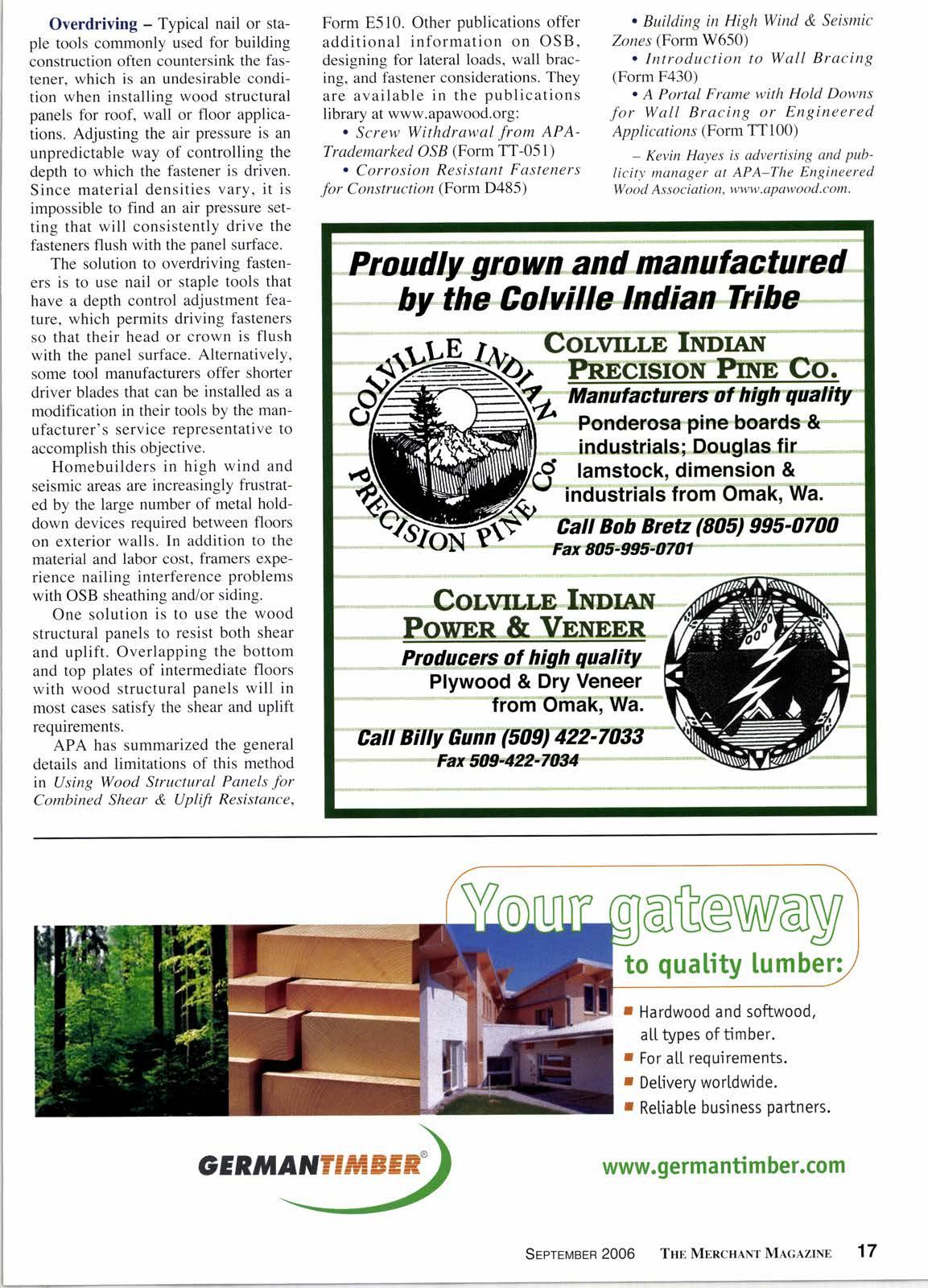
3 minute read
critical in nditions
By Kevin Hayes APA-The Eneineered Wood Association
the actual sheathing is l9l32" with all fasteners overdriven l/8". the net result is a 15132" panel that meets the design shear requirements.
guidelines help determine the affect of overdriven fasteners.
