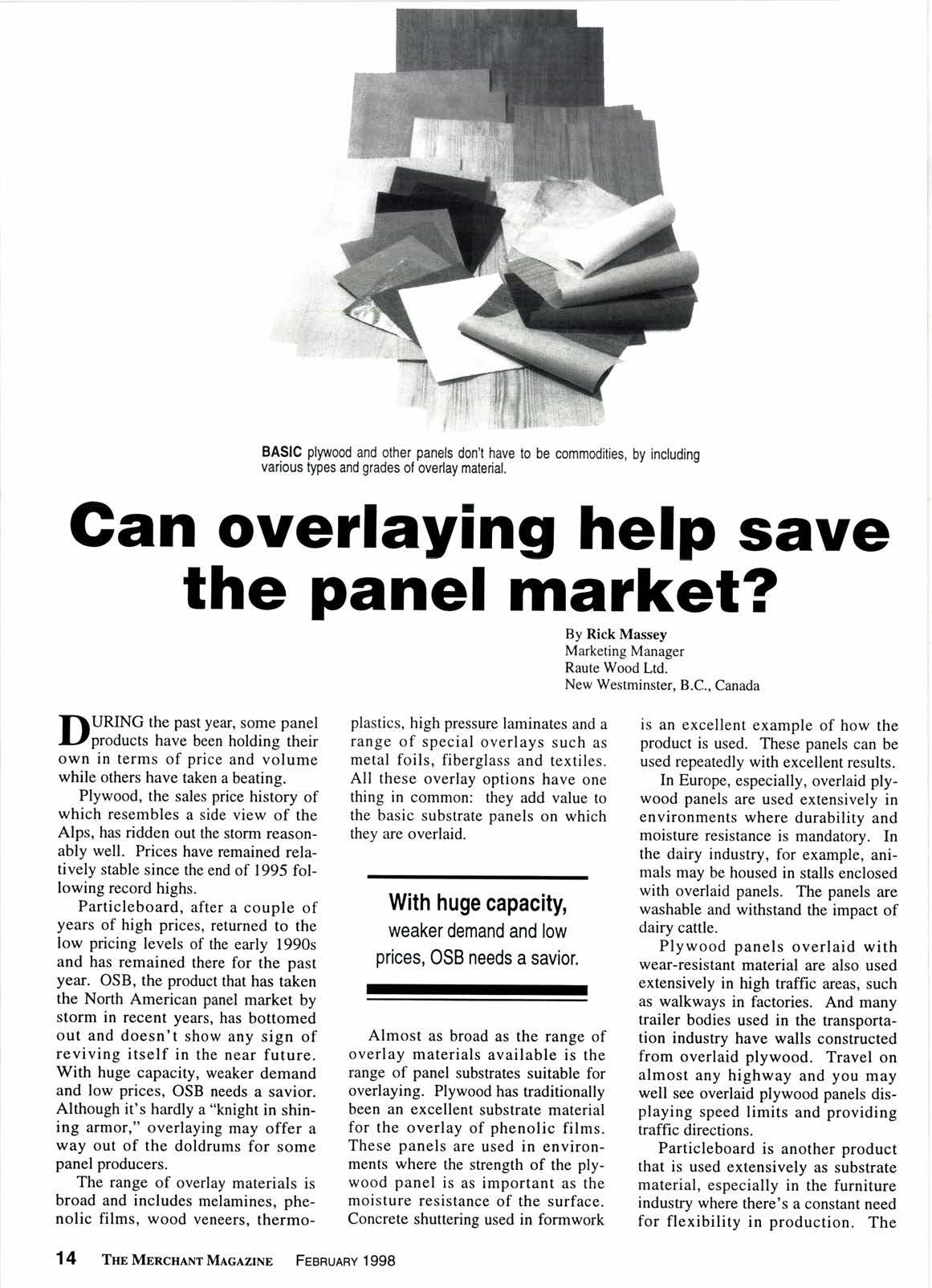
4 minute read
Gan overlaying help save the panel market?
By Rick Massey Marketing Manager Raute Wood Ltd. New Westminster, 8.C., Canada
nURING the past year, some panel I-lproducts have been holding their own in terms of price and volume while others have taken a beating.
