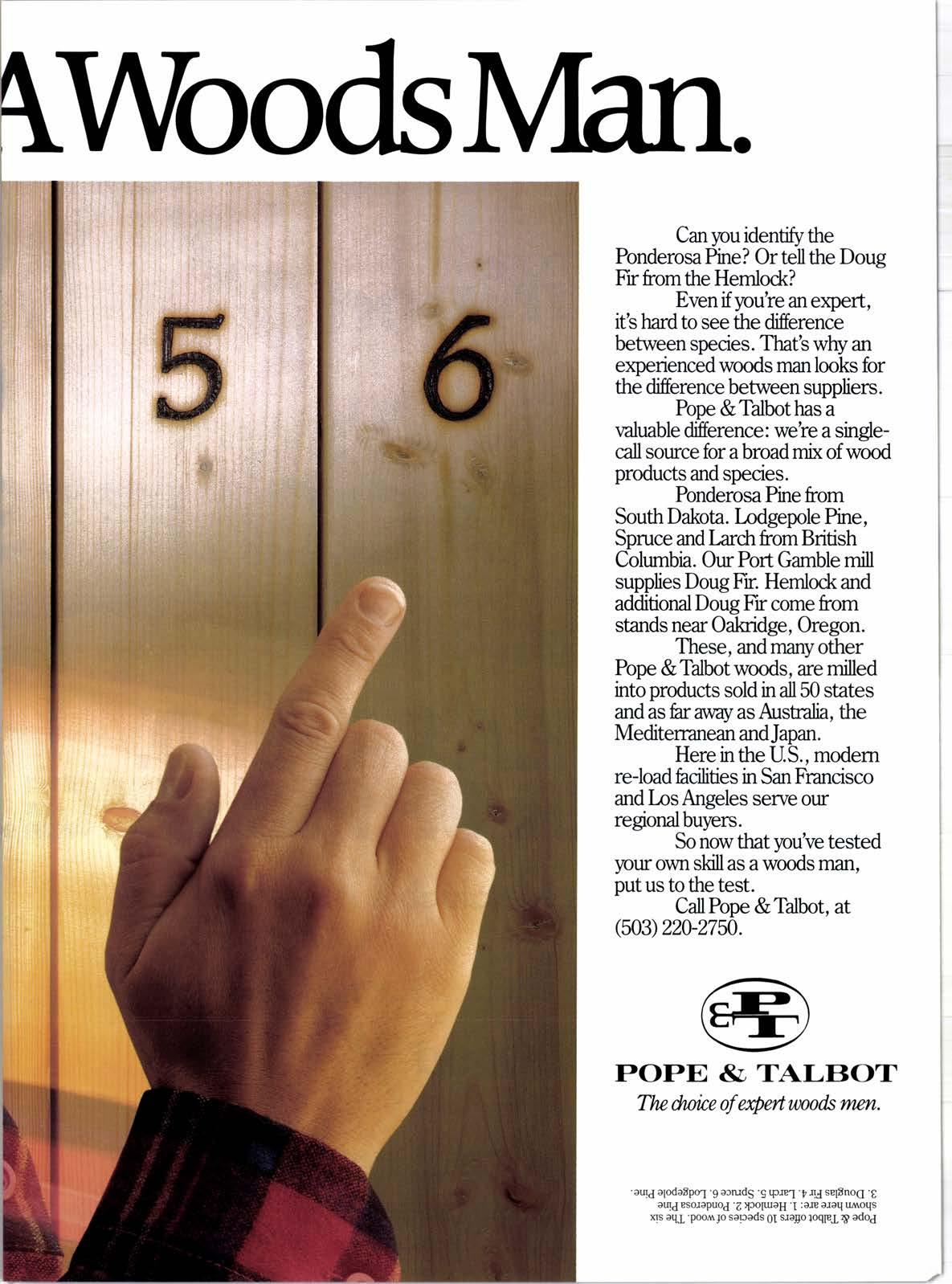
5 minute read
lreods
.
Can you identify the Ponderosa Pine? Or tellthe Doug Firfromthe Hernlock?
Evenif you're an expeft, it's hard to see the difference between species. That's why an experienced woods man looks for the difference between suppliers.
Pope &Talbothas a r,aluable difference: we're a singlecall source for a broad mix of wood products and species.
