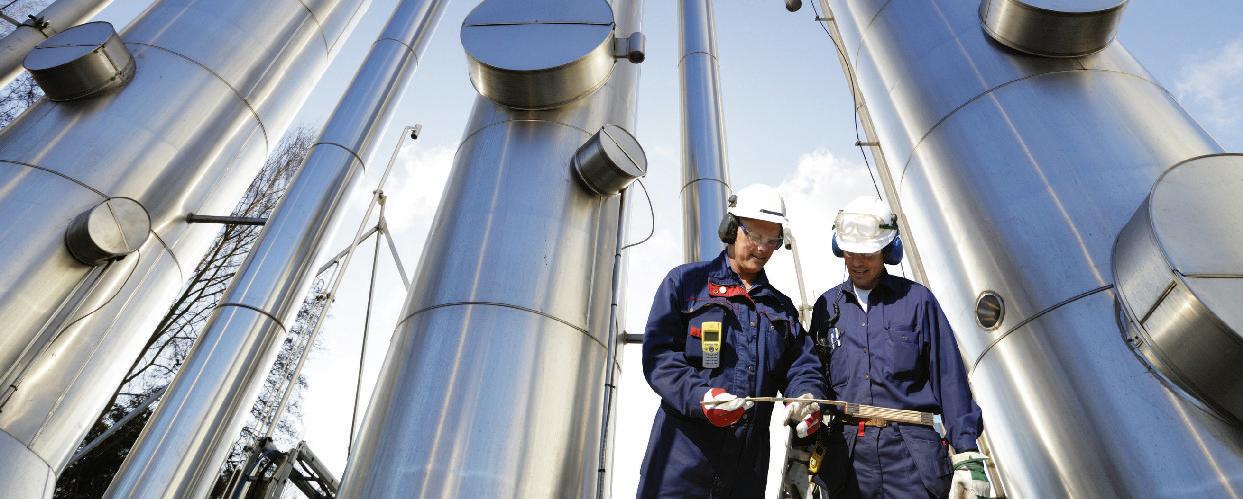
11 minute read
SAFEGUARDING SOCIETY – THE RESPONSIBLE CARE WAY
RAJEEV MARWAH Team Leader – Responsible Care Audit, ICC
As India entered the Phase 3.0 lockdown and began preparing for Unlock 1.0, a series of shocking incidents happened in the Indian Chemical Industry. These incidents once again tarnished the image of the Indian Chemical Industry which already has a poor safety record. Several cities in India fall under the highly polluted and critical areas.
Advertisement
It may be recalled that in 1984, as an aftermath of the Bhopal incident of Union Carbide, the legislative environment governing the Chemical Industry underwent a sea change. This transformation was across the globe, as each country effected and implemented strict laws.
As a result, one such response, termed the Responsible Care (RC) Initiative took birth in Canada in 1985 and was adopted in the United States in 1988. Responsible Care® is a voluntary commitment by the global chemical industry to drive continuous improvement and achieve excellence in environmental, health and safety and security performance. ICCA (International Council of Chemical Associations) is an international body which driver the RC program globally, and has so far, been adopted by over 65 countries. Responsible Care requires member companies to certify to their Environmental, Health, Safety and Security (EHS&S) Management Systems and to continually improve upon their EHS&S performance. India also adopted the RC in 1993. Indian Chemical Council (ICC) has taken up the responsibility of spearheading this initiative, for industries in India.
In view of the lockdown which has impacted all industries across the globe, RC assumes renewed importance.
In order to disseminate information about RC among the Chemical Industry, ICC organized a series of webinars from April 18 to April 30, 2020. More than 150 participants attended each session.
The Responsible Care program has the following seven codes, each with a specific focus area. RC is a Top Down approach and hence begins with Top Management Commitment.
1. 2.
3. 4. 5. 6.
7. Process Safety Code Employee Health and Safety Code Pollution Prevention Code Emergency Response Code Distribution Code Product Safety and Stewardship Code Security Code

PROCESS SAFETY CODE
Process Safety may be defined as follows:
The implementation of engineering practices, process designs and operating and maintenance procedures, which minimize or eliminate the risk of injury or death from the operation of a physical or chemical process.
