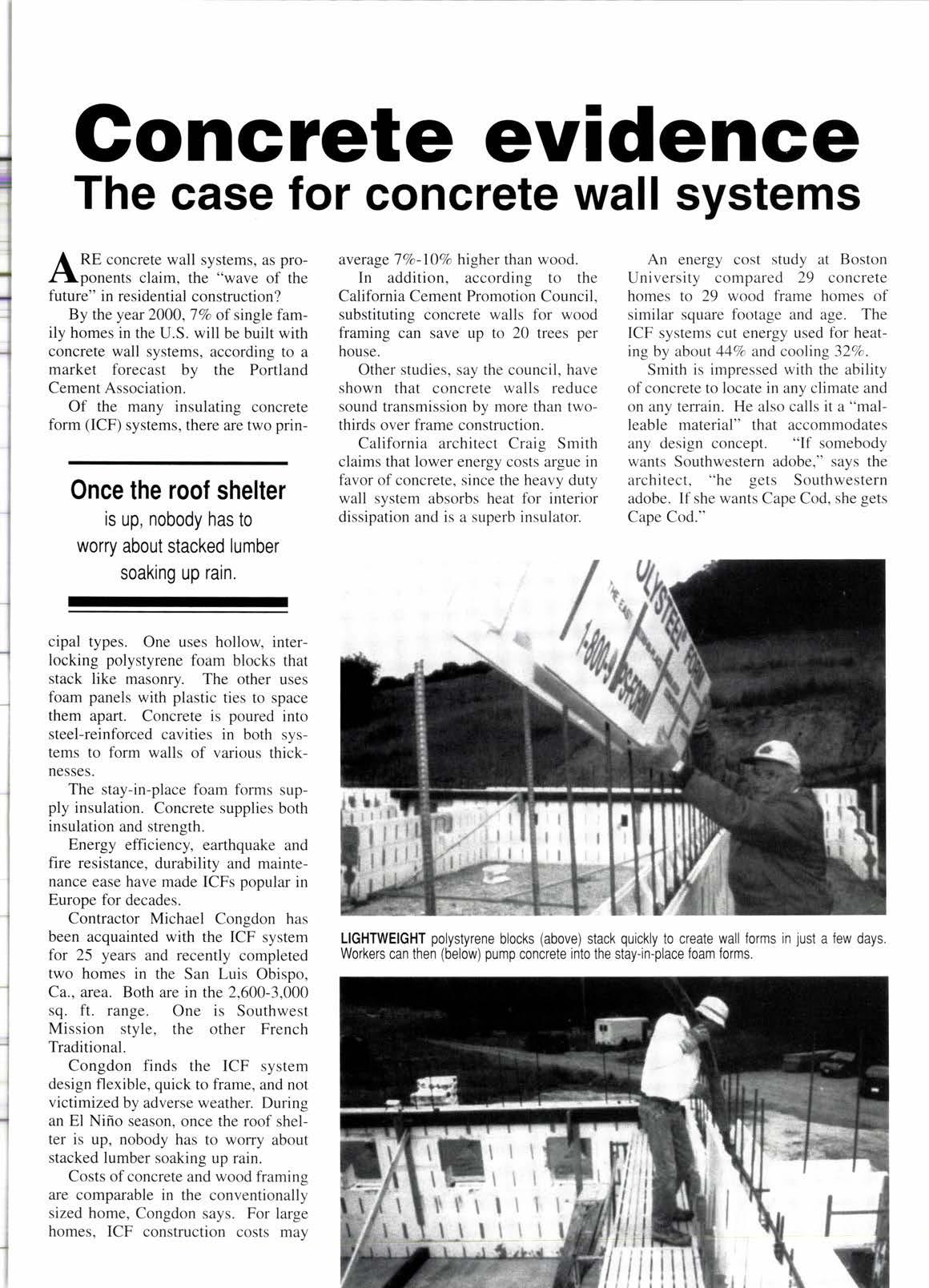
6 minute read
Concrete euidence The case for concrete wall systems
A RE concrete wall systems. as proll,ponents claim, the "wave of the future" in residential construction?
By the year 2000, 1Vo of single family homes in the U.S. will be built with concrete wall systems, according to a market forecast by the Portland Cement Association.
Of the many insulating concrete form (ICF) systems, there are two prin- average 7%o-lo%o higher than wood. cipal types. One uses hollow, interlocking polystyrene foam blocks that stack like masonry. The other uses foam panels with plastic ties to space them apart. Concrete is poured into steel-reinforced cavities in both systems to form walls of various thickNCSSES.
In addition, according to the California Cement Promotion Council, substituting concrete walls for wood framing can save up to 20 trees per house.
Other studies, say the council, have shown that concrete walls reduce sound transmission by more than twothirds over frame construction.
California architect Craig Smith claims that lower energy costs argue in favor of concrete, since the heavy duty wall system absorbs heat for interior dissipation and is a superb insulator.
