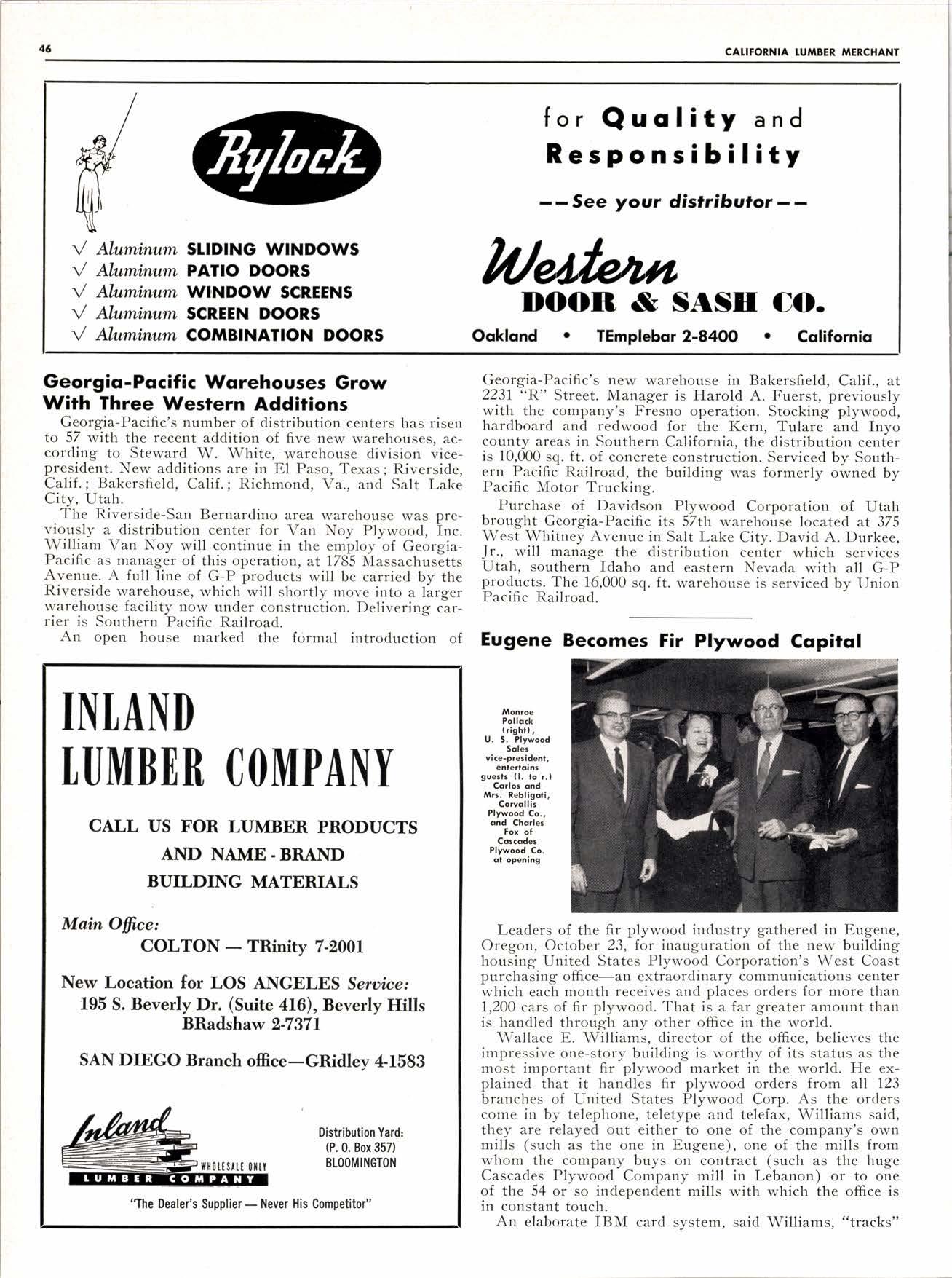
4 minute read
for Quolity and Responsibility
-- See your distribulor - - t/ Alaminnm 9UDING WINDOWS t/ Alumirrurn PAIIO DOORS t/ Al,uminunr. WINDOW SCREENS t/ Aluminunr. SCREEN DOORS t/ Alumirntm COIIBINATION DOORS
Georgio-Pocific Worehouses Grow Wirh Three Western Addirions
Georgia-Pacific's number of distribution centers has risen to 57 with the recent addition of five new warehouses. according to Steward W. White, warehouse division vicepresident. New additions are in El Paso, Texas; Riverside, Calif. ; Bakersfield, Calif.; Richmond, Va., and Salt Lake City, Utah.
