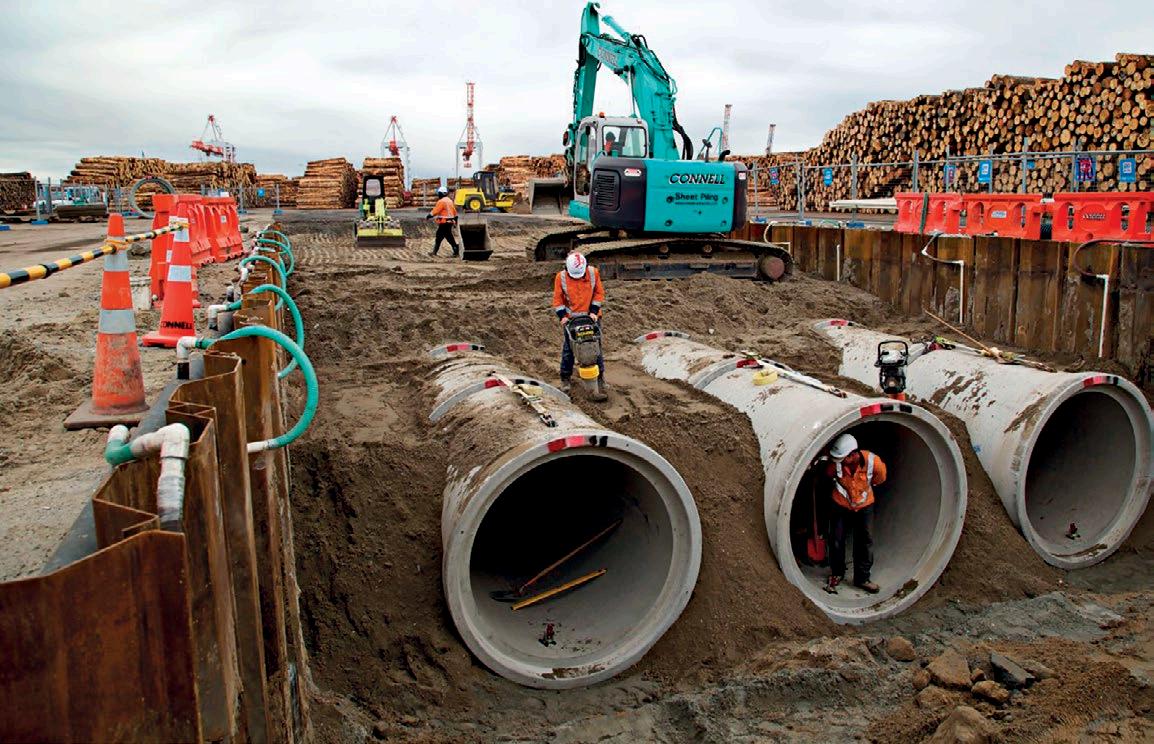
6 minute read
Connell Contractors
Stormwater artery
keeps industrial heart of Mount Maunganui beating
Advertisement
While stormwater systems perform a simple function, laying them can be far from easy. Connell Contractors knows this only too well – navigating everything from a four-lane highway to a penguin colony during its build in and around the Port of Tauranga.
CATEGORY 3
PROJECT: Stormwater Upgrade, Tauranga CONTRACTOR: Connell Contractors H amilton-based Connell Contractors was given the challenging task of putting together a 500-metre pipeline that would take stormwater from Mount Maunganui’s industrial area to Tauranga Harbour.
From the town’s shipping channel, the pipeline had to cross two sea walls, a log yard, rail tracks, heavily-trafficked port roads and a four-lane highway. A bevy of critical services also needed to be relocated, including 33 kilovolt power, water mains and fuel lines.
The $7.98 million project was undertaken between February and December 2014. Complex and risky, Connell Contractors was more than up to the job.
Heading up a formidable list of challenges was having to conduct operations in a busy and dangerous port environment; not to mention orchestrating a large number of consultants, subcontractors and suppliers. One of the trickier parts of the project happened at the harbour outfall.
Project manager Dave Connell says this was down to the “gravity pipe” having existing stormwater flows introduced as work progressed. Sheetpile walls were built to isolate this and other pipes from the high tide. Stormwater was then pumped over. The pumps struggled to handle rainfall at times, so pipe bulkheads were used to let the pumps catch up.
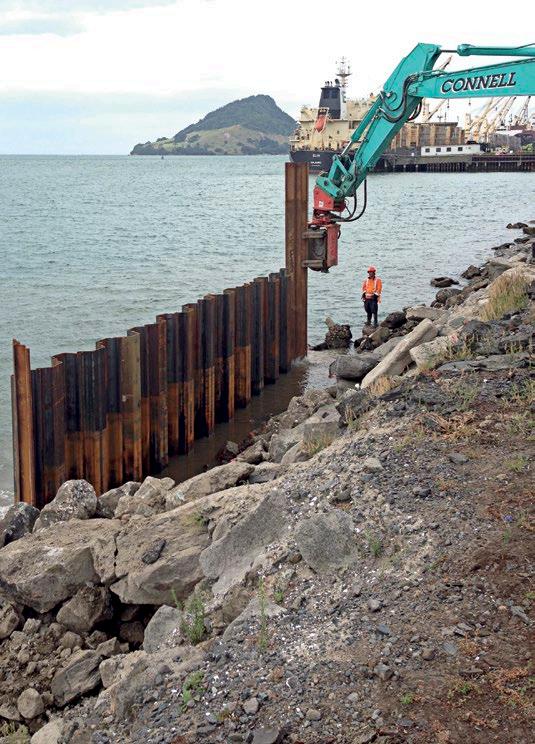