An energy cost study at Boston University compared 29 concrete homes to 29 wood frame homes of similar square footage and age. The ICF systems cut energy used for heating by about 447o andcooling32%o. Smith is impressed with the ability of concrete to locate in any climate and on any terrain. He also calls it a "malleable material" that accommodates any design concept. "If somebody wants Southwestern adobe," says the architect, "he gets Southwestern adobe. If she wants Cape Cod, she gets Caoe Cod."
The stay-in-place foam forms supply insulation. Concrete supplies both insulation and strength.
Energy efficiency, earthquake and fire resistance, durability and maintenance ease have made ICFs popular in Europe for decades.
Contractor Michael Congdon has been acquainted with the ICF system for 25 years and recently completed two homes in the San Luis Obispo, Ca., area. Both are in the 2,600-3,000 sq. ft. range. One is Southwest Mission style, the other French Traditional.
Congdon finds the ICF system design flexible, quick to frame, and not victimized by adverse weather. During an El Niflo season, once the roof shelter is up, nobody has to worry about stacked lumber soaking up rain.
Costs of concrete and wood framing are comparable in the conventionally sized home, Congdon says. For large homes, ICF construction costs may
Itr/OOD composites and plastic
Y Y lumber will continue to provide real competition to wood in established applications, according to research by Principia Partners.
The new study, "Wood Composites and Plastic Lumber in North America 1999," predicts double-digit growth in North America for these substitute products for at least the next l0 years.

The researchers attribute the gains of wood composites and plastic lumber to performance advantages over traditional wood, including: x Wood composite material can be worked and then painted to look like painted wood reportedly with greater
* Plastic materials resist rot and insects, providing an inherently longer life than wood. This is especially true in outdoor applications such as decks and marine applications. Resistance to rot and insects was the catalyst for the application of Fibrex years ago when the material was used for the door sill of an exterior door frame.
The Market By Material
intrinsic durability. Further, the material can be injection or compression molded or extruded to produce complex shapes.
x Wood composites and plastic lumber can be pigmented and colorized during processing which eliminates the need to paint the surface. Ultra-violet retardant additives can be used in the melt phase to protect the colors lrom fading. again ensuring a relatively long life. This continues to be an area of further technological advancement for these products, particularly in decking uses.
* Wood composites absorb less moisture than traditional wood and have a higher modulus of elasticity than PVC, providing superior performance in demanding applications.
Economically, wood composites and plastic lumber are not inexpensive to produce, and accordingly sell for higher prices than their wood equivalents. However, total installed cost is often purported to be less than wood based on easier installation methods.
In addition. the life expectancy is such that in the long run, a wood composite can be less costly and a better investment than its wood counterpart.
Wood-thermoplastic composites use a wide range of polymers in various proportions, with the primary wood forms being fiber/flour and the primary plastic materials including low density polyethylene (PE), high density polyethylene, polyvinyl chloride (PVC), and polypropylene (PP).
Plastic lumber is defined as pre- dominantly post-consumer recycled thermoplastic material containing no wood fiber, that is extruded into various forms for use as wood replacements. The commingled plastic material is often extruded into dimensional lumber forms that can be nailed. sawn and otherwise worked like wood.
PE-based composites account for the bulk of the market today (see chart on previous page), with 322 million lbs., or 57Vo of the total volume in 1998. Each of the remaining materials-PP-based composites, PVC wood composites and plastic lumberaccount for comparable shares of the remaining market. The total size of the plastic lumber and wood composites market in 1998 was 565 million lbs. valued at approximately $220 million.
"Written specifications for structural materials are generally beyond the performance capabilities of most wood composites today," says Principia Partners analyst Lou Rossi. "As the industry matures and specifications are written with these materials considered, wood composites may gain some acceptance in more demanding applications."
