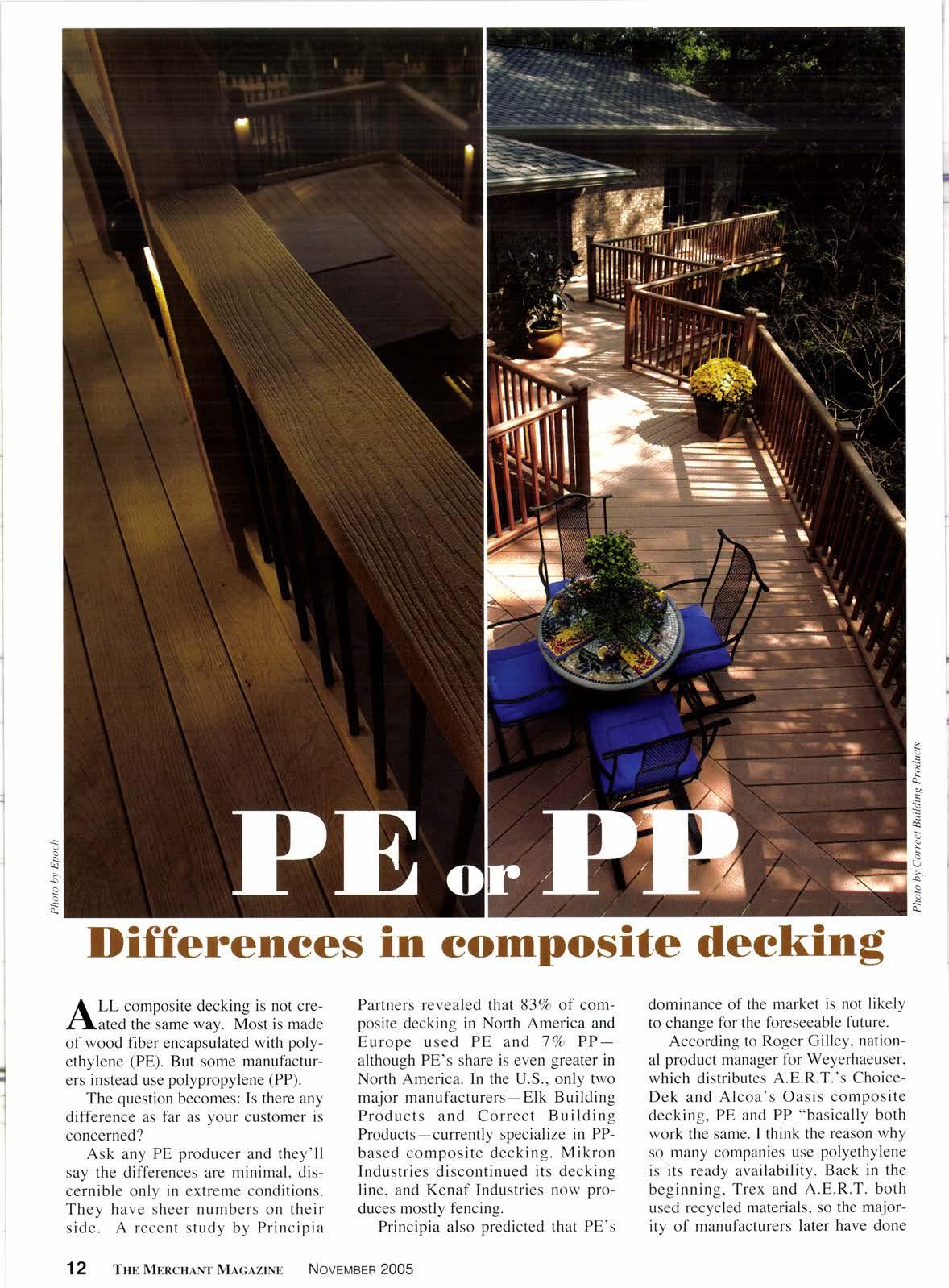
3 minute read
Differenees in eomposite deeking
A LL composite decking is not cre.Cl,ated the same way. Most is made of wood fiber encapsulated with polyethylene (PE). But some manufacturers instead use polypropylene (PP).
The question becomes: Is there any difference as far as your customer is concerned?
Ask any PE producer and they'll say the differences are minimal, discernible only in extreme conditions. They have sheer numbers on their side. A recent study by Principia
Partners revealed that 83% of composite decking in North America and Europe used PE and 1Vo PPalthough PE's share is even greater in North America. In the U.S., only two major manufacturers-Elk Building Products and Correct Building Products-currently specialize in PPbased composite decking. Mikron Industries discontinued its decking line. and Kenaf Industries now produces mostly fencing.
