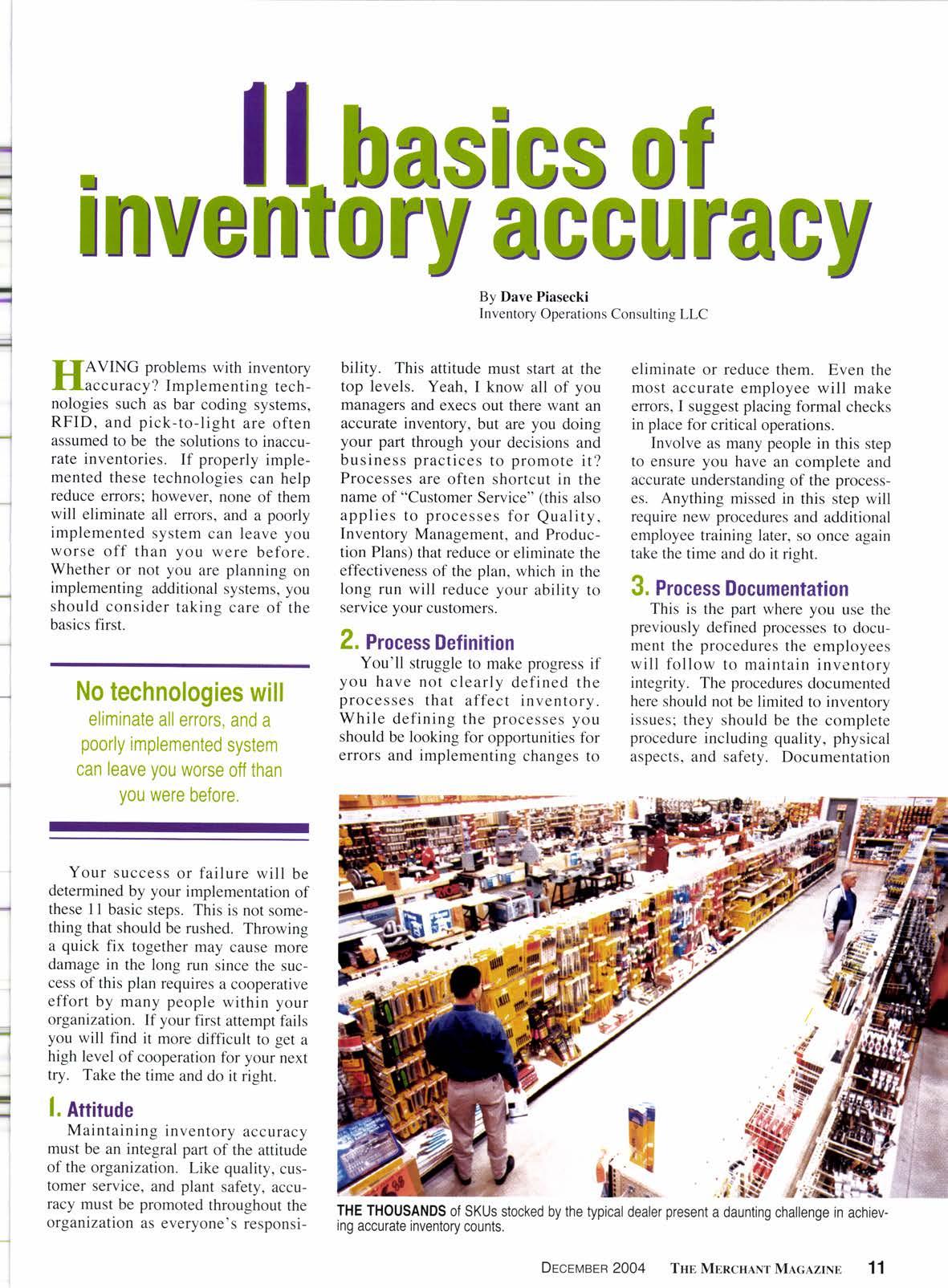
8 minute read
.h|,ory accuracy baslcs of tnv
By Dave Piasecki lnventory Operations Consulting LLC
HfJiTfl ,ti "l;ix:"1,T;1:':n
nologies such as bar coding systems, RFID, and pick-to-light are often assumed to be the solutions to inaccurate inventories. If properly implemented these technologies can help reduce errors; however, none of them will eliminate all errors, and a poorly implemented system can leave you worse off than you were before. Whether or not you are planning on implementing additional systems, you should consider takins care of the basics first.
