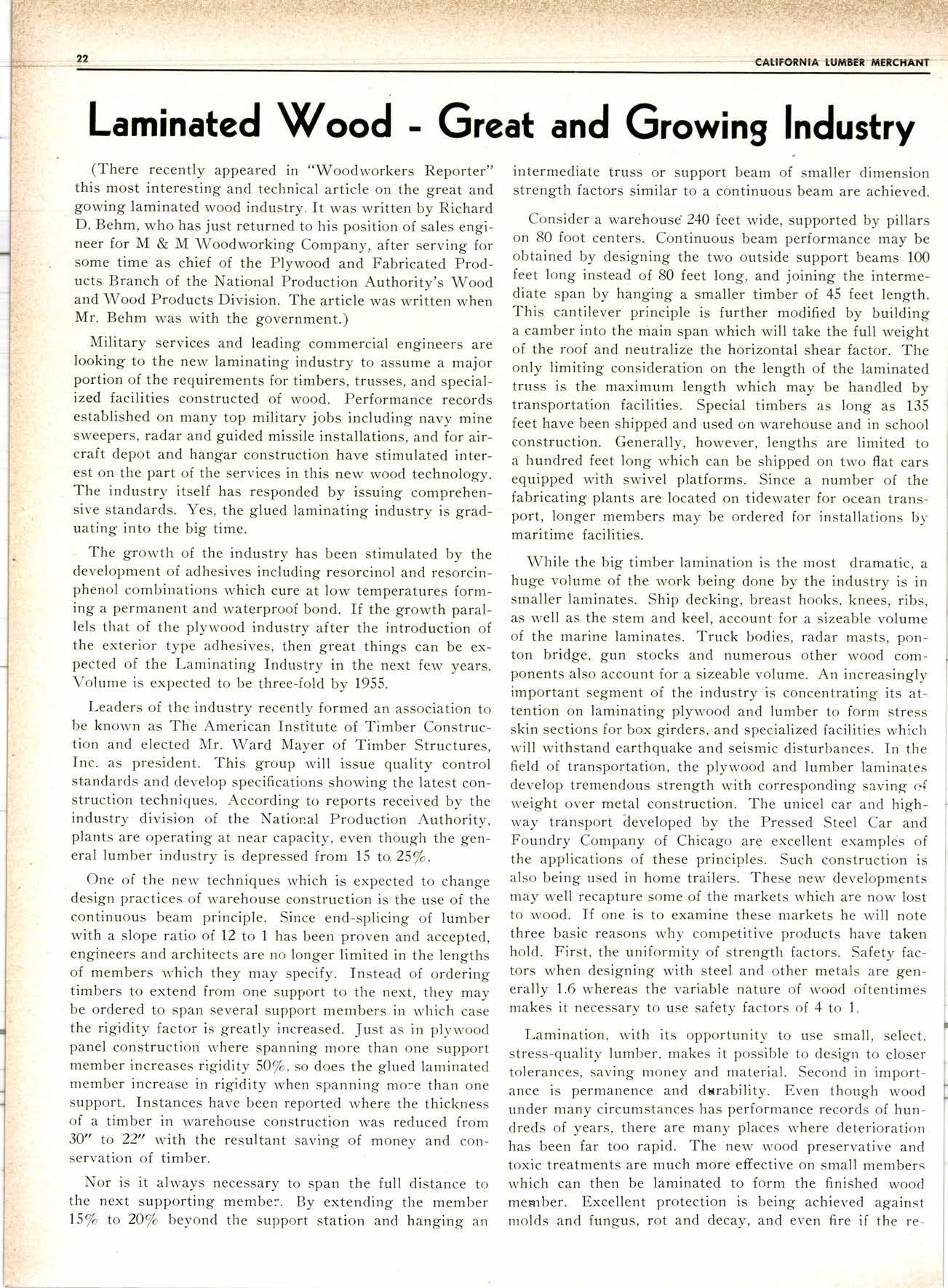
4 minute read
Laminated \(/ood r Great and Gro*ing Industry
(There recently appeared in "Woodworkers Reporter" this most interesting and technical article on the great and gowing laminated wood industry. It was written by Richard D. Behm, who has just returned to his position of sales engineer for M & M Woodworking Company, after serving for some time as chief of the Plywood and Fabricated Products Branch of the National Production Authority's Wood and Wood Products Division. The article was wriiten when Mr. Behm was with the government.)