Principia also predicted that PE's dominance of the market is not likely to change for the foreseeable future.
According to Roger Gilley, national product manager for Weyerhaeuser, which distributes A.E.R.T.'s ChoiceDek and Alcoa's Oasis composite decking, PE and PP "basically both work the same. I think the reason why so many companies use polyethylene is its ready availability. Back in the beginning, Trex and A.E.R.T. both used recycled materials, so the majority of manufacturers later have done
Indeed. sorne PE manufacturers. such as Louisiana-Pacific WeatherBcst. tout thcir products as more environmentally friendly by advertising their "100t/o recycled content." Since PP is a plastic that contains no rec)clcd products, the recycled content of its composite decking is limited to its percentage of wood-based materials - typically about trvo-thirds.
Trex's Greg Ratlief noted four major reasons why most manufacturers choose PE:
Availability of recycled PE.
Cost of recycled PE.
. Ease of processing the PE, in wood/plast ie eomposiles.
PE's low tcmperature properties.
"There are other reasons such as translucency and static discharge," Ratlief noted. "but these are not as importflnt in rvood/plastic composites."
Bryan Buhrts, technical director for TimberTech, explained, that r.vhilc "either polymer can be formulatcd successfully, the industry really startcd rvith recycled HDPE (post consumer scrap), such as grocery bags and milk jugs. Knolving the success of the recycled product. some manufacturers naturally started with virgin HDPE to make a superior. more consistent product."
Proponents of polypropylene, horvever, are convinced their polymer makes for bettcr prtlducts. PP's advantages. they say, include:
. Higher herrt def-lection tempcrature. That's the temperature rvhere the cornposite begins to sag under load. For PP. that temperature is 210'F. fbr PE 170'F.
. A harder composite, providing bettcl scratch resistance.
A higher coefficient of friction. reportedly making it less slippery than other types of compositc or wood decking, especially rvhen rvct.
. A stiffer matcrial rvith ii lesscr tendency to bounce.
. Lorver expansion/contraction. rraking it dimensionally stable.
Little lendency to creep. meaning the deck boards do not florv or sag clver time r'vhen exposed to high tcrnperatures or loads.
Unlike PE. PP is much hardcr to process, because it has a higher softcning pclint, said Martin Grohman. president of Correct Building Products. "You only have a srnall r.vindow to get polypropylene hot and soft cnclu-sh so that it lvill encapsulate the rvood fiber." Grohman said. "There really isn't a rnelting point for polypropylerre. lts soliening point is 350'" rvell above thc softening point for polyethylene."
Grohman characterizes the extrusion process fbr PP as "challenging" because it requires high temperatures for softening the polymer rvithout crossin-e over into the scorching point for wood fibers, generally around 400'. That gives PP, which sofiens around 3-50', a relatively small window to be substantially heated so that it will become soft and malleable enough to encapsulate the wood fiber. PE, softens around 250'.
He says PP is stronger. stil'l'er. hardel and mclre durablc because it's made up of longer chains of polymer than PE. But these sarne pr()pcrties also make it a rnore difficult polymer to process.
Grohman believes composites rvith polypropylene offer the potential fbr eventual use in structural applications. "Polypropylcne really is the strongest plastic on the market, and I think the day rvill come r.vhen it will be certified for structural use." he said. "We're rvorking on it."
Yet PE manufacturers firil to see a demonstrable difference rvith PP. TimberTech, fclr clne, has evaluated both products numerous times. Its tests have confirmed PP's higher softening temperature, resulting in lcss creep at elevated tempcratures. PP also rvas shorvn to provide slightly higher modulus of elasticity (MOE) and modulus of rupture (MOR).
Yet the higher processing temperature increased cost and energy. HDPE rvas also much easier to extrude. resulting in less scrap.
And, PP was not as thermally stable. "With PP, you are required tcr add a stabilizer package, lvhich adds apploximately .02/lb. to thc comoound cost." said TimbcrTcch's
Buhrts. "You can also overcome the PP advantages of MOE, MOR and creep by adding mineral to the HDPE formulation. The addition of mineral helps in other areas, such as reducing rvater absorption. HDPE rvill have better impact propcrties rvhen compared to PP, especially cold tcmperature impact."
