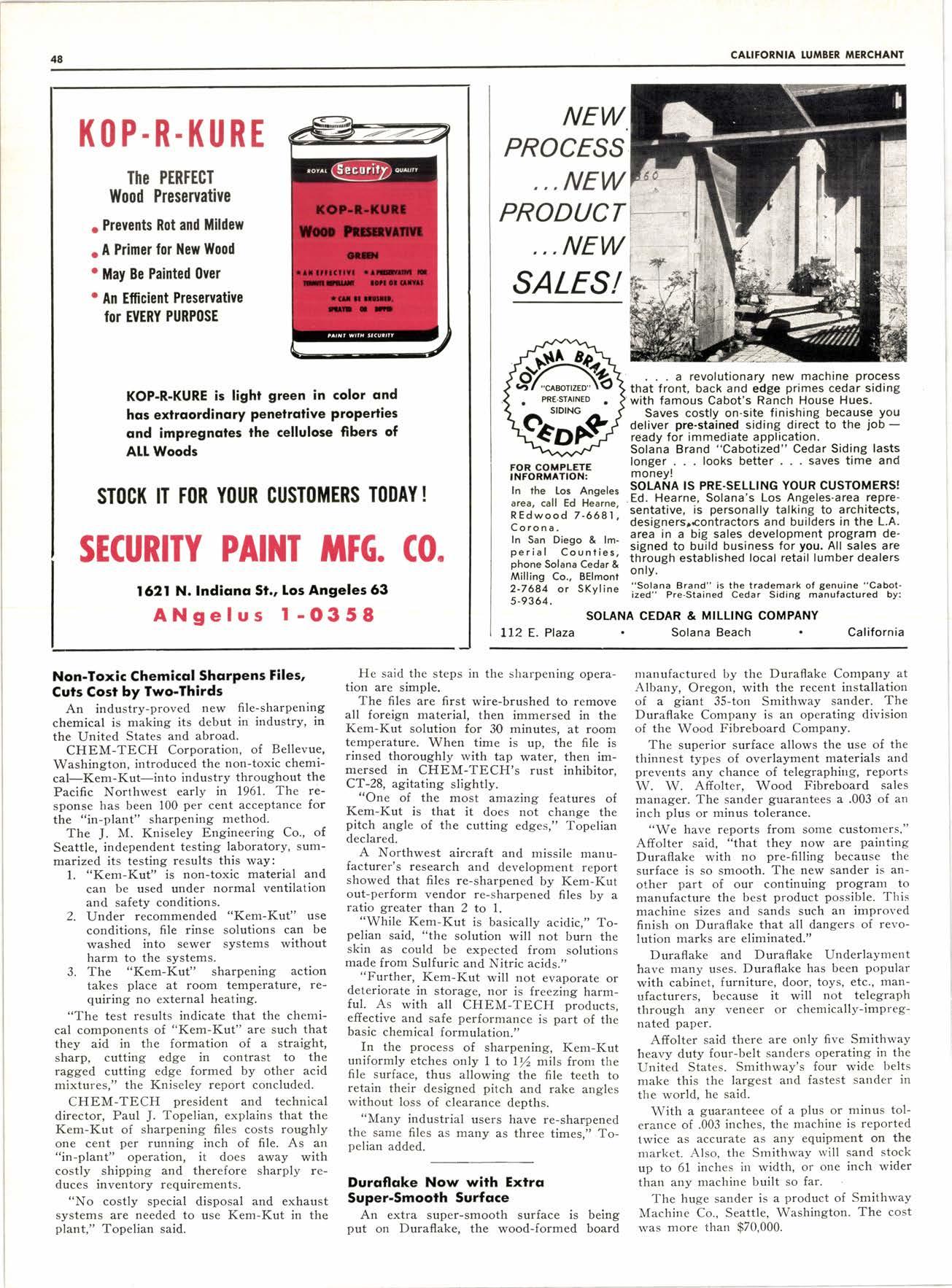
3 minute read
Kl|P.R.KURE
ThE PERFECT
Wood Preservative
Prevents Rot and ilildew
A Primer for l{ew Wood
'ilay 8e Painted Over
' An Effcient Preservative for EVERY PURP0SE
KOP-R-KURE is light green in color qnd has extrqordincry penetrotive properfies ond impregnoles the cellulose ftbers of ALI Woods
PROCESS ... NEW PRODUCT ... NEW EALEE!