Military services and leading commercial engineers are looking to the new laminating industry to assume a major portion of the requirements for timbers, trusses, and specialized facilities constructed of wood. Performance records established on many top militarv jobs including navy mine sweepers, radar and guided missile installations, and for aircraft depot and hangar construction have stimulated interest on the part of the services in this new wood technology. The industry itself has responded by issuing comprehensive standards. Yes, the glued laminating industry is graduating into the big time.
The growth of the industry has been stimulated by the development of adhesives including resorcinol and resorcinphenol combinations which cure at low temperatures forming a permanent and waterproof bond. If the growth parallels that of the plyrvood industry after the introduction of the exterior type adhesives, then great things can be expected of the Laminating Industry in the next few years. Volume is expected to be three-fold by 1955.
Leaders of the industry recently formed an association to be known as The American Institute of Timber Construction and elected Mr. Ward Mayer of Timber Structures, Inc. as president. This group will issue quality control standards and develop specifications showing the latest construction techniclues. According to reports received by the industry division of the National Production Authority, plants are operating at near capacity, even though the general lumber industry is depressed from 15 to.25/o.
One of the new techniques which is expected to change design practices of warehouse construction is the use of the continuous beam principle. Since end-splicing of lumber with a slope ratio of 12 to I has been proven and accepted, engineers and architects are no longer limited in the lengths of members which they may specify. Instead of ordering timbers to extend from one support to the next, they may be ordered to span several support members in which case the rigidity factor is greatly increased. Just as in plywood panel construction rvhere spanning more than one support member increases rigidity 50/o, so does the glued laminated member increase in rigidity when spanning mo:e than one support. Instances have been reported where the thickness of a timber in tvarehouse construction was reduced from 3U' to 27' with the resultant saving of money and conservation of timber.
Nor is it al.ivays necessary to span the full distance to the next supporting membe:. By extending the member 15/o to 2O/o beyond the support station and hanging an intermediate truss or support beam of smaller dimension strength factors similar to a continuous beam are achieved.
Consider a warehous€ 240 leet wide, supported by pillars on B0 foot centers. Continuous beam performance may be obtained by designing the two outside support beams 100 feet long insteail of 80 feet long, and joining the intermediate span by hanging a smaller timber of 45 feet length. This cantilever principle is further modified by building a camber into the main span which will take the full weight of the roof and neutralize the horizontal shear factor. The only limiting consideration on the length of the laminated truss is the maximum length which may be handled by transportation facilities. Special timbers as long as 135 feet have been shipped and used on warehouse and in school construction. Generally, however, lengths are limited to a hundred feet long which can be shipped on two flat cars equipped with swivel platforms. Since a number of the fabricating plants are located on tidewater for ocean transport, longer members may be ordered for installations b1, maritime facilities.
While the big timber lamination is the most dramatic, a huge volume of the work being done by the industry is in smaller laminates. Ship decking, breast hooks, knees, ribs, as well as the stem and keel, account for a sizeable volume of the marine laminates. Truck bodies, radar masts, ponton bridge, gun stocks and numerous other wood components also account for a sizeable volume. An increasingly important segment of the industry is concentrating its attention on laminating plyr,r'ood and lumber to form stress skin sections for box girders, and specialized facilities which rvill withstand earthquake and seismic disturbances. In the field of transportation, the plywood and lumber laminates develop tremendous strength with corresponding saving c{ rveight over metal construction. The unicel car and highway transport developed by the Pressed Steel Car and Foundry Company of Chicago are excellent examples of the applications of these principles. Such construction is also being used in home trailers. These new developments may well recapture some of the markets which are now lost to wood. If one is to examine these markets he rvill note three basic reasons why competitive products have taken hold. First, the uniformity of strength factors. Safety factors when designing with steel and other metals are generally 1.6 whereas the variable nature of wood oftentimes makes it necessary to use safety factors of 4 to 1.
