
15 minute read
EPDs slowly gaining acceptance for road work, but challenges remain
By Russell W. Snyder, CAE
Green may be the most popular color in the color wheel these days, but moving environmental-awareness and sustainability beyond a marketing slogan to a robust and trusted system for procurement is proving to be a daunting challenge, even for a green-centric state like California.
Take EPDs, for example. Environmental Product Declarations (EPDs) appeared to be a logical first step for project owners to better understand the environmental impacts of the construction materials used in a project. But raising awareness about EPDs has been a challenge from Day 1. So has agreeing on what should go into an EPD, and ensuring that the information is accurate and comparable. Adding to the challenges, gathering and quantifying the data needed to produce the underlying environmental Lifecycle Assessment (LCA) and Product Category Rules (PCR) is an excruciatingly slow and timeconsuming (expensive) process, which has further slowed the ability of the EPD concept to catch on. Still, the forward progress is unmistakable.
“It is coming whether you like it or not,” says Greg Reader, an engineer with CalAPA associate member LASTRADA Partners who was the point person for developing EPDs when he was a Technical Specialist for CalAPA member George Reed Inc. “Get in front of this. It’s an opportunity to be a leader in our industry and shape the future. That’s my best advice. Confront this with your eyes wide open.”
Indeed, the steady drumbeat from project owners to better understand the environmental impacts of the projects they design and build and the materials they use continues unabated. Local agencies in particular increasingly call for EPDs on projects, triggering a frenetic conversation on the state of the science and the practicality and feasibility of generating them. At the same time, a cottage industry has developed to generate EPDs that may not meet stringent international standards for quality and transparency, further muddling the EPD picture.
“It is a recipe for chaos and bad decisions and cheating if done wrong,” says John Harvey, Ph.D., P.E., Director of the University of California Pavement Research Center. He urged a step-wise approach whereby agencies request EPDs, evaluate them and set regional baselines based on the information they gather from the first one to two years of EPDs. Some EPDs currently contain national baselines, Harvey said, which may or may not be accurate and relevant to what is achievable locally.
“What we are concerned about,” he said, “is local agencies that are moving straight to procurement and looking to accept quasi-EPDs with non-transparent data, and ‘go / no-go’ specifications that have baselines that may produce no incentive to improve if they are set too low or be very difficult to achieve even with significant innovation if set too high.”
Long term, many familiar with the EPD concept see California public agencies continuing to ask for EPDs, and eventually require them for projects. Ultimately, these people say, project owners may establish those baselines for projects from data gleaned from EPDs, and use that to determine winning bidders in a low-bid environment, which is most worrisome to the industry given the nascent state of EPD science and application. That concern was shared by the UCPRC’s Harvey.
“The idea is to collect information, using real EPDs, based on real operations, that undergo a critical review and are transparent,” Harvey said. “A goal could be to go to an incentive-disincentive model, rather than disqualifying potential bidders in a go/no-go system and possibly driving up prices. With an incentive-disincentive model, if you are good, you are rewarded. If you are not good, there is a disincentive. And as the overall industry and local competitors continue to innovate as reflected in incoming EPDs, the baseline for incentives and disincentives continues to be adjusted to drive innovation.”
Left: Jackie Wong of Caltrans delivers a presentation on Environmental Product Declarations at the CalAPA Spring Asphalt Pavement Conference held March 20, 2019 in Ontario.
Below: Greg Reader provides a contractor’s perspective of EPDs at the CalAPA Spring Asphalt Pavement Conference March 20, 2019 in Ontario.
The asphalt pavement industry has advocated for a similar approach, which has proven to be successful in spurring innovation and investment in other aspects of construction by contactors and suppliers always highly motivated to go after incentives.
“We need to develop the expertise to evaluate EPDs, and make them credible from the customer’s perspective,” Harvey said. “Among the state DOTs, Caltrans has really taken the lead on this.”
