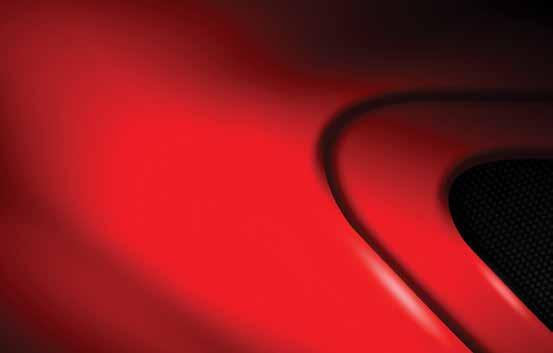
49 minute read
PUBLISHER’S PAGE
OUR STORY IS YOUR STORY
For the last 20 years we’ve covered a lot of ground together
BY DARRYL SIMMONS
Time sure flies when you’re having fun. It seems like just yesterday when Remy Rousseau and I were pondering cover ideas for the first edition. Lorenzo D’Alessandro was the inaugural cover story. It was a great call, as we enter the 20th year of publishing, he exemplified and still does, the mission of Collision Repair magazine: to champion and celebrate the successes of Canada’s collision repair industry. In those days, change was happening at what we thought was breakneck speed. The industry was in transition, pivoting from bodyshops that primarily focused on getting work out the door to high-tech and highly trained repair facilities. Insurer relations were different -- appraisers and adjusters were key linchpins in the process. Now we’re looking at artificial intelligent (AI) estimating with automatic parts ordered at point of impact. high price liability to avoid litigation, shops are scrambling to get ‘approved’. But as we saw in the United States with one OEM who reached capacity, there are no guarantees out there. So around and around we go
For the past two decades we purposely focused our editorial direction on the people of the industry. This is the backbone regardless of the processes, or lack thereof. No matter how this industry changes and progresses, it will always be the people who make the difference. There’s not enough room to mention the names here, but we are here now due to the foresight an vision of industry leaders such as Sam Mercanti, Des D’Silva, Steve Leal, Tony Canade, Michael Macaluso, Ken Freisen, Julio Bruno, Jay Perry, Tom Bissonnette, Nick DiLuca, Roland Taube, Lorenzo D’Alessandro – and who could forget Sam Piercey, whose prose published
For the past two decades we purposely chose to focus on the people of the industry
In addition most of the tasks done by the insurers in the ‘old days,’ are now done at the shop level with computer software.
Over the past two decades we documented and reported as the industry image transformed for the better. In fact, we may have even played a role in improving the public image. From 2000 to today, the number of shops in the country was halved. Although shop numbers shrank, productivity and repair volumes increased across the country.
Along with improved efficiencies, we saw the development of insurers as partners, sharing administrative paperwork ultimately handled at the shop level. To think, at one point, shops never relied on a computer -- their sole role was fixing a car based on an appraiser’s estimate.
Today, more than 75 percent of the dollar volume of repairs is conducted by some sort of network, be it a franchise, buying group or multi-shop-owner. However, the more things change, the more they stay the same. The new trend is certification and pretty much we are right back at the starting line of the insurer Direct Repair Programs (DRP) of 20 years ago. With the behemoth players involved and the risk of in our magazine still rings as relevant today as it did when he first wrote it.
But this is not a trip down Memory Lane, at least not yet. Our 20th Anniversary Edition is coming up soon and we want everyone to take part. After all, our story is your story and who can tell it better than those who lived through it carving out the destiny with toil, sweat and a lot of swear words.
Our editors and writers are on hand ready to hear from you and receive your pictures, comments and anecdotes. Think of it as a yearbook, as a record to pass down to the next generation. Never before has anyone put together an account of the industry in this manner.
This is an industry built with pride and welldeserved success. The history of Collision Repair magazine is the history of Canada’s collision repair industry. Let’s do it justice and celebrate with style. It’s a great story, let’s tell it together.
PUBLISHER
Darryl Simmons
publisher@collisionrepairmag.com
ASSOCIATE PUBLISHER
Orest Tkaczuk | orest@mediamatters.ca
EDITOR
Allison Rogers | allison@mediamatters.ca
STAFF WRITERS
Max Reid | max@mediamatters.ca
ART DIRECTOR
Yvonne Corvers | yvonne@mediamatters.ca
GRAPHIC DESIGN INTERN
Victoria Volkova | victoria@mediamatters.ca
VP OF INDUSTRY RELATIONS & ADVERTISING
Gloria Mann 647.998.5677 | gd.mann@rogers.com
DIRECTOR OF BUSINESS SOLUTIONS
Ellen Smith 416.312.7446 | ellen@mediamatters.ca
INDUSTRY RELATIONS ASSISTANT
Wanja Mann (647) 998-5677
wanjamann1@gmail.com
DIGITAL OPERATIONS MANAGER
Cassie Doyle | cassie@mediamatters.ca
CONTRIBUTORS
Tom Bissonnette, David DiCenzo, Burak Edirnecik, Stefano Liessi, Julia Lloyd, Jay Perry, Chelsea Stebner, Dianne Park Thach,
SUBSCRIPTION Single edition $10.99 One-year $59.99 ( 8 issues) Collision Repair™ magazine is published bimonthly, and is dedicated to serving the business interests of the collision repair industry. It is published by Media Matters Inc. Material in Collision Repair™ magazine may not be reproduced in any form without written consent from the publisher. The publisher reserves the right to refuse any advertising and disclaims all responsibilities for claims or statements made by its advertisers or independent columnists. All facts, opinions and statements appearing in this publication have been compiled and included with the permission, though not necessarily the endorsement, of the editor, or of independent columnist contributors, and are in no way to be construed as those of the publisher, or as endorsements of them.
PRINTED IN CANADA ISSN 1707-6072 CANADA POST CANADIAN PUBLICATIONS MAIL SALES PRODUCT AGREEMENT No. 40841632 RETURN POSTAGE GUARANTEED
Send change of address notices and undeliverable copies to: 317 Reid St., Peterborough, ON K9J 3R2
“We acknowledge the financial support of the Government of Canada”
Collision Repair magazine is published by Media Matters Inc., publishers of:
QUICKEST, SIMPLEST AND MOST ACCURATE 3D MEASURING SYSTEM IN THE WORLD
Made in Canada - NO Moving Parts, NO Lasers, NO Targets, NO Adaptors, NO Magnets - NO Arms, NO Extensions, NO Wires, NO Wi-Fi, NO Bluetooth - NO Calibration Needed, MITCHELL chassis data
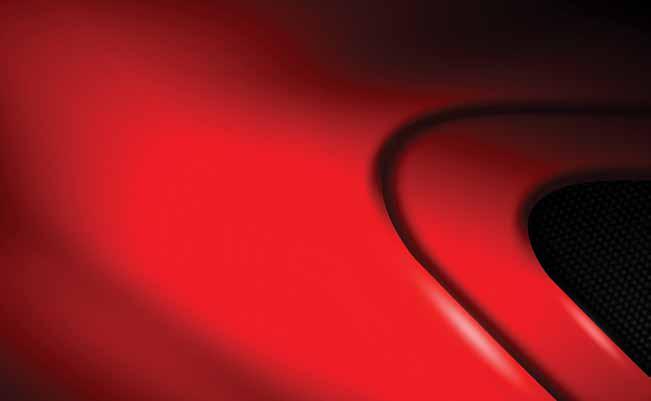
NEW
NOW INCLUDES WHEEL ALIGNMENT DIAGNOSTICS SOFTWARE
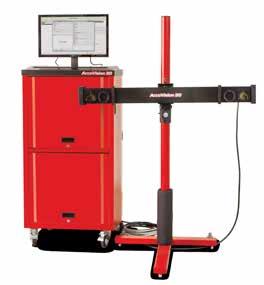
ACCUVISION-3D®

IS RECOGNIZED BY CERTIFICATION PROGRAMS - Certified Collision Care - CCIAP - Honda - ICBC
ACCUVISION-3D ®
IS RECOGNIZED BY Smart Spot welder CERTIFICATION PROGRAMS - CCIAP Automatic setting of parameters ACCUVISION-3D - Honda ® Water cooled for hi productivity IS RECOGNIZED BY 22 ft. long cable, No EMF emissions CERTIFICATION PROGRAMS - CCIAP Output 14,000 Amps, 450 daN or 700 daN Input 50 Amps, 208-240V, 3 Phase - HondaAUTOMATIC, INVERTER Approved by OEMs RESISTANCE SPOT WELDERS 3680 model wi-Fi, enabled for factory Updates and diagnostics 3664 & 3680
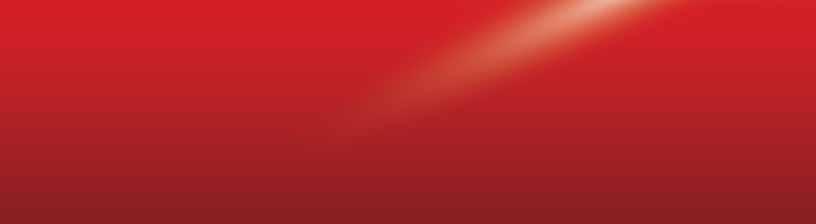
50-DAV-1WM
Wall Mount, 8 CFM, Air operated, Dry Vac system for Aluminum dust, 100% Stainless Steel construction, 20ft.Air/Vac hoses incl.
