
8 minute read
HAITSMA BETON
from ConcepTueel 29-1
by ConcepT
SLENDER BEAMS SAFEGUARD CLEARANCE HEIGHT
Author: ing. W.K. (Wim) Vos MSEng
Advertisement
WIDENING OF EXISTING VIADUCTS KOERHUIS AND WILPSEDIJK ON THE A1
An extra lane over a distance of 55 km is being added to the A1 between Apeldoorn and Azelo. Contracted by Heijmans, Haitsma Beton is supplying the prefab beams for the widening of two viaducts on the A1 and two new special viaducts across the A1. Wagemaker produced the overall design for the structures for this project. The biggest challenge is maintaining the minimum clearance outline beneath the two widened viaducts, which will be achieved using extremely slender beams.
Traffic intensity on the A1 motorway is increasing all the time. This results in many delays on the A1 East between Apeldoorn and Azelo near Almelo. Good traffic flow on the A1 motorway is extremely important for the region’s economy. That is why Rijkswaterstaat, the Provinces of Overijssel and Gelderland and the Cleantech Region are expanding the A1 between Apeldoorn and Azelo between 2019 and 2025.
FIG. 1
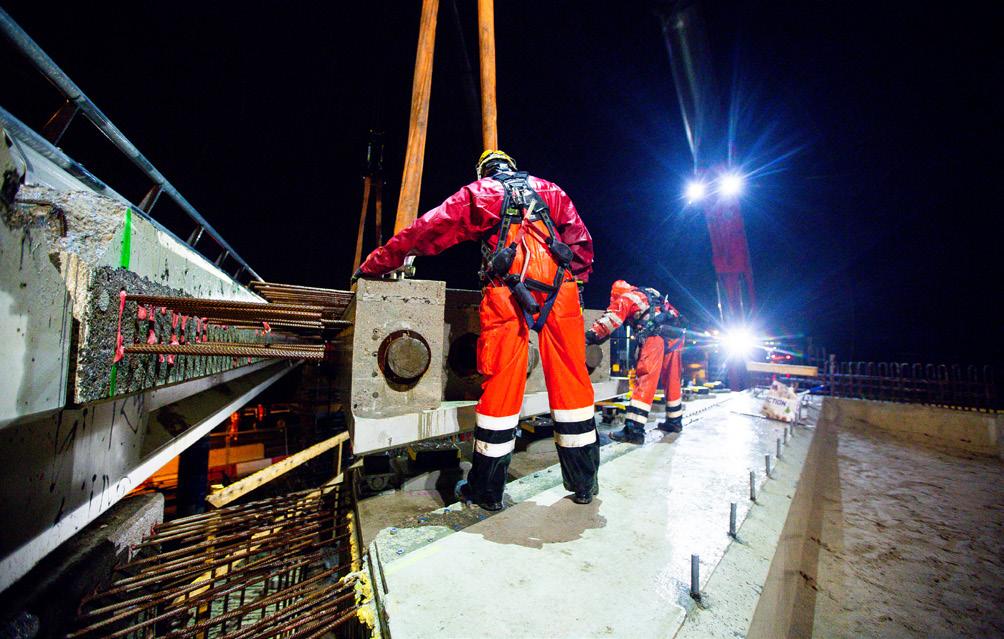
Assembly prestressed prefab beams Koerhuis viaduct | Photo: www.bouwfotografe.nl
Four structures Part of the solution for the A1 East is the widening of the A1 to include additional lanes as well as the widening of two viaducts: Koerhuis viaduct over the N348 at Deventer and Wilpsedijk viaduct over the N790 at Wilp. Two new viaducts will also be constructed. The Oxersteeg ecoduct will be constructed east of Deventer. This is a viaduct over the A1 next to the existing viaduct for car traffic. The new viaduct will be a passage for animals, pedestrians and cyclists. This will be achieved through combining a cycle and footpath with a green zone. Finally, De Wakels cycle viaduct over the motorway in the Rijssen area will be entirely renovated. The reason for this is that the central column of the existing viaduct is restricting the widening of the A1. The main span of the new cycle viaduct is almost 40 metres and will be achieved using box girders.
Slender dimensioning The widening of the Koerhuis and Wilpsedijk viaducts forms a considerable challenge. Koerhuis viaduct is the largest, with a total length of almost 83 metres and three intermediate supports. This viaduct is being widened by around five metres (2 x four beams) on the north side and by almost nine metres (3 x four beams) on the south side. Wilpsedijk viaduct is a lot smaller, with one span of 20.5 metres. This viaduct is being widened by five metres on both sides (two beams per side).
