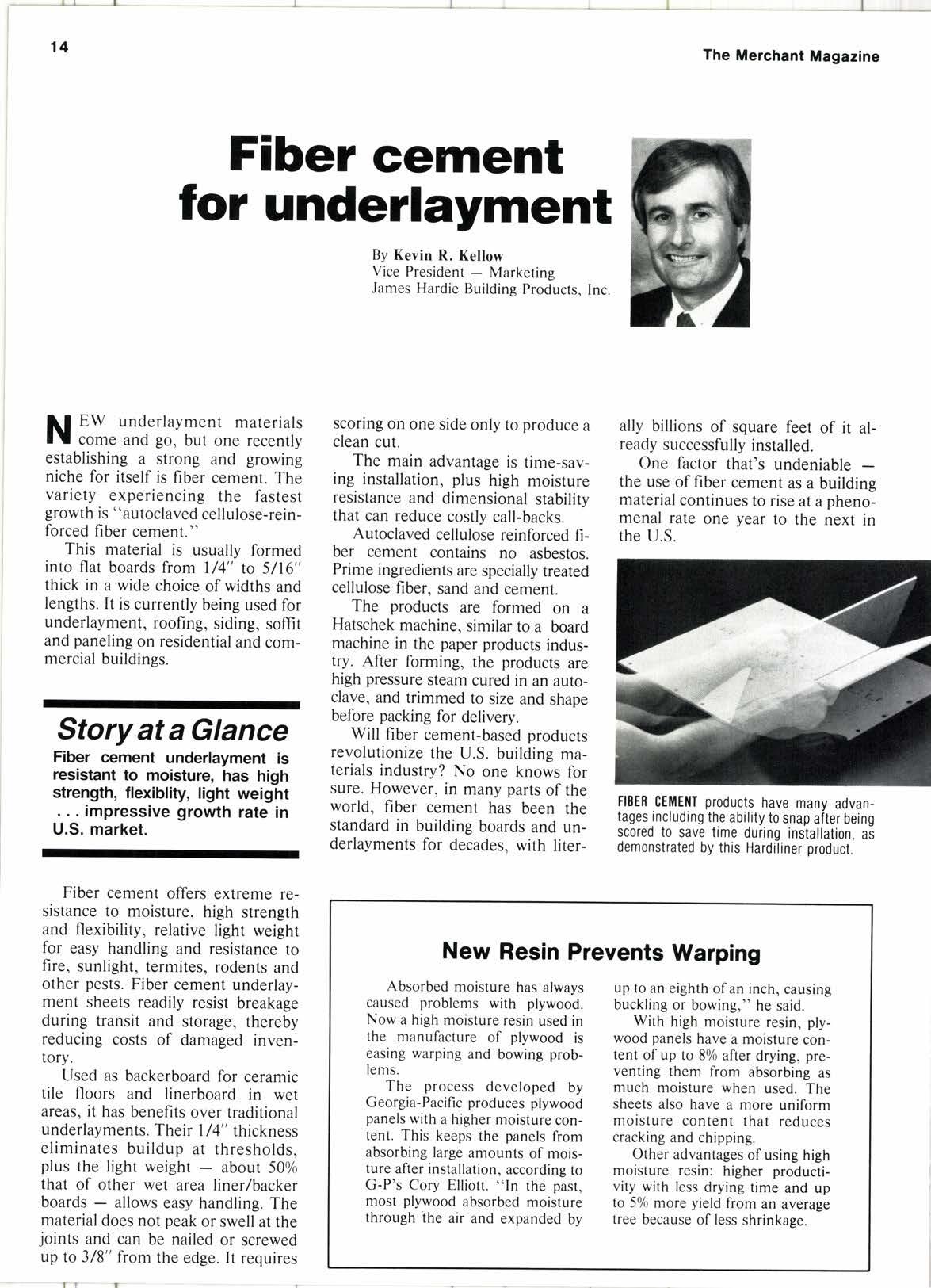
2 minute read
Fiber cement for underlayment
By Kevin R. Kellow Vice President - Marketing
James Hardie Building Products, Inc.
ll EW underlayment materials
|
! come and go, but one recently establishing a strong and growing niche for itself is fiber cement. The variety experiencing the fastest growth is "autoclaved cellulose-reinforced fiber cement."
This material is usually formed into flat boards from l/4" to 5/16" thick in a wide choice of widths and lengths. It is currently being used for underlayment, roofing, siding, soffit and paneling on residential and commercial buildings.
Story at a Glance
Fiber cement underlayment is resistant to moisture, has high strength, flexiblity, light weight . impressive growth rate in U.S. market.
Fiber cement offers extreme resistance to moisture, high strength and flexibility, relative light weight for easy handling and resistance to fire, sunlight, termites, rodents and other pests. Fiber cement underlayment sheets readily resist breakage during transit and storage, thereby reducing costs of damaged inventory.
Used as backerboard for ceramic tile floors and linerboard in wet areas, it has benefits over traditional underlayments. Their 1/4" thickness eliminates buildup at thresholds, plus the light weight - about 50% that of other wet area liner/backer boards - allows easy handling. The material does not peak or swell at the joints and can be nailed or screwed up to 3/8" from the edge. It requires scoring on one side only to produce a clean cut.
The main advantage is time-saving installation, plus high moisture resistance and dimensional stability that can reduce costly call-backs.
Autoclaved cellulose reinforced fiber cement contains no asbestos. Prime ingredients are specially treated cellulose fiber, sand and cement.
The products are formed on a Hatschek machine. similar to a board machine in the paper products industry. After forming, the products are high pressure steam cured in an autoclave, and trimmed to size and shape before packing for delivery.
Will fiber cement-based products revolutionize the U.S. building materials industry? No one knows for sure. However, in many parts of the world, fiber cement has been the standard in building boards and underlayments for decades, with liter- ally billions of square feet of it already successfully installed.
One factor that's undeniablethe use of fiber cement as a building material continues to rise at a phenomenal rate one year to the next in the U.S.
New Resin Prevents Warping
Absorbed moisture has always caused problems with plywood. Now a high moisture resin used in the manufacture of plywood is easing warping and bowing problems.
The process developed by Georgia-Pacifi c produces plywood panels with a higher moisture content. This keeps the panels from absorbing large amounts of moisture after installation, according to G-P's Cory Elliott. "ln the past, most plywood absorbed moisture through the air and expanded by up to an eighth of an inch, causing buckling or bowing," he said.
With high moisture resin, plywood panels have a moisture content of up to 80/o after drying, preventing them from absorbing as much moisture when used. The sheets also have a more uniform moisture content that reduces cracking and chipping.
Other advantages of using high moisture resin: higher productivity with less drying time and up to 5olo more yield from an average tree because of less shrinkage.