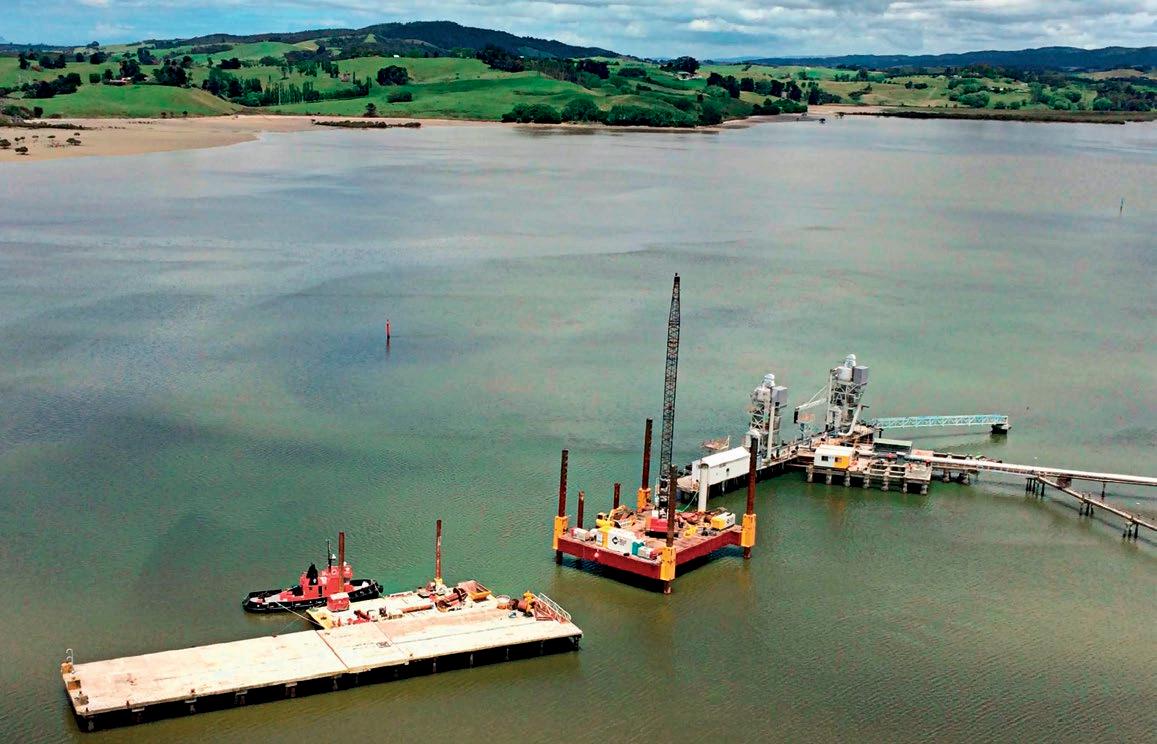
3 minute read
Brian Perry Civil
Concrete solutions
for concrete problems
Advertisement
One of Brian Perry Civil’s most recent projects – an upgrade of Golden Bay Cement’s Portland berthing facility – wouldn’t have been too difficult had it not been for one thing – the work site was 1.3 kilometres from land.
CATEGORY 3
PROJECT: Portland Berthing Facility, Northland CONTRACTOR: Brian Perry Civil F or onlookers, the crews regularly making their way to and from the Golden Bay Cement’s (GBC) Portland berthing facility might well have been preparing for a D-Day type invasion. After all, to get the job done, Brian Perry Civil (BPC) had to employ planes, trains and barges.
In spite of these sizable logistic difficulties this major build – which included the installation of several piles during a shutdown in early January – went off without too many hitches. And, unlike D-Day, there were no casualties involved.
In fact, of the close to 12,000 man hours BPC itself clocked on the job, when all was said and done not a single accident needed to be recorded with WorkSafe.
BPC project manager Luke Clark explains that shutdown windows needed to be planned meticulously so that the construction did not impact on everyday loading activities at the facility.
Fortunately robust upfront planning, strong experience and hard work offset all the potential risks of a delayed project.
The project was successfully completed in April 2015. To meet this timeframe, Luke says that the material had to be helicoptered to the site, barged (five kilometres from Whangarei) and trained (with an 800 kilogram limit) to the site.