Ponderosa Pine from South Dakota. l,odgepole Pine, Spruce and Larch from British Columbia. Our Port Gamble mill supplies Doug Flr. Hemlock and additional Doug Fir come from stands near Oakridge, Oregon. These, and many other Pope &Talbotwoods, are milled into products sold in all50 states and as fu auray as Australia, the Meditenznean and Japan. Here in the U.S., modern reload hcilities in San Francisco and [,os Angeles serve our regional buyers.
So now that youVe tested your own shll as a woods man, put us to the test.
CallPope &Talbot, at (503)220-2750.
POPE & TALEBOT
The dnite of exbertwoods m.en.
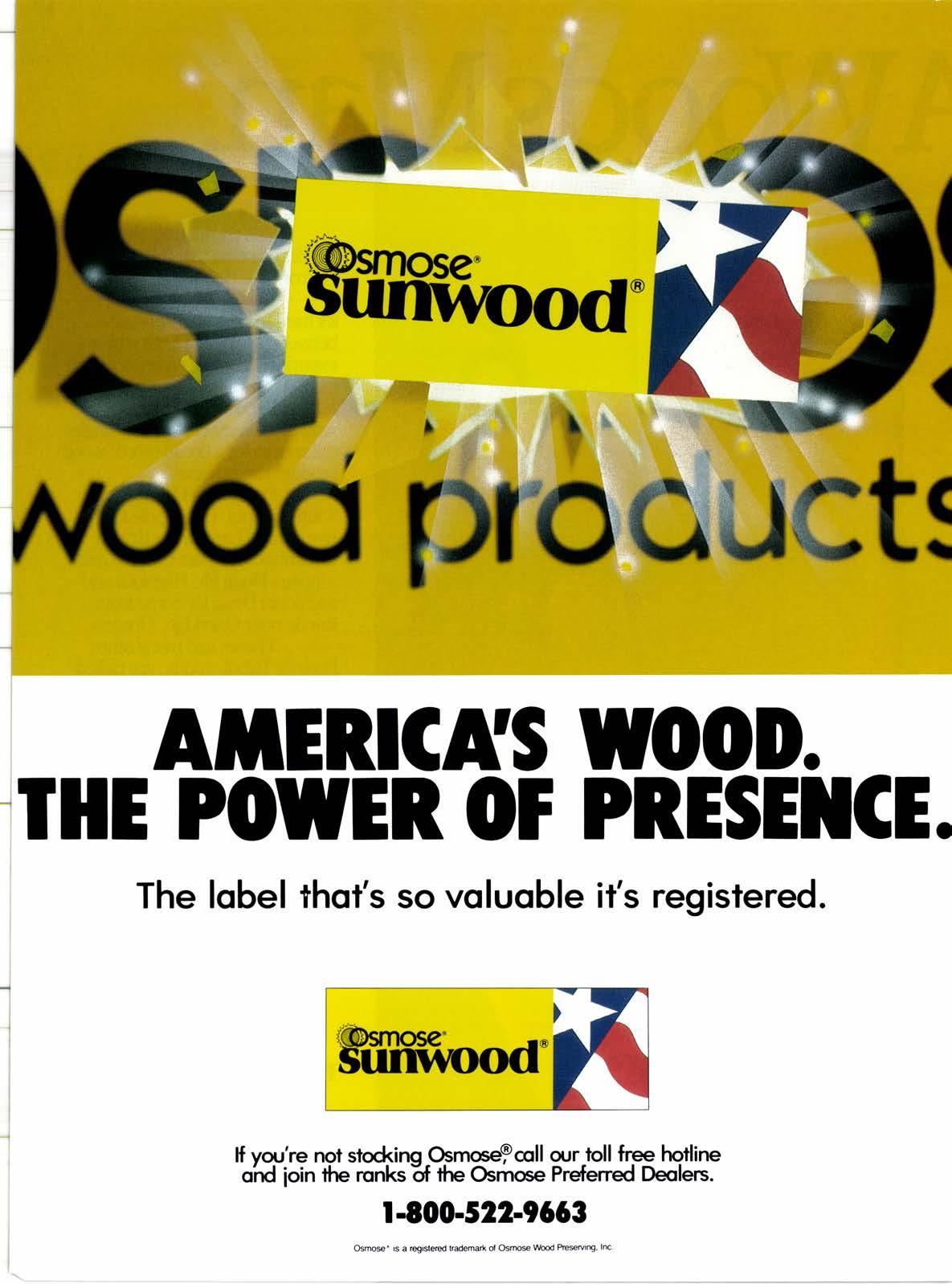
Eugene Planing Mill Retirement
Ansel Hyland has retired from his family's Eugene Planing Mill in Eugene, Or., after more than 60 vears.
