, Pa., has achieved the 50001 Ready designation from the Department of Energy (DOE).
Based on the ISO 50001 (Energy Management System) program, the 50001-Ready program is designed to help facilities identify their energy management gaps, while providing technical tools and resources that help organizations build a culture of structured energy improvement.
JLG’s Shippensburg facility manufactures a broad range of mobile elevating work platforms (MEWPs) and telehandlers.
“JLG has long been a forerunner in the design and manufacture of environmentally friendly equipment and sustainable technologies,” said Frank Nerenhausen, president, JLG. “As the access industry leader, we view protecting the environment through responsible operations as one of our greatest responsibilities. As such, we continuously look for ways to reduce our carbon footprint.
“Strategic energy management not only helps to reduce our company’s energy related spending, but it also improves JLG business processes. I’d like to congratulate our Shippensburg management team for being progressive and the first of all Oshkosh plants to achieve the 50001 Ready recognition. This achievement positions JLG to implement compliant ISO 50001 programs well into the future.”
According to the DOE, implementing a structured energy management system can be a key step for 50001 Ready companies, including JLG, to: • Cut operational costs • Achieve continual operational improvement • Improve risk management • Stay competitive in the marketplace For more information, visit www.jlg.com.
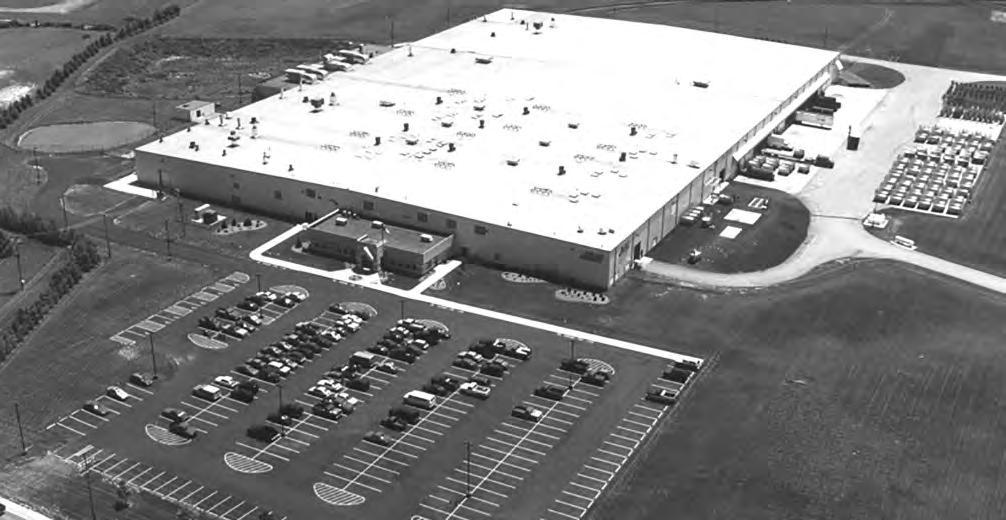
JLG Industries Inc. announced that its manufacturing facility in Shippensburg, Pa., has achieved the 50001 Ready designation from the Department of Energy (DOE).
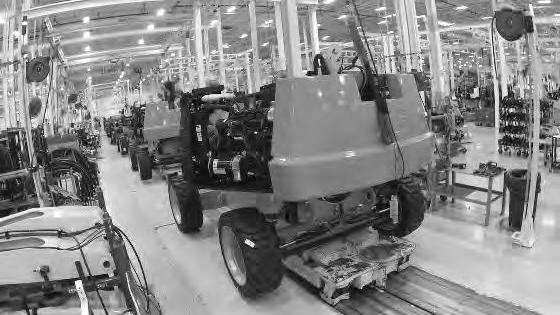
Based on the ISO 50001 (Energy Management System) program, the 50001-Ready program is designed to help facilities identify their energy management gaps, while providing technical tools and resources that help organizations build a culture of structured energy improvement. JLG’s Shippensburg facility manufactures a broad range of mobile elevating work platforms (MEWPs) and telehandlers.
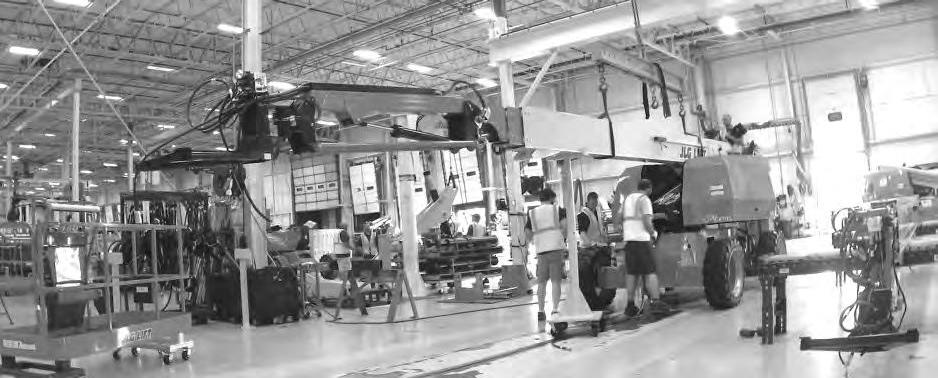
Association of Equipment Manufacturers (AEM) senior vice president of government and industry relations Kip Eideberg issued the following statement applauding the Problem Solvers Caucus on its new report of bipartisan policy recommendations to build a strong, successful 21st century infrastructure network for America:
“Americans are ready for a transformational investment in our nation’s infrastructure so we can grow our economy, improve our quality of life and protect our environment for the generations to follow,” said Eideberg.