. a revolutionary new machine process that front, back and edge primes cedar siding with famous Cabot's Ranch House Hues. Saves costly on-site finishing because you deliver pre-stained siding direct to the jobready for immediate application.
l62l N. Indiona 51., Los Angeles 63 ANgelus I -0358
Non-Toxic Chemicol Shqrpens Files, Cuts Cost by Two-Thirds
An industry-proved new file-sharpening chemical is making its debut in industry, in the United States and abroad.
CHEM-TECH Corporation, of Bellevue, Washington, introduced the non-toxic chemical-Kem-Kut-into industry throughout the Pacific Northwest early in 1961. The response has been 100 per cent acceptance for the "in-plant" sharpening method.
The J. M. Kniseley Engineering Co., of Seattle, independent testing laboratory, summarized its testing results this way:
1. "Kem-Kut" is non-toxic material and can be used under normal ventilation and safety conditions.
2. Under recommended "Kem-Kut" use conditions, file rinse solutions can be washed into sewer systems without harm to the systems.
3. The "Kem-Kut" sharpening action takes place at room temperature, requiring no external heating.
"The test results indicate that the chemical components of "Kem-Kut" are such that they aid in the formation of a straight, sharp, cutting edge in contrast to the ragged cutting edge formed by other acid mixtures," the Kniseley report concluded.
CHEM-TECH president and technical director, Paul J. Topelian, explains that the Kem-Kut of sharpening files costs roughly one cent per running inch of file. As an "in-plant" operation, it does away with costly shipping and therefore sharply reduces inventory requirements.
"No costly special disposal and exhaust systems are needed to use Kem-Kut in the plant," Topelian said.
FOR COilPLETE TNFORMATIOI{: ln the loc Angeles area, call Ed Hearne, R Edwood 7 -6681 , Corona. In San Diego & lmperial Counties, phone Solana Cedar & Milling Co., BElmont 2-7681 or SKyline 5-9364.
11.2 E. Plaza
Solana Brand "Cabotized" Cedar Siding lasts longer looks better saves time and money!
SOLANA IS PRE.SELTING YOUR CUSTOMERS!
Ed. Hearne, Solana's Los Angeles-area representative, is personally talking to architects, designerspcontractors and builders in the L.A. area in a big sales development program designed to build business for you. All sales are through established local retail lumber dealers only.
"Solana Brand" is the trademark of genuine "Cabotized" Pre-Stained Cedar Siding manufactured by:
SOLANA CEDAR & MILLING COMPANY
Solana Beach California
He said the steps in the sharpening operation are simple.
The files are first wire-brushed to remove all foreign material, then immersed in the Kem-Kut solution for 30 minutes, at room ternperature. When time is up, the file is rinsed thoroughly with tap water, then immersed in CHEM-TECH's rust inhibitor, CT-28, agitating s1ightly.
"One of the most amazing features of Kem-Kut is that it does not change the pitch angle of the cutting edges," Topelian declared.
A Northwest aircraft and missile manufacturer's research and development report showed that files re-sharpened by Kem-Kut out-perform vendor re-sharpened files by a ratio greater than 2 to 1.
"While Kem-Kut is basically acidic," Topelian said, "the solution will not burn the skin as could be expected from solutions made from Sulfuric and Nitric acids."
"Further, Kem-Kut will not evaporate or deteriorate in storage, nor is freezing harmful. As with all CHEM-TECH products, effective and safe performance is part of the basic chemical formulation."
In the process of sharpening, Kem-Kut uniformly etches only I to lrl mils from the file surface, thus allowing the file teeth to retain their designed pitch and rake angles without loss of clearance depths.
"Many industrial users have re-shar'pened the same files as many as three times," Topelian added.
Durqflqke Now with Extra Super-Smooth Surfoce
An extra super-smooth surface is put on Duraflake, the wood-formed manufactured by the Duraflake Company at Albany, Oregon, with the recent installation of a giant 35-ton Smithway sander. The Duraflake Company is an operating division of the Wood Fibreboard Company.
The superior surface allows the use of the thinnest types of overlayment materials and prevents any chance of telegraphing, reports W. W. Affolter, Wood Fibreboard sales manager. The sander guarantees a.003 of an inch plus or minus tolerance.
"We have reports from some customers," Affolter said, "that they now are painting Duraflake with no pre-filling because the surface is so smooth. The new sander is another part of our continuing program to manufacture the best product possible. This machine sizes and sands such an improved finish on Duraflake that all dangers of revolution marks are eliminated."
Duraflake and Duraflake Underlayment have many uses. Duraflake has been popular with cabinet, furniture, door, toys, etc., manufacturers, because it will not telegraph through any veneer or chemically-impregnated paper.