G raduating from high school in 1928, he joined his father, Wilbur, at the mill which his grandfather, Clarence Somers, had started in 1904. At that time, the operation was housed in one building on the southeast corner of Third Avenue and Lawrence Street. It now is a complex of seven buildings spread over more than 200,000 sq. ft. ofspace on all four corners of the intersection.
"We just slowly expanded," Hyland says. "When a vacant lot or a house came up for sale, we bought it, some for as little as $1,000. In all 14 homes or lots have gone into the three square block building complex."
Hyland has seen many changes in the business. He recalls. "There was just my dad and me and three employees during the depression. Cabinet makers earned 25 cents an hour. I never received a salary from l!28 until 1934. I lived at home and worked for my board and room an{ clothing."
The business was started by Somers, who came to Eugene from Nebraska, as a remanufacturing and finishing mill for the small sawmills scattered through the area. Hyland's fatherjoined the planing mill in 1922 and later took over. Hyland remembers that his mother, sister and two younger brothers also helped out in the business. "Our dad took us to a movie at the old Rex Theater every Saturday night," he says. "That was our incentive for working."
The mill thrived in World War II and the years following. A $500,000 fire in the dry kiln and two warehouses filled with lumber slowed its progress in 1964. However, the firm soon rebuilt and continued to expand.
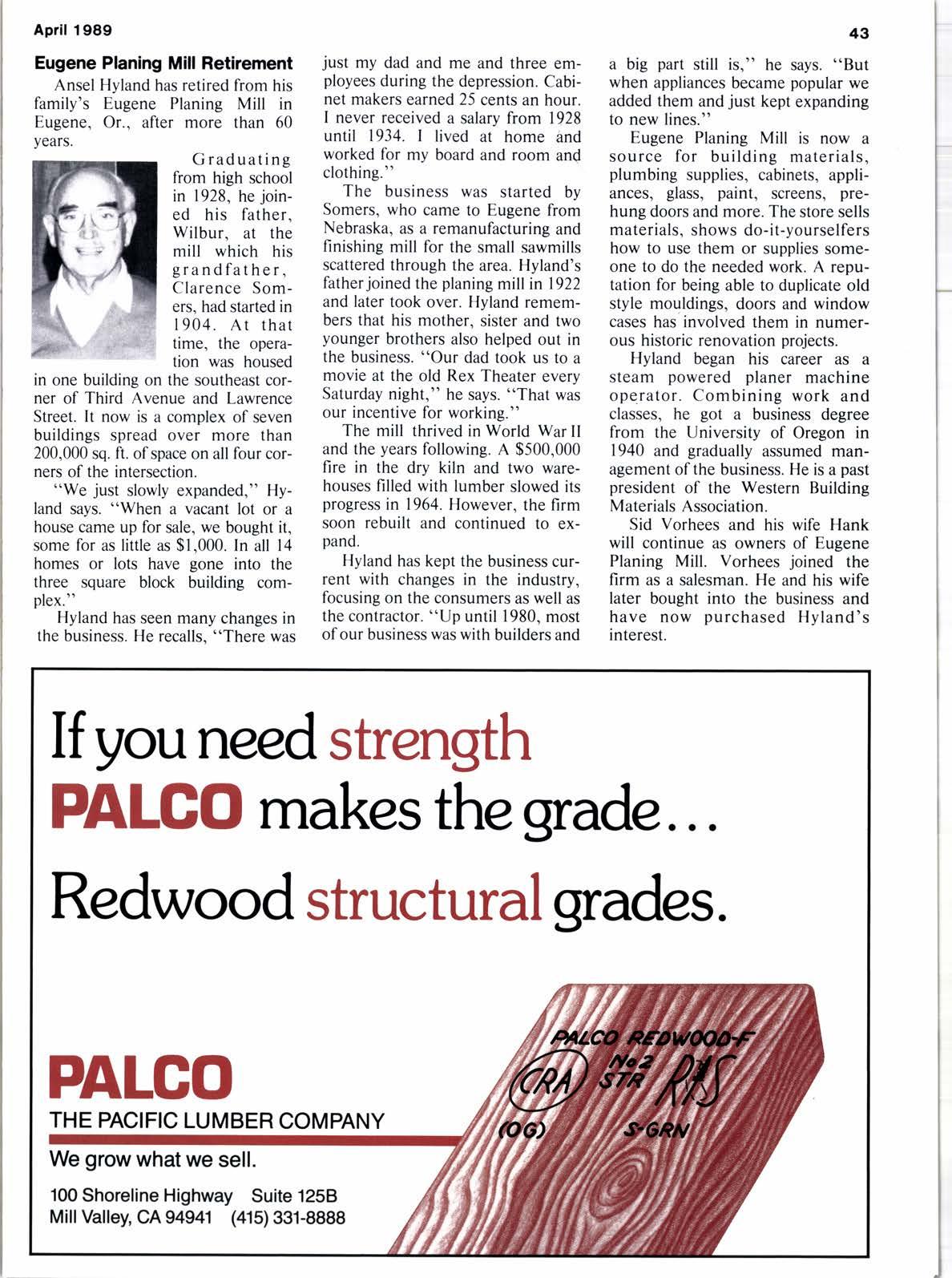
Hyland has kept the business current with changes in the industry, focusing on the consumers as well as the contractor. "Up until 1980, most of our business was with builders and a big part still is," he says. "But when appliances became popular we added them and just kept expanding to new lines." ing
