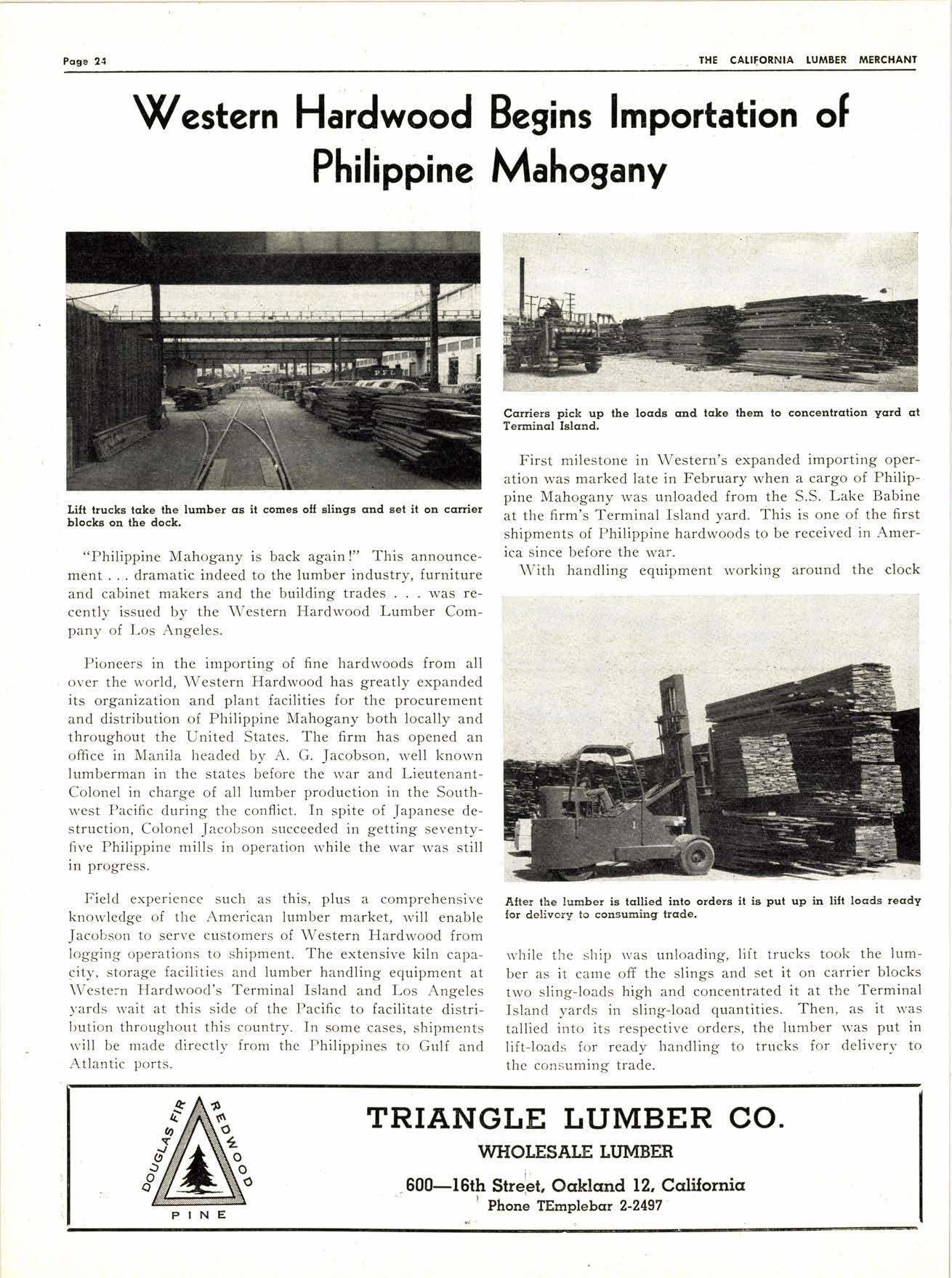
4 minute read
\Testern Hardwood Begins lmportation of Philippine Mahogany
"Philippine Mahogany is back again !" This announcement dramatic indeed to the lumber industry, furniture and cabinet makers and the building trades was recently issued by the Western Hardwood Lumber Company of Los Angeles.
Pioneers in the importing of fine hardrvoods from all over the world, Western Hardwood has greatly expanded its organization and plant facilities for the procurement and distribution of Philippine Mahogany both locally and throughout the United States. The firm has opened an olfice in Manila headed by A. G. Jacobson, well known Iumberman in the states before the rvar and LieutenantColonel in charge of all lumber production in the Southwest Pacific during tl.re conflict. In spite of Japanese destruction, Colonel Jacobson sttcceeded in getting seventyfive Philippine mills in operation while the l,var rvas still in progress.