The importance of Process Safety may be summarized as follows: z System should be designed to proactively prevent or mitigate incidents z Should integrate different aspects of risk z Establish risk- based awareness of the safety impact of the technology, facilities and personnel z System should be designed to prevent unintended hazardous releases z Should provide for continual improvement
Focus areas emerging from the discussions during the webinar on Process Safety are summarized below. z Periodicity of Review of documents must be defined by each company z Detailed discussions on the importance of manpower Change in Management of Change z Importance and duration of
Preservation of fitness records of employees was explained z Importance of Selection of z
z
z
z
z z
z
z Contractors and feedback regarding HSE Discussions on importance of QRA, LOPA, HIRA, MCLS etc Discussion on how to operate with lean manpower during a pandemic Responsibility of preparation of Off-site Emergency plan to be clearly defined Importance of Work Permits was highlighted Understanding Asset Integrity Importance of Pre-startup Safety Review especially after lockdown Understanding Process Safety Incident Review Tracking Leading and lagging Indicator
EMPLOYEE HEALTH AND SAFETY CODE
The webinar highlighted the importance of Employee Health and Safety especially in the Chemical Industry. EH&S is embedded deep in the guiding principles of RC.
The Employee Health and Safety Code requires companies to ensure that not only permanent employees but also contractual workers and even visitors are allowed to enter / work on the premises after having gone through the mandatory training/ information sharing. This helps all persons on the premises to be aware of the dangers that he/ she may be exposed to, while on the site and what to do in case of an emergency.
While the importance of Employee Health and Safety was understood well by the participants in general, the following points were discussed in detail. z Employee participation – importance of teamwork even in formulating policies, laying down
SOP and work instructions for carrying out jobs at the shop floor z JSA and HIRA- Job Safety Analysis and Hazard Identification & Risk
Analysis including categorization of Hazards z Globally Harmonized Safety Data
z
z
z
z
z Sheets- Use of 16-point SDS for evaluation of Hazard and dissemination of information regarding the products being handled Importance of clear written down and updated SOPs for effective communication Training as an effective means for imparting knowledge and information about the SOPs to be followed Effective use of tools for incident investigation – why why, Fault Tree analysis, FMEA- root cause for each incident to be established Understanding the importance of maintenance of Safety Equipment Ascertaining the difference between Medical Surveillance and Medical Fitness
POLLUTION PREVENTION CODE
The Chemical industry in India already has a poor image with respect to pollution, as many cities in India are highly polluted and growth / expansion in these cities has been banned. With this background in mind, the webinar started with stressing the need for understanding importance of Pollution Prevention especially as it is ingrained in the latest UN Sustainable Goals as well.
Mainly the pollutants can be classified into the broad categories as under. z Greenhouse Gas (GHG)
Emissions z Carbon Dioxide (CO2) Emissions z Sulphur Oxides (SOx) Emissions z Nitrogen Oxides (NOx) Emissions z Particulate Matter (PM) z Wastewater z Hazardous Waste
Discussions during the webinar were focused around the following areas. z Inventory Management – taking stock of the hazardous chemicals stored at a particular site and finding avenues for reducing the z
z
z inventory to minimize the hazard Planning for reduction of the pollutants and implementation of the plans Monitoring and Measurement of progress of the plans Groundwater monitoring and protection
EMERGENCY RESPONSE CODE
The Emergency Response Code requires the companies to assess the concerns of the community and develop procedures and effective measures to address issues arising out of an accident.
The importance of this code was highlighted during the webinar and appreciated by all the participants
more so in the light of the spate of accidents that have taken place in the recent times.
The webinar focused on the importance of having a written, updated and well-rehearsed emergency response plan with the communication channels clearly defined.