Eugene Planing Mill is now a source for building materials, plumbing supplies, cabinets, appliances, glass, paint, screens, prehung doors and more. The store sells materials, shows do-it-yourselfers how to use them or supplies someone to do the needed work. A reputation for being able to duplicate old style mouldings, doors and window cases has involved them in numerous historic renovation projects.
Hyland began his career as a steam powered planer machine operator. Combining work and classes, he got a business degree from the University of Oregon in 1940 and gradually assumed management of the business. He is a past president of the Western Building Materials Association.
Sid Vorhees and his wife Hank will continue as owners of Eugene Planing Mill. Vorhees joined the firm as a salesman. He and his wife later bought into the business and have now purchased Hyland's interest.
COMPLY Lap Siding is a profit-building luxury that you can't afford to be without.
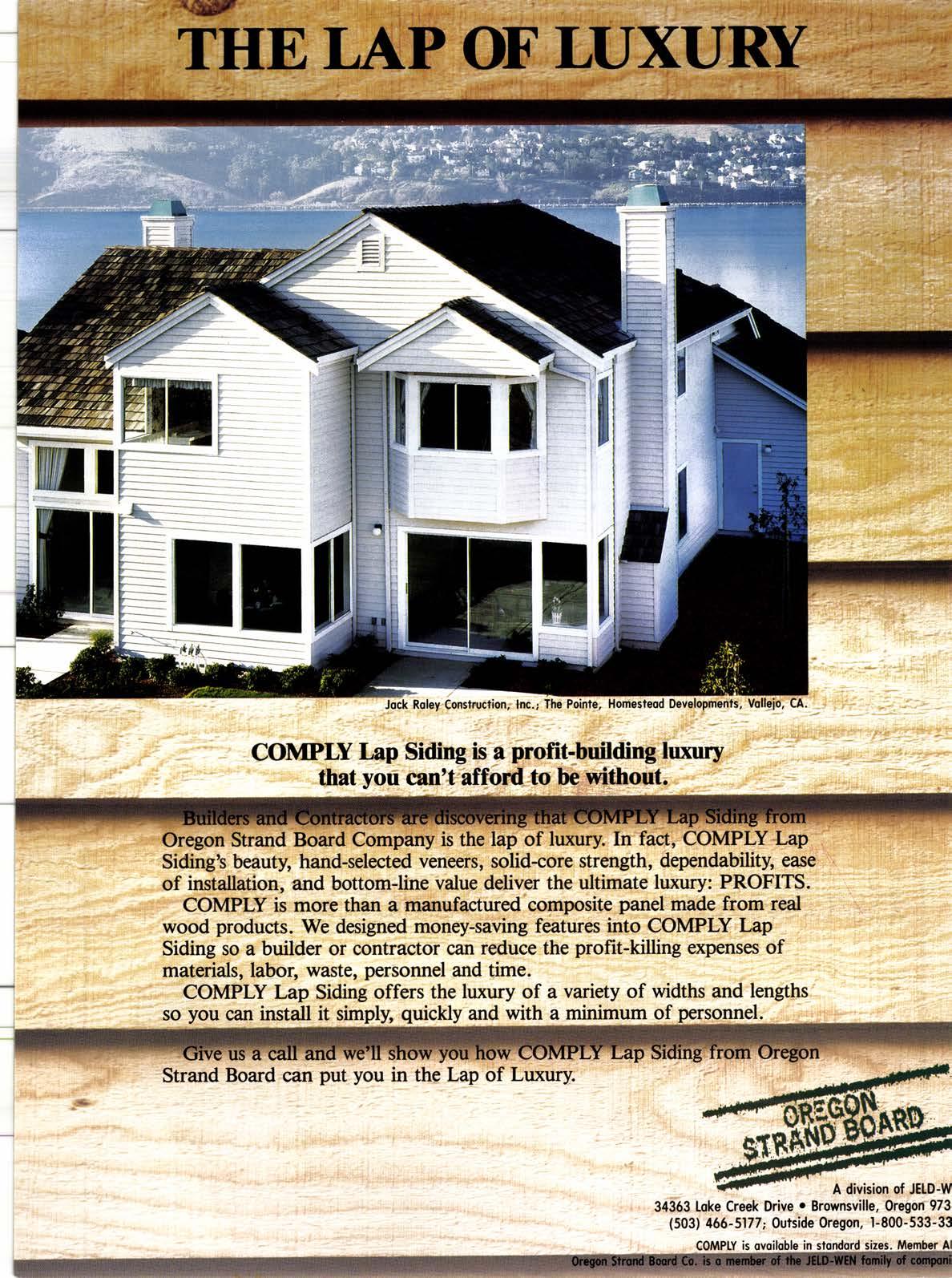
Oregon Strand Board Company is the lap of luxury. In fact, COMPLY Lap Siding's beauty, hand-selected veneers, solid-core strength, dependability, ease of installation, and bottom-line value deliver the ultimate luxury: PROFITS.
COMPLY is more than a manufactured composite panel made from real wood products. We designed money-saving features into COMPLY Lap Siding so a builder or contractor can reduce the profit-killing expenses of materials, labor, waste, personnel and time.
COMPLY Lap Siding offers the luxury of a variety of widths and lengths so you can install it simply, quickly and with a minimum of personnel.
Strand Board can US ld we'il snow you now uuMt put you in the Lap of Luxury.
New High Tech Treating Phnt
Cornett Wood Treating Co., White City, Or., is installing a state of the art treating facility that incorporates the technology to not only meet, but to exceed EPA guidelines with no air discharge, no fluid discharge, and no solid discharge.
In addition to safety devices to meet all EPA specifications, the plant will have a backup system capable of handling any emergency.
