
13 minute read
in the Engine Room
Technical Safety Precautions during Machinery Maintenance in the Engine Room
Introduction
The Engine Room is a complex space accommodating the majority of the most crucial pieces of machinery for the vessel’s operation such as the main engine, diesel generators, boilers, air compressors, coolers and pumps. Taking into consideration that every part of the Machinery equipment is also intertwined with piping systems, tanks, cabling, lifting arrangements and various tools, it is evident that works in the Engine Room can prove challenging. Therefore, when planning and executing maintenance or repairs on machinery, the crew must always take into consideration all the safety guidelines provided by the equipment Makers as well the precautions based on the nature of the work to be done e.g. welding, electrical works etc.. The following guidelines include crucial points to ensure safe and efficient work for machinery-related items onboard. a) Engine Room Personnel Maintenance jobs shall be carried out exclusively by qualified personnel using the necessary Personal Protective Equipment (PPE). Attention must be paid to the following:
Safety shoes, hearing •
protection, work gloves and protective headwear must be worn when there is risk of falling objects, loud noises and sharp edges or oily surfaces.
Safety googles must be used when working with compressed air, hydraulics and grinders, or when there is risk of getting foreign objects in the eyes.
A fall protection harness and arrestor equipment is recommended when working in places on the engine where there is risk of falling or slipping.
Gloves made of neoprene or PVC shall be used when removing O-rings and other rubber/plastic-based sealing materials which have been subjected to abnormally high temperatures and may have a caustic effect when touched directly.
Figure 1: Personal Safety Protective Equipment
Gloves must always be used when working on or near hot surfaces. All crew members must ensure that their uniforms are clean, dry and properly cover the whole body.
• Jewelry, wrist bands or rings must be removed before work as these can put the worker at risk, especially when working with rotatory tools or performing electrical work. • When working in groups, always discuss the procedure, action plan and hazards of the jobs prior to initiating the work. In all cases, without exception, please consult the PPE Matrix that is included By Christina Toki in FIM, with instructions on what PPE is required for each task. Also, never forget two of the strongest tools you have to stay safe during work: the Daily Work Planning Meeting (DWPM) and your LMRA cards (doing your Last Minute Risk Assessments BEFORE commencing any task). Follow them wisely and consistently, and stay safe! b) Special Dangers A number of situations may lead to risk of serious injury to the body. The following recommendations must always be observed:
Opening cocks may cause discharge of hot liquids or gases
Dismantling parts may cause the release of springs - Do not stand near turbochargers in case of any abnormal running - Do not stand near crankcase doors or relief valves nor in corridors near doors to the engine room if an alarm is set off for: • oil mist • high lube oil temperature • no piston cooling oil flow • or a scavenge box fire
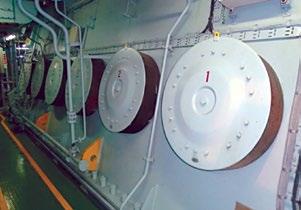
Figure 2: Main Engine relief valves
c) Cleanliness The engine and engine room must always be kept clean, with floors and surfaces free of oil, soil and dirt.