While the importance of the emergency response plan was known to all participants, the finer details of the Emergency Response code were highlighted and appreciated by all. The details of the discussions are summarized below. z Understanding the importance of an On-going dialogue with the community, understanding issues and addressing them z Assessment of Potential risks and laying down a well-rehearsed response plan for addressing those risks. The importance of understanding the concept of
Maximum Credible Loss Scenario was explained in detail. z Importance of pre-defined trained manpower for communication during an emergency was stressed z Training of on-site responders including training/imparting
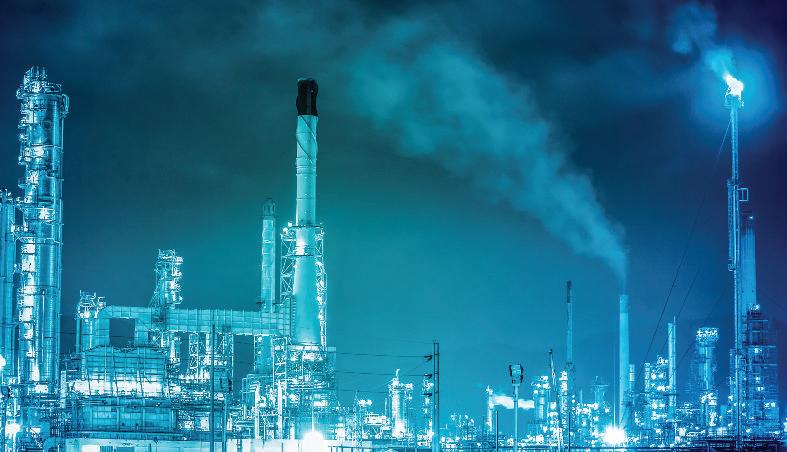
z knowledge about the role of manpower not directly involved in an emergency The need for testing the emergency plan through frequent drills was stressed. Shortcomings observed during these drills should be overcome.
DISTRIBUTION CODE
While most participants stated that they have a checklist for the trucks/ tankers, they were not aware of the intricacies of the code except for the
persons who were aware about RC.
The aim of the distribution code was explained to the participants. z Reducing the risk of harm posed by the distribution (transportation) of chemicals to the general public; to carriers, distributors, contractors and chemical industry employees and to the environment. z Responding to public concerns about safety of products in transit. z Participating with government and others creating responsible laws, regulations and standards to safeguard the community, workplace and environment.
Some of the important
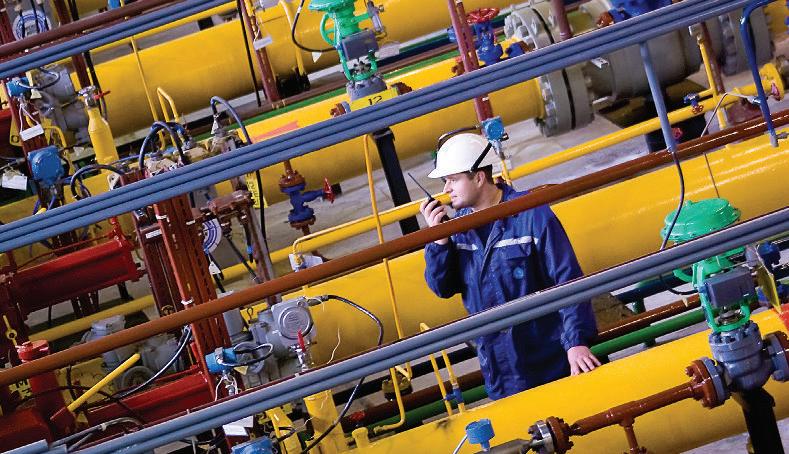
discussions that took place during the webinar are listed below. z Regular evaluation of chemical distribution safety and security risks should be strengthened by the companies - the hazards of the material, the likelihood of accidents/incidents and the potential for human and environmental exposure from release of the material over the route of transport and handling in distribution chain. z Identification of likely hazards in z
z
z
z
z handling of the material due to loss of containment in transit or during loading – unloading. Hazard communication to the driver and the customer/ distributor in the form of (M)SDS, TREM-Card, Labels etc. Journey Risk Analysis should be done by the companies for all routes where transportation of hazardous chemicals takes place – JRA to take into account the material hazards and also the mode of transport like, Vehicle, rail, pipeline, shipping etc. and the route related issues such as road condition, population etc. The companies should plan to combat/ tackle any emergency
which may happen during transportation. A mock drill should be conducted to consider emergency planning and preparedness at third party and off-site warehouses etc. Training of company employees and contractor employees to meet transport regulations and internal company requirements for safe handling of materials needs to be strengthened. Driver recruitment, driver training. (3day training as per z CMVR) Training of company employees, Training of LSP employees should be equal importance. System for internal reporting and investigation of chemical distribution accidents / incidents, and implementation of preventive measures should form a part of the emergency plan. Corrective and preventive actions arising from such investigation to be incorporated in safety planning for distribution. Such information should be shared with all relevant stakeholders.
