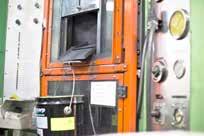
2 minute read
Custom Magnets for Design Specific Applications
Bunting provides complete engineering, design, and consulting services. Our expert engineering team complements your design and manufacturing team to develop a permanent magnet or a complete magnetic assembly specific to your need and application.
Custom blended neodymium powders mixed with resin:
The most significant feature of our bonded magnet processes is our ability to precisely target the magnetic performance and utilise net-shaping techniques, allowing us to achieve even the most complicated shapes. We offer a number of different performance levels and can create a precise blend to give you the most effective solution and achieve the level of performance that is needed for your specific application.
Pressure bonded at press tonnages from 4 to 200:
Based on techniques used in ceramics, powder metal, and harmaceuticals, compression moulded magnets require the lowest level of non-magnetic binder, thus producing the highest magnetic performance in bonded magnets. The use of compression moulding is typically used in rare earth alloy products such as Neodymium Iron Boron.
The most common shapes produced by this method are 2-D rings, but discs, blocks, and segments can also be produced by this method. The binders used in compression moulding are typically epoxy resins, which have good dimensional stability and resistance to chemicals. Some are able to withstand temperatures in excess of 250 °C.
We have a wide range of compression bonding capabilities, ranging from 4 tons up to 200 tons to give you the exact product for your needs.
Injection moulded to meet customer requirements:
Bunting uses injection moulding to create intricately shaped magnets that boast highly desirable properties. Injection moulding is an ideal process for applications that require high levels of precision, highly complex shapes, and insert or over-moulding. By utilising injection moulding, many identical components can be created in a short amount of time, making injection moulding appealing for high volume production.
Full inspection and certification capabilities:
Bunting is ISO 9001:2015 certified, ITAR registered and DFARS compliant. Bunting’s world-class manufacturing facility includes an option for glove box clean air assembly and an end of line pass/fail test to ensure spotless products that promise to uphold your brand and reputation. Our magnet materials and assemblies meet your quality and precision standards while maintaining a competitive price.
Rapid prototyping to speed up design timelines:
When working with our engineers, you are involved with the design process from start to finish. We have an on-site prototype manufacturing facility and our engineers are backed by our world-class manufacturing team, delivering you a product in two weeks or less. We provide as much application engineering as needed, and allow you to receive more than one prototype at a time if you are configuring multiple parts together. Our rapid prototyping capabilities allow you to receive real results in real time.
One-stop shop for magnetic assemblies and subassemblies:
Bunting is a one-stop shop specialising in magnetic assemblies. With our extensive knowledge of CNC machining, magnet fabrication, and final assembly capabilities, we can meet any magnetic assembly need no matter the complexity. We utilise the latest and leanest technologies applied to assembly processes such as bonding, fastening, and potting. Assemblies can be welded, sleeved, or encapsulated. Our final processes (post assembly) include final grind, balancing, and field mapping, allowing Bunting to deliver a quality driven and precise magnet assembly no matter the complexity.