Figure 3: M/E Lower platform free of oil
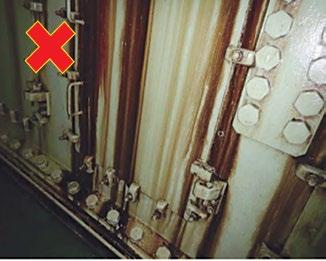
Figure 4: Oil leakage on the M/E
Oil spills shall be immediately removed and oily rags shall be collected and stored by the crew to avoid risks of accidents due to slippery floors and fire incidents. The exterior of the engine should be kept clean, and the paintwork maintained so that leakages can be easily detected. Bilges are to be painted a light color to assist in visually identifying a fresh leak and their chemical cleaning is to be completed periodically. clean of oil and water lead to PSC Detentions If there is a risk of grit or sand blowing into the engine room, stop the ventilation and close the ventilating ducts, skylights and engine room doors. Welding or other work that causes the spread of grit and/ or swarf must not be carried out near the engine unless it is closed or protected and the turbocharger air intake filters are covered. d) Fire Prevention i. Fuel leaks According to reports, approximately 50-60% of engine room fires are attributed to fuel leaks. Loosening joints, fractured pipes and mechanically damaged pipes on both high and low pressure fuel lines, pipe unions that are over or under tightened, the use of unsuitable seals or gaskets which deteriorate due to the effects of heat are some of the reasons that trigger an oil fire. To avoid oil spraying on hot surfaces and electrical installations, the flanged connections must be guarded using anti-splashing tape. In the case of the anti-splashing tape being temporarily removed for maintenance or repair, it must be reinstalled upon the completion of the relevant work. ii. Pipe Insulation Preventing oil leaks is one half of the problem; the other being effective cladding or shielding of hot surfaces so that they do not present a source of ignition if an oil leak occurs. It is a SOLAS requirement that surfaces, which are at temperatures above 220°C that might come into contact with oil as a result
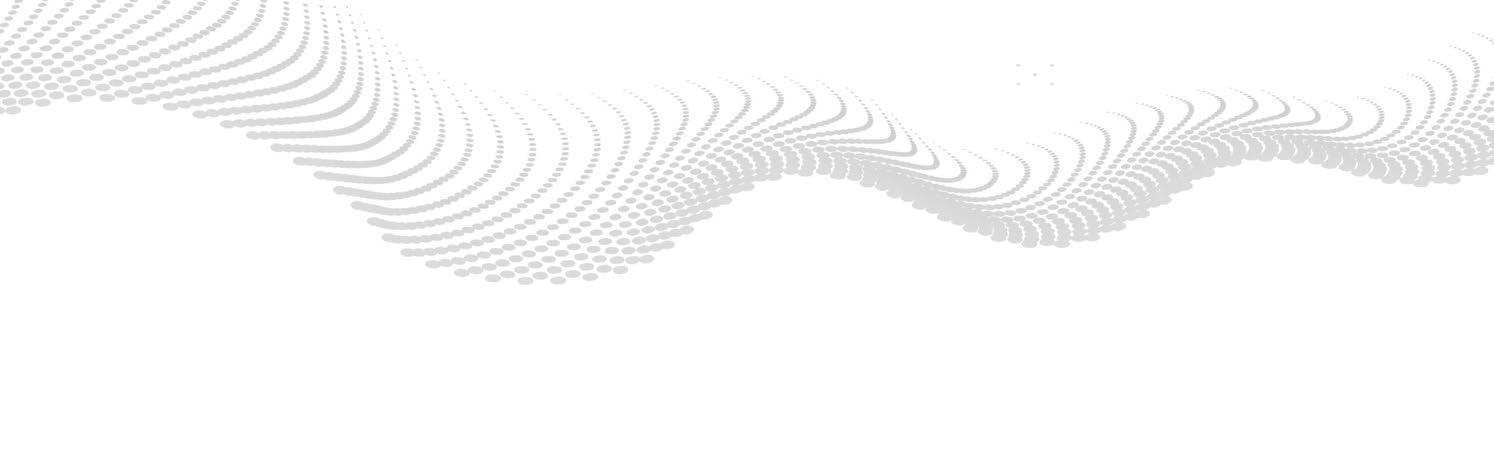
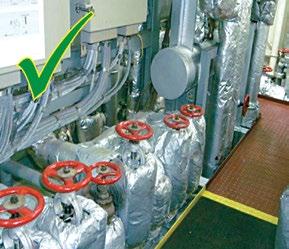
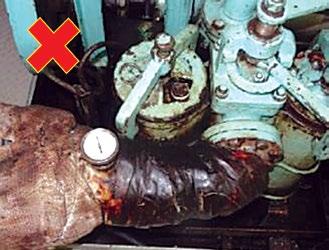
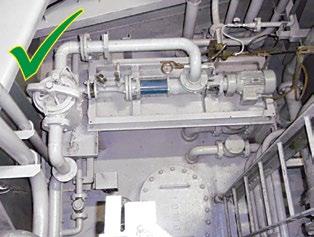
Figure 5: Bilge areas must be
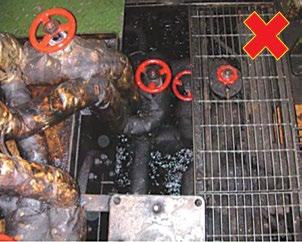
Figure 6: Oil contamination is dangerous for Fire incidents and may
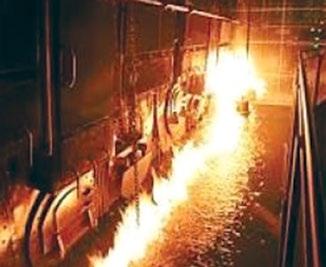
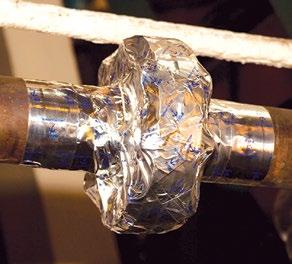
of system failure, are properly insulated.
