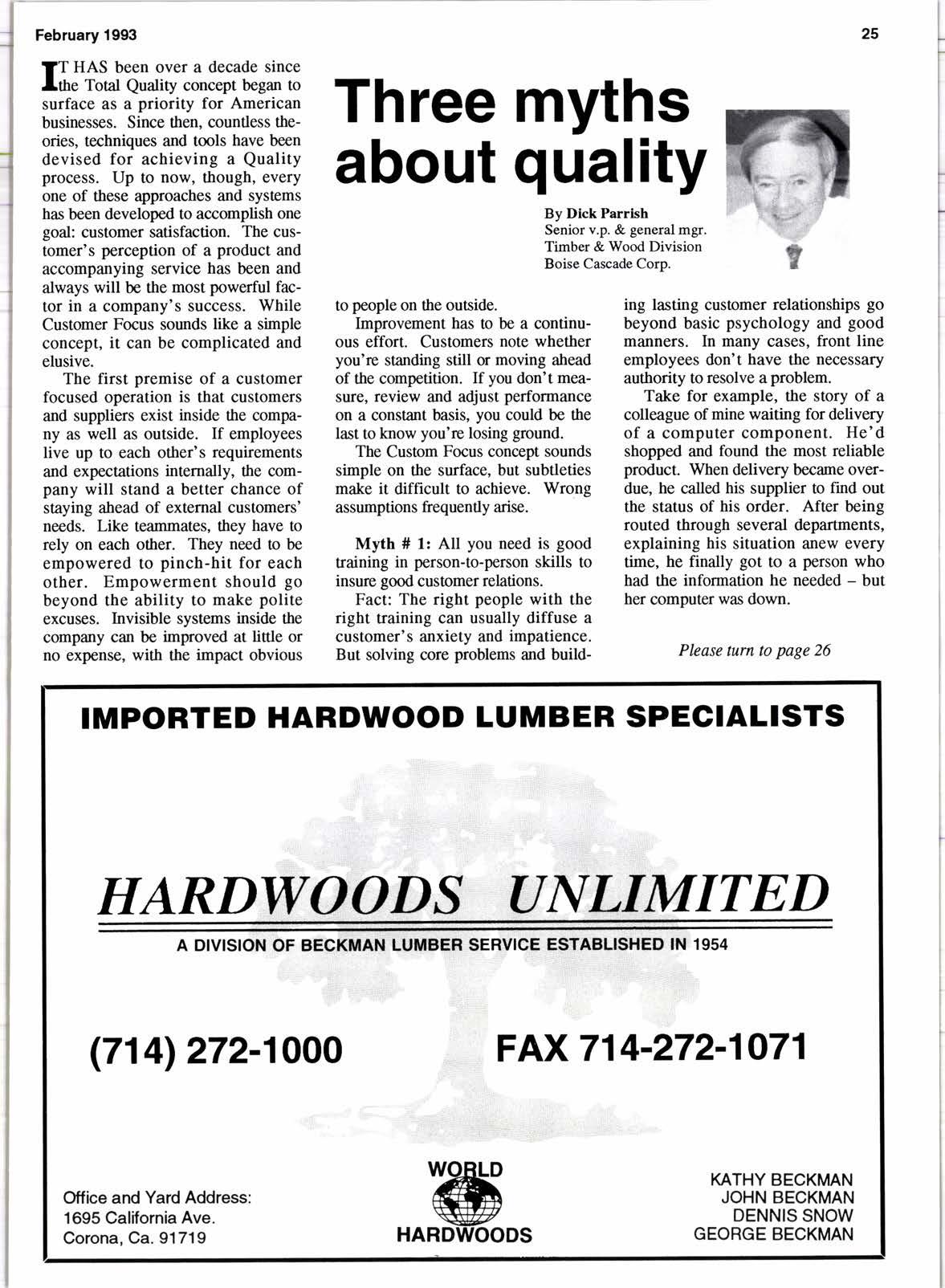
5 minute read
Three myths about quality
By Dtck Parrlsh Senior v.p. & general mgr. Timber & Wood Division Boise Cascade Corp.
to people on the outside Improvement has to be a continuous effort. Customers note whether you're standing still or moving ahead of the competition. If you don't measure, review and adjust perfomtance on a constant basis, you could be the last to lnow you're losing ground.
The Custom Focus concept sounds simple on the surface, but subtleties make it difficult to achieve. Wrong assumptions ftequently arise.
Myth # 1: All you need is good training in person-to-person skills to insure good customer relations.
Fact: The right people with the right training can usually diffuse a customer's anxiety and impatience. But solving core problems and build- fing lasting customer relationships go beyond basic psychology and good manners. In many cases, front line employees don't have the necessary authority to resolve a problem.