ACCUVISION-3D ®
IS RECOGNIZED BY CERTIFICATION PROGRAMS - CCIAP
- Honda
arslanauto.com
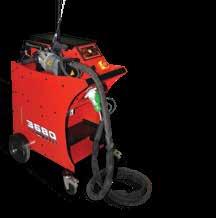
50-DAV-5
Floor model, 8 CFM, Air Operated, Dry Vacuum for Aluminum Dust, 100% Stainless Steel construction, 20ft.Air/Vac hoses incl.
50-WAV-5
Floor Model, 8 CFM, Air Operated WET Vacuum for Aluminum Dust, 100% Stainless Steel construction, 20ft.Air/Vac hoses incl.
accuvision-3D.com Contact your distributor or Call (800) 465-8575

PEOPLE ON THE MOVE
JEFF LABANOVICH | CHIEF OPERATING OFFICER | CARSTAR CANADA
Jeff Labanovich has been named chief operating officer for CARSTAR Canada. Labanovich has been a part of the CARSTAR Canada family for more than 15 years, joining first as a franchise partner and then the corporate team in 2018. As COO, Labanovich will continue to lead the insurance and operations team and will have an increased role in driving overall strategy for the CARSTAR Canada business.
CHARLES AUBRY | ACCOUNT MANAGER | PROGI
Progi has named Charles Aubry has been appointed to the position of major account manager for automotive paint companies in Canada and abroad. Having only joined the team at Progi three years ago, Aubry quickly climbed the ladder at the company thanks to his “down-to-earth ideas to improve productivity in collision shops and the sound advice he gave them at the height of the COVID-19 pandemic.”
TONY MAMMONE | VP OF OPERATIONS | CARSTAR CANADA
Tony Mammone has been named vice president of operations for CARSTAR Canada. Touting more than 20 years of experience in the collision repair space, Mammone served on the insurance side of the industry as a field adjuster before advancing to a number of leadership roles. As vice president of operations, Tony will continue to lead the operations team but have an increased role in managing our insurance teams, aligning the company’s overall strategy.
SONIA BOUTHILLETTE | FIX AUTO CANADA
Sonia Bouthillette has been appointed vice president of operations for Fix Auto Canada. Bouthillette is a results-oriented professional with over 20 years in the automotive industry, said Fix Auto. She joined the company’s operations in 2009 as director of insurance relations and has held several regional and national roles within the sales and operations functions. In her new role, she will be responsible for the network’s operational efficiencies in the Canadian collision repair business.
Pre 8am LTL Delivery Dedicated Logistics Pre 8am Package Delivery
MOST RELIABLE PRE 8AM DELIVERY SERVICE
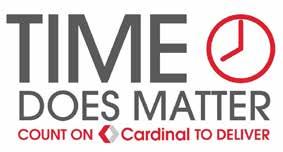
The new SATA filter 500 series 100% technically clean air
Air flow with 4 connections approx. 3.800 Nl/min (135 cfm) Optimised compressed air treatment through separation of water, particles and harmful substances Fine filter and activated charcoal filter cartridges fit perfectly by being simply inserted - without screw fittings or additional seals Maintenance-free bayonet lock with haptic and acoustic feedback Line connection optionally left or right Synchronised maintenance: Filter maintenance only necessary every 6 months for all stages
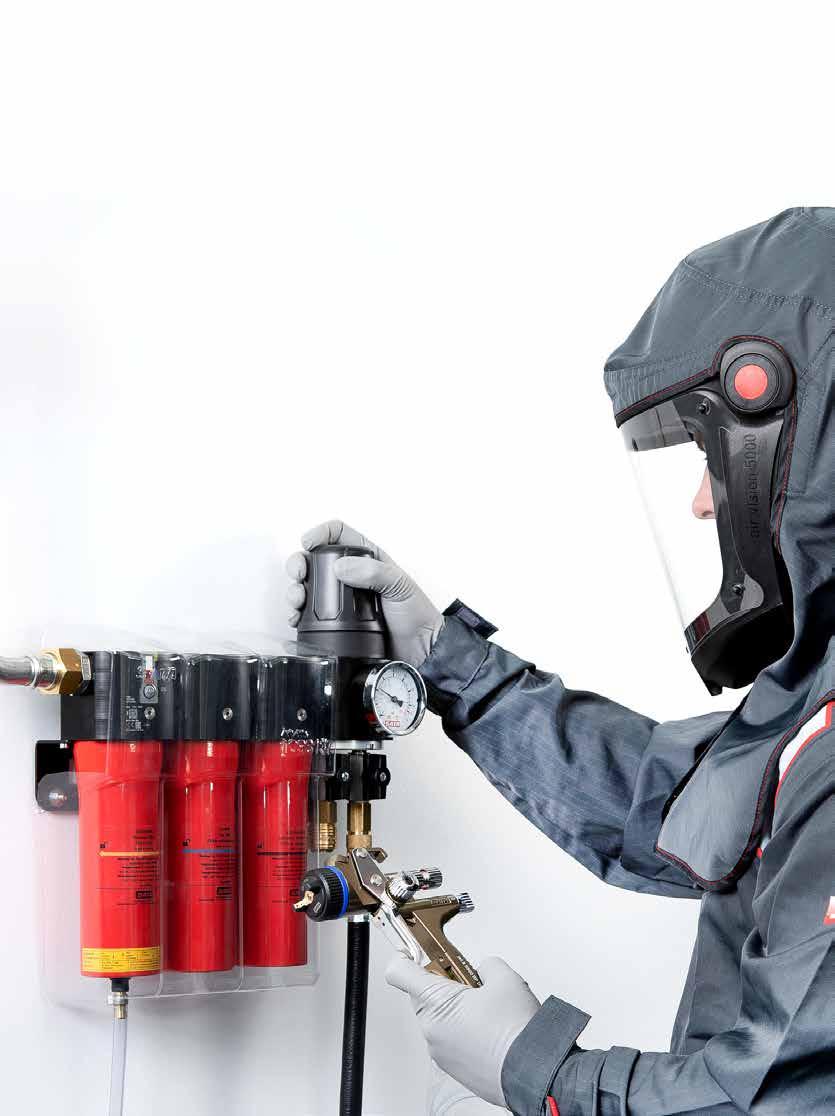
YouTube

SATA Canada Inc. 125 Buttermill Avenue Vaughan, ON L4K 3X5 Phone: +1 905 660 1101 Toll-free: +1 844 554 SATA (7282) Fax: +1 905 760 1250 contact@sata.ca www.sata.ca
MASTERING THE JUGGLING ACT
Jeff Hampshire’s journey to perfecting production
CCS Southgate Collision Centre is located in Edmonton, Alberta.
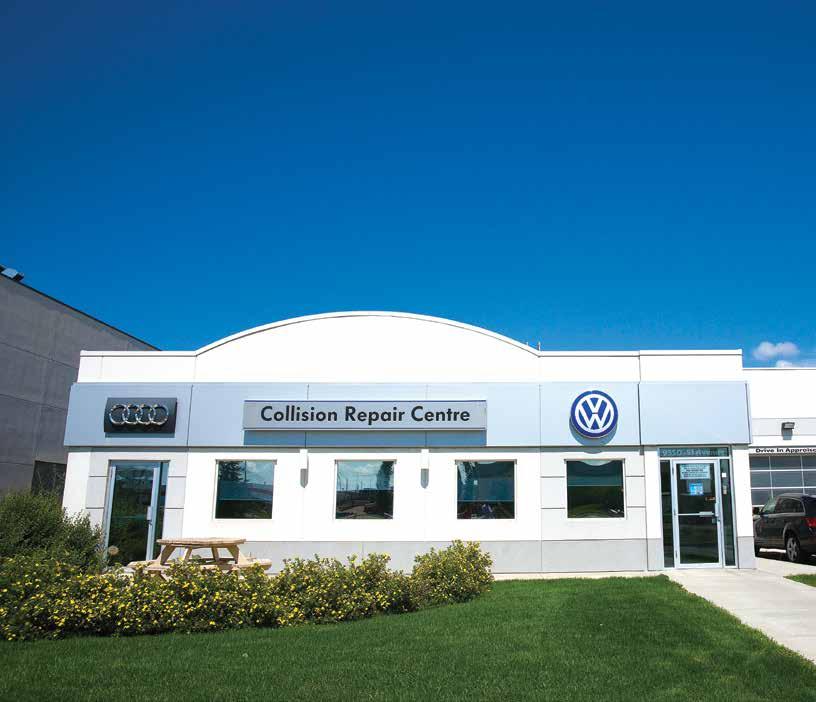
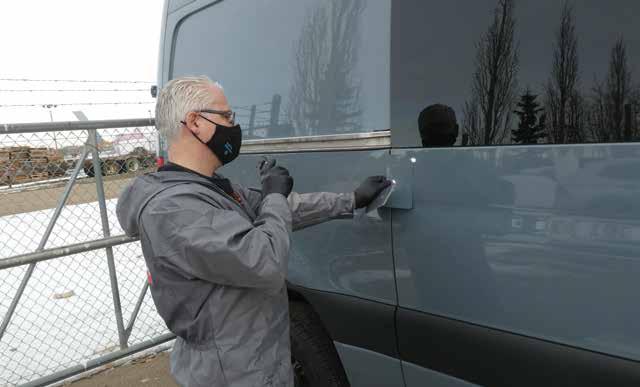
CCS Southgate Collision is hugely proud of the long-standing status of its staff—all but one employee has been with the company for upwards of 10 years.

