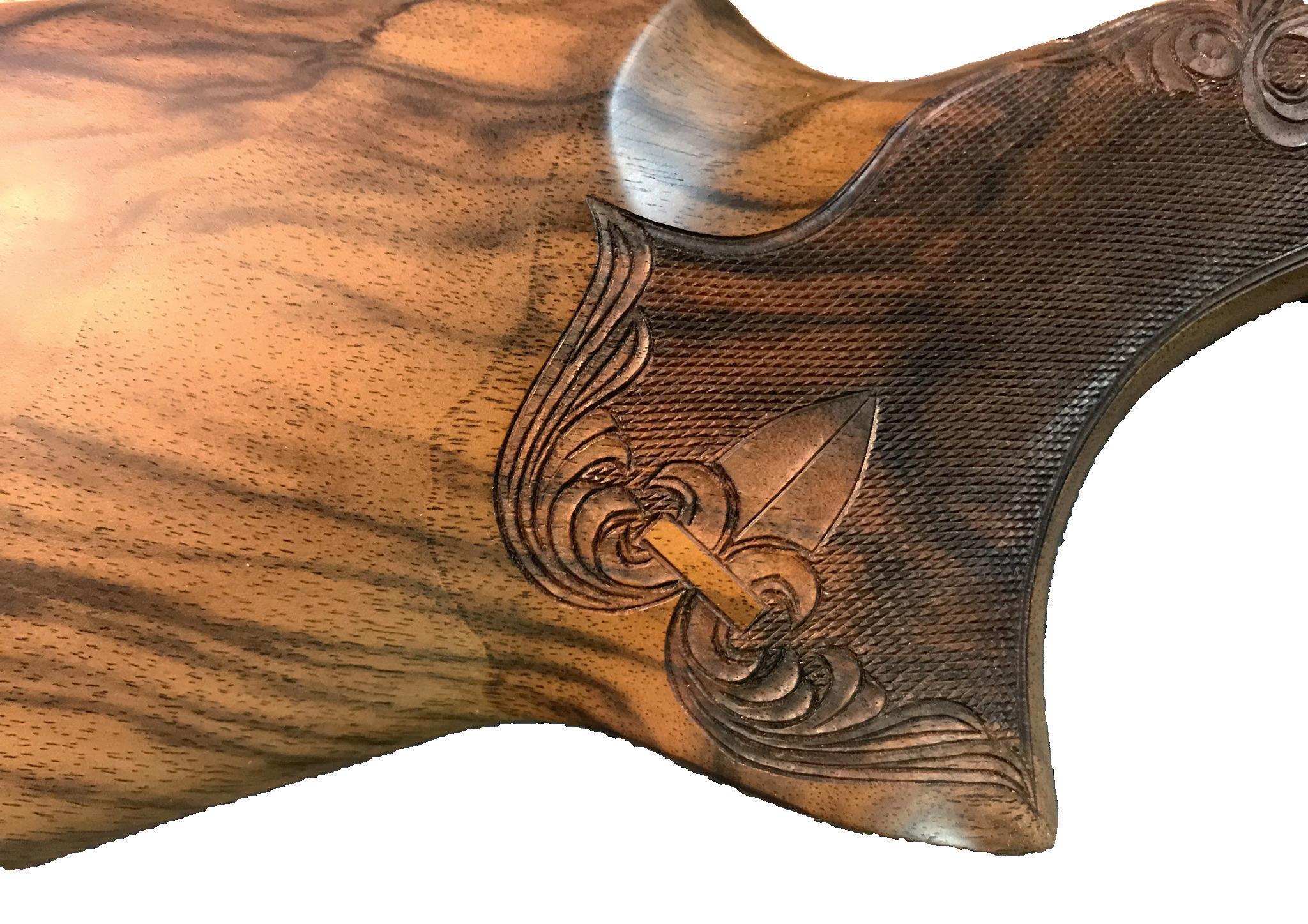
5 minute read
JOHN REESE ENGRAVING
CUSTOM STOCK CHECKERING, RESTORATION AND CUSTOMIZATION BY DANA FARRELL
The proverb: “Necessity is the mother of invention” came to mind, but with a different twist, when John Reese told me his life story. John didn’t invent something; he re-invented himself when a back injury forced him to leave the construction industry and find a new way to put food on the family table.
Advertisement
John was injured while building gas stations in Florida, when he found himself in need of a job. At the urging of his brother, he moved from sunny Florida to Polson, Montana, where local gunstock maker Bob James was looking for a stock checkerer. John, who had been an artist since his youth, jumped at the chance to learn a new skill that might eventually also serve as a creative outlet.