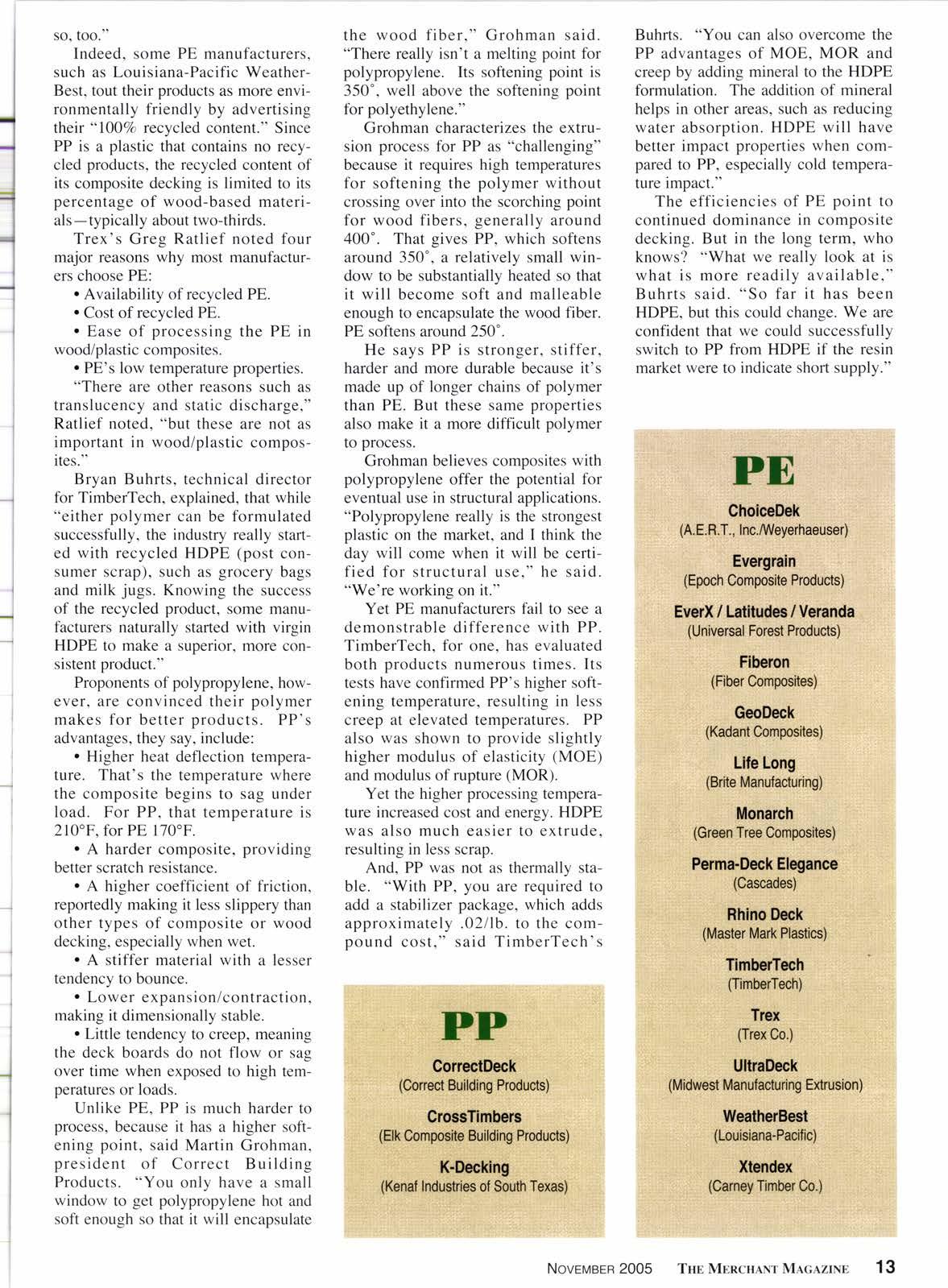
The efficiencies of PE point to c()ntinued dominance in eomposite decking. But in the long term, who knor'vs? "What rve really look at is rvhat is more readily availablc." Buhrts said. "So far it has bcen HDPE, but this could chan-se. Wc are confident that rve could successfully srvitch to PP fiom HDPE if the resin market were to indicate short supply."
ChoiceDek (A.
Evergrain {Epoch Composite Products)
EverX / Latitudes / Veranda iUniversal Forest Products) Fiberon (Fiber Composites)
GeoDeck (Kadant Composites)
Life Long (Brite Manufacturing)
Monarch (Green Tree Composiles)
Perma-Deck Elegance (Cascades)
Rhino Deck (Master Mark Plastics)
TimberTech (TimberTech)
Trex (Trex Co.)
CorrectDeck
GrossTimbers
K-Decking
UltraDeck (Midwest Manufacturing Extrusion)
WeatherBest (Louisiana-Pacific)
Xtendex {Carney Timber Co.)