The emergence of EPDs has coincided with a greater public awareness of the impact to the environment from many human activities. EPDs got their start in pavements in the Netherlands 20 years ago, and received a boost in the United States when they were included in the U.S. Green Building Council’s LEED v4 rating system, which included a materials and resources credit that rewards product teams for using products that are accompanied by ISO 14044-compliant LCAs or ISO 14025-compliant EPDs. The newest version of the rating system, LEED v4.1, goes a step further by rewarding projects that select materials which have been “optimized” based on the data provided in EPDs, demonstrating a willingness to utilize a tool that project teams may not yet fully understand. On the federal level, the Energy Independence and Security Act requires the U.S. General Services Administration to evaluate and recommend green building certification systems to assess progress made toward agencies’ missions and goals. The Federal Highway Administration’s EPD information web page for pavements acknowledged that “specifics on how to interpret and apply the general rules (of EPDs) have proven to be varying from one application to another.”
In California, the California Department of Transportation (Caltrans) created a sustainability program and communicated its desire to incorporate environmental Life Cycle Assessment (LCA) and possibly EPDs in its decision-making. Some local agencies have also signaled their desire to incorporate EPDs in the procurement process, with Marin County emerging as one of the early adapters.
EPDs gained additional urgency in 2017 when a bill was introduced in the California Legislature, AB262, authored by Assemblyman Rob Bonta, D-Oakland, and Assemblywoman Susan Talamantes Eggman, D-Stockton, that would require the use of EPDs in the state procurement process.
CalAPA expressed concern that the bill was too far ahead of the industry’s ability to produce EPDs, and the premise was built on a go/

no-go system based on national averages that were hard to define. The bill was ultimately modified and all references to asphalt were deleted. The bill eventually passed the Legislature and was signed into law on Oct. 15, 2017 by then-Gov. Jerry Brown. Although references to asphalt were removed from the bill, Caltrans signaled its intention to eventually seek EPDs for construction materials.
The National Asphalt Pavement Association (NAPA), a CalAPA partner, has been developing an EPD program since 2013, which culminated with the Emerald EcoLabel tool, which was designed to make it easy for asphalt producers to create EPDs.
EPDs come from an environmental life cycle assessment and seek to capture and quantify information on the impacts to the environment from materials that are used in construction, and present them in a manner that is standardized and easy to understand by project owners and the public. EPDs are meant to represent the impact of raw material acquisition, energy use and efficiency, content of materials and chemical substances,
Left: Presenters at a CalAPAsponsored “webinar” on the subject of Environmental Product Declarations broadcast out of the CalAPA offices in West Sacramento. The Jan. 8, 2019 webinar featured presenters from NAPA, Caltrans and the University of California Pavement Research Center.
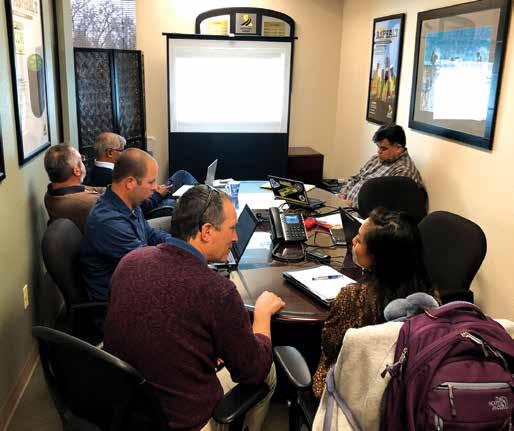
emissions to air, soil and water, and waste-generation, so-called “cradle to gate.”
Developing an EPD can be a daunting, complex and expensive proposition, which is greatly simplified and made more cost-effective with NAPA’s Emerald Eco-Label tool. For companies seeking to produce an EPD, NAPA suggests assigning a subject-matter expert within a given company, and then have them study the various educational materials and quizzes available on the NAPA website devoted to the topic. NAPA webinars to introduce the concept, which are free to CalAPA members, are advertised periodically on the NAPA website. After some familiarity with EPDs is established, NAPA then suggests the company move on to understanding the process of utilizing the NAPA “Emerald Eco-Label” tool – which is a feebased, web-based product. The company subject-matter expert will need to work with others to oversee the gathering of data that will be input into the tool, such as plant energy, mix-design component sources, warm-mix asphalt technologies, haul distances from suppliers, use of recycled materials, etc. EPDs are specific to each plant, so data gathered must be site-specific. NAPA has developed a spreadsheet to aid in the data-gathering process. More information on this topic is available at the NAPA on-line store.