“When you are up front, you have to juggle a whole bunch of different things. We have to keep the insurance companies on our good side, and we have to keep the technicians happy. We must keep the customers pleased and we need to be able to maintain a profit to stay in business.” – Jeff Hampshire, bodyshop manager, CCS Southgate Collision
Jeff Hampshire, bodyshop manager for CCS Southgate Collision Centre.
BY MAX REID
When you’re running a high-volume, dealership-affiliated shop in a major city, it can be easy to get lost in the shuffle.
You can get overwhelmed by the competition, lose focus on your staff and maybe even see the quality of your shop’s work start to slip.
It takes a cool temperament, a wealth of experience and a genuine passion for quality repair work to set you apart from the crowd—all things that are second nature to Jeff Hampshire and his team at CCS Southgate Collision Centre.
Jeff is an industry veteran and an old-school bodyman at heart, and even though he’s no longer on the farm fixing up his old ‘68
Cutlass, he still applies the same care and dedication to repairing his customer’s cars as he would his own. Twelve employees strong and with certifications from Audi and Volkswagen under his belt, Jeff and CCS Southgate have nowhere to go but up in their home base of Edmonton, Alberta. But there is an entire career of growth and lessons learned that have led up to this point. That is why Collision Repair sat down for an interview with Jeff Hampshire, to share in his insights and experiences coming up in the collision repair industry. “What really got me started into wanting to become a bodyman was when I was about sixteen years old and I was in my garage working on my old ‘68 Cutlass,” Jeff recalled. “I bought a can of Bondo from Canadian Tire, sanded a fender down and primed it. “I thought I did a pretty darn good job of it and I brought my dad over, back on the farm,” Behold, Jeff’s very first stress test. “He gave it a hit and the Bondo fell right out of it. From there I decided I was going to learn how to do this properly.’ Jeff took this tough lesson in stride and doubled down on the hobby that would one day become the trade that supports his family.
“After that, I had a love and passion for cars and it’s kind of what got me into the trade. I loved doing custom work back in the old days. Now I love doing the collision work,” said Jeff.
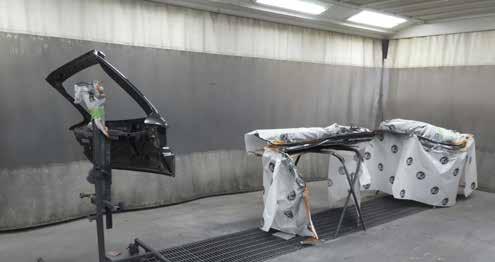
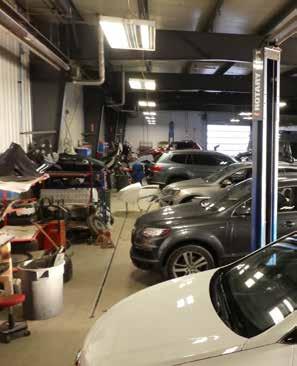
With direct Volkswagen and Audi programs, CCS Southgate Collision sources all of its repair info from OE sites and through the training it receives from Audi and Volkswagen, which it calls “second-to-none.”
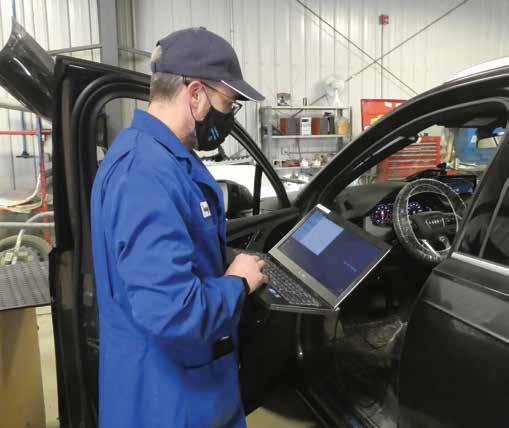
Jeff credits much of his success to his ability to secure an Audi certification for his shop and his partnership with CCS which he says has led to more business coming through his doors, as well as access to top-of-the-line training and resources from his OEM affiliates.
Over the years, Jeff went on to develop his chops at bodyshops around Edmonton, making his way as a technician in an always-changing industry.
For one reason or another, his path often crossed into the managerial side of things throughout his career, and eventually after working as an assistant manager at another shop in town, Jeff realized his knack for leadership and dove in headfirst.
“Through my whole career, I’d gone from being a technician in the back to helping to run the shop and going back and forth doing different things,” said Jeff.
“Sixteen years ago, I entered into the dealer group here and I never looked back.”
Jeff proved he could do it all, having developed a keen understanding of the bodyshop and its many moving pieces during his own time in the repair bay.
“I kind of slid into it fairly easily. I mean, they are two different roles and I had to learn to look at things differently. When you start thinking of the costs of everything and trying to keep all that in line; it’s different when you’re a technician who thinks, ‘This is what I need to do the job, and this is the number of hours it will take.’”
Jeff quickly realized that his mentality around repair work would have to change in order to be successful.
“When you are up front, you have to juggle a whole bunch of different things. We have to keep the insurance companies on our good

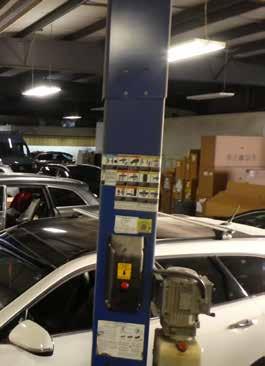
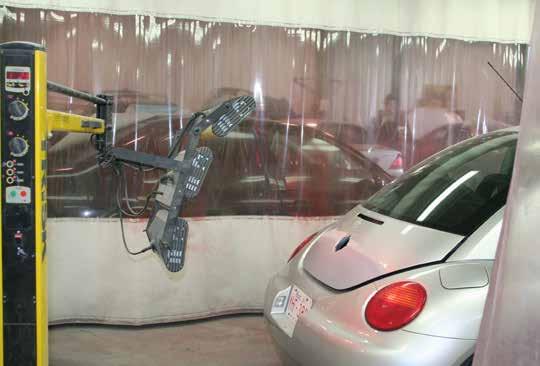
Pre-pandemic, CCS Southgate Collision pushed through approximately 160 cars per month.
side, and we have to keep the technicians happy. We must keep the customers pleased and we need to be able to maintain a profit to stay in business.
“When you’re in the back shop and you’re focused on fixing the car and doing what you need to make that car right, you don’t consider there’s so much to juggle to make this all happen properly.’”
It would be hard to argue that Jeff has not struck that balance between businessman and bodyman perfectly, however, as even in spite of
the uncertainty of the last year, he and his loyal team continue to deliver impressive results.
“During our normal operations, when times were busy (pre-COVID), we were running about 160 cars a month. Right now, we’re averaging about a hundred,” said Jeff.
Though he would be the first to admit that CCS Southgate wouldn’t be where it is today without the hard work of his staff.
“At the moment we have 12 employees. One of things we pride ourselves on is the high number of long-term employees we have. All but one of my staff have been here for more than 10 years—two of them have actually been here right from the get-go. They were brought in in the detail department and worked their way up.”
Jeff admitted that there’s little he feels more pride in, than seeing one of his techs rise up in the industry and hone their craft. In fact, when he’s not working to build his own brand at Southgate, Jeff makes a special point to give back to the programs that brought him the loyal and trustworthy staff that he has today.
“I believe in the apprenticeship program and I’m actually part of a pre-enrollment program and I’ve been on the board for years since it was first started here in Alberta,” said Jeff.
“I believe in the apprenticeship program and training wholeheartedly. We need training
and certification, and I don’t think it should be taken lightly. These vehicles are complex, and everybody’s safety relies on somebody being trained properly to repair them.”
Jeff credits much of his success to his ability to secure an Audi certification for his shop and his partnership with CCS which he says has led to more business coming through his doors, as well as access to top-of-the-line training and resources from his OEM affiliates.
“We have all the direct Volkswagen and Audi programs, so it’s not like we’re getting third-party information—we’re getting it directly off the Audi and Volkswagen sites and the training we get from Audi and Volkswagen is second-to-none.
“That’s one nice thing about being part of a dealership too, is with a lot of our cars we work in conjunction with the service department to make sure that everything is back the way the factory intended it to be.”
But when it comes down to it, the dealership affiliation and fancy certifications are just bonuses to a craft that Jeff has already shown himself to be a master of. Were he back on the farm, Jeff would still be pouring his heart into every repair he makes and thinking not only of making the customer’s day, but his own staff as well.
“The interaction with people is really what drives me. Going back out with a customer at the end of that repair and walking them to their car and just having them get their car back and just be excited about it again.
He continued, “And of course, my family is always motivating me to succeed because I want to provide for them and it’s the same with my staff. I want to give them an opportunity to make as much money as they possibly can in this industry and hopefully a good working condition to do it in.”
Jeff and his team continue their hard work at CCS Southgate every day, always looking to secure more certifications, train more staff and create the best bodyshop environment possible.
These vehicles are complex, and everybody’s safety relies on somebody being trained properly to repair them.” – Jeff Hampshire, bodyshop manager, CCS Southgate Collision
DELVING INTO DIGITAL
3M has invested in asTech, citing a “continued commitment to advance the digitization” of the aftermarket supplies giant. Terms of the deal were not disclosed. “The 3M Ventures strategic investment in Repairify [asTech’s parent company] enables us to accelerate our solutions and offerings across the entire automotive ecosystem,” stated Cris Hollingsworth, president of Repairify, regarding the investment. “We seek to make strategic investments that will advance our innovation and growth,” said Ben Wright, director, 3M Ventures. “We are moving rapidly to an even more digital-first world, and we see those shifts in the automotive aftermarket. This investment signifies our continued commitment to advance the digitization of 3M as well as of the customers we serve.” According to asTech’s press release, “terms and conditions of the investment…will be announced in a separate press release later.”
