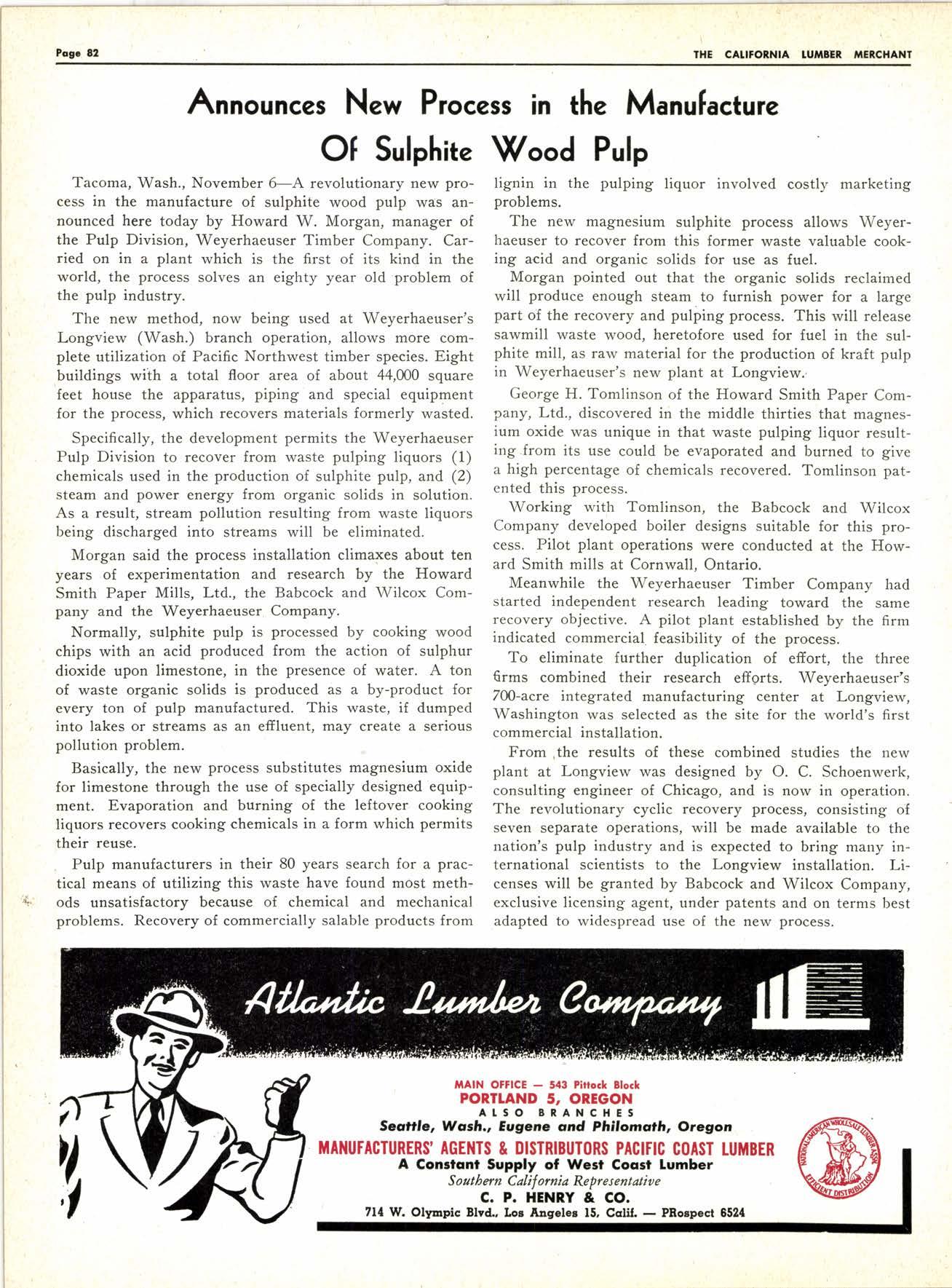
2 minute read
Announces New Process in the Manufacture Of Sulphite Wood Pulp
Tacoma, Wash., November 6-,4' revolutionary new process in the manufacture of sulphite wood pulp was announced here today by Howard W. Morgan, manager of the Pulp Division, Weyerhaeuser Timber Company. Carried on in a plant which is the first of its kind in the world, the process solves an eighty year old problem of the pulp industry.
The new method, now being used at Weyerhaeuser's Longview (Wash.) branch operation, allows more complete utilization of Pacific Northwest timber species. Eight buildings with a total floor area of about 44,m0 square feet house the apparatus, piping and special equipment for the process, which recovers materials formerly wasted.
Specifically, the development permits the Weyerhaeuser Pulp Division to recover from waste pulping liquors (1) chemicals used in the production of sulphite pulp, and (2) steam and power energy from organic solids in solution. As a result, stream pollution resulting from waste liquors being discharged into streams will be eliminated.
Morgan said the process installation climaxes about ten years of experimentation and research by the Howard Smith Paper Mills, Ltd., the Babcock and Wilcox Company and the Weyerhaeuser Company.
Normally, sulphite pulp is processed by cooking wood chips with an acid produced from the action of sulphur dioxide upon limestone, in the presence of water. A ton of waste organic solids is produced as a by-product for every ton of pulp manufactured. This waste, if dumped into lakes or streams as an effluent, may create a serious pollution problem.
Basically, the new process substitutes magnesium oxide for limestone through the use of specially designed equipment. Evaporation and burning of the leftover cooking liquors recovers cooking chemicals in a form which permits 'their reuse.
Pulp manufacturers in their 80 years search for a practical means of utilizing this waste have found most meth. ods unsatisfactory because of chemical and mechanical problems. Recovery of commercially salable products from lignin in the pulping liquor involved costly marketing problems.
