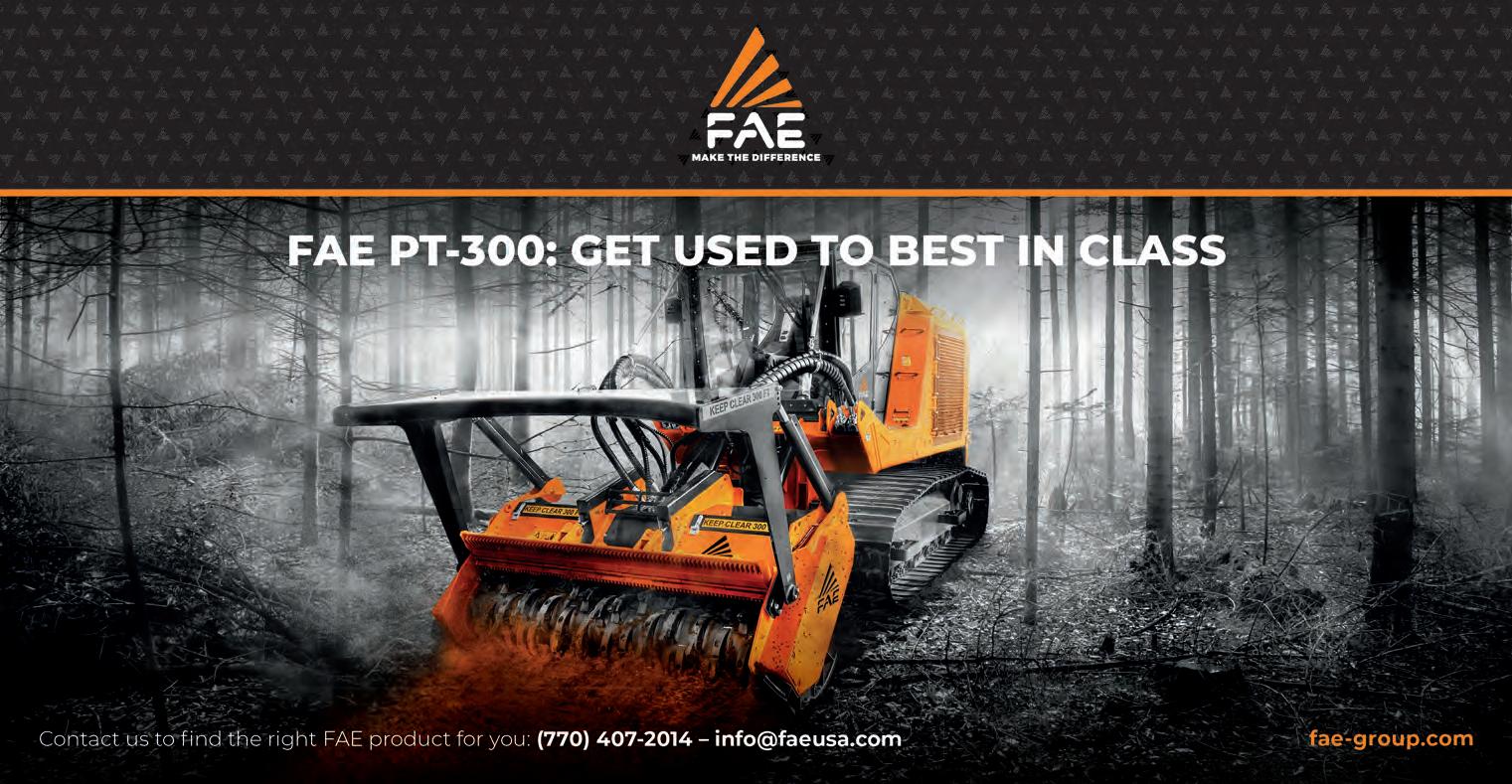
7 minute read
METSO OUTOTEC LAUNCHES CONCORDE CELL FLOTATION TECHNOLOGY
Metso Outotec is launching Concorde Cell flotation technology for efficient fine and ultrafine particle recovery.
This Planet Positive technology sets a new benchmark in high-intensity pneumatic flotation, reducing plant operation costs and contributing to sustainability of operations through minimized energy and water consumption per tons of metal produced, according to the company.
The Metso Outotec Concorde Cell technology is the first fine and ultra-fine flotation solution for more finely disseminated and complex orebodies that have previously been inaccessible.
