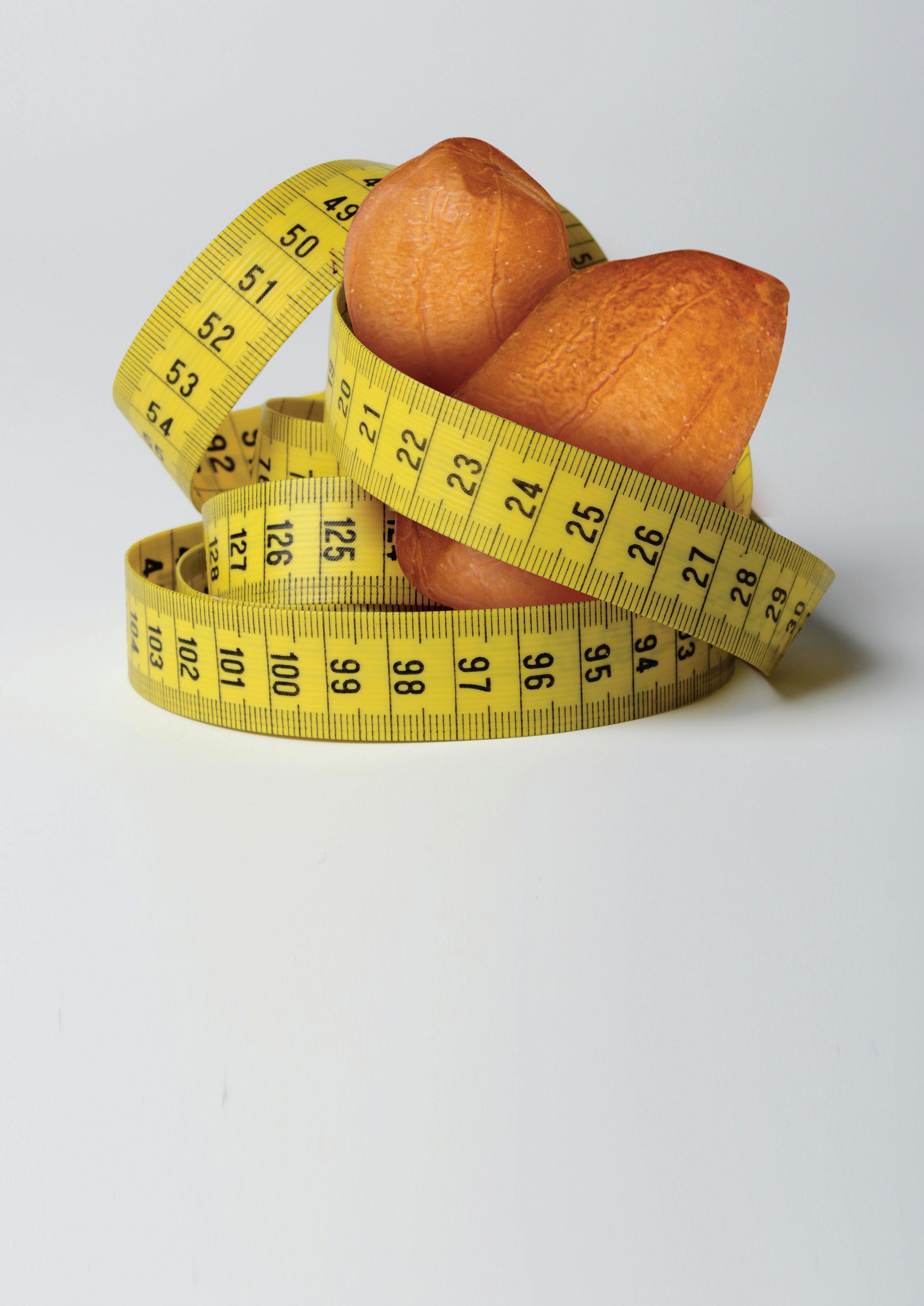
3 minute read
Final Sizing: Preparing Peanuts for Delivery
In previous editions of World Peanut Magazine we covered the many steps the peanuts go through in the processing plant: drying, storage, cleaning, shelling, gravities and stoners, and color/laser sorting . Once all that is done, the peanuts are ready for the last industrial process before packing: final sizing. The kernels are now sound and free of foreign material; the next step is to classify them by size in order to achieve the commercial specifications – or grades – desired.
There are essentially three attributes involved in sizing: size itself (big –small), shape (round – long) and density (higher – lower density).
According to the established world trade practices in peanuts, size can be determined essentially in three ways:
1. Sizing based on screens, where each commercial size is defined by specifying the screens (usually designated in 1/64 of inches or 0.5 milimeters) used to produced it. The screen may determine both size and shape.
2. Sizing based on count, where each commercial size is defined as per the number of kernels in one ounce of peanuts. The relevant variables in this case are size and density.