No technologies will eliminate all errors, and a poorly implemented system can leave you worse off than you were before.
Your success or failure will be determined by your implementation of these I I basic steps. This is not something that should be rushed. Throwing a quick fix together may cause more damage in the long run since the success of this plan requires a cooperative effort by many people within your organization. If your first attempt fails you will find it more difficult to get a high level of cooperation for your next try. Take the time and do it righr.
l. Attitude
Maintaining inventory accuracy must be an integral part of the attitude of the organization. Like quality, customer service, and plant safety, accuracy must be promoted throughout the organization as everyone's responsi- bility. This attitude must start at the top levels. Yeah, I know all of you managers and execs out there want an accurate inventory, but are you doing your part through your decisions and business practices to promote it? Processes are often shortcut in the name of "Customer Service" (this also applies to processes for Quality, Inventory Management, and Production Plans) that reduce or eliminate the effectiveness of the plan, which in the long run will reduce your ability to service your customers.
2. Process Definition
You'Il struggle to make progress if you have not clearly defined the processes thataffect inventory. While defining the processes you should be looking for opportunities for errors and implementing changes to eliminate or reduce them. Even the most accurate employee will make errors, I suggest placing formal checks in place for critical operations.
Involve as many people in this step to ensure you have an complete and accurate understanding of the processes. Anything missed in this step will require new procedures and additional employee training later, so once again take the time and do it right.
3. Process Documentation
This is the part where you use the previously defined processes to document the procedures the employees will follow lo maintain inventory integrity. The procedures documented here should not be limited to inventory issues; they should be the complete procedure including quality, physical aspects, and safety. Documentation should be as clear and comprehensive as possible. It should be written for a specific task within a specific job responsibility, it should include everything the employee needs to know to complete the task and nothing else.
For example, if a stock clerk's responsibility is to notify the supervisor of any discrepancies, that is all it should state in the procedure for the stock clerk even though there will be additional procedures for dealing with the discrepancy. Procedures should also include the correct method for filling out and processing paperwork, the sequence and timing of entering data, and any checks that are required to be performed. If there are any exceptions to a procedure they should be specified in the document, allowing undocumented exceptions to a procedure will decrease its effectiveness.
Be realistic; procedures are not a "wish list," they are the documentation of the requirements of a specific task. You must be prepared to enforce compliance to all procedures.
Once you have completed the documentation, first distribute the procedures to a few key employees, then take a couple of weeks for you and the key employees to monitor existing operations to see if anything was missed or is incorrect. Then the procedures should be officially put into effect and distributed to all employees.
4. Employee Training
Handing out a written procedure does not constitute employee training. It is important to set a training schedule to go through all of the procedures with groups of employees. Take whatever time is necessary to ensure
MoreTips for a More Accurate Inventory
Dedicate positions to manage inventory. result from iust one employee's erro6. Make sure you have control of which employees are alf ecting your inventory. Don't be afraid to put Checks in place. This is especially true lor employees and Some people feel checking or rechecksupervisors consumed withmeeting sched- ing work is admhting failure or is a wasle ules, keeping operations running, and since it "should be done right the lir$Jitne,' ensuring quality control. Inventory accuracy but remember, everyone makes plislakes. will never be a primary responsibility of lf you find there are cedain"ar€as that are these lypes oJ positions. Also,within your highly prone to enorsoi"prilical parts olyour material handling/warehousepositions, limit operationwherge,gplstake canhave signifithe peopledoing miscellaneous type inven- cant detripehlaf"effect, consider putting tory adiustments.
Control employee turnover.
