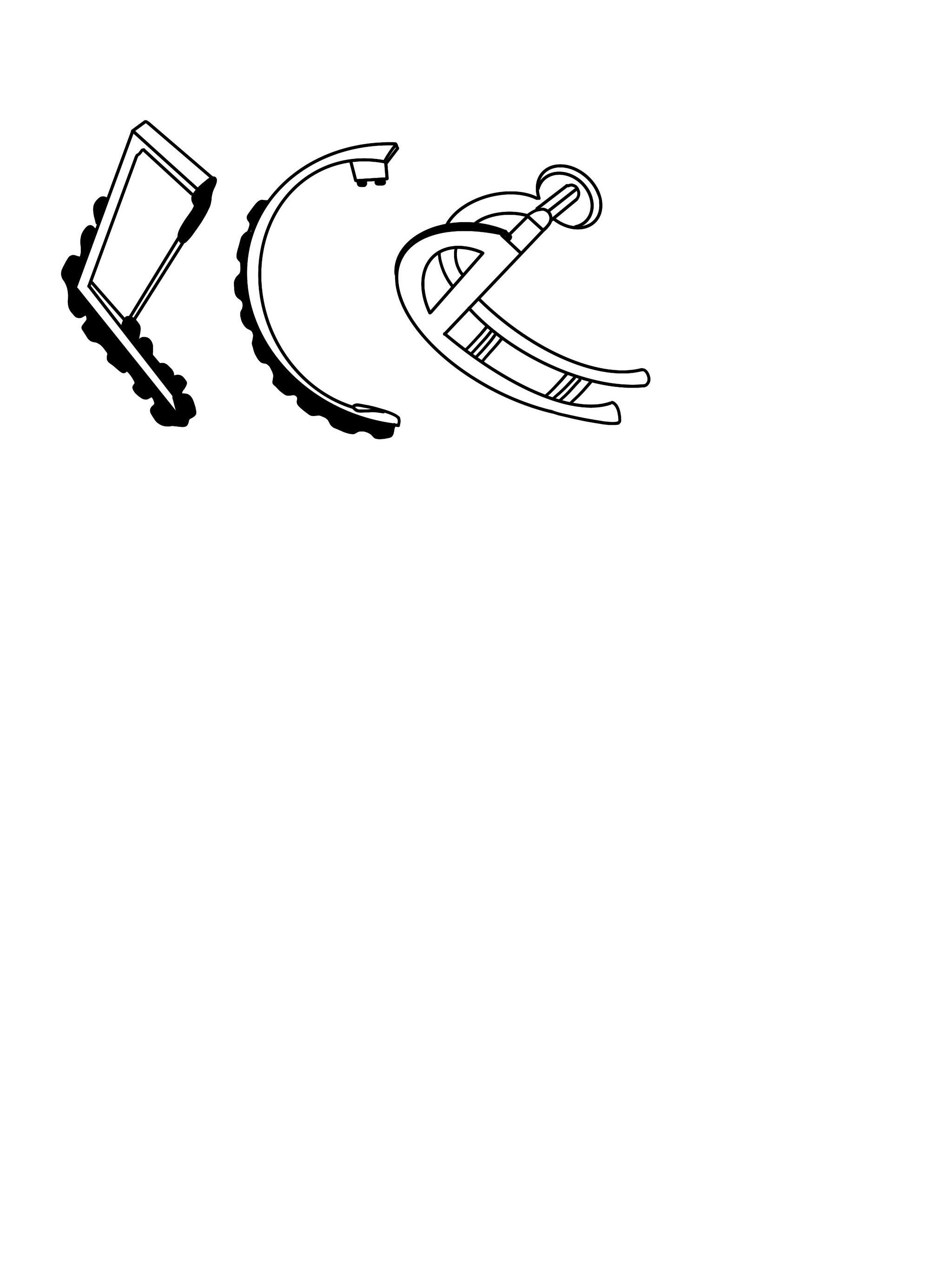
2 minute read
Iterative Design & Ideation Phase 02
from RHex Robot
Initial Ideation and Concept Sketching
Once the background research was acquired and initial inspiration and motivation was taken from both the biology and locomotion and insects and the original R-Hex designed at the University of Pennsylvania, ideation and concept sketching took place, in order to gain a clearer perspective of the desired outcome. The following diagram covers the different design phases and how the final R-Hex design was congregated.