The Riverside-San Bernardino area warehouse was preyigusly a distribution center for Van Noy Plywood, Inc. William Van Noy will continue in the employ'of Georgia- Pacific as manager of this operation, at 1785 MassachusEtts Avenue. A full line of G-P products will be carried by the Riyerside warehouse, which will shortly move into a lirger warehouse facility now under construction. Delivering carrier is Southern Pacific Railroad.
An open house marked the formal introduction of
Georgia-Pacific's new warehouse in Bakersfield, Calif., at 223I "R" Street. Manager is Harold A. Fuerst, previously with the company's Fresno.operation. Stocking plywood, hardboard and redwood for the Kern, Tulare and Inyo county areas in Southern California, the distribution center is 10,000 sq. ft. of concrete construction. Serviced by Southern Pacific Railroad, the building was formerly owned by Pacific Motor Trucking.
Purchase of Davidson Plywood Corporation of Utah brought Georgia-Pacific its 57th warehouse located at 375 West Whitney Avenue in Salt Lake City. David A. Durkee, Jr., will manage the distribution center which services Utah, southern Idaho and eastern Nevada with all G-P products. The 16,000 sq. ft. warehouse is serviced by Union Pacific Railroad.
Leaders of the fir plywood industry gathered in Eugene, Oregon, October 23, lor inauguration of the new building housing United States Plywood Corporation's \Mest Coast purchasing omce-an extraordinary communications center which each month receives and olaces orders for more than 1,200 cars of fir plywood. That is a far greater amount than is handled through any other office in the world.
Wallace E. Williams, director of the office, believes the impressive one-story building is worthy of its status as the most important fir plywood market in the world. IIe explained that it handles fir plywood orders from all 123 branches of United States Plywood Corp. As the orders come in by telephone, teletype and telefax, Williams said, they are relayed out either to one of the company's own mills (such as the one in Eugene), one of the mills from whom the company buys on contract (such as the huge Cascades Plywood Company mill in Lebanon) or to one of the 54 or so independent mills with which the office is in constant touch.
An elaborate IBM card system. said Williams. "tracks"
TUMBER FOR, EVERY PURPOSE
DOUGTAS FIR
ROUGH OR SURFACED DIiAENSION
CATIFORNIA REDWOOD
ROUGH OR SURFACED
. GREEN OR DRY ond ALL OTHER PACIFIC COAST SPECIES
WHOtESAtE LUMBER DIRECT MItL SHIPMENTS_RAIT OR TRUCK_CARGO
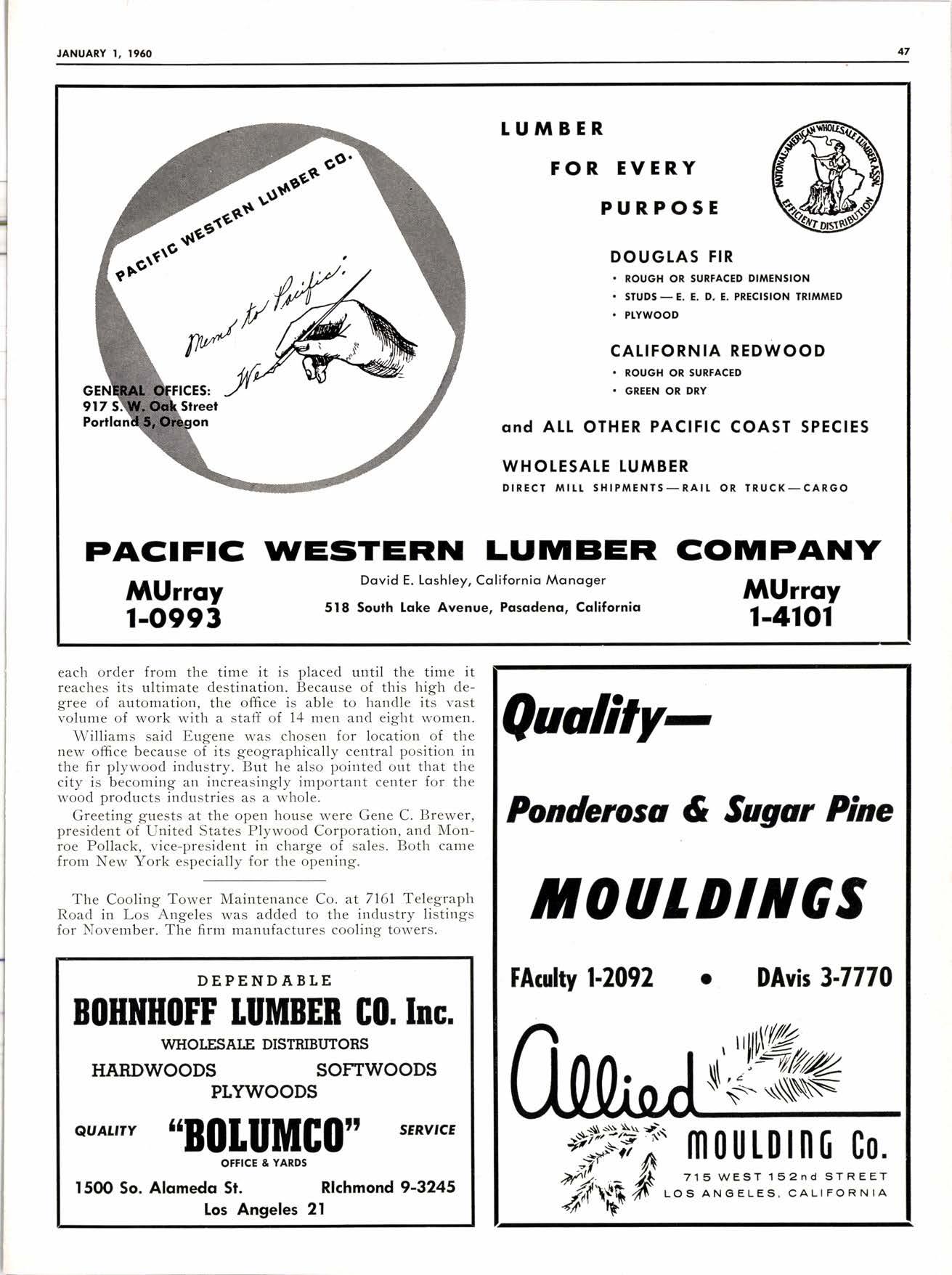
Dqvid E. Loshley, Colifornio Monoger
