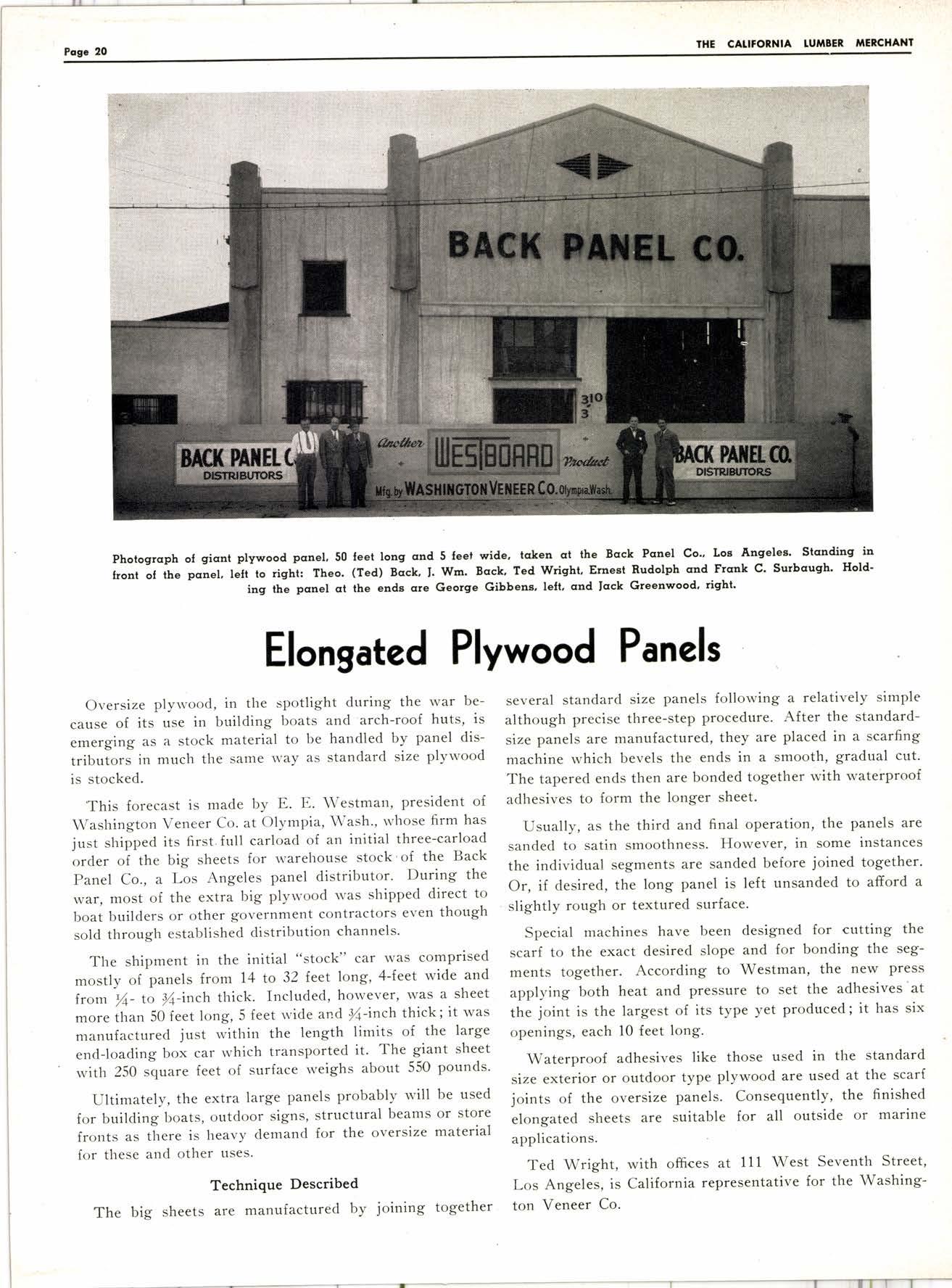
1 minute read
Elongated Plywood Panels
Oversize plyrvood, in the spotlight during the war because of its use in building boats and arch-roof huts, is emerging as a stock material to be handled by panel distribuiors in much the same way as standard size plywood is stocked.
This forecast is made by E. E. Westman, president of Washington Veneer Co. at Olympia, Wash', whose firm has just shipped its first.full carload of an initial three-carload orde. o?-the big sheets {or rvarehouse stock'of the Back Panel Co., a Los Angeles panel distributor' During the war, most of the extra big plyw'ood was shipped direct to boat builders or other government contractors even though sold through established distribution channels'
Tl-re shipment in the initial "stock" car was comprised mostly of panels from 14 to 32 feet long, 4-feet wide and lrom-/a- to sl-inch thick. Included, however' was a sheet more than 50 feet long, 5 feet rvide and sf-inch thick; it was manufactured just witl-rin the length limits of the large endJoading box car which transported it' The giant sheet with 250 .qu"t. feet of surface weighs about 550 pounds'
Ultimately, the extra large panels probably will be used for building boats, outdoor signs, structural beams or store fronts as there is heavy demand for the oversize material for these and other uses.
Technique Described
The big sheets are manufactured by joining together several standard size panels following a relatively simple although precise three-step procedure. After the standardsize panels are manufactured, they are placed in a scarfing machine which bevels the ends in a smooth, gradual cut' The tapered ends then are bonded together with waterproof adhesives to form the longer sheet.
Usually, as the third and final operation, the panels are sanded to satin smoothness. llowever, in some instances the individual segments are sanded before joined together' Or, if desired, the long panel is left unsanded to afford a slightly rough or textured surface.
Special machines have been designed for cutting the scarf to the exact desired slope and for bonding the segments together. According to Westman, the new press applying both heat and pressure to set the adhesives'at the joint is the largest of its type yet produced; it has six openings, each 10 feet long.
Waterproof adhesives like those used in the standard size exterior or outdoor type plywood are used at the scarf joints of the oversize panels. Consequently, the finished elongated sheets are suitable for all outside or marine applications.
Ted Wright, with offices at 111 West Seventh Street, Los Angeles, is California representative for the Washington Veneer Co.