Advertisement
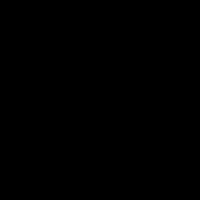
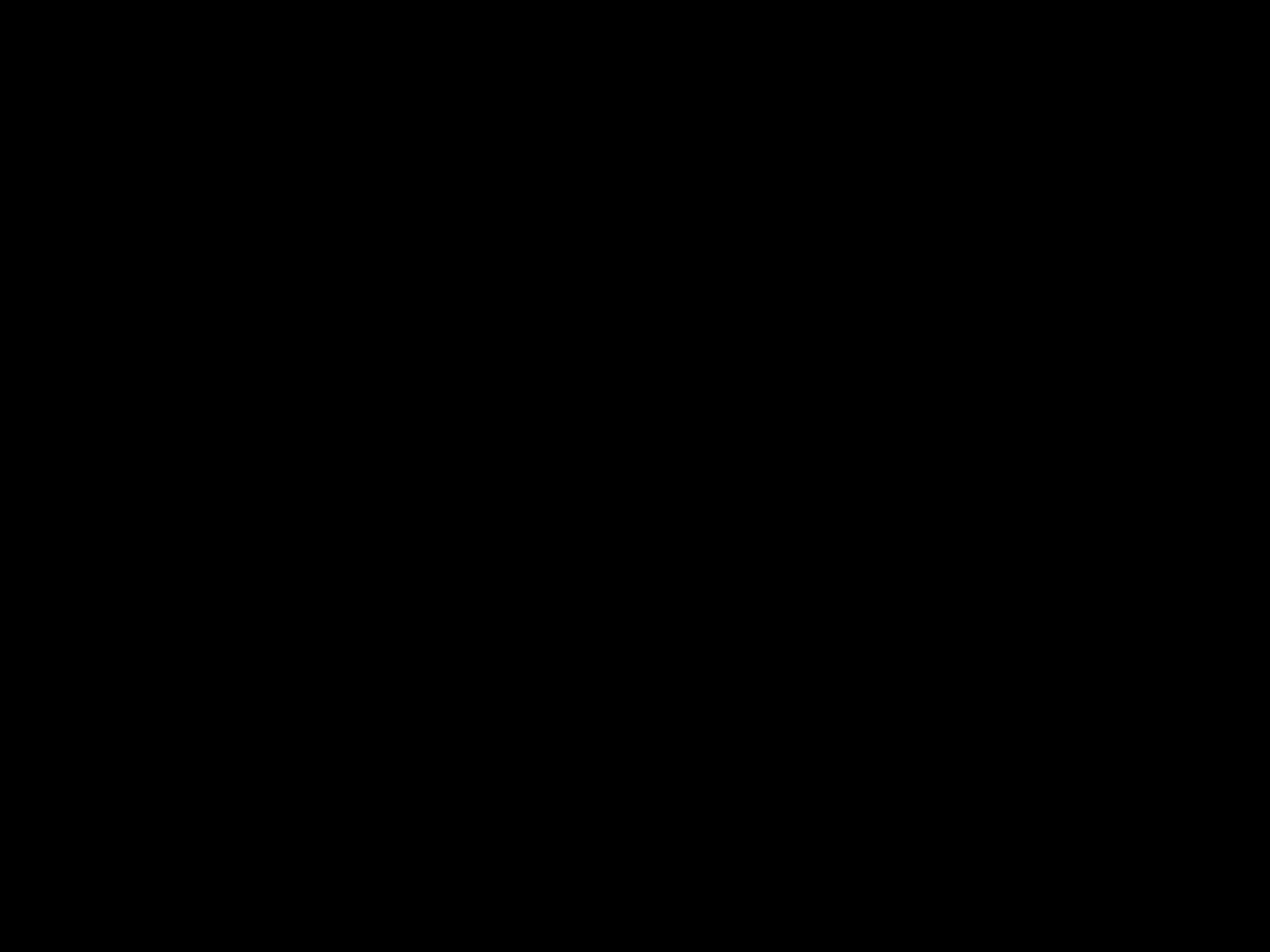
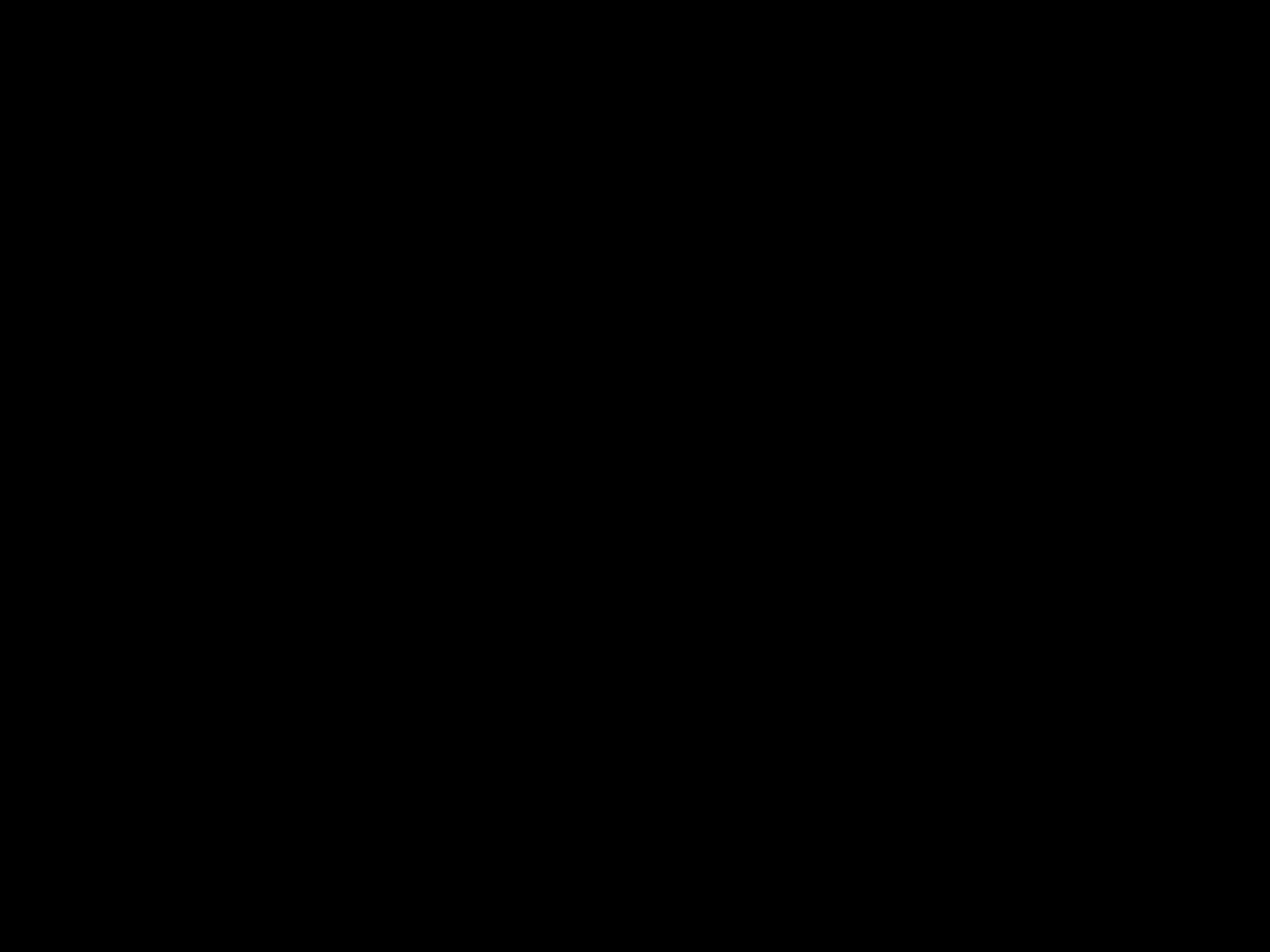
Background Research
Extensive research was conducted in order to develop an understanding on previously modelled R-Hex robots, which provided a foundation of knowledge to build upon. This information was then used to start iterative generation of possible outcomes of the
MARKET ANALYSIS & INSPIRATION
An analysis of pre-designed R-Hex robots was directed with the objective of finding areas of interest and inspiration