“The need to process more finely disseminated and complex ore grades, as well as the declining ore grades and the demand for improved flotation selectivity, all bring new challenges to minerals processing flowsheets. The new Concorde Cell technology helps flotation circuits overcome these challenges and recover the previously unachievable ore value,” said Antti Rinne, vice president, flotation at Metso Outotec.
The Concorde Cell forced-air Blast Tubes treat 100 percent of fresh feed combined with tailings recycling for improved performance, allowing finer grinding to get extra liberation without the risk of valuable particles lost into tailings.
“Combining the well-proven TankCell technology with Concorde Cells is a low-risk and high-benefit approach for minerals processing flowsheets. The cell produces very high shear and extremely fine bubbles, which increases recovery in particles under 20 microns,” explained Rinne.
• Superior recovery of fine and ultra-fine particles • Very high shear environment with increased bubble surface area flux for faster flotation kinetics
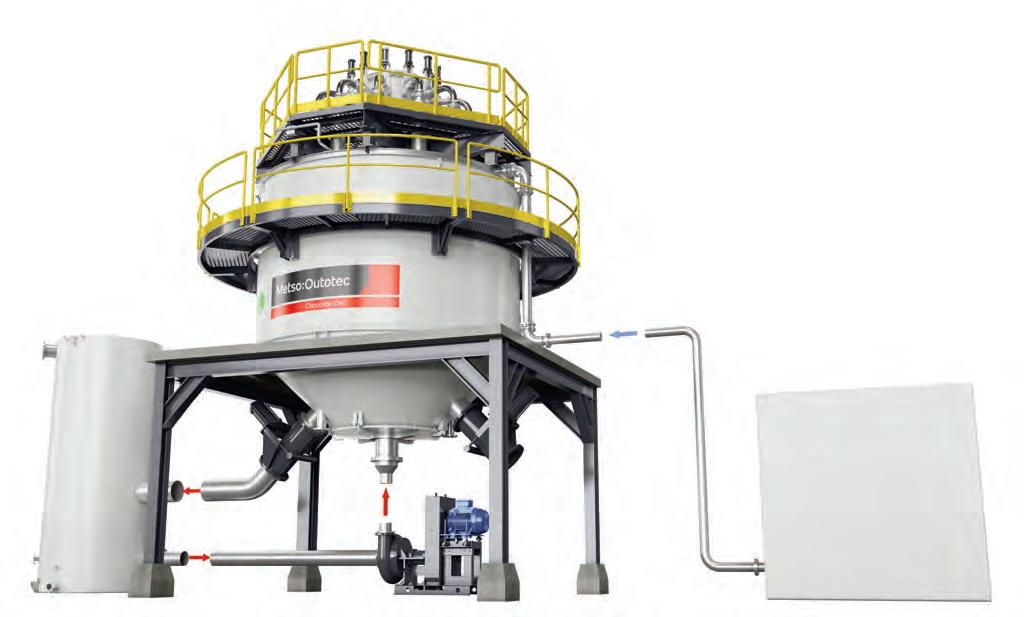
• Optimized froth recovery and improved selectivity • Forced air allowing wider process control and stability for further flotation optimization
The offering also includes Blast Tube retrofit kits for upgrading the metallurgical performance of self-aspirated pneumatic flotation cells to the Concorde Cell technology. In addition, Metso Outotec can provide a complete slurry handling package for the Concorde Cell, including pumps, spare parts, as well as optimization and maintenance services. For more information, visit www.mogroup.com.
