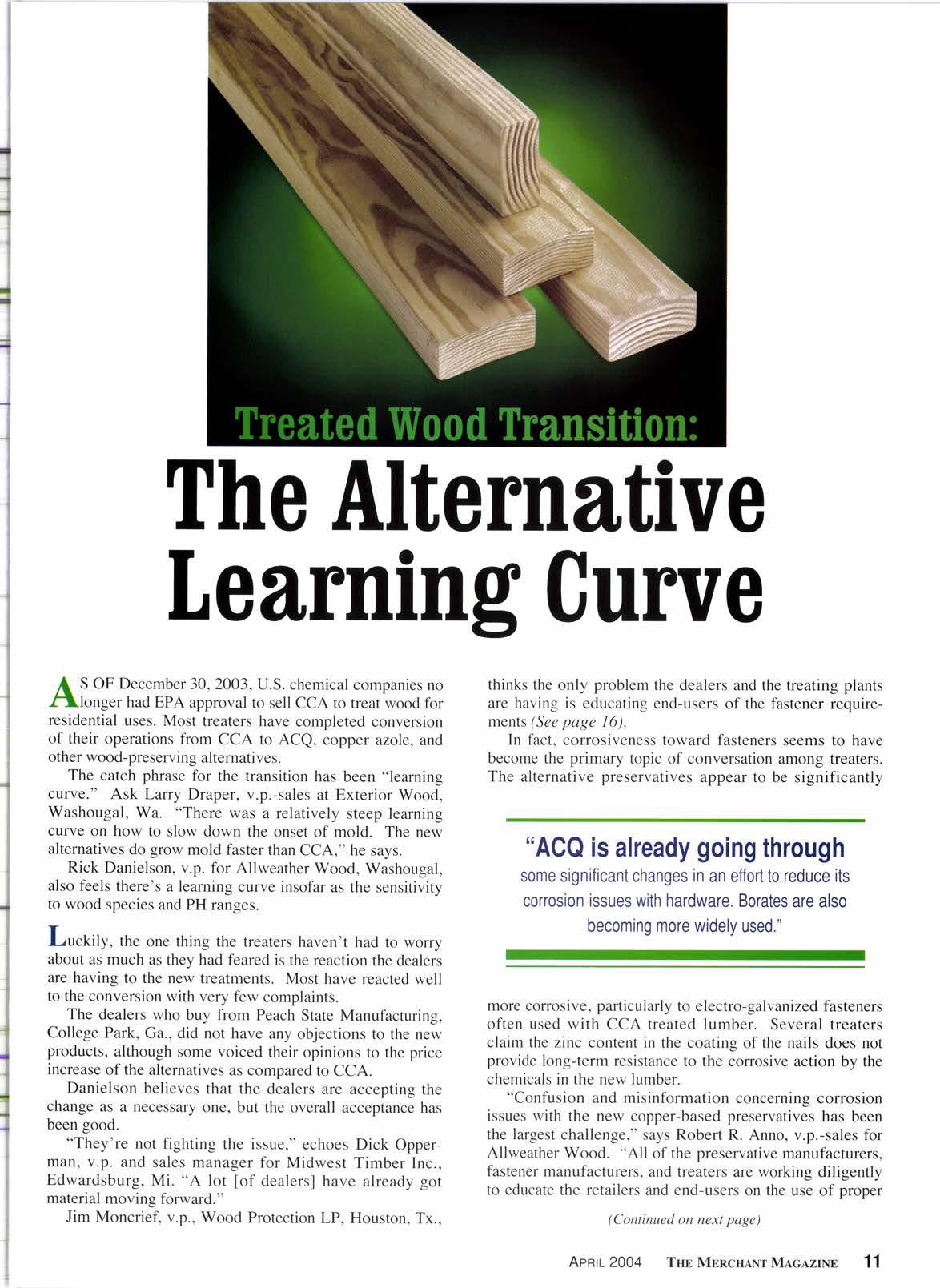
2 minute read
The Alternative learning Curve
A S OF December 30. 2003. U.S. chemical companies no .Cl,longer had EPA approval to sell CCA to treat wood for residential uses. Most treaters have completed conversion of their operations from CCA to ACQ, copper azole, and other wood-preserving alternatives.
The catch phrase for the transition has been "learning curve." Ask Lany Draper, v.p.-sales at Exterior Wood, Washougal, Wa. "There was a relatively steep learning curve on how to slow down the onset of mold. The new alternatives do grow mold faster than CCA," he says.
Rick Danielson, v.p. for Allweather Wood, Washougal, also feels there's a learning curve insofar as the sensitivity to wood species and PH ranges.
l:uckily. the one thing the treaters haven't had to worry about as much as they had feared is the reaction the dealers are having to the new treatments. Most have reacted well to the conversion with very few complaints.
The dealers who buy from Peach State Manufacturing, College Park, Ga., did not have any objections to the new products, although some voiced their opinions to the price increase of the alternatives as compared to CCA.
Danielson believes that the dealers are accepting the change as a necessary one, but the overall acceptance has been good.
"They're not fighting the issue," echoes Dick Opperman, v.p. and sales manager for Midwest Timber Inc., Edwardsburg, Mi. "A lot [of dealers] have already got material moving forward."
Jim Moncrief, v.p., Wood Protection LP, Houston, Tx., thinks the only problem the dealers and the treating plants are having is educating end-users of the fastener requirements (See page 16).
In fact. corrosiveness toward fasteners seems to have become the primary topic of conversation among treaters. The alternative preservatives appear to be significantly some significant changes in an effort to reduce its corrosion issues with hardware. Borates are also becoming more widely used." more corrosive, particularly to electro-galvanized fasteners often used with CCA treated lumber. Several treaters claim the zinc content in the coating of the nails does not provide long-term resistance to the conosive action by the chemicals in the new lumber.
"Confusion and misinformation concerning corrosion issues with the new copper-based preservatives has been the largest challenge," says Robert R. Anno, v.p.-sales for Allweather Wood. "All of the preservative manufacturers, fastener manufacturers, and treaters are working diligently to educate the retailers and end-users on the use of proper
(Continued on next page)
Treated Wood Transition
(Continued from previous page) fasteners with the copper-based preservatives."
Tom Evans, president of Coastal Treated Lumber, Hopwood, Pa., agrees: "Most of the grumbling is about having to stick different fasteners. Some dealers are still unsure about what retentions they need for their marketing. For example, while dealers in Raleigh, N.C., are happy with dimension lumber treated to .25, dealers on the outer banks not three hours away want .40."
Heather Rockwell, general manager at Bestway of New England, Lancaser, Ma., has heard objections about the cost of the fasteners and concerns that the fasteners won't disintegrate when used with ACQ treated wood.
"We looked at both CCA and ACQ, but there are corrosion issues and terrible issues with mold," says David Bond, director of operations at Permapost, Hillsboro, Or. "The chemical companies haven't solved the problem yet."
Due to the chemical and processing changes, the new lumber is more expensive than CCA. The change in price, however, generally has not affected sales.
"The only reason that the marketplace did not accept ACQ earlier is the basic fact that those in construction are