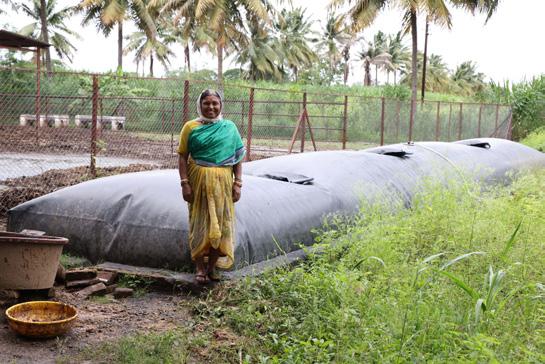
40 minute read
Driving with SUSTAINABILITY BIOGAS
“At Sistema.bio, we are committed to optimizing our supply chain and production operations by implementing effective inventory management techniques. We monitor inventory levels, and make use of effective ordering and production methods to reduce wastage. Using our robust inventory management and supply chain, we can service that last-mile demand within a given timeframe and with a high-quality threshold in extremely remote rural áreas,” shares Piyush Sohani, MD, Sistema.bio India, during this exclusive interview…
How did the seeds of Sistema. bio take fruition? The increasing adoption of biogas paves way for eco-friendly practices as well. Kindly elaborate how Sistema.bio works towards addressing and enhancing the same?
Advertisement
In 2010, Alex Eaton and Camilo Pagés founded Sistema.bio in Mexico to address the challenges of poverty, food security, and climate change. In rural areas, smallholder farmers face a lack of affordable and reliable energy sources that limit their production and living standards. Biogas was a potential remedy to these problems, our co-founders worked on developing a scalable and costeffective biogas system for smallholder farmers.
Our biodigesters convert organic waste, such as animal manure, into renewable energy in the form of biogas. Depending on the needs of different farmers and the size of their farms as well as the availability of feedstock, the system is modular. It can be altered to suit their requirements. Biogas technology from Sistema.bio can help farmers generate renewable energy and reduce their reliance on fossil fuels. As a result of the bioslurry produced, crop yields and soil health can be improved, reducing synthetic fertilizer usage.
Kindly enlighten us on the value chain of Sistema.bio from Waste to Value.
Livestock manure can pose serious threats to the environment and human health if not managed adequately. Usually, the waste generated from livestocks at farms is dumped by the roadside to decompose which is then used as Farm Yard Manure (FYM) in agricultural practices or as dried dung cakes for cooking. This leads to two main issues. First off, it causes the discharge of methane gas, a pollutant for the environment. Second, it can also result in groundwater contamination during rainy seasons.
Our cutting-edge technology solves these problems by turning animal waste into a useful resource for both farmers and the environment. By feeding the livestock waste into a biodigester, methane gas is produced, which can be used for cooking. This reduces the need for LPG and supplies a sustainable energy source to farmers. Additionally, the biodigester also produces bioslurry that is richer in nutrients than the conventional Farm Yard Manure (FYM), providing farmers additional advantages.
What were the challenges that you encountered during this journey?
The Government of India (GoI) is driving the use of biogas plants, especially with smallholder farmers, dairy farmers and creating a value chain that will immensely contribute to enhancing the livelihoods of dairy farmers and promotion of green energy. However, while biogas plants have existed in India for over six decades, the acceptance levels were very low due to high cost, amount of land they occupied, the required civil construction, minimal or no training and no support in postinstallation maintaining them.
Piyush Sohani is an entrepreneur by heart and passionate about sustainable technologies and social development. Prior to leading Sistema.bio India, Piyush had worked with a number of credible organizations including TERI, Tata Consultancy Services and Indian Oil. He has a vision to create a world where waste is a resource, and farmers are empowered and productive. Piyush has a Masters degree from TERI University in renewable energy engineering and management.
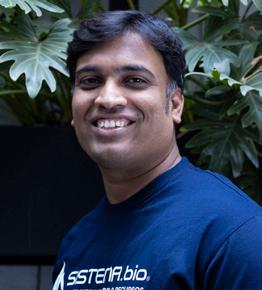
The biodigesters we provide are designed to offer farmers sustainable waste-to-energy solutions, open avenues for generating additional income, and reduce greenhouse gas emissions at farms by up to 80%, reducing their monthly costs for LPG cylinders and chemical fertilizer.
The first task was for us to overcome the farmers' mindset, demonstrate these advantages of our technology to them, and convince them that our innovative biogas plants have the potential to overcome the challenges presented by old biogas plants.
What crucial role does the supply chain have in the value chain?
As a technology-based enterprise, we specialize in manufacturing biodigesters using top-of-the-line material and processes. Our main value proposition is to make sure that our biodigesters last for more than ten years without causing any major difficulty to the farmers. Because we operate in rural regions and seek to establish the trust of farmers, it is vital that our material selection and manufacturing procedure be executed efficiently. Our biodigesters must function flawlessly to make sure farmers are happy and to support sustainable agricultural methods.
We use more than 20 different types of materials, ranging from industrialgrade polyethylene to different kinds of steel, to accomplish this. Since we produce hundreds of biodigesters each month and distribute them worldwide, we have put in place a strong supply chain system to guarantee reliable quality and prompt delivery. To assure the greatest level of quality and dependability for our clients, we actively monitor and manage these difficulties, which are similar to those faced by any business due to global dynamics affecting material demand and price variations.
What are the supply chain best practices you have implemented at Sistema.bio?
At Sistema.bio, we are committed to optimizing our supply chain and production operations by implementing effective inventory management techniques. We monitor inventory levels, make use of effective ordering and production methods, to reduce wastage. Using our robust inventory management and supply chain, we can service that lastmile demand within a given timeframe and with a high-quality threshold in extremely remote rural áreas.
In order to be cost-effective, we place a high priority on developing trusting relationships with our suppliers and obtaining raw materials in bulk in advance. Our logistics management system speeds up deliveries, improves delivery precision, and consumes less fuel. We have developed an efficient supply chain structure to ensure the consistent quality and prompt delivery of our biodigesters.
You have been associated with leading global players who are volunteering sustainability. How do you view sustainability and how are you working towards empowering small dairy farmers?
Sustainability is a core concept at Sistema.bio guiding all of our operations, from sales and service to packaging and product design and production methods. We place a huge emphasis on how the decisions we make now will affect society, the economy, and the environment in the long run as part of our commitment to sustainable development. In terms of markets, financing, and technology, we are aware that small dairy producers frequently confront substantial obstacles. As a result, we work to give these farmers greater control over their own lives by giving them the tools they need to become more independent and sustainable.
Our strategy includes providing dairy farmers with cutting-edge biogas technology as well as the funding they need to access it. The bio-slurry produced from our biodigesters, encourages organic farming methods and lessens dependency on hazardous chemical fertilizers. To help dairy farmers maintain their biodigesters successfully and reap the most benefits possible, we also provide extensive assistance and instruction.
How is the deployment of new age technologies helping the company in the journey?
Technology plays a crucial role in every step of our business process, allowing us to work quickly and effectively. Mobile apps enabled with GPS allow us to locate farmers in the rural areas and provide the best service. Each piece of information pertaining to farmer orders is logged by our sales team using a mobile app, and this information is then sent to our main CRM platform. In order to create the necessary systems, our manufacturing team uses this information. It is also integrated with our financial accounting system to keep track of orders and payments.
We employ a centralized customer care procedure and the same mobile app to track system installations and service in order to guarantee excellent customer service. Additionally, we also provide accessories like smart energy and gas meters to clients who want to track their gas and power usage from biogas, as well as their financial savings on LPG.
What are the global best practices that you are imbibing in India?
Our efforts to advance sustainable agricultural practices in India are intended to reduce negative environmental effects, increase agricultural output, and improve farmer welfare. Due to their success in striking a balance between environmental preservation and agricultural expansion, these practices are gaining attention on a global scale. Our cutting-edge technology is enabling farmers to become independent and well-equipped with the tools to obtain renewable energy, embrace organic farming methods, and efficiently utilize waste, hence lowering greenhouse gas emissions.
We keep open and solid communication with our partners, suppliers, and farmers as part of our commitment to ensure the effectiveness of our supply chain practices. We consistently attempt to enhance our procedures and quality control measures to address any difficulties that may develop, and our inventory and logistics management system is created to maximize our efficiency.