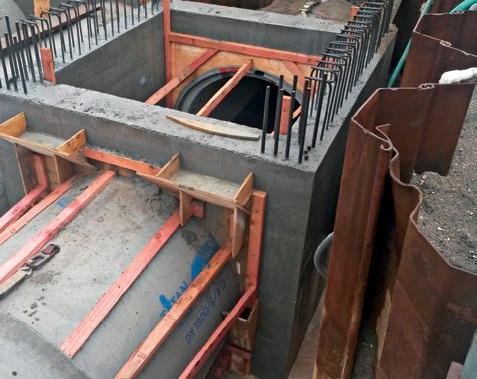
To limit contamination, pumped discharges entered the harbour through decant bins that kept solids in and liquids out. In one of many innovations, wellpoint tubes were used to deal with the presence of groundwater sitting two metres below surface level. These tubes were poked into the ground and pumps sucked out the offending water.
Sections of pipe were laid in depths of up to five metres. The 1.8 diameter sections were so colossal that it took a 10-tonne forklift to move them.
Crossing road and rail lines was a cinch thanks to a sophisticated method of tunnelling called pipe jacking. This was made possible with specialist assistance from directional drilling firm Smythes.
To channel existing fuel lines around the new stormwater pipes, the project team designed a special duct that was delivered in two sections and stitched together on site.
From day one, scrupulous conditions were placed around environment, dust and sediment control. Connell Contractors wisely adopted a risk management approach – best exemplified by the adage ‘an ounce of prevention is worth a pound of cure’.
“There was no room for error anywhere on site. A fuel spill or concrete wash would flow to the harbour with little time for containment and there was significant risk of contamination through a burst hydraulic hose or similar,” says Dave.
“Construction threw up all kinds of unforeseen problems including penguins nesting in the sea wall and discolouration of discharges due to high levels of tannins in the port stormwater.”
Mitigation saw pumps put behind secondary wall containment systems known as bunds. These quickly proved their worth when a pump set suffered an electrical fault and caught fire. The Fire Service turned up, using foam to put out the fire. Thanks to the bunds, all foam residue was contained.
At times, construction was hampered by heavy rain. In all, 300mm of rain fell. The works were under water several times.
“[To mitigate this] we placed temporary weirs in front of the pipes with drainage metal to prevent the ingress of sand when heavy rain was predicted,” says Dave.
“Staff were rostered to monitor the site in bad conditions. High winds especially from the west had the potential to move a significant amount of sand. However, our dust control system and well-maintained haul roads coped well.”
The proof in the pudding is that Connell Contractors never once fell foul of its strict environment and resource consent conditions.
Important to the success of the project was keeping stakeholders involved and updated, including road users and nearby residents. Dave says all requests were accommodated – including one from a blind person who lived two kilometres away but was disturbed by compactor vibrations.
The project developed “excellent relationships” with its iwi monitors and the general public were notified about operations through local radio, newspaper and electronic signboards.
The last word goes to a highly impressed client. Tauranga City Council’s Clark Butcher enthuses about the practical and productive way that Connell Contractors went about its job; also applauding its “constructive and confident” approach.
The fact that the job was done on time and well within budget was also sure to have gone down tremendously well! l
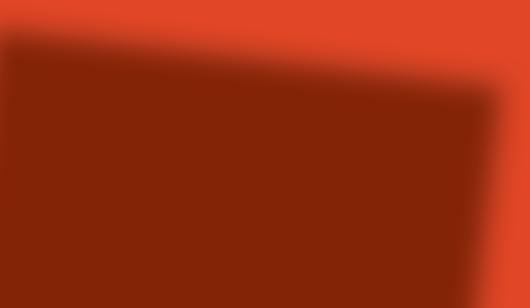