TWENTY THOUSAND STRONG
A Change.org petition created in support of the Your Data. Your Choice campaign demanding consumer access to vehicle data has garnered more than 20,000 signatures. The Canadian campaign advocating for consumer control of vehicle data–which is currently ruled by OEMs–was first announced in November 2020 by the Automotive Industries Association of Canada (AIA Canada). The U.S. Your Data. Your Choice petition has nearly 30,000 signatures so far.
FIGHT FOR YOUR RIGHTS
An active voice in the debate surrounding vehicle data rights, the CAR Coalition, a U.S.-based lobbying group advocating for “Right to Repair” legislation for collision repairers, has released their organization’s Call-to-Action. The CAR Coalition released a video where they outlined their call on government to draft consumer-minded legislation that aligns with the organization’s four key principles of “safety first, empower consumer choices, foster industry competition and keep consumer costs low.” An excerpt from the video states that “When a vehicle needs to be serviced or is damaged, the repair process is personal for the owner. It can also be overwhelmingly expensive. This is why it is so important that consumers have options when it comes to vehicle maintenance and repair. The auto manufacturers should not dictate how, when, or where a vehicle is repaired – the vehicle owner should. In today’s advanced world, the how, when, and where comes in the form of data. What’s more, vehicle owners should be in control of any data their vehicle produces. This will ensure they have the ability to take their vehicle to the repair shop of their choice and not be limited to manufacturer-only repairs.”
PLAYING MATCHMAKER
Oakville, Ontario-based company CrashBay is poised to play matchmaker with the launch of their new collision centre search engine. The automotive e-commerce company first launched CrashBay in 2019, and now with the updated ability to search through a database of thousands of certified repair shops, they are helping connect drivers and repairers across Canada and the U.S. and get them through what CrashBay founder, John Harvey, referred to as an often “confusing, fragmented and inconsistent process.” Users simply go to the company’s website and enter their city into the search bar. The search engine then identifies all nearby shops, from which you can then narrow down further into specific certifications and even book appointments straight from the website. Membership for shops to be a part of CrashBay’s online network is always open, and promises that “signing up includes several benefits for car repair businesses, including increasing brand visibility, accessing a wide variety of marketplace benefits, and the ability to book extra work,” according to the press release.
TAKING ON TOUCHLESS
COVID-19 has sent the automotive claims process digital, with the majority of insurance carriers adopting virtual claims processes in the last year, says Mitchell International’s latest industry trends report. According to Mitchell’s report and data and analytics company LexisNexis Risk Solutions, 95 percent of auto insurance carriers are embracing virtual claims handling, with many now setting their sights on touchless estimates. For the North American auto insurance industry, automated or ‘touchless’ estimates remain the end goal—but technological evolution needs to take place to strive closer to such an objective. The transformation from field appraisals to the “Holy Grail” of touchless claims is not done overnight or entirely by machine, says Mitchell. Appraisers are a key to developing and improving processes through introducing automation gradually through implementing virtual estimating and human-machine collaboration in guided estimating. The guided estimating process involves artificial intelligence (AI) that guides the appraiser through each decision point. The goal s to put more power in the appraiser’s hands while leveraging the AI for useful recommendations. Following this process comes the implementation of fully automated claims.
For the collision repair claims space, touchless claims remain the “Holy Grail” end goal, says Mitchell.
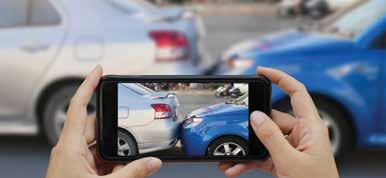
PASSING ON PUBLIC TRANSIT
A new report calculates that millions of Toronto transit riders dropped their TTC habits in favour of ride-sharing platforms Uber and Lyft, resulting in a revenue loss of at least $74 million in 2019. According to the report, released by a group called RideFair Coalition, in 2019 an estimated 31.4 million TTC trips were lost to the two major ridesharing platforms. The shift to Uber and Lyft not only means a financial hit for the TTC, the report says, but also more private vehicles circulating on Toronto roads. The RideFair Coalition says it is a diverse group of individuals and organizations supporting “fair regulations” for ride-hailing. Its founding members include two Toronto taxi companies as well as the Amalgamated Transit Union Local 113. While similar reports for other major Canadian cities are not currently available, some ridesharing apps—including Lyft in Vancouver—will present public transit alternatives like nearby TransLink and BC Ferries alongside ride-booking options, giving customers a full breadth of choice. Neither Uber nor Lyft in Toronto presents the same opportunity.
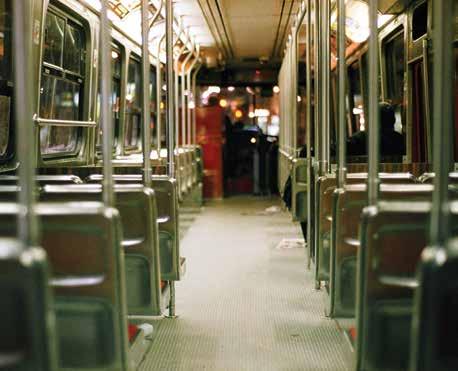
Even pre-pandemic, Canadians were leaning toward the prospect of ridesharing or taxi use over public transit options in Toronto.
PERFECT YOUR PAINTING IN THE BOOTH
Pro Spot’s Anti-Static Gun Ion Spot
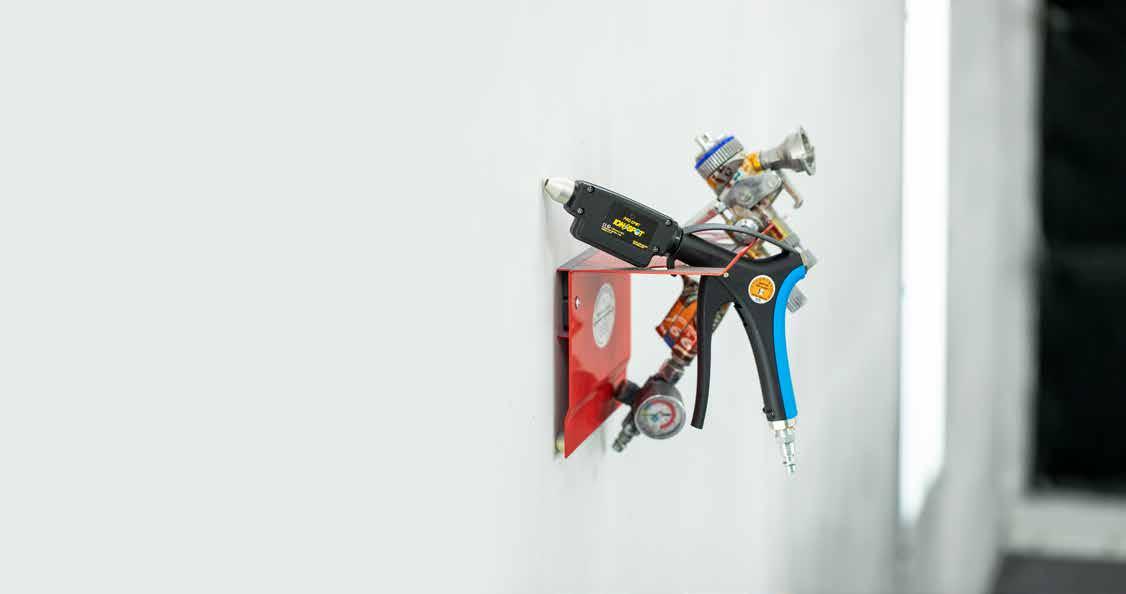
• Eliminate static and dust in seconds • Improves paint adhesion • No batteries - paint booth safe
Contact Your Distributor Today
Li-Cycle is raising funds for global expansion by going public on the New York Stock Exchange (NYSE) in a deal that values the battery recycler at US$1.7 billion. The five-year-old private company has unveiled plans to merge with Peridot Acquisition Corp., an NYSE-listed special acquisition corporation (SPAC). If approved by shareholders in both companies, the transaction will bring US$615-million into Li-Cycle. The business combination includes a pre-money equity valuation for Li-Cycle of $975 million and, when combined with the transaction proceeds, represents a combined company pro-forma equity value of $1.67 billion. Upon closing, the combined company will be renamed Li-Cycle Holdings Corp. and will be listed on the New York Stock Exchange under the new ticker symbol “LICY.”
CALIBRATION CONNECTION
asTech has acquired adasThink in what feels like a “natural fit,” for the Canadian startup, said adasThink co-founder Nick Dominato. “There are some amazing synergies that adasThink can have with asTech,” Dominato told Collision Repair. “asTech is a leader when it comes to OEM diagnostics and calibrations, and that aligns with our mission to identify OEM required ADAS calibrations and the required documentation. It was a natural fit. We’re incredibly proud of what we’ve done in this short time. We can’t wait to see where the support of asTech’s its resources, knowledge and technology will bring us.”
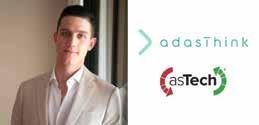
asTech has acquired adasThink in what the Canadian startup founder calls “a natural fit.”