How complex and different is the Indian market than the Western countries?
India has a very diverse culture that varies across regions, religions, and languages. For any organization to be successful in the Indian market, it is crucial for them to comprehend the cultural nuances and preferences of their target audience.
Smallholder farmers in India and the Western countries may share a few similarities including lack of infrastructure, facing adverse effects of climate change and market fluctuations. They both lack access to credit and have limited resources which makes them vulnerable to cost of production, but they belong to very different cultural backgrounds.
Indian smallholder farmers frequently use conventional farming techniques that have been handed down through the centuries. They place a high priority on community-based farming, where agriculture serves as both a means of subsistence and a way of life that is intricately entwined with their religious and social practices. Family and community are important factors in decision-making, and farming is frequently viewed as a family business where several generations coexist on farms.
Farmers in Western nations, on the other hand, are more likely to adopt cutting-edge, technologically advanced farming methods that are significantly affected by industrialized and marketoriented agriculture. They frequently act as independent business owners, basing their choices on market dynamics, academic research, and financial factors. Although family farming remains significant, it may not have the same cultural significance as it does in India, and they may place a greater emphasis on individualism and independence.
You have also come up with the concept of a biodigester carbon programme. How does this work and how does this help in achieving SDGs?
The primary objective of Sistema.bio is to enhance farmer livelihoods while fostering environmental sustainability. Since we are aware that farmers often possess limited resources, we are continually looking for novel methods to make our technology affordable for them.
New avenues for climate financing have recently opened up as a result of the global climate change movement. Businesses like ours can lower carbon emission on a massive scale by collaborating with foreign and Indian groups, making biodigesters more affordable to farmers who would not otherwise be able to afford them.
The widespread use of biogas by farmers significantly reduces carbon emissions in the atmosphere, aiding in the accomplishment of the 13th Sustainable Development Goal (SDG) of climate action. Additionally, it aids in the advancement of other SDGs like 1 - No Poverty, 2- Zero Hunger, 3- Good Health & Well-Being, 5- Gender Equality, 7- Affordable & Clean Energy, 8- Decent Work & Economic Growth, 14- Life Below Water, 15-Life on Land.
How do you foresee your innovative biogas technology enhancing agricultural productivity and enhancing farm sustainability?
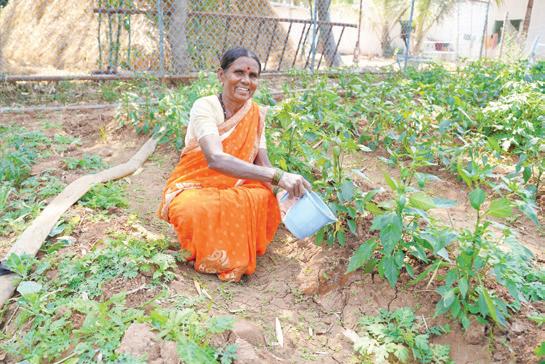
The use of biogas technology on farms could have a wide range of positive effects on sustainability and production. The anaerobic digestion of organic wastes like animal manure, agricultural byproducts, and food waste results in the production of biogas, a renewable energy source, as well as a fertilizer that is rich in nutrients and may be utilized to increase crop yields and soil health.
Farmers may power their farms with sustainable energy by using biogas technology, which reduces their dependency on fossil fuels and greenhouse gas emissions. Additionally, by using the anaerobic digestion process to create nutrient-rich fertilizer, one can increase soil quality and agricultural yields while lowering the demand for synthetic fertilizers and pesticides.
The implementation of contemporary biogas technology has the promise of increasing agricultural production and farm sustainability through the provision of renewable energy, improvement of soil health and crop yields, and decreased impact of agriculture on the environment.
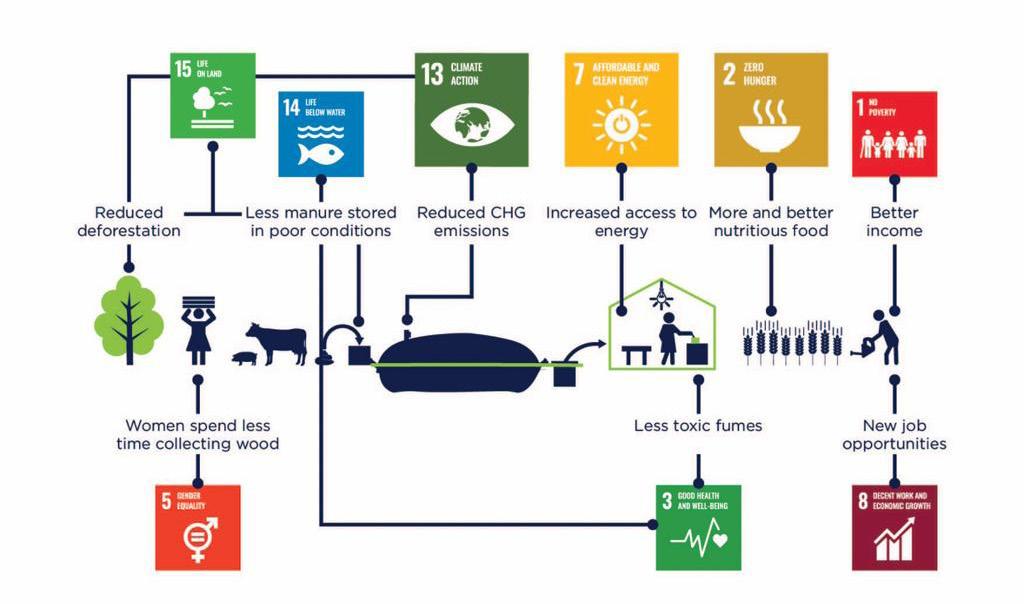
Do you foresee India achieving the ambitious target of Net Zero by
2070. What are the ways to achieve the same and how can corporations work towards realizing the goalpost?
India is definitely on the right track to achieve the Net Zero target by 2070. We need to adopt a number of steps to attain net-zero emissions by 2070, including raising the proportion of renewable energy in the energy mix, enhancing energy efficiency, encouraging sustainable agriculture and transportation, and lowering emissions from industry.
By adopting sustainable practices and reducing their carbon footprint, corporations can contribute to India's Net Zero target. Reducing waste and reusing resources can be achieved through investments in renewable energy sources, energy efficiency improvements, and the implementation of circular economy principles.
Companies that are unable to reduce their carbon footprint through conventional means should consider transforming their business operations by implementing innovative energy solutions. This can include adopting renewable energy sources such as solar, wind, or geothermal, or exploring new technologies such as carbon capture and storage, hydrogen fuel cells, or energy storage systems.
Implementing these innovative energy solutions can not only help industries reduce their carbon footprint but can also provide economic benefits, such as cost savings and increased energy efficiency. In many cases, these solutions can also enhance the resilience of business operations and provide a competitive advantage in the marketplace. Furthermore, corporations can work with the government to develop and implement policies and initiatives that support the transition to a lowcarbon economy.
Sistema.bio India is an Ashden Award winning social enterprise working in clean energy with innovative biogas technology. Within a span of 3 years, the company has over 200 people and is delivering thousands of digesters every month across 14 states in India. Based at the headquarters in Pune, Piyush started Sistema.bio India with a humble team of 22 people in the area of sales and technical operations with a pilot project in Gujarat.