“It was just a few short years ago when NAPA launched the Emerald Eco-Label Environmental Product Declaration (EPD) program, and just recently, NAPA began updating and revising the program,” said Richard Willis, NAPA’s Director of Pavement Engineering & Innovation. “Since we launched, some states have started considering what it would look like to require EPDs in the decision-making process. The Democratic Climate Change Action Plan specifically called for an EPD database to be put together, and more data are becoming available to increase our environmental transparency.”
Willis says more experience with EPDs is needed to ensure they are used properly.
“We can’t forget that the biggest need right now regarding EPDs is education,” he said. “The industry, legislators, and agencies know what EPDs are, but we need to provide further education on how to use them appropriately if they are going to be used; stakeholders need to understand what EPDs can and can’t tell you.” As part of the outreach and educational effort, CalAPA co-sponsored a 90-minute informational webinar on Jan. 8, 2019, featuring NAPA representatives along with local subject-matter experts from industry, Caltrans and University of California Pavement Research Center. A recording of the webinar and presentations were later uploaded to the web for ease of access (a link to the recording is included at the end of this article). Reader, the former Technical Specialist with George Reed Inc., was one of the panelists on the webinar to give a contractor’s perspective in developing an EPD. “The first thing I learned is, the hardest part of doing an EPD is gathering all of the information,” says Reader, who still interacts with contractors in his current job as an engineer for LASTRADA Partners. “The best advice I can give people is to start early, grab the EPD data-gathering sheet that NAPA provides, and start collecting the information that is required, such as electrical consumption and water consumption from the previous year. “That is the most time-consuming part,” he continued. “The next best piece of advice I give people is just to start. You’ve got to [ Continued on page 16 ] California Asphalt Magazine • 2020 Environmental Issue
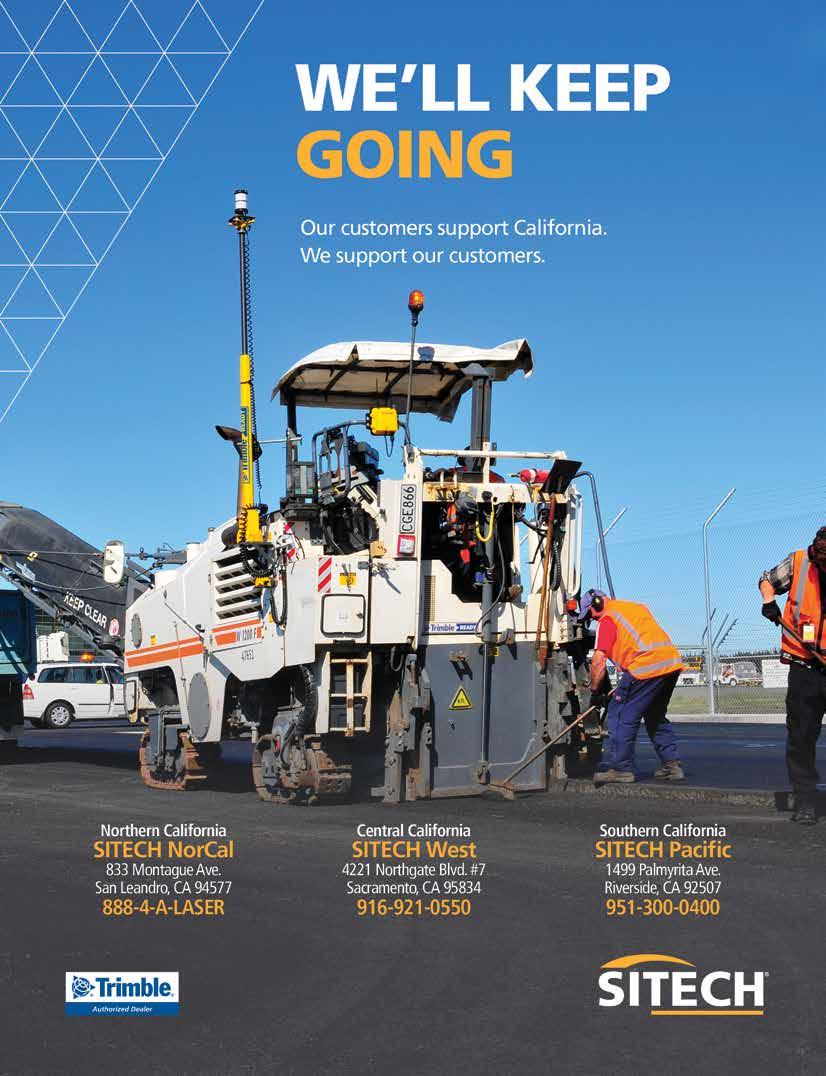
[ Continued from page 14 ] start somewhere. We didn’t wait until EPD language showed up in a project out to bid. We were proactive. We knew this was coming down the road. We decided to be pro-active, and learn about what is involved. We made a couple of EPDs so we could make comparisons — so we could compare, for example, asphalt with zero percent RAP (Reclaimed Asphalt Pavement), 15 percent and 25 percent. A good Quality Control department is pro-active, always studying trends and making adjustments in anticipation of changes. A bad QC Department is always reacting to changes.”