CASH, CREDIT OR CRYPTO?
HGreg auto group is now accepting cryptocurrency for payment on new or used vehicles. The company said the move was made to meet its “desire to constantly evolve and improve [its] customers’ shopping experience.” Cryptocurrencies are not tied to banks or the government and users can spend money anonymously. According to recent reports from Canada’s Associated Press, digital currency has become so popular that more than 300,000 transactions occur in the average day. The most highly-traded cryptocurrency—and the highest valued—is Bitcoin, which hit a record-high Feb. 16 with a single unit trading at US$50,600
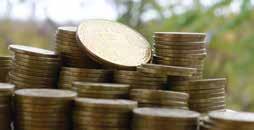
Quebec-based HGreg auto group is now accepting cryptocurrency payments on new or used vehicles.
How’s your 2021 going so far? According to the latest report from Desrosiers Automotive Consultants Inc. (DAC), that may depend on what province you live in, as sales numbers for the light vehicle market are scattered across the board in Canada, with figures ranging drastically from province-to-province. With the experience of the COVID-19 pandemic varying significantly based on the region in which you live, so too do the results found in this latest report from DAC which shows both notable spikes and declines in light vehicle sales on a provincial level. The report shows an estimated 39.1 percent decline in sales in January for Quebec, who faced strict lockdown restrictions and curfews throughout that time. Conversely, Newfoundland experienced a 24 percent jump in sales in the first month of 2021, “albeit at a lower and in turn more volatile volume,” according to the report. Fellow east coast provinces, PEI and Nova Scotia also reported sales increases of 11.9 and 5.2 percent, respectively. Across the country, British Columbia saw a 4.5 percent climb and Alberta a 9.4 percent fall in sales volume. Ontario, which accounted for over half of the sales decrease in 2020, saw its sales fall 19.7 percent in January. Overall, the light vehicle market is down 17.4 percent to an estimated 90,890 units sold, as compared to 109,988 units in January 2020.
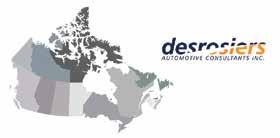
Overall, the light vehicle market is down 17.4 percent to an estimated 90,890 units sold, as compared to 109,988 units in January 2020.
UH-UH, UBER
Many Canadian Uber drivers and couriers are rejecting Uber’s proposal unveiled in mid-March, which aimed to ease tensions between Uber’s independent contractors and the ridesharing/food delivery giant. The proposal for the potential solution to tensions between the company and its contracted workers, Flexible Work+, would have asked that provinces mandate benefit funds for app-based gig employers to provide perks and safety training to employees, while still maintaining the freedom to determine their own working hours. Uber workers are currently classified as independent contractors who are not required to be given benefits or minimum wage like employees would be under provincial laws. According to these workers, the so-called solution “doesn’t address any of the real issues that workers have been talking about,” which include living wages, sick pay and more stability for workers. Uber has countered the requests by arguing that workers want the flexibility to choose when, where and how often they work and don’t want to be tied to formal schedules that could come with traditional employment.
3M Awards 2020 Rick Berg Award
3M recently awarded Brett MacNeil with the 2020 3M Rick Berg Award. Brett is a senior sales account representative in 3M Canada’s Automotive Aftermarket Division dedicated to the Western region.
Brett has demonstrated exceptional service and commitment within his territory to the automotive aftermarket industry, building strong relationships with jobbers and going above and beyond to service his customers and find the best solution for their business, says 3M. Faced with unprecedented challenges from the ongoing global pandemic, Brett pivoted and found new ways to bring value to his customers, focusing on getting them key information and hosting virtual training sessions for them when in-person visits weren’t possible. Brett’s approach to customer service and his strong knowledge of the automotive aftermarket is a testament to the honour of winning the Rick Berg Award.
His actions and efforts have demonstrated professionalism both to the industry and customers, but also to within the 3M team. Brett is a true team player with the capacity to assist his peers and provide valuable input to the leadership team.
Brett is very knowledgeable about the aftermarket challenges and continually strives to find ways to help customers be effective and efficient in their operations.
The Rick Berg Award, named after a former 3M business leader who passed away in 2010, is awarded annually to a 3M sales representative that exhibits the highest level of performance and sales professionalism in the Automotive Aftermarket Division. The winner is a sales leader that exhibits strong ethics and leads by example with passion and energy and Brett is a perfect example of this.
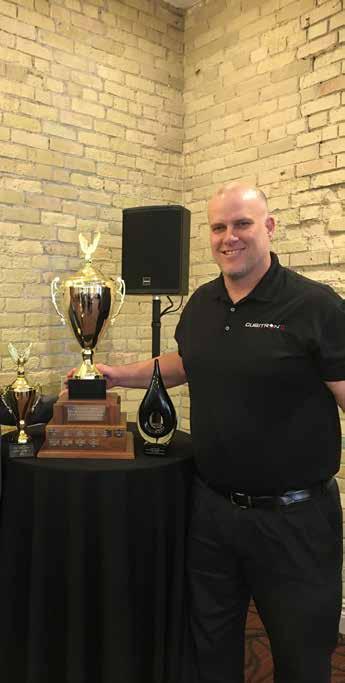
A MANDATORY MOVE
BMW Collision Program Manager Jonathan Inzano is reminding collision repairers that pre- and post-scans are no longer an option with today’s modern vehicles. “Before and after any collision repair there must be a pre- and post-scan,” he told a March Guild 21 call.” Inzano noted that pre- and post-scans also bring the ability to accelerate repairs, in some cases. “A lot of the time it can actually save time in the repair. If you’re pre-scanning a vehicle you are already identifying sometimes the issues in the vehicle versus not identifying them and now having to come back to create a supplement, order more parts, wait for parts to come in—it creates a huge backlog. At the end of the day, scanning is not only necessary but is also an efficiency measure.” The postscan, said Inzano, is crucial to ensure all issues have been rectified. “Some faults will create a dash light as soon as you hop in, but others won’t. There’s really no way to tell unless you scan the car once more, clear the faults and make sure nothing returns. “It’s not optional—it’s necessary,” said Inzano. “It’s your due diligence to the proper thing.”
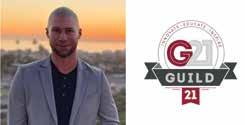
In his second recent appearance on the Guild 21 virtual stage, BMW collision repair program manager reiterated the importance of pre- and post-scans on all collisions and repairs.
PREFERRED PUSH
Assured Performance network’s U.S. branch has announced a “successful” Nissan campaign pitching certified bodyshops to nearly four million Nissan and 500,000 Infiniti customers. Assured Performance said the campaign results in a “tenfold increase” in the number of hits on the OEM’s shop locator tool. The automaker’s consumer awareness campaign aims to “further educated and refer vehicle owners to their nearest Nissan Certified Repair Provider and provide them with important links and instructions.” The campaign touts the tagline, “What’s Done is Done, So Get Repairs Done Right.” Nissan also says the campaign will offer customers free tows to their nearest Nissan certified collision centre within 50 miles (80 kilometres). The automaker nor Canada’s Certified Collision Care—which is powered by Assured Performance—has not clarified whether the same campaign was issued in Canada.

GETTING GROUNDED
Techs that work on hybrid vehicles everyday know the challenges that come with combining traditional combustion engines with battery-electric technology; that’s why the experts at ALLDATA have put together a list of safety tips to keep in mind when working on Honda and Hyundai hybrids. The full list of hybrid tips, safety and otherwise, can be found at ALLDATA.com.
TOYOTA TCB
The people’s voices have been heard and the results are in; Toyota Motor Company has been chosen as Canada’s Most Respected Auto Manufacturer by the Canadian public in a recent nationally representative public opinion survey. “Respect is earned, not just by manufacturing strong products, but through a combination of trusted local service and support, industry leadership, corporate values and genuine community engagement,” said Jeff Munn, executive director of Canada’s Most Respected Award Program. Honda, Subaru, BMW and Mazda rounded out the top five of the 13 total automakers reviewed by the public.
FREEDOM TO CHARGE
According to an announcement from Volvo Cars, the Swedish automaker intends to make the ICE a thing frozen in time, as the company plans to convert entirely to online EV sales by 2030. In a move that the company is saying will “transform the current wholesale market”, Volvo plans to launch a brand-new line of EVs to be available only online in time to make them an exclusively online EV manufacturer by the year 2030.
PEOPLE PLEASERS
As part of a project four years in the making, Hyundai Canada has compiled nearly 87,000 independently submitted customer reviews of their vehicles and are pretty pleased with what they found. “Of those reviews, 40,985 owners have given their vehicles an overall score of 10/10, while 23,208 owners have scored their vehicles 9/10,” according to the press release. Overall, 93 percent of owners rate their Hyundai products as an 8/10 or above. Four years ago, Hyundai partnered with Reevoo, a user-generated content collection platform to help them measure performance and improve their offerings using independent customer feedback.
DAS APPROVAL
Car-O-Liner has earned official approval from Volkswagen for use of the company’s VAS 6755A Resistance Spot Welder on VW’s vehicles going forward. Put through a gauntlet of third-party tests, the welder was based on Caro-Liner’s CTR® 9 spot welder and designed to VW’s high standards of quality and will feature a special Volkswagen 16A welding cap, Volkswagen-specific software and the new Shelf and Clip Kit and Dust Cover. “Volkswagen recognizes that the high performance VAS6755A welder meets their requirements for high-quality repairs of their modern, technologically advanced vehicles,” said Jonny Jangdin, product manager at Car-O-Liner.