Foreword
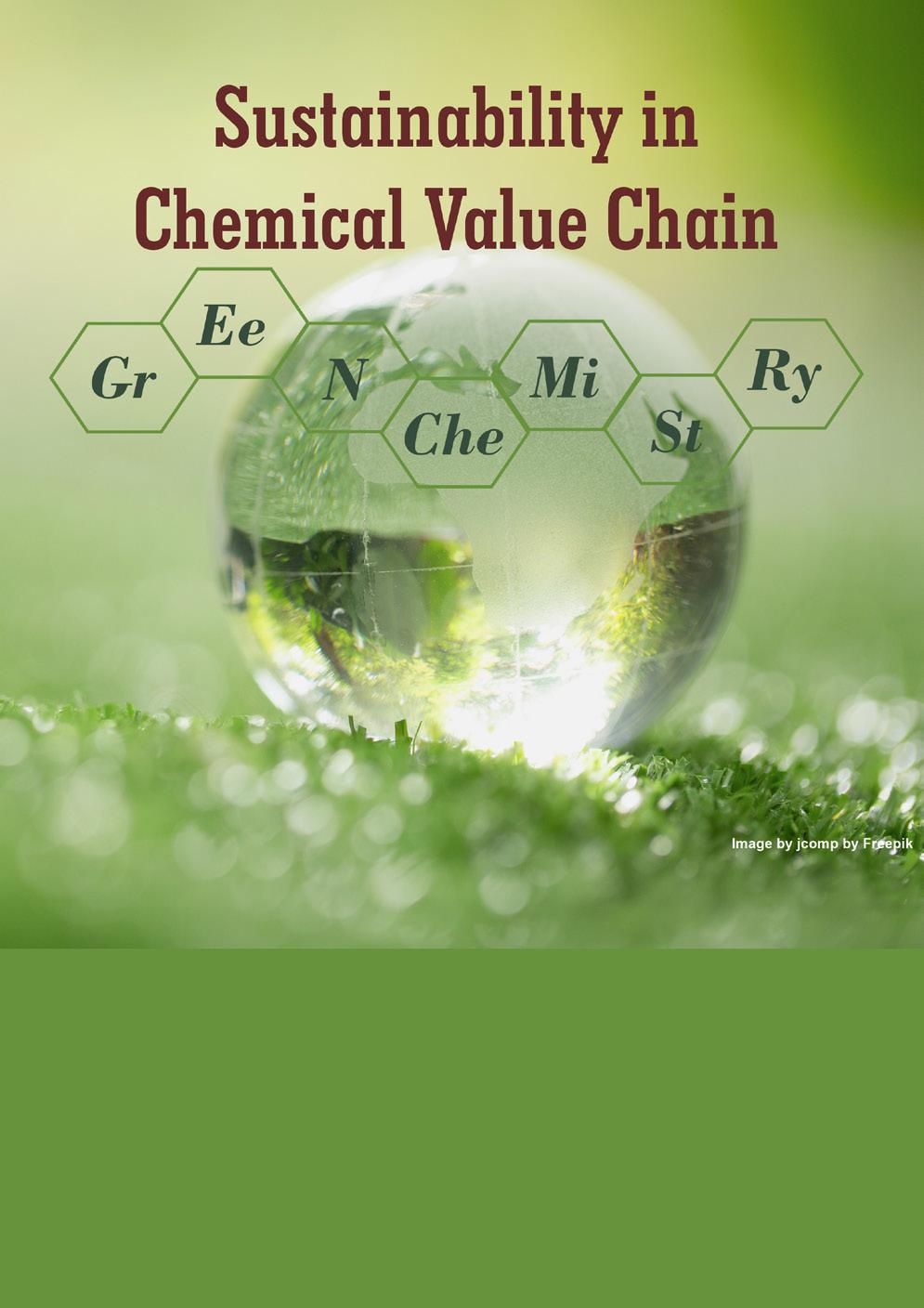
Mr. Shailesh Haribhakti, Board Chairman at some of the country’s most preeminent organisations, ESG (Environmental, Social, Governance) & IR (Integrated Reporting) Evangelist
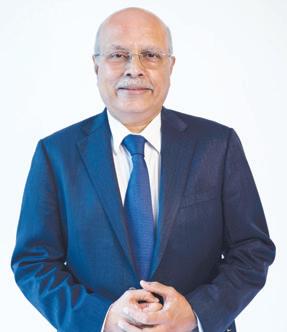
DECARBONISING the chemical industry is a crucial step in the global effort to combat climate change and build a more sustainable future. As one of the largest contributors to greenhouse gas emissions, the chemical industry must take bold action to reduce its carbon footprint and transition to more sustainable practices.
This opportunity arises from the urgent need to reduce greenhouse gas emissions and mitigate the adverse effects of climate change. Chemical companies can achieve this by embracing new technologies, getting closer to end markets, and working within and across value chains to deliver lower-carbon products and solutions. By doing so, they can capture additional value, create new business models, and potentially form entirely new markets in a more circular, lower-emissions economy.
Achieving net-zero emissions across the chemical value chain will require significant capital investment and business transformation, as well as new types of partnerships with key stakeholder groups. Chemical companies can make great strides in developing a circular economy by aggregating demand and supply for postconsumer waste, alternative fuels, and advanced recycled materials, among others, thereby eliminating fossil-based inputs and reducing emissions. Some of the other areas for chemistry-induced decarbonization are:
Chemistry will help us transform coal and water to hydrogen.
Hydrogen and oxygen after extraction will permit carbon to be safely sequestered.
Complete hydrogen, nuclear and geothermal transition will eliminate emission in energy generation altogether and we will draw down over half the carbon.
We can also unravel dumps and fills and release energy.
Recycling plastic in multiple cycles will eliminate need for new production.
Burning pelletised plastic in kilns will be highly recommended.
There are great opportunities for chemical and materials companies to become sustainability leaders and innovation leaders, creating low- and nocarbon products and helping ecosystem partners transition to lower emission solutions while driving long-term growth. Ultimately, the chemical industry has a three-pronged opportunity to lower its own emissions and downstream endmarket emissions, support sustainability targets, and create new value in a more sustainable global economy.
Research conducted by our firm - DialESG is summarized as below:
1. Figure 1 indicates the priority of actions to decarbonize the chemicals industry. These actions present an opportunity to optimize profits, driving value while lowering carbon footprint and enabling a circular economy.
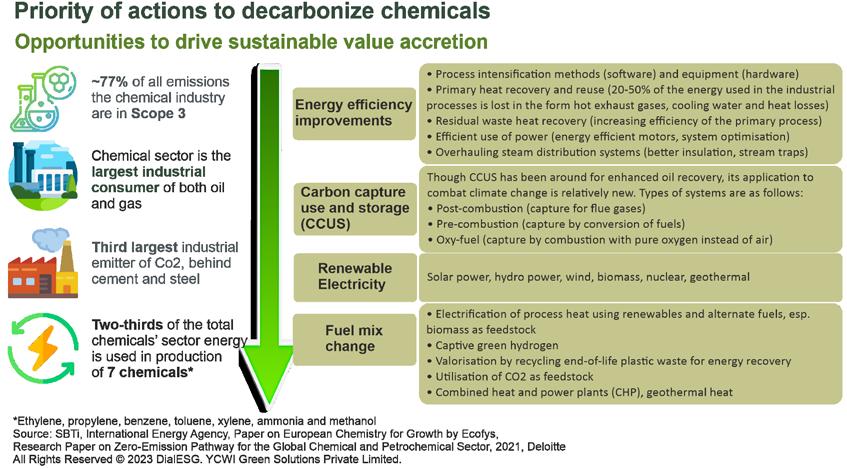
2. There are various sustainable chemicals that are helping several large end-markets to get on the path of a decarbonized transformation. Innovation-led “responsible chemistry” is addressing opportunities in several sectors, some of which include consumer, construction, transport, and electronics. Some of the end uses within these industries include sustainable packaging, end-of-life battery recycling, and robotics. Leading companies in the consumer goods industry target to cut emissions by 50% across operations by 2030.
At DialESG, we are 360 degree comprehensive one-stop ESG solution. In line with our motto “You Commit, We Implement”, we are committed to catalysing on-ground change to accelerate the journey to net positive.