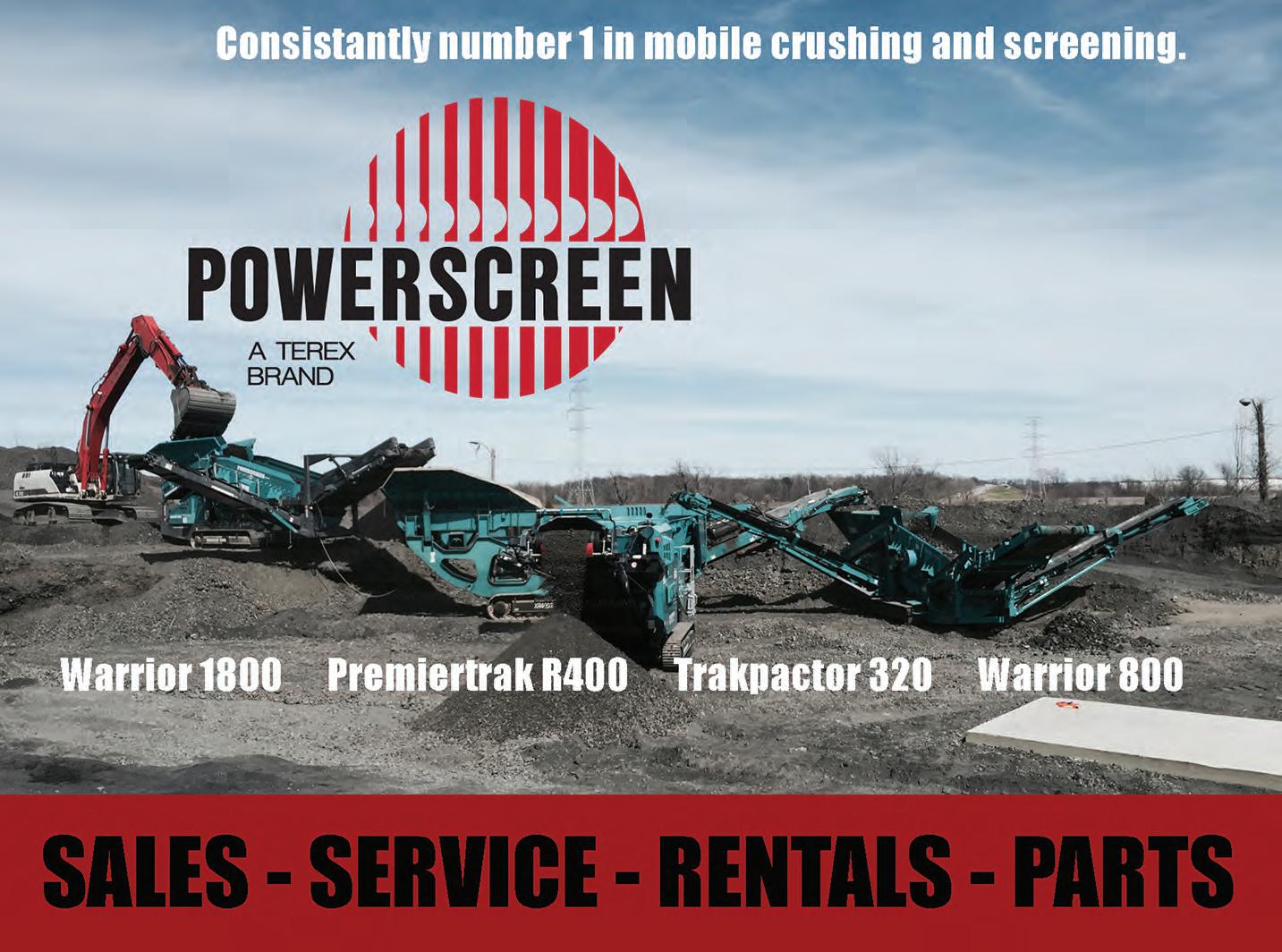
Illinois
Midwest Crushing & Screening, Inc.
13929 S Kostner Ave. Crestwood, IL 60418
www.midwestcrushandscreen.com 847.271.5027 Northern Indiana
(6 Counties) & Michigan
Powerscreen Michiana
255 N. Hetzler Court Angola, IN 46703
www.powerscreenmichiana.com 260.665.5816 • 800.843.4277
Kentucky
Powerscreen Crushing & Screening
11901 Westport Road Louisville, KY 40245
www.powerscreensales.com 502.326.9300 • 800.227.0534
Indiana
Powerscreen Crushing & Screening Indiana
12346 Southeastern Ave Indianapolis, IN 46259 www.powerscreensales.com 317.778.6677 • 800.227.0534
Minnesota
Theco, Inc.