Early Days
Bob James showed John a few checkering basics—like laying out the master line. The rest he learned from instruction books. Despite having no prior experience, he learned quickly by checkering scrap wood eight hours a day, sanding it off, and repeating the process until he became proficient.
After just two weeks of intense practice James was ready to use him on some Brownings he was processing for their custom shop. Twenty to 30 Browning Superposed over/unders would arrive for stocking at a time. The checkering needed was “manufacturer grade” and wasn’t expected to be too exacting, according to John. This opportunity turned out to be the
perfect training ground for a budding checkerer with an artistic background.
After three months on the job John did his first fleur-de-lis pattern, and six months after first picking up the checkering tools, he did his first “stock engraving.”
I asked him why he calls this practice engraving, as opposed to carving like I’ve heard it referred to in the past.
John says he likens the intricate work he performs on stocks to metal engraving, in that it’s more two-dimensional than what usually comes to mind when he hears the term “carving.” In fact, at times he actually emulates the metal engraving on firearms he’s working on.
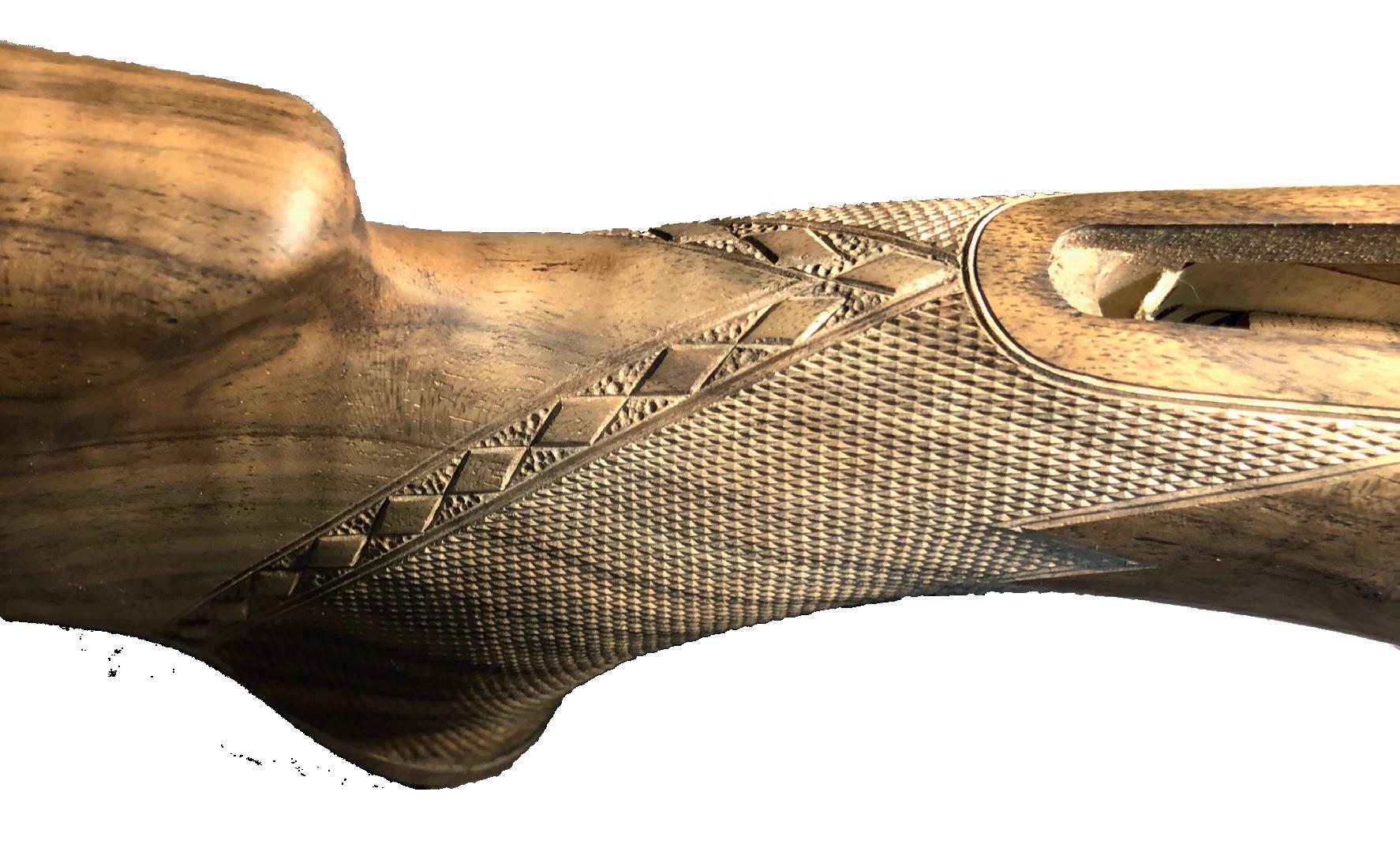
BEAUTIFULLY EXECUTED CHECKERING AND BORDER
Striking Out On His Own
His work with Bob James lasted around four years. Then in 2004 John struck out on his own. He paged through gun magazines for leads and started cold calling companies. He sent out CDs of his work. He started to get his name out there and the jobs began rolling in.