According to McKinsey research, the India’s chemical industry has been a global outperformer in demand growth and shareholder wealth creation over the last decade. The country is set to be the fastest growing global demand centre for chemicals with domestic consumption projected to grow at a 9-10% CAGR in the coming years on the back of rising disposable incomes, a favourable demographic dividend, increasing global preference for biofriendly alternatives, and growing diversification of global chemical supply chains. While this is good news to rejoice, there’s another crucial story unfolding that is set to change the paradigms of chemical industry… it’s the forward-looking companies’ quest to ensure green expanse, which is backed by innovations in Green Chemistry including sustainable manufacturing, sustainable supply chains and sustainable products. Chemical companies that are embracing sustainable practices are building a resilient future to safeguard long-term business continuity as environmental regulations, such as mandatory zero liquid discharge, ‘net-zero’ emissions or carbon neutrality, grow increasingly stringent worldwide. Our Cover Story this time serves to be a great repository of insights from the industry leaders and subject-matter experts who are taking the Big First Step to lead fellow companies follow the Green Path and join the Global Agenda of creating a Green Chemistry…
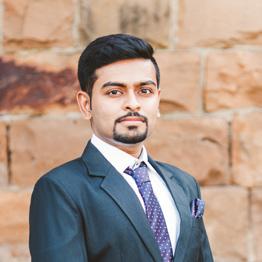
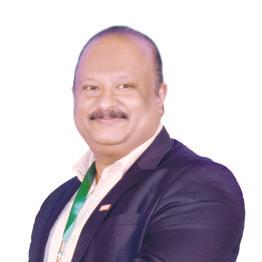
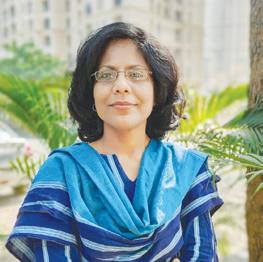
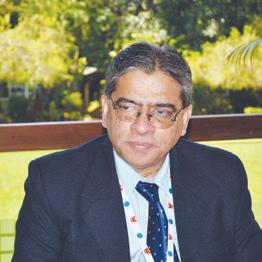
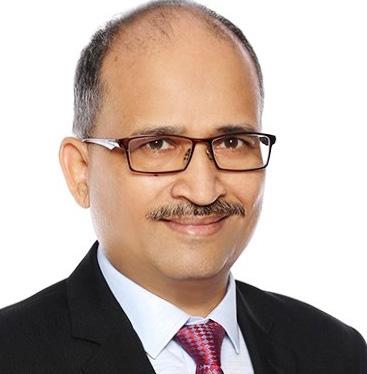
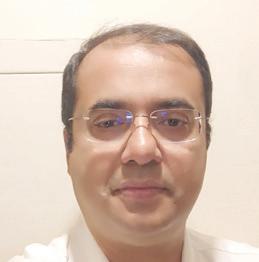
Arecent McKinsey study highlighted that India’s chemical industry has been a global outperformer in demand growth and shareholder wealth creation over the last decade. It now stands poised to play an increasingly dominant role across both consumption and manufacturing in the global arena. Over recent years, changing geopolitical scenarios have led to many countries focusing on domestic self-sufficiency and localized supply chains. However, benchmarking India’s manufacturing competitiveness reveals that India has a strong starting point vis-à-vis other key global chemical clusters that could translate into India becoming the next chemicals manufacturing hub.
While this is a great development, another McKinsey research shows that the chemicals sector alone contributes to 2% of the total global emissions and 1% of India emissions, which demands urgent attention from the stakeholders. Even within the industrials category, chemicals contribute to 7% of total greenhouse gases (GHG) released worldwide. Complex processes across the chemicals value chain are responsible for these high levels. Meanwhile, limited sustainable disposal options add to concerns ranging from incineration emissions to toxicity from non-biodegradable wastes.
Looking at this mounting concern, there is a growing focus on decarbonisation and recycling technologies in order to achieve climateneutrality goals and transition towards a circular economy. In line with this, PwC’s 23rd Annual Global CEO Survey revealed that 58% of the CEOs in the chemical industry were already planning investments focused on sustainability in 2019–20. This development underscores the significance of sustainability in the chemicals sector and its importance for value creation.
Some large chemical companies and chemical industry associations have gone past the mandatory regulations set forth by the government and are setting more standards for the management of chemicals and adoption of clean technologies (e.g. Responsible Care programme).
Dow India implemented the Responsible Care® program for its sites in 2005. Most Dow India sites have zero reportable injury or incident for more than a decade. The company has not only spearheaded industry collaborative platforms like Nicer Globe but is also persistently mentoring other chemical companies to implement Responsible Care codes. Sustainability is one of the strategic pillars of Dow.
Harnessing the innovation capability in collaboration with key customers is crucial for designing the next category of products that are far superior in performance and sustainability. Dr. AN Sreeram, Senior Vice President, Research & Development, and CTO for Dow, during a panel discussion, expressed, “Our world is changing so rapidly, we cannot precisely predict the future. The one constant, however, is that all humans are continually trying to make their lives and the world around us better and want to be able to do it safely and responsibly. What we can focus on is that products and solutions deliver differentiation and value for our customers, while using fewer resources and lowering collective and individual carbon footprint.”
By 2030, Dow envisions to reduce its net annual carbon emissions by 5 million metric tons versus its 2020 baseline (15% reduction). By 2050, Dow intends to be carbon neutral (Scopes 1+2+3 plus product benefits). By 2030, Dow will transform plastic waste and other forms of alternative feedstock to commercialize 3 million metric tons of circular and renewable solutions annually. To do this, Dow will expand its efforts to stop the waste by building industrial ecosystems to collect, reuse or recycle waste and expand its portfolio to meet rapidly growing demand. By 2035, Dow will close the loop by enabling 100% of Dow products sold into packaging applications to be reusable or recyclable.
Similarly, LANXESS announced the target to achieving a climate-neutral supply chain by 2050 – and only offer climate-neutral products from 2050 onwards.
“Sustainability is a key focus area and an increasingly important topic at LANXESS,” highlighted Neelanjan Banerjee, SVP | Global Business Unit Head – Lubricant Additives, LANXESS. “Not only do we have the right products in our portfolio to support our customers across applications and grow with them, but we also offer them more sustainable, more environmentally friendly alternatives. This makes us a frontrunner in the market.”
The company is introducing sustainable light-colour sulfur carriers within the Additin product family. The light sulfur-carriers are based on locally sourced renewable raw materials. They also meet the requirements of the “Lubricant Substance Classification”list (LuSC) – the prime reference for formulators of lubricants who intend to apply for the EU Ecolabel. EU Ecolabel lubricants are more eco-friendly alternatives to conventional lubricants, aiming to decrease the impact of these products on biodiversity, through respecting a wide scope of environmental criteria.
LANXESS created the Scopeblue label for products that either exhibit a sustainable raw material content of more than 50% or offer a carbon footprint of less than half that of their conventional counterparts. In accordance with the mass balance approach the products are chemically identical, i.e., new processes, tools or adaptions are not necessary.
With these as guiding thoughts, here we present to you the insightful opinions of industry veterans who have taken rapid strides in their sustainability journey and are successfully leaving a lasting imprint for others to follow…
India’s chemical industry is one of the top 5 industries in Asia and top 3 in ASEAN. How would you rate the quality of our chemicals companies’ value chain as compared to their parent companies in the Western World?
Arush Kishore, VP, Reliance Industries Ltd.: The Indian chemical industry carries a legacy of innovation. We have leverage in people, process over our counterparts in the western world and China. Adopting sustainable practises with our global counterparts offers us the opportunity to increase efficiency, which is hindered due to gaps such as in infrastructure, lower tech adoption and skills gap in India.
Biju Mathew – Director, Supply Chain Operations, BASF India Ltd.: There is a scope for improvement. However, the industry is moving in the right path towards sustainability. Indian Government is also supporting the same with policies & incentives. Chemical companies in India often face obstacles in feedstock availability due to lagging cracker capacity and low access to building blocks and key minerals.
Seema Mohanty, Global Supplier Manager (Associate General Manager) for Fungicides, Bayer India: It is an interconnected world today, and more so for our supply chains. For example, a chemical company in Europe may have its supplier base in India or other countries. So, the value chain of a company in Europe may comprise of companies based in various parts of the world. Therefore, I believe, we should not see companies as a standalone entity, but as a part of an ecosystem.
Now, coming to the chemical industry in India, it is highly encouraging to see the quantum of investments happening and earmarked for the sector. The industry is evolving and is in a very interesting growth trajectory. It is therefore very encouraging to see focus of top managements across major chemical companies in India towards plant and process safety and sustainability topics. Let us not forget that different companies are in different maturity levels in their journey towards safety and sustainability. However, as several big companies are pledging their net zero targets and working with their suppliers in different countries to address their own Scope 3 emissions, everyone is benefitting!