14833 164th Ave. S.E, Big Lake, MN 55309
www.thecoinc.com 763.263.0505 Ohio
AGGCORP
22800 Lakeland Blvd. Cleveland, OH 44132
www.aggcorp.net 614.309.6854
Missouri & Kansas

Powerscreen Central
9001 Hickman Mills Drive Kansas City, MO 64132 www.powerscreensales.com 816.718.9600 • 800.227.0534
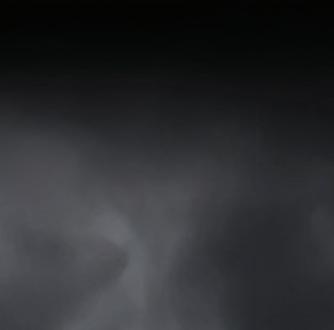
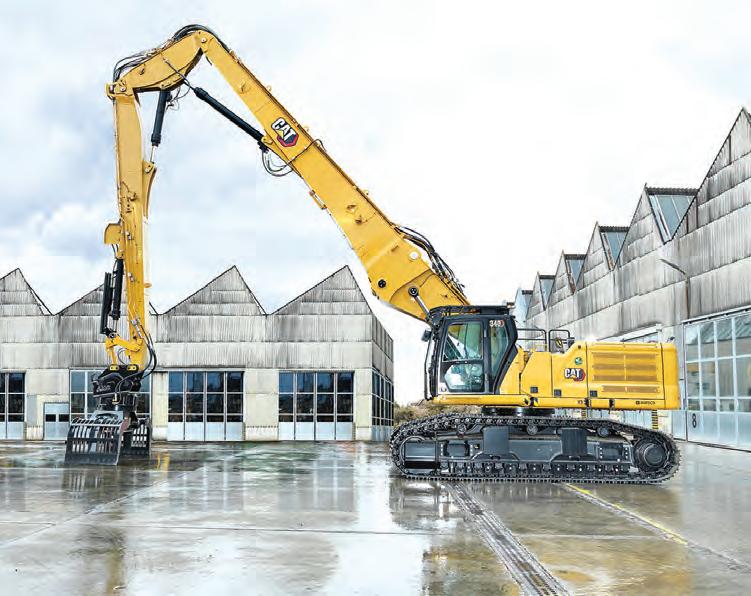
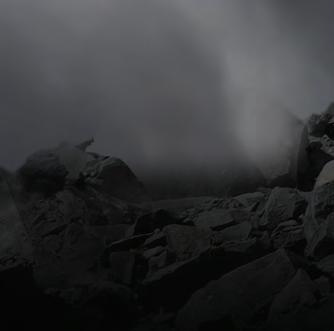
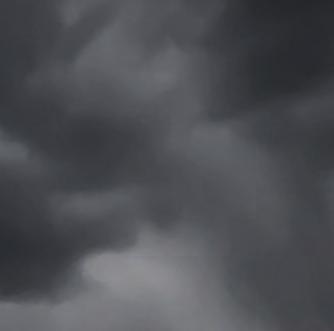
FORCE MULTIPLIER
A new era is being ushered in with Rammer® fully investing in Allied® Construction Products to deliver enhanced products, service, and support the growing North American markets. The combined forces will be stronger than ever, bringing you the latest Rammer technology with Excellence and Performance Series breakers as well as our pioneering Ho-Pac and Skid-Pac compactor drivers. Together, and stronger than ever, the world-famous Rammer and Allied continue to prove... there’s no match for experience and innovation.
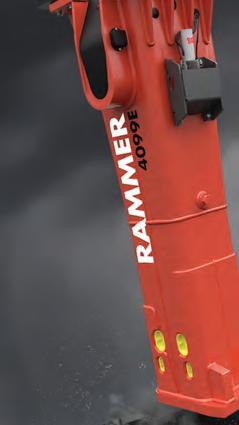
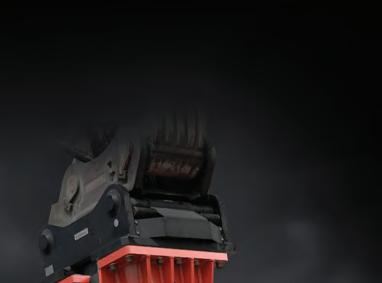
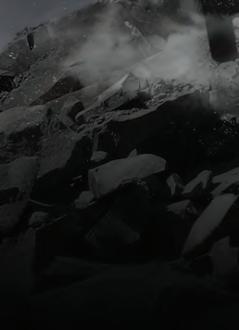
800-321-1046 / www.alliedcp.com

EXPERIENCE & INNOVATION
HIGHWAY EQUIPMENT COMPANY
www.highway-equipment.com
1405 Timken Place SW Canton, OH 44706 330-915-8391
Three stick options are available at lengths of 9 ft. 2 in., 10 ft. 6 in. and 12 ft. 10 in., providing ultimate flexibility for maximum machine utilization.