The new magnesium sulphite process allows Weyerhaeuser to recover from this former waste valuable cooking acid and organic solids for use as fuel.
Morgan pointed out that the organic solids reclaimed will produce enough steam. to furnish power for a large part of the recovery and pulping process. This will release sawmill waste wood, heretofore used for fuel in the sulphite mill, as raw material for the production of kraft pulp in Weyerhaeuser's new plant at Longview.'
George H. Tomlinson of the Howard Smith Paper Company, Ltd., discovered in the middle thirties that magnesium oxide was unique in that waste pulping liquor resulting.from its use could be evaporated and burned to give a high percentage of chemicals recovered. Tomlinson patented this process.
Working with Tomlinson, the Babcock and Wilcox Company developed boiler designs suitable for this process. Pilot plant operations were conducted at the Howard Smith mills at Cornwall, Ontario.
Meanwhile the Weyerhaeuser Timber Company had started independent research leading toward the same recovery objective. A pilot plant established by the firm indicated commercial feasibility of the process.
To eliminate further duplication of effort, the three trms combined their research effgrts. Weyerhaeuser's 700-acre integrated manufacturing center at Longview, Washington was selected as the site for the world's first commercial installation.
From ,the results of these combined studies the new plant at Longview was designed by O. C. Schoenwerk, consulting engineer of Chicago, and is now in operation. The revolutionary cyclic recovery process, consisting of seyen separate operations, will be made available to the nation's pulp industry and is expected to bring many international scientists to the Longview installation. Li. censes will be granted by Babcock and Wilcox Company, exclusive licensing agent, under patents and on terms best adapted to widespread use of the new process.
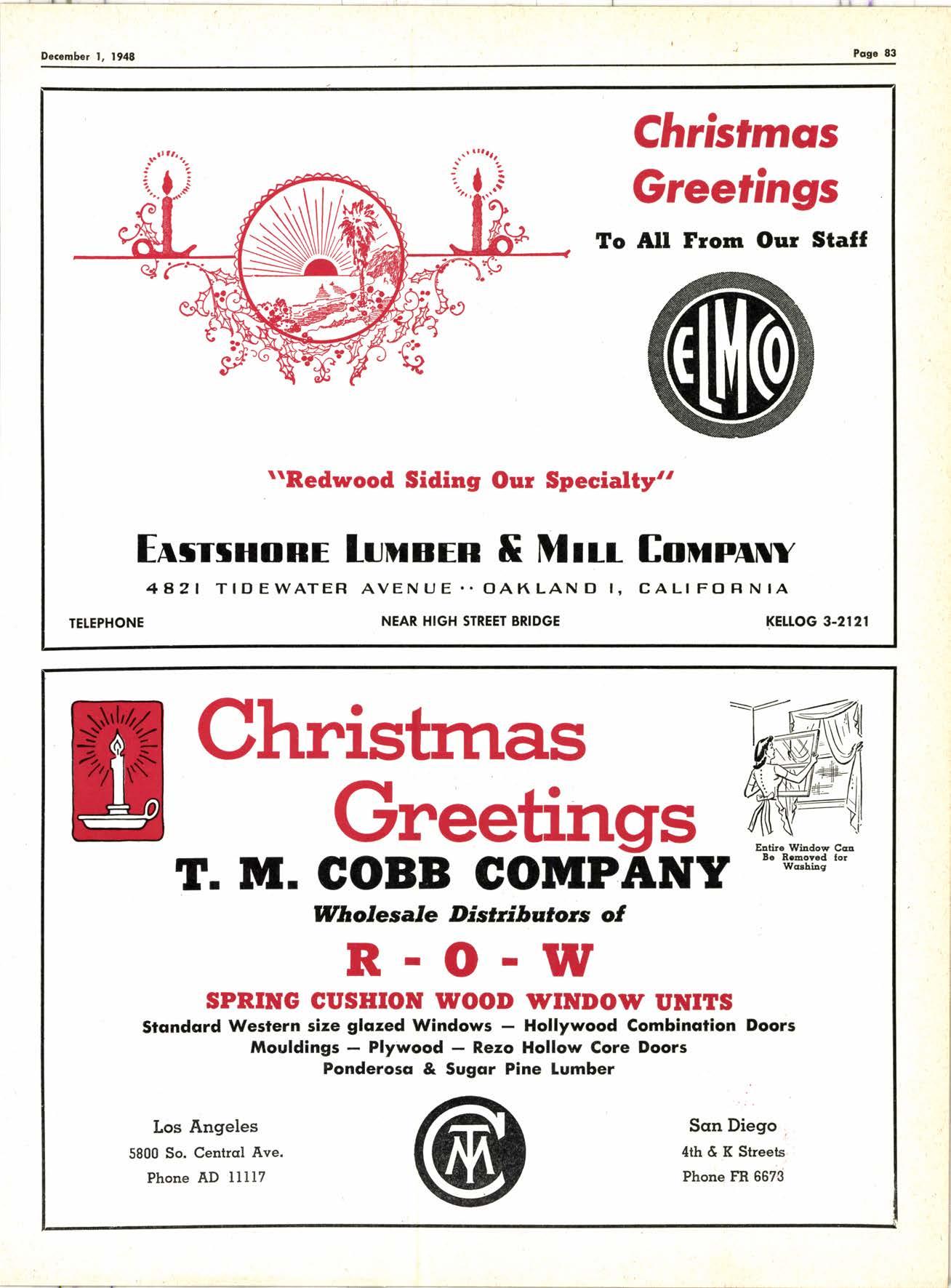