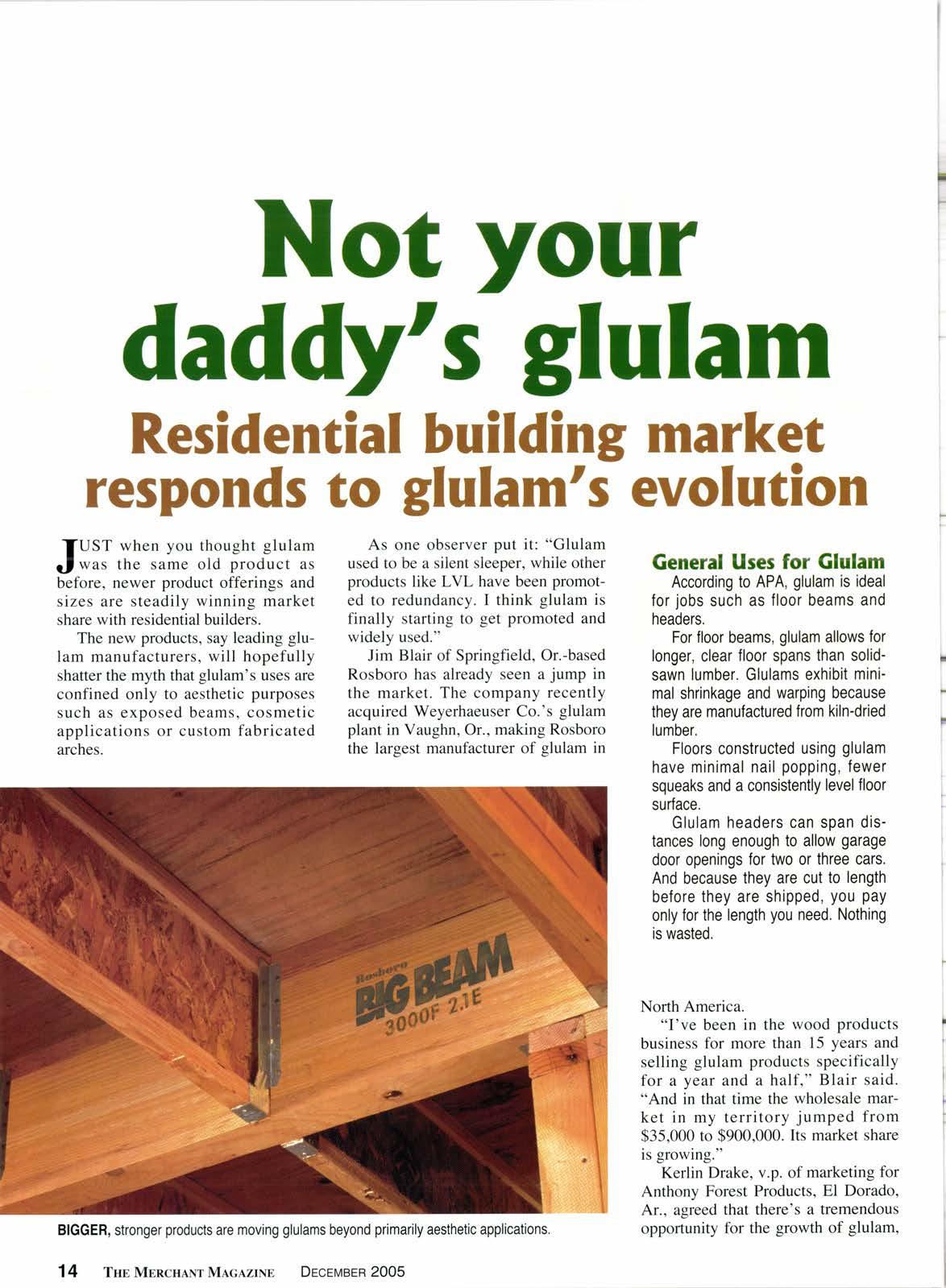
4 minute read
Not your daddy's glulam
Residential building market responds to glulam's evolution
TUST when you thought glulam j was the same old product as before, newer product offerings and sizes are steadily winning market share with residential builders.
The new products, say leading glulam manufacturers, will hopefully shatter the myth that glulam's uses are confined only to aesthetic purposes such as exposed beams, cosmetic applications or custom fabricated arches.