Figure 9: Well-maintained insulation Figure 10: Insulation soaked in oil that requires replacement
The crew must regularly check the integrity of the insulating materials and rectify any gaps identified. Significant attention shall be paid to equipment of complex design such as turbochargers or bents and flange joints on pipelines. For those areas, routine surface temperature measurements are also suggested. Insulation contaminated by oil or other flammable products must be renewed and insulation removed during maintenance must always be fully restored. iii. Welding and paints Welding shall be carried out only after ensuring that there are no naked lights and no explosive gases, vapors or liquids present in the engine room. The surrounding area must always be inspected prior to welding to make sure that no flammable item is in the vicinity. Before carrying out any kind of hot work, make sure that the hot work checklist and risk assessment forms have been duly filled. It is of the utmost importance to ensure that the requirements in FIM Chapter B for hot work and entry into enclosed spaces (if applicable) have been followed, including obtaining the required authorization and issuance of permit, be it from the shore management or on board according to the relevant matrix. All safety procedures must be strictly followed while carrying out such jobs in enclosed spaces. Attention is also drawn to the danger of fire when using paint and solvents with a low flash point. Porous insulating material soaked with oil from leakages is flammable and should be
Figure 7: Anti-splashing tapes applied on flanges Figure 8: Image shows fuel oil ablaze after spraying onto hot surface
renewed.
Chart 1: Most common causes of Fires (DNV, 2000)
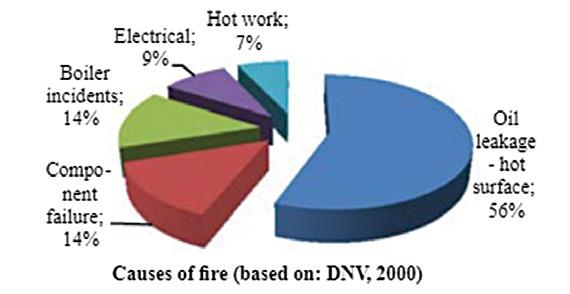
e) Turning Gear Before engaging the turning gear, make sure of the following: 1. The starting air supply is shut off. 2. The main starting and slow turning valves are blocked. 3. The indicator cocks are open. The turning gear must be operated by the remote control and only by the person working on the engine. The remote control should always be kept in optimal working condition and any fault in the device or cable must be rectified before use. Warnings must be given before each turning. Operation of the turning gear from the switchboard must not take place while maintenance work is in progress inside the engine.