Much of John’s early work was retracing laser applied checkering on high end stocks. Laser engraving is great for mass production, but lasers cannot detect the subtle differences in oils and resins in the wood, often resulting in a melted or staggered look. This is where a skilled human touch is invaluable.
The 45 year old Reese admits to a love/hate relationship with wood. He loves the challenge of working with it because “every piece of wood is different and no matter how perfect you want it to be, sometimes the wood won’t let you have your way.” But, he “can’t get too crazy on certain pieces of wood” and has to back off, because the particular piece of wood just won’t allow it. This stifling of his creativity is where the hate comes in. Interestingly enough, it’s often the inexpensive guns that clients want more elaborate designs on. Common, working class folks bring him their production grade guns and want high-grade wood embellishments because the gun has sentimental value. John has checkered all different types of wood and even engraved a plastic Xbox controller—and “it came out awesome,” he told me.
Another important segment of John’s work is purely utilitarian. “Half of my work is just purely function—clients with hunting guns. When they call me, they’re not asking to make their gun look pretty, they’re saying they’ve lost the grip on their gun because it’s worn out. They don’t want to spend $300 on their $500 gun” he said.
Gun restoration is also a service John provides, which can include stock refinishing and re-checkering and/or stock engraving. He’s been entrusted to restore the finish and checkering on many guns over a century old, by several collectors—sometimes with the priceless metal still attached.