518 South Lqke Avenue, Posodeno, Cqliforniq each order from the time it is placed until the time it reaches its ultimate destination. Because of this high degree of automation, the offrce is able to handle its vast volume of work with a staff of 14 men and eight women.
Williams said Eugene was chosen for location of the new office because of its geographically central position in the fir plywood industry. But he also pointed out that the city is becoming an increasingly important center for the wood products industries as a whole.
Greeting guests at the open house were Gene C. Brewer, president of United States Plywood Corporation, and Monroe Pollack, vice-president in charge of sales. Both came from New York especially for the opening.
The Cooling Tower Maintenance Co. at 7161 Telegraph Road in Los Angeles was added to the industry listings for NTovember. The firm manufactures cooling towers.
NOVOPTY AND THE PARTICLE BOAR,D INDUSTR,Y
A recent survey of the world's forest products industries by the United Nations Food and Agricultural Organization (FAO) stated that "the particle board industiy is the youngest of the existing forest industries but its growth in the past decade has been phenomenal."
The survey reported the following figures for world particle board output (in million square feet, 3f 8', basis) : t951-62.1, 1952-t24.3, t953--233.9, 1954-464.4, 19557 54.8, r956-t,244.1, t95S-3,567 .4.
Novoply was first introduced in Switzerland in 1947. United States Plywood Corporation started manufacturing it in this country in 1951 under license from its inventor-, a Swiss wood technologist named Fred Fahrni, who is now head of the Fahrni Institute in Zurich and has issued licenses to-producers in 14 counties. Licensees meet at regu- lar intervals to trade notes on know-how in technology, plo- duction and sales. The new plant in South Boston-,- in its planning, has therefore had the benefit of the latest worldwide thinking in wood and resin technology.
Particle boards of various types are now manufactured by approximately 60 firms in the United States. Their common denominator is that they are constructed of wood particles-whether fakes, chips, shavings or saw- dust-bonded under pressure with a resin- or other binder.
Novoply is_ an engineered three-ply board consisting of dense outer layers of resin-impregnated flakes bondeil to an.inner layer of chips. When it first appeared, one commentator called it "the wood nature should have invented.', Because it. has_ no grain direction, and because of its patented. sandwich-type constrlgtion, Novoply shows e*iep- tional dimensional stability. These properiiis have brougfit it into wide demand as a-material iortloset and cupboird sliding and bifold doors, for dinette and table underlayment, for partition and wall panels, and a wide variety of other uses.