(l) If all nails are overdriven into panels by up to l/l6" during constnrction under dry conditions (moisture content less than 16%o), no reduction in shear capacity is necessary.
(2) If no more than 20Vc of the fasteners around the panel perimeter are overdriven by l/16" to l/8". no reduction in shear capacity is necessary.
(3) If all fasteners around the panel perimeter appear to be overdriven by the same amount, and it appears that panels have been rvetted during construction, no reduction in shear capacity is necessary. (It can be assumed that the fastener embedment is due to panel thickness swelling. This can be verified by measuring the thickness of panels where fasteners appear to be overdriven, and comparing to measurements where panels have been protected from the weather or to the original nominal panel thickness. which is part of the APA trademark.)
(4) If actual panels used in construction are thicker than the required minimum nominal panel thickness upon which the design shear capacity is based, and the overdriving is less than or equal to the difference between the two panel thicknesses. then no reduction in shear capacity is necessary.
For example, if design shear for the construction requires a l5/32" minimum nominal panel thickness and
(5) If more than 20Vc of the fastenen around the perimeter of panels are overdriven by more than l/16" or if any are overdriven by more than l/8". additional fasteners shall be driven to maintain the required shear capacity. For every two fasteners overdriven. one additional fastener shall be driven. If nails were used in the original installation. and are spaced too close to allow the placement of additional nails. then approved staples must b€ used for the additional fasteners required.
Porver-driven fasteners are an acceptable substitute for hand-driven fasteners provided they are of equivalent size and quality. Several things should be considered rvhen using porver-driven fasteners. including:
Contact - Lightweight, pneumatic nail or staple tools do not provide sufficient force against the panel to ensure that the panel is tight against the framing. This can cause problems rvith fastener "pop" or squeaks rvhen fastening floor sheathing or underlayment. Norrnally the force required to eliminate gaps beneath underlayment or floor sheathing can be provided by the operator if he stands on the panel. or applies hand pressure adjacent to rvhere the fastener is being driven.
Thin Galvanizing - Power-driven fasteners must be smooth and uniform in diameter to avoid jamming the feed mechanism of the nail or staple tool. The usual electrogalvanizing, which provides the required smoothness. is too thin to provide long-term corrosion resistance. Where a high degree of corrosion resistance is required. it rvill usually be necessary to use fastenen of materials that do not conode. such as aluminum or stainless steel.
Overdriving - Typical nail or staple tools commonly used for building construction often countersink the fastener, which is an undesirable condition when installing wood structural panels for roof, wall or floor applications. Adjusting the air pressure is an unpredictable way of controlling the depth to which the fastener is driven. Since material densities vary, it is impossible to find an air pressure setting that will consistently drive the fasteners flush with the panel surface.
The solution to overdriving fasteners is to use nail or staple tools that have a depth control adjustment feature, which permits driving fasteners so that their head or crown is flush with the panel surface. Alternatively, some tool manufacturers offer shorter driver blades that can be installed as a modification in their tools by the manufacturer's service representative to accomplish this objective.
Homebuilders in high wind and seismic areas are increasingly frustrated by the large number of metal holddown devices required between floors on exterior walls. In addition to the material and labor cost, framers experience nailing interference problems with OSB sheathing and/or siding.
One solution is to use the wood structural panels to resist both shear and uplift. Overlapping the bottom and top plates of intermediate floors with wood structural panels will in most cases satisfy the shear and uplift requirements.
APA has summarized the general details and limitations of this method in Using Wood Structural Panels for Combined Shear & Uplift Resistance,
Form E510. Other publications offer additional information on OSB, designing for lateral loads, wall bracing, and fastener considerations. They are available in the publications library at www. apawood.org:
. Screw Withdrawal from APATrademarked OSB (Form TT-051)
. Corrosion Resistant Fasteners for Construction (Form D485)
. Building in High Wind & Seismic Zones (Formw650)
. Introduction to Wall Bracing (Form F430)
A Portal Frame with Hold Downs for Wall Bracing or Engineered Applications (Form TT 100)
- Kevin Hayes is advertising and publicity manager at APA-The Engineered