Plywood, the sales price history of which resembles a side view of the Alps, has ridden out the storm reasonably well. Prices have remained relatively stable since the end of 1995 following record highs.
Particleboard, after a couple of years of high prices, returned to the low pricing levels of the early 1990s and has remained there for the past year. OSB, the product that has taken the North American panel market by storm in recent years, has bottomed out and doesn't show any sign of reviving itself in the near future. With huge capacity, weaker demand and low prices, OSB needs a savior. Although it's hardly a "knighr in shining armor," overlaying may offer a way out of the doldrums for some panel producers.
The range of overlay materials is broad and includes melamines, phenolic films, wood veneers. thermo- plastics, high pressure laminates and a range of special overlays such as metal foils, fiberglass and textiles. All these overlay options have one thing in common: they add value to the basic substrate panels on which they are overlaid.
With huge capacit$
weaker demand and low prices, 0SB needs a savior.
Almost as broad as the range of overlay materials available is the range of panel substrates suitable for overlaying. Plywood has traditionally been an excellent substrate material for the overlay of phenolic films. These panels are used in environments where the strength of the plywood panel is as important as the moisture resistance of the surface.
Concrete shuttering used in formwork is an excellent example of how the product is used. These panels can be used repeatedly with excellent results.
In Europe, especially, overlaid plywood panels are used extensively in environments where durability and moisture resistance is mandatory. In the dairy industry, for example, animals may be housed in stalls enclosed with overlaid panels. The panels are washable and withstand the impact of dairy cattle.
Plywood panels overlaid with wear-resistant material are also used extensively in high traffic areas, such as walkways in factories. And many trailer bodies used in the transportation industry have walls constructed from overlaid plywood. Travel on almost any highway and you may well see overlaid plywood panels displaying speed limits and providing traffic directions.
Particleboard is another product that is used extensively as substrate material, especially in the furniture industry where there's a constant need for flexibility in production. The tremendous growth of the RTA furniture business has generated a huge growth in the use of overlay materials, particularly thin veneers, films and melamines. As consumers in the developing nations improve their purchasing power, this sector of the overlaid panel business is expected to grow rapidly.
MDF (medium density fiberboard) and HDF (high density fiberboard) are two products that have readily adapted to the overlay business. Laminated flooring, in particular, has burst onto the home decorating scene in an unprecedented manner. winning a significant share of the non-carpet market in a relatively short period of time. Developed in Europe and exploited to its fullest potential in North America, laminated flooring uses MDF, HDF or particleboard as the substrate. The face material, often a wood "look-alike," is impregnated or glued onto the surface of the substrate. With its fine properties, laminated flooring has become a popular product. Some of the special advantages offered by laminated flooring are its scratch and impact resistance and its resistance to UV light, direct heat and staining. It is also a designer product, available in an infinite number and variety of colors and patterns. It's easy to keep clean and may be non-allergenic, especially important when considering respiratory conditions. It has a relatively thin profile, making it excellent for the home renovation market, and it's fast and simple to install. Also, at the end of its life cycle it can be disposed of without undue impact on the environment.
OSB, too, is getting in on the overlay act. Although the unevenness of the panel's surface does not make OSB a suitable candidate in many overlay applications, there have been a number of successes. One large U.S. producer has for a number of years been turning OSB into exterior siding material with the application of proprietary overlay material. Despite some early quality setbacks, the technology has been embraced by the construction industry and OSB siding, given the right climatic and installation conditions, performs well.