Twenty years ago, checkering as an art and occupation was beginning to die off due to the emergence of automated machinery. When John first started out, carbide blades for power checkering tools were readily available, but within a few years there was a three to six month wait for blades—or even to have power tools rebuilt. He attributes that to lack of demand, due to the practice of laser engraving. For a while he was “cutting with dull blades and his power tools were falling apart.” Luckily, that trend has now stabilized and there is plenty of hand engraving work coming in.
A large percentage of John’s customers find him by word of mouth, because people willing to send their gun to a stranger across the country “tend to want to know
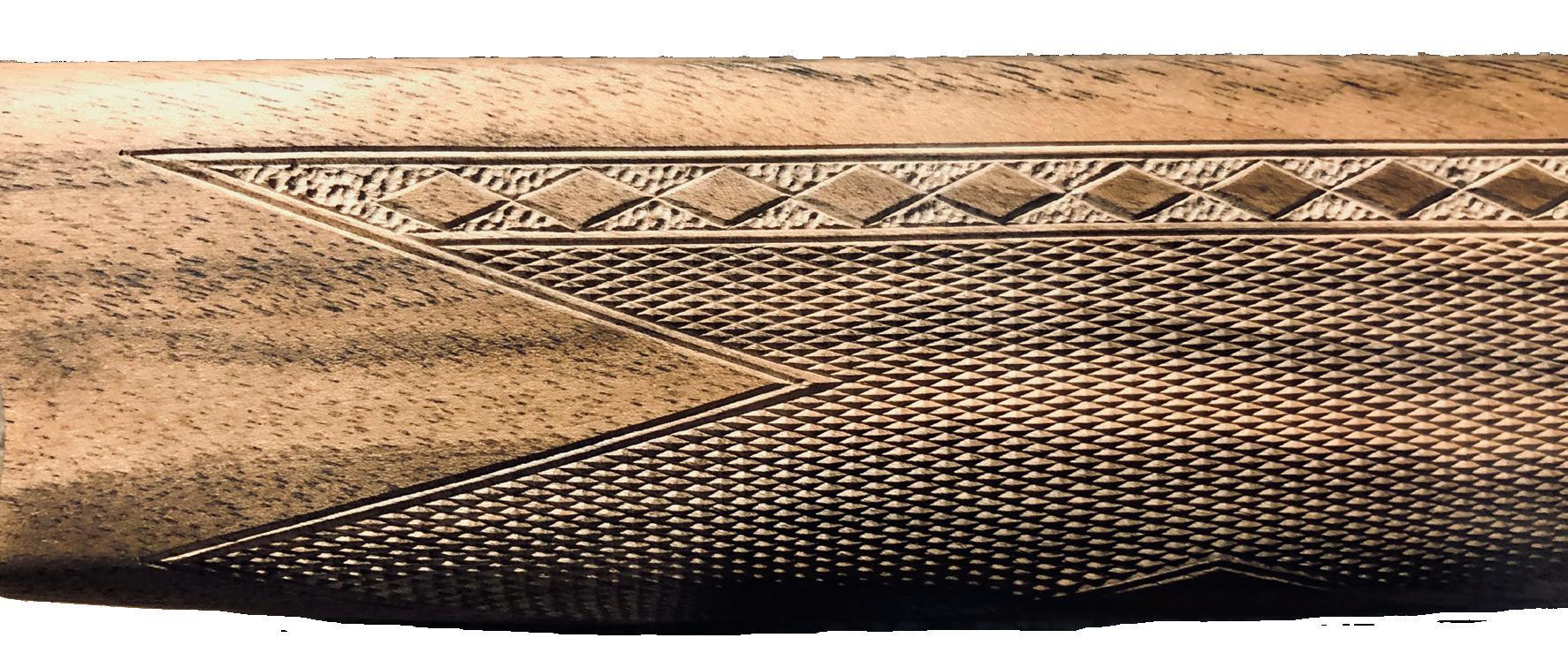
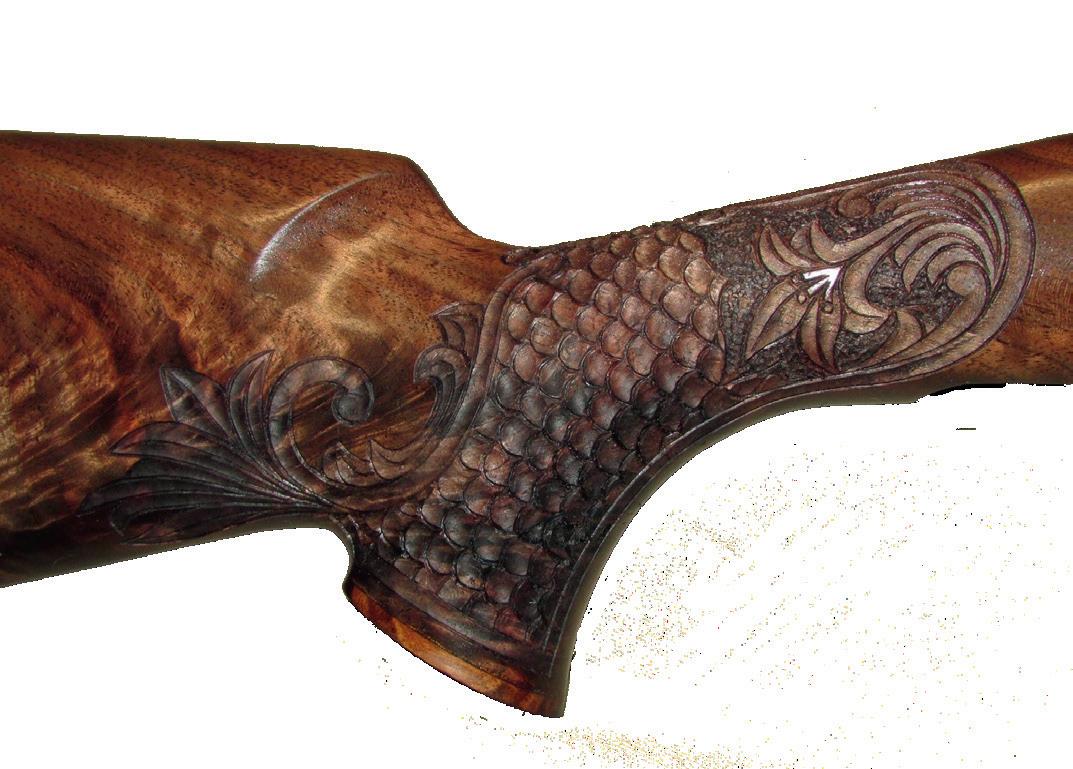


that someone they are acquainted with had a good experience.”
Unleashing His Creativity
What kind of job enthuses Reese the most? “The harder, the better” he says. He loves it when a customer wants to employ stock engraving in combination with checkering and enjoys the creative process of drawing up a unique pattern. Many customers referred by past clients have enough faith in his abilities to give him free creative reign—an artist’s dream. Those are the jobs he lives for. They might give him a few details of what style they like and let him build upon the idea from there. John has even engraved gamebirds on stocks and would like to do more game scenes.
He has plans to eventually take up metal engraving and build a one-of-a-kind custom gun, “front to back,” learning each aspect of the business as he goes. He’s excited at the thought of adding metal engraving to his talent portfolio and is confident he will be a quick study. Metal engraving, he feels, will more fully allow him to unlock his creativity potential.
In the meantime, you can check out John Reese Engraving (formally Custom Diamonds Engraving Inc.) at https://checkeringgunstocks.com n