Fvdluate your storago.areas. -lknow, easier said than done. You've-,...' Crowded, uq"grganized areas become invested the time into training them, nqwjgr"' "black holes' for missing product. Cowded ure outwhat you needtodoto leep'them. areas also increase damage to product that Once you have gotten your,pr_o,oesses and is often disposed of without invenlory corp1scedures under control ysu'will find that rections being made. Highdensity storage .aen+ er$oyees will become your #1 source makes it difficult to accurately count prodof errors. My elpdrience shows a new uct. Maintaining propel lighting, shelf and employeegenetally makes two tofive times product labeling, and organization makes it as many,mistakes as a one-year employee easier tostock, pick and count p.roduct. and.five to 10 times as manymistakesas a five-year employee. These numbers are Know your inventory system. based _on operations that track accuracy
The more you know about how your and pfimote continuous improvement. lf specific inventory system works, the more your6 nottracking accuracy,your five-year successful you'll be in optimizing its feaemployees may be making as niany mis- tures. Computer systems are regularly takeEas they did during their first year. blamed forthings that ayeqsually turn pJllg-"
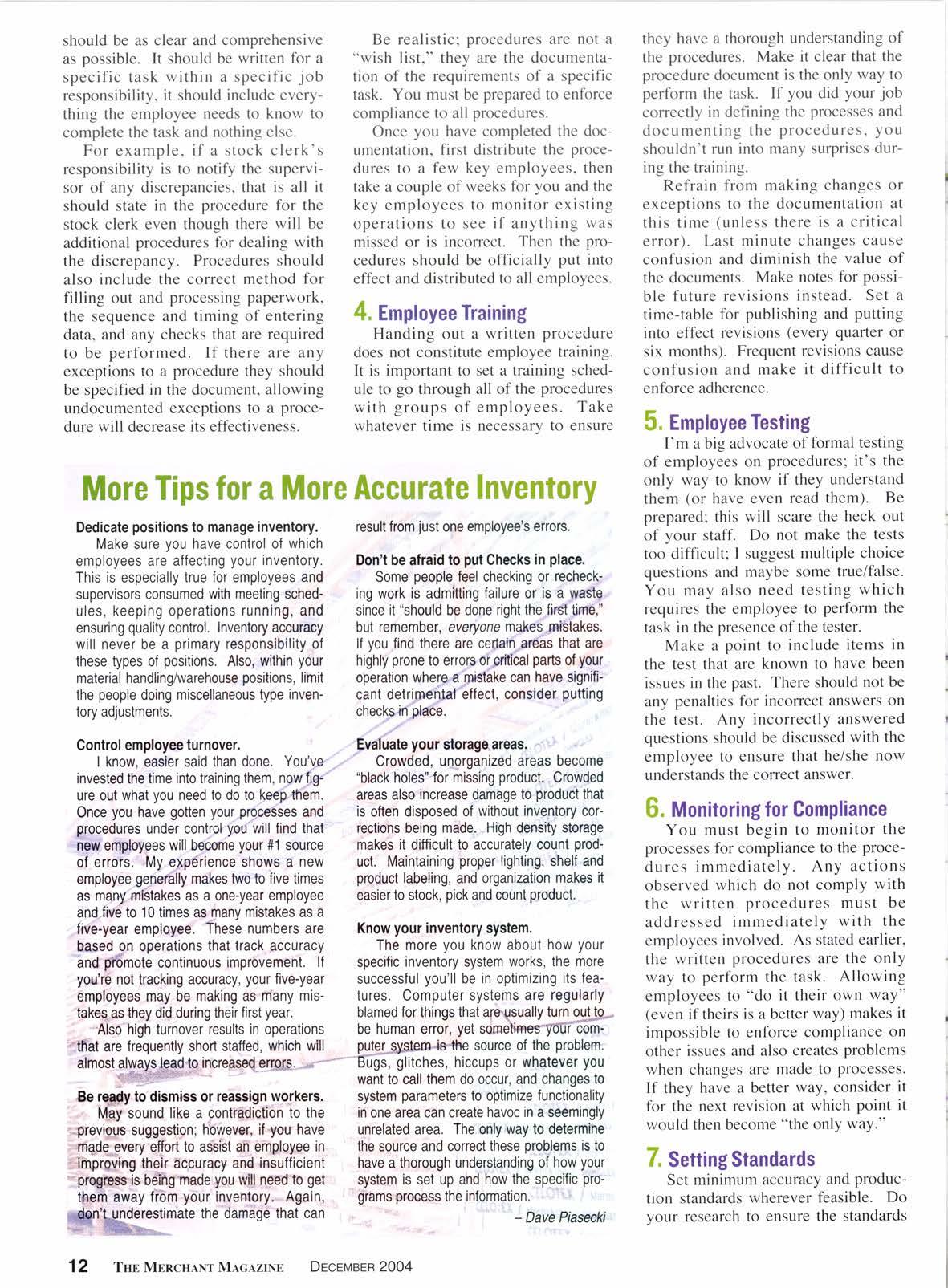
'Also high turnover results in operations be human error, yet sometmesldUf com1itfiat are frequently short staffed, which will pglgt,Syslem".ts'{he source of the problem. almostalway-sklltoincreaseQerrg;g Biigs, glitches, hiccups or whatever you ps$tt't*irs"' ' - wanttocall them do occur, and changes to Be rgly to dismiss or reassign workers. systemparameters to optimize functionality [fty sound like a conti'€dictiOn to the in one areacan create havoc in a seemingly -*?revry4p suggestion; however, if 'you have unrelated area. The only way to determine {nqde-_gryery effort to asbist an employee in the source and correct theseproblems is to tiinprpy.iry their accuraoy and insufficient haveathoroggh understanding of how your esis bdngrmde you wflt need to get system is set up and how the specific proaway fibm your inventory. Again, grams process the information. rr inver*ory. $ramsprooess in{ormation. .'r. the damage that can i - Davepiasec*i they have a thorough understanding of the procedures. Make it clear that the procedure document is the only way to perform the task. If you did your job correctly in defining the processes and documenting the procedures, you shouldn't run into many surprises during the training.