V Raju, Business Head & Sr VP – 3PL Contract Logistics, All Cargo Supply since the past five years. Production of certain chemicals has been significantly restricted by the various pollution control boards. Industries are unable to increase production to meet the demand. Over the past five years, there has been no capacity expansion by any of the companies because clearances are not given by PCBs. This has dented our exports which provides huge opportunities and, of late, is also impacting domestic industries, this has led to large scale imports from China. The domestic industry is simply unable to meet the demand due to policy bottlenecks. This is why Chinese manufacturers are hurting our industry.
Chain:
The chemicals industry is expected more than double and touch $300 billion by 2025 from $147 billion now. The chemical sector is expected to double to $300 billion by 2025, clocking an annual growth rate of 15-20%. To achieve this, the government is also working on a draft chemical policy that will focus on meeting the rising demand f0r chemicals and reduce imports. The industry is also targeting chemical exports of $28 billion by 2025 from $12 billion in FY17. The domestic chemical industry is the third largest in Asia and seventh in the world.
One of the reasons for slower chemical industry growth are the norms of pollution control board,
We need to go into the direction of an integrated steering of global supply chains in times when supply chains are becoming even more complex each day. We need to deploy smart business solutions and digitalization to gain business and focus on customers and process orientation according to business needs (resilience and responsiveness). Industry 4.0 must go together with logistics 4.0. Regarding data, shippers must think outside the box — that is ‘think beyond the factory gate’ to realize the true potential. The sooner we receive relevant information, the faster we can react. In our experience, customers for logistics services are most successful when they analyse processes together with their logistics partners and, in consequence, can take the right strategic decisions. We try to receive information about planned shipments as early as possible; this allows us to align our expertise with the customers’ information in the best way possible.
Source: McKinsey & Co.
Sanjay Desai, Co-founder & Regional Director, Humana International (S)
Pte Ltd.: Indian chemical sector is an essential centrepiece of modern Indian economies, touching everyday life via many other industrial products. Chemical sector is increasingly under pressure for its large environmental footprint, a heavy user of oil/ gas, and other energy resources, emitting gigatons of greenhouse gases each year.
Two major initiatives by the Government, ‘Make in India’ and ‘AatmaNirbhar Bharat’, are aptly designed for the chemicals & Oil/Gas petrochemicals sector to flourish. The industry needs to build ecosystem – this entails the creation of Petroleum, Chemicals and Petrochemicals Investment Regions (PCPIRs) across all four corners of the country. It will enhance infrastructure linkages for a hub-and-spoke model and finally, integrating value chains using initiatives like multi-modal parks throughout the country.
India’s attractiveness as a chemical manufacturer has been rising because of its ability to build manufacturing ecosystem at less cost than in the developed world. Many Indian specialty chemical organisations have developed distinctive capabilities and established supply chain networks with global organisations. While our standards are not the best or world-class, we are making progress and quality improvements each year, especially after the Covid aftermath.
Supply chains have a greater role to play in ensuring sustainability in chemical industry. How are you addressing the same? How do you think the industry players are dealing with it?
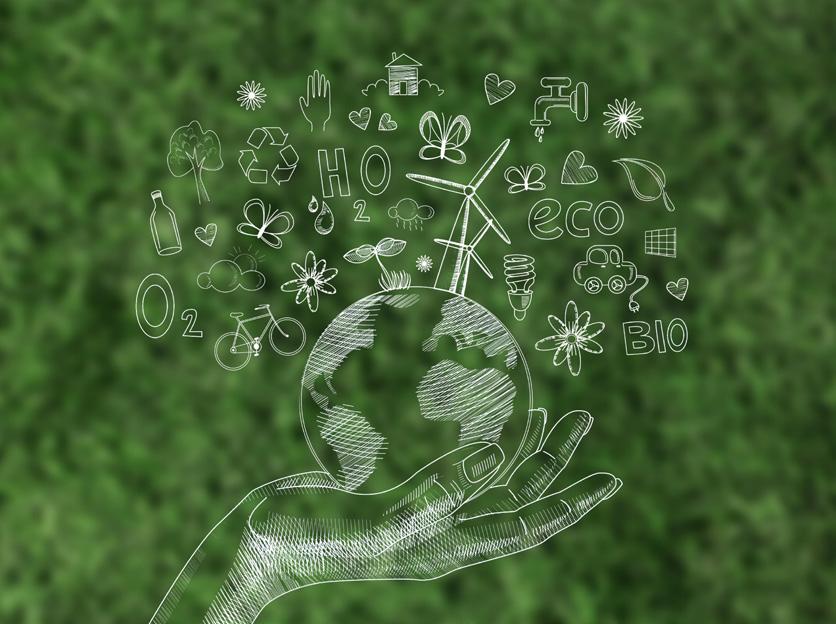
Arush Kishore: We are identifying both near-term and long-term projects to implement sustainable practises, especially in logistics, stakeholder management, process improvement and technology upgrade. We are looking for the best sustainable practises across industries and developing new solutions in our area. We have our R&D initiatives in place, which is helping us develop newage technology. We are putting in place a monitoring system to ensure reliable implementation.
Biju Mathew: Supply chain plays a major role in sustainability throughout the value chain of chemical industry –starting from sustainable procurement of raw materials (renewable raw materials or RMs manufactured by taking Zero Carbon emissions into consideration), sustainable transportation of RMs and efficient processes to manufacture finished goods which addresses the Net Zero Carbon Emissions concept and finally recycling of products, wherever possible (e.g.: Plastics).
BASF has taken a systems approach to align suppliers’ interests with environmental, social and governance objectives, with a clear assessment process to earn ongoing business. One such example is Together for Sustainability –an initiative created by leading chemical companies including BASF and the India chapter was launched in 2016. Suppliers selling to TfS member companies are subjected to rigorous assessments that often go beyond compliance with local law. The TfS motto is “an audit for one is an audit for all.” In practice this means that when a supplier undertakes an audit, the results are posted on a secure database and made available to all TfS member companies. All parties save time and money. Companies which do not meet the standards are given support to improve.
Seema Mohanty: That is true! Supply Chain and Procurement have a lot of interfaces, both within the company and to the external world. That brings in possibilities towards sustainability initiatives across multiple fronts. Let us see some examples:
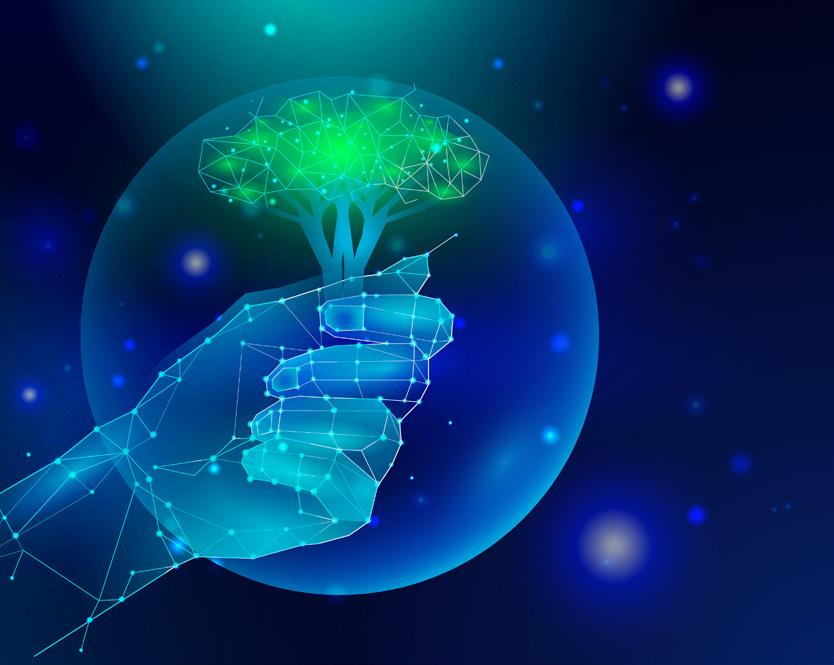
Sourcing: One can choose the right suppliers, i.e., those who adhere and strive towards sustainability (by taking various measures like adhering to human rights, trying to reduce energy consumption, transitioning towards renewable energy, moving towards less waste generation, etc. Sourcing teams can work with technical teams to evaluate if a more environmentally friendly material can be used, etc.