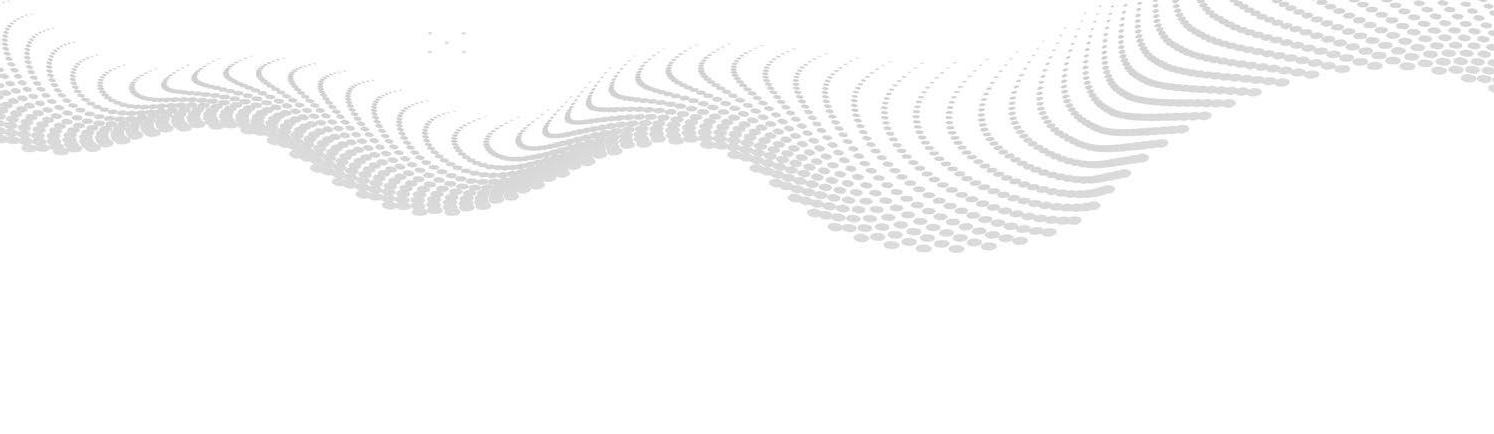
Figure 11: Guidelines for engaging/ disengaging the turning gear must be thoroughly followed.
When the turning gear is engaged, check that the indicator lamp ‘Turning gear in’ has switched on. It is also suggested that warning placards with the words ‘Turning gear engaged’ are made and hung at all maneuvering stations whenever the turning gear is engaged, irrespective of whether the safety devices are functional. These placards should be removed only after disengaging the turning gear.
f) Entering the Crankcase or Cylinder
If the crankcase is opened before the engine has cooled down, welding and the use of naked flames will result in the risk of explosions and fire. Prior to entering the crankcase, the crew must check that the starting air supply to the engine and the starting air distributor are shut off and that the main starting valve is locked. Before entering, ventilate the crankcase for about 30 minutes after stopping the engine. When working in the crankcase, a safety harness and fall arrestor equipment is strongly recommended. The turning gear should always be operated exclusively by the personnel who enter the crankcase or cylinders. Work in the crankcase is a minimum two-man job and requires good communication that must be maintained at all times.



g) Lifting Appliances Prior to any use, lifting appliances/tools must be visually inspected for cracks, corrosion, excessive wear, loose fasteners, deformations and damage. Unidentified or damaged tools and tools not clearly marked with Safe Working Load (S.W.L.) or Work Load Limit (W.L.L.) must not be used.

Figure 14: The S.W.L. must not be exceeded under no circumstances.
When using lifting appliances make sure the following guidelines are taken into consideration:
Table 1: Guidelines for planning & executing lifting operation
1 2
3
4 5
6
7 8 9 LIFTING GUIDELINES
Keep clear of the space below a crane with load. Never exceed the lowest Safe Working Load (S.W.L.) of the lifting equipment in the lifting chain. Plan lifting of engine components through all steps of the lifting procedure. Only use designated lifting points. Use tackles between the engine room crane and component, when lifting loads below 500 kg. Make sure the lifting attachments are tightened into full contact with the component to be lifted. Make sure to attach the load correctly on the crane hook. Keep the lifting equipment clear of sharp edges. Carefully inspect the wire rope before starting the work and identify any defects.
Wire ropes must not be used when the following defects are identified.
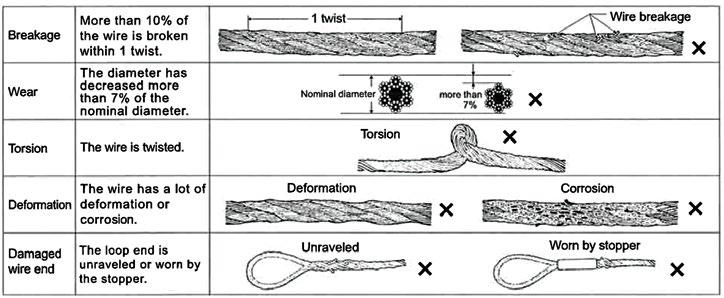
Figure 15: When wire rope defects are identified, no lifting operation shall take place.