PRODUCT SAFETY AND STEWARDSHIP CODE
The participants had many questions about the Product Safety and Stewardship code as it is not very commonly understood by most companies.
The aim of the webinar was to disseminate information and educate the participants about this code.
It was explained that Product stewardship occurs when all those involved in the lifecycle of a product take responsibility to reduce the risk of adverse environmental, health and safety impacts to gain the most value from a product.
It involves commitment by the top management to safety of products through design, communication, continual improvement and information sharing with customers, handlers, distributors and all stake holders.
Most of the discussions in the webinars were centered around understanding the concept of Stewardship in details. Some of the discussions are highlighted below. –A process should be developed by the companies to identify, implement, document and communicate health, safety and environmental measures to manage risk so that products can be safely handled and used for their intended purposes
throughout the lifecycle. Based on risk characterization results, a procedure should be established for management of identified risks in processes, handling, intended use and disposal of product. Process needs to be put in place to prioritize the products that may require a more detailed evaluation, assessment, and risk management controls, as well as identify those substances which may require additional data and information gathering, to remain updated with the latest information on the hazards, eg CMR chemicals Focus should be laid on designing /selection of products and processes (or redesigning existing products and processes) using a system to minimize health, safety and environmental impacts and meet sustainability expectations throughout the lifecycle. An effective way of managing product risk is by attaining the preferred environmental hierarchy: source reduction, reuse, recycle; and disposal. Processes should be developed by the companies to communicate, receive and evaluate product safety and stewardship information from all value chain participants. The information collated by the companies should be reported to ICC to facilitate public understanding of the member industries’ overall product safety commitment and performance by filling the Global Product Strategy Report.
SECURITY CODE
Since the security code has been implemented recently by ICC, the discussions were centered around understanding the concept of the code.
The discussions are enumerated below.
The purpose of Chemical Safety is to protect people from chemicals, while Chemical Security protects chemicals + related information from people. However, both ensure protection of z Workers z Plant facilities z Plant processes z Community z Environment z Economy
The objective of the security code is to z Ensure Commitment and
Implementation of a Security
Program across the full Chemical
Value Chain z Reduce the potential for theft and subsequent misuse, the intentional release of Chemicals or Sabotage of Chemical processes causing a release focusing on fixed facilities. This includes the physical protection z
z
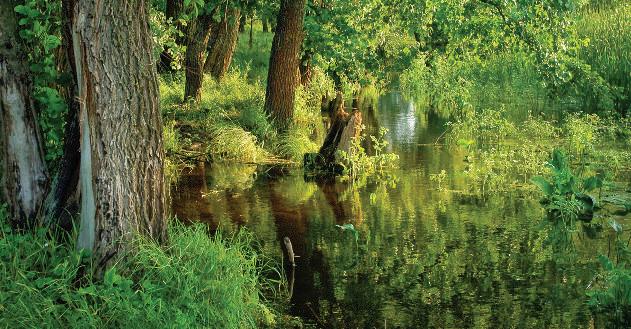
of assets and monitoring the specific assets within a facility Determine the potential Security risks based upon assets Include the development of policies, training, documentation and funding to support security for the life cycle of the chemicals. This concept is based on five pillars and the companies are expected to incorporate an overall management system that
supports these five pillars
The five pillars of this system are z Physical Security z Transport Security z Inventory Management z Personnel management z Information Security
Needless to say, these pillars have to be built on the foundation of the company involving its culture, procedures, regulations and management philosophy.
The process starts with carrying out a Security Vulnerability Assessment and developing the system as laid down above. The SVA forms the basis of the entire management system.
ABOUT THE AUTHOR: RAJEEV MARWAH (born October 29, 1958) is a graduate engineer from India’s premier engineering institution – Indian Institute of Technology Delhi and is an MBA from the prestigious Faculty of Management Studies, Delhi University. He has over 35 years of hands on experience in the Chemical Industry. He has led teams of more than 200 technical and managerial staff and officers. Currently he is a freelance consultant working in areas associated with Environment, Safety, Energy and Process optimisation and is currently associated with Indian Chemical Council as a team Leader for Responsible Care assessment. Rajeev has delivered several lectures / presentations and has done assessment of several industries for the Indian Chemical Council.