Transportation (Road): Avoiding partially loaded trucks.
Transportation (Sea): Using double stacked containers wherever possible, instead of single stacked. There is no point in paying to transport air in the free space in single stacked containers.
Mitesh Gangar, Head - Business & Supply Chain (Commercial), Aarti Industries: We are recycling Packaging Material – where possible, drums and jumbo bags are being recycled. We are minimizing waste by ensuring dedicated tankers for liquid products (thus avoiding cleaning cycles) and also attempting milk-runs wherever possible.
V Raju: The supply chain and warehouse system in chemical industry are on the verge of adopting the latest technologies and using different software innovations to sustain well in the market to operate effectively and in a full-fledged way. Sustainable operations are easy to access as it is simple to go through all the processes in a quick way to catch the customer’s eyes. The e-commerce business model is quite a trend in productively managing the manufacturing industries, chemical warehouses, and supply chain operations in plants. It also helps keep track of the inventory, logistics, and product shipping in real-time delivery at the correct address. The business owner uses the newest software or technologies to manage the work accordingly to serve the purpose. The latest technologies or trends that make it more worthy are listed to fetch the customer’s attention in the broader term. Example of easier usage of sustainability process can always commence in industries from the procurement process implemented in the factory. This will always be supported by sustainability initiatives in the supply chain operations, be it warehouse or distribution functions.
Sanjay Desai: The chemical industry, in general, has always been at the forefront to rising global concerns, like climate change, GHG emissions and the energy crisis. It can help create a pathway to a sustainable future by developing ecofriendly products using green resources and resource- efficient technologies. It is evident in last 3-4 years more than ever before. This shift towards sustainability requires the adoption of circular business models, use of renewable feedstocks and a defined process to reuse & recycle endof-life products. Companies leveraging such opportunities will have considerable growth prospects and the option to reposition themselves in new business ecosystems. Most chemical organisation in India try to follow / comply principles of Responsible Care including REACH Certification. Their broader objectives are to drive sustainability in their value chain operations. A few critical/ major elements of these are:
Adapt and institutionalise sustainable framework across end-to-end value chain
Engage stakeholders 100% from beginning for alignment on common outcomes
Priorities materials Issues which affect EHS / customers and employees
Integrate sustainability in your core business models as top priority
Measure, monitor, report, improve and remunerate
How will you describe Covid’s impacts to Supply Chain globally? Do you see a change in the way supply chains are being demystified?
Arush Kishore: Supply chain has become the key discussion point after Covid-19 across organizations. Reliability of supply chain with disruption handling capacity is taking up as much mind space as the financial indicators of the organization. Every organization is trying to maintain agility in supply chain planning without a higher width of error cushions to handle disruptions. Beyond a point, one can’t plan or provision for disruptions as it becomes prohibitive. The people, process, platforms play is being figured out by each organization as is optimum for it.
Biju Mathew: The advent of Covid-19 significantly impacted supply chains globally as it disrupted operations, causing shortages, delays, and in some cases shutdowns. It exposed the weaknesses and vulnerabilities in the supply chain and pushed further the need for building resilient and agile supply chains that can adapt quickly to changing conditions. We see many organizations are now adopting new supply chain approaches such as diversifying the supplier base, focusing on risk management, optimize inventories, and investing in digital technologies to enhance visibility and respond faster to changing conditions.
Seema Mohanty: Covid brought in a lot of focus and ‘glamor’ into supply chain functions. The initial phase of Covid and lockdowns required supply chain functions to deal with a lot of unknown unknowns. While people were talking about work from home, supply chains were moving goods physically across continents. Securing supplies, in spite of all odds, were a primary focus. As Covid situation started to get better, supply chains were impacted by geopolitical tensions and shipping constraints to name a few. All these bring home the fact that since there is a lot of interconnectedness, our supply chains will be prone to impacts from various factors every now and then. In this context, chemical supply chains are taking various steps to be more prepared for any event, whatsoever. Initiatives are being taken by various companies to have more backward integration, to source locally or to source from multiple geographies in order to reduce the risk of getting impacted. But there is no one solution. Only those who are agile enough to keep up with changing situations, will be the ones to survive. Risk management measures will play a vital role. Being resilient is the key.
Mitesh Gangar: Covid caused substantial disruption in supply chain globally and for a short while, people moved from ‘Just-in-time’ to ‘Just-in-case’. All the disruptions are now stabilized and there is a move to rationalize inventories. We see a lot of digitalization of processes, be it with transporters or shipping lines or customs departments. There is a definite move towards making transactions paperless and having a single source of truth.
Sanjay Desai: In sheer $ terms, global economies would have lost close to 9.0 trillion USD since Feb-2020. While the global trade is recovering fast, Covid-19 impacts across specific goods, services and trade partners are highly diverse, creating pressures on global supply chains. Covid-19 forced organisations globally to re-think/ re-design their end-to-end value chain strategy. It forced them to develop new sources of multiple suppliers/manufacturers in different countries in order to be resilient to shocks, volatile demand & supply variations. Many industries hastened their e-commerce and omni-channel supply chain models way ahead of its time, into true unified people process and technology integration. Organisations were scrambling to implement control tower visibility to manage the risks upfront in the value chain by making use of AI and ML technology. Covid-19 also created a renewed focus to integrate ESG objectives with each functional vertical accessing ESG data into their reporting. While Covid-19 was a global catastrophic disaster, it brough in a few positives –blessings in disguise!
What are the challenges of decarbonising supply chains?
Seema Mohanty: Let us keep aside the cost aspect and look at the other potential challenges. Scope 1 and Scope 2 emissions pertain to one’s own operations, so they are comparatively easier to collect data and monitor improvements. However, unless one is following Science-Based emissions and reduction targets, there is no uniform way of measuring and reporting Scope 1 and Scope 2 emissions as well. Real challenge comes when we speak about Scope 3 emissions. This is because there are several tiers of suppliers, perhaps in different countries, and with their respective maturity levels in their own sustainability journey.
Oftentimes it is important to work together with some of the key Scope 3 suppliers to bring them up to speed in their target setting and in taking actions. Collaboration, knowledge sharing and learning from one another is the key. Another important challenge is about Intellectual Property (IP) protection. It is important to find out ways to ensure IP protection, while we, at the same time, encourage suppliers to be transparent and share data.
We must remember that Environmental, Social and Governance (ESG) reporting is a pretty new phenomenon and is still evolving. So, there is no one way of reporting and consolidation of data yet. This is a challenge especially when one works across data of several suppliers. It is a journey we all are taking. There is no playbook to guide us yet. But we will all learn along the way!
In your opinion, is it practical to achieve the importance of ‘Net Zero’ pledge and how critical it will be for the organisations to manage their Scope 3 emissions?
Arush Kishore: Net Zero Pledge offers us to look at our entire value chain in a holistic way with the aim of standardisation of practises, development and upgrade of regulatory and policy mechanisms, and technical advancement. Reliance has committed to being ‘Net Zero’ by 2035, with a focus on new energy, new mobility, and new connectivity. For us, all types of emissions carry equal weight. All partners are also adopting sustainable practises with a focus on emission control.
Biju Mathew: Addressing climate change is the greatest challenge of this Century and we, at BASF, standby this challenge. Achieving Net Zero emissions is a critical goal for organizations to address climate change, and BASF has set a target to achieve Net Zero emissions by 2050. To achieve this goal, it is important for organizations to manage their Scope 3 emissions, which refer to emissions that occur outside of an organization's direct control. While it can be challenging, it is practical to achieve this goal with the right strategies and technologies in place. Managing Scope 3 emissions is especially important for companies, as these emissions often account for a sizeable portion of their carbon footprint.
While BASF is continuously working to achieve Net Zero CO2 emissions by 2050, more customers are making environmentally conscious purchasing decisions. At the same time, we are working intensively to significantly reduce the carbon footprint of our production and thus of our products. Strategies that companies can adopt to manage their Scope 3 emissions include switching to non-fossil feedstock, engaging with suppliers to promote sustainable practices and reduce emissions throughout the supply chain & developing circular economy program.
