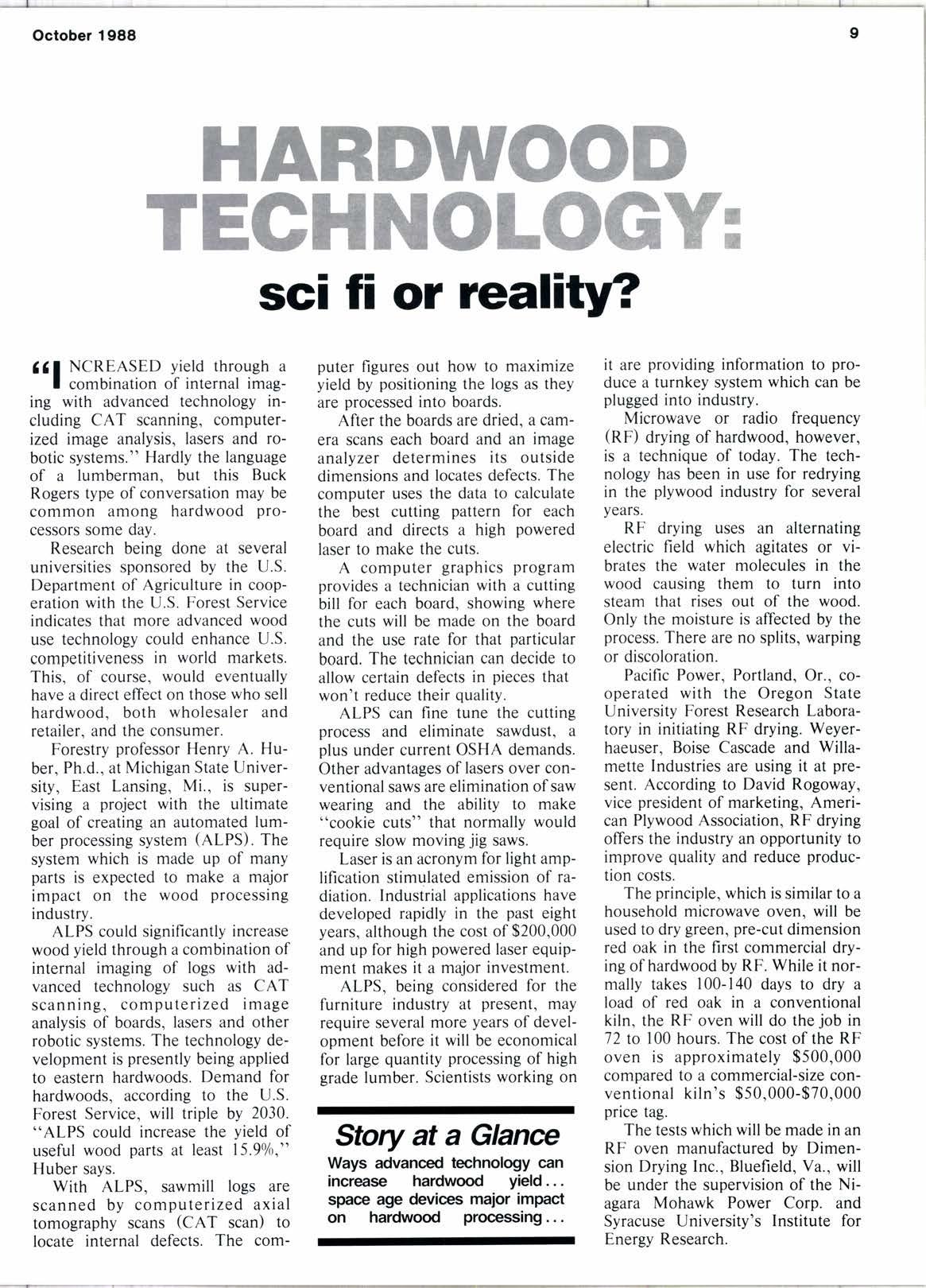
3 minute read
HAR&1'U0(}X' TEG*"XWmkffi&Wm sci fi or reality?
JJI NCREASED yield through a I combination of internal imaging with advanced technology including CAT scanning, computerized image analysis, lasers and robotic systems." Hardly the language of a lumberman, but this Buck Rogers type of conversation may be common among hardwood processors some day.
Research being done at several universities sponsored by the U.S. Department of Agriculture in cooperation with the U.S. Forest Service indicates that more advanced wood use technology could enhance U.S. competitiveness in world markets. This, of course, would eventually have a direct effect on those who sell hardwood, both wholesaler and retailer, and the consumer.
Forestry professor Henry A. Huber, Ph.d., at Michigan State University, EastLansing, Mi., is supervising a project with the ultimate goal of creating an automated lumber processing system (ALPS). The system which is made up of many parts is expected to make a major impact on the wood processing industry.
ALPS could significantly increase wood yield through a combination of internal imaging of logs with advanced technology such as CAT scanning, computerized image analysis of boards, lasers and other robotic systems. The technology development is presently being applied to eastern hardwoods. Demand for hardwoods, according to the U.S. Forest Service, will triple by 2030. "ALPS could increase the yield of useful wood parts at least 15.90/0," Huber says.
With ALPS, sawmill logs are scanned by computerized axial tomography scans (CAT scan) to locate internal defects. The com- puter figures out how to maximize yield by positioning the logs as they are processed into boards.
After the boards are dried, a camera scans each board and an image analyzer determines its outside dimensions and locates defects. The computer uses the data to calculate the best cutting pattern for each board and directs a high powered laser to make the cuts.
A computer graphics program provides a technician with a cutting bill for each board, showing where the cuts will be made onthe board and the use rate for that particular board. The technician can decide to allow certain defects in pieces that won't reduce their quality.
ALPS can fine tune the cutting process and eliminate sawdust, a plus under current OSHA demands. Other advantages of lasers over conventional saws are elimination of saw wearing and the ability to make "cookie cuts" that normally would require slow moving jig saws.
Laser is an acronym for light amplification stimulated emission of radiation. Industrial applications have developed rapidly in the past eight years, although the cost of $200,000 and up for high powered laser equipment makes it a major investment.
ALPS, being considered for the furniture industry at present, may require several more years of development before it will be economical for large quantity processing of high grade lumber. Scientists working on
Story at a Glane
Ways advanced technology can increase hardwood yield.. space age devices major impact on hardwood processing...
it are providing information to produce a turnkey system which can be plugged into industry.
Microwave or radio frequency (RF) drying of hardwood, however, is a technique of today. The technology has been in use for redrying in the plywood industry for several years.
RF drying uses an alternating electric field which agitates or vibrates the water molecules in the wood causing them to turn into steam that rises out of the wood. Only the moisture is affected by the process. There are no splits, warping or discoloration.
Pacific Power, Portland, Or., cooperated with the oregon state University Forest Research Laboratory in initiating RF drying. Weyerhaeuser, Boise Cascade and Willamette Industries are using it at present. According to David Rogoway, vice president of marketing, American Plywood Association, RF drying offers the industry an opportunity to improve quality and reduce production costs.
The principle, which is similar to a household microwave oven, will be used to dry green, pre-cut dimension red oak in the first commercial drying of hardwood by RF. While it normally takes 100-140 days to dry a load of red oak in a conventional kiln, the RF oven will do the job in 72 to 100 hours. The cost of the RF oven is approximately $500,000 compared to a commercial-size conventional kiln's $50.000-$70.000 price tag.
The tests which will be made in an RF oven manufactured by Dimension Drying Inc., Bluefield, Va., will be under the supervision of the Niagara Mohawk Power Corp. and Syracuse University's Institute for Energy Research.