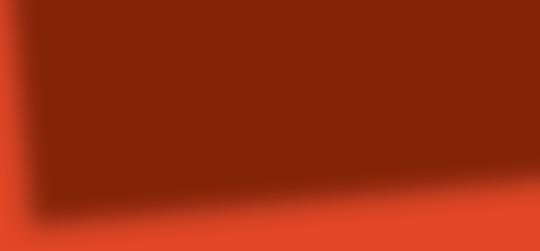

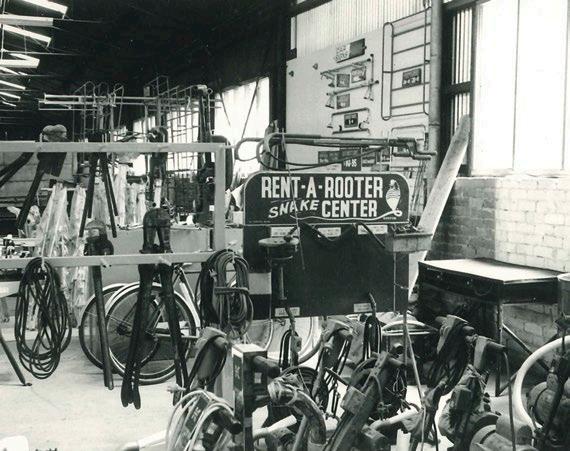
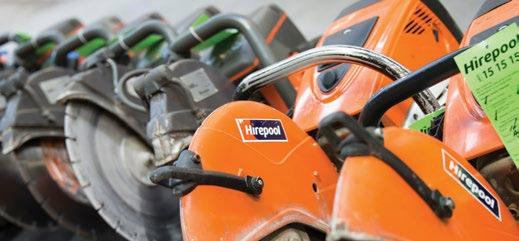
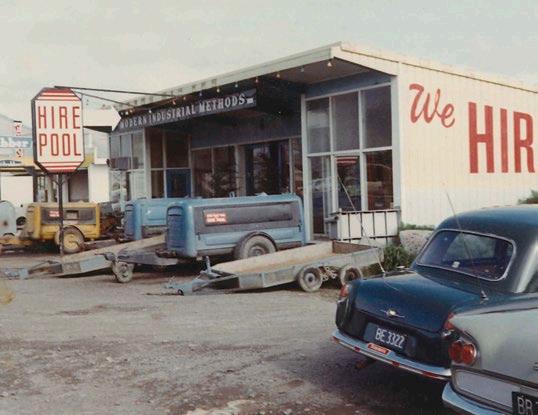