Seema Mohanty: I would rather say Net Zero is no longer a choice. It has become imperative. Sooner than later, every organization and every government have to take this pledge and work towards it. This will be a step in the right direction to tackle climate change. In this context, for companies, managing their Scope 3 (both upstream and downstream) emissions become key. Data shows that Scope 3 emissions constitute the significant part of emissions by a company, actual range varying as per the industry one is in of course. Let me here focus on the upstream part only, i.e., the emissions which are coming from one’s suppliers and their suppliers and so on. It is a complete chain. One cannot just focus on their own operations and stop there. One has to look beyond. And that is when the magic happens. All this brings in its own set of challenges but opens up numerous opportunities as well. It is all about collaboration, transparency, and interdependence. One cannot achieve their net zero target unless their suppliers are also striving towards it and sharing their data.
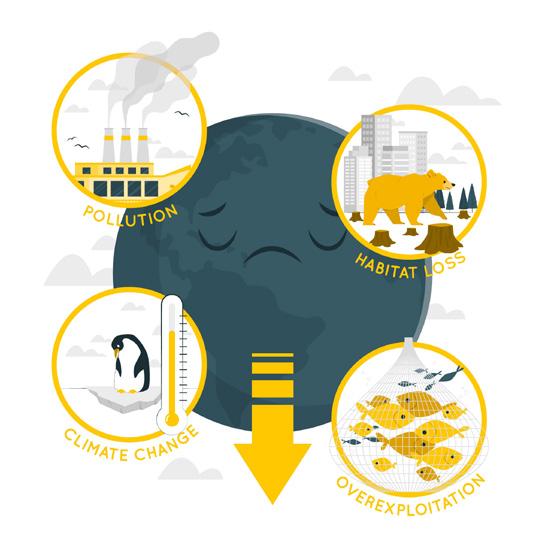
Mitesh Gangar: As a chemical intermediates company, we are net producers of carbon based chemicals, so Net Zero needs to be redefined for context. As a company, we will be declaring SBTi-based targets by the end of this year. Given that Supply Chains have become global, >60-70% of the emissions will come from Scope 3 and increased engagement with the entire supply chain network will be crucial.
Sanjay Desai: Climate change has been a challenge for last decade and it would remain the same for next 10 years. In order to tackle the Net Zero emission, each of us including governments, communities, organisations need to work together and achieve GHG emission to drop half by 2030 and then to Zero in 2050. What it means, is carbon dioxide (CO2) emissions need to drop by 50% from where we are today in 2023. There is no room for negotiation in these objectives.
This is an incredibly daunting task, especially for organizations to address carbon emission outside of their own scope called ‘The Scope 3 emissions’. Controlling Scope 3 emissions is very difficult as these are caused by our service providers within the entire value chain. Organizations need to collect the right data from their suppliers, vendors, service providers to engrain sustainability cadence in their financial & operational processes. Organizations need to set right expectations from their partners/suppliers regarding outcomes of their actions. Organizations need to communicate Science-based carbon emissions targets to their partners / suppliers, which should be monitored regularly by the leadership team.
What are the key initiatives taken by your company in empowering sustainability in the entire value chain and specially supply chain?
Arush Kishore: We shifted to new recyclable packaging material and reusable plastic pallets instead of wooden pallets in our warehousing operations. Switching to BS-VI vehicles and looking to adopt new-age fuels such as LPG, hydrogen, and electricity are our main targets to manage GHG emissions. We have established a driver training institute, a tech-based emergency response programme, and a vehicle health assurance programme, considering the hazardous nature of the products. We have digitalized and automated our procedures. These are the classic elimination, substitution, and control strategies. Still, there is a lot of scope for improvement, but we are committed to implementing, upgrading, and enabling our operations for sustainability, as we have demonstrated that it enhances efficiency.
Biju Mathew: Sustainability is clearly integrated in not only BASF’s purpose and vision – i.e.: ‘We Create Chemistry for a Sustainable Future’, but also in our business strategies as well. Some of the areas where we are paying special emphasis on the topic include:
Increasing usage of low/zero carbon transportation
Transition from fossil fuels to renewable fuels for captive energy demand
Measure and track carbon footprint across the value chain
Scale up recycling of materials and maximize circularity across the value chains
Engaging with suppliers (Materials & Services) to promote sustainability and reduce emissions throughout the supply chain.
Mitesh Gangar: We have been Responsible Care certified and have received a Gold Rating under Ecovadis in 2022. We have also been rated high (90%+ scores in all sites) wrt. the ‘Together for Sustainability’ audits. We have created a centralized Logistics Control room to monitor all road vehicle movement and share alerts with drivers, transport partners and have support available within a 50 km radius for all key transport routes. We regularly train driver partners on the various chemicals, hazards, and good practices.
V Raju: As warehouse service providers to good number of chemical companies in the country, we ensure that we are able to ensure that the following sustainability measures are initiated in our warehouses pan-India in different locations:
Utilization of EV for distribution in many of our warehouses
Implement solar panels in many of our warehouses across the country
LED lights in the warehouses
Packing material as part of valueadded services used are from recycled material
Green logistics in our warehouses
Sewage treatment plants
Digitization of warehouse operations processes
Not allow vehicles to run on idling engines
Promote green plantation in available open areas in and around warehouses
What are the current best practices of a sustainable supply chain in the chemical industry in India being followed by the client as well as the ecosystem of their 3PL Partners?
Arush Kishore: Empowerment of our business partners is paramount for us at Reliance. We have collaborated with industry experts for knowledge sharing initiatives and developing supportive institutions. Journey management is one of our key initiatives to adopt best practises with our 3PL partners. With the enablement of vehicle tracking systems and driver training institutions, we are able to reduce violations and major incidents. We have trained around
21,000 drivers in the last five years for defensive driving. We do considerable heavy lifting in capability enhancement of our associates.
Biju Mathew: BASF is already a frontrunner in offering customers a portfolio of products with lower carbon footprints to enable their decarbonization and we believe in assuming responsibility along the entire value chain. We continue to work towards reducing greenhouse gas emissions from our business activities – in our own production and, together with our partners, along the value chain. We calculate carbon footprints for around 45,000 sales products to increase carbon transparency for our customers. These Product Carbon Footprints (PCF) include all product-related greenhouse gas emissions generated until a BASF product leaves the factory gates (‘Cradleto-Gate’). The extraction of the raw materials we require and the production of purchased precursors account for the largest share of the PCF. We currently use industrial averages and values from commercial databases as the basis for calculating these upstream emissions. In 2021, we introduced a global Supplier CO2 Management Program to create transparency and better steer and, in the long term, reduce upstream emissions. In a first step, we ask our suppliers to provide PCFs for our raw materials. We support them by sharing our knowledge of evaluation and calculation methods. In this way, we are also contributing to the standardization of PCF calculation. In a second step, we want to work with our suppliers on solutions to reduce productrelated emissions and establish the PCF as a criterion for our purchasing decisions. We are also encouraging the adoption of low / zero carbon transportation.
Sanjay Desai: The push for greater sustainability in chemicals industry is far more than financial or compliance exercise. It is creating new opportunities for chemical producers to sell green products into differentiated markets. There are many best practices that chemical sector is deploying. Major ones are:
Renewed focus on business model innovation,
Collaborative engagement with supplier /partners through the entire value chain
Technology enabled procure-to-pay excellence supported by operational execution,
Circular product and service design with focus on re-use / reduce wastages,
Strategic customer engagement to understand their expectations on delivery and
Focused investment strategy beyond $ encompassing ESG reporting into financial performance.
How important is the role of emerging technologies in positioning organisations to achieve their sustainable goals in the next 2-3 years? Can you elaborate a couple of Key Technologies that would be facilitating the change?
Arush Kishore: Digitalization, energy transition to renewables, energy storage facilities, new mobility, and a circular economy will make a huge difference in achieving sustainability goals. New Connectivity is helping organisations optimise their output and manage risk. Its role will be essential to the operation's goal. A stupendous access to speedy information highway, at all places and all times, is just around the corner. We are not ready for it.