and to potentially improve what was already offered on the market. Although the original R-Hex is bio-inspired, improvements to achieve a superior performance and durability of the robot
IDEATION & CONCEPT SKETCHING
The final stage of the ideation phase was concept sketching and iteration. Iterative sketching was essential when deciding what the form the chassis and legs would be. The sketches shown below are improvements inspired on pre-existing R-Hex models
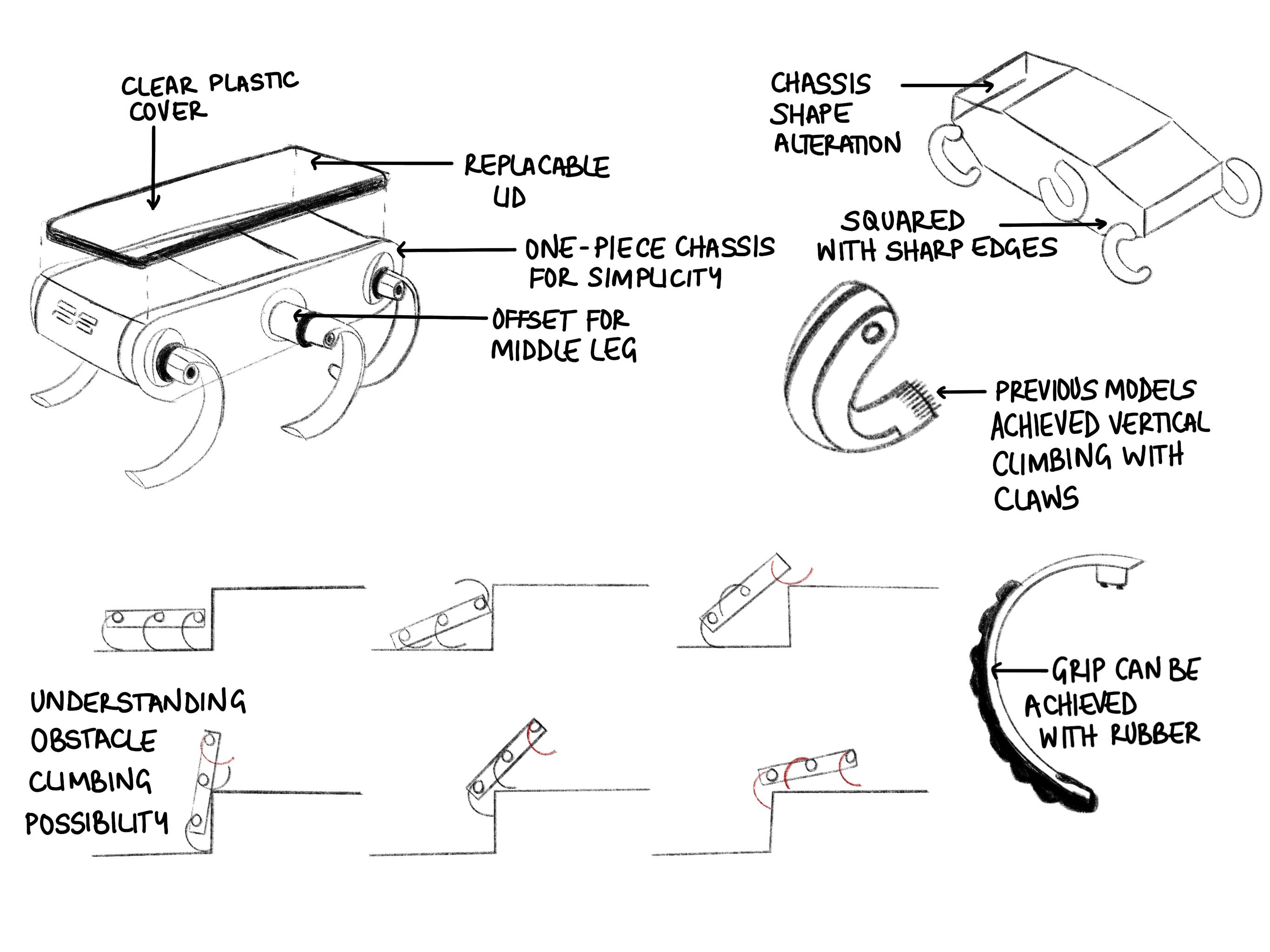
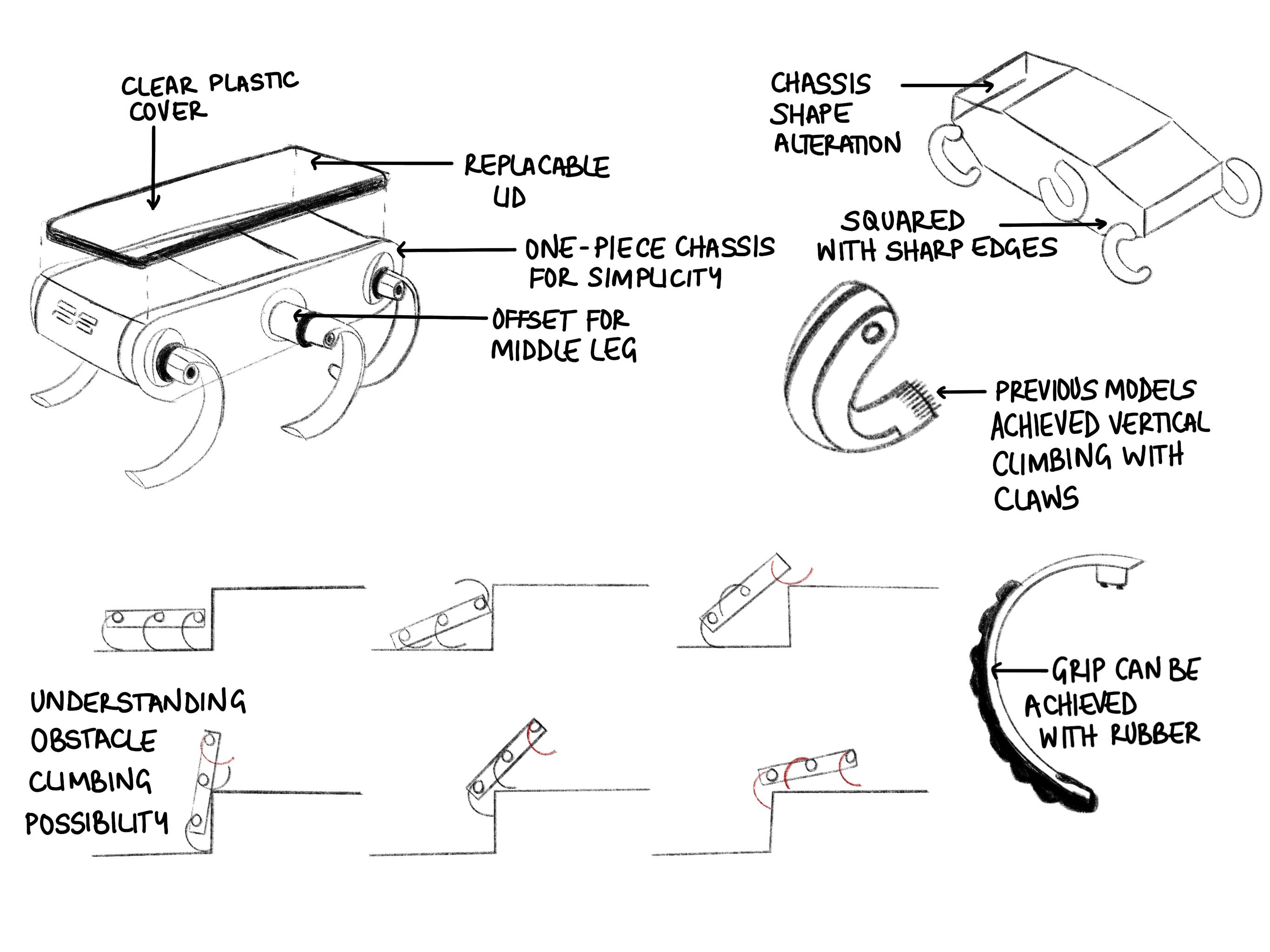