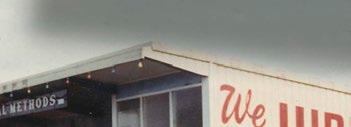
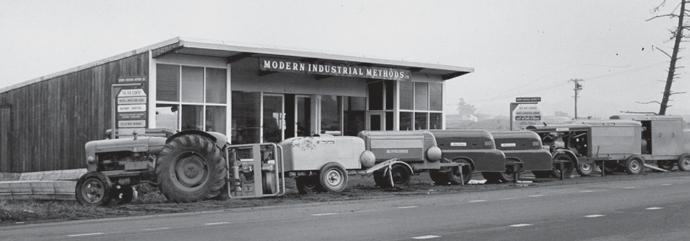
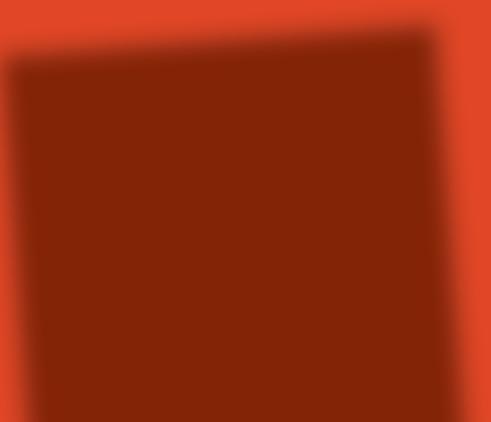


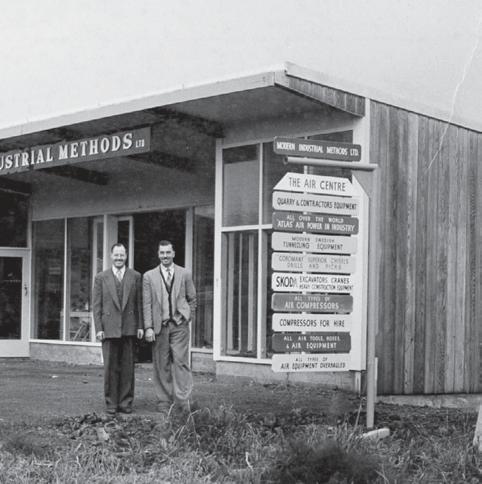
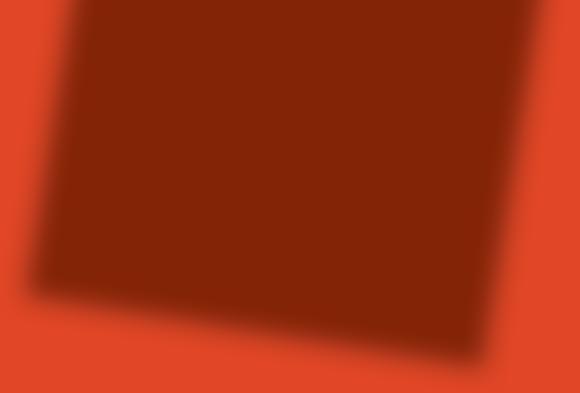
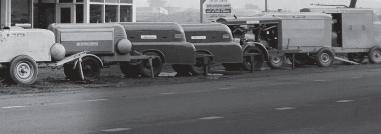
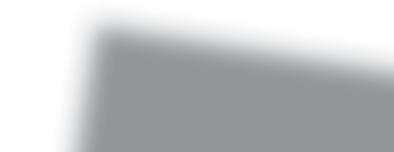


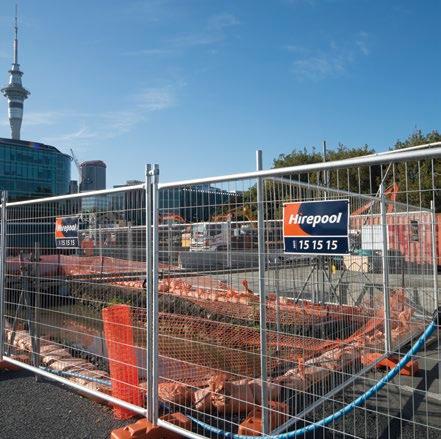
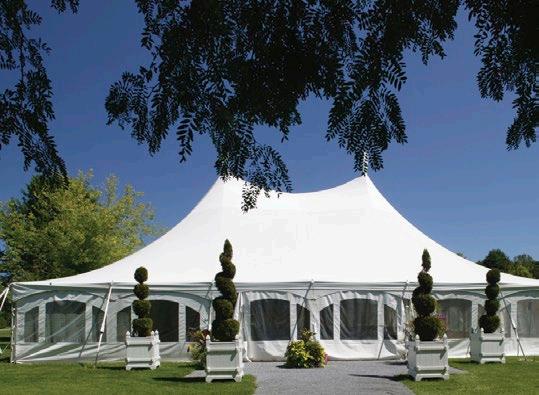