The existing decks of both structures have a cross slope of 2%. This means that the top side of the widenings will also need to be constructed with the same camber. A 9-metre widening will result in the outer edge of the deck being 180 mm lower. This will not achieve the required minimum clearance outline for the road that passes underneath. It was not possible to make any modifications to the alignment of the underlying road network. This means that, to achieve the required clearance height, the bottom of the beams in the transverse section will be aligned horizontally. This will progressively reduce the construction height of the beams towards the edge of the deck. The lower construction height means that the prestressing will be almost horizontal in the beam, resulting in almost no upwards prestressing load. It is, therefore, necessary to use a curved box to satisfy the minimum arch requirements. Widening of Koerhuis viaduct Three beams are required to realise the approximate 9-metre widening on the south side. Two horizontal beams are required for the north side. With the four fields, this results in a total of twelve beams for the south side and eight for the north side. The widening will form one deck construction together with the existing deck. The existing deck of KW037 Koerhuis comprises prestressed prefab beams finished with a topping. This topping is cast at the site of the intermediate supports, which results in a statically indeterminate deck construction. This creates hogging moments in the deck construction. The deck widening also needs to be constructed using the same statically indeterminate system. That is why the four beams will be linked longitudinally. This will be achieved via protruding reinforcement, continuous prestressed channels and a wet connection joint. Considering the significant weight of these solid prefab specials, it is also necessary to partly prestress the beams. Without this prestressing, the beams may simply collapse under their own weight during lifting. The interconnection of the reinforcement and longitudinal prestressing creates one long continuous beam of approximately 83 metres. However, the beams also need to work together as one unit in the transverse direction. To achieve this, starter bars needed to be anchored into the existing deck every 125 mm, into both the top and bottom of the topping. Over 2,600 holes needed to be drilled in the existing deck for this. All these starter bars must be anchored at exactly the right location and at the right depth. This is necessary as the equivalent number of starter bars protrude from the prefab specials, also with a centre-to-centre distance of 125 mm. The starter bars from the prefab beams and the anchored starter bars in the existing deck, fit together like a zip. Cross section of the Koerhuis viaduct widening with 3 new beams to the left of the existing deck | Figure: Wagemaker FIG. 2
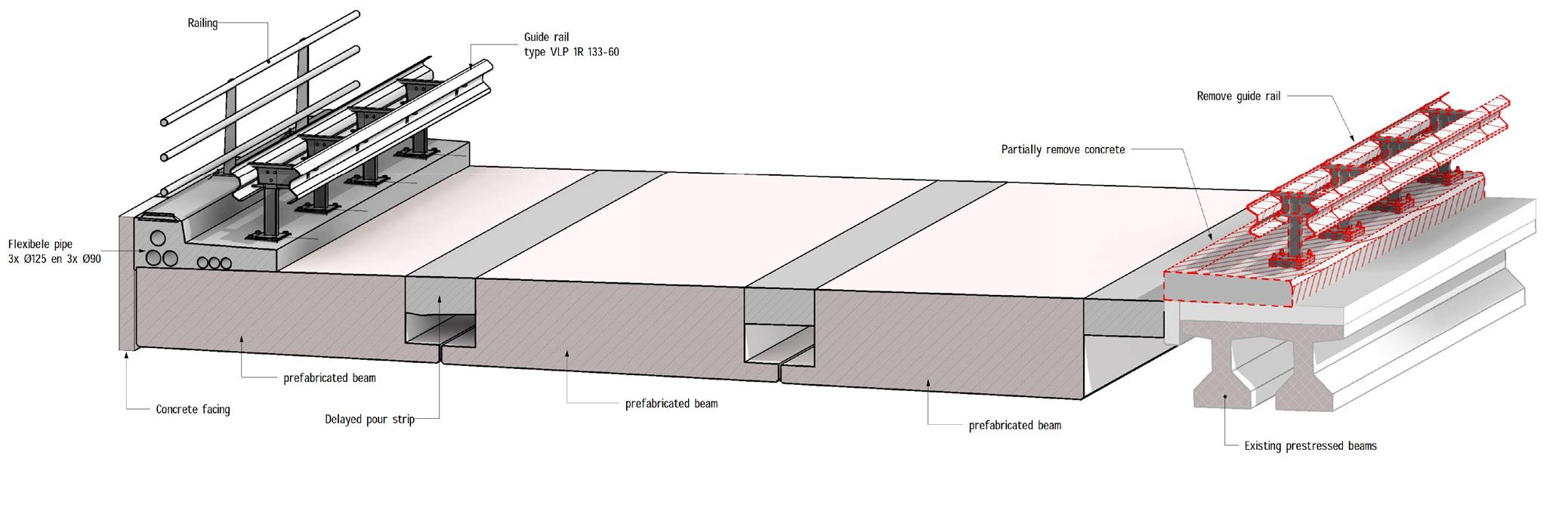
FIG. 3
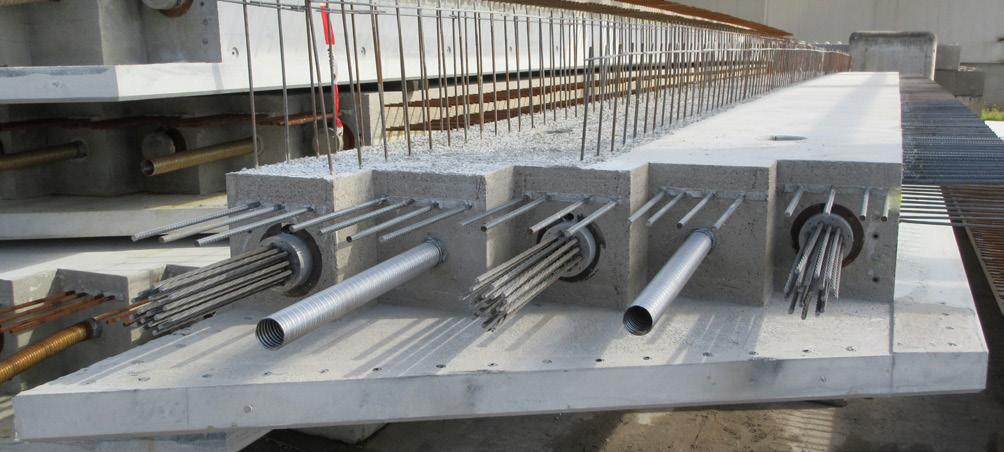
Prefab beam in the curing location at Haitsma Beton | Photo: Haitsma Beton B.V.
Widening of Wilpsedijk viaduct The same construction method with starter bars is also being used in the Wilpsedijk viaduct widening. An additional focus point for the Wilpsedijk viaduct is the transverse prestressing in the existing deck. No
starter bars could be anchored at the location of this prestressing, which meant that the physical and structural integration of the reinforcement for the pouring strip became quite a puzzle. This was finally achieved through good coordination between all parties. The starter bars from the prefab beams and the anchored starter bars in the existing deck, fit together like a zip | Wagemaker FIG. 4

