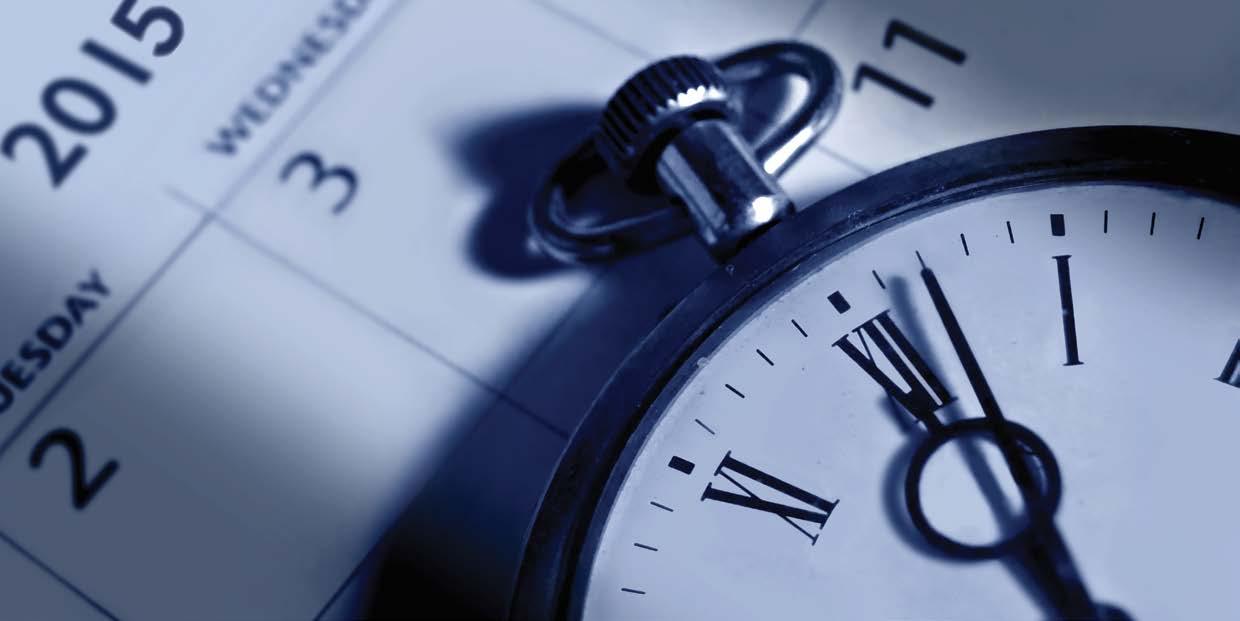
8 minute read
Construction schedules
DEVELOPMENT, DELAY ANALYSIS & BEST PRACTICES
BASELINE SCHEDULE In preparing a bid, the Contractor estimates the resources (labour, materials, equipment and supervision/ management) necessary to meet the requirements set out in a Request for Proposal (RFP) which details the scope of work to be delivered and the timelines in terms of a schedule. Following award of a contract to the successful Contractor, the detail to which schedule requirements are set out in the contract documents often depend on the approach adopted by the Owner and can vary from a detailed schedule of work to start and end date expectations.
It is anticipated that the Contractor will come up with a schedule that is logical, practical and achievable. By way of example, GC3.5 (Construction Schedule) of CCDC2 – 2008 Stipulated Price Contract requires that the Contractor submit a detailed schedule within a prescribed timeframe and states that the Contractor shall (emphasis added):
“…prepare and submit to the Owner and the Consultant prior to the first application for payment, a construction schedule that indicates the timing of the major activities of the Work and provides sufficient detail of the critical events and their inter-relationship to demonstrate the Work will be performed in conformity with the Contract Time;”
and
“…monitor the progress of the Work relative to the construction schedule and update the schedule on a monthly basis or as stipulated by the Contract Documents;” and
“…advise the Consultant of any revisions required to the schedule as the result of extensions of the Contract Time as provided in Part 6 of the General Conditions - CHANGES IN THE WORK.”
Upon review and approval by the Owner, the submitted schedule becomes the construction schedule or baseline schedule. Again the level of review scrutiny these schedules undergo varies upon the approach taken by the Owner with some taking a deep look into the intended delivery sequence, timing and methodology.
SCHEDULE DEVELOPMENT In developing the schedule and complying with the contract documents, a Contractor is often required to achieve specific expectations which set out the use of proprietary industry standard software and methodology based on utilizing Critical Path Methodology for scheduling a set of tasks that 1) lists all the activities required to complete the project, 2) establishes the duration of each activity, 3) determines the start and end dates of each activity, 4) recognizes the dependencies between activities, and 5) shows the critical path leading to the completion date.
SCHEDULE CHANGES The baseline schedule is then used to measure and report performance as the project proceeds, including identifying any delays or improvement opportunities to the contracted dates. Therefore, the accuracy of the baseline schedule is not only critical to the Contractor who has to plan resources but also the Owner who has an expectation in terms of the achievement of completion dates.