Figure 12: Work in the crankcase requires meticulous communication and planning. Figure 13: Special attention must be paid prior to entering the M/E Crankcase.
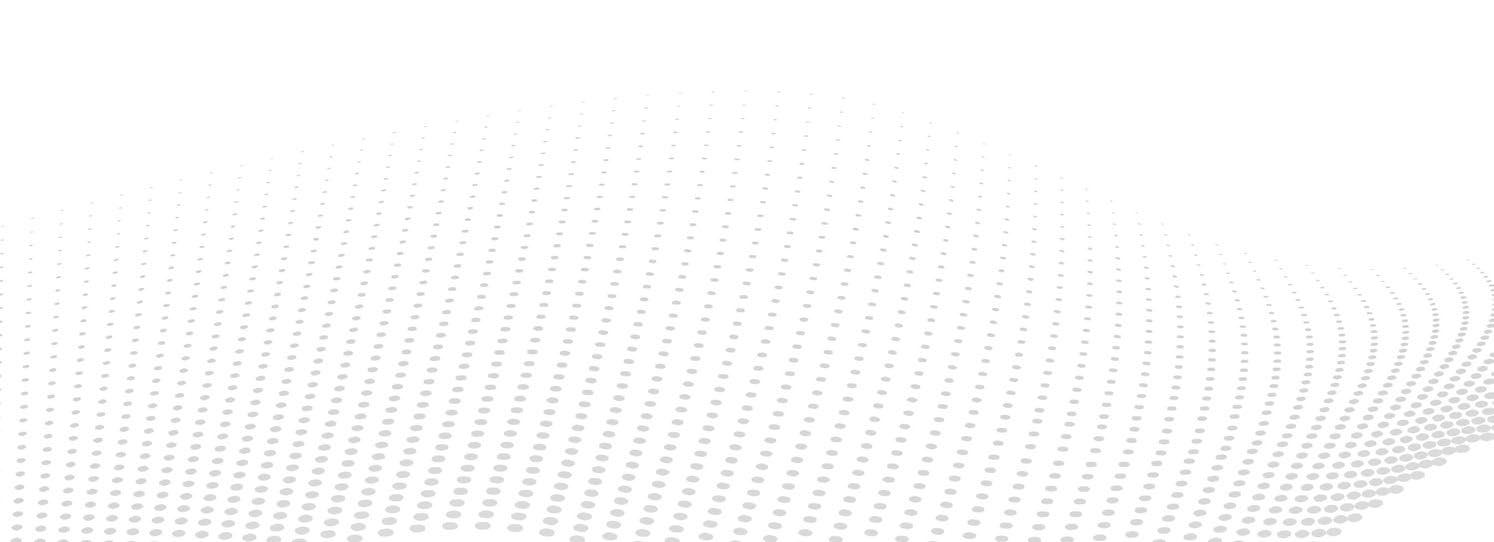
(A) (B) (C) Figure16: Wire rope with (A) corrosion, (B) loosening of the individual wires and (C) appearance of pinch points.
When using chain tackles, be aware of the lifting angle. When using hooks, keep in mind that only hooks with safety latches are allowed for lifting.