Biju Mathew: Emerging technologies are critical for the organizations to achieve sustainable goals. For instance, i) development in product technologies can help the organizations to switch to non-fossil feedstock like bio-based feedstock or recycling based feedstock. Such technologies avoid fossil resource consumption and enables CO2 reduction through a gradual transition in existing assets ii) Adoption of renewable energy source like solar and wind power iii) Digital technologies like artificial intelligence, machine learning, blockchain and automation are enabling organizations to improve supply chain transparency, especially in measuring the product carbon footprint, reducing waste and optimizing operations.
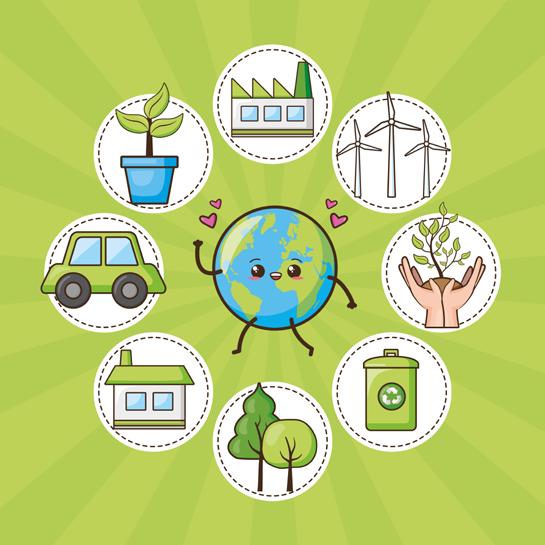
Seema Mohanty: We are all talking about sustainability, decarbonization, carbon neutrality, Net Zero, etc. If we delve a little deeper, all these involve a lot about collecting data, interpreting the data, benchmarking the data, setting actionable targets with the help of data and keep repeating the above steps to monitor improvements. And all the above are across various processes, initiatives, products, suppliers, timelines, etc. As one can imagine, it is not practical enough to do all this manually. This is where technology comes into play –to simplify data collection, validation, interpretation, and monitoring. Technology is the backbone for implementing decarbonization programs at scale. The technology landscape is also evolving as we all are in a learning trajectory of what works well and what does not!
V Raju: A recent PwC study found that chemicals companies plan to invest 5% of annual revenues on digitization over the next five years and nearly a third of them reported having already reached an advanced level of digitization. These initiatives can produce near-term benefits across three primary business dimensions: operations, customerfacing, and organizational. In operations, the application of digital technologies to functions such as maintenance is already improving plant and network performance and minimizing downtime, reducing operating costs by 2-10%. But there are greater savings to be had. By using digitization to integrate business and manufacturing systems, optimize production footprints, and redesign processes, chemicals companies can capture gains of up to 25% in capacity utilization. Chemical companies have long struggled to make the shift from ‘product sellers’ to ‘solution providers’ in the customer-facing aspect of their business. Digitization can make a big difference in this regard. For example, with an application in the paper chemicals segment, suppliers are using sensors and other digital technologies to track how their products are integrated into their customers’ operations; in turn, this enables chemical companies to improve their products based on utilization patterns and enhance their ability to proactively address customer needs. Among the results for chemicals firms, are stickier customer relationships, a greater share of customer budgets, and the potential for increased revenue based on provable performance metrics. Advances in machine learning offer chemical companies a valuable opportunity to do more with fewer people and effectively lower the cost of running the business. Moreover, greater processing power and decision-support systems enabled by artificial intelligence can help reduce organization layers and create a more efficient and potentially innovative operation, in essence, removing traditional centralized spans of management hierarchy and replacing them with more localized control.
Warehouse technology is an effective, sustainable, and cost-efficient solution to addressing the challenges of the warehouse. Especially now, when the market is transitioning to e-commerce platforms that are accessible and open 24/7/365, it is becoming increasingly crucial to move warehouses from relying too heavily on costly human labor and into a more automated and technologyfocused operation – a transition called ‘Warehouse Digitalization’.
Sanjay Desai: Digitization is the new currency that is transforming the face of manufacturing processes across chemicals industries. Advance analytics and machine learning have changed the picture of research and development in the chemical sector. Using high-throughput optimization, chemical companies are able to create and modify molecules that have more useful properties. Additionally, they will be able to imitate tests using advanced analytic tools and techniques, employ predictive ability to progressively improve formulations for quality and profitability. Further, technologies like Internet of Things (IoT), cloud computing, analytics, are bringing a complete overhaul in operations.
How do you foresee the sustainability dynamics taking centre stage in chemical supply chain? How are chemical companies poised to play a catalytic role in this journey?
Arush Kishore: Covid-19 has already placed sustainability on the central stage. Two important stakeholders – customers and investors – have already differentiated themselves based on the sustainable practices. Industry all together is shifting in the direction of Sustainability. Investor and customers both are looking for value in sustainability efforts across industries. With the new-found focus on ESG investing, stakeholders are looking at chemical companies to create value addition from these activities to become an attractive option. Sustainable practices are under discussion at every forum available starting from board meetings to knowledge sharing sessions. I will give you an example of the PET recycling facility at Reliance. Being one of the largest producers of PET, we aim to recycle 5 billion PET bottles in our plants. This is one example of a sustainable practise that supports environment while adding monetary value. In the upcoming future, we will see a lot of such innovations in the chemical industry.
Biju Mathew: In many areas, products and innovations based on chemistry are the key to a climate-neutral future.
V Raju: Sustainability in supply chain demonstrated by chemical companies that operate with concern for natural and human resources—can mean increased customer loyalty. Incorporating green logistics into chemical warehousing as part of the supply chain can also yield better business productivity and improve a business’s bottom line. In global supply chains, chemical warehouses produce environmental pollution mostly from heating, cooling, and lighting. Generally, the bigger the warehouse, the larger the carbon footprint. Warehouse managers can measure the carbon footprint of their operations by considering key performance indicators: emissions, natural resource use, and amount of waste and recycling. Studying total carbon dioxide emissions, as well as energy consumption, water consumption, and rate of product or material use, will reveal areas where companies can apply green initiatives.
For example, a chemical warehouse with a high electricity bill might discover that alternative lighting sources— like natural light, automatic lights, or other renewable energy options—offer savings. Likewise, the discovery that a warehouse consumes large quantities of water from a natural source might inspire change. By installing water flow reduction mechanisms or a rainwater capture system, warehouses can reduce, offset, or optimize water use.
Sanjay Desai: The Indian chemicals market is expected to reach $8501,000Bn by 2040, comprising a 10-12% share of the global market. The last few years of disruption has hastened the transformation for the chemical industry. It has become critical for companies to address supply chain vulnerabilities, while addressing the imperative for Decarbonization, ESG and Agile Resiliency. While companies have built procurement and analytics capabilities to better monitor and manage raw material prices, customer demand volatility. However, inflation in energy prices is putting their competitiveness in the international market at risk. The most effective protection will come from creating a capability that integrates margin management around sourcing, risk management, pricing, and product and technology development. To succeed in 2023 and beyond, Indian chemical companies must build resilience, accelerate investments in new and greener technologies, hasten M&A across industry and develop margin management as core mindset.
How can 3PL companies and service providers add value in the sustainability journey of chemical companies and bring difference?
V Raju: Implementation of digitization in various warehouse operations enabling optimization of manual processes and better usage of available resources at warehouses, use techniques like AI, IO, Analytics, WMS, TMS and various other robotics at warehouse level, will help in improving the productivity and efficiency in the operations, in turn facilitating the sustainability journey of chemical companies. Planning and scheduling the deliveries to customers can be done better with judicious usage of the various software systems, totally avoiding the use of paper receipts or manual deployment of personnel. Energy conservation techniques help reduce energy consumption at storage locations. Following initiatives can further add value to sustainability journey of the chemical company as well:
Our chemical warehouses and facilities have rainwater harvesting and waste-water management systems to collect rainwater, store it and use it effectively.
During monsoons, excess surface water is percolated through percolation wells and ground water recharge wells to increase ground water levels.
Paver blocks used in parking zones of facilities to facilitate the percolation of water into the ground during monsoons.
Reusing resources at supply chain and storage facilities: Environmentfriendly blocks made of fly ash are used for construction. Fly ash is residual waste generated in power plants. These bricks reduce environmental burden and are more sustainable.
We are moving from using wooden pallets to wrought iron or steel pallets that are stronger, more longlasting and can be reused effectively.