Reader said the EPD information was useful when his former company brought in outside experts to evaluate plants and make recommendations for improvements, not only for efficiency but also for environmental impact.
Reader agreed with UCPRC’s Harvey on a slow and careful approach to implementing EPDs in the asphalt pavement industry.
“The slower approach would be the better approach,” Reader said. “This eventually is going to become required. Agencies will be gathering data to establish baselines, in five or 10 years, and then possibly setting limits or caps, and compare EPD vs. EPD when evaluating bid price, not just the overall cost, but the overall lifecycle cost as well. But the Product Category Rules are changing. There are a lot of assumptions upstream, and some of those assumptions are going to change in 2022.”
Reader said he has been part of a committee advising NAPA on the next generation of the Emerald Eco-label on-line software, which likely will include an Impact Analysis Tool to help plant operators understand the result of various changes to plant equipment or procedures.
Companies participating in the Emerald Eco-Label program may be asked by NAPA to verify the data used in the company’s EPD, and random audits may be conducted to ensure that users are correctly inputting the data, all in the interest of ensuring the final EPD produced is robust. Since EPDs are relatively new, and the “rules of the road” have only recently been developed, it is in the best interests of the industry to ensure that published EPDs are accurate and comparable.
Jacquelyn Wong, P.E., is the project lead for the EPD program within the Caltrans Materials Engineering & Testing Services section, and was another of the presenters at the 2019 CalAPAsponsored EPD webinar. She recently held a meeting July 9 with stakeholders to assess the current state of EPDs for the state transportation department and what is likely to be the way forward.
In the opening of the meeting, she reminded attendees that Caltrans sees EPDs as linked to broader goals of environmental sustainability, staying ahead of legislative mandates, and creating a standardized, rigorously enforced process that quantitatively assesses environmental impacts while at the same time reducing the number of spurious “green” claims that are flooding the marketplace. Caltrans is also interested in a system that is both transparent and implementable, she said.
She also noted how construction materials make up a large part of total Caltrans spending, which presents an opportunity for big impacts in the reduction of Greenhouse Gases. About two-thirds of the $6.8 billion (or $4.56 billion) that Caltrans spent last year was on construction projects, and based on bid quantities that works out to about $1 billion a year for the procurement of aggregate base, asphalt and concrete.
Wong acknowledged that EPDs only provide a slice of the overall GHG impact, focusing on raw materials acquisition, transportation and manufacturing. There are many more components to the product lifecycle that have environmental implications, including transportation from the plant, installation, usage, maintenance, repair, replacement, refurbishment, de-construction, transportation of de-constructed materials, waste processing, disposal, and the potential for reuse and recycling.
When the Caltrans EPD effort got underway, one of the initial goals was to identify 20 potential pilot projects and include the production of an EPD in the bid as a separate bid item in 2019. Ultimately seven projects were selected and included in bids, but not until the 2020 fiscal year. A major hindrance to the identification of more projects, Wong said, was the lack of understanding among Caltrans personnel and contractors about what EPDs are, and the capability to produce them. There were also wide variations in the prices contractors affixed to the EPD bid item, ranging from $500 to $5,000, which generally does not include the cost of staff time in developing an EPD. She noted that the cost typically drops with each mixspecific EPD that is produced.
The focus for the pilot projects is on projects with large quantities of construction materials. She said the goal for the current fiscal year that began July 1 is to identify 100 projects, although she is realistic about the chances to reach that lofty target after only seven projects were identified the year prior.