Refrain from making changes or exceptions to the documentation at this time (unless there is a critical error). Last minute changes cause confusion and diminish the value of the documents. Make notes for possible future revisions instead. Set a time-table for publishing and putting into effect revisions (every quarter or six months). Frequent revisions cause confusion and make it difficult to enforce adherence.
5. Employee Testing
I'm a big advocate of formal testing of employees on procedures; it's the only way to know if they understand them (or have even read them). Be prepared; this will scare the heck out of your staff. Do not make the tests too difficult; I suggest multiple choice questions and maybe some true/false. You may also need testing which requires the employee to perform the task in the presence of the tester.
Make a point to include items in the test that are known to have been issues in the past. There should not be any penalties for incorrect answers on the test. Any incorrectly answered questions should be discussed with the employee to ensure that he/she now understands the correct answer.
6. Monitoring for Gompliance
You must begin to monitor the processes for compliance to the procedures immediately. Any actions observed which do not comply with the written procedures must be addressed immediately with the employees involved. As stated earlier, the written procedures are the only way to perform the task. Allowing employees to "do it their own way" (even if theirs is a bcttcr way) makes it impossible to enforce compliance on other issues and also creates problems when changes are made to processes. If they have a better way, consider it for the next revision at which point it would then become "the only way."
7. Settlng Standards
Set minimum accuracy and Production standards wherever feasible. Do your research to ensure the standards are high enough and yet still achievable. You will have to enforce these standards so it is critical to set them correctly. If in doubt, set them lower, you can always increase them later when more data is available. If you set them too high you have put yourself in a difficult position when it comes time to enforce them.
B, TrackingAccuracy
Whether you have set standards or not I still suggest you track accuracy organizationally and individually. Accuracy tracking should always be measured as a percentage of total transactions. Tracking accuracy as flat numbers (number of errors) puts your more productive employees at a disadvantage and at an organizational level will be skewed by variances in business activity.
Accuracy tracking should be communicated to staff in a positive manner; it is a tool to facilitate improvement in processes and people. Just by simply tracking and communicating accuracy you'll see immediate reductions in errors even if standards are not set. We all want to be accurate; the problem is we all think that we are accurate and it's always the other guy who is makins all of the mistakes.
9. Accountability
People must be held accountable for following documented procedures. You have spent the time to document the procedures, provide the training, and the testing. If someone is not folIowing the procedures they must be dealt with with appropriate disciplinary action. It's that simple. You may be amazed as to how much just one individual not following procedures can screw up your inventory.
If you don't hold employees accountable you may as well throw out everything you have done to this point. Mistakes are mistakes and everyone makes them; however, not following a specified procedure is a conscious decision made people not doing what they were instructed to do.
10, Gount, Count, Count
We would like to believe that since we have taken the above steps we should now assume our inventory is accurate. Not necessarily. You will have to count it to determine the accuracy as well as determining areas needing additional evaluation.