Take for example, the story of a colleague of mine waiting for delivery of a computer component. He'd shopped and found the most reliable product. When delivery becane overdue, he called his supplier to find out the status of his order. After being routed through several depar0nents, explaining his situation anew every time, he finally got to a person who had the infomntion he needed - but her computer was down.
Please turn to page 26
Myths About Quality
Continuedfrompage 25
Everyone had been understanding and courteous. They'd done everything in their power, but could not solve the problem. A few even voiced frustration at intemal systems that prevented helping him. when the product finally arrived, it performed as promised, but my colleague's impression of that company will be forever tainted.
Customer service personnel need access to every level of every department. If they don't have the authority to make a decision, they should be able to reach the person who can. In a company with Total Quality culture, Customer Focus pervades every area every office, every plant, every work station.
Myth f2: I can't do more for my customers without sacrifi cing something on my end.
Fact: When problems are approached correctly, your company is likely to benefit as much from the solution as the customer. Boise Cascade initiated a Total Quality commifinent several years ago which has led to a number of breaktbroughs in customer satisfaction. One of the most successful projects involved the ready date notification process of truckload shipments from our plywoodmills.
This project was targeted because of disparities in infomration circulating anong and between intemal peo- ple and external customers. customers were not notified that their shipment was ready until the order was sitting in the yard. This meant they could not schedule pickups in advance, nor alert their customers for delivery. They were losing time and increasing shipping fees. We were wasting yard space.
Customer feedback and suggestions proved invaluable in mapping a new plan. From the beginning it was obvious that any solution would involve deparfinents across the entire division. Solving this problem was a test of both our people's training and their faith in our Total Quality system.
A cross functional team was fonned witl volunteers from departments involved. With flow charts, cause-and-effect diagrams and other problen-solving tools, they documented the entire process, identified root causes and set about improving the situation.
Plywood customers are now notified of their ready date for trucks the week prior to the ship date. This saves them scheduling time and allows them to predict delivery dates for clients.