“It doesn’t happen quickly,” she said, adding that she wants to ensure that each pilot project results in a quality EPD. Eventually,
she said, Caltrans envisions EPDs are something requested for all projects and just part of the normal cost of doing business for a contractor.
She also said the department is emphasizing the importance of high-quality EPDs.
“An EPD enhances the way we think about the environmental impacts of the materials we use on our construction projects,” Wong said. “Like how we consider Life-Cycle Cost Accounting (LCCA), we want to also consider environmental impacts on a lifecycle basis to support our three pillars of Sustainability: People, Planet and Prosperity, which can also be categorized as Social, Environmental and Economical.”
Wong and others interviewed for this story share a comment belief that EPDs are here to stay, and that companies and agencies would be well-served to understand them better and how to use them properly as part of an overall strategy of moving toward a more sustainable construction program.. CA
Russell W. Snyder, CAE, is executive director of the California Asphalt Pavement Association. Joseph Shacat, NAPA’s Director of Sustainable Pavements, contributed to this article.
REFERENCES: A recording of the CalAPA-NAPA “Webinar” held on Jan. 8, 2019 on the subject of Environmental Product Declarations in California can be accessed here: https://www.youtube.com/watch?v=9u8- tYuEpy4&feature=youtu.be
Federal Highway Administration “Tech Brief: Environmental Product Declarations, Communicating Environmental Impact for Transportation Projects” (2020). FHWAHIF-19-087. Issued July 2020.
Willis, R.J. (2017) NAPA Launches Emerald Eco-Label Tool. Asphalt Pavement, Published by the National Asphalt Pavement Association, Vol. 22, Issue 3, May-June 2017, pp 22. Dylla, H. (2016) An Update of the NAPA EPD Program. Asphalt Pavement, Published by the National Asphalt Pavement Association, Vol. 21, Issue 1, Jan-Feb. 2016, pp 24-27.
Santero, N., Gadonniex, H., Wong, S. (2014) Defining Environmental Impact: The What, How and Why of Environmental Product Declarations (EPDs). California Asphalt, Journal of the California Asphalt Pavement Association, Vol. 18, Issue 4, July 2014, pp. 12-14. Information on the U.S. Green Building Council’s LEED v.4 international standard for the design, construction and operation of structures can be found here: https://www.usgbc.org/leed/v4
Federal Highway Administration “Environmental Product Declarations And Product Category Rules” informational page. Updated May 14, 2019. Accessed July 12, 2020: https://www.fhwa.dot.gov/pavement/ sustainability/articles/environmental.cfm
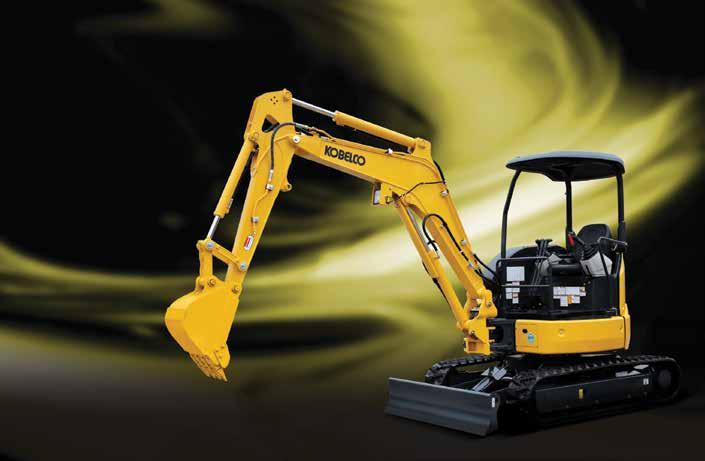
Full-Size Performance, Short-radius Agility and Quiet Operation COMPACT YET TOUGH MINI
Model : SK35SR-6E Program : 0% for 54 months and 90 Day deferral options for qualifying customers
WORK SMARTER – NOT HARDER
www.scottequip.com Serving California For 50 Years!
SOUTHERN CALIFORNIA’S PREMIER EQUIPMENT DEALER
Fontana / 909-822-2200
14635 Valley Blvd., Fontana, CA 92335
Santa Fe Springs / 562-777-0775
10918 Shoemaker Ave., Santa Fe Springs, CA 90670