As one observer put it: "Glulam used to be a silent sleeper, while other products like LVL have been promoted to redundancy. I think glulam is finally starting to get promoted and widely used."
Jim Blair of Springfield, Or.-based Rosboro has already seen a jump in the market. The company recently acquired Weyerhaeuser Co.'s glulam plant in Vaughn, Or., making Rosboro the largest manufacturer of glulam in
General Uses for Glulam
According to APA, glulam is ideal for jobs such as floor beams and headers.
For floor beams, glulam allows for longer, clear floor spans than solidsawn lumber. Glulams exhibit minimal shrinkage and warping because they are manufactured from kiln-dried lumber.
Floors constructed using glulam have minimal nail popping, fewer squeaks and a consistently level floor surface.
Glulam headers can span distances long enough to allow garage door openings for two or lhree cars. And because they are cut to length before they are shipped, you pay only for the length you need. Nothing is wasted.
North America.
"I've been in the wood products business for more than 15 years and selling glulam products specifically for a year and a half," Blair said. "And in that time the wholesale market in my territory jumped from $35"000 to $900,000. Its market share is growing."
Kerlin Drake, v.p. of marketing for Anthony Forest Products, El Dorado, Ar., agreed that there's a tremendous opportunity for the growth of glulam, as well as other engineered wood products. "You have to market the right size parts to the wholesaler, to the supplier, then to the builder, to eliminate skews for inventory to have the right product for the right application," he said.
Doug Calvert, president of Calvert Co., Inc., a glulam manufacturer in Vancouver, Wa., said he thinks that glulam usage will continue to rise.
"It's such a good product and easy to use, and we can make it in a lot of different shapes, as opposed to some of our competitor products," Calvert said.
More depth, cleaner fit
There's a good reason for the market jump. Newer glulam products have numerous advantages over competing products, making it easily accepted by builders, suppliers and architects.
Most importantly, unlike past products, the newer generation of glulam products, such as Rosboro's BigBeam, are now engineered to match standard l-joist depths, ranging from 9-112" , ll-7 18' , l4u, I6u , 18", and other applications, like wall framing widths of 3-112",5-7116', and 7".
"Builders like the fact that they can seamlessly use our products with other framing applications. Plus, it's a clean system and flushes up with an I-joist, so Sheetrock can be smoothly applied directly over," added Blair.
Similar products like Anthony Forest Products' Power Beam and Rosboro's IJC-Z F are available in 3-ll2" and 51/2" widths that readily match2x4 and 2x6 wall framing.
*It's3-112" that matches a3-112" application; it's 5-112" that matches a 5-112" application," Drake said. "It's used and sold in one-piece applications. LVL is like l-3l4". You have to nail and glue several pieces together."
Other benefits
Both builders and suppliers also like glulam because of its light weight. Suppliers can offer builders a light yet stable and durable product, and its reduced weight enables builders to install it more quickly than competing products.
Compared to other products like LVL, which is more dense, glulam products are also easier to nail. Builders can use "a much smaller glulam to cover the same span, as opposed to solid lumber," Calvert noted.
Glulam generally has a single-ply member, whereas LVL has several plys that need to be assembled on the jobsite. Sometimes two to three plys of LVL are required to do the work of a one-member glulam.
One of the biggest complaints from builders is that LVL never has the same depth. "When builders nail two pieces together, you're always trying to fix something," said Blair. "With glulam, the size always stays the same."
Using glulam can also means substantial cost savings.
"A lot of times, you don't need the strength of a Parallam or LVL," Calvert said. "You can use a 2400-F Doug fir glulam or a 2600-F southern pine glulam that would be cheaper than a piece of LVL or Parallam."
Known for their structural strength, glulams are also being specified by architects because they're more attractive than other products.
"Parallam is more of an industrial-grade product. We can make an architectural grade, and it's much more pleasing aesthetically than some of our competitor products," Calvert noted.
Many applications
In addition to being manufactured as a one-piece appli- cation, builders also like workhorse glulam products for a wide range of uses. Steve Szymanski of Truss Systems Inc., Little Chute, Wi., says his builder pros use Rosboro's BigBeam for tall walls, headers and beams, both structural and architectural.
