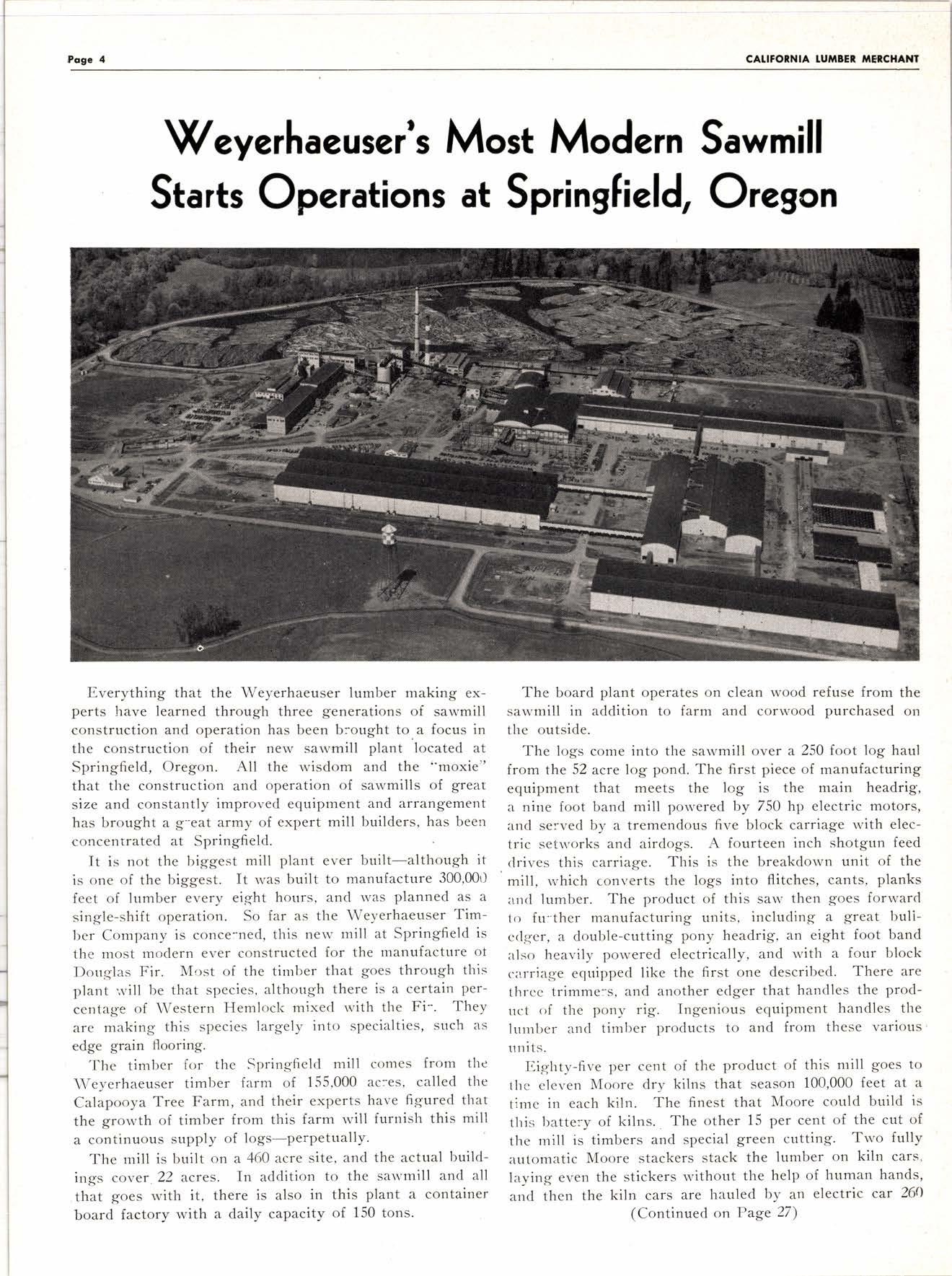
2 minute read
\(/"yerhaeuser's Most Modern Sawmill Starts Op"rations at Sprin glield, Oregon
Everything that the Weyerhaeuser lumber making experts have learned through three generations of sawmill construction and operation has been b:ought to.a focus in the construction of their new sarvmill plant located at Springfield, Oregon. All the wisdom and the ''moxie" that the construction and operation of sawmills of great size and constantly improved equipment and arrangement has brought a g-eat army of expert mill builders, has been concentrated at Springfield.
It is not the biggest mill plant ever built-although it is one of the biggest. ft was built to manufacture 300,0011 feet of lumber every eight hottrs, and rvas planned as a single-shift operation. So far as tl-re Weyerhaeuser Tim'l>er Cornpany is conce-ned, this nerv rnill at Springfield is the most modern ever constructed for the manufactttre ot Douglas Fir. Mcst of the timber that goes through this plant '"vill be that species, although there is a certain percentage of Western Hemlock mixed rvith the Fi-. They are making this species largely into specialties, such as edge grain flooring.
'Ihe timber for the Springfield mill comes from the Weyerhaeuser timber farm of 155,000 ac:es, called the Calapooya Tree Farm, and their experts have figured that the growth of timber from this farm will furnish this mill a continuous supply of logs-perpetually.
The mill is built on a 460 acre site, and the actual buildings cover. 22 acres. In addition to the sawmill and all that goes with it, there is also in this plant a container board factory with a daily capacity of 150 tons.
The logs come into the sawmill over a 250 foot log haul from the 52 acre log pond. The first piece of manufacturing equipment that meets the log is the main headrig, a nine foot band mill powered by 750 hp electric motors, and se:ved by a tremendous five block carriage with electric setu,orks and airdogs. A fourteen inch shotgun feed drives this carriage. This is the breakdown unit of the mill, rvhich converts the logs into flitches, cants, planks :rrrd lumber. The product of this sau' then goes forward to fu:'ther manufactttring units, including a great bulie<lger, a double-cutting pony headrig, an eight foot band :rlso heavily powered electrically, and with a four block c:rrriage equipped like the first one described. There are thrcc trimme:s, and another edger that handles the prodrrct of the pony rig. Ingenious equipment handles the lru'nber and tirnber products to and from these various rrnits.
Eighty-five per cent of the product of this mill goes to the eleven l\lloore dry kilns that season 100,000 feet at a time in each kiln. The finest that Moore could build is this battery of kilns. The other 15 per cent of the cut of the mill is timbers and special green cutting. Two fully :rutomatic Moore stackers stack the lumber on kiln cars. laying even the stickers withottt the help of human hands, and then the kiln cars are hauled by an electric car 26O
(Continued on Page 27)