Lamination, with its opportunity to use small, select. stress-quality lumber, makes it possible to design to closer tolerances, saving money and material. Second in importance is permanence and durability. Even though wood under many circumstances has performance records of hundreds of years, there are rnany places where deterioration has been far too rapid. The new wood preservative and toxic treatments are much mord effective on small members which can then be laminated to form the finished wood mesrber. Excellent protection is being achieved against molds and fungus, rot and decay, and even fire if the re-
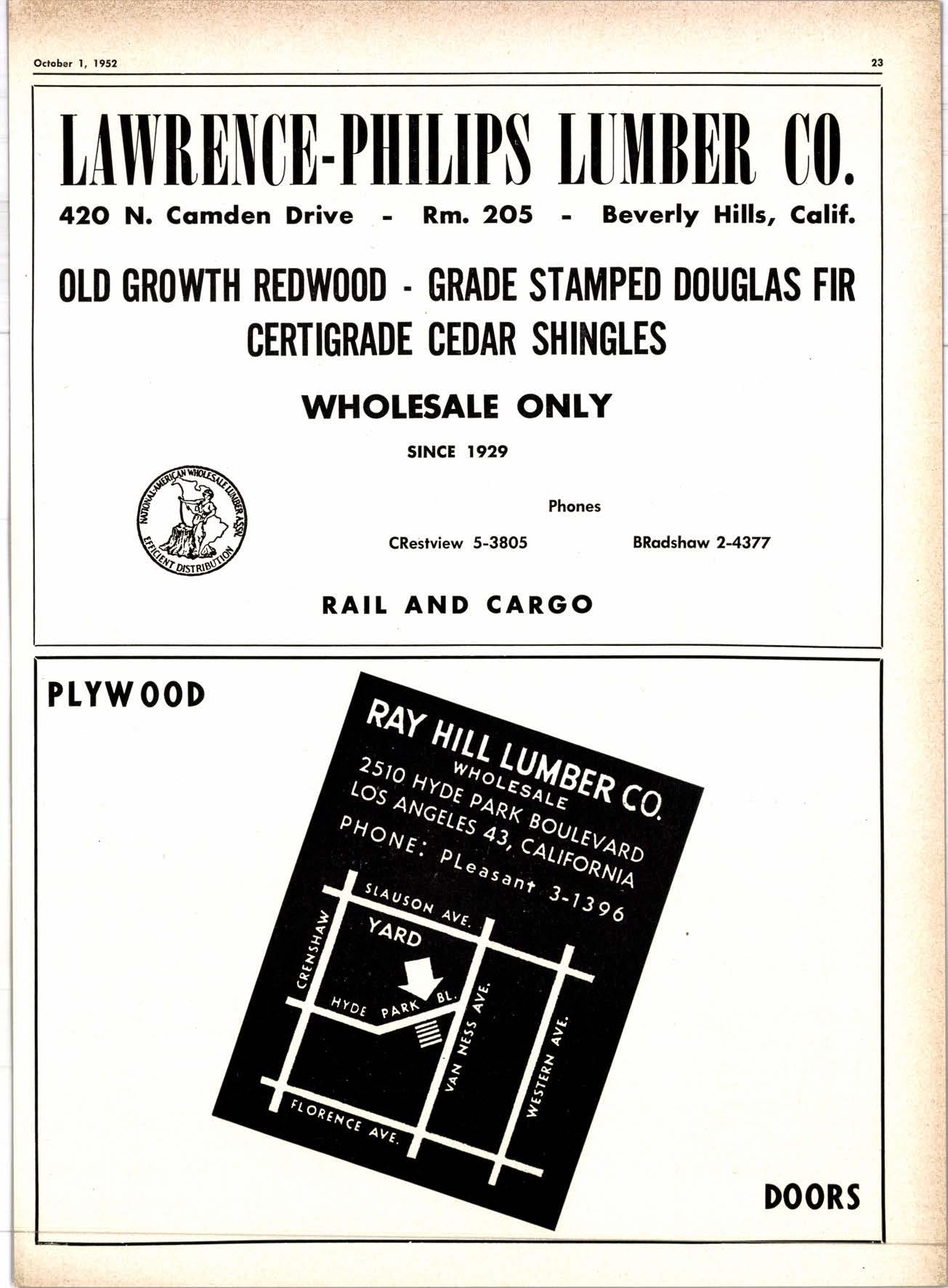