“Material then had to be installed by the team on the Jack Up Barge. A key driver for the project was the 17-day window
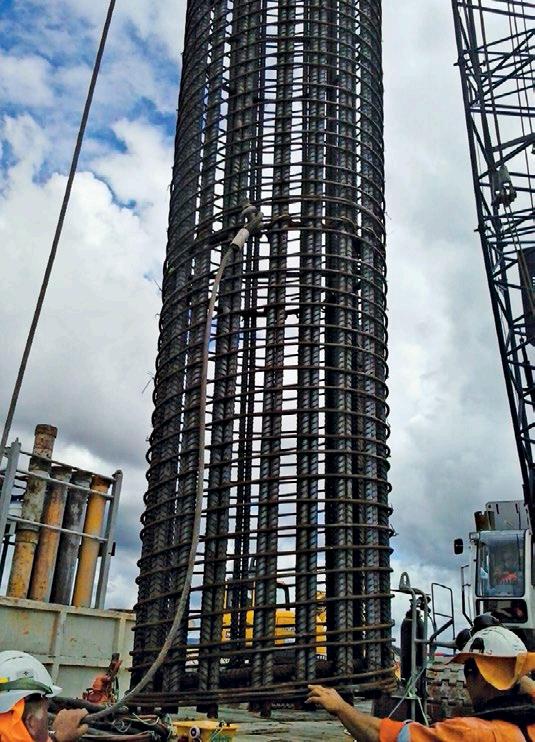
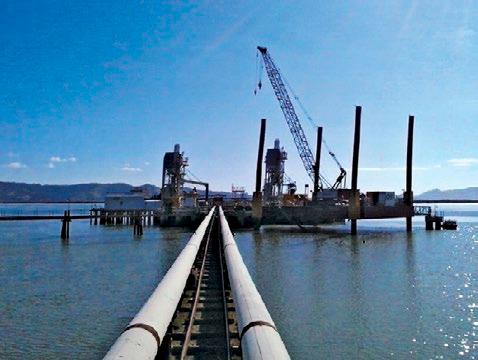
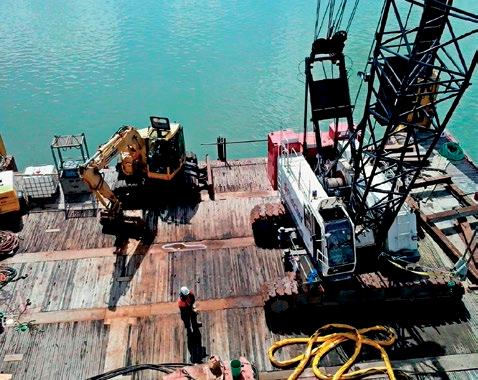
where the ship was in dry dock in early January,” Luke says.
“During this time the team pulled out all the stops to ensure the critical new piles and fenders were installed for the ship’s return.
“In this period we had to complete the three critical casing installations, cages and concrete in the bottom plug, scaffold the face, weld fender cleats and spool brackets on, attach fenders, shift barges and all other equipment out of the way.”
A good incentive to get all this completed in the required timeframe was the implications of not doing so – which, among other things, would have stopped 30,000 tonnes of cement leaving the port each month. As you might expect, that would not have made the client happy.
“If we did not achieve this we would have had to move and then work around the ship and barge movements [their schedules change daily]. This would have involved setting up temporary fender lines [extra piles] and a huge delay to the programme,” Clark says.
“If we delayed the ship or barge there would be huge consequences not only for the project but for GBC supply North Island-wide, as they cannot keep up with demand by road and the cement stocks would have run out.”
Apart from the narrow time constraints, the team experienced other logistical issues too. In fact, at one point the casings were delayed. They were supposed to arrive on November 24 and the shipments had to be split into three 11.8 metre lengths.
However, due to unforeseen circumstances, the majority didn’t turn up until December 18. It then required four to five days to paint and splice the 23.8-metre casings. Given their size and weight only one could be completed at a time, which added undue pressure on the work programme.
Luke credits his team and all contractors involved for getting the job done efficiently and without drama. Careful planning, vast technical know-how and hard work no doubt also played a role.
Now that the job is complete, BPC’s main client is also singing the contractor’s praises.
General manager of GBC Ian Jones says: “The project has been a resounding success against all of its objectives. From a safety and environmental perspective, all staff were kept safe and environmental stakeholders were impressed with the delivery.
“From a programme perspective the works were delivered on time and the important three week shut-down window was achieved. From a budgetary perspective the BPC effort has bettered the budget and resulted in a cost saving for the collective team.”
A testimony that even D-Day leader Eisenhower would have been proud of. l