Field experience such as this, plus a comprehensive knorvledge of the American lumber market, will enable Jacobson to serve customers of Western Hardwood from logging operations to shipment. The extensive kiln capacity, storage facilities and lumber handling equipment at Weste:n Hardwood's Terminai Island and Los Angeles yards 'rvait at this side of the Pacific to facilitate distribution througl.rout this country. In some cases, shipments rvill be n.rade directly from the Philippines to Gulf and Atlantic ports.
First milestone in Western's expanded importing operation was marked late in February when a cargo of Philippine Mahogany was unloaded from the S.S. Lake Babine at the firm's Terminal Island yard. fhis is one of the first shipments of Philippine hardwoods to be received in America since before the war.
With handling equipment working around the clock rvhile the sl.rip rvas unloading, lift trucks took the lumber as it came off the slings and set it on carrier blocks two sling-loads high and concentrated it at the Terminal Island vards in sling-load quantities. Then, as it u'as tallied into its respective orders, the lumber rvas put in lift-loads for ready handling to trucks for deliverv to the consuming trade.
STRABLI HANDWOOD GO.
1906 t9{8
HARDWOOD TUMBER
TACOilIA TUIIBAB $AI,T$
714 W. Olympic Blvd. tOS ANGEIES 15, CALIF.
Telephone PRospect ll08
PANEIS
FrooRrNo DowErs
UPSON
MASONITE PRODUCTS CANEC
GABGO and RAIL NEPRESENTING
537 FIRST STREET
OAKTAND 7 CATIFORNIA
Sell This
Sinlc
Sctt
t -lo, imrned.iate proft ol these modera ainh retB you mcke cr_lcsling curtomer lor your business-q good prospect Ior tr _complete Peerlegs kitchenl Mais oI complete ne-to"poier c& Iree. Write lor literalure cnd prices on lhose deerless siul sets.
Every tirre you selt oae and. f atute proft!
St. Paul d Tccomcr Lumber Co.
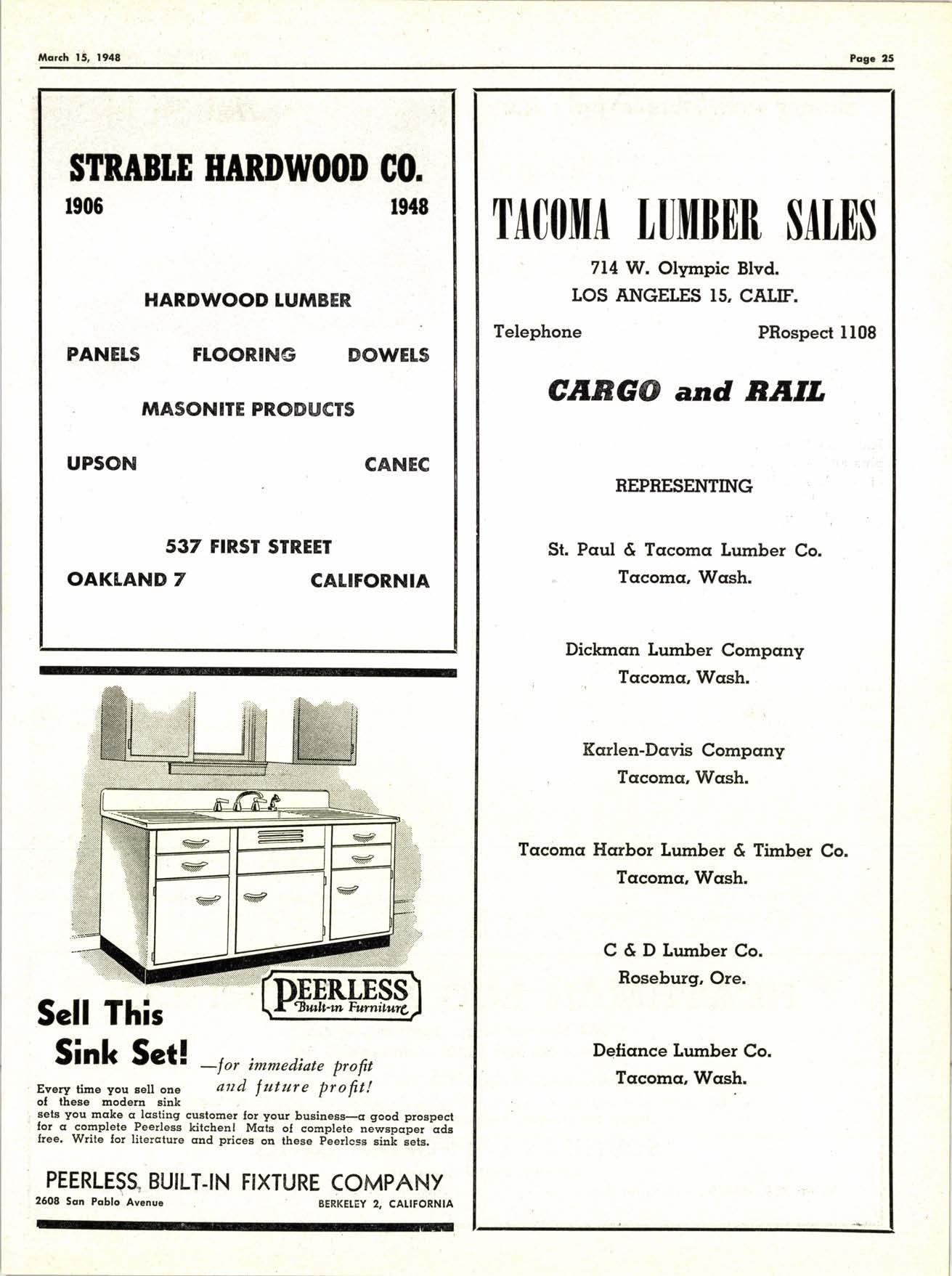
Tccomcr, Wcrsh.