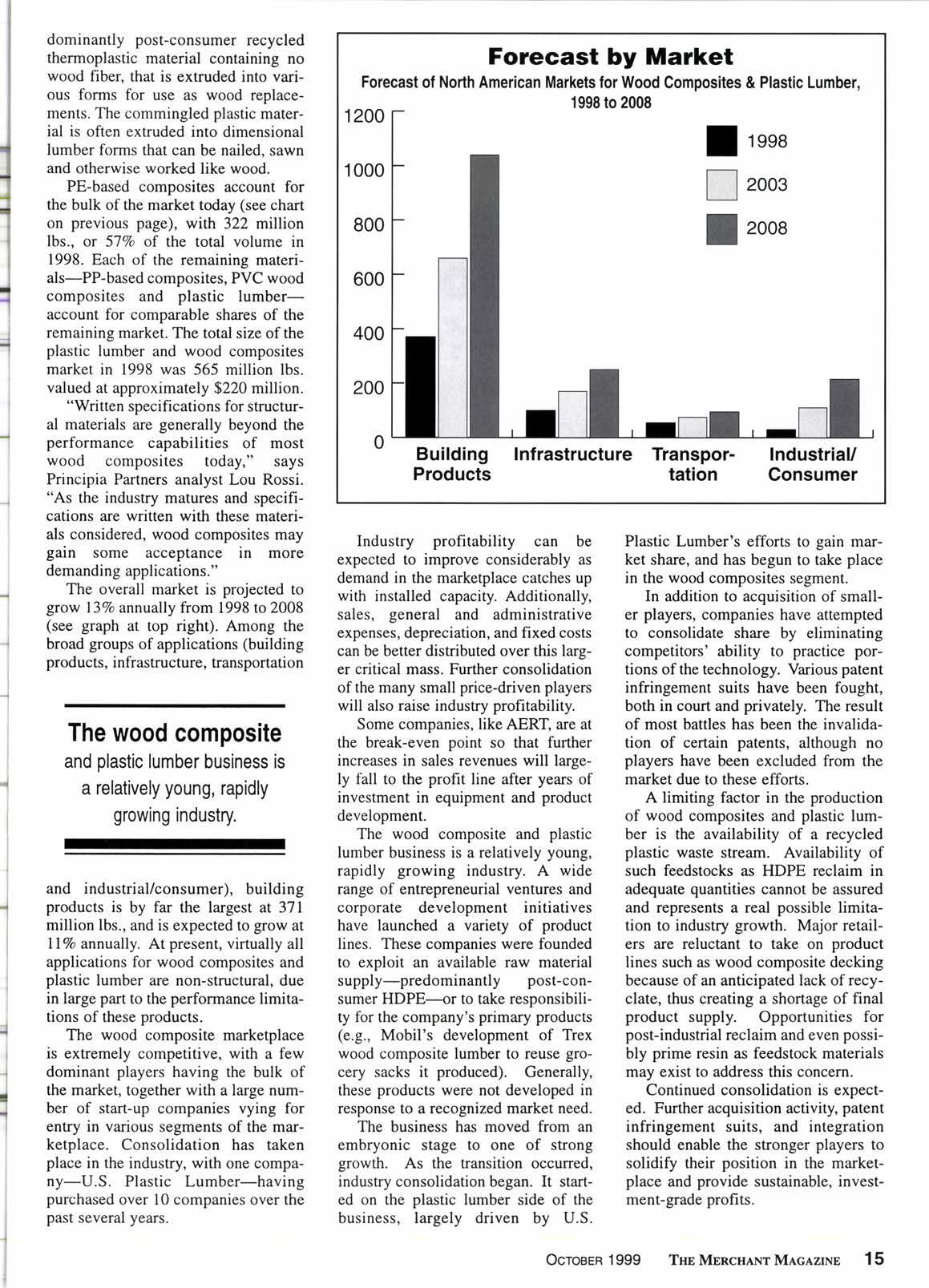
The overall market is projected to grow l3Vo annually from 1998 to 2008 (see graph at top right). Among the broad groups of applications (building products, infrastructure, transportation and industrial/consumer), building products is by far the largest at 371 million lbs., and is expected to grow at I 17o annually. At present, virtually all applications for wood composites and plastic lumber are non-structural, due in large part to the performance limitations of these products.
The wood composite and plastic lumber business is a relatively young, rapidly growing industry.
The wood composite marketplace is extremely competitive, with a few dominant players having the bulk of the market, together with a large number of start-up companies vying for entry in various segments of the marketplace. Consolidation has taken place in the industry, with one company-U.S. Plastic Lumber-having purchased over l0 companies over the past several years.
Forecast by Market
Industry profitability can be expected to improve considerably as demand in the marketplace catches up with installed capacity. Additionally, sales, general and administrative expenses, depreciation, and fixed costs can be better distributed over this larger critical mass. Further consolidation of the many small price-driven players will also raise industry profitability.
Some companies, like AERT, are at the break-even point so that further increases in sales revenues will largely fall to the profit line after years of investment in equipment and product development.
The wood composite and plastic lumber business is a relatively young, rapidly growing industry. A wide range of entrepreneurial ventures and corporate development initiatives have launched a variety of product lines. These companies were founded to exploit an available raw material supply-predominantly post-consumer HDPE-or to take responsibility for the company's primary products (e.g., Mobil's development of Trex wood composite lumber to reuse grocery sacks it produced). Generally, these products were not developed in response to a recognized market need.
The business has moved from an embryonic stage to one of strong growth. As the transition occurred, industry consolidation began. It started on the plastic lumber side of the business, largely driven by U.S.
Plastic Lumber's efforts to gain market share, and has begun to take place in the wood composites segment.
In addition to acquisition of smaller players, companies have attempted to consolidate share by eliminating competitors' ability to practice portions of the technology. Various patent infringement suits have been fought, both in court and privately. The result of most battles has been the invalidation of certain patents, although no players have been excluded from the market due to these efforts.
A limiting factor in the production of wood composites and plastic lumber is the availability of a recycled plastic waste stream. Availability of such feedstocks as HDPE reclaim in adequate quantities cannot be assured and represents a real possible limitation to industry growth. Major retailers are reluctant to take on product lines such as wood composite decking because of an anticipated lack of recyclate, thus creating a shortage of final product supply. Opportunities for post-industrial reclaim and even possibly prime resin as feedstock materials may exist to address this concern.
Continued consolidation is expected. Further acquisition activity, patent infringement suits, and integration should enable the stronger players to solidify their position in the marketplace and provide sustainable, investment-grade profis.