Internal operations dramatically improved. Our truckload inventory time was reduced from an average of four days to under a day and a half. The project made it easier for extemal customers to do business with us. It also improved internal efficiency and morale and spawned improvement opportunities. Improving internal processes not only improves productivity, it contributes a host of other workplace benefits.
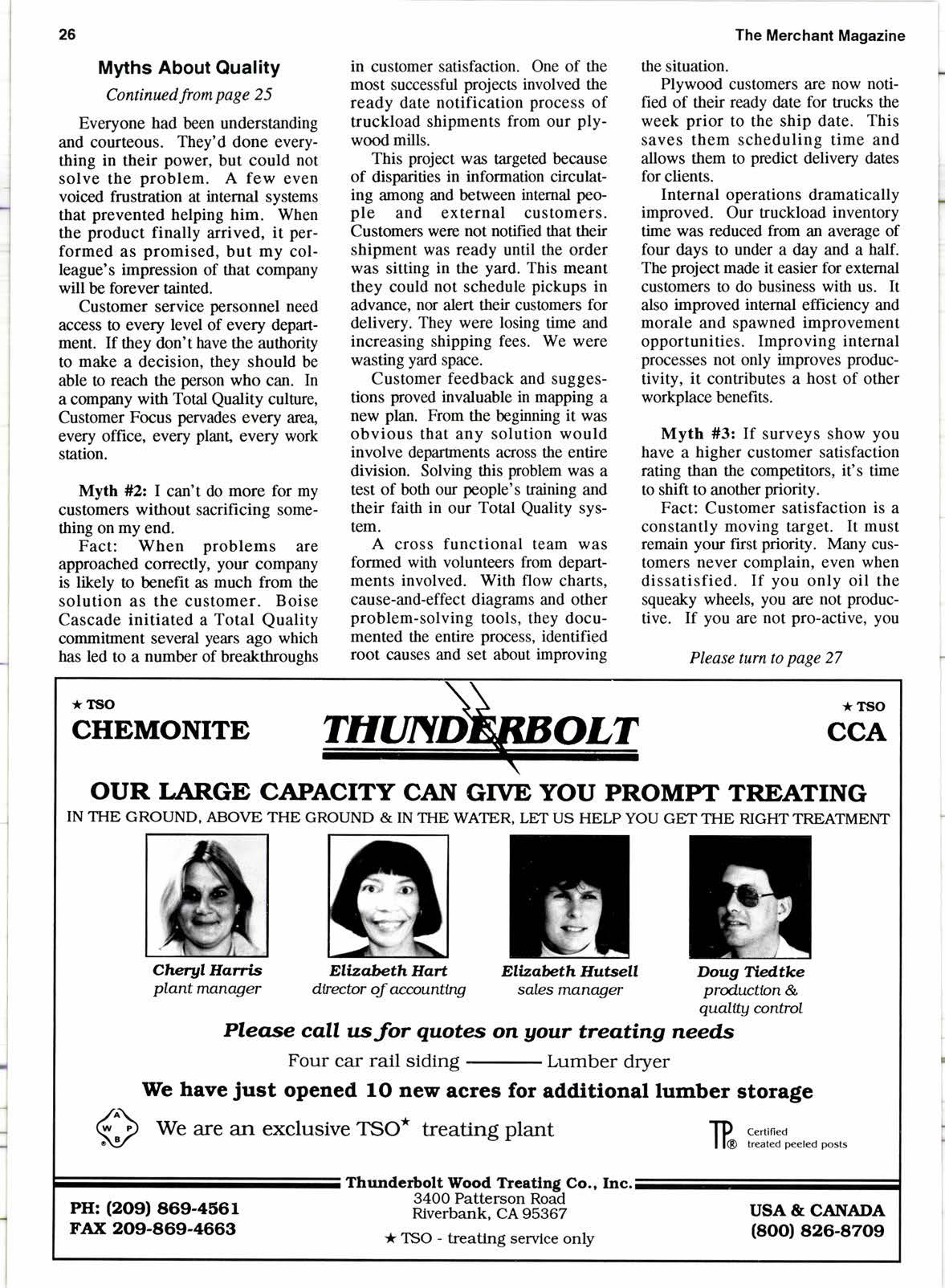
Myth #3: If surveys show you have a higher customer satisfaction rating than the competitors, it's time to shift to another priority.
Fact: Customer satisfaction is a constantly moving target. It must remain your frst priority. Many customers never complain, even when dissatisfied. If you only oil the squeaky wheels, you are not productive. If you are not pro-active, you
Please tum to page 27
ccA Little Threat to sea Life
Results are expected this spring from a study investigating the effects of CCA treated piling on marine organisms.
Funded by Hickson Corp., tie research will answer questions about possible toxicity. "Marine life grows abundantly on treated wood Piling," Bill Baldwin, vice president for environmental and technical services at Hickson, said. "We lnow of no hazards and hope this study, using the most scrupulous scientific procedures, will fill a research void and determine definitively there is a no basis for concern."
National Gypsum Value Set
National Gypsum Co. said a bankruptcy court's determination of a $350 million value for the company is a "big step forward" in the wallboard manufacturer's efforts to reorganize. A committee of bond and credit holders had challenged the company's plan saying it overpaid senior creditors and underpaid junior creditors and proposed a plan which valued the company at $630 million.
are fighting a losing battle.
Myths About Quality
Continuedfrom page 26
Companies depend on customers, intemal as well as external, to keep them in business. In a Total Quality environment, improvements affecting one are likely to affect the other.
Customer satisfaction needs to be constantly evaluated and reevaluated. Any way that you can customize your product and accompanying service will be perceived by your customer as added value and build loyalty to maintain a lasting relationship.
The project at our plywood mills is but one of many examples of how the Total Quality process is improving business at Boise Cascade. In a relatively short time, we have seen dramatic benefits - not only for our external customers, but for ouf own people. Total Quality is effective as a problem solving tool, as a morale booster for employees, and as a guide to customer satisfaction. I am convinced it is the most powerful management approach yet developed in this half of the Twentieth Century.