INSURANCE NEWS
Car-O-Liner’s VAS 6755A Resistance Spot Welder has been approved for use on Volkswagen vehicles.
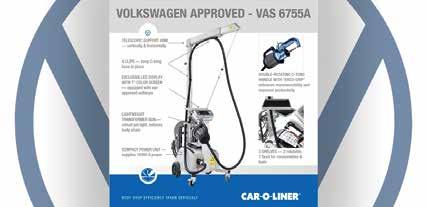
SETTING THE SCORE
Nova Scotians with good credit are in for a treat if they drive under Co-operators General Insurance, now that the company has announced that credit scores can now be used as a rating factor for auto insurance, following the regulator’s approval. According to the regulators, this move from Co-operators is likely a symptom of increasing competition in the credit-based insurance market. “Co-operators…noted several competitors had introduced credit information in their rating algorithms and said it wanted to avoid being put at a competitive disadvantage,” said regulators.
CHEQUE PLEASE, NO TIP
Meeting its promise to return a portion of the $600 million in savings accrued during the pandemic, the Insurance Corporation of British Columbia (ICBC) has announced that drivers in the province will have rebate cheques in their pockets come March. All customers who had a policy with ICBC from April to September of 2020 are eligible for a one-time rebate of about $190 per customer. According to ICBC, the $190 cheque makes up for 19 percent of the average premium rate paid by BC drivers during the pandemic and is to be sent out to 2.86 million drivers in the province.
British Columbian drivers will soon be happy to (finally) see insurance rebate cheques in their mailboxes.
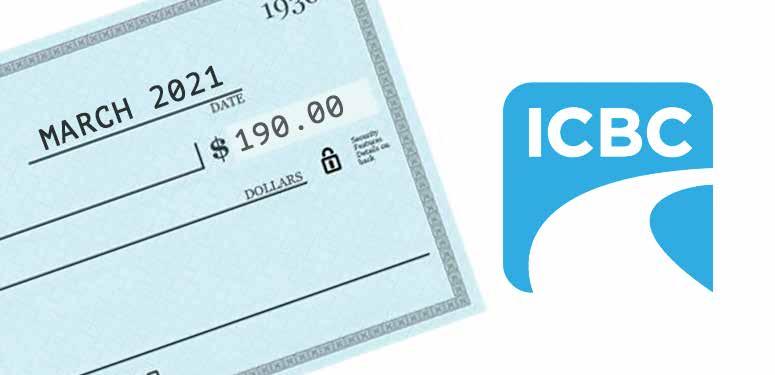
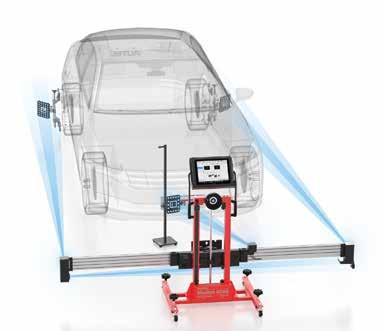
When technicians speak about the calibration of Advanced Driver Assistance Systems words like accuracy and precision are always used. Because they know just how sensitive the cameras, sensors and components of these systems are and that an improperly aligned component and/or one incorrectly calibrated can have dangerous consequences.
True ADAS calibration professionals realize that every requirement and instruction set forth by the vehicle OE is there for reason and that shortcuts have no business being taken on the shop floor.
Case in point, an examiner for the Insurance Institute for Highway Safety (IIHS) looked at the failure of a Honda Civic’s forward collision autobraking system, which in their test resulted in delayed action and subsequent obstacle collision at 20 mph. The IIHS examiner found that the technician had failed to follow OE procedures including parking the vehicle on level ground, identifying the center of the vehicle and properly measuring distance from target to vehicle. That was never done, “they were just eyeballing it,” the IIHS examiner said.
The IIHS examiner never said why the technician failed to follow the correct procedures—lack of the right tools or equipment, poor training or that he simply found the measuring process time consuming and/or tedious and decided to take a shortcut. And why the excuse is unimportant, it’s true, the setup processes for the ADAS calibrations are time consuming, and tedious. Calibration systems developers have heard technician’s lament and answered with new systems or adaptions for existing ones that not only drastically cut the setup time but also ensure a more precise positioning of the vehicle. No plumb bobs, no chalk, no measuring tape.
Autel’s IA800 is one such solution and it is the definition of efficiency. Described as an Intelligent ADAS optical positioning system, the IA800, employs six high resolution cameras and ADAS positioning software, to transform Autel’s Standard Calibration frame into a rapid yet precise frame centering and vehicle distancing unit, enabling technicians to accomplish frame to vehicle placement in less than a minute. Compare that with the mechanical tools setup that takes on average 40 minutes.
Wheel clamps with camera targets are attached to the rear wheels and a standing target component is placed in the front of the vehicle by the vehicle badge. The tablet, now placed securing on the frame, is paired with the cameras.
The system recognizes the positioning targets and calculates the current angle, distance and offset position of the frame to the vehicle. The technician simply follows the onscreen instructions to move the frame or adjust the angel of it until the current values match the required values. A green check mark will display for each parameter once the required position values are achieved. That’s it, the vehicle is ready for calibration. The IA800 is a game changer for efficiency and precision.
American automotive technology company CCC Information Services is reporting a more than 50 percent year-over-year increase in claims processed using artificial intelligence (AI) and deep learning. The company also reports that more than 5 million unique claims have been processed using a CCC deep learning AI solution, and the number of claims using two or more of its AI applications has more than doubled year-over-year. Today, more than 75 U.S. auto insurers are actively applying CCC’s advanced AI to power claims decisions and improve policyholder experiences, said the company via online press release. The company says the sharp growth is spurred by a combination of increased adoption, expanded applications and the more than 300-strong library of AI models supporting personalized claims decisions.
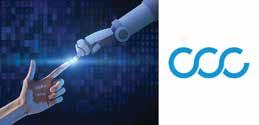
Artificial intelligence (AI) is claiming its stake in the collision repair space as U.S. insurers make moves to power claims processes with AI operations.
MOBILE OFFICES
Bell Canada and Honda have teamed up to ensure that Canadian drivers are never offline when they’re on the road, as the automaker announced that all new Honda and Acura models will be equipped with built-in Wi-Fi hotspots. Drivers will be able to stream with up to seven devices through the Bell.ca/ConnectedCar program over Bell’s 4G network.
BEWARE THE BATTERIES
With electric vehicles gaining popularity, emergency responders may be in serious danger–especially since the automaker’s emergency response guides are reportedly not up to par. According to a new report conducted by National Transportation Safety Board (NTSB) emergency responders may not be able to rely on emergency response guides provided by automakers when dealing with an electrical vehicle fire. The investigation examined three electric vehicle crashes resulting in fires and one non-crash fire involving an electric vehicle. In each case, emergency responders faced major safety risks related to electric shock, thermal runaway, battery ignition and reignition, and stranded energy.
A partnership between Canadian auto parts manufacturer Magna International and material and chemical giant DuPont is looking to elaborate on the concept of using adhesives rather than welding to bond vehicle liftgates. Spurred by increasing demand for lighterweight vehicle solutions as electrification spreads, the two companies are currently attempting to simplify the manufacturing process, reduce the required bonding time and accelerate the curing process. The challenge comes in ensuring a flexible process that works for all automakers and meets customer demands, said Sid Asthana, global director of material science for Magna. The companies also maintain the technology will be “a critical component” in future automobiles, especially autonomous vehicles.
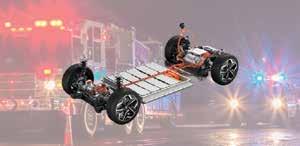

The first bonded liftgate by Magna appeared on the 2020 Acura RDX and the 2019 Jeep Cherokee, which won the company a first-place finish in the body exterior category at the 2018 Society of Plastics Engineers (SPE) Automotive Awards.
VOLKS-REALITY
Volkswagen is exploring virtual reality (VR) training delivery to educate collision repair students on the automaker’s technology, repairing mixed materials, joining techniques, electric vehicle repairs and more. During February’s SkillsCanada Automotive Technology Summit, Volkswagen collision repair program manager Scott Wideman delivered a demonstration and discussion of the automaker’s endeavours in VR training. The demo featured two videos: the first documenting a battery repair on a 2020 Volkswagen e-Tron, and the second featuring body repair technology with mixed material substrates and joining techniques. Wideman said the OEM has already launched its VR battery repair concept training for Audi technicians and it is working to someday introduce VR welding training. “The VR program will allow [students] to see what speed they are welding at, what the weld penetration is, the quality of the weld, so they can maintain that skill and develop it further,” he said. “Think of the impact and what it would mean for technicians in the field.”