3. For specific usage, a count distribution requirement can be added to the previous two counting methods, limiting the percentage of big and small kernels to a maximum. In this case all attributes of size, density and shape can be considered.
An example of sizing standard is the one proposed by the American Peanut Shellers Association. See the table on pages 24-25 for the standards set for the runner variety.
Screen types
Available screen types in the market can be classified as follows:
1. Screens with round holes
2. Screens with slotted holes
3. Wired screens
Wired screens usually have a higher opening ratio and are mainly used for removing dust and powder. Slotted screens are used for peanut kernel sizing and also to separate splits (peanuts halves) from wholes. Round holes screen concentrates of shapes as well as sizes; they are used, for example, to remove small round peanut kernels from splits.
These screen types can be found as a flat metal screen (as in pics. 1,2 and 3) or as a rolled metal screen 4
Sizing methods
Different equipment can activate the screens in different ways to achieve the kernel separation.
1. Flat machines use different configurations, with an inclined deck with an angle that ranges from 6 to 12°. The product is fed at the higher end and flows down in two ways:
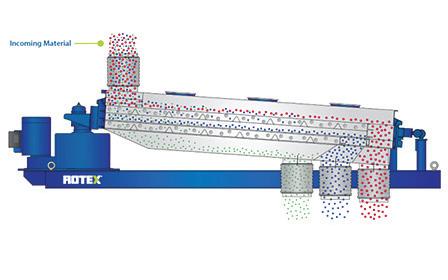

A. SHAKING MOVEMENT: Screens are moved by an eccentric shaft describing an ellipse on the vertical plane, moving the product down. 5
B. ROTATING MOVEMENT: Screens are moved by an eccentric shaft describing an ellipse on the horizontal plane, moving the product down. 6
2. Cylindrical screen machines use a different configuration: the cylindrical screen rotates with an inclination. The product is fed at the higher end and flows down by gravity in contact with the screen.
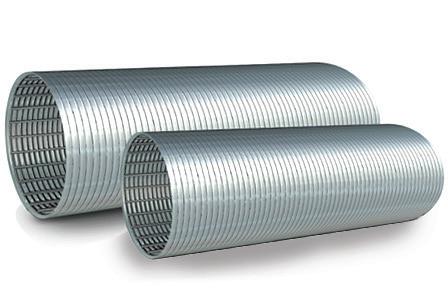
Sizing strategy
After all, peanuts come from mother nature, therefore variability from season to season, as well as from variety to variety, and from farm to farm, is wide. Accordingly, shellers must adjust the size of screen holes/slots to account for this variability and achieve their customers’ requirements.
Grade Standard Tolerances
Section 1. Jumbo Runner. Jumbo Runner consists of shelled Runner type peanut kernels of similar varietal characteristics which are whole and free from foreign material, damage, and minor defects, and which will either meet an average of 38-42 count per ounce or which will not pass through a screen having 21/64 x 3/4 inch openings.
(1) 1.00 percent for other types of peanuts; (2) 5.00 percent for sound peanuts which are split or broken; (3) 3.50 percent for damage and minor defects combined; (4) 0.20 percent for foreign material; (5) 9.00 percent for moisture; (6) 6.00 percent for sound whole kernels which will pass through the prescribed screen as to fall through; or if size is based on count per ounce, the average count per ounce shall be within the specified range. (7) otherwise meet Minimum Quality Standards published in 7CFR, Part 996 as to fall through.
Section 2. Medium Runner. Medium Runner consists of shelled Runner type peanut kernels of similar varietal characteristics which are whole and free from foreign material, damage, and minor defects, milled through a screen having 21/64 x 3/4 inch openings and which will not pass through a screen having 18/64 x 3/4 inch openings.
(1) 1.00 percent for other types of peanuts; (2) 5.00 percent for sound peanuts which are split or broken; (3) 3.50 percent for damage and minor defects combined; (4) 0.20 percent for foreign material; (5) 9.00 percent for moisture; (6) 6.00 percent for sound whole kernels which will pass through the prescribed screen as to fall through; and (7) otherwise meet Minimum Quality Standards published in 7CFR, Part 996 as to fall through.
Section consists of shelled Runner type peanut kernels of similar varietal characteristics which are whole and free from foreign material, damage, and minor defects, milled through a screen having 18/64 x 3/4 inch openings and which will not pass through a screen having 16/64 x 3/4 inch openings.
No.
(1) 1.00 percent for other types of peanuts; (2) 5.00 percent for sound peanuts which are split or broken; (3) 3.50 percent for damage and minor defects combined; (4) 0.20 percent for foreign material; (5) 9.00 percent for moisture; (6) 6.00 percent for sound whole kernels which will pass through the prescribed screen; and (7) otherwise meet Minimum Quality Standards published in 7CFR, Part 996 as to fall through.