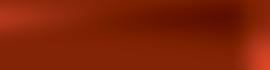


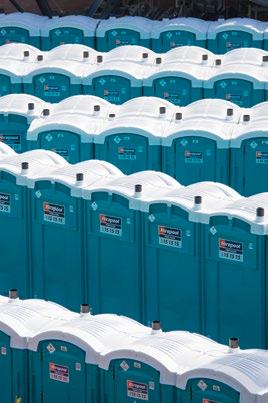
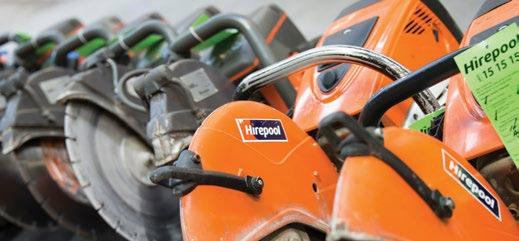

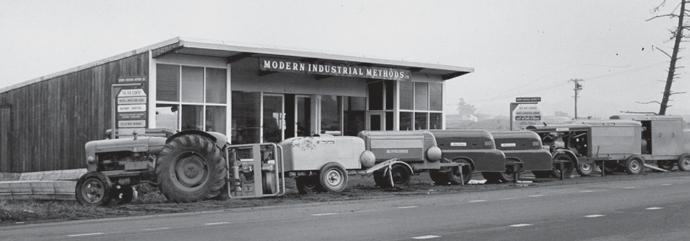

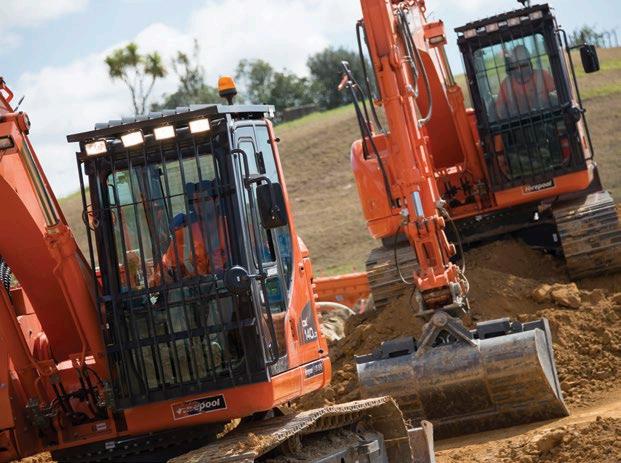
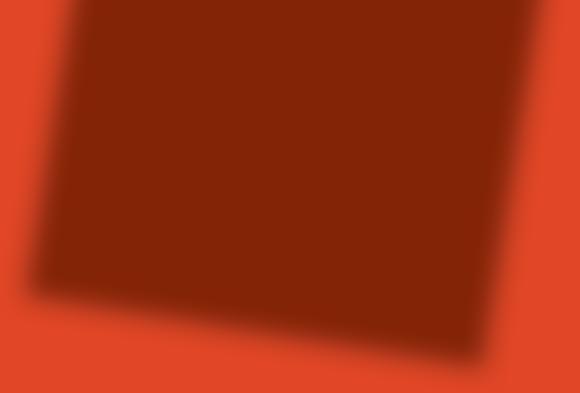
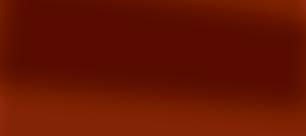
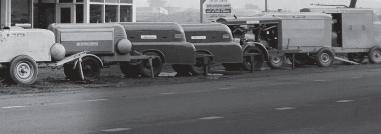
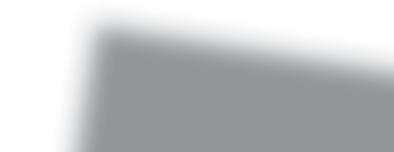