The facility will treat lumber, plywood and poles using CCA-C a waterborne preservative registered for use with the EPA. Treated material will be kiln dried after treatment. To meet Pacific Northwest market demand for a cedar brown color, an acrylic based pigmented stain will be applied to the surface of the wood. Treating production capacity will be approximately 40 million b.f. per year or 170 thousand b.f. per shift on a two shift basis.
The project is being coordinated by JayBee, Inc., Hillsboro, Or., who will handle the turnkey system installation. Rentokil and CSI are suppliers and consultant$.
The lumber handling system will require a minimum of plant operators: four equipment operators, two forklift drivers and a treatment plant operator. They will be able to process a half million board feet per shift.
The lumber handling system will unstack, incise, sort, stick and stack lumber from 2"x4" through 6"x14" and in lengths from 6 ft. through 24 ft.
Three 50 thousand b.f. dehumidification dry kilns will be used to predry lumber to assure maximum chemical penetration.
Incoming lumber will be off-loaded from trucks under roofand stored inside prior to entering the lumber handling system. The infeed to the incising and stacking system is located in this area which can store about two million board feet. The entire operation is conducted under roof, over two acres, to prevent rain water and then ground water from being contaminated. Treated lumber storage also can handle about two million board feet.
Treated packages coming from the stacker will be stored near the feed-through chains which can cycle a full shift of lumber into the drip pad area. The fork lifts handling storage will never drive onto the drip pad and the drip pad fork lift will never leave that area. There will be storage space for two shifts' production, allowing the lumber a 24 hour drip time.
After the drip pad, the loads will be put into the dry kilns to fix the CCA. Then they will be stored in the treated wood storage area prior to wrapping and shipping by either truck or rail.