Notwithstanding schedule reporting which may identify changes to the baseline schedule, Owners sometimes remote themselves from the schedule as they expect the Contractor to be responsible for the ‘means and methods’ and Owners do not wish or perceive to be interfering in the schedule which is deemed to be in the Contractor’s custody.
In contrast, Contractors continue to report progress and identify items that are delayed and that may lead them to a remedy under the contract i.e. extension of time and relief from liquidated damages, if they apply. In parallel, the Owner is interested in self-induced Contractor delays and delays that the Owner is not responsible for.
The reality is that whilst there is debate about what happened and who is responsible i.e. are the delays down to the Owner, Contractor or shared, the project continues to suffer and an adverse environment sets in as time is money for not only the Owner and Contractor but also others such as Consultants, Sub Contractors who become embroiled in allegations and counter allegations.
PROJECT RECORDS As with having a solid baseline schedule and reporting mechanism in place, having a solid record keeping system is also vital for establishing what happened. Fundamentally, there needs to be a way to measure changes in the schedule and project records are a way to assess such changes in parallel with a regularly updated schedule that captures delays.
Records need to be quantitative in nature in order to assess what the actual delay is, along with its potential impact, and should be regularly updated and maintained. As with a schedule, the records should be shared with the project team such that they become contemporaneous information and far more persuasive, if required, in dispute resolution proceedings.
Finally, project records should meet the requirements of the contract, in terms of format, content or validation. Specific dates described in the contract should be kept in mind, with all activities monitored with regard to those dates. Further, detailed labour and procurement records should also be maintained.
ANALYSIS OF DELAY There are a number of methods used to analyse delay and the applicability of each depends on the particular circumstance including the complexity of the delay, outcome objectives and remedies under the contract. Sometimes the term Forensic Delay Analysis (FDA) is used to define the analysis of delays to the schedule. Recognizing that each method can justify a paper in its own right, the main FDA methods can be briefly summarized as follows:
1. As-built vs. As-planned
This method takes a project’s as built information and compares it with the as planned information in order to check for variances. It is an effective method if a good (logic linked) base schedule is instituted from the very start of the project. Generally, this method is best suited to simple assessments where there is no question on who is liable for the delay.
2. Collapsed As-built
This method adopts a factuallybased approach to establish cause and effect and can be used when there is no planned schedule and is used retrospectively. If a Contractor has no planned schedule in place, at the end of the project an as-built schedule can be reconstructed by using detailed as-built information. This method can take account of any concurrent delays.
3. Impacted As-planned
This method is typically used if a
Contractor has good base schedule that is network linked and accurately reflects logic. This method starts with a baseline schedule and inputs delays or extension of time events into the schedule which then shows the impact on the completion date. Whilst this method can be used both retrospectively and prospectively it does not account for the actual as-built situation.
4. Time Impact Analysis
This method requires there to be a good base schedule clearly detailing the critical path which is updated regularly in conjunction with reliable and up to date project records. This method is useful to establish the delays that were not the fault of the
Contractor (excusable delays). In this approach, it is vital that any delay is recorded before any mitigation.
It is both retrospectively and prospectively applicable. However, time impact analysis it can be complicated and difficult to follow all delays and difficult to communicate.
BEST PRACTICES There is a heightened level of scrutiny of construction schedules, particularly as high profile projects continue to suffer extensive delays that are translating into substantial budget challenges. This is making it necessary to ensure that the schedule is just not considered as another part of the contract documents but also a logical, workable and dynamic decision making tool. Therefore, there are a number of best practices that should be considered: 1. The schedule should use industry recognized software and be a workable management tool that attracts a high degree of trust in order to satisfy the legitimacy and accuracy of its outputs. 2. The schedule should describe the work, display logical links between work activities and define the critical path. Additionally, it should state the start and finish dates of each work activity and access dates for each phase or section. 3. Seasonal shutdowns should be shown.
For example, a delay at the start of a project may delay the commencement of activities by pushing the actual start date into the winter shutdown period, precipitating a further delay. 4. Dates for off-site activities, such as those for delivery, design and procurement should be identified. The schedule should also have provisions for floats or time risk allowances to for items which the Contractor is deemed to have considered. 5. Integrating cost analysis into a schedule provides greater control in tracking costs already or potentially incurred throughout the time period of the project. By cost coding the schedule, work packages are able to be filtered allowing for more detailed analysis. 6. In the event that a schedule analysis is necessary and in advance of carrying out such an analysis, there should be a good understanding of the integrity of the baseline schedule (if there is one) and the outcome objective of the schedule analysis exercise. 7. A detailed schedule analysis for the purpose of arbitration or litigation may take a different form to a detailed schedule analysis submitted for the purpose of illustration which is aimed at a negotiated settlement. Finally, the data from the baseline schedule and any schedule updates should be shared with the project team to ensure that these become part of the contemporary project records. Recognizing that each project has different schedule expectations, the construction schedule is a key component of project delivery and project participants should make themselves familiar with this document.
About the author: Arif Ghaffur, B.Sc (Hons.), PQS, FRICS, MCIArb, is the Founder and President of Lakeland Consulting Inc providing Commercial Management Services with a focus on Business Improvement, Contracts Management and Dispute Resolution Services.