DEMOLITION from page 32
working at height, the UHD front is work tool camera ready.
The demolition cab is equipped with Falling Object Guard Structure (FOGS), and front and roof P5A, 0.4 in. laminated glass for safety. The windshield and roof glass feature one-piece parallel wipers with three intermittent settings with washer spray. Standard rearview and sideview cameras provide enhanced visibility of the operating area on the in-cab monitor. A 360-degree bird’s eye camera system is optional.
Simplified Maintenance
Maintenance intervals are extended and more synchronized on the Cat 340 UHD Excavator to lower operating costs and reduce service time. Offering a 50 percent longer service life, the new hydraulic filter improves filtration and features a 3,000-hour change interval while anti-drain valves keep the oil clean during filter replacement. The engine air intake filter with pre-cleaner delivers double the dust holding capacity of the previous design.
Grouped on the right-hand side of the machine, all fuel filters change at a synchronized 1,000-hour interval. Operators conveniently track filter life and maintenance intervals on the new in-cab monitor.
A ground-level shutoff switch stops all fuel to the engine and shuts down the machine, improving safety while servicing. The machine’s new flat engine hood improves rear visibility and incorporates a wide opening design for simplified servicing and oil level checking. All other daily maintenance routine checkpoints are easily accessible from ground level as is the location for draining fuel system water and fuel tank water to help save time. To efficiently collect fluid samples for analysis, all Cat S·O·S ports are conveniently accessed from ground level.
Technology Increases
Management Efficiency
Beyond Cat payload, the new 340 UHD with the single retrofit boom is equipped with a host of Cat technologies designed to drive productivity and service efficiency. Cat E-fence and Cat Grade with 2D automatically guides depth, slope and horizontal distance to grade through the touchscreen monitor to boost machine productivity. The machine automatically compensates for excavator pitch and roll caused by sloping ground conditions through use of GPS and GLONASS systems.
Standard Cat Product Link captures critical machine operating data and condition and reports this data to field managers and the office via VisionLink, boosting fleet management efficiency. Remote Troubleshoot analyzes real-time machine data captured by Product Link for diagnostics without impacting machine productivity and saving a service trip to the jobsite. Remote Flash conveniently assures the 340 UHD is working with the most current version of on-board software by updating around the machine’s production schedule.
For more information, visit cat.com.
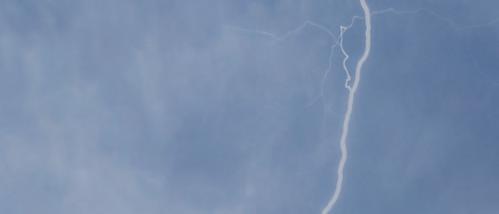