Afiolter said there are only five Smithway heavy duty four-belt sanders operating in the United States. Smithway's four wide belts make this the largest and fastest sander in the world, he said.
With a guaranteee of a plus or minus tolerance of .003 inches, the machine is reported twice as accurate as any equipment on the market. Also, the Smithway will sand stock up to 61 inches in width, or one inch wider than any machine built so far.
The huge sander is a product of Smithway being Machine Co., Seattle, Washington. The cost board was more than $70,000.
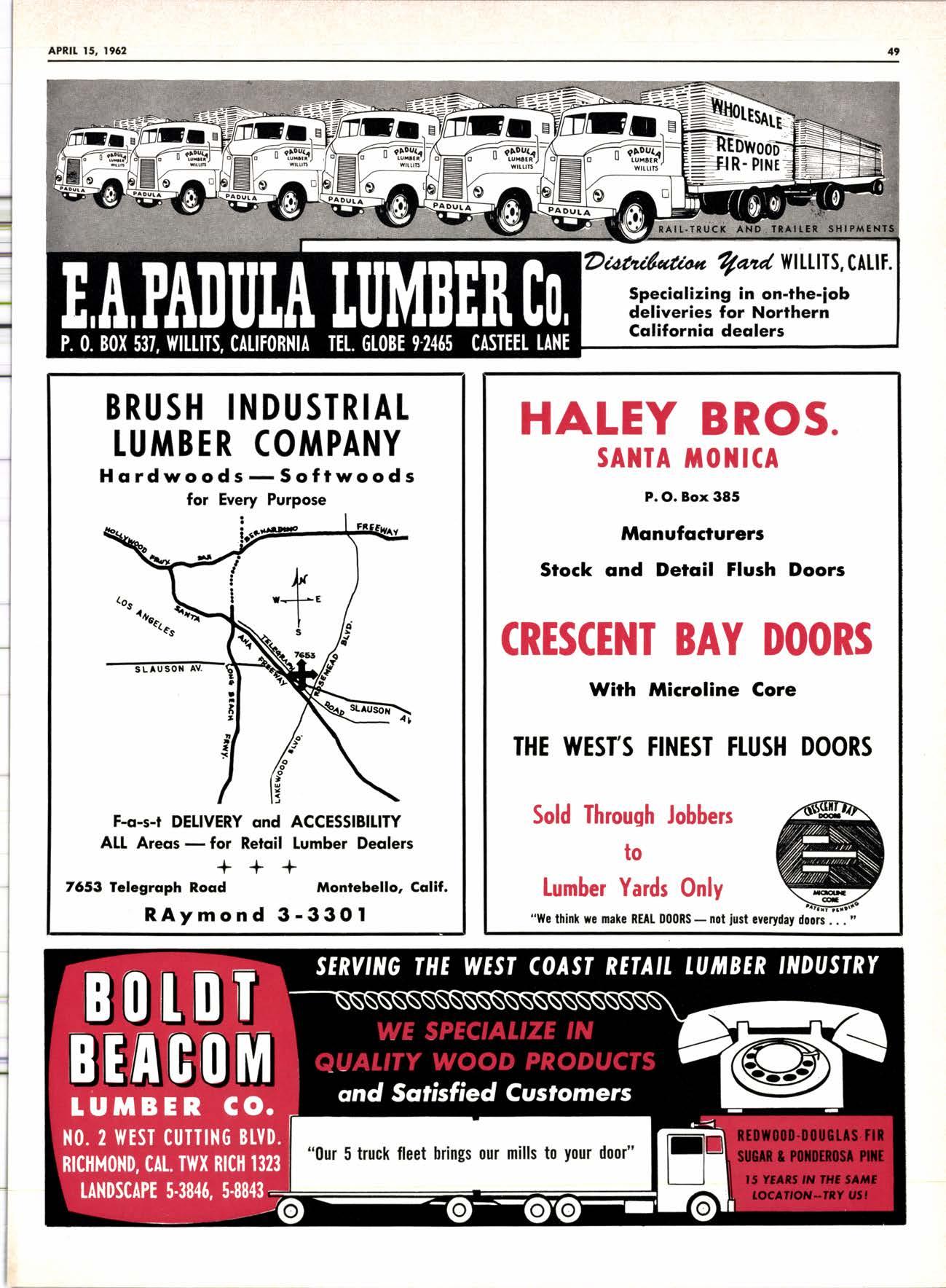