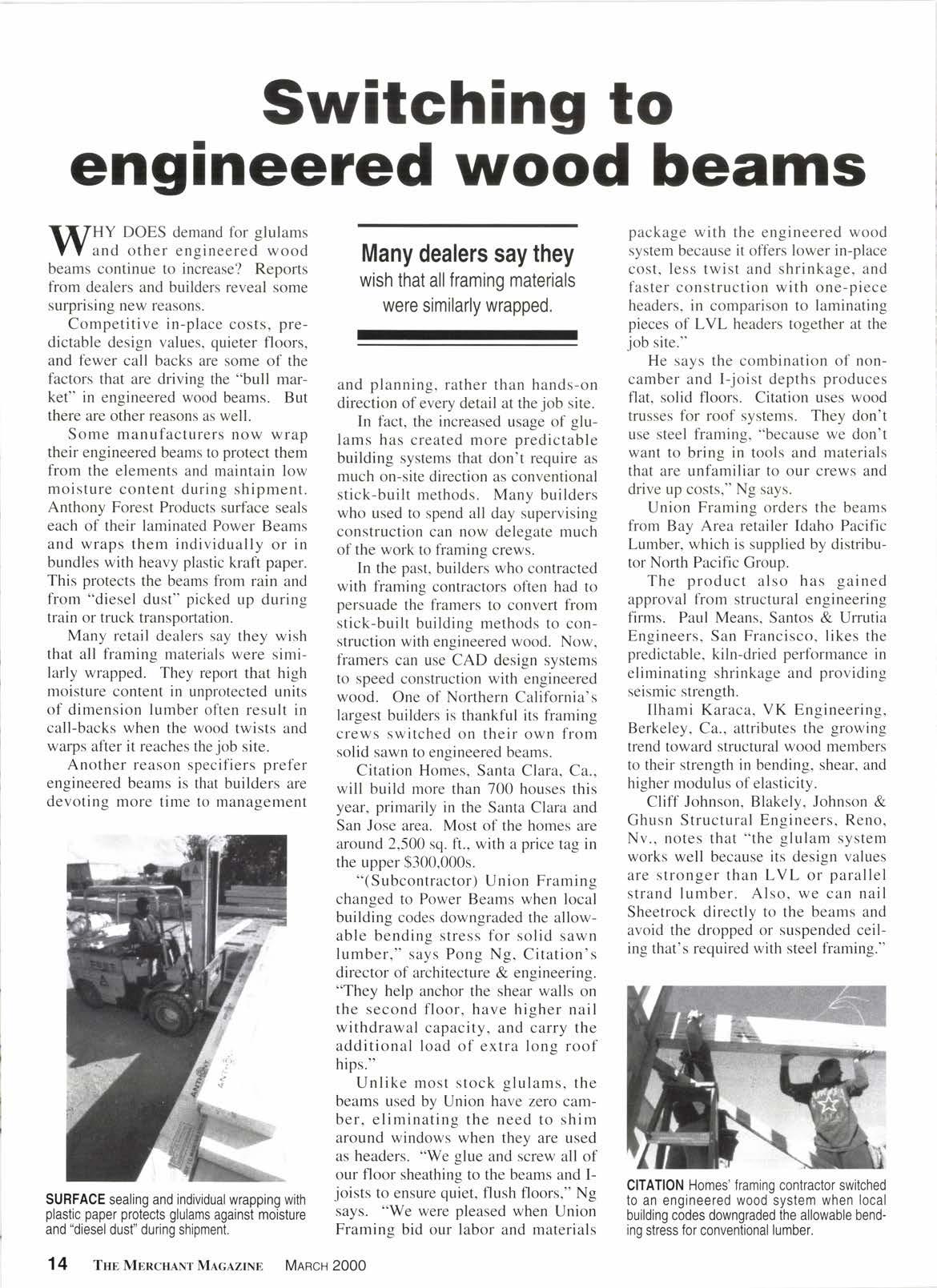
2 minute read
Switching to engineered wood beams
II/HY DOES demand for glulams
V Y and other ensineered wood beams continue to inirease? Reports from dealers and builders reveal some surprising new reasons.
Competitive in-place costs, predictable design values, quieter floors, and f-ewer call backs are some of the factors that are driving the "bull market" in engineered wood beams. But there are other reasons as well.
Some manufacturers now wrap their engineered beams to protect them from the elements and maintain low moisture content during shipment. Anthony Forest Products surface seals each of their laminated Power Beams and wraps them individually or in bundles with heavy plastic kraft paper. This protects the beams from rain and from "diesel dust" picked up during train or truck transportatron.
Many retail dealers say they wish that all framing materials were similarly wrapped. They report that high moisture content in unprotected units of dimension lumber often result in call-backs when the wood twists and warps after it reaches the job site.
Another reason specifiers prefer engineered beams is that builders are devoting more time to management
Many dealers say they wish that allframing materials were similarly wrapped, and planning, rather than hands-on direction ofevery detail at thejob site.
In fact, the increased usage of glulams has created more predictable building systems that don't require as much on-site direction as conventional stick-built methods. Many builders who used to spend all day supervising construction can now delegate much of the work to framing crews.
In the past, builders who contracted with framing contractors often had to persuade the framers to convert from stick-built building methods to construction with engineered wood. Now, framers can use CAD design systems to speed construction with engineered wood. One of Northern California's largest builders is thankful its framing crews switched on their own from solid sawn to engineered beams.
Citation Homes, Santa Clara, Ca., will build more than 700 houses this year, primarily in the Santa Clara and San Jose area. Most of the homes are around 2,500 sq. ft., with a price tag in the upper $300,000s.
"(Subcontractor) Union Framing changed to Power Beams when local building codes downgraded the allowable bending stress for solid sawn lumber," says Pong Ng, Citation's director of architecture & engineering. "They help anchor the shear walls on the second floor, have higher nail withdrawal capacity, and carry the additional load of extra long roof hips."
Unlike most stock glulams, the beams used by Union have zero camber, eliminating the need to shim around windows when they are used as headers. "We glue and screw all of our floor sheathing to the beams and Ijoists to ensure quiet, flush floors," Ng says. "We were pleased when Union Framine bid our labor and materials package with the engineered wood system because it offers lower in-place cost, less twist and shrinkage, and faster construction with one-piece headers, in comparison to laminating pieces of LVL headers together at the job site."
He says the combination of noncamber and I-joist depths produces flat, solid floors. Citation uses wood trusses for roof systems. They don't use steel framing, "because we don't want to bring in tools and materials that are unfamiliar to our crews and drive up costs." Ng says.
Union Framing orders the beams from Bay Area retailer Idaho Pacific Lumber, which is supplied by distributor North Pacific Group.
The product also has gained approval from structural engineering firms. Paul Means, Santos & Umrtia Engineers, San Francisco, likes the predictable, kiln-dried performance in eliminating shrinkage and providing seismic strength.
Ilhami Karaca, VK Engineering, Berkeley, Ca., attributes the growing trend toward structural wood members to their strength in bending, shear, and higher modulus of elasticity.
Cliff Johnson, Blakely, Johnson & Ghusn Structural Engineers, Reno, Nv., notes that "the glulam system works well because its design values are stronger than LVL or parallel strand lumber. Also, we can nail Sheetrock directly to the beams and avoid the dropped or suspended ceiling that's required with steel framing."