COMPANY WRENCH
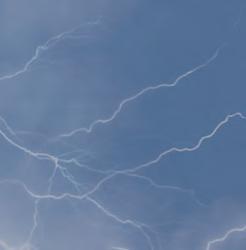
www.companywrench.com 4805 Scooby Lane NW Carroll, OH 43112 866-262-4181 4510 East 71st Street Cleveland, OH 44105 440-439-4567 920 Deneen Avenue Monroe, OH 45050 513-649-8105 1515 W. Epler Avenue Indianapolis, IN 46217 317-782-8850 1330 KY-151 Frankfort, KY 40601 502-699-2681
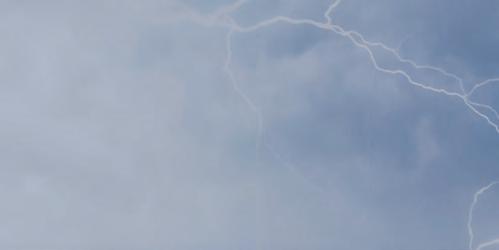
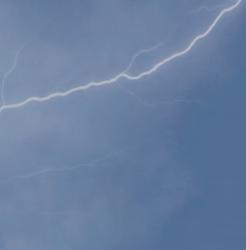
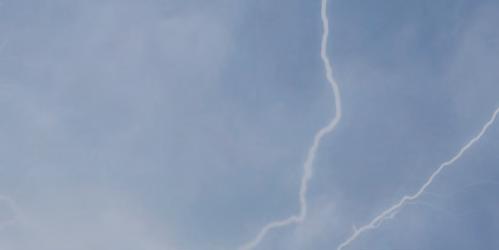
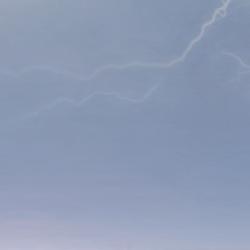
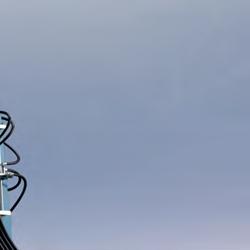
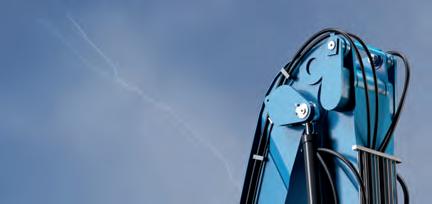
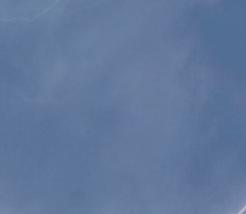
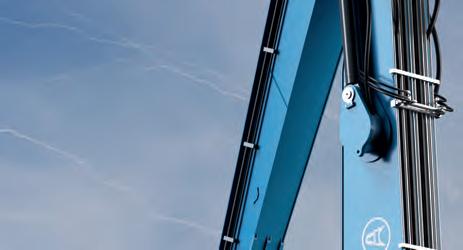
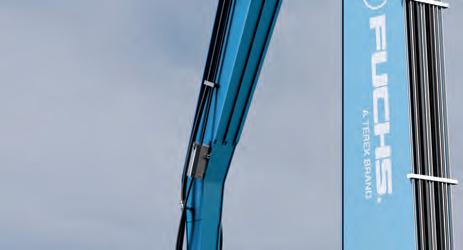
McCOY
mccoycf.com 200 Erb Industrial Dr. Fenton, MO 63026 636-349-0200 Foristell, MO 636-463-2500 Cape Girardeau, MO 573-334-0563 Cuba, MO 573-885-0500 Owensboro, KY 270-684-2339 Paducah, KY 270-554-1131 Mount Vernon, IL 618-244-6800 Evansville, IN 812-473-0484
mhl375
F-SERIES
LBAILER
GNORTS . E E. NEICFIEF .T
Dis evco r M r ore
uF chs oW rld- lC ass
Material Handlers
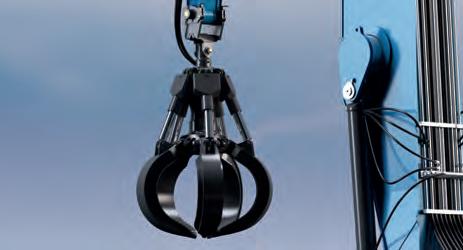
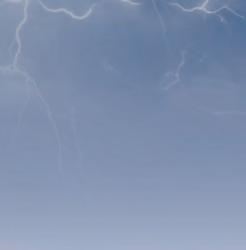
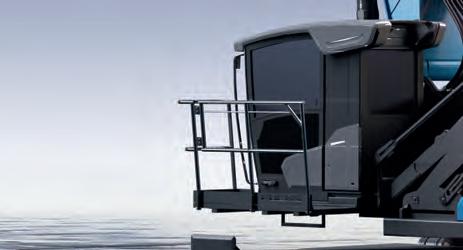
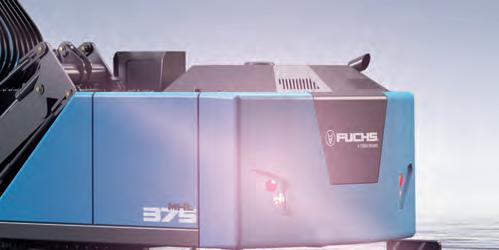
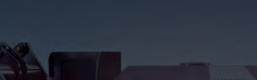
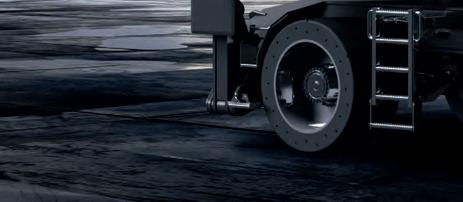
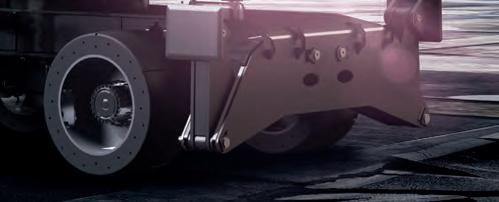

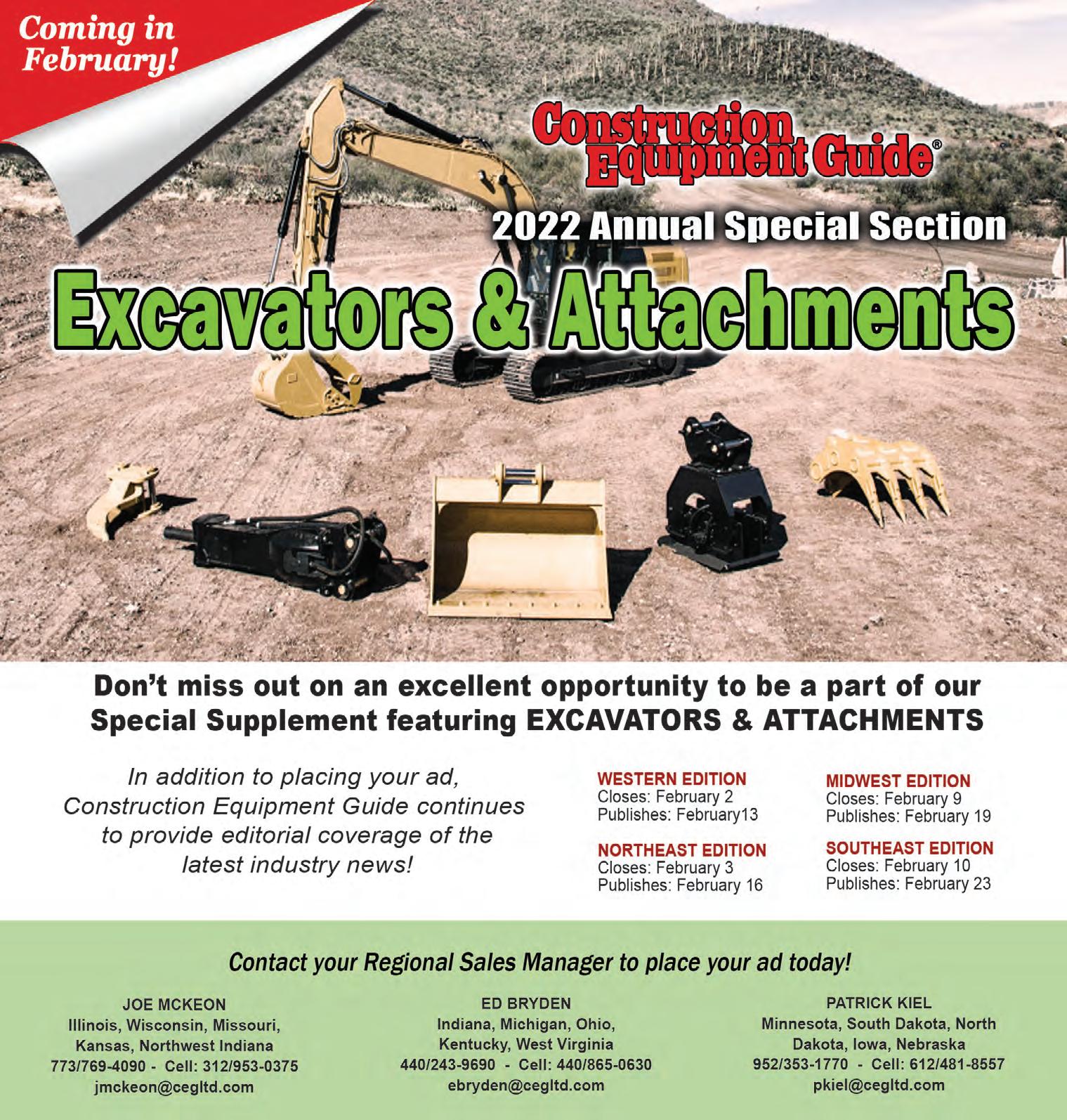