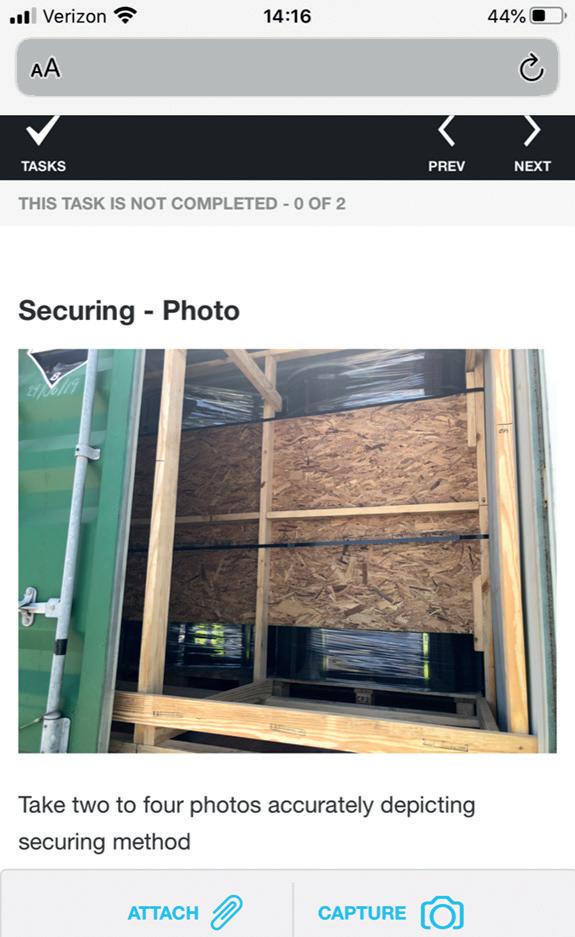
6 minute read
News bulletin – safety
NEWS BULLETIN
SAFETY
REMOTE SURVEYS FROM NCB
National Cargo Bureau (NCB) has launched a remote container inspection service, based on the Hazcheck Inspections database and access portal developed by NCB subsidiary Exis Technologies, as part of its long-running mission for the safety of life and cargo at sea. The new service uses mobile devices to connect customers with NCB’s experienced team of surveyors, so they can review and inspect container transport units remotely. The information and media files that the customer captures remotely via the device (below) are automatically uploaded to the mobile platform.
“We are delighted to be able to offer this new service to our customers,” says Ian Lennard, NCB president. “Container inspections need to be carried out in a timely manner and on a global scale, particularly in locations where dangerous goods expertise may not be available. We are able to conduct remote inspections for customers throughout the supply chain, improving safety as well as helping with the overall efficiency of shipping containers.”
NCB has already carried out remote inspections for three of the top ten container lines: Evergreen, Maersk and Hapag-Lloyd. Capt YS Hwang, deputy head of operations at Evergreen, reports: “NCB recently carried out some remote inspections on our Ever Pride vessel in Taiwan following a fire caused by undeclared seed cake. The remote capability of the inspection process allowed us to investigate the cause of the fire immediately upon the vessel’s arrival after the box discharged ashore, with direct help from an experienced team of surveyors with dangerous goods expertise, rather than waiting for them to be available to travel to the port to carry out a survey in person. We would definitely use this method of container inspection again in the future.” www.natcargo.org
GET IT RIGHT OR PAY
Wan Hai Lines (WHL), the Taiwan-based containership operator, has introduced penalties for shippers found to have mis-declared container contents. “From now on, if the declarations and shipping forms and documents enclosed are not true and not accurate, WHL has the rights to immediately stop or suspend the delivery of the cargoes or terminate the contract of delivery for the cargoes at any time during the carriage,” the company says.
Those responsible for misdeclaration – shipper, freight forwarder, consignee or other notifying party - will be liable for all damaged and losses and will also be penalised by WHL to the tune of $30,000 per dangerous goods container or $20,000 per container for non-hazardous goods. Mis-declaration includes not only falsification of the contents of the container but also the weight of the box.