Dickmcrn Lumber Compcny
Tqcomc, Wcrsh.
Kcrlen-Dcvis Compcny
Tccomc, Wcsh.
Tccomc Hcrrbor Lumber d Timber Co.
Tccomcr, Wash.
C&DLumberCo.
Boseburg, Ore.
Deficrnce Lunber Co.
Tccomcr, Wcsh,
Boat Patch Glue Applicator
A casual remark plus an individual's ingenuity has developed an almost revolutionary time saver in the plywood plant of The Long-Bell Lumber Company at Weed, California.

It's a boat patch glue applicator which has trimmed 40 per cent off the usual time required for gluing up of boat patches. With the time saving brought about by the invention, the process of patch preparation has also b'een increased.
A casual remark by millwright Hap Delong as he watched Mrs. Auda Samples rack and spray the patches, was overheard by the Panel Foreman Mario Marchi. After Delong had repeated the remark to Marchi, the ingenious mechanic ditappeared into his workshop and started to work.
The first model of the glue applicator gave almost a Rube Goldberg appearance with its rubber bands, bobby pins and any ofher handy material. The model 'ivas made of wood. Despite the fact that practically everything except the kitchen sink rvas incorporated in the first boat patch glue applicator, the gadget performed its task with regularity and determined success.
A bit of redesigning, with the expanding of this part and the whittling away of another, and the applicator entered the machine shop to emerge a member of the steel family.
The applicator is in reality a miniature glue spreader with the exception of the two wheels. They are grooved to a "V" shape to take the boat patches. The wheels rotate in Urea Resin glue and the operator merely pushes the boat patch down between the two "V" shaped 'ivheels and the spring tension then carries it on through to complete the gluing process.
The glue applicator has one fixed wheel rvith the other operating on a slide with spring tension to allow the wheels to follow the contour of the patch resulting in a uniform spread of glue on the edge. Rubber shields fit closely around the wheels to keep the excess glue from sides of the wheels. The control of glue spread is accomplished with a small doctor bar.and the excessive glue is kept in the hopper pan.
Most common method of applying glue to boat patches requires the placing of patches face to face on racks and
A boot pctch stcrls througb the lcbor scrving boct pctch gluer. the application of the glue with spray guns or brushes. After which it is necessary to separate the patches which After this operation the racked patches are allowed to dry. have adhered to one another due to excessive glue.
Marchi's boat patch glue applicator eliminates the necessity of pairing up, racking and separating the patches in addition to the application of glue by spray gun or brush. In addition to saving 40 per cent of the time generally used for the operation, the convenience and speed of handling the patches has been increased.
After the operation has passed the patches between the grooved u,heels of the applicator, the patches are placed in drawers for procuring before being used in the hot plate patch. The placing of the patches in drawers make storage of the patches less cumbersome.
The boat patches are used to replace defects with clear wood after defects such as knots and pitch pockets have been removed. A "Defect Cutter" cuts a hole the exact size of the boat patches.
The Long-Bell Plywood plant at Weed is the oldest on the Pacific Coast operating in pine. The plant was established in 1910 as a veneer plant and the product was used entirely by the company in its own door manufacturing operation. As the demand for plywood increased, the operation rvas expanded with the result that the plant has been undergoing extensive modernizing operations for the past few years. The modernization will be completed as soon as machinery is made available.
Fern Trucking Company
Offers Combined Service Of:
Trucking '
Ccrr Unlocrding
Pool C<rr Distribution
Sorting
Sticking lor Air Drying
Storing oI Any Qucrntity ol Forest Products
Ten Hecvy Duty Trucks crnd Trailers
Fourteen 3-Axle All Purpose Army Lumber Trucks
Seven 16,000 lb. Lilt Trucks
Twenty-Seven Acres Pcved Lcrnd ct Two Locqtions
Served by L. A. Junction Rcilro<rd
Shed Spcrce lor Two Million Bocrrd Feet
Spur Trcck to Accommodcrte Thirty Rcrilrocrd Cars
Bccked by Twenty-two yecrrs ol Experience in Handling Lumber crnd Forest Products
This Compcrny Is Owned crnd Opercrted by FEBN-crndo I. Negri
4550 Mcrywood Ave., Los Angeles ll lEflerson 7261