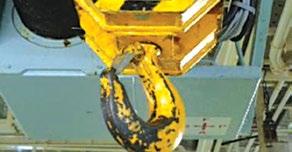
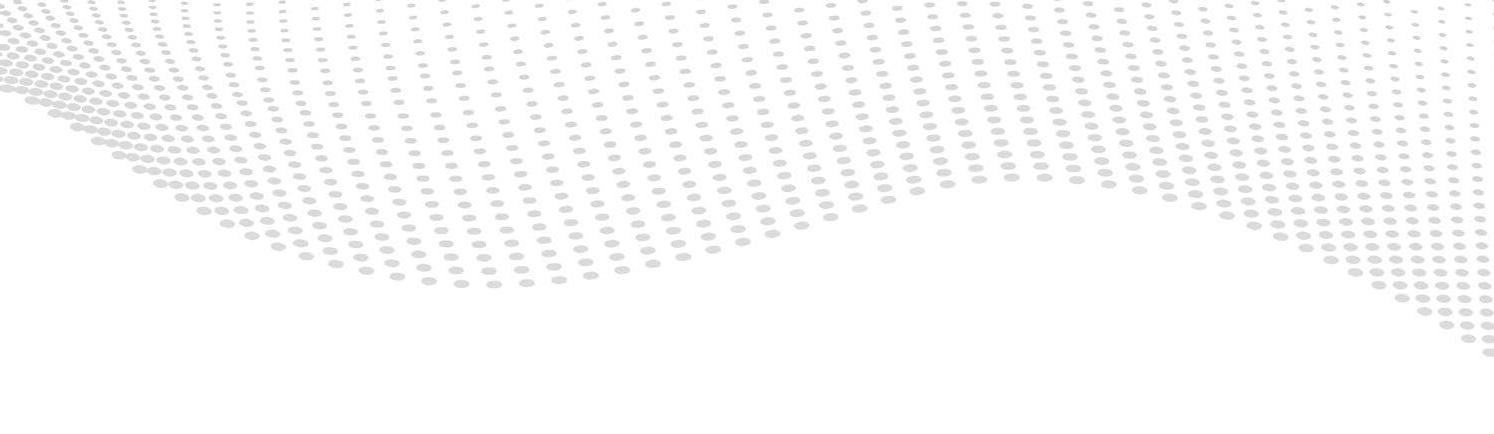
Figure 17: Hook with safety latch When using eye screws/eye nuts, be aware of the loading direction, as lateral loading is prohibited.
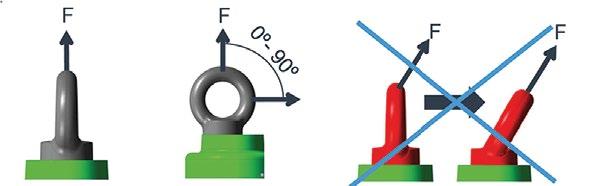
Figure 18: Loading direction of eye screws to be taken into consideration
h) Electric Shock Hazards Electric shock is the physical stimulation or trauma caused by the flow of electricity through the human body that can occur during contact with or by being near live (energized) electrical parts. Electrical Shock hazards may occur due to: • Defective electrical tools: Untrained or unqualified personnel attempt electrical power connections • Improper electrical phasing: Damaged wire insulation as a result of hot work processes • Corroded connectors: Attributed to saltwater intrusion or contact • Worn or frayed electric cables: Inadequate electrical isolation, failure to test for de-energization, and improper lockout/tags-plus application • Electric cables pinched in hatches/doors: Tools and equipment not properly grounded • Electric cables struck by grinders/saws: Blind-side drilling into electrical conductors An electric shock can occur without direct contact with electricity and is the predominant root cause of burn injuries. Safeguards against common causes of electrical hazards are: 1. Using appropriate PPE (rubber gloves, rubber boots) and using appropriate insulating rubber mats when required 2. Testing and regular maintenance of equipment 3. Regular testing of overload devices 4. Checking that insulation is in good condition 5. Checking connections are made properly
Figure 19: Always wear protective clothing, rubber gloves, rubber knee pads and safety shoes to avoid risk of shock. Further instructions on the use of PPE for Electrical hazards can be found in FIM Chapter B. i) Alarms It is important that all alarms lead to prompt investigation and remedy of the error. No alarm is insignificant. Never cancel an alarm (even a repetitive / annoying one) without first investigating it thoroughly and establishing for yourself the actions to be taken. Always remember that Risk Normalization is to be avoided, and cancelling alarms without checking is a common mistake – it has to stop! The most serious alarms are equipped with slow-down and/or shut-down functions. It is, therefore, important that all engine operation personnel are familiar and well- trained in the use and importance of the alarm system. j) Lighting Ample working light should be permanently installed at appropriate places in the engine room spaces, and portable working lights should be obtainable everywhere. 24V safety lamps must be available for use inside the engine.