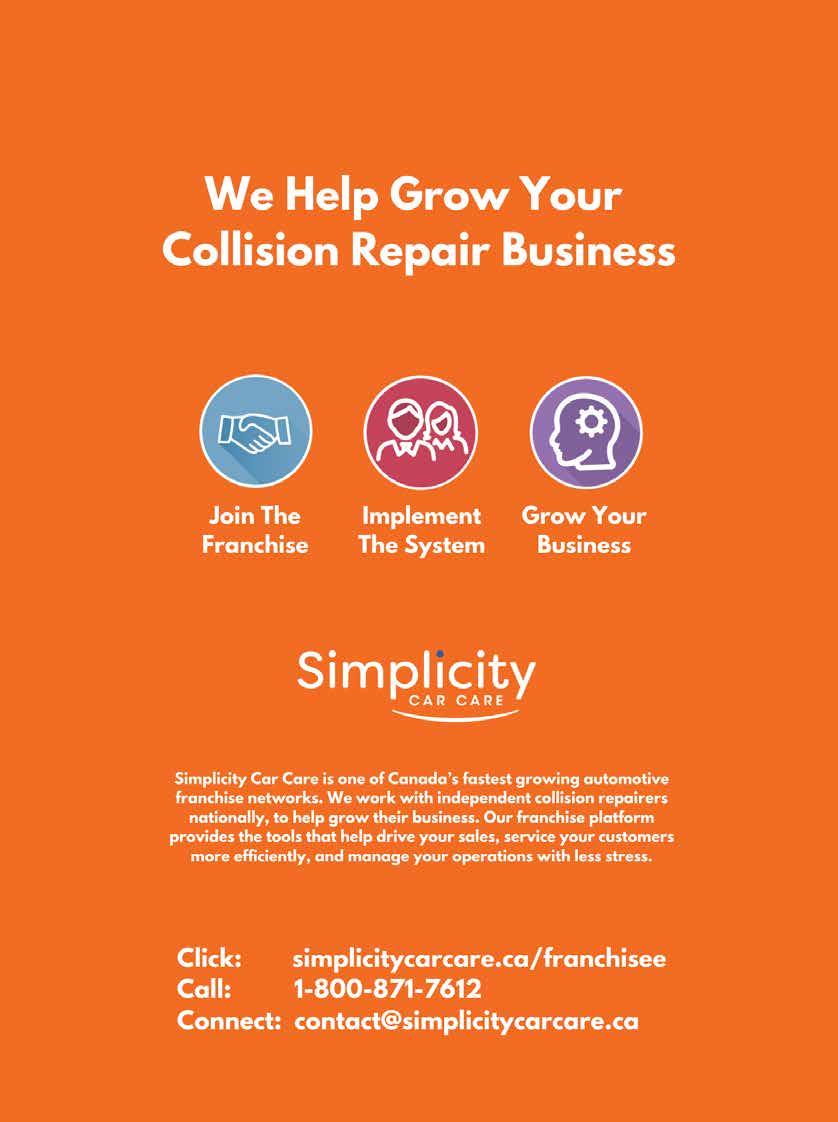
AND THE KITCHEN SINK
A Nanaimo man may have better luck with Judy after his demand to the British Columbia Supreme Court for $32 trillion and an audience with Queen Elizabeth fell on deaf ears, following his harrowing bike accident. Tyler Adam Chamberlin filed a civil suit against the Insurance Corporation of British Columbia (ICBC) in November of 2018 after he was allegedly struck in a hit-and-run while riding his bicycle in Nanaimo. Most recently, Chamberlin represented himself at his March 1 B.C. Supreme Court hearing, which included lawyers for ICBC, the Attorney General of Canada, the Attorney General of British Columbia, the City of Nanaimo, Nanaimo Regional General Hospital and the Chief Electoral Officer of British Columbia. At the hearing, Chamberlin presented his modest demands: $32 trillion, the “reconstruction” of the RCMP, 500,000 shares in Tesla, the suspension of trade between Canada and China, the release of various classified documents, an MRI of his entire body, the dismantling of Transport Canada, a private meeting with the Queen and the “cleaning up of the swamp,” which was not defined in the court documents. On March 5, judge Douglas Thompson dismissed Chamberlin’s suit, saying his claims were “scandalous, vexatious, and otherwise an abuse of process.” Claims suggesting that the driver involved in the hit-and-run incident was the Hamburglar in the middle of a getaway have not yet been verified.
PUT THE BILL ON BELL
About seven months ago, David Rooney received a car wash he never asked for. The high-pressure water excavator the Bell employee used did the job a little too well and left in Rooney $1,500 in the hole for paint repairs to his 2012 Hyundai Genesis. It was an honest mistake. The employee splashed some mud on Rooney’s car and used the highpowered earth-boring tool to try and gently wash away the mess. “There was quite a wash of water, probably 10 feet high,” said Rooney. Rooney assumed that receiving compensation for the damage would be simple, especially considering that the employee admitted he was at fault—but Bell had other plans, Rooney was dragged into a legal battle with the company and Super Sucker Hydro Vac Service; the company hired on Bell’s behalf. Telecommunications companies often have the right in Canada to enter onto a person’s property in order to carry out maintenance deemed essential. However, according to John Lawford, the executive director of the Public Interest Advocacy Centre, often when damage is done on such visits, the victim is often out of luck when it comes to receiving compensation.
TRY, TRY AGAIN
Next time you think you can get sneaky about your vehicle’s insurance, think again, as a Halton Region police officer was forced to have a car impounded after the driver was pulled over twice within 20 minutes, in Oakville, Ontario in early March. On just the first charge, the driver was facing a minimum $5,000 fine, however, thanks to their clearly lacking stealth skills, now faces up to $50,000 in additional fines as well as the potential for a one-year license suspension.
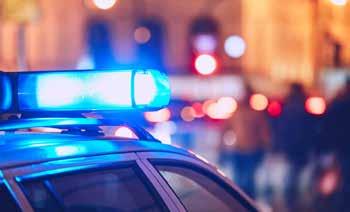
THERE’S SPIDERS IN THERE!
The idea may feel a little creepy at first glance, but the science is far from mad. A researcher from the University of Denver is proposing that Alaskan spiders and insects could possess the properties to transform the production of antifreeze. Recent University of Denver research suggests that the natural antifreeze compounds found in some Alaskan spiders and insects, as well as the Antarctic toothfish, could provide natural alternatives to the harmful chemicals used to produce traditional antifreeze products. An effort is now being made to replicate the glycoproteins in the toothfish that prevent its blood from freezing in cold waters, in order to be created into an organic antifreeze compound.

Arachnids and antifreeze, a natural combo.
THE KICKER
In late January a video of a Toronto man launching his most powerful roundhouse kick on an oncoming SUV began making rounds, prompting the internet to question his sanity. In a video shared to Instagram, the man—initially behind the wheel of a moving car— slams on his brakes to allow some ill-time jaywalkers to pass. The man then spots an SUV approaching the pedestrians at a reduced speed and deeming himself Superman in the blink of an eye, launches himself from his vehicle and into the path of oncoming traffic. Seemingly unaware that the approaching SUV has spotted the pedestrians and has slowed down to let them pass, the man then launches a kick to the vehicle’s tire before collapsing in pain in the middle of the highway.
You cannot fight a car, no matter what your personal trainer says.
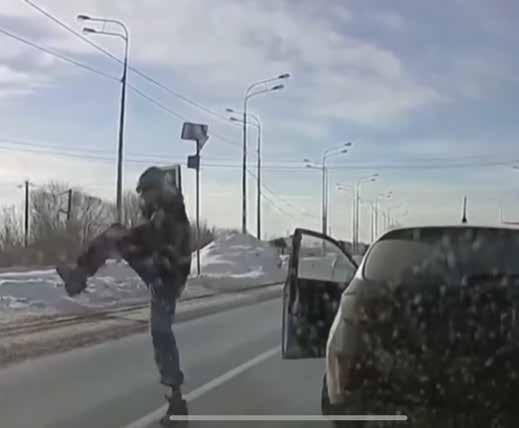
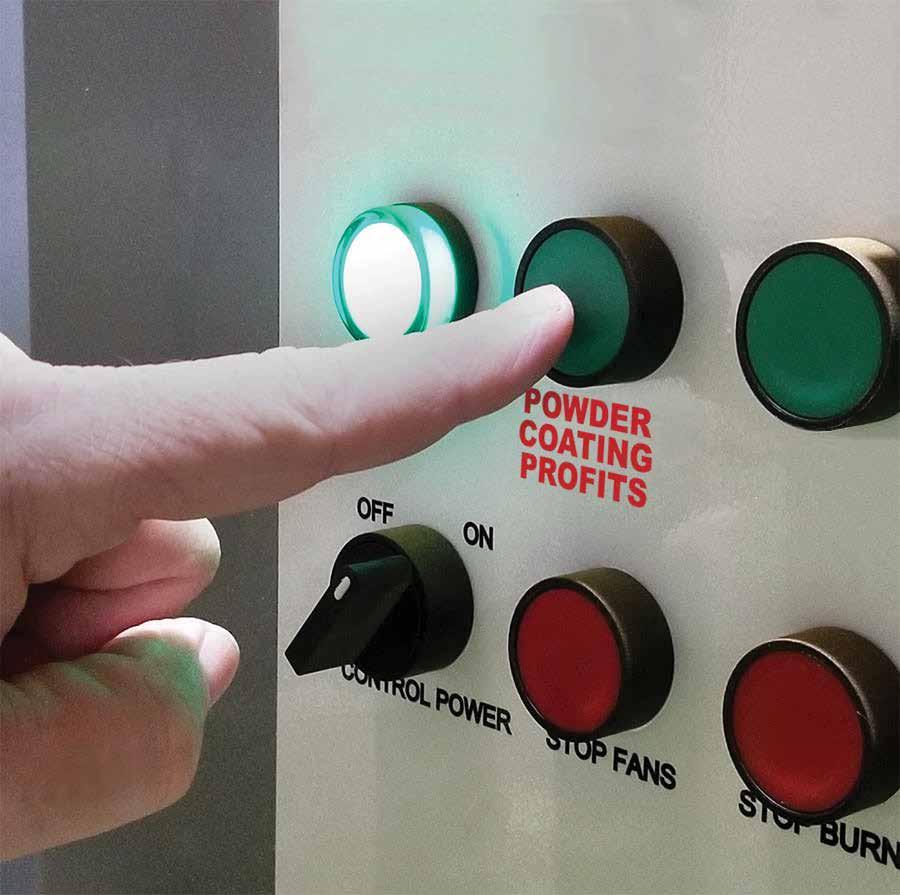
SETTING PACE
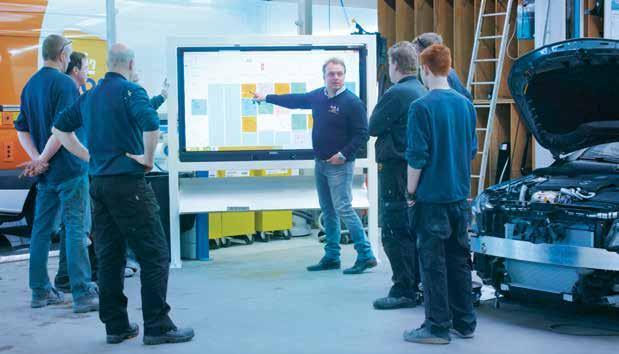
What is top production—and how do you achieve it?