Creating one construction After all the beams for the widening had been installed, these “separate beams” needed to form one construction. This took place by first filling the pouring strips and the wet connections between the new beams with concrete. Continuous prestressing was applied once the concrete was sufficiently cured, in which the prestressing in the field was as low as possible, and was as high as possible for the intermediate supports. Interconnecting the beams longitudinally creates a statically indeterminate deck construction. As the space between the existing deck and the new deck construction is still open, the prestressing remains entirely in the new deck section, which can also deform freely without causing forces in the existing deck. This also enables shrinkage and creep of the beams to occur freely without causing structural response in the existing deck. Once most of the shrinkage and creep formation has occurred, the pour strip is finally cast between the existing deck and the new deck. This took place over one weekend, which kept the A1 open to traffic. In that weekend, the traffic was directed to the central lane as far as possible. This kept the vibrations in the curing pour strip to the minimum to enable good connections between the new and existing decks. Once the pour strip had reached the required concrete strength, the existing deck and widened deck started to work together as one construction and the widening was complete.
Client, Heijmans Project Leader, Hans ten Voorde from Heijmans Infra BV: “Twenty beams from 16.70 metres to 26.60 metres in length were delivered in early December 2019 for the Koerhuis viaduct. The heaviest beam is around 125 tonnes. For the Wilpsedijk viaduct there were four beams of 20.92 metres. These structures are extremely special because the ‘continuation’ of the existing cross slope of the A1, combined with the available minimum clearance outline of the underlying road network, placed restrictions on the available construction height. Heijmans and Wagemaker have resolved this by designing solid prestressed beams that can be cast together using wet connections.” In the end, the beam assembly ran really smoothly. The hundreds of starter bars from the box girders were a perfect match. This meant that these could be installed well within the allotted time.
Why choose Haitsma Beton? Hans ten Voorde: “In realising this structure we were seeking a company that had all the disciplines in house - production, assembly and post-stressing - as well as a company in whom we had confidence that the elements could be produced in this way. Being able to contribute ideas and having an eye for quality and precision were important aspects. We found the right price-quality partner in Haitsma Beton. A great example of this is that Haitsma Beton took the initiative to lay the beams for the Koerhuis structure next to each other in the curing location to enable detection of any potential conflicts between the starter bars. I find such initiatives to control risks to be really positive.” Ten Voorde concluded: “During the many consultations between Haitsma Beton, Wagemaker and Heijmans, the aim was always to work together to achieve the best solution. Openness, looking critically at each other, but having understanding for each other’s viewpoints contributed to the good cooperation on this project and resulted in a fantastic widening of the structures.”
FIG. 5

Assembly prefab beams Wilpsedijk structure | Photo: www.bouwfotografe.nl