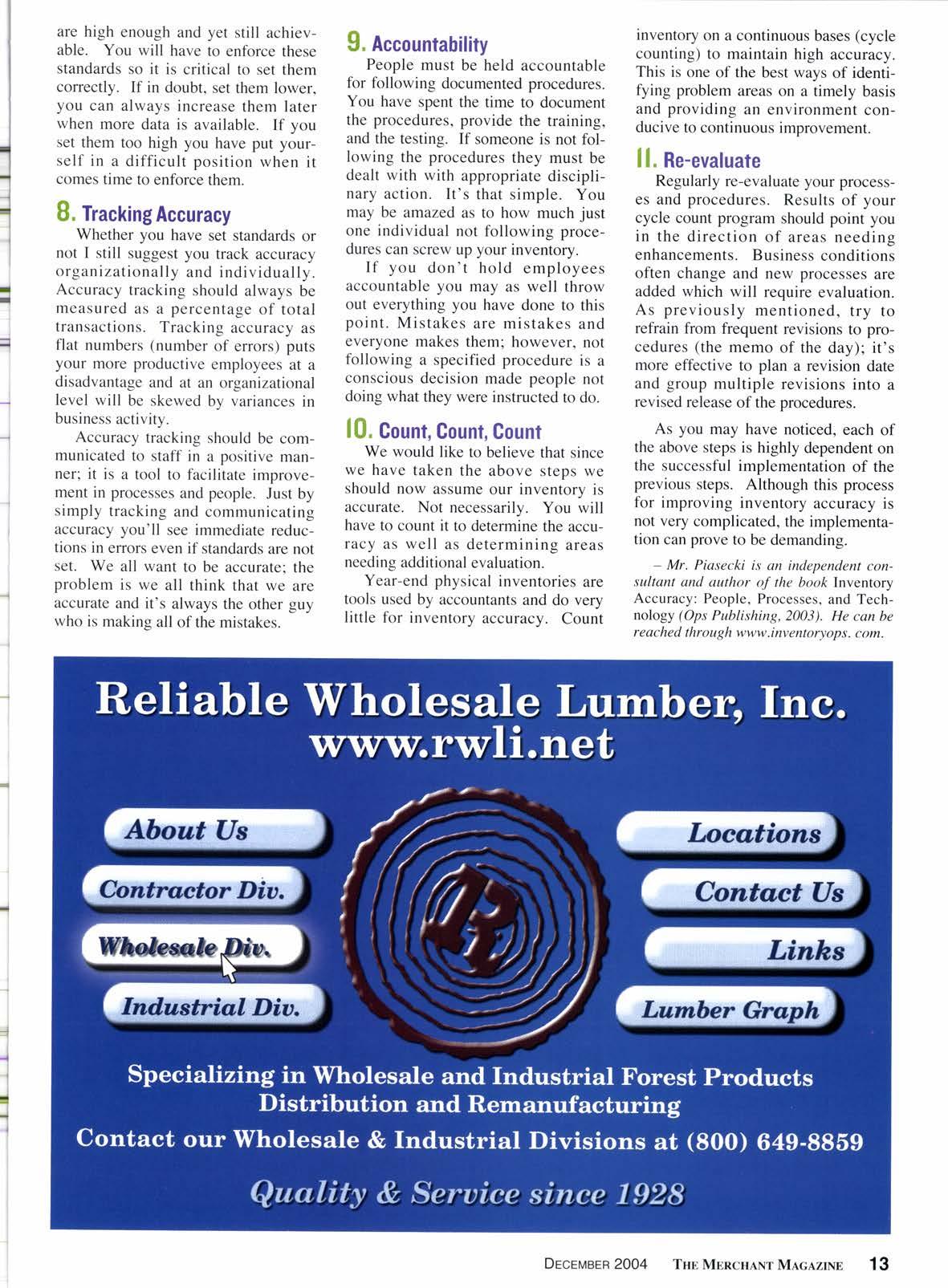
Year-end physical inventories are tools used by accountants and do very little for inventory accuracy. Count inventory on a continuous bases (cycle counting) to maintain high accuracy. This is one of the best ways of identifying problem areas on a timely basis and providing an environment conducive to continuous improvement.
ll. Re-evaluate
Regularly re-evaluate your processes and procedures. Results of your cycle count program should point you in the direction of areas needing enhancements. Business conditions often change and new processes are added which will require evaluation. As previously mentioned, try to refrain lrom frequent revisions to procedures (the memo of the day); it's more effective to plan a revision date and group multiple revisions into a revised release of the procedures.
As you may have noticed, each of the above steps is highly dependent on the successful implementation of the previous steps. Although this process for improving inventory accuracy is not very complicated, the implementation can prove to be demanding.
- Mr. Piasecki is an independent consultant and author of the book Inventory Accuracy: People, Processes, and Technology (Ops Publishing,2003). He can be reac he d thr o u gh www.inv entoryops.com.