BY DAVID DICENZO
John Cox, Acoat services manager for AkzoNobel, the creator of CarBeat.
The unique analytics that run in the background with CarBeat have proved to be extremely useful for owners striving for better efficiency.
Numbers are important to Mark DeLorenzo. The second-generation owner of Toronto-based Ryding Auto estimates that his collision shop would ideally service between five and 12 cars a day, depending on the size and complexity of the job.
Those were pre-pandemic figures, of course. A lot has changed in the past year. DeLorenzo echoes what many collision industry owners are saying, suggesting there has been a drop of business somewhere between 30 and 50 percent since COVID-19 radically changed the average person’s driving habits.
Regardless of that dip in the quantity of vehicles that go through the shop daily, numbers remain critical to Ryding’s success. DeLorenzo prioritizes efficiency in order to achieve what for him is top production.
He views the whole process like a Formula 1 pit stop, when the car rolls up to that exact spot so the crew can change tires and add fuel with surgical precision.
At Ryding, DeLorenzo has helped that process by developing and refining a colourized magnet tracking system that he began to implement in phases over the past couple years.
“It’s all about beating the clock,” says DeLorenzo, recalling the days when he was constantly approached by staff members about each progressive step for every car in the shop.
“The customer comes in and is given a number, which stays with the car. We go through the steps to repair the car and at the end, that number comes back.
“It’s simple.”
It’s similar to the concept of a conveyor belt with a car entering at one end and leaving at the other. From the initial estimate, through scheduling, acquisition of parts and authori-
zations, dismantling, and the ultimate repair, the car is closely monitored during each step. A green cap, for example, means ‘ready to go,’ orange is a ‘rush,’ and red means ‘hold,’ among other colours used.
The communication component–texts and emails to keep customers in the loop on progress–is generated by Mitchell RepairCenter software, which automatically sends messages after DeLorenzo has inputted relevant information.
Meeting both the customers’ needs and those of a dedicated staff means everything to the owner. The shop was established in 1965 by DeLorenzo’s father Rocky, who recently passed away at the age of 87.
There’s a reputation to maintain and as they have done since Rocky started the company, Ryding does an excellent job getting vehicles in and out with minimal wait time.
And it’s getting better. DeLorenzo’s personal system, complemented by the management software, proved to be a big hit.
In the full year he began using it before the pandemic, he believes Ryding was able to service between 10 and 30 percent more cars a day. And since then, the shop has implemented even more measures to ensure a smooth process, including layout changes and simple fixes like strategically placing tools and equipment in specific areas to reduce wasted motion.
“You have to manage your time properly,” he says. “It works well because everyone here can easily follow the system. There was a lot of wasted time previously.
“The Mitchell RepairCentre system will also tell me when I’m at capacity.”
While DeLorenzo has established his own method of striving for top production, there are several industry tools that can help the process. Sophisticated digital programs like CarBeat and ProgiPlanning offer shops a high-tech approach in the quest to maximize efficiency.
“It’s all about beating the clock.” – Mark DeLorezno, owner of Ryding Auto

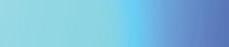

Rather than track a car’s progress manually with magnetic tiles or a dry erase marker, CarBeat tracks production digitally with a drag-and-drop screen. The system currently has about 200 users throughout North America.
Second-generation owner Mark DeLorenzo says his top-production system allowed Ryding was able to service between 10 and 30 percent more cars a day.
John Cox, the Acoat Services Manager at CarBeat’s creator, AkzoNobel, refers to the innovative program as a “visual production management tool.” It is the digital evolution of a whiteboard, which AkzoNobel has worked on implementing with customers for years.
Rather than track a car’s progress manually with magnetic tiles or a dry erase marker, it is done digitally with a drag-and-drop screen. The system currently has about 200 users throughout North America.
Cox is clear about something though – CarBeat is just one tool and any business serious about achieving top production has to embrace both a mentality and culture change.
“Ultimate production capability is based on communication and flow,” says Cox. “You can’t over produce for the next department or under produce so that there are bottlenecks or gaps.
“We preach the concept of a Process Centered Environment or PCE.”
AkzoNobel holds boot camps and provides educational content around their 10 building blocks, with the ultimate goal of continuous improvement and flow so that when a vehicle enters production within a shop, nothing will slow it down.
“The tangible goal everyday should be to produce ‘X’ amount of hours and that will be determined by what we feel is the facility’s production capability,” Cox explains. “There are a lot of parameters around that. If you have too much work on site, you will produce less. But if you have the right amount, it will allow you to achieve your optimum production capability.
“CarBeat is a tool that can help manage that. It is visual so everybody in the facility understands the state of production and accountability.
“Ultimately, the mindset of the entire organization needs to focus on maximizing productivity. It’s culture, it’s utilizing standard operating procedures, it’s understanding your capabilities.”
Cox adds that every time a vehicle moves from one part of a shop to another, there is a timestamp. The unique analytics that run in the background with CarBeat have proved to be extremely useful for owners striving for better efficiency.
All collision shops across the continent are hoping for a bounce back after the past year of drastic reductions in repairs. And Ryding is no exception. Until the numbers begin to ascend, the main focus is doing the best possible, most efficient job on the vehicles that do roll through.
It’s actually a time when top production seems critical because owners like DeLorenzo cannot absorb the impact of delays.
“We want to run things like a Swiss clock,” he says with a smile.
THE OEM AND ADAS
Are you ready to offer proper, compliant calibrations?
To adhere to OE Certifi cation requirements, you have to tackle the topic of Advanced Driver Assistance Systems in repairs. Each OEM presents a different set of requirements—from software, to test drives and beyond.
Automaker guidelines cover all elements of the repair process, from detailed diagnosing methods to the amount of empty fl oor space surrounding the vehicle. Moreover, where one OEM’s calibrations require specifi c scan tool, others allow for a third-party service, such as AirPro.
Add to that mix the bevy of aftermarket scan tools; understanding all the options is crucial.
Maintaining OEM certifi cations is another element of the ADAS conundrum. If your facility deals with one automaker primarily, achieving certifi cation with its associated program is wise to consider.
The aforementioned ideas also come into play when subletting ADAS calibrations to any qualifi ed third party. If partnering to sublet, you must physically verify and ensure your partner is an expert in the brand, and an informed, reliable resource that respects the importance OEM-required calibrations, proper tools and processes.
Once your business embraces consistency in the application of OE Service Procedures, you’ve conquered a vital step in achieving ADAS calibration capability.


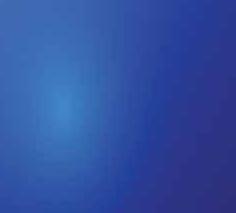
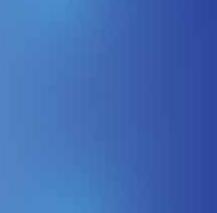
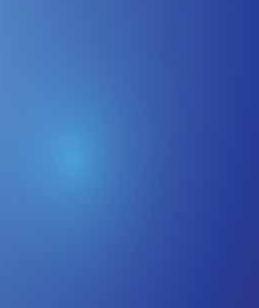

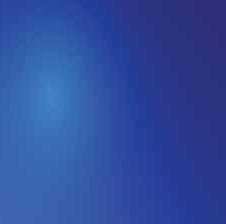
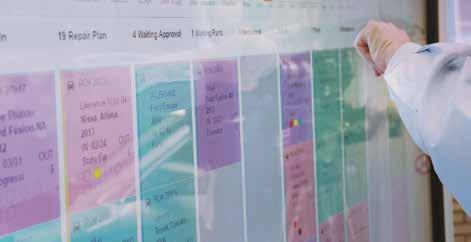
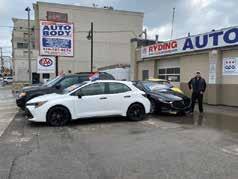
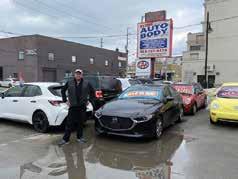