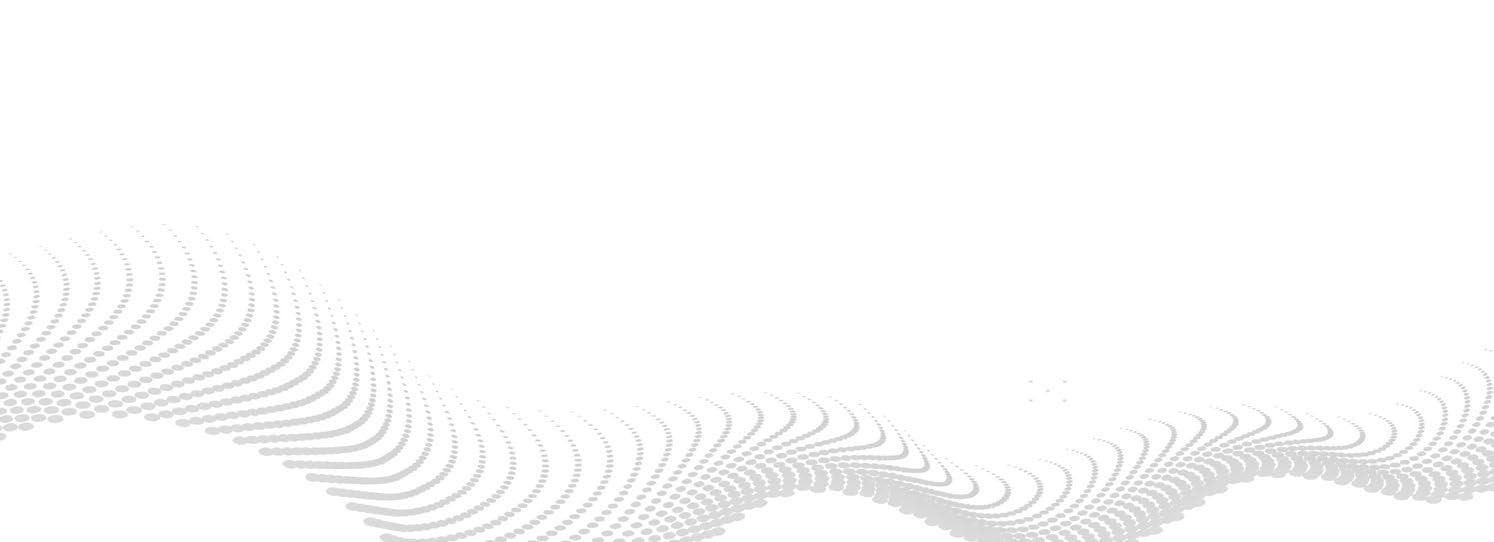
Figure 20: Working lamps to be properly stored for cable protection
k) Storing and Securing Large spare parts should, as far as possible, be placed near the area of use, well secured and accessible by crane. Under no circumstances should the engine parts be stored on engine galleries while the engine is running.
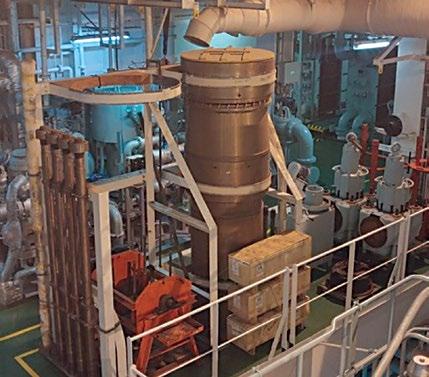
Figure 21: Large spare parts shall be properly supported and secured
All spares should be protected against corrosion and mechanical damage. The stock should be checked at intervals and replenished in good time. If paints and thinners are carried onboard, they should be stored in their original container, protected from direct sunlight in a dry, cool and well ventilated space, away from incompatible materials, hot areas and exhaust gases or vapours. Hand tools should be securely fastened and placed on easily accessible tool panels. Special tools should be securely fastened close to the area of use in the engine room. Oxygen and acetylene bottles must be stored outside the engine room and accommodation areas. They must not be stored together but kept apart and securely lashed. Lockers containing gas bottles must be properly identified and marked accordingly. Conclusion
Nobel Prize winner poet Pablo Neruda introduced us to his poem titled ‘The Sea’ with the verse saying ‘I need the sea because it teaches me, I don’t know if I learn music or awareness’. And even though music is an enjoyable companion of many seafarers, awareness is an imperative necessity in order to safeguard human life and the integrity of the vessel.