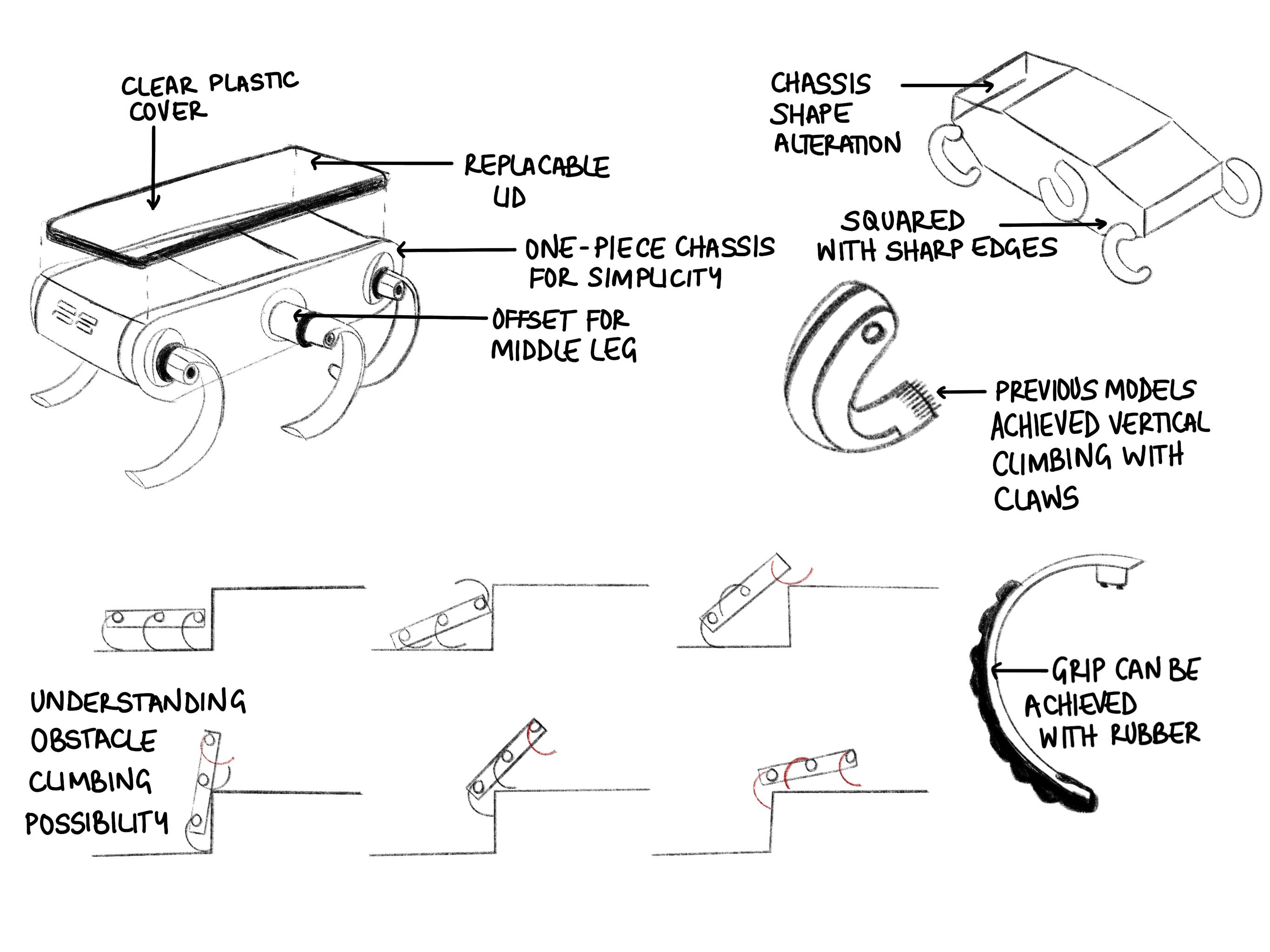
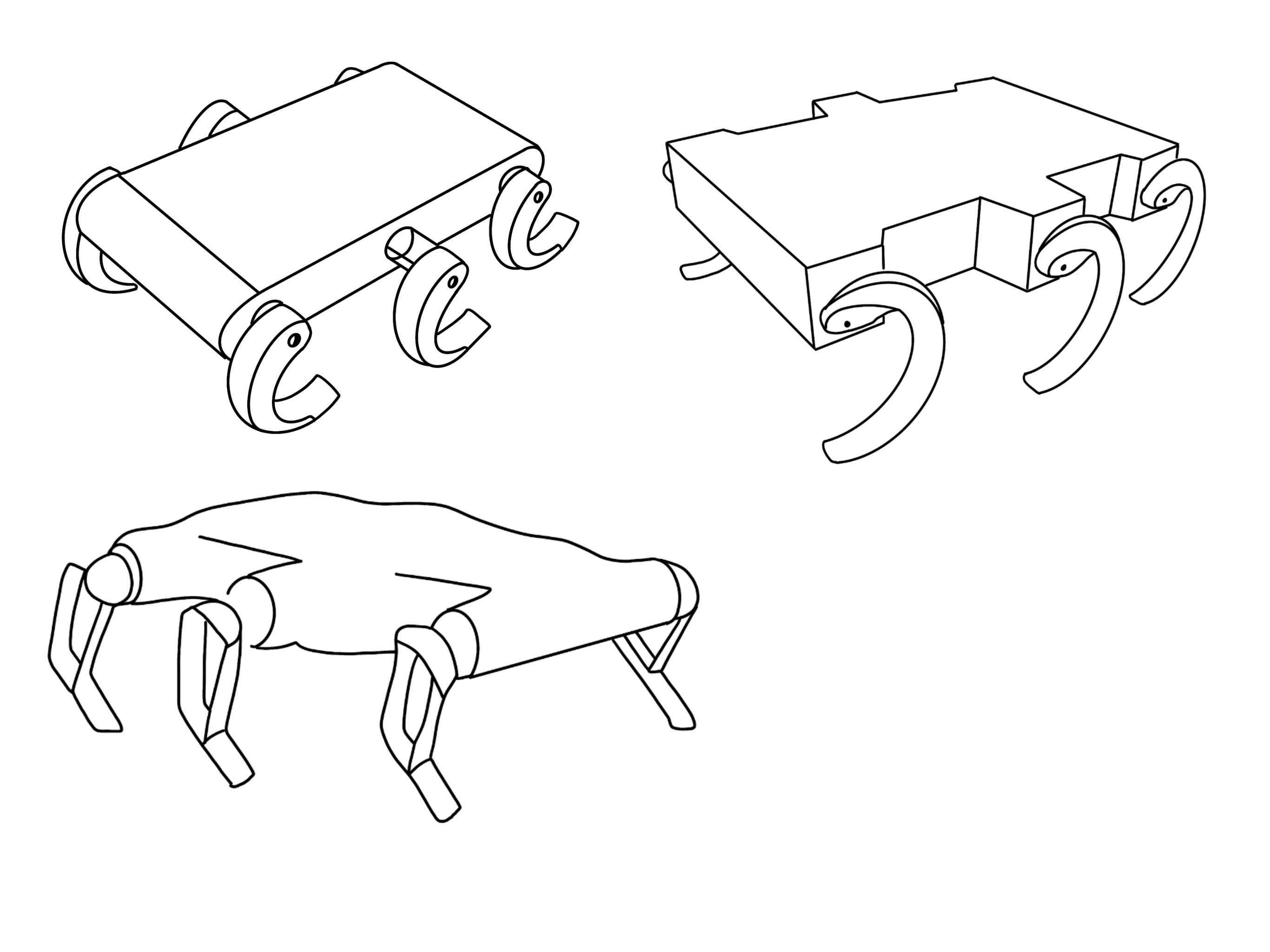
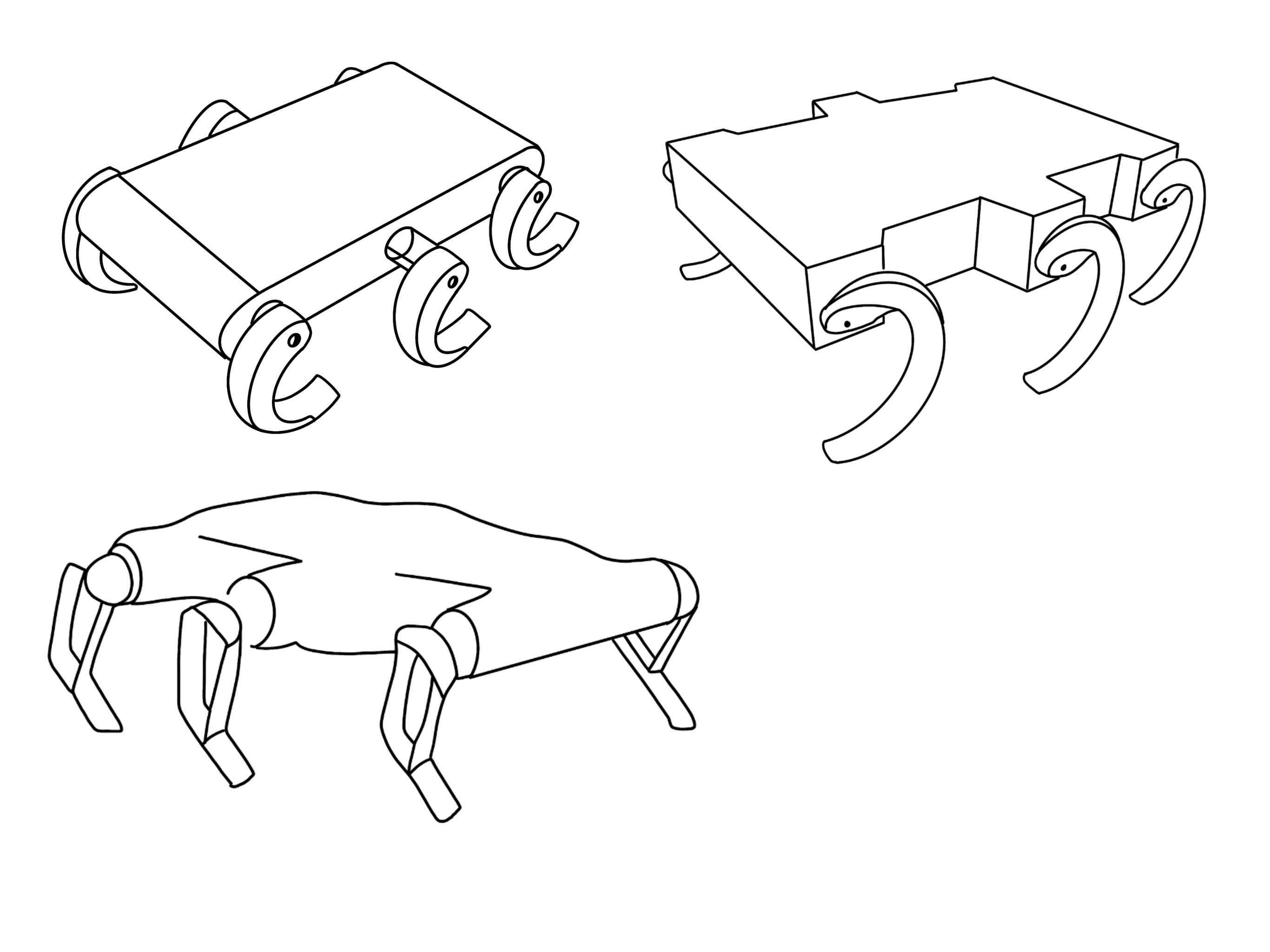
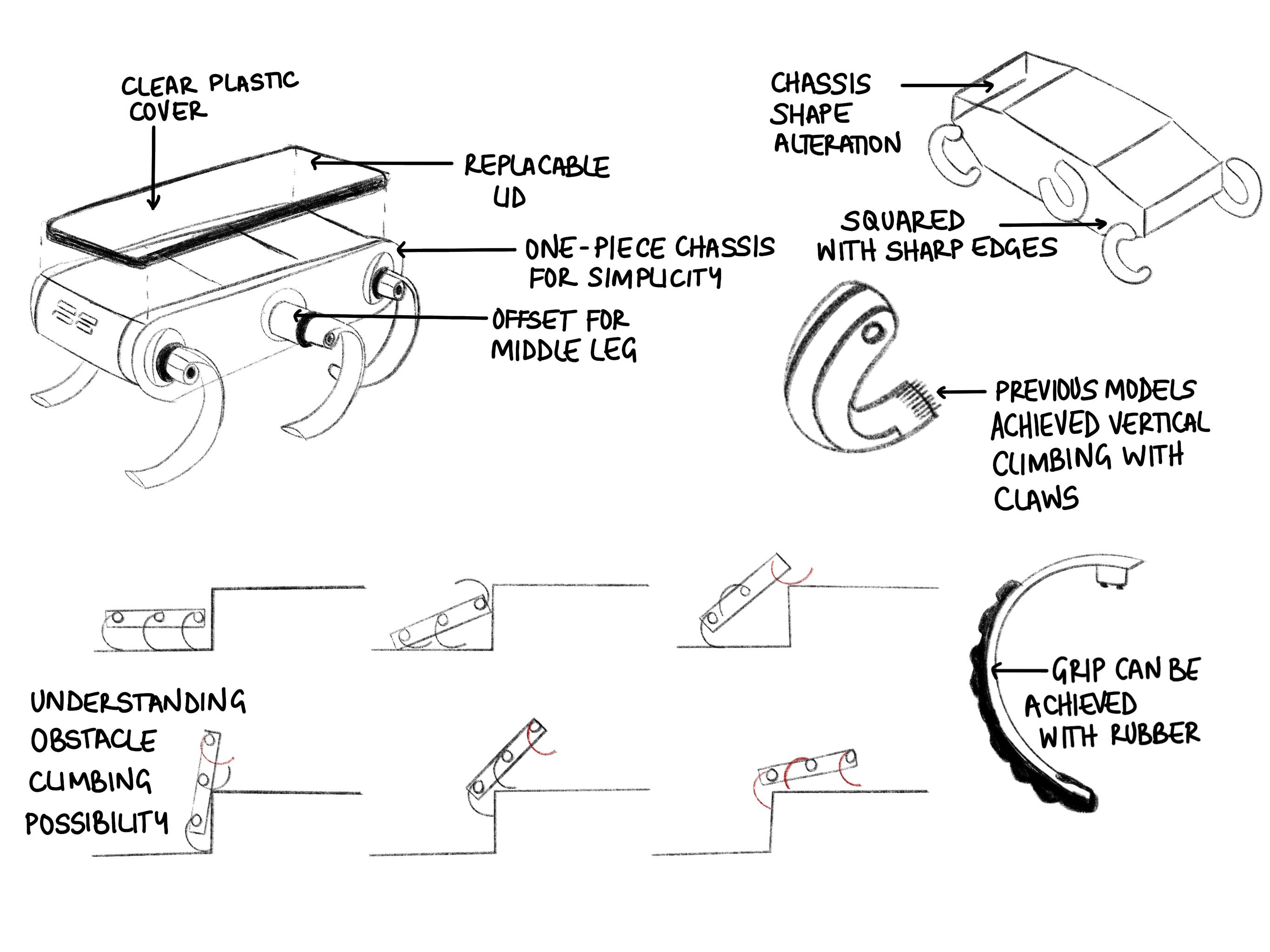
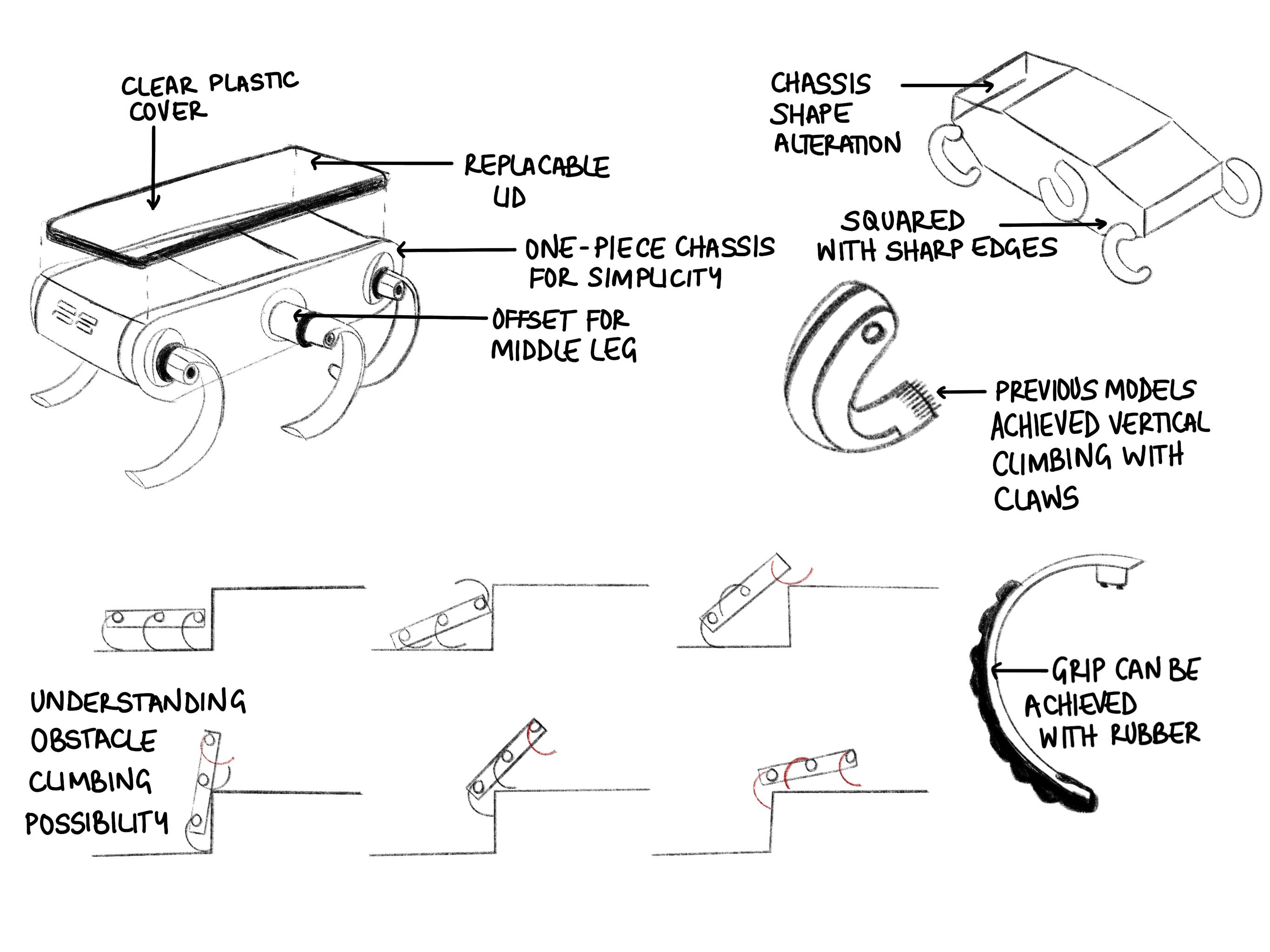
Mechanical Design 03
Leg and Body Design and other Design Specifications
The main objectives of the mechanical design were to improve the conventional robot’s frame durability, in terms of fatigue and achieving similar or superior performance to past robots. The overall dimensions of RHex were altered in order to achieve a mini version of the original model (54×39×13.9 cm) in order to achieve a smaller, more affordable version of the RHex.
Leg Design
The legs of the RHex are considered to be the most important component of the RHex Design6 and they must have high strength, flexibility and smooth motion ability. Although the robot’s legs have been designed in several ways, usually dependant on the overall structure design and application, the majority of RHex model’s are a cockroach-inspired, using six legs to traverse uneven terrain with a series of open-loop stable gaits. The way their legs are shaped is key to simplifying control architecture through mechanical intelligence, and have been proven across a wide array of unstructured terrains.

Subsequently, this version of RHex, maintains the original curved shape of the legs since they have proved to be characteristically flexible, deflecting under the robot’s weight when in contact with the floor. Small rubber bands were attached to the legs’ outer surfaces for extra grip. The following diagram show the shape and dimensions of one of the hexapod’s legs.
Body Design
There were design limitations that were considered before designing the chassis to fit in carried components such as motors, batteries and other robot controllers. In addition, stability considerations were made such that the centre of gravity of the body must be exactly centred in the RHex body. Furthermore, the body design had to be rigid with a low bodyweight (under 300g) and components had to be carefully mounted in order to prevent unexpected faults during functioning.
The chassis of the RHex was carefully designed in order to be inside the weight limit of 300g while being outstandingly resistant to impact and lightweight. The body dimensions were agreed to be 165×100×40 mm (excluding leg diameter) in order to make the robot compact and versatile, ideal for a wide range of applications, including navigation through tight spaces.
The selected material for the chassis of the robot was bent pieces of aluminium sheet metal. The bends in the lateral parts serve to stiffen the chassis, keeping it from flexing under applied load and allowing for thinner sheet metal to be used in order to reduce both weight and overall cost.