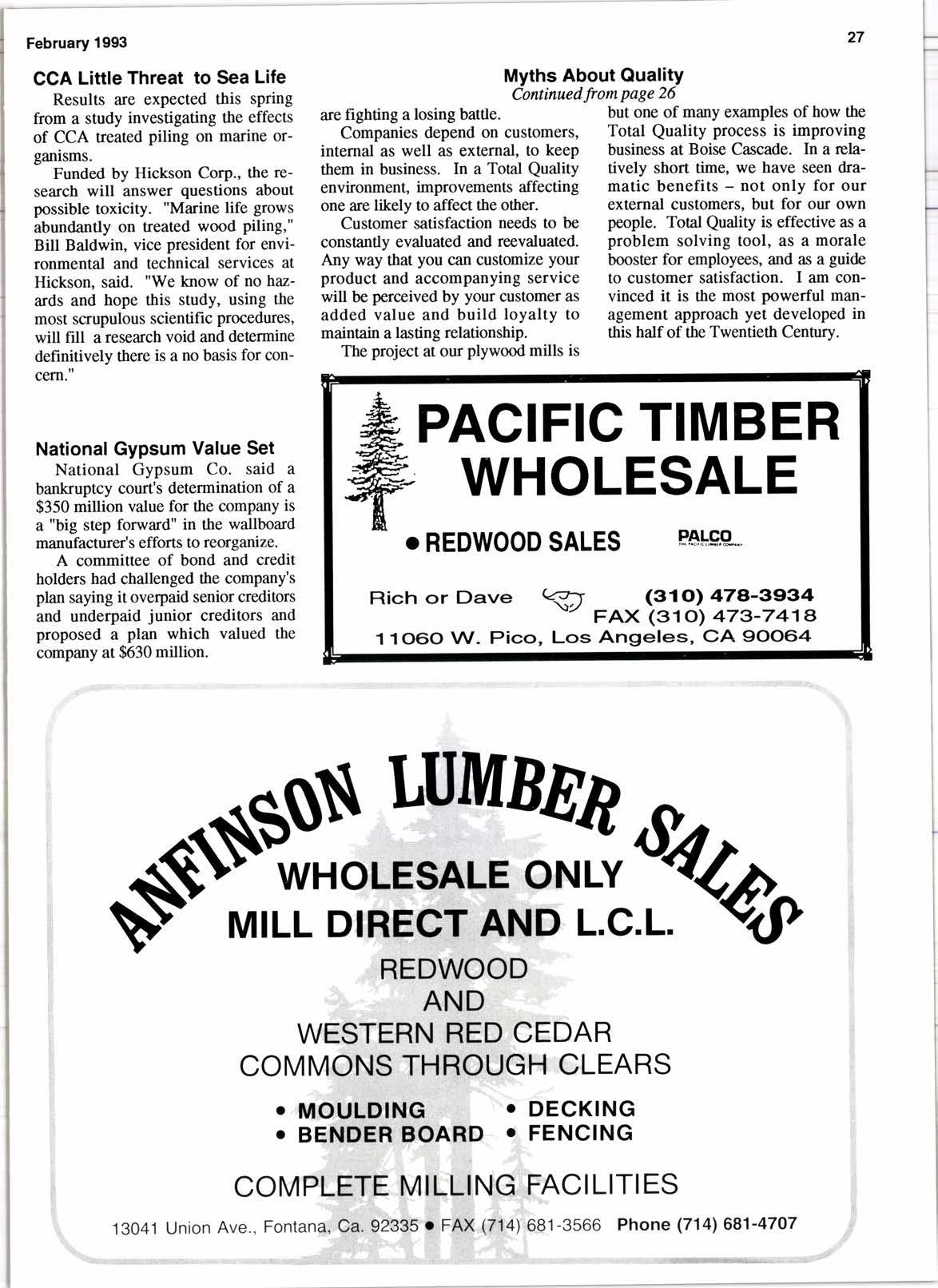
Structural Panel Tariffs Cut
Tariffs have been cut in half on U.S. and Canadian plywood and completely eliminated on oriented strand board, waferboard and particleboard under a tariff reduction schedule implemented by both countries.
Tariff on Canadian plywood entering the U.S. has been rcduced to l07o and will be phased out in equal annual increments, reaching zero Jan. l, 1998. The tariff, now 7.57o, on U.S. plywood entering Canada will be reduced in the same rnanner.
Reduction was made possible by resolution of a long standing dispute between the two counries over harmonization of structural wood panel performance standards. Standards developed by a Binational Comminee of technical experts are now approved and recognized in both cormtries.
The American Plywood Association has been accredited as a certification agency by the Standards Council of Canada. Without this, U.S. structural wood panel manufacturers would have been virtually excluded from the Canadian market.
Fire Gode Task Force Forms
Proposed changes in sprinkler fre patio furniture, tools, garden hose, codes that could significantly increase trash bags, trash cans, bird feeders, tgt"iletj'costs have prompted fonna- plastic pots, sprinklers, pails, tion of an industry task force to de- sprayers, toys, small appliances and velop less costly sprinkler alterna- foampackaging. tives.
"The new systems could cost each lnange_s^1vlich may ake effect as rerairer or manufacturer an average of early as 1994 apply to Group "A" $25,000 per store with no significant plastics including paint trays and improvement in safety," said spokesbrushes, drop cloths, shop vacuums, man Jim Tomes. Home Depot and tool boxes, truck boxes, flashlights, HomeBase have joined the tasi force. t.a.u1d1y tubs, foam pipe insulation, HomeQuarters and Eagle Hardware ABS drain pipe, shower enclosures, or€ considering taking part. lighting, telephones, smoke detectors,
SOFTWOOD, ., HARDWOOD ., PLYWOOD . PALLET STOCK