Production is expected to begin in early summer.
Falllng Lumber Kills Worker
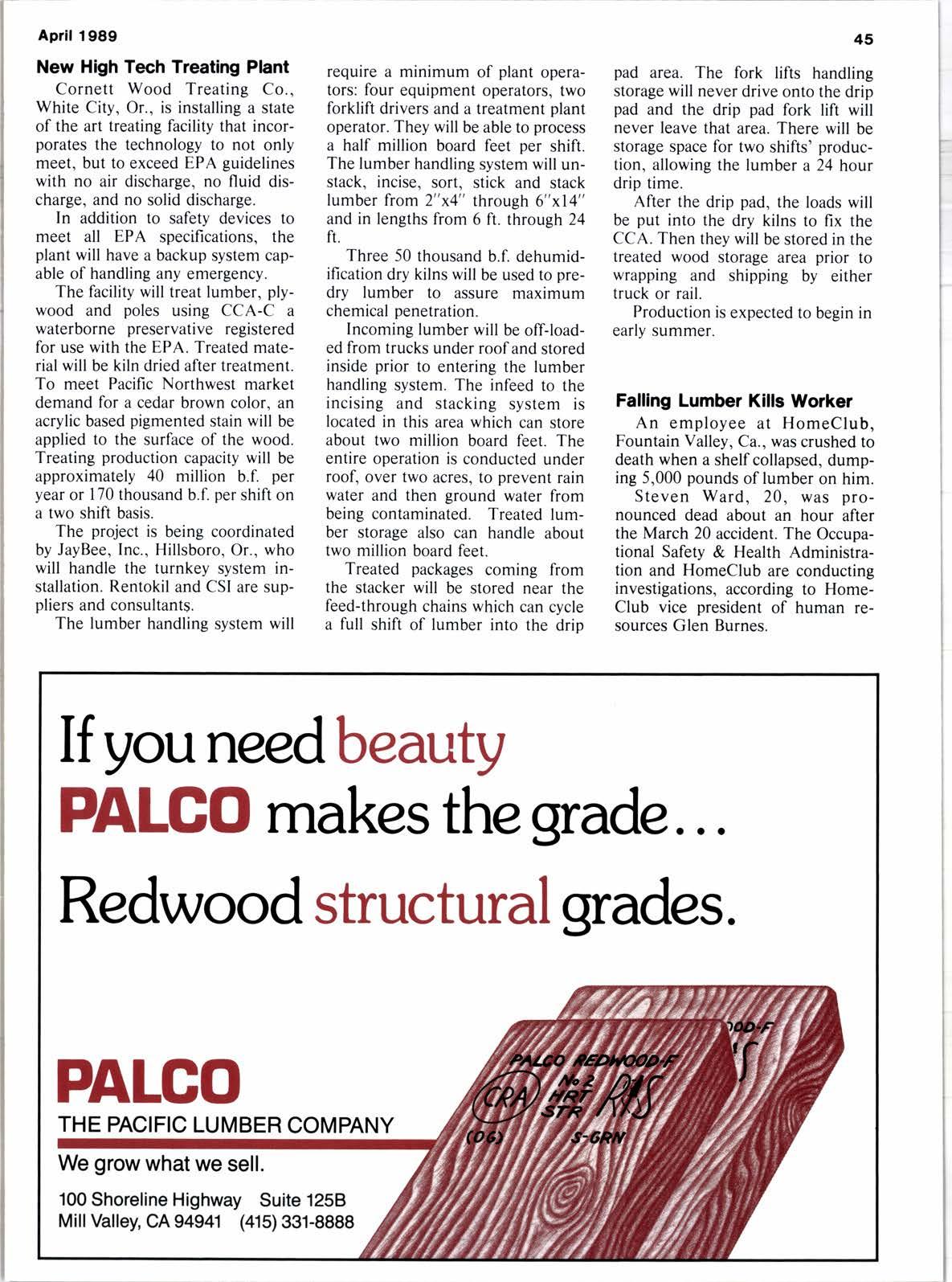
An employee at HomeClub, Fountain Valley, Ca., was crushed to death when a shelf collapsed, dumping 5,000 pounds of lumber on him.
Steven Ward, 20, was pronounced dead about an hour after the March 20 accident. The Occupational Safety & Health Administration and HomeClub are conducting investigations, according to HomeClub vice president of human resources Glen Burnes.