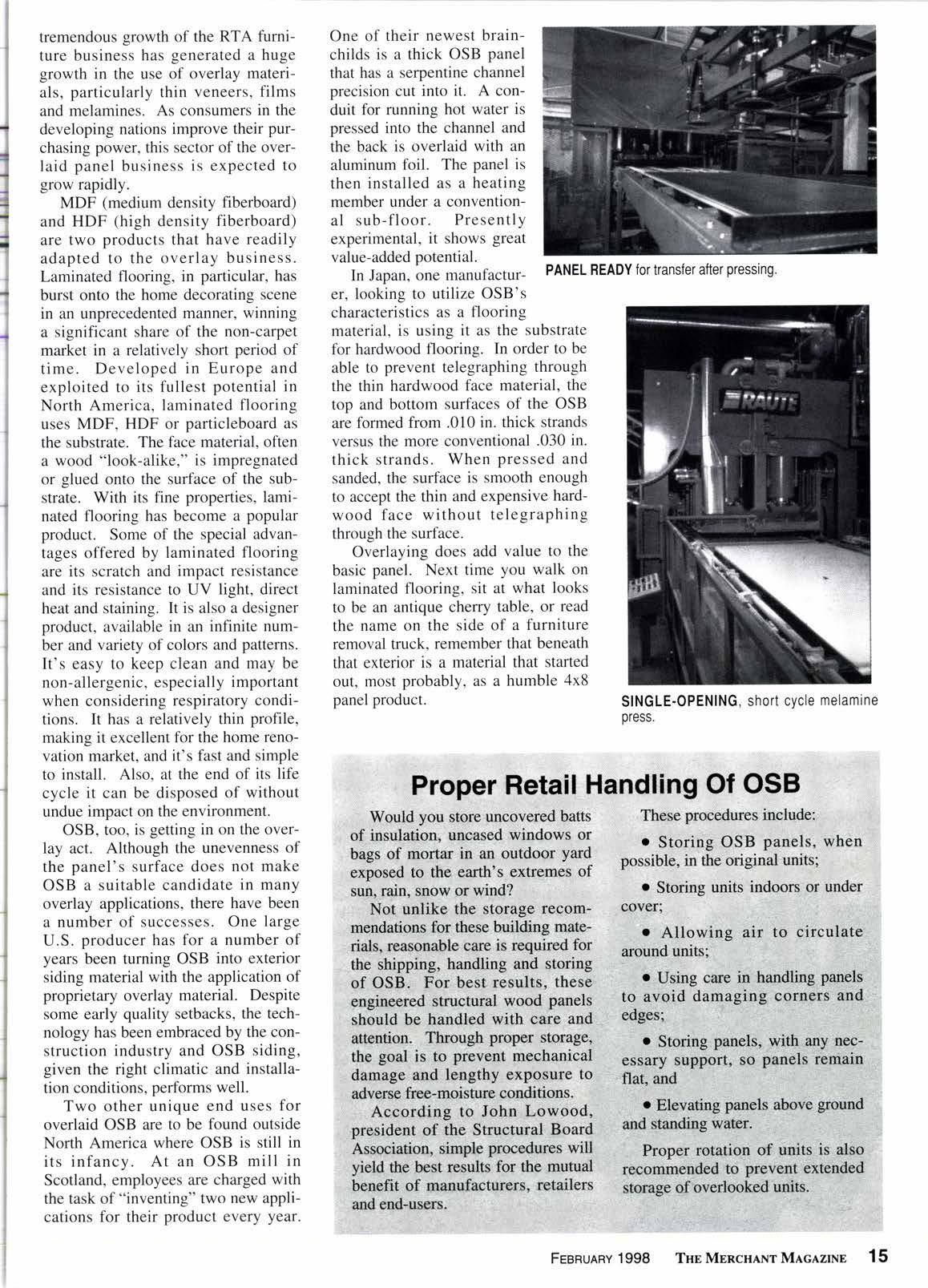
Two other unique end uses for overlaid OSB are to be found outside North America where OSB is still in its infancy. At an OSB mill in Scotland, employees are charged with the task of "inventing" two new applications for their product every year.
One of their newest bratnchilds is a thick OSB panel that has a serpentine channel precision cut into it. A conduit for running hot water is pressed into the channel and the back is overlaid with an aluminum foil. The panel is then installed as a heating member under a conventional sub-floor. Presently experimental, it shows great value-added potential.
In Japan, one manufacturer, looking to utilize OSB's characteristics as a flooring material, is using it as the substrate for hardwood flooring. In order to be able to prevent telegraphing through the thin hardwood face material, the top and bottom surfaces of the OSB are formed from .010 in. thick strands versus the more conventional .030 in. thick strands. When pressed and sanded, the surface is smooth enough to accept the thin and expensive hardwood face without telegraphing through the surface.
Overlaying does add value to the basic panel. Next time you walk on laminated flooring, sit at what looks to be an antique cherry table, or read the name on the side of a furniture removal truck, remember that beneath that exterior is a material that started out, most probably, as a humble 4x8 panel product.