It is interesting to note that the original impetus for a board such as Novoply arose from the necessity of Europeans to utllize as high a percentage as possible of their wood supply. Much of the material used in particle boards was, in former years, simply discarded.
But now, at an integrated plywood-lumber-logging operation such as the vast U.S. Plywood complex at Anderson, California, use in Novoply of peeler cor6s and other remnants gives profitable utilization of 8O/o to 85/o of the tree, as compared with a wood industry average in the neighborhood of 55/o.The new U.S. Plywood plant in South Boston will utilize just as high a percentage, producing not from selected left-overs but from "round logs."
Novoply is produced under rigid quality controls. The proportion of resin to chips and flakes, for example, is care-
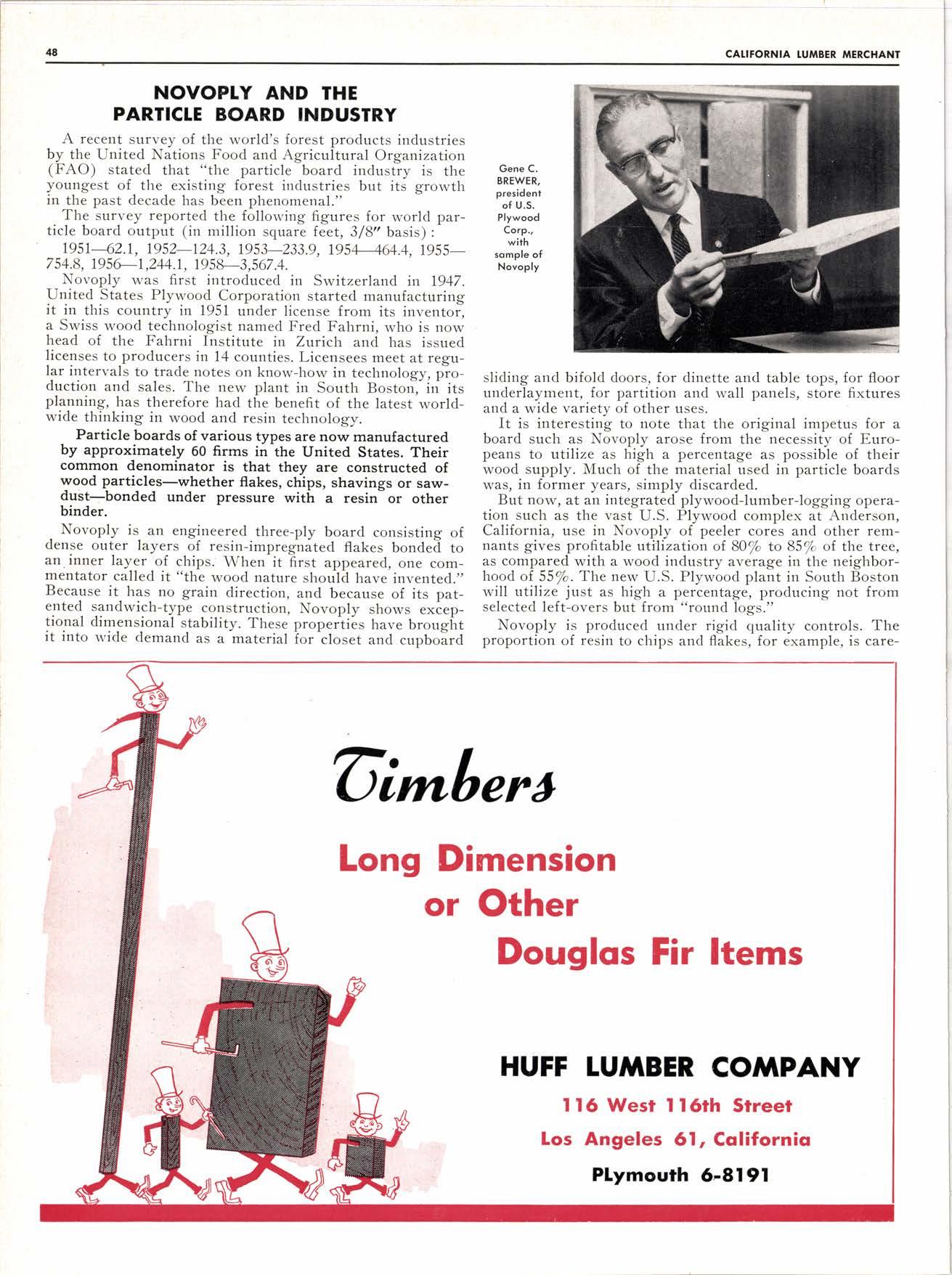