“The Association of Equipment Manufacturers applauds the 58 Republicans and Democratic members of the Problem Solvers Caucus for putting forward a set of bipartisan and commonsense policy solutions that will address today’s challenges and capture future opportunities.
“President Biden’s American Jobs Plan, bipartisan support in Congress for a surface transportation reauthorization bill, and today’s unveiling of the Rebuilding America’s Infrastructure Report for the 117th Congress by the Problem Solvers Caucus, point to growing momentum for a modern, sustainable and equitable infrastructure for all Americans. We urge the business community and policymakers to put policy ahead of politics and to work together to embrace and advance an affirmative vision for 21st century infrastructure and break free from the same old policies that have failed to move our country forward.”
The Association of Equipment Manufacturers recently joined the Brookings Institution in unveiling a new report outlining a new affirmative vision for U.S. infrastructure titled “Rebuild With Purpose: An Affirmative Vision for 21st Century American Infrastructure.” The Association of Equipment Manufacturers also announced its commitment to a set of national policy priorities to revitalize the infrastructure systems that move the American economy, including fiscal health, resilience, workforce and digitalization.
For more information, visit www.iv2050.org.
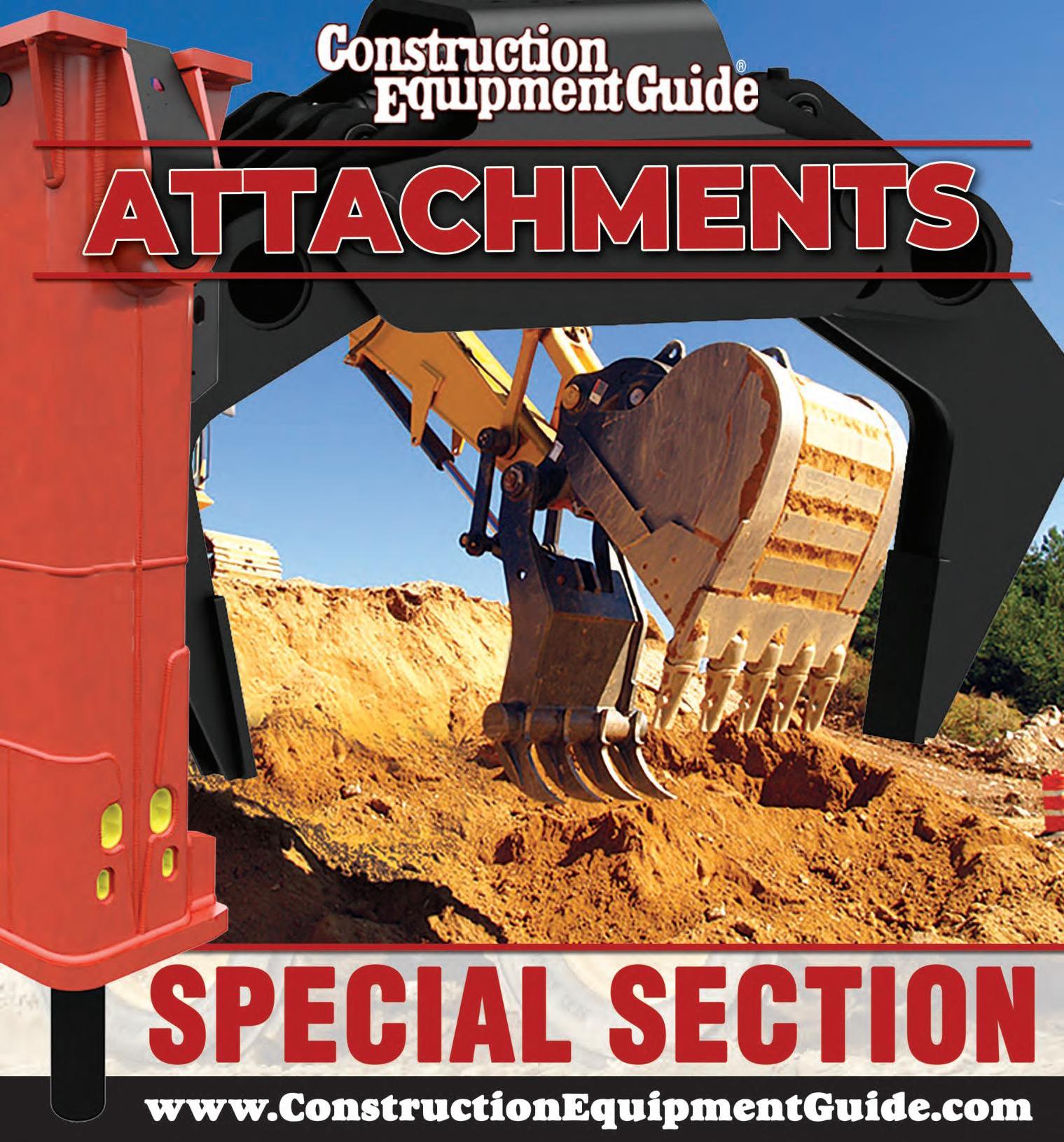