WHL’s move follows shortly after Pacific International Lines (PIL) introduced a similar level of charges for the shipper and/or consignee for mis-declaration of the cargo weight, as well as holding them responsible and liable “for all corrective measures, claims, fines, liabilities, losses, delays, damages or expenses arising in consequence of such misdeclaration”. www.wanhai.com www.pilship.com
GET THE RIGHT SHED
TT Club has published a guidance document on warehouse risks under its TT Brief series. The publication comes at a time when the warehousing and intermediate storage of dangerous goods have some under the spotlight following the Beirut explosion in 2020 and when players throughout global supply chains are having to adapt their logistics practices to deal with congestion, delays and higher freight costs.
“Arguably, warehouses have become an increasingly important node, as supply chain actors reconsider just-in-time supply chain models, adopting a more conservative approach, near-shoring and generally holding increased stock at the point of production or market,” TT Club says. “Some actors in the supply chain will have been forced to demonstrate agility over the last two years, perhaps embarking on new or increased warehouse capacity requirements to meet evolving business needs. Those exploring warehousing operations however, should not be complacent and develop an understanding of the associated risks.”
In light of those changes, the TT Club guidance focuses on the issues that need to be considered when choosing a storage warehouse. Inevitably, it says, there are practical issues that will be paramount: location, proximity to transport networks, capacity, availability of labour and rental prices and/or land costs. The document examines in particular the risks and potential liabilities that a warehouse customer
can face and how those risks can be mitigated.
More information on the new guidance can be found on the TT Club website at www.ttclub.com/news-and-resources/publications/ tt-brief/choosing-a-storage-warehouse/.
CARGO INTEGRITY GROUP EXPANDS
The Bureau International des Containers (BIC) and the International Federation of Freight Forwarders Associations (FIATA) have joined the five original partners in the Cargo Integrity Group, established last year to bring together international freight transport and cargo handling organisations with different roles in the supply chain and a shared dedication to improving safety, security and environmental performance throughout the logistics supply chain and to promote the use of the Code of Practice for Packing of Cargo Transport Units (the CTU Code).
Both FIATA and BIC have already worked closely with the Group and will now contribute directly to faster and more effective progress in reducing incidents, accidents and biosecurity issues in the international supply chain by bringing their complementary perspectives, resources and networks to the Group. The original members of the Cargo Integrity Group are the Container Owners Association (COA), the Global Shippers Forum (GSF), ICHCA International, TT Club and the World Shipping Council (WSC).
“FIATA has long supported the work of the Cargo Integrity Group and has already collaborated with its stakeholders to promote the CTU code. By joining the group, FIATA reaffirms its commitment to improving the safety and security of sea freight in the best interest of its customers,” says director general Dr Stéphane Graber.
Douglas Owen, BIC secretary general, adds: “With safety and sustainability at the very core of BIC’s mission, topics like cargo safety, proper declarations and the avoidance of pest contamination are clearly of high interest to us. We’ve been supporting the promotion of the CTU code in communications both with our members and externally since it was first published, and most recently sponsored one of the CTU Quick Guide translations.” fiata.org www.bic-code.org
CLS ADDS DGIS
Creative Logistics Solutions (CLS), which provides multi-carrier shipping software to major retailers, distributors and e-commerce companies, has integrated Labelmaster’s Dangerous Goods Information System (DGIS) into its software solutions. This move will allow CLS’s customers to automatically create compliant shipping documents and labels.
“In today’s dynamic and competitive supply chain market, shippers need a seamless, end-to-end shipping solution that drives operational efficiencies and provides peace of mind that shipments are compliant with the latest regulations,” says Malcolm Johnson, vice-president, strategy and business development at CLS. “Integrating DGIS enables organisations to automate and streamline their shipping processes by providing all of the necessary DG shipping forms and rules within the InfoShip/Vx platform. This eliminates the need for companies to decouple DG shipping from their traditional shipping workflows and processes and the need for them to learn and manage multiple user interfaces.”
“Shipping dangerous goods can be complex and challenging. As a result, companies often tend to shy away from shipping DG or, in some cases, may not even be aware that they’re shipping hazmat,” adds Kristen Dapore, director of business strategy at Labelmaster. “Having a compliant shipping solution in place will enable organisations — whether large global enterprises or small e-commerce companies — to grow and add dangerous goods SKUs into their inventory mix without worrying about compliance. Companies adding those products will be able to begin shipping them quickly and efficiently and scale their operations more easily while taking proactive steps to mitigate risk and avoid supply chain disruptions.” www.creativelogistics.com www.labelmaster.com