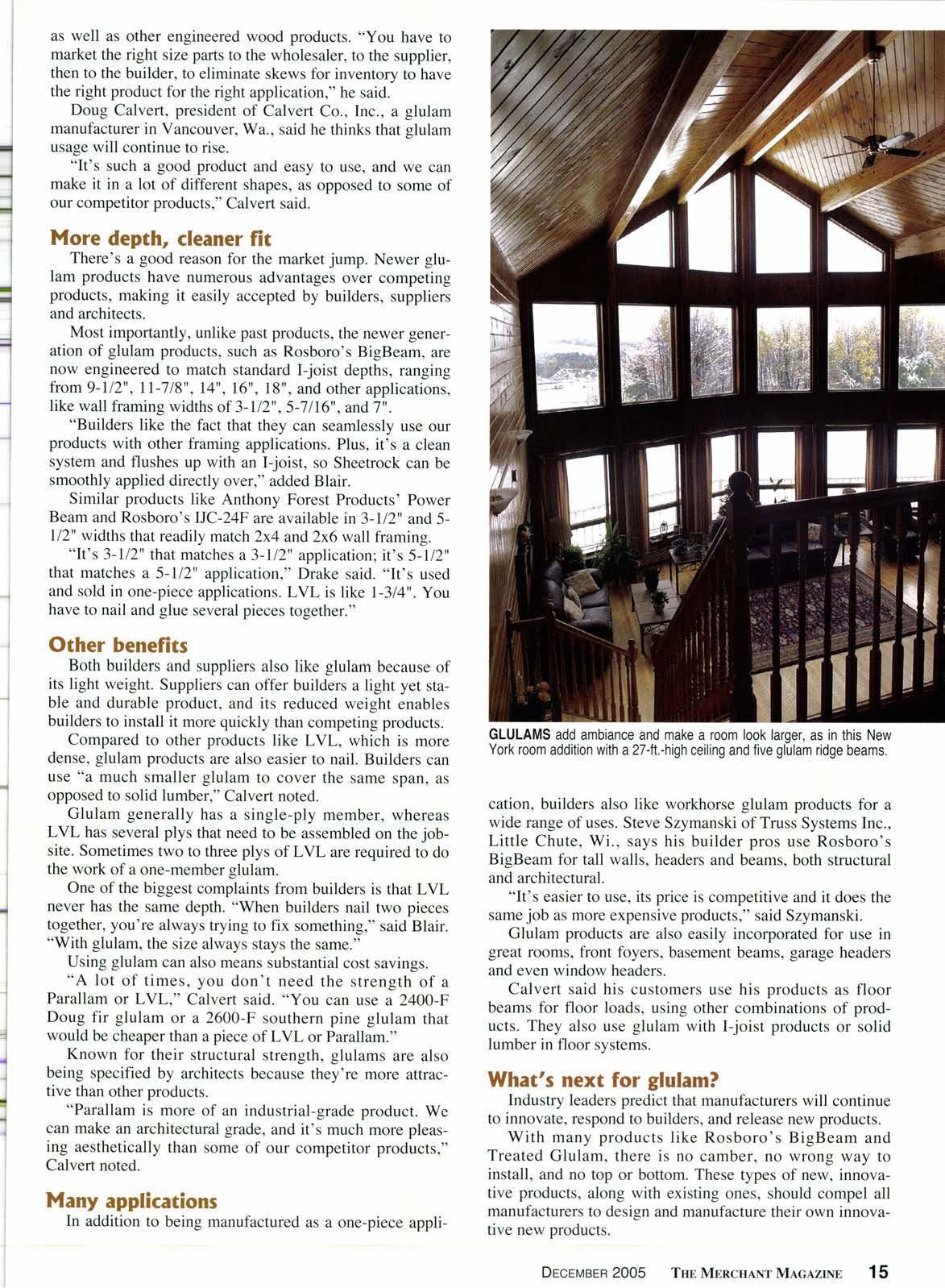
"It's easier to use, its price is competitive and it does the same job as more expensive products," said Szymanski.
Glulam products are also easily incorporated for use in great rooms, front foyers, basement beams, garage headers and even window headers.
Calvert said his customers use his products as floor beams for floor loads, using other combinations of products. They also use glulam with I-joist products or solid lumber in floor systems.
What's next for glulam?
Industry leaders predict that manufacturers will continue to innovate, respond to builders, and release new products.
With many products like Rosboro's BigBeam and Treated Glulam, there is no camber, no wrong way to install, and no top or bottom. These types of new, innovative products, along with existing ones, should compel all manufacturers to design and manufacture their own innovative new products.